Système de porte - Définition, fonction, types, diagramme
Qu'est-ce que le système de déclenchement
Le terme porte est défini comme l'un des canaux qui en fait conduit dans la cavité du moule , et le terme gating ou système de gating fait référence à tous les canaux au moyen desquels le métal en fusion est acheminé vers la cavité du moule.
Fonctions d'un système de déclenchement
Les fonctions d'un système de blocage sommes :
- Fournir une alimentation continue et uniforme de métal en fusion , avec le moins de turbulence possible dans la cavité du moule. Une turbulence excessive entraîne l'aspiration d'air et la formation de scories.
- Pour fournir le casting avec du métal liquide au meilleur emplacement, obtenir une solidification directionnelle appropriée et des cavités de retrait d'alimentation optimales.
- Pour remplir la cavité du moule avec du métal en fusion dans le tome le plus court possible pour éviter les gradients de température.
- Fournir avec un minimum d'excès de métal dans les portes et contremarches. Un taux d'entrée de métal inadéquat, d'autre part, entraînera de nombreux défauts dans le moulage.
- Pour prévenir l'érosion des parois du moule.
- Pour éviter les scories , poncer et autres particules étrangères d'entrer dans le moule.
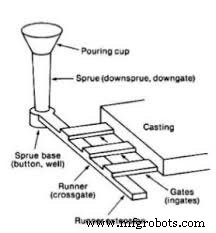
Système de porte
Un système de vannes est généralement composé de (1) bassin de coulée , (2) grappe , (3)coureur , et (4) flux –hors porte . Ils sont illustrés à la Fig. 11.85.
1. Bassin verseur
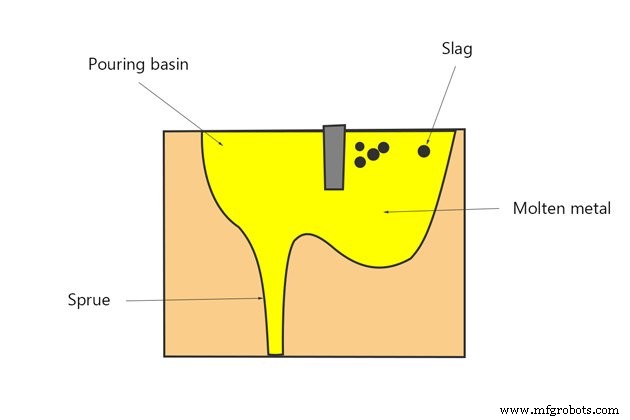
Bassin verseur : – Cette partie du système d'injection est réalisée sur ou dans le haut du moule. Parfois, un en forme d'entonnoir l'ouverture qui sert de bassin de coulée, est pratiquée au sommet de la carotte dans la chape. L'objectif principal du bassin de coulée est de diriger le flux de métal de la poche de coulée vers la cheminée, d'aider à maintenir le débit requis d'écoulement de métal liquide et de réduire les turbulences et les vortex à l'entrée de la cheminée.
Le bassin doit être assez grand et doit être placé près du bord de la boîte de moulage pour remplir rapidement le moule. En outre, il doit être suffisamment profond pour réduire la formation de tourbillons et maintenu plein pendant toute l'opération de coulée pour compenser le retrait ou la contraction du métal.
2. Sprue
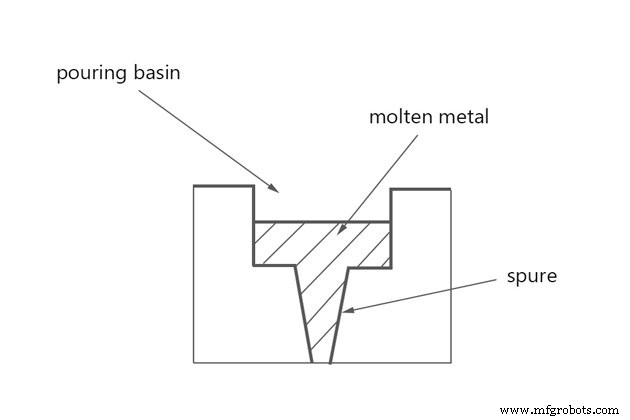
Sprue : Le passage vertical qui traverse la chape et relie le bassin de coulée au coureur ou à la porte s'appelle la carotte.
La section transversale d'une carotte peut être carrée, rectangulaire ou circulaire. Les carottes sont généralement effilées vers le bas pour éviter l'aspiration d'air et un endommagement du métal. Les carottes jusqu'à 20 mm de diamètre sont de section ronde tandis que les carottes plus grandes sont souvent rectangulaires. Une carotte ronde a une surface minimale exposée au refroidissement et offre la plus faible résistance au flux de métal. Dans une carotte rectangulaire, l'aspiration et la turbulence sont minimisées.
3. Coureur
Coureur : Dans les grandes pièces moulées, le métal en fusion est généralement transporté de la base de la carotte à plusieurs portes autour de la cavité à travers un passage appelé le coureur. La lisse est généralement préférée dans la drague, mais elle peut parfois être située dans la chape, selon la forme du lancer. Il doit être profilé pour éviter l'aspiration et les turbulences.
4. Porte
Portail : Une porte est un passage à travers lequel le métal en fusion s'écoule du canal d'alimentation vers la cavité du moule. L'emplacement et la taille des portes sont agencés de manière à ce qu'elles puissent alimenter le métal liquide à la coulée à une vitesse compatible avec la vitesse de solidification. Une porte ne doit pas avoir d'arêtes vives car elles peuvent se briser lors du passage du métal en fusion et par conséquent des particules de sable peuvent passer avec le métal liquide dans la cavité du moule. Cependant, les portes doivent être situées à un endroit où elles peuvent être facilement retirées sans endommager le moulage.
Types de système de déclenchement
Selon leur position dans la cavité du moule, le déclenchement peut être généralement classé comme (1) déclenchement supérieur , (2) porte de séparation , et (3) gating inférieur . Les différents types de systèmes d'obturation dans le processus de coulée sont :
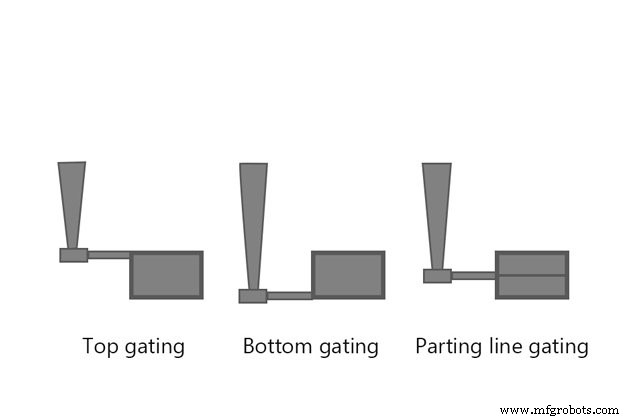
Portes supérieures
Dans le système de déclenchement supérieur , le métal en fusion du bassin de coulée s'écoule directement dans ça. Une crépine, faite de sable sec ou de matériau céramique, est principalement utilisée au niveau du bassin de coulée pour contrôler le flux de métal et ne laisser entrer que du métal propre.
Dans le cas des coulées légères, des portes en forme de coin appelées portes en coin peuvent être fournis. Pour les pièces moulées massives en fer, des portes crayons sont utilisées. Dans ce type de porte, la carotte est constituée d'une série de fentes alimentées à partir d'une coupelle verseuse. Il contrôle le taux d'écoulement du métal puisque le poids du métal en fusion est divisé de manière égale entre ses différentes fentes ou branches, ce qui réduit considérablement le poids effectif de la tête. De plus, les scories (ou scories) sont retirées du métal liquide dans le godet verseur au-dessus de la porte.
Dans la porte des doigts , une modification de la porte en coin, le métal est à nouveau autorisé à atteindre dans un certain nombre de flux. La porte annulaire utilise un noyau pour briser la chute du métal en fusion et envoie le métal en fusion dans le moule dans la bonne position, tout en retenant le laitier.
L'avantage du déclenchement par le haut est que tout le métal entre dans la coulée par le haut, et le métal le plus chaud vient donc se reposer au sommet de la coulée. En conséquence, des gradients de température appropriés favorables à une solidification directionnelle vers les colonnes montantes situées sur le dessus de la coulée sont atteints. Les portes elles-mêmes peuvent être conçues pour servir de contremarches. L'inconvénient du top gating système est l'érosion du moule par la chute du métal. La cavité du moule doit donc être suffisamment dure et solide pour résister à l'impact.
Portes de séparation
Dans les portes de séparation , le métal liquide pénètre dans la cavité du moule par le côté du moule au même niveau que le joint ou la ligne de séparation du moule. La disposition consistant à fournir une porte au niveau de la ligne de séparation dans une direction horizontale par rapport à la coulée permet l'utilisation de dispositifs capables de piéger efficacement tout laitier, saleté ou sable qui passe avec le métal dans la cheminée.
Porte d'écrémage
Dans une porte d'écrémage , tout corps étranger plus léger que le métal de base remonte par le passage vertical de la porte d'écrémage et est ainsi piégé. La porte de ligne de séparation avec écrémage et starter est utilisée pour piéger les scories et les corps étrangers dans le moule et pour servir de restriction pour contrôler le débit du métal.
Une autre méthode efficace pour piéger les scories consiste à utiliser une porte d'écumage avec un coureur de tourbillon, généralement appelée porte de tourbillon . Le laitier, en raison de l'action du tourbillon, arrive au centre d'où il monte dans la porte du tourbillon. La porte avec bobine rétractable remplit la double fonction de collecteur de scories ou de scories et de réservoir métallique pour alimenter la coulée au fur et à mesure qu'elle se rétracte.
Les portes de séparation sont très simples à construire , et très rapide à réaliser . Ils produisent des résultats très satisfaisants lorsque la traînée n'est pas très profonde, et s'avèrent très avantageux lorsqu'ils peuvent être introduits directement dans l'élévateur. Dans ce système, le métal le plus chaud atteint le riser, favorisant ainsi la solidification directionnelle. De plus, les coûts de nettoyage des pièces moulées sont réduits par l'entrée dans les colonnes montantes, car aucune porte supplémentaire n'est nécessaire pour connecter la cavité du moule à la colonne montante. L'inconvénient réside dans le fait que certaines turbulences peuvent se produire lorsque le métal liquide tombe dans la cavité du moule.
Portes inférieures
Dans les portes du bas , le métal du bassin de coulée s'écoule vers le fond de la cavité du moule lors de la traînée.
Porte en corne
La porte en corne ressemble à la corne d'une vache. Il permet de réaliser le moule en chape et traînée uniquement; il n'y a pas besoin d'un "contrôle ”. La porte en corne a tendance à produire un effet de fontaine dans la cavité du moule. Dans un autre type, noyau de sable sec forme la porte inférieure. La cheminée est incurvée à l'extrémité inférieure pour former un collecteur de scories, salissures, etc. Ce type de porte permet de réaliser le moule en deux caissons.
Le principal avantage des portes inférieures est que la turbulence du métal est maintenue à un minimum tout en empêchant la coulée et l'érosion du moule. Le métal est autorisé à monter doucement dans le moule et autour des noyaux. Les portes inférieures, cependant, souffrent de certains inconvénients :le métal continue à perdre de sa chaleur en remontant dans la cavité du moule. La solidification directionnelle est donc difficile à réaliser. De plus, la colonne montante ne peut pas être placée près de l'entrée de la porte où le métal est le plus chaud.
Taux de déclenchement
La vitesse d'écoulement du métal à travers la cavité du moule est fonction de la section transversale de la carotte, des glissières et des portes. Les caractéristiques dimensionnelles d'un système de déclenchement peuvent être exprimées en termes de rapport de déclenchement. Le terme "taux de déclenchement ” est utilisé pour décrire les aires de section transversale relatives des composants d'un système de porte en prenant la surface de la base de carotte comme unité, suivie de la surface totale de la glissière et enfin de la surface totale de la porte.
Un système de porte ayant une carotte de 1 cm², un coureur de 3 cm² et trois portes, chacune ayant une section transversale de 1 cm2, aura un rapport de porte de 1:3:3. Le rapport de déclenchement révèle si la section transversale totale diminue ou augmente vers la cavité du moule. En conséquence, il existe deux types de systèmes de déclenchement dans le processus de coulée :pressurisé et sans pression ou à écoulement libre comme un système d'égout.
Système de déclenchement sous pression
Le système de fermeture sous pression a moins de section transversale totale aux entrées de la cavité du moule qu'à la base de la carotte. Ainsi, un système sous pression aurait un rapport de 1 : 0,75 : 0,5, 1 : 2 : 1 et 2 : 1 : 1. Cela produit un effet d'étranglement qui met sous pression le métal liquide dans le système. Comme ce système est de faible volume pour un débit de métal donné, il en résulte une moindre perte de métal et un meilleur rendement.
D'autre part, comme ce système se maintient plein de métal et fournit un effet d'étranglement, des vitesses de métal élevées peuvent avoir tendance à provoquer de fortes turbulences au niveau des jonctions et des coins et dans la cavité du moule. Ceci est cependant généralement adapté aux métaux ferreux et au laiton.
Système de déclenchement non pressurisé
Dans le système de porte sans pression , la section transversale de la carotte est inférieure à la surface totale de la glissière et à celle des ingates. Les rapports utilisés sont 1 :2 :2. 1:3 :3, etc. Ce système de gating produit donc des vitesses de métal plus faibles et permet des débits plus importants. En conséquence, il réduit les turbulences dans le système d'injection et les jaillissements dans la cavité du moule. Ce système est généralement adapté aux métaux tels que l'aluminium et le magnésium.
Nous avons essayé de couvrir toutes les parties importantes du sujet Système de déclenchement , types de système de déclenchement dans le processus de coulée et ses éléments. J'espère que vous avez apprécié l'article. Veuillez donner votre avis dans la section des commentaires ci-dessous.
Technologie industrielle
- Qu'est-ce qu'un hyperviseur ? Définition | Types | Exemples
- Conception du système de portes | Coulée | Sciences de la fabrication
- Qu'est-ce que l'estampage ? - Types, fonctionnement et application
- Qu'est-ce que le soudage ? - Définition | Types de soudage
- Qu'est-ce que le casting ? - Définition | Types de coulée
- Qu'est-ce qu'une perceuse ? - Définition, pièces et types
- Usinage CNC :définition et types de machines CNC
- Qu'est-ce que le forgeage ? - Définition, processus et types
- Qu'est-ce que le placage métallique ? - Définition, types et avantages