Planification des processus Estimation et calcul des coûts
Dans cet article, vous découvrirez l'estimation et l'établissement des coûts de la planification des processus et divers termes associés pour une compréhension claire.
Processus d'estimation et de calcul des coûts
ÉVALUATION DES COÛTS
Une conception de processus n'est pas complète tant que l'on n'a pas une bonne idée du coût nécessaire à la fabrication du produit. En général, la conception la moins coûteuse réussira sur un marché libre. Il est donc essentiel de comprendre les éléments qui composent le coût.
Éléments de coûts : Les constitutions d'un produit ou d'éléments de coût peuvent être globalement regroupées en (1) les coûts récurrents ou les coûts de fabrication ou les coûts d'exploitation et (2) coûts non récurrents. Ils peuvent à nouveau être classés comme coûts directs , coûts indirects tandis que les coûts d'investissement relèvent des coûts non récurrents. Les coûts récurrents comprennent tous les coûts directs et indirects, tandis que les coûts en capital relèvent des coûts non requis.
Direct Coûts
Coûts directs sont les coûts des facteurs qui peuvent être directement attribués à la fabrication d'un produit spécifique. Ceux-ci comprennent les coûts du matériel et de la main-d'œuvre. Coût matériel est le coût de ce matériau qui entre dans le produit fini et comprend tous les déchets qui ont été coupés du stock d'origine. Coût de la main-d'œuvre varie d'une machine à l'autre et est généralement calculé en multipliant le temps requis pour une opération par le taux de main-d'œuvre. Ainsi, le temps de mise en place et de réalisation d'une opération doit être estimé pour connaître son coût de main d'oeuvre.
Indirect coûts
Coûts indirects sont les coûts des facteurs qui ne peuvent être attribués qu'indirectement à la fabrication d'un produit spécifique. Ils sont parfois appelés overheads ou sur les coûts . Les frais généraux sont généralement calculés en multipliant le temps de fonctionnement par un taux de frais généraux. Un tel taux est obtenu en divisant le total des coûts indirects applicables à une unité de fabrication pour une période de temps (disons un mois ou une semaine) par le nombre total d'heures de travail direct au cours de la même période.
Capital coûts
Coûts d'investissement sont des coûts non récurrents ou des coûts non récurrents qui comprennent des installations amortissables telles que des usines, des bâtiments ou des équipements et outils de fabrication, et des coûts en capital non amortis, tels que des terrains. Les coûts d'investissement sont déterminés en répartissant les principaux coûts des machines et des outils sur une base horaire ou entre les pièces produites.
Le coût total d'un produit est le coût direct de fabrication du produit plus tous les coûts indirects attribués à la fabrication du produit.
Pour que l'ingénieur de procédé utilise les données de coût comme un outil pour aider à analyser le problème de fabrication, les coûts peuvent être plus judicieusement regroupés en coûts fixes et coûts variables.
Fixed costs include preparation costs such as of tooling setting up, etc., and also the interest and depreciation costs which are independent of the quantity of the product manufactured.
Variable costs are those costs which vary as the quantity of product made varies. This includes the direct labour and material costs, and also that part of the indirect costs which will vary as production varies. The total cost of a product can also be seen to be fixed cost plus variable cost.
Cost Structure
Cost structure : The elements of cost can be combined to give the following types of cost:
Prime cost =Direct material + Direct labour + direct expenses.
Factory cost =Prime cost + Factory expenses.
Manufacturing cost =Factory cost + Administrative expenses.
Total cost =Manufacturing cost + Selling and distributing expenses.
STANDARD COSTS
In cost accounting actual or recorded costs or standard or predetermined costs are used. The nomenclature actual cost is misleading. Usually average labour rates are used rather then the actual ones and arbitrary allocations are made for use of capital equipment and for general and administrative costs. Also actual costs are compiled long after the job in completed. This approach is chiefly aimed at financial accountability than cost control.
Standard costs are based on the proposition that there is certain amount of material in a part and a given amount of labour goes into the part’s manufacture. In a given period of time costs tend to vary around some average cost per unit or per hour. Through the use of standard costs, guesswork is reduced and a standard that measures performance is established. Each part and assembly has a standard cost card on which is recorded the standard material, labour, and overhead costs, and the total cost.
The system of standard costs consists of two parts :(1) a base standard and (2) a current standard. The base standard is determined infrequently, e.g., once a year, and the current standard represents the later cost. The difference between the two is the cost variance.
ESTIMATING LABOUR COSTS
All direct and in direct costs excluding labour costs are determined by the accounts department of the plant. Process planners are mostly concerned with labour costs which are directly related to the process of manufacturing. However, the total time required by workers to perform an operation may be divided into following classes :
The time to perform an operation also includes time for personal needs, time to change and re-sharpen tools, etc. which are taken to be about 20 per cent of the sum of all other times. Besides, there are inspection or checking times which vary from instrument to instrument.
Each operation on a particular type of machine tool is divided into a number of small elements. These elements can be standardized, measured and then recorded. This is mostly done under Time and Motion study . Standard data is also available for various times. Machining times are calculated with the help of formulae for each machining operation which takes into account the feeds, speeds, depth of cut and tool travel plus tool approach.
Machine time : All machining times can be calculated with the basic formula
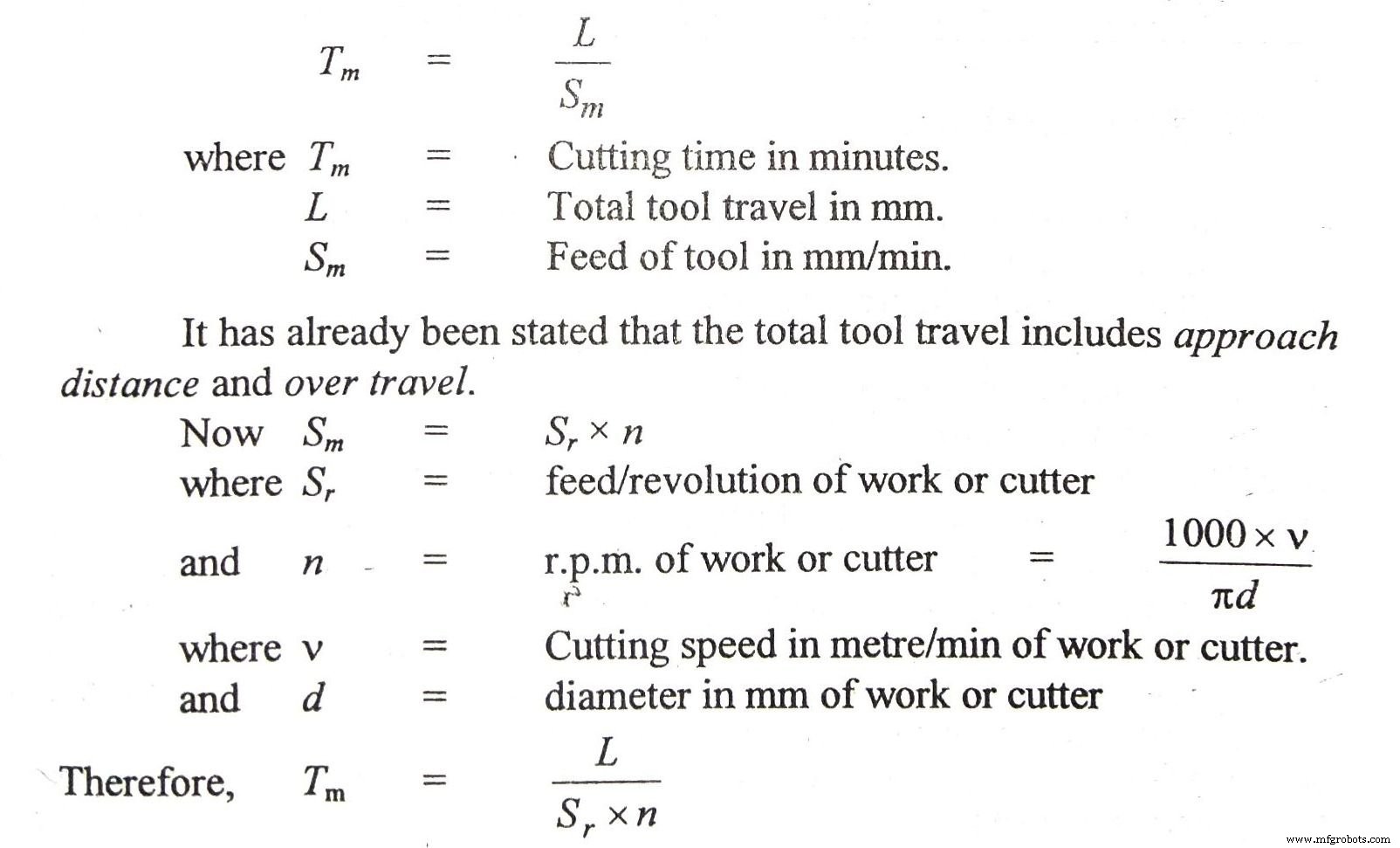
Calculation of machining time for each operation and their feed, speed and depth of cut have been given in each chapter or they may be available in hand books.
Methods of Costing
The method used to develop cost evaluation fall into three categories:methods engineering , cost by analogy , and statistical analysis of historical data .
In the methods engineering approach, that is usually followed, the separate elements of work are identified in great detail and summed into the total cost per part. A typical, but simplified example, is the production of a simple fitting from a steel forging.
Technologie industrielle
- Qu'est-ce que le fraisage ? - Définition, processus et opérations
- Qu'est-ce que le forage ? - Définition, processus et conseils
- Qu'est-ce que la métallurgie des poudres ? - Définition et processus
- Qu'est-ce que le brochage ? - Processus, travail et types
- Qu'est-ce que l'usinage chimique ? - Travail et processus
- Qu'est-ce que l'usinage par ultrasons ? - Travail et processus
- Qu'est-ce que le soudage au gaz ? - Pièces, processus et application
- Qu'est-ce que le rodage ? - Définition, processus et outils
- Qu'est-ce que le forgeage ? - Définition, processus et types