Repenser les systèmes de contrôle pour les pads multi-puits
Les exigences en matière de données et de contrôle entraînent le besoin d'une architecture de contrôle modulaire et évolutive.
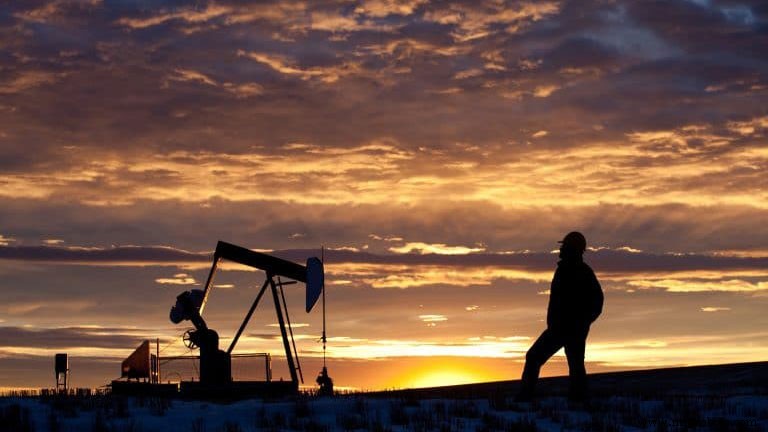
Les progrès du forage ont stimulé l'évolution des opérations pétrolières et gazières, passant de champs simplistes à un seul puits à des champs à plusieurs puits plus complexes.
Aujourd'hui, de nombreux producteurs utilisent des techniques de fracturation hydraulique et de forage latéral pour placer 10 puits ou plus sur une plate-forme. Certains opérateurs poussent même leurs opérations jusqu'à 52 puits sur une seule plate-forme.
Ces progrès ont non seulement augmenté les récupérations de production des puits, mais ont également créé des opportunités de production entièrement nouvelles dans des zones non conventionnelles. Ils ont également permis aux producteurs de pétrole et de gaz de réduire leur empreinte opérationnelle.
Cependant, malgré tous les avantages des tampons multipuits, leur augmentation importante de la taille et de la portée a créé un nouveau défi. La densité plus élevée de plusieurs puits sur une seule plate-forme augmente l'équipement requis sur site et entraîne des exigences de données et de contrôle beaucoup plus importantes.
Les architectures de contrôle traditionnelles qui ont été utilisées pendant des décennies sont poussées à leurs limites et ne peuvent tout simplement plus être durables. Au lieu de cela, des systèmes de contrôle plus avancés sont nécessaires pour gérer les architectures évolutives requises par les plateformes de puits modernes.
En conséquence, les opérateurs et les constructeurs d'équipements qui les soutiennent doivent maintenant modifier, voire changer radicalement, leur approche des systèmes de contrôle pour ces plateformes multipuits.
Évolution de la technologie RTU
Les producteurs de pétrole et de gaz en amont se sont appuyés sur la technologie des unités terminales à distance (RTU) pour le contrôle des sites de puits pendant des décennies. Initialement, le coût de mise en œuvre des RTU et les défis liés à leur programmation limitaient les appareils à une simple acquisition et un contrôle des données.
Au fil du temps, cependant, les RTU ont intégré davantage de fonctionnalités, notamment les E/S, les communications et la programmation CEI-61131. Ces capacités ont permis aux opérateurs pétroliers et gaziers de surveiller davantage de points de données, d'enregistrer l'historique et les alarmes, et d'ajouter des calculs plus complexes dans les RTU. Les constructeurs d'équipements et les sociétés d'ingénierie ont également commencé à développer des applications spécialisées pour les commandes d'élévation artificielle des têtes de puits avec des contrôleurs à microprocesseur propriétaires.
Finalement, pratiquement tous les fabricants d'ascenseurs artificiels ont développé leur propre RTU pour contrôler et optimiser leurs solutions respectives. Les sociétés d'ingénierie ont également développé leurs propres méthodes avec des applications RTU légèrement différentes, tandis que les fabricants d'instruments ont introduit de nouveaux instruments pour mesurer à peu près n'importe quel point de processus requis.
Récemment, cependant, les exigences accrues associées aux opérations multi-puits ont commencé à dépasser les capacités de la technologie RTU.
Appareils poussés à leurs limites
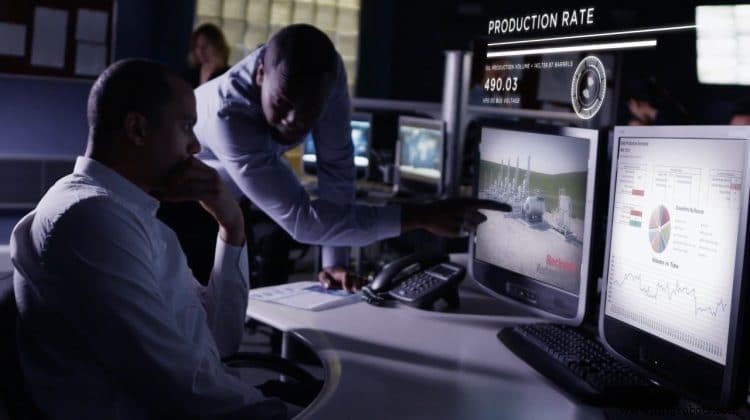
Chaque puits d'une plate-forme multipuits nécessite une élévation artificielle, une mesure du débit, un contrôle de l'équipement et une mesure du niveau. Cela crée plus d'E/S et de demande de contrôle qu'une seule RTU ne peut gérer. Par conséquent, les producteurs de pétrole et de gaz sont obligés d'acheter des RTU supplémentaires et de répartir le contrôle des applications et des sites sur plusieurs unités.
Les producteurs de pétrole et de gaz ont réussi à implémenter plusieurs contrôleurs RTU sur une plate-forme de puits, mais ils rencontrent des problèmes courants avec ces architectures. Certains de ces problèmes incluent :
- Gestion des modifications de plusieurs configurations ou programmes à chaque plateforme de puits.
- Gestion de la communication des nombreuses RTU sur site (par exemple, communications peer-to-peer).
- Communications SCADA vers le matériel de plusieurs fournisseurs
- Exécution non fiable des programmes personnalisés dans les RTU.
La demande ultime sur les dispositifs RTU survient lorsqu'un contrôle de pad multi-puits beaucoup plus important est nécessaire. Cela peut inclure une opération avec 10 ou même plusieurs dizaines de puits sur une seule plate-forme de puits. La densité plus élevée de puits sur une plate-forme augmente également l'équipement requis sur place. Par exemple, bon nombre de ces plateformes de puits ont leur propre séparateur.
Il devient également plus économique d'installer des unités de compression de pipeline, des unités de récupération de vapeur (VRU) et des tours VRU en raison du taux élevé de gaz naturel produit à partir de la plate-forme. Des unités de transfert commercial automatique (LACT), des machines de transfert d'eau et d'injection de produits chimiques sont également couramment observées sur ces plates-formes de puits.
De plus, de nombreux producteurs de pétrole et de gaz investissent dans des bâtiments électriques appelés maisons électriques. Ces bâtiments abritent la distribution électrique principale, les centres de commande de moteurs (MCC), les commutateurs de réseau et les alimentations sans interruption (UPS), et ils sont souvent contrôlés sur le plan environnemental.
Toutes ces augmentations (équipements, instrumentation de terrain et applications) ne font qu'aggraver les problèmes courants des architectures RTU.
Ils créent également de nouveaux défis en matière de service et d'assistance. L'utilisation de plusieurs RTU a conduit à de multiples configurations d'application et programmes pour les maintenir. Cela oblige également les opérateurs pétroliers et gaziers à travailler avec plusieurs fournisseurs.
De plus, avoir plusieurs appareils de plusieurs fournisseurs nécessite également que les travailleurs aient plus de formation et d'expérience pour les prendre en charge. Alors que certains producteurs disposent d'un personnel complet avec suffisamment de personnel qualifié pour gérer l'entretien des systèmes de contrôle des puits, beaucoup ne le sont pas. Ces producteurs doivent s'appuyer sur l'assistance du fabricant ou sur l'assistance technique sous contrat pour entretenir leurs systèmes de contrôle.
Passer à des systèmes de contrôle modulaires et évolutifs
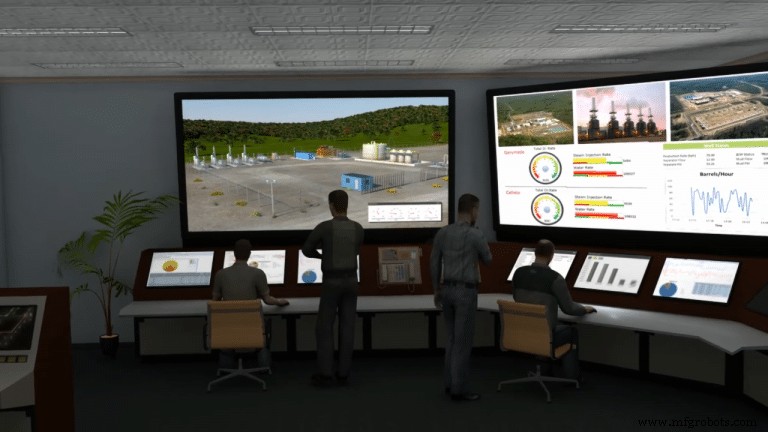
Les RTU ont rempli leur rôle pendant des décennies en gérant des exigences de contrôle simples, une interaction simple entre les appareils de terrain et des communications simples. Mais ils ne suffisent plus dans les environnements d'exploitation plus complexes d'aujourd'hui.
De nombreux producteurs de pétrole et de gaz qui ont rencontré des problèmes courants de RTU ont trouvé une solution alternative viable sous la forme d'un contrôleur logique programmable (PLC) modulaire et évolutif. La technologie PLC a été affinée pendant des années dans des environnements de contrôle de processus industriels qui sont tout aussi robustes que la production de pétrole et de gaz en amont.
Les automates offrent un certain nombre d'avantages par rapport aux RTU :
- Modularité : Certaines RTU prennent en charge le matériel modulaire. Mais équilibrer les exigences du module avec les exigences de l'application et du contrôle dans une RTU est beaucoup plus difficile que dans un API. De plus, les modules tiers pour les RTU ne sont généralement pas disponibles car les RTU ne sont pas des architectures ouvertes, contrairement aux API.
Une grande variété de modules sont disponibles pour les API qui permettent de surveiller et de contrôler une grande variété de instruments de terrain. La prise en charge de la communication pour de nombreux types de réseaux différents est également prise en charge via une configuration modulaire. - Évolutivité : Ceci est important lorsque l'on considère comment un tampon multi-puits est assemblé. Un seul puits sera souvent installé sur un site à plusieurs puits, et ce n'est que des mois, voire des années plus tard, que des puits et des équipements supplémentaires seront mis en ligne.
Dans ces cas, les constructeurs d'équipements veulent être en mesure de construire des patins d'équipement hors site, puis de les brancher et de les configurer simplement sur la plate-forme de puits. Ils veulent réduire le besoin de tranchées, de tirage de câbles, de terminaisons de câbles, d'installation de panneaux et d'instruments sur le terrain pour aider à réduire les coûts. L'évolutivité de la programmation et du matériel est requise dans ce cas, et c'est exactement ce qu'offre la technologie PLC. - Facilité de programmation : Historiquement, les API étaient considérés comme une toile vierge pour l'automatisation et le contrôle. Seules les firmes d'ingénierie ou les programmeurs expérimentés savaient comment repartir de zéro et développer le contrôle requis dans un automate.
Cependant, les automates modernes disposent de bibliothèques de code pré-développé et documenté qui peuvent être ajoutés rapidement dans un processus presque mode glisser-déposer. Certains fournisseurs d'API ont également des bibliothèques pétrolières et gazières en amont pré-développées qui peuvent être configurées sur site. Les producteurs de pétrole et de gaz n'ont besoin que d'activer et de configurer les données requises à partir de l'IHM pour démarrer un automate ou pour ajouter du matériel de skid dans un système existant.
Cela peut éliminer le besoin de quelqu'un comme un puits technicien spécialisé pour connaître l'environnement de programmation et écrire un nouveau code lors de l'ajout de matériel.
De plus, les modifications de programme et de configuration peuvent être effectuées en ligne dans un automate sans arrêter le processus. Les RTU ne peuvent traditionnellement pas accepter de telles modifications sans être mises hors ligne et téléchargées. Il s'agit d'un différenciateur essentiel dans un environnement moderne de plateforme multipuits, car l'arrêt du système de contrôle entraîne une perte de production. - Fonctionnalité d'E/S à distance : Les RTU n'ont traditionnellement pas de fonctionnalité native d'E/S distantes, contrairement aux API. Cela peut réduire les coûts d'installation. De plus, lorsque des skids d'équipement sont ajoutés à un site, ils peuvent être livrés avec des E/S et des instruments prémontés et câblés. Le démarrage de ces skids est aussi simple que de brancher un câble Ethernet dans un commutateur et de configurer les E/S dans le contrôleur.
Améliorer la gestion du cycle de vie
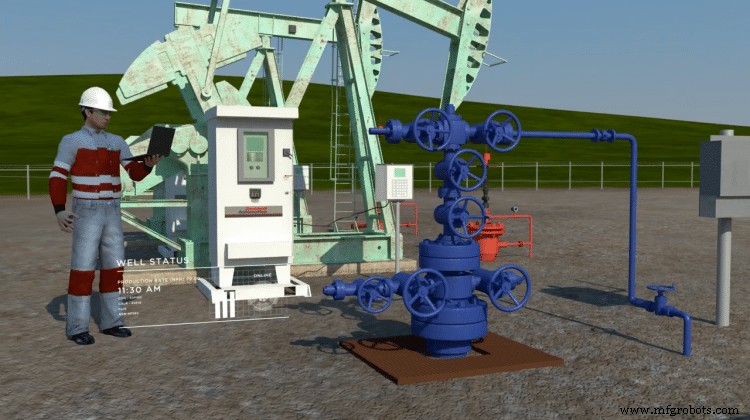
La gestion du cycle de vie des pads de puits peut être un casse-tête majeur pour les équipes d'exploitation. Les puits peuvent passer par de nombreux états d'écoulement différents, y compris l'écoulement naturel, la pompe submersible électronique (ESP) ou la pompe à cavité progressive (PCP) et la pompe à tige de pompage. Et le type de flux et le cycle de vie peuvent varier considérablement.
Plusieurs RTU sont souvent utilisés uniquement pour contrôler les différents cycles de vie du puits. Changer la RTU signifie changer les pilotes de communication vers le système SCADA, car la RTU physique au niveau du puits est du matériel d'un nouveau fournisseur. Et la configuration de la RTU pour contrôler l'application et l'installation de ce matériel sur le système est souvent un processus fastidieux.
Une plate-forme de puits basée sur PLC peut apporter un soulagement significatif dans ce domaine, offrant des avantages d'efficacité et d'optimisation que les opérateurs n'auraient peut-être jamais cru possibles.
En utilisant les architectures matérielles d'E/S modulaires et évolutives offertes par un API, les opérateurs peuvent installer des modules d'E/S là où se trouve l'instrumentation et envoyer ces données à l'API. Et quelle que soit l'approche de conception d'E / S utilisée par un producteur de pétrole ou de gaz, le matériel du système de contrôle restera constant, les communications avec le système SCADA utiliseront les mêmes pilotes et le système restera en ligne et contrôlera toutes les applications comme des mises à jour sont faites. Pendant tout ce temps, il ne reste qu'un seul programme d'automate à maintenir.
Il y a aussi la question du support des applications du fournisseur. Comme déjà mentionné, de nombreux fournisseurs créent leurs propres applications pour une variété de besoins de production en amont, et chaque fournisseur utilise généralement un type de RTU différent. Par conséquent, les fournisseurs ne peuvent généralement prendre en charge que quelques applications spécifiques, pas toutes.
La prise en charge des fournisseurs de PLC sur les conceptions de pads multipuits augmente chaque jour. Cela inclut la prise en charge des applications de contrôle d'équipement, de levage artificiel et de mesure de débit. L'automatisation de l'équipement est facilement gérée grâce à des environnements de programmation riches et à une grande variété de modules d'E/S et de communication. La mesure du débit est également prise en charge avec la mesure du débit conforme à l'AGA et à l'API, la prise en charge de l'étalonnage et les rapports de transfert de garde vers les systèmes SCADA. Les applications de portance artificielle, bien qu'elles ne soient pas aussi répandues dans les automates programmables, sont également développées rapidement pour prendre en charge tous les types de portance artificielle.
Enfin, de nombreux producteurs de pétrole et de gaz ont exprimé leur frustration à l'idée que les applications RTU soient une « boîte noire ». Cela signifie que le système est conçu avec des entrées spécifiques destinées à contrôler uniquement des sorties spécifiques.
Une approche de boîte noire empêche la flexibilité car elle ne permet pas aux producteurs de pétrole et de gaz de modifier le fonctionnement du système. Par conséquent, ils doivent soit changer de fournisseur pour répondre à leurs besoins, soit simplement vivre avec la technologie dont ils disposent, sachant qu'elle ne fonctionne pas aussi efficacement qu'ils le souhaitent.
Un système basé sur PLC, en revanche, peut être modifié sur le terrain avec des outils industriels courants (IEC-61131), offrant une flexibilité beaucoup plus grande.
Adopter la nouvelle normalité
Le PLC a longtemps été considéré comme une solution plus adaptée aux installations de fabrication qu'au contrôle des plates-formes de puits. Mais les plateformes de puits modernes d'aujourd'hui sont essentiellement de petites usines. Ils ont des bâtiments, des services publics ou des générateurs à environnement contrôlé, et des exigences de données et de contrôle beaucoup plus importantes.
Cela en fait une solution idéale pour un API. Un système de contrôle de pad multipuits qui utilise les capacités modulaires et évolutives d'un API peut réduire les coûts et les temps d'installation, améliorer la disponibilité de la production et faciliter la gestion du cycle de vie.
Zack Munk est responsable du développement des activités pétrolières et gazières onshore en amont pour Rockwell Automation.
Système de contrôle d'automatisation
- Construire des systèmes de fabrication flexibles pour l'industrie 4.0
- ASM Assembly Systems utilise le robot Sawyer de Rethink Robotics pour les contrôles de qualité
- Considérations pour les panneaux de commande AFD
- Avantages des technologies embarquées pour la conception modulaire
- Solutions simples pour les anciens systèmes d'automatisation
- Les entreprises fixent des délais pour les systèmes intelligents
- Top 10 des flux de travail pour les fabricants
- Systèmes locaux vs globaux pour le contrôle de la production
- Avantages de l'utilisation de VIA dans les pads