Systèmes de palettes linéaires :une voie directe vers la rentabilité ?
Un logiciel amélioré donne un coup de pouce majeur aux systèmes de palettes linéaires
Adam Hansel, directeur des systèmes et des ventes, DMG Mori (Hoffman Estates, IL) le résume parfaitement :« Allez dans n'importe quel magasin. Demandez-leur s'ils veulent automatiser. La réponse est oui. 100 %." Mais quel type d'automatisation ? Et quelles machines et processus ? Pour une grande variété d'entreprises, la réponse logique est un système de palette linéaire qui intègre plusieurs machines de découpe de métal, et éventuellement des opérations supplémentaires. D'un autre côté, "logique" ne signifie pas toujours "facile" ou "sans souci".
Ne confondez pas FMS avec les systèmes de pool de palettes
Un système de palette linéaire de base, également connu sous le nom de système de fabrication flexible (FMS), automatise le chargement et le déchargement d'un ou plusieurs centres d'usinage avec des pièces à partir d'un emplacement de stockage central. Les pièces se déplacent sur un rail droit, portées par un véhicule avec des axes de mouvement supplémentaires qui lui permettent de déplacer le travail dans une machine et sur sa table et de le ressortir une fois terminé. Les opérateurs configurent les travaux sur une station centrale, et non sur les machines individuelles, et un ordinateur central contrôle la distribution et l'exécution du travail.
Dans la configuration la plus courante, les pièces sont boulonnées sur des fixations, qui sont à leur tour boulonnées sur des palettes uniformes. Cela maximise la flexibilité du système puisque n'importe quel travail peut être envoyé à n'importe quelle machine à tout moment tant que la machine est configurée pour cette palette standard. Une autre caractéristique clé des systèmes de palettes linéaires est la possibilité de les étendre après leur installation initiale pour inclure des machines-outils supplémentaires, plus de stockage et même des opérations non usinées comme l'inspection. Certains systèmes ont 10 centres d'usinage ou plus et des dizaines d'étagères à palettes empilées sur trois niveaux.
Ainsi, un système de palette linéaire diffère d'un système de pool de palettes, ce dernier pouvant être considéré comme une "extension non intelligente de la machine", comme Bob Baldizzi, spécialiste des systèmes et des grandes machines, Doosan Machine Tools America, (Pine Brook, NJ) a expliqué. « Dans un système de pool de palettes, un logiciel supplémentaire sur la machine elle-même exécute le système. Vous êtes généralement limité à indiquer au logiciel quel programme est associé à quelle palette dans le pool et la séquence dans laquelle vous souhaitez que ces palettes passent par la machine. C'est ça. Il n'y a pas de calendrier de production. Pas de gestion des données. Aucun rapport. Il s'agit simplement d'une plus grande extension du système de palettes à la machine. » Les systèmes de pool de palettes sont généralement des arrangements circulaires, bien qu'ils puissent être linéaires, ce qui ajoute à une confusion possible.
"Les systèmes de pool de palettes que j'ai vus ont généralement la même pièce sur les cinq ou six palettes", a déclaré David Suica, président de Fastems LLC (West Chester, OH). « Si vous voulez changer des pièces, vous devez généralement changer l'outillage à l'intérieur de la machine, le programme de pièces et tous les décalages nécessaires pour chaque pièce. Les pools de palettes conviennent pour une série de la même pièce. Mais si vous voulez fabriquer exactement ce dont vous avez besoin dans les quantités que vous pouvez vendre, un système de palettes linéaires est généralement une meilleure solution. »
Utilisation de la broche supérieure à 90 %
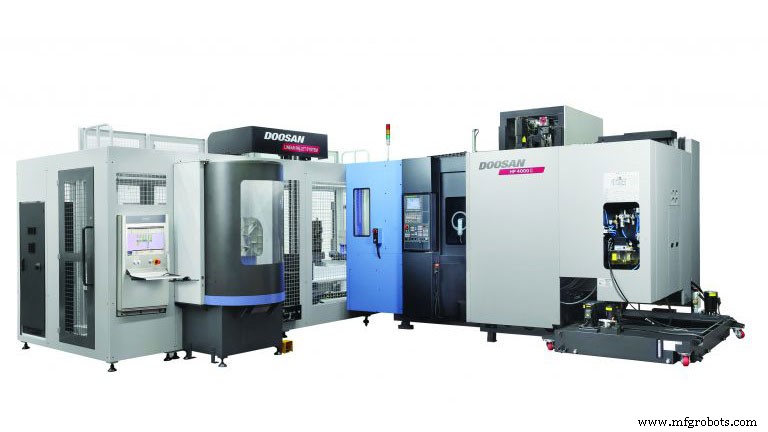
Les situations diffèrent, mais il semble qu'aucun atelier d'usinage n'atteigne plus de 50 à 60 % d'utilisation de la broche sans FMS, tandis que quiconque en utilise un correctement verra des taux de 90 % ou plus. Et dans certains cas, la disparité est encore plus grande. Hansel a déclaré que "l'utilisation de la broche est probablement de 30 % ou moins dans la plupart des cas s'ils ont un mélange de machines alimentées manuellement. Il est tout simplement impossible d'effectuer des changements de pièces, des changements de fixations et de planifier efficacement de nombreuses ressources sur un presse-papiers. » Comme l'a expliqué Suica, « la plupart des temps d'arrêt d'une machine sont causés par des humains… qui attendent un outil… qui découvrent le programme… qui poinçonnent manuellement les décalages d'outils. Une fois cette heure de configuration passée, vous ne la récupérez jamais pour la production. »
Cela indique l'amélioration la plus importante et la plus significative des systèmes de palettes linéaires au cours des dernières années :le logiciel. À un degré ou à un autre, tous les fournisseurs de FMS proposent un logiciel de planification de la capacité qui permet de maximiser le débit du système. Hansel a décrit un scénario typique :« Supposons que vous ayez plusieurs machines, 180 outils dans chaque magasin, 24 montages et certains travaux qui doivent sortir pour respecter vos contrats. Vous définissez des paramètres tels que la priorité des travaux et les numéros dont vous avez besoin à certains moments. Ou disons que vous construisez une voiture. Vous ne produirez pas deux essieux et trois roues. Vous auriez besoin de quatre roues. Ainsi, vous pouvez dire au logiciel de produire des tailles de lot. Dans les deux cas, le logiciel calcule automatiquement comment utiliser correctement vos ressources pour obtenir la production dont vous avez besoin. Si vous planifiez correctement et préparez les appareils et l'outillage, puis laissez le logiciel faire le travail pour vous, un taux d'exécution de 90 à 95 % est tout à fait réalisable.
Bon ajustement pour les ateliers d'emploi… et plus encore
A qui profite un FMS ? Toute personne, d'un petit atelier à une entreprise fabriquant 100 000 pièces ou plus, dans certaines situations. John Einberger, responsable de la gamme de produits, Makino Inc. (Mason, OH) a déclaré :« Le point idéal pour cette technologie est quelqu'un qui a une variété de produits à exécuter, dans un ordre quelque peu aléatoire, avec des cycles de production relativement courts. En effectuant la mise au travail hors du centre d'usinage, vous augmentez l'utilisation de la broche.
"Mais il existe également des applications pour des volumes de production plus élevés parmi les personnes qui ont une production saisonnière", a-t-il poursuivi. "Par exemple, disons qu'ils fabriquent 80 000 de quelque chose par an, mais ils ne le font que pendant trois mois, puis ils exécutent une variante ou quelque chose de différent pendant les quatre mois suivants. L'industrie du groupe motopropulseur des véhicules récréatifs correspond à ce type de schéma de production. Pendant la saison morte, ils fabriquent ce dont ils ont besoin pendant la saison, comme des moteurs de bateau lorsque les motoneiges se vendent et des moteurs de motoneige lorsque les bateaux se vendent. Notre FMS a été un outil très utile pour les clients dans ces situations de volume élevé. »
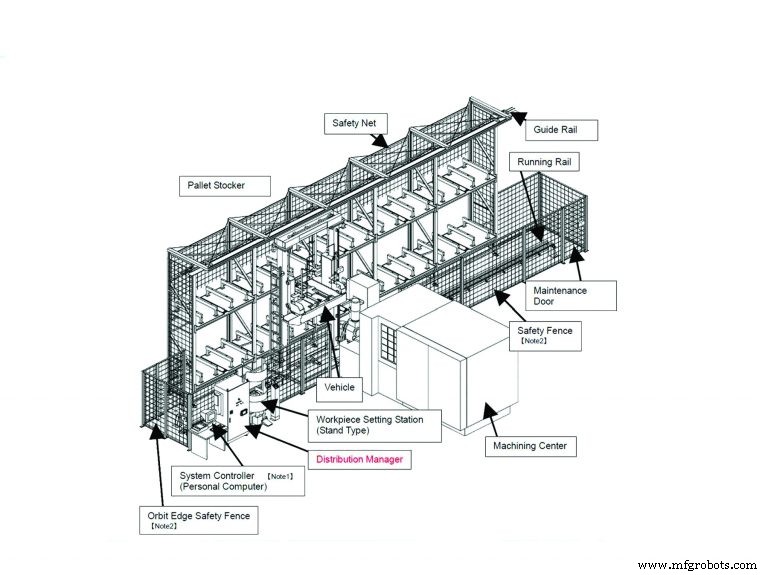
Hansel a ajouté qu '«il est assez courant pour les personnes qui n'utilisent que cinq ou six numéros de pièces différents de les placer sur un système de palettes linéaires. C'est parce que vous avez beaucoup de redondance dans un tel système. Les horizontales ont généralement de grands magasins d'outils qui vous permettent de mettre des outils redondants dans le magasin pour effectuer des quarts de travail plus longs. Si l'outil se casse ou s'use, vous pouvez simplement passer au suivant. D'un autre côté, les gens de Liebherr (Saline, MI) ont souligné que les cellules de manutention de palettes sont les plus rentables lorsque le temps de cycle pour toutes les pièces d'une palette donnée totalise plus de cinq minutes. Sinon, vous perdriez du temps à attendre que le véhicule change de palette.
Pour vous donner une idée de la popularité de ces systèmes, Einberger a déclaré que Makino a installé 575 de ses systèmes de palettes linéaires au cours des 20 dernières années en Amérique du Nord seulement.
Pas seulement pour les horizontaux
Traditionnellement, les systèmes de palettes linéaires connectaient généralement des centres d'usinage horizontaux, car « une machine horizontale est presque toujours livrée avec un changeur de palettes », explique Baldizzi de Doosan. « Vous avez toujours une deuxième palette dans une zone de poste de chargement que l'opérateur utilise, dans un environnement autonome, pour charger et décharger les pièces pendant que la machine est en marche. C'est un avantage dans un FMS car la grue peut charger et décharger de la zone du poste de chargement sans interrompre le cycle d'usinage. Un centre d'usinage vertical typique n'a pas cela, pas plus que la plupart des machines à cinq axes, bien que des fabricants comme Doosan équipent désormais les machines à cinq axes de changeurs de palettes pouvant être connectés à un FMS. »
En plus de mélanger les types de centres d'usinage, il est également possible d'intégrer d'autres fonctions dans un FMS. Vous pouvez également intégrer des machines de différents constructeurs, mais dans ce cas, il serait peut-être préférable de travailler avec une société d'automatisation « agnostique » comme Fastems :« Nous pouvons avoir une machine de marque X pour une opération d'ébauche, une machine de marque Y pour une tolérance serrée. application, un Zoller avec des corrections d'outils automatiques écrivant sur une puce, une MMT, une station de lavage et un système d'ébavurage, tous entièrement intégrés », a déclaré Suica. "Notre logiciel gèrerait même automatiquement les décalages d'outils et les données d'inspection."
Certaines de ces options nécessitent un robot dans une ou plusieurs stations, ou le remplacement du véhicule FMS traditionnel par un robot sur rails. Einberger a déclaré que Makino propose ce dernier hybride « en réponse à certaines exigences, principalement dans le domaine des structures aérospatiales. Certains de ces clients souhaitent charger automatiquement des pièces dans une machine à l'aide d'un robot sur rail, car ils veulent avoir l'avantage de pouvoir commencer par charger la pièce sur une surface plane, puis prendre le sous-fixation et le charger dans un centre d'usinage horizontal.
"Cette approche est également très avantageuse sur les pièces multi-opérations où la première opération peut être une opération à quatre axes et la seconde une opération à cinq axes dans le même centre d'usinage", a-t-il poursuivi. "Ainsi, la palette un sur le centre d'usinage serait une pierre tombale à quatre axes qui accepte la pièce sur une sous-plaque, tandis que la deuxième palette sur le même centre d'usinage serait sur une table de cinquième axe qui accepte la même pièce sur la même sous-plaque pour une opération ultérieure sur cinq axes. Les systèmes de robot sur rail comblent l'écart entre un FMS de manutention de palettes et un robot de manutention de pièces discrètes. »
D'autre part, Baldizzi a averti que l'obtention d'un type de flexibilité vous fait perdre un autre. "Nous commençons à voir la demande d'adaptation à différentes palettes, comme effectuer certaines fonctions à l'horizontale et d'autres sur une machine à cinq axes avec des capacités de rotation, nécessitant une palette différente. Le plus est que vous pouvez mettre toutes ces machines dont vous avez besoin pour effectuer l'opération sur le FMS. L'inconvénient est que vous perdez une partie de la flexibilité du FMS car le logiciel doit s'assurer que cette palette ne va que sur cette machine particulière à ce moment précis. Alors que si vous avez plusieurs machines sur un FMS qui sont toutes identiques, le travail qui est boulonné sur une palette peut aller n'importe où, n'importe quand, n'importe comment."
Coûts et défis
Selon Einberger, le coût d'un FMS initial comprenant le système ferroviaire, le véhicule, la station de travail et les supports de stockage de palettes représente environ les deux tiers du coût d'un centre d'usinage donné, à l'exclusion des montages. Donc, étant donné la promesse de doubler votre débit, c'est une bonne récompense. Mais Hansel a déclaré que "bien que les gens aiment vraiment l'idée d'avoir beaucoup de palettes, ils sous-estiment parfois le coût de l'installation. Ainsi, lorsqu'ils prennent une décision sur les machines à acheter, le coût réel de l'équipement n'est parfois pas inclus, ce qui peut les empêcher d'utiliser pleinement le système. Par exemple, vous bénéficiez d'un fonctionnement sans éclairage ou de l'élimination d'un troisième quart de travail uniquement si vous pouvez charger suffisamment de travail pour faire fonctionner la machine pendant huit heures ou plus. »
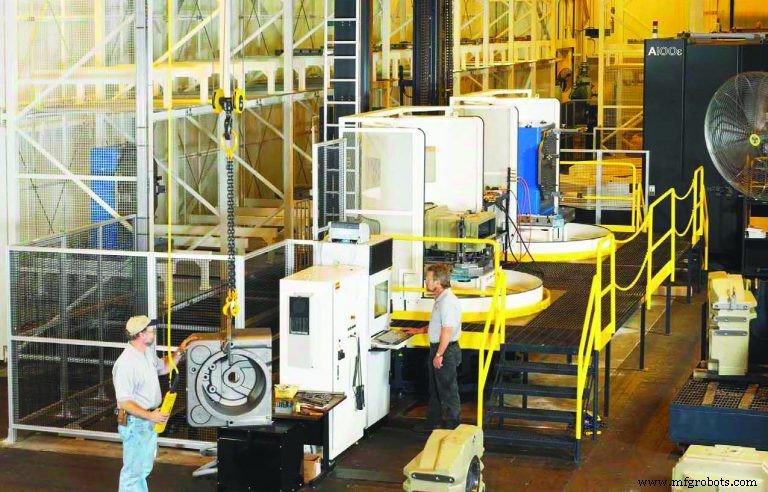
Cependant, tout le monde s'accorde à dire que le plus grand défi avec un FMS est opérationnel. Comme le dit Suica :"C'est la même chose que pour votre PC :les ordures entrantes équivaut à la sortie des ordures. Si vous avez de bons programmes, les décalages d'outils sont connus; si vous avez votre emploi du temps, cela fonctionne très bien. La chose la plus importante pour la plupart des entreprises est la discipline requise pour s'assurer qu'elles sont prêtes. Ce n'est pas différent de la discipline que chaque entreprise met dans son service comptable. Vous faites correspondre les factures, assurez-vous qu'elles sont correctes, assurez-vous de payer la taxe. Ce n'est pas facile, mais c'est aligné exactement et terminé. Vous pouvez faire la même chose dans l'atelier de fabrication et l'intégrer, et vous pouvez supprimer l'élément humain à l'origine de l'erreur. »
Suica a également averti que "la plupart des palettes linéaires et des systèmes robotiques ont tendance à être des îlots d'automatisation. Ils savent ce qu'ils savent et ils ne sont connectés à rien d'autre au sein de votre exploitation. Vous pouvez avoir un progiciel ERP [planification des ressources d'entreprise] qui suit vos commandes, l'apport de matières premières, etc. Vous avez dépensé beaucoup d'argent en outils, en déterminant les décalages d'outils et en systèmes de mesure. Mais le flux d'informations entre tous ces systèmes finit toujours par être manuel. Ce relatif manque d'intégration empêche les entreprises de réaliser d'importantes économies de main-d'œuvre.
Suica a déclaré qu'il n'est pas rare d'avoir huit ou neuf machines en cours d'exécution avec seulement quelques personnes si vous intégrez pleinement ces systèmes. «Nous travaillons actuellement sur un système qui compte huit machines qui seront gérées par trois personnes, dont l'une fait juste une vérification parce qu'elle ne voulait pas automatiser cela. Il fonctionnera en deux équipes, il y aura donc six personnes sur cette ligne, alors qu'il y en a maintenant 14. Mais vous avez besoin d'un niveau élevé d'intégration des systèmes pour le faire, sinon vous avez toujours besoin d'un groupe de personnes pour dire à l'automatisation quoi faire. L'intégration et le logiciel sont essentiels. Il en va de même pour la formation et l'assistance, c'est pourquoi DMG Mori, Makino et d'autres disposent d'équipes et d'installations dédiées à l'automatisation.
Le logiciel ne résout pas tout, cependant. Baldizzi a souligné que la fiabilité mécanique est absolument primordiale :« Si vous raccordez une machine, ou plus important encore plusieurs machines, à un FMS et qu'il tombe en panne, l'utilisation de la broche de ces machines tombe à zéro. N'oubliez pas que l'endroit où l'opérateur se tenait pour charger le centre d'usinage horizontal est désormais inclus dans le FMS. Les boutons poussoirs ont disparu. Il y a très peu de chances que vous puissiez charger et décharger manuellement et efficacement les pièces de cette machine. Alors regardez sous le capot pour vous assurer que le FMS est mécaniquement capable de fournir ce temps de disponibilité de 90 %."
Pour les constructeurs de haute qualité, cela inclut de faire passer l'alimentation haute tension triphasée à travers une barre omnibus au-dessus du véhicule, comme le troisième rail d'un métro, sans pièces mobiles autres que le point de contact. « Les systèmes moins robustes attachent le véhicule à une série de câbles dans un chemin de câbles qui suit le véhicule lors de ses allers-retours. Cela provoque des points de fatigue car les câbles se plient continuellement », a déclaré Baldizzi. "Deuxièmement, nous utilisons des yeux optiques enfermés dans un tunnel pour les communications de données qui doivent se produire entre les servovariateurs, les moteurs, la commande, etc., éliminant ainsi le besoin de ces câbles.
"Je vérifierais également si le FMS dispose de canaux, de conduits et de tuyauteries de liquide de refroidissement pour m'assurer que tout liquide de refroidissement qui reste sur les palettes une fois qu'elles sont stockées est récupéré et renvoyé soit dans les réservoirs de liquide de refroidissement de la machine, soit dans un référentiel central, plutôt que de faire un gâchis sur votre sol », a conclu Baldizzi.
Système de contrôle d'automatisation
- Machine à coudre
- Infineon lance un capteur Hall linéaire intégré monolithiquement pour les systèmes ASIL D
- Timken acquiert le fabricant de solutions d'automatisation Intelligent Machine Solutions
- ZF dévoile le nouveau cockpit "SHI"
- Comment fonctionnent les systèmes SCADA ?
- Systèmes embarqués et intégration de systèmes
- Possibilités d'efficacité énergétique dans les systèmes de pompage
- Les changeurs de palettes acceptent des volumes élevés, des tolérances serrées
- Approches pratiques de l'automatisation