Meilleur contrôle qualité avec les pièces imprimées en 3D
Les gabarits et les montages bien conçus permettent des processus de fabrication efficaces et allégés, mais l'investissement en ingénierie requis pour les produire peut être limité aux opérations aux ressources limitées. Ici, nous vous montrons comment Markforged utilise nos imprimantes Mark Two pour améliorer nos processus de contrôle qualité en développant de meilleurs outils de fabrication avec des pièces imprimées en 3D.
Derrière chaque imprimante Markforged se trouve l'assurance que chaque sous-système a été rigoureusement vérifié par notre équipe de contrôle qualité pour la cohérence et le respect de nos spécifications d'ingénierie de précision. Les tests de qualité de chaque système de chaque imprimante ont cependant un coût :chaque étape d'inspection augmente le temps de fabrication total d'une imprimante, et un temps de processus d'impression plus long réduit notre capacité à répondre rapidement aux changements imprévisibles de la demande. En tant que petite entreprise en croissance rapide, l'agilité de fabrication est primordiale pour répondre aux besoins de notre clientèle croissante. En conséquence, Markforged doit être intelligent sur la façon dont nous validons les sous-systèmes dans la fabrication, en termes à la fois de temps investi dans le processus d'inspection réel, ainsi que de temps d'ingénierie requis pour le développer. Pour cette raison, nous imprimons souvent en 3D nos gabarits et montages de fabrication, car l'imprimante Mark Two nous permet de prototyper, tester et déployer rapidement des améliorations de processus pour une utilisation efficace de notre temps d'ingénierie et de fabrication.
Un exemple particulier de l'itération rapide que nos imprimantes nous permettent d'obtenir est un gabarit d'étalonnage de précharge d'extrudeuse en nylon que nous utilisons dans notre fabrication. L'extrudeuse est l'un des éléments fondamentaux de l'impression 3D Fused Filament Fabrication (FFF). Pour une explication rapide et détaillée du fonctionnement d'une extrudeuse, consultez ce guide bien fait du blog de RepRap Squad.
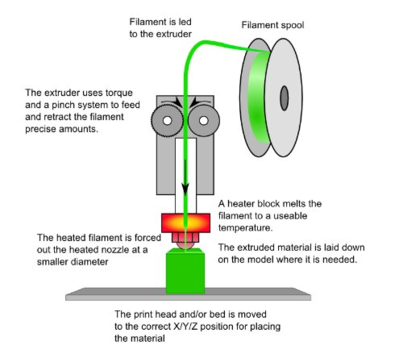
Pour garantir une qualité d'impression constante sur toutes les imprimantes, toutes nos extrudeuses de nylon sont vérifiées pour s'assurer que le « système de pincement » mentionné dans l'image ci-dessus applique une force au filament de nylon qui correspond à nos spécifications de tolérance technique. Cette force est générée à l'intérieur de l'extrudeuse par une paire de ressorts, dont la précharge, ou niveau de compression initiale, peut être ajustée afin de modifier la force exercée par l'extrudeuse. Initialement, le processus de calibrage de cette extrudeuse a été effectué vers la fin de l'assemblage de l'imprimante à l'aide d'un gabarit conçu par Phillip, l'un de nos ingénieurs mécaniciens spécialisé dans l'instrumentation des machines, et assemblé à partir de pièces que nous avons découpées au jet d'eau et usinées à l'extérieur avec un assez long, délai de deux semaines. Alors que le gabarit a produit des résultats extrêmement précis, il a fallu beaucoup de temps pour recevoir et assembler ses composants, nous avons constaté que nous devions modifier la conception lorsque les pièces sont arrivées, et avons finalement dû passer plus de temps à les retravailler sur notre propre fraiseuse CNC en interne. Du point de vue de la fabrication, nous avons également découvert au fil du temps que presque toutes les extrudeuses que nous recevions de notre fournisseur nécessitaient un ajustement. Depuis le in situ le gabarit de mesure était plus difficile à localiser avec précision sur l'extrudeuse installée que si l'extrudeuse était retirée de l'imprimante assemblée, ce qui rajoutait au temps de fabrication de notre imprimante, nous avons décidé de développer un appareil capable de mesurer rapidement un lot d'extrudeuses tel que reçu de notre fabricant, alors qu'il était encore facile d'accéder aux vis de réglage.
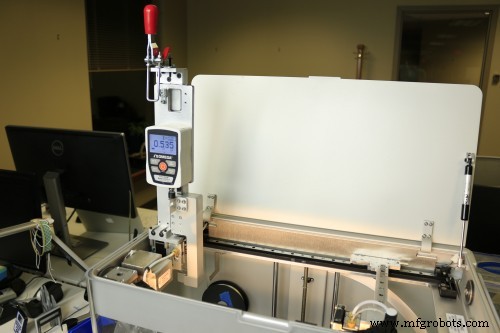
Nous avions quelques exigences de conception en tête lorsque nous avons développé le nouveau luminaire. La première consistait à produire rapidement, ex situ — hors de l'imprimante — appareil de validation qu'un opérateur pourrait utiliser pour calibrer des lots d'extrudeuses à la fois. La seconde consistait à incorporer une conception poka-yoke, de sorte que l'extrudeuse s'insère dans son support de réceptacle d'une seule et unique manière, empêchant l'opérateur de calibrer incorrectement l'extrudeuse par accident. Enfin, l'encombrement devait être assez compact - idéalement dans une enveloppe d'encombrement de 12 "x 12", car il vivrait dans notre usine de fabrication et ne pourrait pas prendre trop de place sur la paillasse.
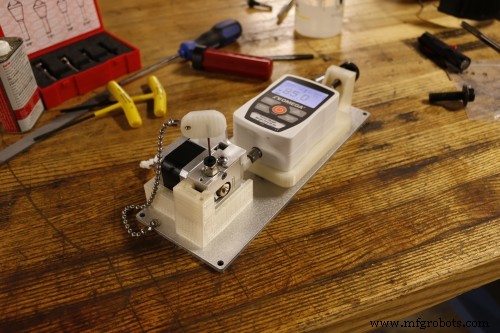
Bennett, un autre de nos ingénieurs mécaniciens (dont vous vous souvenez peut-être de notre article sur les charnières vivantes et les éléments de flexion) a produit le gabarit d'étalonnage final que vous pouvez voir ici. L'ensemble du système est basé sur un dynamomètre Omega (un de la série DFG35 pour être exact). L'extrudeuse de nylon est insérée dans son réceptacle à gauche du gabarit dans l'image ci-dessous, avec la roue libre à ressort flottante qui ajoute de la force au système pointant vers la sonde de mesure de la jauge. L'ensemble dynamomètre est fixé sur un rail linéaire qui lui permet de coulisser librement le long de l'axe de déplacement de la roue folle flottante. Enfin, une vis à oreilles à tête flottante est vissée dans un insert en laiton fondu de telle sorte que sa rotation enfoncera le dynamomètre dans l'ensemble de renvoi à ressort sans appliquer de couple sur le dynamomètre.
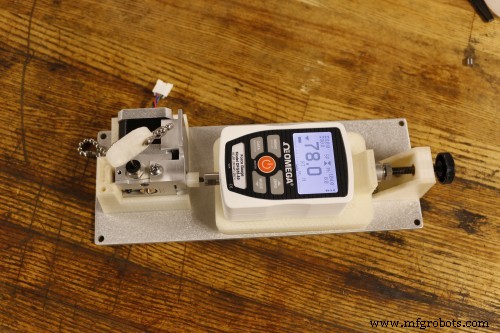
Bennett a ajouté un certain nombre de fonctionnalités à ce gabarit qui sont uniques à la fois à l'impression 3D et à la fabrication de pièces de force industrielle avec une imprimante Markforged. Comme vous pouvez le voir dans l'image ci-dessous, il a utilisé une technique de placement de fibres que nous appelons « rayage de fibres » pour ajouter quelques couches de fibres toutes les 20 à 40 couches d'impression, produisant une pièce extrêmement solide tout en restant en termes de coût et de matériau. efficace. De plus, le réceptacle de l'extrudeuse a été produit rapidement et à moindre coût en tant que pièce unique, avec une géométrie qui aurait nécessité un usinage CNC coûteux avec plusieurs configurations de machine.
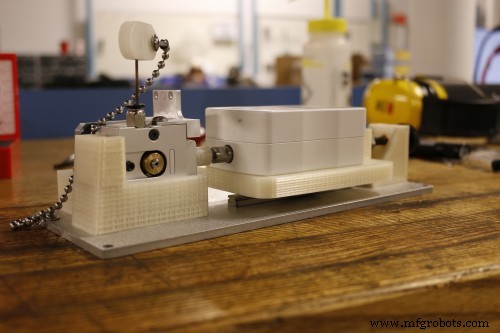
Le produit final vit maintenant dans notre usine de fabrication, où il nous a permis de réorganiser nos processus de contrôle qualité pour une utilisation plus efficace du temps de nos techniciens de fabrication, ce qui nous permet de mettre plus d'imprimantes Mark Two entre les mains de nos clients.
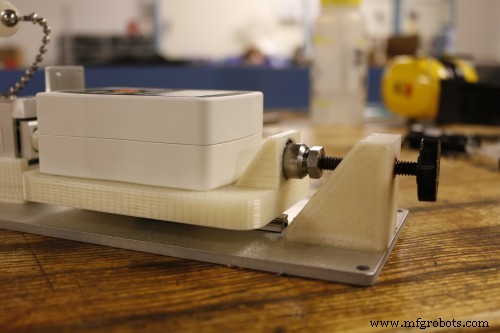
impression en 3D
- Finir des pièces imprimées en 3D avec… des crayons ?
- Impression du fusible 1 avec le fusible 1
- Moulage par injection avec des moules imprimés en 3D :téléchargez notre nouvelle étude technique
- Amélioration du contrôle qualité avec le cycle de Deming
- Drones extrêmes imprimés en 3D
- GÖPEL améliore le contrôle qualité dans la fabrication automobile avec Universal Robots
- Automatisation du contrôle qualité à l'aide de la technologie
- Qu'est-ce que le contrôle qualité ?
- Le plan d'échantillonnage en contrôle qualité