Conception pour la fabrication additive d'accessoires et d'outillage
Voici pourquoi la conception pour la fabrication additive n'a toujours pas été adoptée par la majorité des entreprises. La conception traditionnelle des luminaires est motivée par les capacités et les limites des machines sur lesquelles nous les fabriquons. Les fabricants utiliseront le plus souvent des CNC à 3 axes ou des machines-outils manuelles pour créer des équipements d'atelier.
Afin d'être à la fois rentables et rapides, ces luminaires ont tendance à rester très volumineux. En effet, les fabricants souhaitent limiter le temps passé sur les équipements de production et consacrer plus de temps à la fabrication des produits des clients. Cela conduit les entreprises à considérer la production d'accessoires comme une activité sans valeur ajoutée, malgré leur importance dans la production de produits finaux.
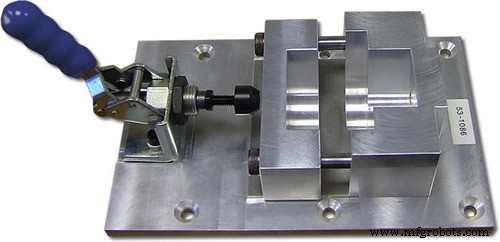
Les problèmes que ces fabricants finissent par nous signaler sont leur temps machine (c'est-à-dire le délai d'exécution partiel) et le manque de ressources en main-d'œuvre disponibles. Les délais de livraison des pièces dans un atelier d'usinage sont souvent calculés en semaines, et lorsque vous obtenez enfin du temps machine, vous finissez par perturber ou retarder autre chose. Une fois que vous avez la machine, vous aurez soit besoin d'un machiniste pour écrire le code, soit manuellement pour faire le travail vous-même. Vous avez donc besoin d'un opérateur qualifié capable de faire le travail.
Bien que nous fabriquions généralement des pièces complexes avec des géométries organiques, nous nous retrouvons souvent avec la conception de montage « blocs sur une plaque ». Cependant, cela a du sens. Nous voulons limiter le temps que nous prenons sur nos machines et notre matériel de stock se présente généralement sous forme de barres carrées, de tubes ou de feuilles. Ce statu quo nous laisse avec de longs délais de livraison, de gros appareils encombrants qui doivent être stockés autour de nos installations et un rapport coût/pièce élevé si l'on considère le coût de la main-d'œuvre et du temps machine.
L'additif "Quick Fix"
En réponse à ces défis, de nombreux fabricants ont adopté la solution additive « quick fix ». Ils se sont tournés vers la fabrication additive pour tenter de relever les défis internes en matière de temps et de ressources.
Sans avoir à apporter de modifications à la conception, l'imprimante propose immédiatement une soupape de décharge sur la file d'attente de l'atelier d'usinage et tourne les pièces plus rapidement, sans surveillance de jour comme de nuit. Il permet une production de luminaires moins chère, ne nécessitant aucun travail manuel tout en utilisant une variété de matériaux pour répondre aux exigences des pièces. Dans de nombreux cas, il offre également une amélioration ergonomique instantanée par rapport à un homologue en métal solide.
Ainsi, lorsque nous vérifions avec les utilisateurs de fabrication de FDM, nous voyons beaucoup de ces conceptions.
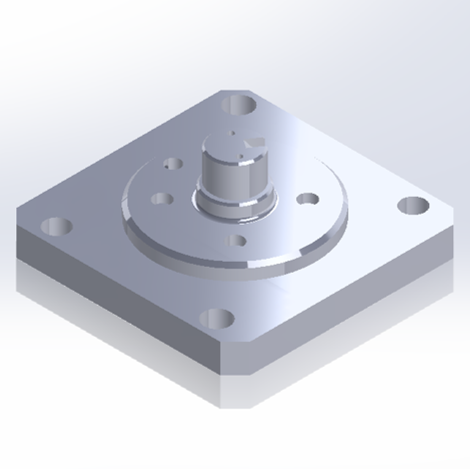
Ceci est un exemple d'un de nos clients. Ils fabriquent 12 de ces luminaires chaque année en aluminium. Leur boutique est toujours occupée, ils finissent donc par sous-traiter leur production. Avec leurs méthodes actuelles, un appareil leur coûte plus de 3 000 $ et prend 4 à 6 semaines pour se procurer. Ce scénario n'est que trop courant lorsque nous discutons avec les entreprises manufacturières.
Comparez cela avec un luminaire imprimé en 3D ABS solide. Le coût serait de 190 $ et la production prendrait environ 19 heures, soit un peu moins d'une journée.
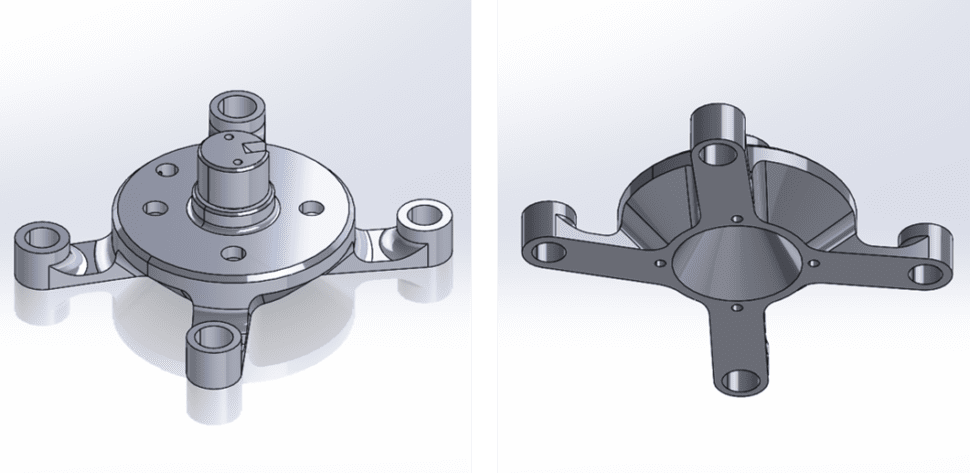
Lorsque nous appliquons la conception pour les principes additifs, nous pouvons aller plus loin dans ces améliorations. En utilisant la conception vue ci-dessus, nous pouvons à nouveau réduire le coût à 76 $ et le temps d'impression à 11 heures. Cela représente un coût de 60 % et un gain de temps de 42 % par rapport à l'impression du design traditionnel.
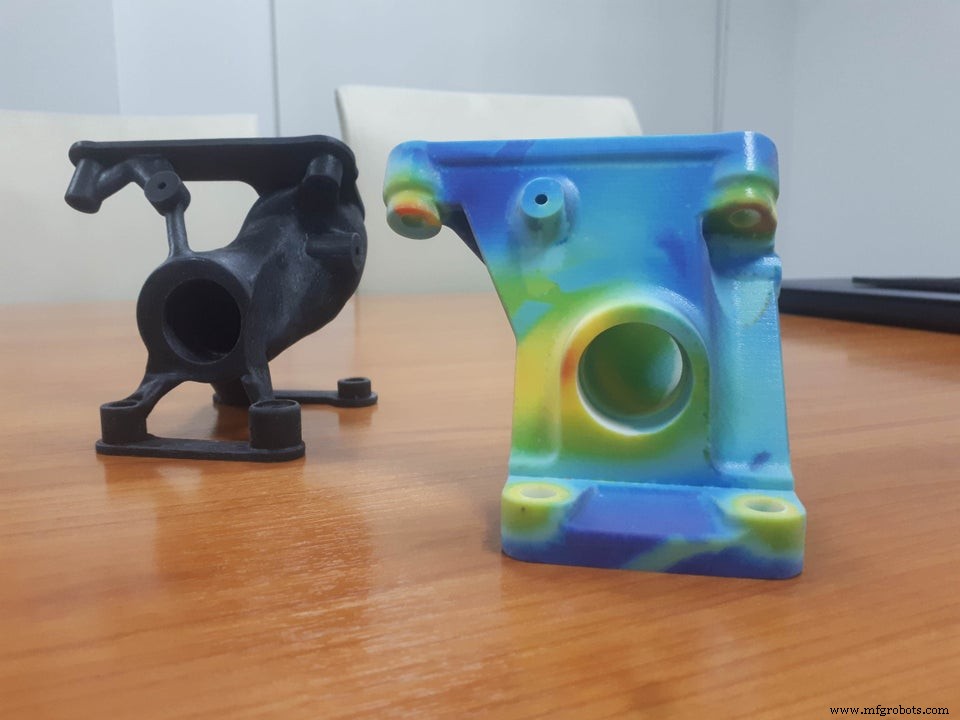
Erreurs courantes lors de la conception pour la fabrication additive
Avant d'entrer dans les meilleures pratiques de conception, je voulais passer en revue quelques malentendus sur la conception pour l'additif et mettre en évidence 2 erreurs courantes que les gens commettent.
L'expression « conception pour additif » est un terme extrêmement large. Vous pouvez le considérer comme un niveau inférieur à un terme comme « conception pour la fabrication ». Parfois, les gens seront confus lorsqu'ils nous poseront des questions sur la conception pour l'additif et nous demanderons :« Qu'essayez-vous de faire ? » et "Quelle machine utilisez-vous ?"
Cela est important car chaque type d'imprimante 3D a son propre ensemble de bonnes pratiques. Il existe maintenant des dizaines de types d'imprimantes 3D, des noms comme FDM, SLA, Polyjet, Binder Jet, DMLS, etc. Chacune a des variations au sein de cette sous-famille. Tout comme un moulin et un tour ont des principes de conception différents, chaque système d'additifs aura un ensemble unique de règles.
Beaucoup de gens supposent également que la fabrication additive résout tous leurs problèmes sans aucun inconvénient. Bien que l'additif soit extrêmement polyvalent et ait eu un impact énorme sur la fabrication, ce n'est pas la solution miracle qu'il peut être. Un exemple de ceci pourrait être des composants que vous pouvez facilement vous procurer à bas prix. Nous avons reçu des demandes pour imprimer des pièces que vous pouvez acheter en ligne pour quelques centimes, comme des boulons, des vis et autres. Nous devons comprendre et évaluer quelles applications nécessitent l'impression 3D, et quand les composants produits en série sont une meilleure option.
Erreurs courantes
Les deux erreurs les plus courantes que nous constatons lors de la conception pour la fabrication additive sont le décorticage et le creusement des pièces imprimées en 3D FDM. Je ne fais pas référence à un remplissage inexistant ou extrêmement clairsemé, je veux plutôt parler de la modélisation dans des cavités creuses dans la géométrie de la pièce dans le but d'économiser de l'argent sur les coûts des matériaux.
Presque à chaque fois, cela a le contraire de l'effet escompté. Les imprimantes FDM nécessitent un support pour les surplombs. Lorsque les concepteurs de pièces creuses ou coques, ils créent souvent de très grands surplombs qui doivent être remplis de matériaux de support. Parfois, les pièces évidées peuvent avoir un matériau de support impossible à retirer une fois l'impression terminée !
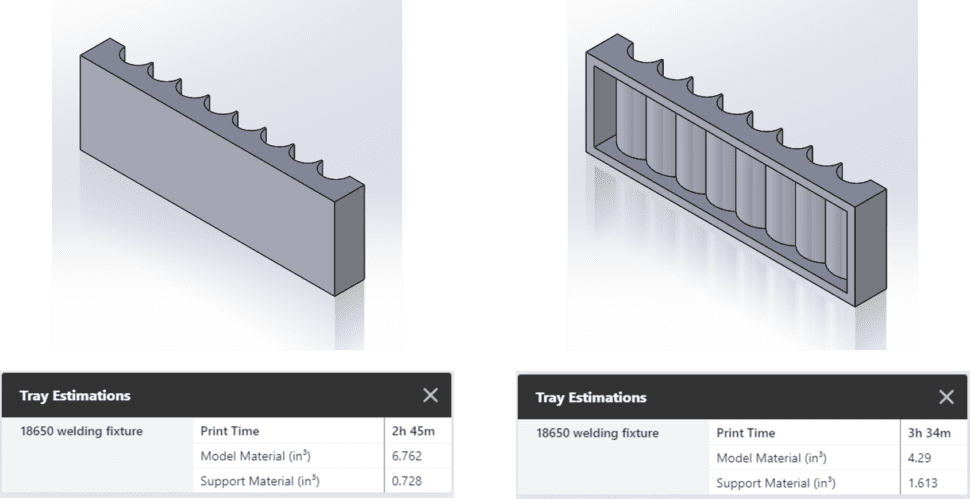
Dans cet exemple de bombardement, nous avons une légère réduction de l'utilisation globale des matériaux, mais notre temps de construction a augmenté de près d'une heure. En effet, les systèmes qui basculent entre le modèle et le matériau de support unique doivent constamment basculer chaque couche entre les deux matériaux.
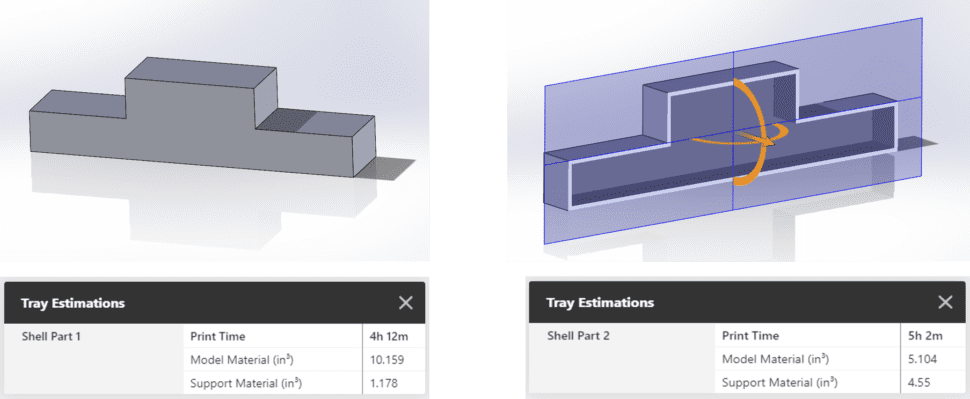
L'évidement nous montre à nouveau une légère diminution de l'utilisation globale du matériau mais une augmentation du temps d'impression. En plus de cela, ce scénario crée des supports piégés qui ne peuvent jamais être retirés de l'impression finale.
6 Conception de règles additives pour FDM
Maintenant que nous comprenons les défis et les malentendus de la conception pour la fabrication additive (DFAM), examinons certaines des règles de conception les plus simples et les plus courantes que vous pouvez utiliser avec votre imprimante FDM.
1. Angles autoportants
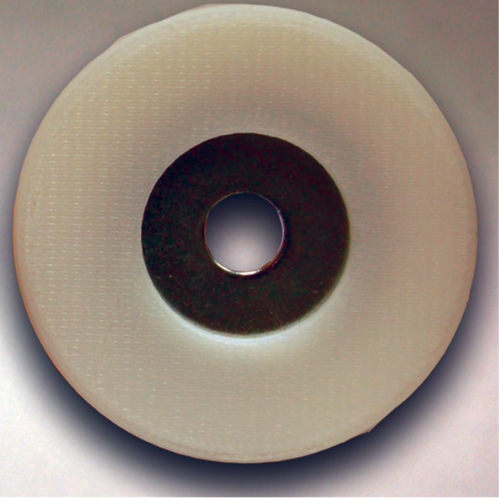
Parfois appelée règle des 45 degrés, cette règle stipule que les pièces FDM n'ont pas besoin de supports tant que les surplombs sont inférieurs à 45 degrés par rapport à la verticale. Il s'agit de l'une des modifications de conception les plus rapides et les plus simples que vous puissiez apporter aux pièces existantes. Cela réduira l'utilisation du matériel de support et réduira les temps d'impression. Une note importante à cette règle est que tous les matériaux n'utilisent pas 45 degrés comme seuil. Cela variera selon le type de matériau, tombant généralement entre 40 degrés et 60 degrés.
2. Élimination du matériel des fonctionnalités encombrantes
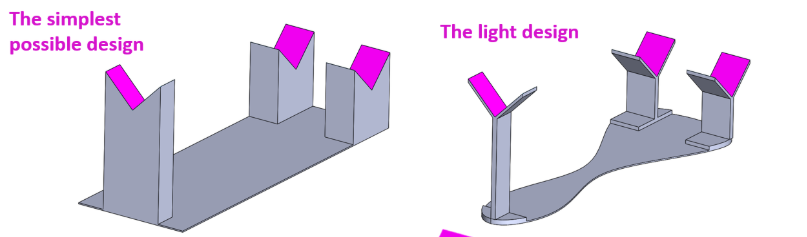
L'élimination du matériau des éléments volumineux est généralement ce que recherchent les ingénieurs lorsqu'ils conçoivent des coques ou des pièces creuses. Il est vrai que vous pouvez réduire considérablement l'utilisation de matériel lors de l'impression 3D, mais nous devons être attentifs à la façon dont nous le faisons.
L'une des astuces que vous pouvez utiliser lorsque vous essayez d'éliminer de la matière est de vous concentrer sur les surfaces de contact. Commencez par concevoir des points de contact, comme le rose vu ci-dessus, où la pièce interagira avec le luminaire. À partir de ce point, votre conception peut être basée sur l'objectif final de la pièce, qu'il s'agisse d'ajouter une résistance supplémentaire ou d'alléger généralement.
3. Force sélective par visages
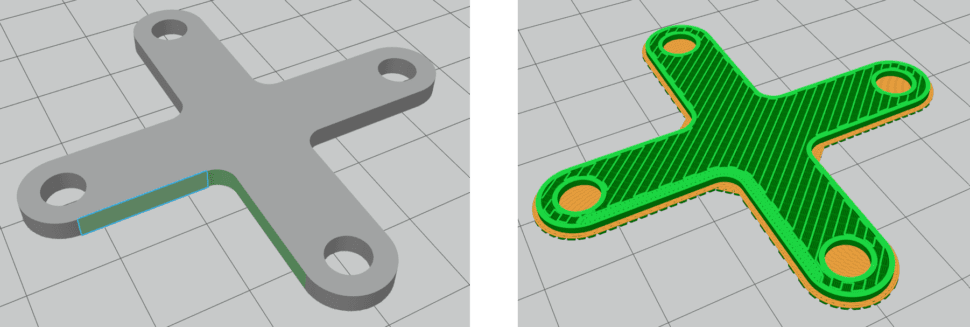
La résistance sélective par face est un autre outil utilisé pour concevoir des pièces légères tout en maintenant l'intégrité structurelle. GrabCAD Print permet aux utilisateurs d'importer une géométrie CAO native ; des choses comme les visages et les corps peuvent être référencées dans le programme. Nous pouvons sélectionner des corps et des faces individuels et spécifier les densités de remplissage et les épaisseurs de paroi. Cela nous permet de ne mettre du matériau que là où nous avons besoin de plus de résistance afin que nous n'ayons pas à imprimer toute la pièce complètement solide.
4. Force sélective par corps
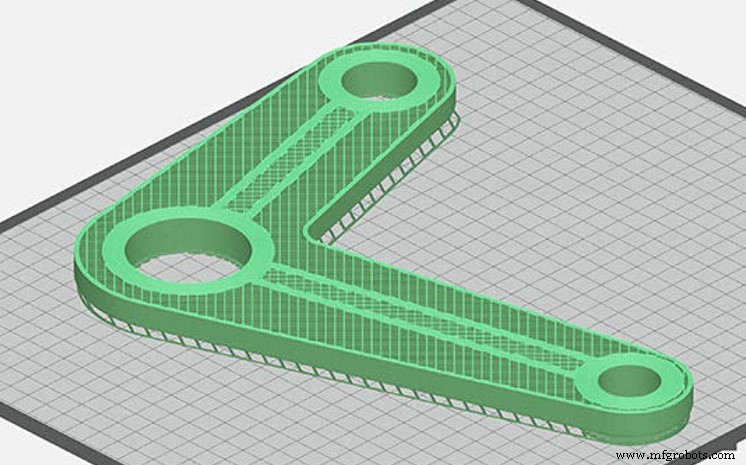
Tout comme la résistance sélective par face, la résistance sélective par corps permet aux utilisateurs de contrôler les niveaux de remplissage entre des corps CAO distincts. Il s'agit d'un exemple simplifié, mais en ajoutant des corps minces dans une pièce, vous pouvez créer des nervures structurelles, garantissant des performances mécaniques tout en conservant une pièce clairsemée et légère.
5. Insert en métal
Les inserts métalliques sont un excellent choix si une zone d'une pièce imprimée en 3D va subir une usure excessive. Au lieu d'avoir constamment à réimprimer toute la pièce, placer un insert métallique comme un écrou, une rondelle ou un insert fileté thermofixé permettra une plus grande durée de vie de la pièce.
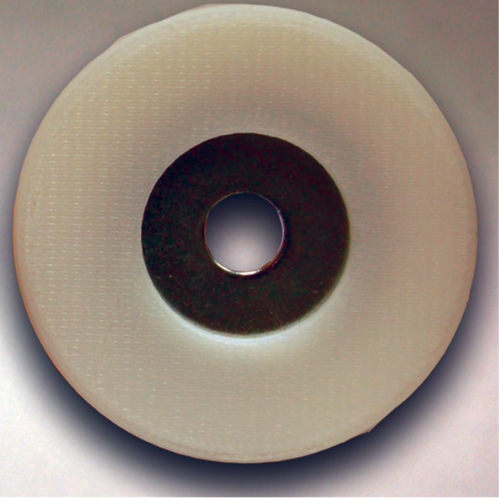
Les inserts intégrés tels que les écrous et les rondelles nécessitent qu'un trou soit modélisé dans la géométrie CAO où ils seront placés. Pour inclure une rondelle ou un écrou dans votre impression, configurez votre imprimante pour qu'elle fasse une pause d'une couche ou deux avant de boucher le trou où l'insert sera placé. Cela vous permet d'aller à l'imprimante, de déposer l'encart et de reprendre l'impression. Si vous imprimez directement sur une surface métallique, nous vous recommandons de vaporiser la surface de contact métallique avec un spray acrylique pour garantir la qualité d'impression.
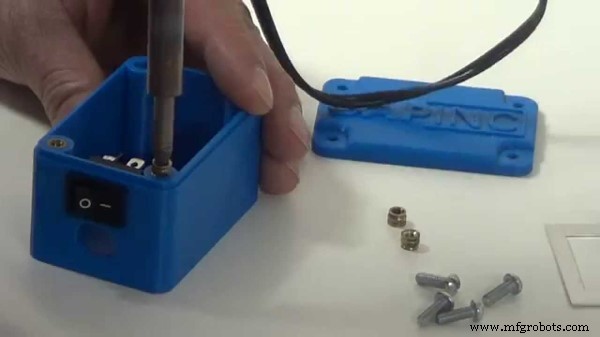
Les inserts thermofixés permettent un enfilage répété auquel le plastique nu ne peut pas résister. Ceux-ci sont placés après l'impression à l'aide d'un fer à souder. Il est important que vous laissiez un peu de matériau extra solide pour que l'insert puisse mordre sur les côtés du trou où il va être placé. Dans GrabCAD Print, vous pouvez spécifier la taille de l'insert que vous prévoyez d'utiliser et le logiciel modifiera automatiquement la taille du trou et fournira du matériau mural supplémentaire.
6. Assemblées consolidées
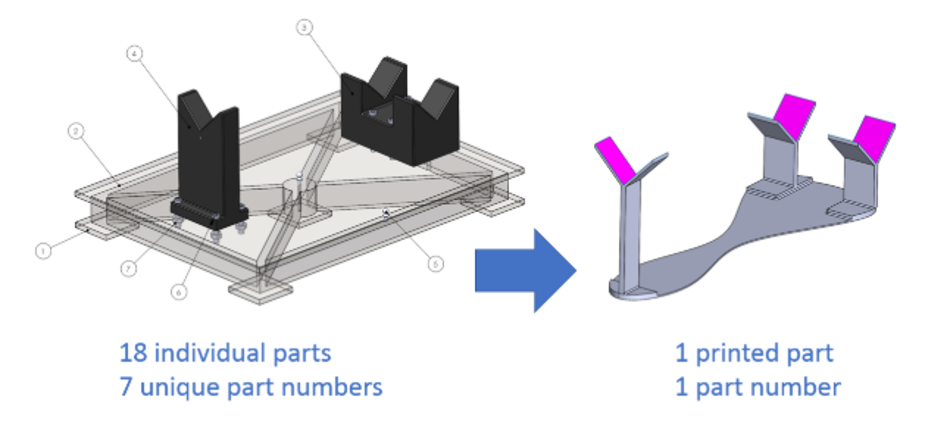
En revenant à l'exemple du montage encombrant, on constate que l'impression de cette pièce réduit le nombre de pièces de 18 à 1 et peut être fabriquée sans aucun assemblage.
Une autre méthode populaire utilisée par ceux qui ont besoin d'appareils plus complexes consiste à utiliser ce qu'on appelle des outils hybrides. Ces outils hybrides intègrent des éléments tels que des attaches métalliques, des circuits hydrauliques, des tuyaux flexibles et d'autres accessoires nécessaires pour des applications plus avancées.
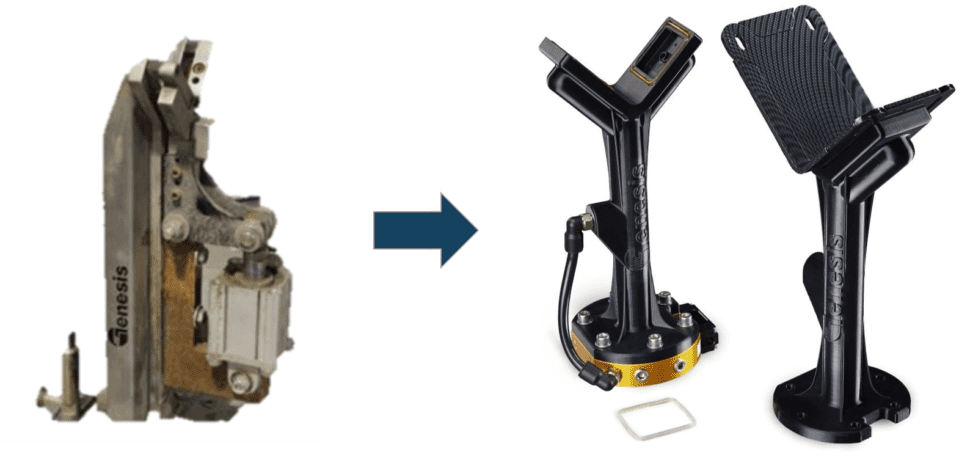
Cet exemple de Genesis Systems montre un outil de bout de bras traditionnel fabriqué à côté d'un outil imprimé en 3D repensé qui incorpore des conduites d'air et des attaches métalliques. Genesis a pu réduire considérablement le poids de l'outil, leur permettant d'utiliser un robot plus rapide, plus petit et moins cher pour cette application.
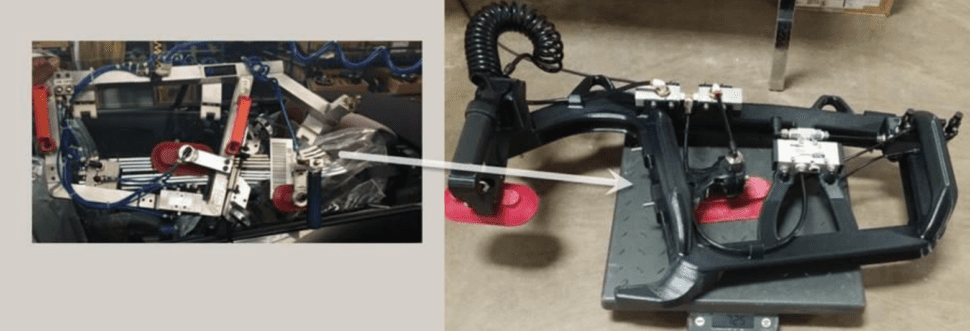
L'exemple suivant vient de Ford. L'outil d'origine sur la gauche est créé en aluminium et est utilisé pour aider les opérateurs à installer des fenêtres sur leurs cabriolets. Ce luminaire était très volumineux malgré sa fabrication en aluminium. Cela endommagerait également la peinture de la voiture s'il n'était pas contrôlé, ce qui entraînerait un retard et un coût supplémentaire. La refonte imprimée en 3D sur la droite incorpore les mêmes conduites d'air et attaches nécessaires tout en utilisant des nervures internes pour le soutien. Le nouveau design imprimé en 3D pèse moins de 7,5 livres.
Conception pour une conclusion additive
Pour conclure, nous avons parlé de :
- Les outils fabriqués de manière traditionnelle et la manière dont nos méthodes de fabrication et nos matières premières déterminent nos choix de conception. Nous avons évoqué la volonté de réduire les délais d'approvisionnement des pièces ainsi que les principales contraintes étant la disponibilité des machines et la main d'œuvre qualifiée.
- Même lorsqu'elles utilisent des conceptions traditionnelles, les entreprises voient toujours des avantages à passer à la fabrication additive. Ces conceptions imprimées directement améliorent généralement les délais, les coûts et l'ergonomie globale en raison de leur légèreté.
- Incompréhensions concernant l'expression "conception pour la fabrication additive", comme le fait que le terme est trop large. Nous avons examiné les erreurs courantes de creusement et de décorticage lors de l'utilisation de la technologie d'impression FDM.
- Enfin, nous avons passé en revue 6 conseils de conception simples que vous pouvez mettre en œuvre sur vos futures conceptions afin de réduire davantage le temps de fabrication, le coût de la pièce et d'améliorer la fonctionnalité globale
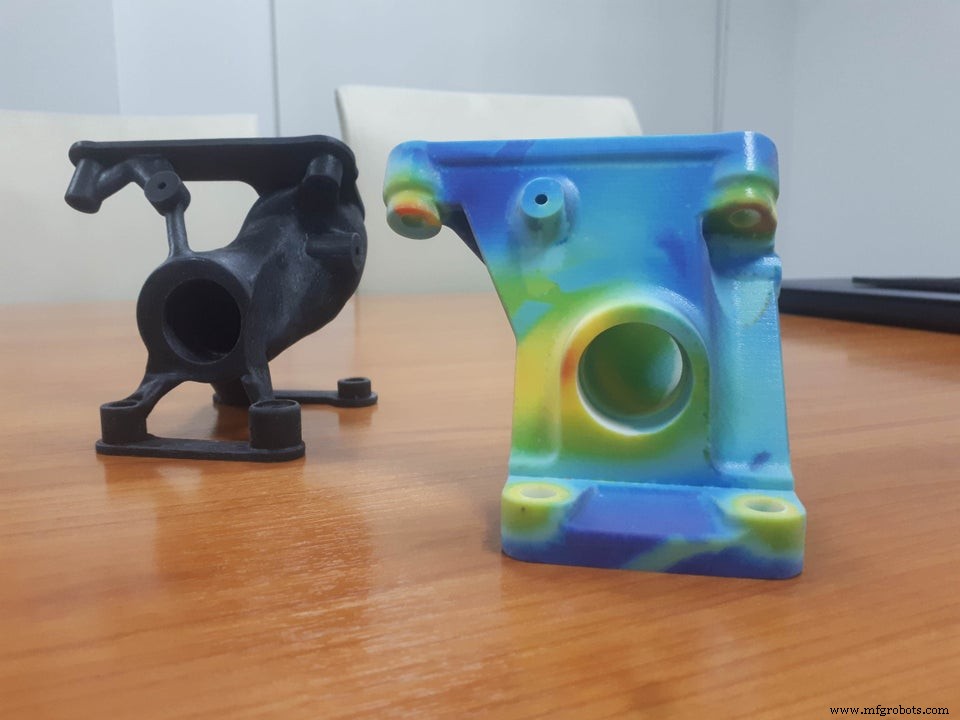
Optimisez vos conceptions pour l'impression 3D
Du concept à la production. CADimensions peut vous aider à chaque étape du processus
Services CADimensionsimpression en 3D
- 4 tendances d'automatisation prometteuses dans la fabrication additive
- Fabrication additive et moulage par injection — une nouvelle vision des cycles de production
- 6 raisons pour lesquelles vous devez envisager la conception pour la fabrication additive
- 4 questions brûlantes pour la fabrication additive en 2019
- Présentation des vendredis AM et du podcast additif
- Essentium et Lehvoss s'associent pour développer des matériaux pour la fabrication additive
- Conception pour la fabrication de PCB
- Fabrication additive en médecine et en dentisterie
- Pourquoi la conception pour la fabrication est-elle importante ?