Entretien d'experts :Wiener Mondesir, cofondateur d'Arevo, sur la production du premier cadre de vélo en fibre de carbone imprimé en 3D au monde
La société Arevo, basée dans la Silicon Valley, a fait la une des journaux en 2018 après avoir dévoilé ce qu'elle a appelé le premier cadre de vélo en fibre de carbone imprimé en 3D au monde. Le cas d'utilisation a présenté les capacités uniques de la technologie d'impression 3D composite exclusive d'Arevo, qui combine la robotique et le logiciel pour produire des pièces composites légères et personnalisées.
Depuis lors, Arevo s'est associé au fabricant de vélos, Franco Bicycles, pour fournir des cadres monocoques en fibre de carbone imprimés en 3D pour une nouvelle marque de vélos électriques.
Cette semaine, nous avons le plaisir de discuter avec Wiener Mondesir, cofondateur et directeur de la technologie d'Arevo, de la technologie exclusive d'Arevo, des avantages de l'impression 3D composite et de ce que l'avenir réserve à la fabrication de composites.
Pouvez-vous nous parler un peu d'Arevo ?
Chez Arevo, notre objectif est de permettre la fabrication de pièces composites à grande échelle. Nous le faisons avec une confluence de robotique, de matériaux et de logiciels.
Lorsque vous examinez l'ensemble de l'industrie des composites, la fabrication de pièces composites représente une très grande opportunité. La fibre de carbone peut être plus résistante que certains métaux et elle est légère, elle a donc un large attrait dans de nombreuses industries.
Mais pour un certain nombre de raisons, l'adoption de la fabrication de composites a été étouffée, donc l'opportunité n'est pas abordée. L'une des raisons à cela est l'inefficacité des processus de fabrication.
La fabrication de composites est actuellement très exigeante en main-d'œuvre, en ressources et en capital, ce qui signifie qu'elle ne s'adapte pas vraiment à de grands volumes. Les industries qui ont vraiment pu capitaliser sur la fabrication de composites sont celles qui pouvaient se permettre l'analyse de rentabilisation, comme l'aérospatiale et l'industrie automobile très haut de gamme.
De plus, les cycles de conception sont longs en raison d'un logiciel inadéquat et d'une simulation inefficace. Une autre raison souvent négligée est le manque de compréhension des composites dans d'autres industries.
Arevo s'attaque à tous ces problèmes. Nous repensons la fabrication des composites en utilisant ce que nous appelons la numérisation des composites.
Nous avons choisi de résoudre ce problème en développant un logiciel qui comble le manque de connaissances.
Vous commencez avec un modèle 3D et notre logiciel effectue l'analyse, propose l'orientation finale optimale, la bonne quantité de matériau et produit des instructions pour fabriquer la pièce en utilisant notre technologie de fabrication.
Prenons l'exemple d'une toile d'araignée. Lorsque vous regardez une toile d'araignée, c'est une structure 3D qui a la bonne quantité de matériau pour son objectif.
La fibre, ou la soie dans le cas de la toile d'araignée, n'utilise que la bonne quantité de matière et est parfaitement placée là où elle doit être. Nous nous en inspirons pour proposer une méthode optimisée d'impression 3D de pièces composites.
Voilà donc notre mission en tant qu'entreprise :permettre la fabrication de composites à grande échelle.
Quels sont les avantages de l'impression 3D composite ?
Les composites en fibre de carbone offrent un excellent rapport résistance/poids, vous obtenez donc un matériau vraiment solide mais léger.
Lorsque vous regardez la tendance de l'impression 3D, de nombreuses techniques différentes utilisent des structures en treillis pour un métal léger, qui est naturellement dense et lourd.
Mais si vous commencez avec un matériau léger et solide comme la fibre de carbone dès le départ, vous obtiendrez le résultat final beaucoup plus rapidement. Ainsi, les composites sont bien mieux adaptés à certaines applications que même les types de produits à structure en treillis métallique, qui ont fière allure mais ne servent pas nécessairement l'objectif.
La complication avec la fibre de carbone est qu'elle est anisotrope, ce qui signifie qu'il est fort dans une direction. C'est ce qui le rend un peu plus difficile à gérer sans outils spécialisés.
Chez Arevo, nous avons développé l'ensemble d'outils pour les concepteurs, vous n'avez donc pas besoin d'avoir un doctorat pour fabriquer avec des composites en fibre de carbone. Notre logiciel s'en charge.
Votre cadre de vélo imprimé en 3D en fibre de carbone a été largement médiatisé lors de son dévoilement. Quel a été le processus de création du cadre du vélo, de la conception à la production ?
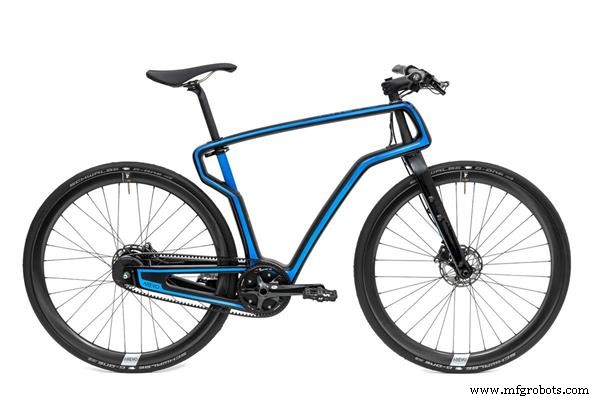
Cette application particulière a commencé comme un moyen de montrer ce qui est possible avec la technologie.
Un cadre de vélo est très accessible, mais il a une forme très complexe et est une grande structure qui nécessite une charge, une torsion et la capacité de prendre du poids. C'était donc l'application parfaite pour démontrer notre technologie.
Si vous prenez du recul et regardez les vélos composites traditionnels d'aujourd'hui, ils passent de la conception au prototypage, puis jusqu'à la production. Ce processus prend près d'un an.
Par ailleurs, les vélos composites traditionnels sont fabriqués selon un processus très manuel. Les cadres sont liés ensemble de 20 à 30 pièces et jusqu'à 40 personnes touchent chaque cadre. C'est un processus très laborieux et vous vous retrouvez avec un produit très coûteux qui n'évolue pas nécessairement.
Les designs sont également très similaires, vous ne pouvez donc pas obtenir beaucoup de personnalisation.
Avec notre technologie, nous avons raccourci ce processus de près d'un an à quelques jours seulement. Le logiciel d'Arevo prend une conception CAO et effectue une conception générative isotrope sur le cadre qu'un concepteur propose. Il optimise également l'orientation et fait une analyse prédictive.
La prochaine étape a lieu dans notre usine de fabrication. Nous avons construit une usine de fabrication en Californie qui peut produire des cadres de vélo personnalisés à la demande en utilisant notre technologie de robotique et de dépôt.
Lorsque nous avons lancé le vélo, nous avons été approchés par tous les grands fabricants de vélos car ils étaient intéressés par la liberté de conception offerte par la technologie.
Lorsque vous regardez le design du cadre de vélo Arevo, il fait en réalité un détour par rapport au design de vélo conventionnel. Il n'a pas de hauban, par exemple, et il est très différent d'un vélo traditionnel.
Le vélo d'Arevo est un vélo monocoque fabriqué avec des fibres de carbone très résistantes orientées dans l'orientation optimale dans l'espace 3D. Nous sommes en mesure de réaliser le design dans une structure monocoque qui le rend très solide et léger.
Nous pouvons régler le trajet réel du vélo à l'aide d'outils logiciels. Nous pouvons régler la rigidité dans certaines régions du vélo et permettre une conduite encore plus dynamique si cela est souhaité, à la demande. Avec les vélos traditionnels, vous essayez essentiellement de toujours refaire le même cadre.
Un cadre imprimé en 3D, en revanche, ouvre un nouveau modèle commercial pour une industrie habituée au très long processus d'introduction d'un nouveau vélo sur le marché. Aujourd'hui, environ un million de cadres composites sont fabriqués chaque année. Et maintenant, vous pouvez réellement introduire des cadres très personnalisés à la demande avec notre technologie.
Notre objectif est de continuer à créer de nouvelles applications qui tirent parti de cette capacité.
L'approche personnalisée de la production est-elle un modèle commercial évolutif ?
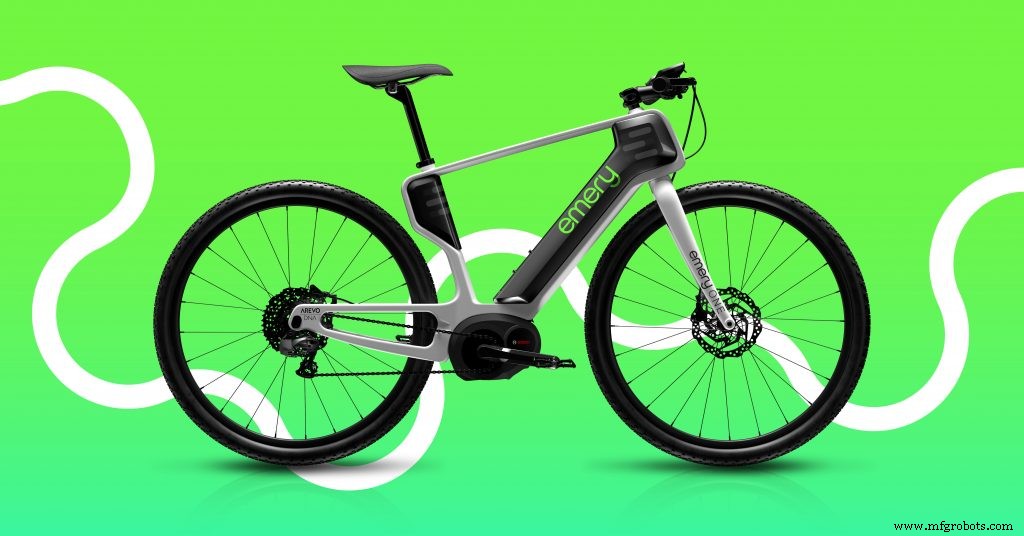
La personnalisation a une grande valeur lorsqu'il s'agit de vélos. Chaque personne est unique. Vous devenez plus fatigué lorsque vous ne conduisez pas un vélo conçu, configuré ou ajusté pour votre cadre. Ainsi, un vélo est en fait un bon véhicule pour démontrer la valeur de la personnalisation.
Il y a toute une tendance autour de la micro-mobilité et de la possibilité de se promener avec un véhicule très pratique. Le vélo représente cela. Dans de nombreux pays, c'est un moyen de transport dominant.
Lorsque vous avez besoin de personnaliser la forme et la fonction, vous ne pouvez pas le faire sur un marché de masse. Mais avec notre technologie, un consommateur peut concevoir le cadre et notre logiciel peut garantir que le cadre qu'il a conçu est structurellement solide.
Ensuite, ils peuvent l'envoyer à nos cellules d'impression 3D pour fabriquer ce vélo à la demande. Ainsi, le processus du concept à la production est très simplifié.
Quelles autres applications envisagez-vous avec votre technologie ?
Aujourd'hui, nous nous concentrons sur les applications de vélo et de mobilité. Ce sont des applications qui peuvent tirer parti de la proposition de valeur que nous proposons, qui est très légère, un rapport résistance/poids élevé et des produits personnalisés.
Lorsque vous examinez les différents secteurs, il est vraiment important d'améliorer les performances. dans le secteur du sport, ainsi que dans les secteurs de l'automobile, de l'énergie et de l'aérospatiale.
Nous avons un tas d'applications différentes sur lesquelles nous travaillons où légères, hautes performances et haute personnalisation sont requises. Et ce sont les domaines clés où notre technologie peut être utilisée.
Comment la robotique s'intègre-t-elle dans votre technologie ?
Lorsque vous examinez l'impression 3D, la plupart des impressions 3D sont basées sur des couches et les couches sont déposées dans les plans X et Y. Lorsque vous regardez les propriétés des pièces fabriquées avec ce processus, elles ont tendance à souffrir dans la direction Z.
Nous utilisons un robot six axes entièrement articulé pour déposer notre fibre de carbone dans les directions X, Y et Z. Nous avons éliminé le problème de force Z qui afflige d'autres technologies basées sur des couches, car nous sommes capables de nous étendre dans la direction Z. C'est l'une des capacités uniques de notre technologie de dépôt. La robotique y joue un grand rôle.
Le deuxième aspect est l'échelle des pièces pouvant être imprimées. Aujourd'hui, la plupart des systèmes sont relégués à une certaine enveloppe de construction, ce qui signifie que vous ne pouvez fabriquer que des pièces d'une certaine taille. Si vous dépassez une certaine taille, la pièce devra être découpée en sous-ensembles pour faire une structure plus grande.
Nos robots offrent une capacité d'enveloppe de construction infinie car nous pouvons placer nos robots sur le portique pour fabriquer des pièces aérospatiales. En même temps, le même robot peut fabriquer un vélo. La portée de nos robots est un volume de quatre mètres de haut. Essentiellement, c'est très évolutif en termes de nous donner cette enveloppe à gros caractères.
Comment décririez-vous l'état actuel du marché de l'impression 3D composite ? À quel point la technologie est-elle avancée ?
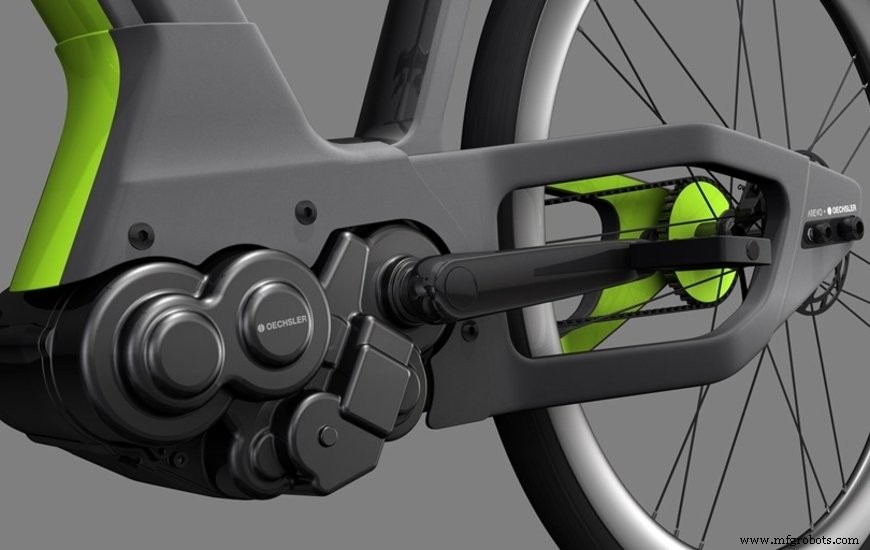
L'industrie des composites pratique l'additif depuis un certain temps. C'est juste que la complexité des géométries a été très limitée à ce que l'on pouvait adapter sur un moule, comme des pièces avec une très petite courbure. De plus, les couches sont généralement posées manuellement, ce qui donne une pièce d'une complexité assez limitée.
L'impression 3D composite existe donc depuis un certain temps. Mais maintenant, des choses comme la robotique automatisée ou les systèmes mécatroniques, qui automatisent le placement de la fibre, permettent des géométries plus complexes.
De nombreuses entreprises adoptent une approche différente pour automatiser la fabrication de composites, allant de différents types de systèmes de résine à différents cas d'utilisation.
Et c'est très utile.
Dans l'ensemble, je pense que le secteur de l'impression 3D composite se porte bien, Arevo en tête.
Quels sont les défis auxquels l'industrie est confrontée, que ce soit l'impression 3D en général ou l'impression 3D composite en particulier ?
Je pense que les plus grands défis découlent du manque d'outils logiciels disponibles pour explorer ce qui est possible avec l'additif. Vous avez l'esprit d'examiner les techniques de fabrication traditionnelles, et nous avons été formés aux techniques de fabrication traditionnelles.
Les gens commencent souvent avec des pièces qui ont été fabriquées de manière traditionnelle et veulent forcer l'ajout d'additifs à cette pièce, mais ça ne correspond pas toujours.
Mais lorsque vous exploitez vraiment ce que vous pouvez faire avec un additif, qu'il soit à base de métal, de composite ou de polymère, en termes d'unicité et de complexité, vous avez vraiment besoin d'outils pour vous guider tout au long de ce processus et informer les concepteurs et ingénieurs.
Comment voyez-vous l'évolution du secteur au cours des cinq prochaines années ?
C'est très encourageant. Depuis la création d'Arevo, nous nous sommes toujours concentrés sur les pièces de production.
Lorsque vous examinez l'ensemble de l'industrie aujourd'hui, il est vraiment encourageant de voir que tout le monde parle de pièces de production. C'est le thème commun.
À l'avenir, je m'attends à ce que l'industrie commence également à parler de qualité et d'évolutivité. Lorsque vous commencez à fabriquer des produits, la production à grande échelle et avec une plus grande répétabilité sera l'objectif principal de l'industrie.
Assurer la qualité des pièces et des processus est actuellement un sujet de discussion important pour la fabrication additive. Quelle est l'approche d'Arevo à ce sujet ?
L'une des percées clés qu'Arevo a pu réaliser est notre procédé de dépôt par laser.
De plus, nous utilisons des algorithmes d'apprentissage automatique capables d'effectuer des inspections in situ. Nous avons une suite de capteurs et nous sommes en mesure de faire une inspection in situ sur une pièce en cours de fabrication.
Cela nous permet d'obtenir un matériau imprimé très homogène avec moins de 1% de vides. Vous pouvez faire une coupe transversale d'une pièce et lorsque vous la présentez au microscope, vous pouvez observer un matériau imprimé très homogène.
Cela se traduit par des pièces de très haute qualité lorsque vous passez à des applications très exigeantes comme l'aérospatiale. Ce contrôle qualité in situ, combiné à notre surveillance en boucle fermée, est ce qui nous permet d'avoir une qualité reproductible et prévisible.
Que réservent les 12 prochains mois à Arevo ?
Au cours des 12 prochains mois, nous nous concentrerons sur l'exécution de la fabrication. Depuis que nous avons lancé le vélo, nous avons en fait plus de demandes que nous ne pouvons répondre. Notre objectif pour l'année prochaine est de continuer à lancer de nouvelles applications, mais principalement d'augmenter notre capacité pour répondre à la demande actuelle.
Pour en savoir plus sur Arevo, visitez : https://arevo.com/
impression en 3D
- Entretien d'experts :Guillaume de Calan, PDG de Nanoe, sur l'avenir de l'impression 3D céramique
- Entretien d'experts :John Kawola, président d'Ultimaker, sur l'avenir de l'impression 3D
- Entretien d'experts :Simon Fried, cofondateur de Nano Dimension, sur l'essor de l'impression 3D pour l'électronique
- Entretien d'experts :Philip DeSimone, cofondateur de Carbon, sur la transition vers une production à haut volume avec l'impression 3D
- Entretien d'experts :Rush LaSelle de Jabil sur l'avenir de la fabrication additive
- Entretien d'experts :Greg Paulsen de Xometry sur l'essor du modèle commercial de fabrication en tant que service
- Entretien d'experts :vice-président des partenariats technologiques de VELO3D sur l'extension des capacités de l'impression 3D métal
- Présentation du premier smartphone en fibre de carbone au monde
- Toray crée la première fibre de carbone poreuse au monde avec une structure à pores continus de taille nanométrique