25 startups d'impression 3D qui nous passionnent le plus en 2019
La dernière décennie a vu une vague d'activité pour l'industrie de l'impression 3D. De nouvelles entreprises continuent d'entrer sur le marché, se joignant à l'effort de transformation de la fabrication grâce à l'impression 3D.
Des systèmes matériels aux logiciels et services, la prolifération de nouveaux acteurs perturbant le marché est incroyablement excitante. Alors que le paysage de la fabrication additive continue de changer et d'évoluer, nous avons dressé une liste de quelques-unes des startups prometteuses à surveiller cette année.
Découvrez notre nouvel article explorant 10 startups prometteuses de l'impression 3D en 2020
Impression 3D Métal
Espace de relativité
Année de création : 2016
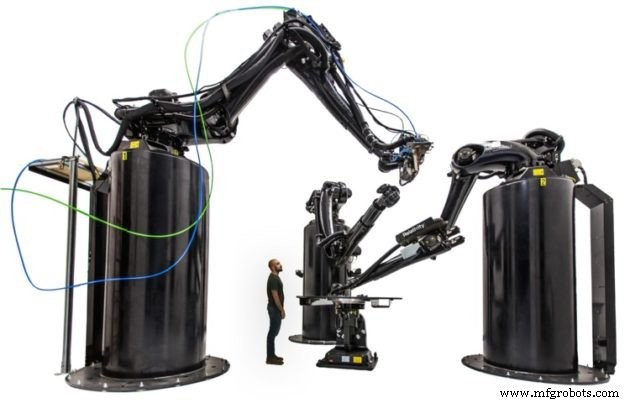
Relativity Space est une entreprise avec une vision unique :créer un jour des fusées entières en utilisant l'impression 3D.
En tant que mission, elle est certainement ambitieuse. Cependant, la société basée à Los Angeles s'est rapidement imposée comme un concurrent sérieux au sein de l'industrie aérospatiale :au cours des trois courtes années d'exploitation de l'espace Relativity, elle a levé environ 45 millions de dollars de financement.
De plus, la société dispose d'un niveau d'expertise impressionnant à exploiter, avec des employés comme SpaceX, Blue Origin et Tesla à bord.
Relatively Space cherchera à accélérer le développement et la production de ses fusées, tout en réduisant la complexité et en augmentant la fiabilité de ses produits. La tâche colossale sera accomplie en partie grâce à l'énorme imprimante 3D Stargate de l'entreprise, aux côtés d'autres technologies d'impression 3D.
D'ici fin 2020, Relativity Space prévoit de pouvoir fabriquer une fusée en moins de 60 jours, 95 % des composants de la fusée étant produits en impression 3D. Plus tard, la société prévoit également d'apporter un jour sa technologie d'impression 3D de fusée sur Mars.
Métal de bureau
Année de création : 2015
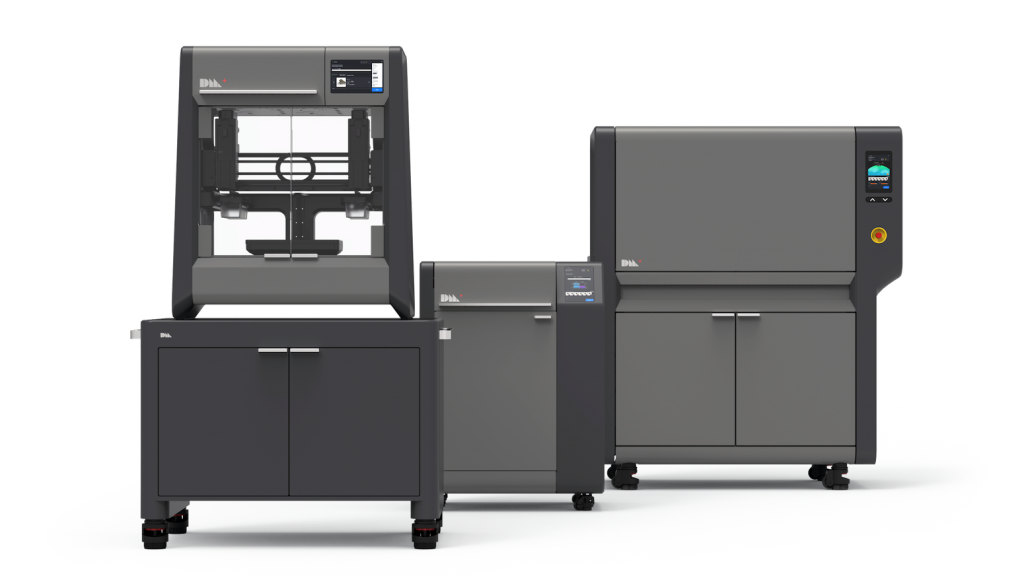
Alors que le secteur de l'impression 3D métal a suscité beaucoup d'attention dans la presse et les médias au cours des dernières années, les défis des coûts élevés, de la complexité et des vitesses lentes doivent encore être surmontés pour que la technologie devienne un concurrent viable pour la production en série.
Desktop Metal a été fondée pour repousser les limites de l'impression 3D métal, ce qui en fait un outil essentiel pour les ingénieurs et les fabricants.
Reconnaissant le besoin d'une impression 3D métal conviviale pour le bureau solution, Desktop Metal a lancé son imprimante 3D DM Studio en 2017, alimentée par une technique de dépôt de métal lié.
En plus de son système Studio, Desktop Metal a également sorti son plus grand système de Production, développé pour un usage industriel. Le système utilise un processus de jet de liant réinventé et, avec des vitesses d'impression beaucoup plus élevées par rapport aux systèmes laser, serait capable de rivaliser avec les méthodes de fabrication traditionnelles telles que le moulage.
Les ruptures technologiques de Desktop Metal contribuent à expliquer la trajectoire presque inédite d'une si jeune startup. Tout récemment, l'entreprise a reçu un financement supplémentaire de 160 millions de dollars, portant son financement total à 438 millions de dollars - le financement total le plus important de toute entreprise d'impression 3D privée à ce jour.
Bien que perturber l'industrie manufacturière de 12 000 milliards de dollars est un tâche ardue, les investissements de géants tels que Google, Ford, BMW et GE soulignent le potentiel futur de la technologie Desktop Metal ainsi que le potentiel de l'impression 3D métal dans son ensemble.
Alliages numériques
Année de création : 2017
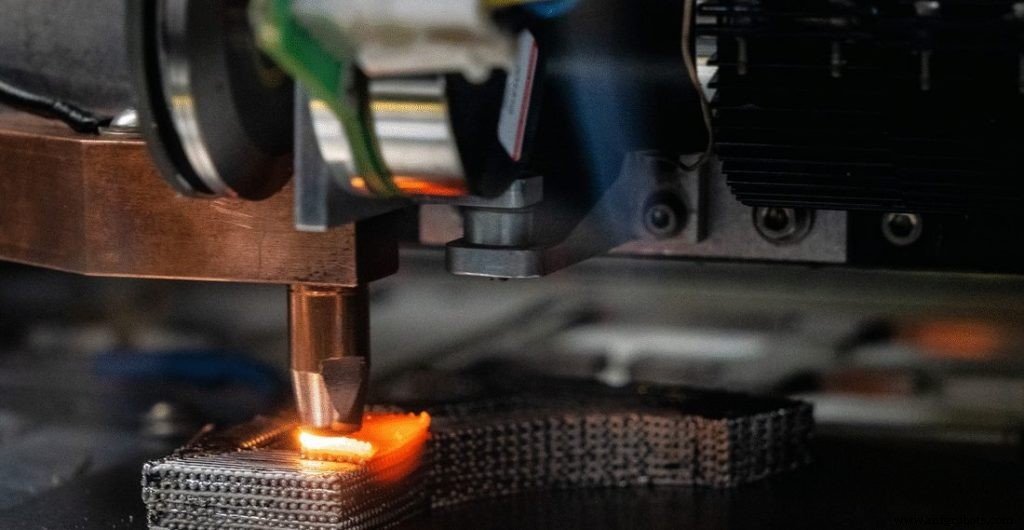
Au cours des deux dernières années, nous avons vu émerger un certain nombre de nouvelles technologies d'impression 3D métal, et l'impression Joule pourrait bien être l'une des plus excitantes d'entre elles.
La technique brevetée d'impression Joule provient de la startup américaine Digital Alloys et a été développée pour la fabrication additive métallique à grande vitesse. Grâce à cette technologie, l'entreprise espère résoudre trois défis actuels avec l'impression 3D métal :vitesse, coût de production et qualité
Le processus d'impression utilise du fil métallique à faible coût, qui est fondu en appliquant un chauffage résistif. Cette technique permet à la technologie de produire des taux de dépôt élevés de 5 ou 10 kg/heure.
Souhaitant répondre aux besoins de la fabrication automobile, aérospatiale et d'outillage, Digital Alloys envisage de lancer officiellement une entreprise d'impression de pièces vers fin 2019 et commencera à expédier ses imprimantes au début de 2020.
L'injection de 12,9 millions de dollars de financement que la société a reçue l'année dernière contribuera probablement grandement à aider Digital Alloys à atteindre son objectif de perturber le marché de la fabrication de métaux.
Vélo3D
Année de création : 2014
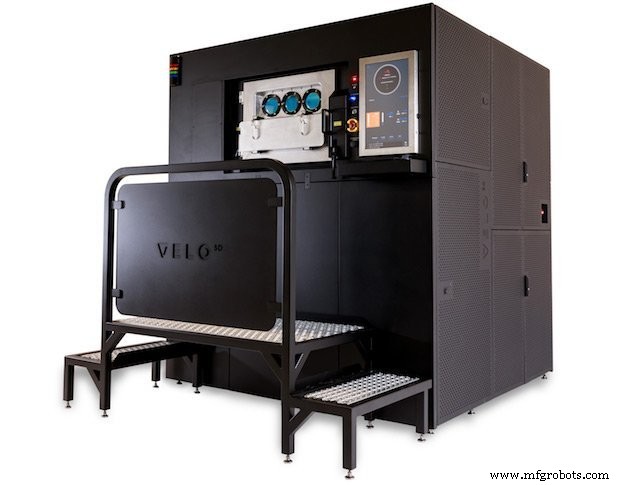
Entreprise qui a gardé sa technologie sous le radar, la société américaine Velo3D est sortie du mode furtif à l'été 2018 avec l'annonce de sa nouvelle imprimante 3D métal Sapphire.
Le système Sapphire, fruit de quatre années de développement, se targue de deux éléments clés :sa technologie Intelligent Fusion et son logiciel de préparation à l'impression Flow. Les deux fonctionnalités fonctionnent main dans la main pour permettre des avantages potentiellement révolutionnaires, comme une répétabilité améliorée et un post-traitement réduit.
Le système Sapphire est également capable d'imprimer des surplombs extrêmes sans avoir besoin de structures de support.
Avec le système déjà disponible à l'achat, Velo3D a maintenant pour objectif d'élargir la sélection de matériaux compatibles identifiant plus d'applications pour la technologie.
Métal Xact
Année de création : 2017
Pour des raisons qui incluent la complexité et les coûts élevés, de nombreuses petites et moyennes entreprises restent réticentes à adopter l'impression 3D de métal sur lit de poudre en interne.
Xact Metal, une société américaine basée en Pennsylvanie, a été fondée pour relever ce défi :rendre la technologie PBF métallique accessible aux chercheurs et aux petites entreprises.
La société compte actuellement trois machines dans son portefeuille de produits, avec le système le plus récent, le XM300C , expédition plus tard cette année.
Xact Metal a pu développer des imprimantes 3D métal avec un prix compris entre 90 000 $ et 175 000 $. Un facteur clé dans le prix relativement bon marché est le système de portique de l'entreprise. Le système de miroir galvanométrique plus cher utilisé pour diriger un laser vers un lit de poudre métallique a maintenant été remplacé par un système de portique XY moins cher.
Ce prix inférieur rend les technologies PBF métalliques plus accessibles aux universités et aux laboratoires et les PME qui ont également besoin de prototypage, d'outillage et de production en petites séries, mais ne pouvaient auparavant pas se permettre d'investir dans ces systèmes en interne.
Impression 3D polymère et composite
Carbone
Année de création : 2013
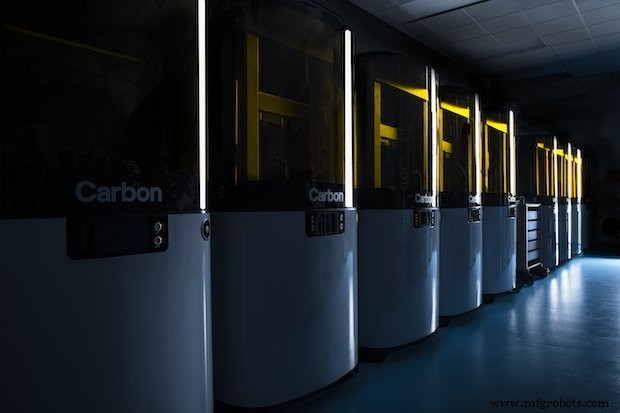
Depuis son entrée dans le paysage de la fabrication additive en 2013, Carbon s'est concentré sur la preuve de la viabilité de l'impression 3D pour la fabrication en grand volume.
L'entreprise a connu une trajectoire ascendante impressionnante, ayant atteint le statut de licorne en 2017.
Un exemple :Carbon bénéficie de partenariats commerciaux avec Adidas et Ford Motor Company, qui sont parmi les premiers à adopter sa technologie exclusive Digital Light Synthesis (DLS), utilisée pour produire des pièces en polymère de qualité industrielle.
Ce qui rend la technologie DLS de Carbon si populaire, c'est qu'elle s'attaque à ce qui a été l'un des plus gros points de friction de l'impression 3D :la vitesse.
Avec DLS, un projecteur projette une lumière UV à travers une fenêtre perméable à l'oxygène sur une cuve de résine photopolymère. Cette approche permet à l'impression 3D DLS de créer des objets à une cadence de 25 à 100 fois supérieure à celle des autres systèmes, en fabriquant des pièces de qualité moulée par injection.
Après avoir lancé son imprimante 3D L1 plus tôt cette année, il semble que Carbon continuera à être un pionnier dans le segment de l'impression 3D polymère.
Markforgé
Année de création : 2013
Markforged vise à rendre la fabrication additive plus accessible et abordable pour ses clients.
La société a fait son apparition avec son imprimante 3D pour fibre de carbone en 2014. Depuis lors, Markforged a développé des imprimantes 3D. qui peut supporter une large gamme de matériaux de qualité technique, y compris la fibre de carbone, le kevlar et l'onyx. La fibre de carbone, en particulier, a une gamme d'applications industrielles et peut, dans certains cas, être une alternative viable aux pièces métalliques.
Comme plusieurs autres fabricants d'imprimantes 3D, Markforged s'est également lancé dans le matériel métallique. segment, ayant lancé son imprimante Metal X en 2017.
La société aurait expédié plus de 2 500 imprimantes 3D industrielles en 2018 et a introduit de nouveaux matériaux dans son système Metal X.
Markforged pourrait-il rejoindre Desktop Metal et Carbon pour devenir une entreprise de licorne ? Alors que le jury n'est toujours pas sur cette question particulière, l'annonce récente par Markforged de son financement de 82 millions de dollars (série D) indique que l'entreprise reste sur une trajectoire de croissance positive.
Avec ce dernier investissement dit à être destinés à la poursuite de la recherche et du développement, les futures annonces de l'entreprise seront certainement intéressantes, c'est le moins qu'on puisse dire.
Roboze
Année de création : 2013
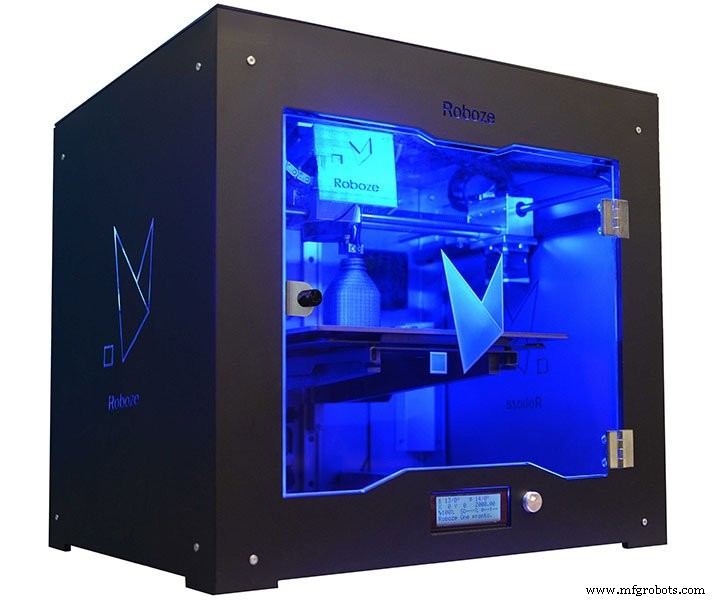
Roboze est un fabricant italien d'imprimantes 3D connu pour la capacité de ses imprimantes 3D à imprimer avec des matériaux hautes performances.
La première imprimante 3D de bureau de la société, la Roboze One, a été lancée sur le marché en 2015. Depuis lors, la société a lancé quatre autres imprimantes 3D ciblant les marchés de bureau, de bureau professionnel et de production.
Les systèmes de Roboze sont basés sur la technologie FFF et équipés d'extrudeuses hautes températures de polymères à haute viscosité (HVP).
L'utilisation des extrudeuses HVP permet aux imprimantes 3D de Roboze de traiter des matériaux hautes performances très recherchés comme le PEEK, l'ULTEM, le PP et le PA renforcé au carbone. Avec ses offres de matériel et de matériaux, Roboze vise les marchés industriels, notamment le médical, l'aérospatial, l'automobile et le pétrole et le gaz.
Alors que l'entreprise continue de se développer, il ne fait aucun doute que son récent financement de 3,4 millions de dollars contribuera grandement à stimuler sa croissance. Pour l'avenir, la société cherche à se développer dans la région EMEA et aux États-Unis, avec pour objectif une croissance de 500 % de son activité d'ici la fin de cette année.
Origine
Année de création : 2015
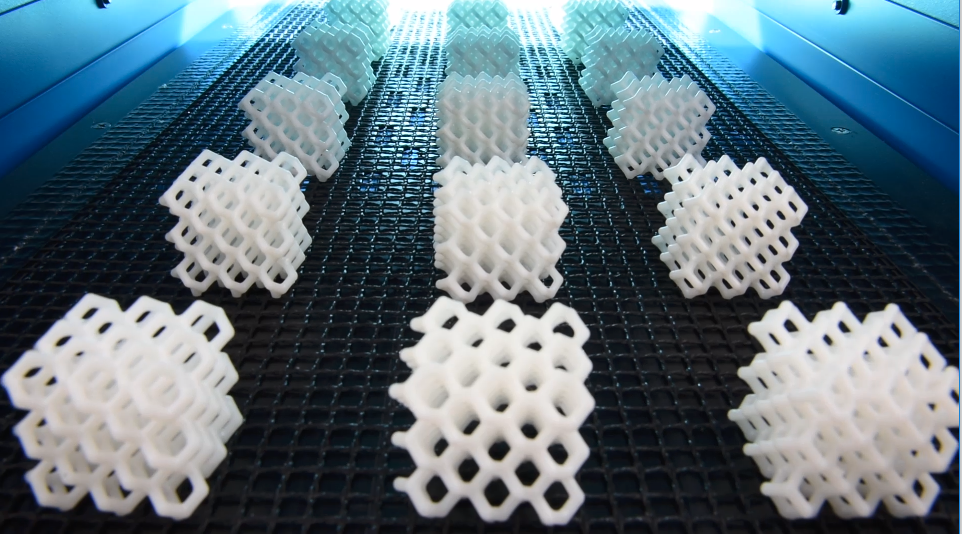
Dire que vous révolutionnez la fabrication des plastiques est une affirmation audacieuse, mais celle de la startup de San Francisco, Origin. La société a dévoilé pour la première fois sa plate-forme, Open Additive Production, à l'automne 2018. La plate-forme présente la vision de la société pour la FA et est basée sur des matériaux ouverts, des logiciels flexibles et du matériel modulaire.
Un modèle de matériaux ouvert, où les développeurs de matériaux peuvent créer des formules chimiques spécifiquement pour la technologie, est au cœur des plans d'Origin visant à faire de l'impression 3D une méthode de production de masse viable.
La société s'est associée à certaines des plus grandes sociétés chimiques au monde telles que BASF et Henkel. Ce réseau ouvert de partenaires de matériaux fournit le soutien nécessaire pour accélérer le développement de nouveaux et meilleurs matériaux de FA.
Côté technologie, Origin a développé un procédé similaire à la stéréolithographie, baptisé Photopolymérisation Programmable (P3), qui repose sur des résines photoréactives. Mais contrairement aux précédents procédés d'impression 3D en résine, P3 ne dépend pas de l'oxygène, ouvrant la porte à une plus grande variété de matériaux, tels que les polyoléfines.
Bien que de nombreux détails sur la technologie d'Origin restent étroitement liés à secret gardé, il semble y avoir quelques ondulations d'excitation à venir :il a obtenu 10 millions de dollars de financement de série A (2018) et prévoit également de sortir son système au salon RAPID + TCT, qui aura lieu fin mai.
Colosse
Année de création : 2016
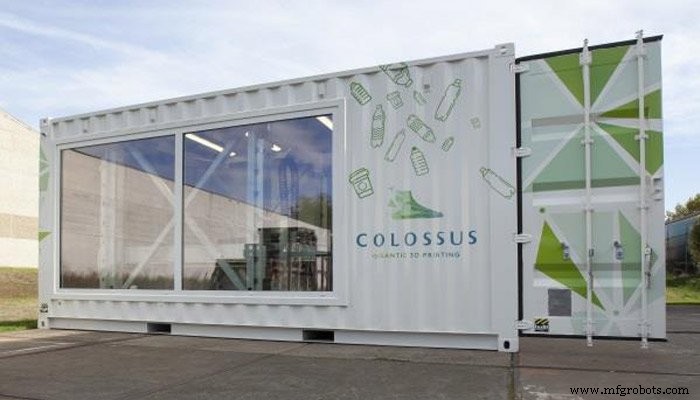
Une entreprise qui cherche à innover dans le domaine de l'impression 3D à grande échelle est le fabricant belge d'imprimantes 3D, Colossus.
Colossus a présenté pour la première fois son imprimante 3D à grande échelle du même nom à Formnext 2018.
L'imprimante 3D Colossus est basée sur Fused Granular Fabrication (FGF), une technologie qui est similaire au FDM mais utilise des pastilles de plastique par opposition aux filaments.
La bien nommée imprimante 3D Colossus a une vitesse d'impression impressionnante (15 kg par heure) et un volume d'impression de 2,67 x 1,5 mètres. Malgré sa taille, l'entreprise affirme que le système d'impression 3D a été conçu pour être facilement transporté et mis à niveau.
Grâce au partenariat de l'entreprise avec Mitsubishi Chemical, dix profils de composés de matériaux ont déjà été pré-testés sur le Colossus. À mesure que la technologie derrière le Colossus s'améliore, les applications à grande échelle dans la fabrication de meubles et la construction ne sont peut-être pas loin d'être hors de portée.
Faire évoluer les solutions additives
Année de création : 2017
La production en série avec l'impression 3D a été un objectif majeur pour l'industrie de la fabrication additive.
Evolve Additive Solutions, une entreprise dérivée de Stratasys, a été lancée avec cet objectif en tête. L'entreprise vise à améliorer radicalement la fabrication des plastiques avec une solution d'impression 3D évolutive.
Issu de Stratasys en 2018, la société a passé près d'une décennie à développer une technologie additive potentiellement révolutionnaire appelée Selective Thermoplastic Electrophotographic Process, ou STEP.
Selon l'entreprise, STEP est « 100 % axé sur la fabrication ». La technologie a été développée pour offrir la flexibilité de la fabrication additive tout en permettant une production en grand volume de pièces en plastique.
STEP est basé sur la technologie propriétaire d'électrophotographie, similaire à celle trouvée dans les photocopieurs et laser standard. imprimantes. Cette méthode est censée permettre la fabrication additive de pièces qui atteignent ou dépassent la qualité des pièces moulées par injection.
Avec plus de 19 millions de dollars de financement et de commercialisation prévus pour fin 2020, il sera intéressant de voir si STEP deviendra bientôt un ajout intrinsèque au processus de fabrication.
Fortifier
Année de création : 2016
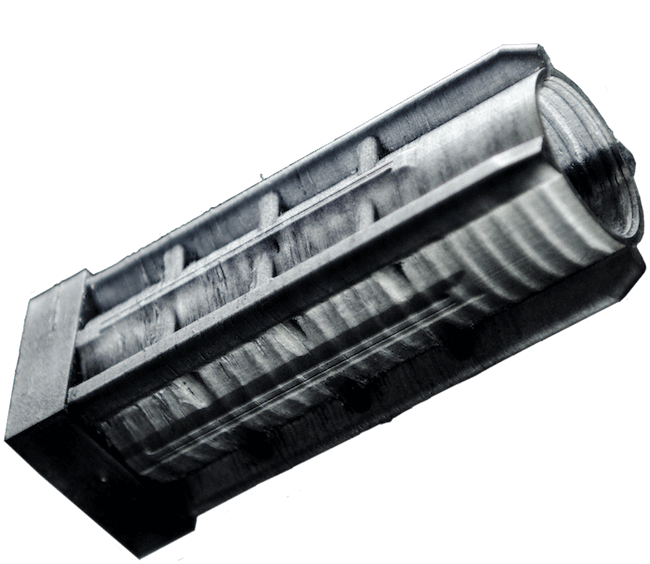
La startup Fortify basée à Boston est une entreprise passionnante proposant une nouvelle technologie de fabrication de composites numériques (DCM) appelée Fluxprint. Il comprend le matériel Fluxprint breveté de Fortify, de nouveaux matériaux composites et le logiciel de conception générative INFORM.
Basé sur un processus qui combine des aimants avec la technologie Digital Light Processing (DLP), la technologie de Fortify est censée être capable de produire des -des pièces composites de qualité qui nécessiteraient normalement des méthodes beaucoup plus exigeantes en main-d'œuvre. Actuellement, les pièces peuvent être produites à partir de matériaux composites en fibre de carbone, en fibre de verre et en céramique.
Ayant reçu 2,5 millions de dollars lors de sa dernière levée de fonds, la société semble être bien placée pour répondre à la demande d'impression 3D composite avancée dans l'industrie manufacturière.
Rize
Année de création : 2014
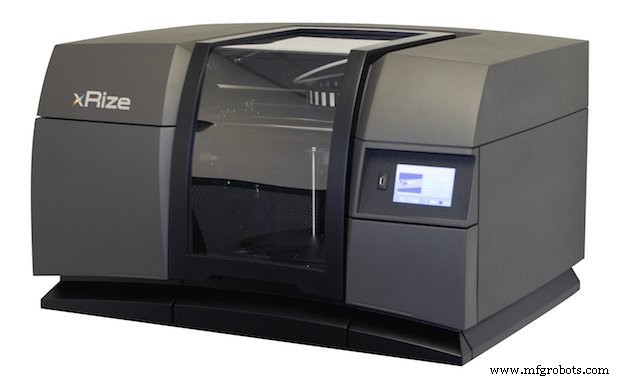
Combiner l'impression 3D industrielle avec la durabilité et la répétabilité est un objectif ambitieux, mais Rize l'atteint de front.
Basé à Boston, le fabricant d'imprimantes 3D a développé une impression 3D propriétaire technologie appelée Dépôt de Polymère Augmenté (APD). APD associe deux procédés d'impression 3D largement utilisés, la fabrication de filaments fondus (FFF) et le jet de matériau, pour permettre des pièces en couleur sans avoir besoin de post-traitement.
Depuis sa création, Riz a introduit deux Systèmes d'impression 3D clés :RIZE ONE, une imprimante 3D hybride de bureau professionnelle, et XRIZE, développé pour les applications d'entreprise industrielle.
Le système XRIZE extrude simultanément des filaments et projette des encres CMJN pour créer des pièces en couleur. Le système dépose également une encre spéciale Release One entre la pièce imprimée et ses supports, simplifiant la tâche généralement ardue de retrait du support - et éliminant le besoin de finition supplémentaire.
Fournir aux utilisateurs l'expérience simple de l'utilisation l'impression 3D industrielle est un objectif qui vaut la peine d'être poursuivi et les imprimantes 3D Rize sont un excellent exemple de la façon dont il peut être atteint aujourd'hui.
Moi Composites
Année de création : 2018
L'impression 3D composite est une technologie émergente avec un grand potentiel pour la fabrication de pièces hautes performances. La startup italienne Moi Composites fait partie du petit nombre d'entreprises proposant une technologie pour l'impression 3D de matériaux composites.
Moi Composites a développé un processus breveté de fabrication de fibres continues (CFM) qui utilise des bras robotiques KUKA contrôlés par des algorithmes spéciaux.
Développés en collaboration avec Autodesk, les algorithmes permettent d'optimiser le dépôt des matériaux fibreux. En utilisant cette approche, des objets aussi grands que 0,8 m x 1 m x 1,2 m peuvent être créés à partir de matériaux tels que des fibres de verre combinées à des résines d'ester vinylique.
Bien que le choix des matériaux soit assez limité, Moi Composites prévoit d'ajouter des fibres de carbone et d'aramide dans un futur proche. Actuellement, la startup agit en tant que service de co-conception et de production de petites séries, de pièces personnalisées et de haute performance, ciblant les industries du médical à la marine, en passant par le pétrole et le gaz et l'aérospatiale.
Aérosint
Année de création : 2016
Le concept d'impression 3D multi-matériaux existe depuis un certain temps, mais jusqu'à récemment, la technologie était limitée à quelques processus comme le FDM et le jet de matériau. Mais et s'il était possible d'utiliser plusieurs matériaux dans l'impression 3D SLS ?
Aerosint est une entreprise qui essaie d'apporter des capacités d'impression multi-matériaux aux technologies de fusion sur lit de poudre.
La startup vise à permettre l'impression 3D polymère haute performance avec zéro déchet et une vaste possibilités matérielles. Aerosint prétend avoir développé le premier (à ce jour) processus d'impression multi-poudre qui peut imprimer des pièces faites de différents matériaux.
Étant donné que la nouvelle approche est encore en phase de recherche et développement — le premier prototype d'Aerosint de son imprimante a été achevée au début de 2018 - il faudra un certain temps pour évaluer les implications réelles de la technologie. Cela dit, nous sommes ravis de voir comment la nouvelle technologie d'Aerosint pourrait potentiellement faire progresser les capacités de fabrication additive sur lit de poudre.
Arevo
Année de création : 2013
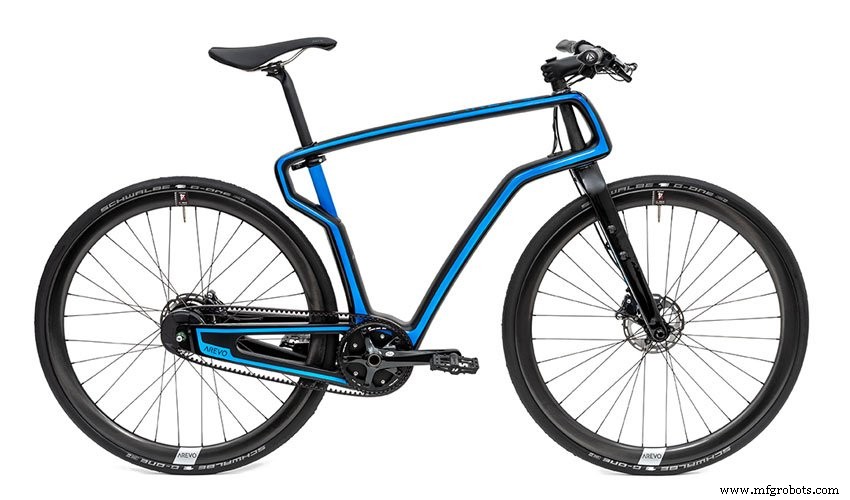
La demande de thermoplastiques plus solides, plus durables et de qualité technique pour la fabrication additive augmente rapidement. La société américaine Arevo vise à répondre à ce besoin avec sa technologie d'impression 3D, capable de traiter les matériaux composites.
Le processus d'impression 3D d'Arevo aborde chaque domaine du trio d'impression 3D :machines, matériaux et logiciels.
La technologie utilise une imprimante 3D robotisée à six axes et un logiciel propriétaire qui optimise le dépôt de matériaux composites. L'entreprise espère que cette combinaison offrira aux concepteurs et aux fabricants la possibilité de créer des produits d'une résistance et d'une durabilité exceptionnelles.
Logiciel d'impression 3D
nTopologie
Année de création : 2015
La fabrication additive offre la possibilité de réinventer le processus de conception, en produisant des conceptions avec des géométries optimisées et très complexes. Cependant, pour y parvenir, nous avons besoin d'une nouvelle génération d'outils de conception, comme l'optimisation de la topologie et la conception générative.
Basée à New York, nTopology fournit des solutions logicielles avancées pour permettre la production de pièces imprimées en 3D légères et optimisées.
La plate-forme nTopology, Element, comprend une gamme d'outils qui incluent la simulation et la conception de treillis. De plus, il utilise un format de fichier LTCX beaucoup plus léger au lieu de STL, ce qui rend le transfert entre le logiciel et d'autres programmes de CAO plus simple et plus rapide.
Avec plus de 7 millions de dollars levés depuis sa création en 2015, nTopology est sur le point d'améliorer encore les capacités de son logiciel pour une utilisation dans les secteurs à forte croissance de la fabrication additive et avancée.
Bêtatype
Année de création : 2012
Pour les entreprises qui luttent pour passer du prototypage à la fabrication avec la fabrication additive métallique, la technologie d'optimisation des processus pourrait être une solution importante.
Prenons l'exemple des implants orthopédiques. La production de modèles d'implants orthopédiques avec impression 3D métallique peut être une tâche difficile, car leur structure géométrique est généralement très complexe. Avant de pouvoir être imprimés en 3D, les fichiers doivent être découpés, générant des paramètres de processus tels que le chemin de balayage laser et la puissance du laser.
Inévitablement, les données de paramètres, qui doivent être envoyées à une imprimante 3D, peuvent finir étant de taille significativement grande. Les grands ensembles de données ont l'inconvénient de ralentir le processus d'impression en raison de la vitesse et de la capacité de stockage limitées des machines d'impression 3D.
La société basée à Londres, Betatype, a développé un logiciel pour surmonter ce défi. Son logiciel de traitement des données, Engine, serait capable d'optimiser des volumes élevés de données de construction, en partie en stockant les données de traitement dans des formats de fichier plus légers qu'un fichier STL (comme le format de fichier ARCH de Betatype). Cela réduit les temps de traitement, permettant finalement la production en série d'implants orthopédiques à un coût nettement inférieur.
Le moteur peut également aider à optimiser un composant fonction par fonction, permettant d'imprimer une pièce avec un meilleur contrôle. Ce niveau d'optimisation permet à Betatype d'obtenir un temps de construction et un coût par pièce réduits.
Mais ce n'est pas seulement le secteur médical qui peut bénéficier du logiciel d'impression 3D métal de Betatype. Par exemple, une récente étude de cas publiée par la société montre comment elle a appliqué son logiciel d'optimisation des processus à l'industrie automobile pour réduire le temps de construction de 444 heures à moins de 30 heures pour un lot de 384 composants métalliques.
Services d'ingénierie et de fabrication d'impression 3D
Morf3D
Année de création : 2015
Morf3D est une société de services de fabrication additive qui fait progresser la technologie d'impression 3D métallique pour les applications aérospatiales. Morf3D a été fondée pour soutenir davantage l'adoption de la FA dans l'aérospatiale, en aidant les entreprises à relever les défis de l'utilisation de la FA.
Morf3D propose une vaste gamme de capacités d'impression 3D métal en interne, y compris le frittage laser direct du métal et fusion par faisceau d'électrons dans une variété de métaux tels que l'aluminium, le titane, l'Inconel et l'acier inoxydable.
L'une des applications réussies comprend des composants en aluminium et en titane imprimés en 3D pour les satellites et les hélicoptères Boeing. Ceci, bien sûr, n'est pas une mince affaire, et témoigne des efforts considérables que l'entreprise met dans l'ingénierie, la production et la qualification de composants aérospatiaux très exigeants.
Rayon rapide
Année de création : 2014
En septembre 2018, Fast Radius a été désignée comme l'une des meilleures usines au monde, grâce à la mise en œuvre d'une gamme de technologies Industrie 4.0.
En utilisant des technologies de fabrication numérique telles que l'impression 3D, Fast Radius vise à créer de nouvelles solutions de chaîne d'approvisionnement pour ses clients, telles que les inventaires virtuels et la production à la demande.
La société s'appuie sur son expertise en fabrication additive pour aider ses clients à identifier et à lancer de nouveaux produits et modèles commerciaux rendus possibles par la technologie,
Pour y parvenir, Fast Radius propose une technologie plate-forme qui identifie les applications pour l'impression 3D, aide à évaluer les aspects techniques et économiques et permet la production de pièces de qualité industrielle à l'aide de la FA.
Le siège social de Fast Radius à Chicago abriterait l'une des installations de FA les plus avancées en Amérique du Nord ainsi que l'une des plus grandes installations de production de carbone.
Un élément clé du service de Fast Radius est un partenariat stratégique avec United Parcel Service (UPS). L'entreprise possède une installation de production sur place à UPS Worldport, la plus grande installation d'emballage automatisée au monde.
Alors que l'impression 3D permet un traitement plus rapide des pièces, le partenariat avec UPS aide l'entreprise à accélérer l'expédition. Avec cette approche, Fast Radius fait un pas en avant pour la fabrication à la demande.
Technologie Conflux
Année de création : 2015
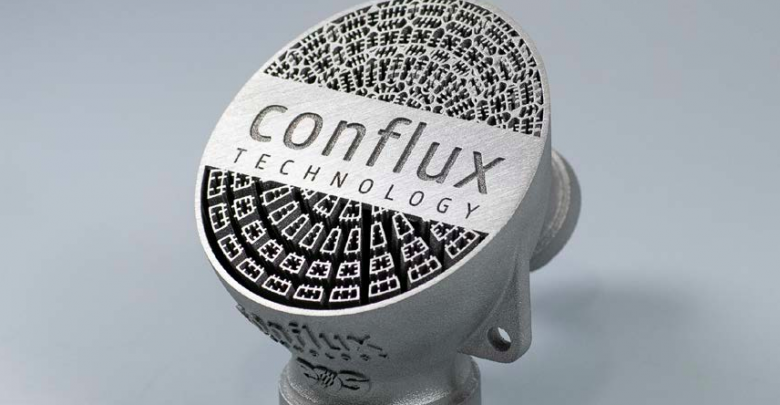
L'ingénierie thermique et des fluides est un domaine qui peut grandement bénéficier de la fabrication additive. La technologie convient parfaitement aux composants thermiques complexes tels que les échangeurs de chaleur, permettant de produire des composants plus légers et plus efficaces.
Conflux Technology est une société australienne qui a reconnu le potentiel révolutionnaire de la FA pour les applications d'échange de chaleur et d'écoulement de fluide. S'appuyant sur son expertise en ingénierie et en FA métallique, l'entreprise se concentre sur la conception et la production de composants thermiques et fluides hautement efficaces.
Soutenu par AM Ventures, Conflux présente des arguments convaincants pour les échangeurs de chaleur imprimés en 3D, offrant des avantages en termes de performances, tels qu'un calendrier de développement rapide et un minimum d'itérations de prototypes.
Fabrication vaudou
Date de création : 2015
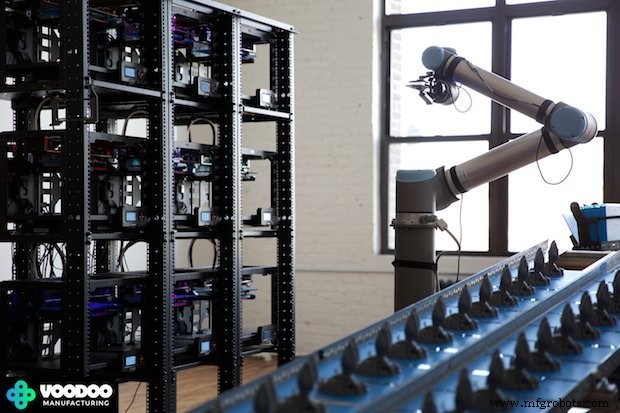
Est-ce qu'une usine d'impression 3D à haut volume basée sur un logiciel, capable de rivaliser avec le moulage par injection, semble trop belle pour être vraie ?
Peut-être pas, car la société Voodoo Manufacturing, basée à Brooklyn, fait exactement cela.
Forte de plus de 6 millions de dollars de financement de démarrage, Voodoo Manufacturing est devenue une ferme d'impression numérique, avec plus de 200 imprimantes 3D en interne.
Propulser le numérique de Voodoo Manufacturing Le concept d'usine est un logiciel et une robotique, qui automatisent les tâches manuelles inefficaces telles que le chargement et le déchargement des plaques de construction des imprimantes.
Grâce à l'automatisation, l'entreprise vise à atteindre 100 % d'utilisation du matériel pour pouvoir fonctionner 24 heures sur 24. Avec des clients comme Nickelodeon, Microsoft, Mattel et Lowe's dans sa liste, Voodoo Manufacturing est en bonne voie pour récolter les avantages les plus prometteurs de la fabrication numérique intelligente avec l'impression 3D.
Impression 3D pour la construction
Apis Cor
Année de création : 2014
Le taux d'adoption de l'impression 3D dans le secteur de la construction étant relativement lent, Apis Cor a conçu une imprimante 3D à grande échelle pour construire des maisons plus rapidement et à moindre coût.
La technologie utilise des matériaux en béton pour imprimer les murs d'un bâtiment sur place en plusieurs jours, contre plusieurs semaines en construction traditionnelle. En 2017, l'entreprise a construit une maison d'habitation en seulement 24 heures pour un coût inférieur à 10 000 $.
Actuellement, Apis Cor s'apprête à étendre les capacités de son imprimante 3D pour pouvoir imprimer des fondations, planchers et toiture. Soutenue par la NASA, la startup mène également des recherches sur la possibilité de créer des abris durables adaptés à la lune, Mars – et au-delà.
Impression 3D pour l'électronique
Nano dimension
Année de création : 2012
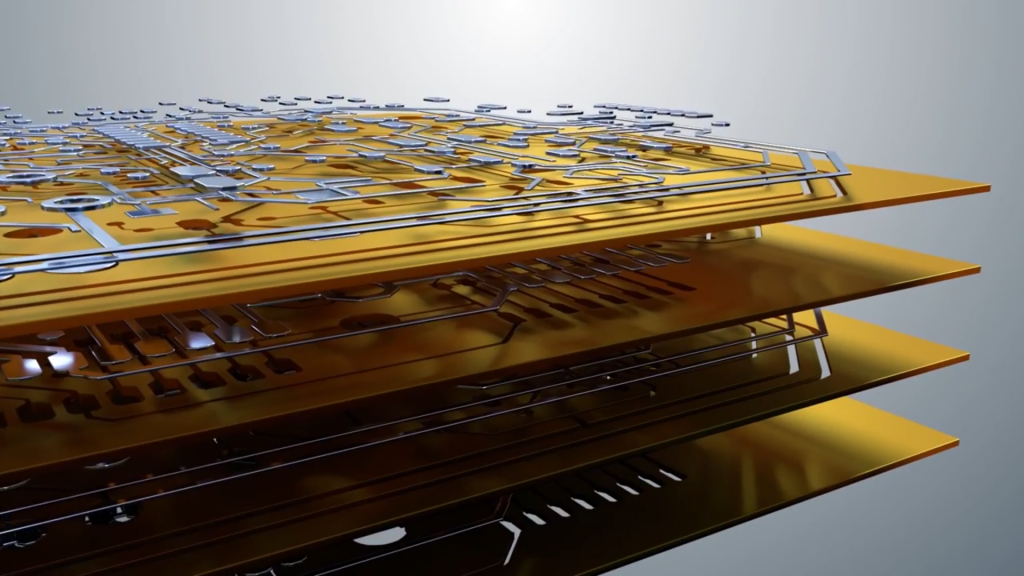
Dans l'industrie électronique, la création de prototypes de composants électroniques est un processus long. Cela implique généralement de sous-traiter les conceptions à un tiers, ce qui retarde le cycle de conception de plusieurs semaines, voire plusieurs mois. Pour les industries critiques telles que l'aérospatiale et la défense, les problèmes de sécurité abondent également.
C'est ici que l'impression 3D prend tout son sens.
Pour répondre aux besoins uniques du développement et de la fabrication de composants électroniques , la société israélienne Nano Dimension utilise l'impression 3D pour permettre aux fabricants de prototyper en interne des composants électroniques tels que des cartes de circuits imprimés (PCB).
Le produit phare de Nano Dimension, la DragonFly 2020 Pro, est une imprimante PCB 3D capable d'imprimer simultanément un polymère diélectrique et un métal conducteur, permettant aux utilisateurs d'imprimer des circuits électroniques directement dans des composants et de créer des prototypes de PCB multicouches.
Grâce à cette technologie, les entreprises pourront imprimer des prototypes en 3D en interne, développant ainsi de nouveaux appareils électroniques plus rapidement et plus efficacement.
Depuis le lancement commercial du DragonFly 2020 Pro en 2017, Nano Dimension a connu une traction croissante sur le marché, en particulier des industries de l'aérospatiale et de la défense, ainsi que des entreprises automobiles et électroniques grand public.
Matériel de post-traitement
Technologies de post-traitement
Année de création : 2014
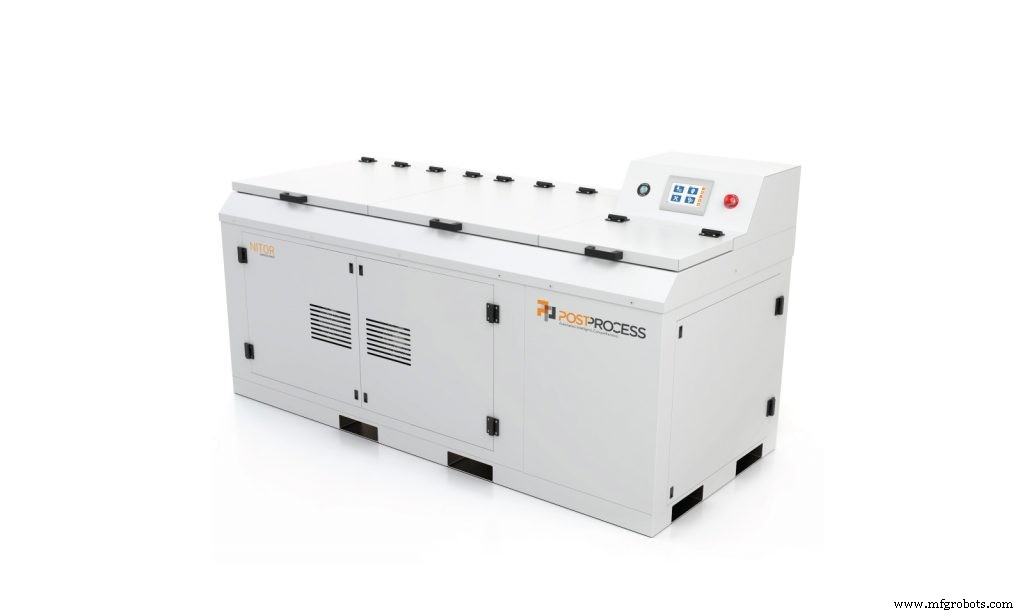
Post-processing has long been considered the most time-intensive stage of the AM process.
For PostProcess Technologies, automation is the solution. Automating the third step of the AM workflow is essential for consistency, throughput and traceability.
The US company offers automated equipment for support removal and surface finishing, suitable for PolyJet, FDM, SLA parts, along with Multi Jet Fusion, CLIP and DMLS parts.
Enabling this level of automation is the integration of software, hardware and chemistry. To eliminate the manual effort in post-processing, the proprietary software helps to control the amount of energy in the machine to automatically remove the supports and give a dramatically improved surface finish.
New Companies, New Opportunities
As we’ve seen in our Additive Manufacturing Landscape for 2019, the industry is being driven in large part by innovative startups offering new and exciting technologies.
While some of the startups featured in this list are still in the early stages, others have already carved out their share of the AM market. That a number of companies have received impressive funding rounds not only points to the individual success of the companies themselves, but also to the confidence of investors in the future of the AM market. We’re excited to see how these companies will evolve and continue to push 3D printing to new horizons.
impression en 3D
- 5 mythes courants sur l'impression 3D
- 6 choses que vous ne saviez pas sur l'impression 3D
- Les goulots d'étranglement du flux de travail d'impression 3D les plus courants – et comment les résoudre
- L'impression 3D pénètre les environnements les plus difficiles… y compris l'espace
- Les prochains modèles d'imprimantes 3D que vous devez connaître
- Salon TCT 2018 :les 10 technologies que nous sommes les plus impatients de voir
- Trois applications d'impression 3D pour sourire
- 10 matériaux d'impression 3D les plus résistants à la chaleur
- Faits sur l'impression laser du métal