Assurance qualité pour l'impression 3D métal : résolution de 3 défis courants
L'assurance qualité (AQ) est sans doute l'étape la plus importante et pourtant l'une des plus difficiles de l'impression 3D.
L'impression 3D étant de plus en plus utilisée dans les applications industrielles hautes performances, la technologie doit fournir de manière cohérente et fiable des pièces de haute qualité avec les propriétés nécessaires pour répondre aux applications exigeantes. En ce qui concerne l'impression 3D métal, cependant, cela a été un défi permanent pour de nombreux fabricants cherchant à investir dans la technologie.
L'article d'aujourd'hui examinera certains des principaux défis auxquels les entreprises sont confrontées lorsqu'elles essaient pour établir des processus d'assurance qualité pour les pièces métalliques imprimées en 3D et explorer certaines des solutions disponibles.
Enjeu 1 :Garantir la qualité de vos matériaux
S'assurer qu'une pièce imprimée en 3D répond aux normes d'applications très exigeantes dépend fortement de la qualité du matériau utilisé.
Cependant, la qualification des matériaux est un défi permanent pour les entreprises produisant ou manipulant des poudres métalliques. Un facteur compliquant le processus est la nécessité de maintenir la pureté des poudres métalliques utilisées pour la fabrication additive.
C'est particulièrement le cas pour les applications critiques pour la sécurité, telles que les pièces d'avions ou les dispositifs médicaux, où le matériau utilisé doit être 100 % exempt de contamination. Les impuretés peuvent altérer les propriétés de la pièce finale, ce qui pourrait, à son tour, entraîner un échec de l'impression.
Cependant, les poudres métalliques peuvent être contaminées de plusieurs manières.
Par exemple, le risque de contamination peut survenir pendant le processus d'impression lui-même ou pendant le stockage, le transport et la manipulation. Prenons le premier exemple :il pourrait, par exemple, rester des résidus d'une autre poudre sur le plateau de fabrication, entraînant le mélange de deux poudres différentes. Un nettoyage minutieux de la plaque de construction après chaque cycle de production est donc une étape préventive importante.
Un autre risque vient de la réutilisation de la poudre, résidu du processus d'impression. Bien que la possibilité de réutiliser le matériau en poudre puisse aider à réduire le gaspillage, il est important de noter que la réutilisation répétée de la poudre de cette manière peut potentiellement modifier la composition des particules, car l'humidité, l'oxygène et l'azote sont absorbés.
Forcément, des méthodes d'essais, adaptées à la fabrication additive, seront nécessaires pour s'assurer qu'il n'y a pas de contamination.
Solution :Envisagez la tomodensitométrie
L'un des moyens les plus précis de détecter la contamination dans les poudres métalliques consiste à utiliser la tomodensitométrie (CT).
Un scanner CT fonctionne en prenant des centaines d'images radiographiques sous différents angles, à partir desquelles une image 3D est créée. Les scanners CT modernes peuvent capturer des détails jusqu'à trois microns, avec certains scanners microCT haute résolution, qui fonctionnent à une échelle micrométrique beaucoup plus petite, atteignant une taille de voxel de 0,5 micron.
L'équipement microCT actuel peut inspecter des métaux allant de l'aluminium et du titane aux alliages métalliques plus lourds comme l'acier inoxydable et l'Inconel.
Lorsqu'ils sont utilisés pour qualifier des poudres métalliques pour l'impression 3D, les scanners CT peuvent fournir aux ingénieurs des données approfondies sur la microstructure des poudres. Ces données peuvent être utilisées pour détecter des contaminants de particules étrangères ainsi que pour mesurer la distribution de la taille et de la forme des particules et détecter la porosité à l'intérieur des particules. L'obtention de ces informations est un moyen pour les ingénieurs de confirmer l'applicabilité de la poudre pour la production.
Expanse Microtechnologies est une entreprise qui fournit des services de tomodensitométrie pour la fabrication additive.
S'exprimant dans une interview avec AMFG, James Hinebaugh, président et co-fondateur de l'entreprise, note que « les poudres sont le point d'intérêt clé sur l'ensemble de la chaîne d'approvisionnement de la fabrication additive. Comprendre ce qui fait une bonne poudre qui s'étale et s'imprime bien est une préoccupation clé pour les entreprises.
« Il est important de comprendre 1) s'il existe une morphologie idéale ou une taille idéale ou une distribution morphologique qui peut bien interagir avec une grande variété d'applicateurs de revêtement et d'imprimantes, et 2) comment nous pouvons réduire les défauts des poudres comme les inclusions et la porosité intraparticulaire qui, selon des études, sont souvent piégés dans une pièce et ne peuvent pas s'échapper de la pièce pendant le processus d'impression.
Ce sont les deux domaines qu'Expanse Microtechnologies aborde avec sa solution propriétaire de numérisation MicroCT.
La société a développé des méthodes avancées de traitement d'images, à partir desquelles elle est capable de générer des rapports détaillés sur la porosité des matériaux, la morphologie des particules et des pores, ainsi que la distribution de la taille et de la forme des particules.
Disposer de ces informations permet aux utilisateurs de la fabrication additive d'identifier tout problème de matière première et de comprendre les liens entre les matériaux qu'ils utilisent et le niveau de qualité des composants imprimés.
Bien que les tests et la qualification des matières premières pour la fabrication additive puissent être difficiles, il s'agit de l'une des étapes les plus importantes pour garantir la qualité d'une pièce fabriquée de manière additive. Actuellement, la tomodensitométrie offre l'un des outils les plus robustes et les plus utiles pouvant être utilisés pour valider les matières premières de la FA.
Défi 2 :Établir le contrôle des processus
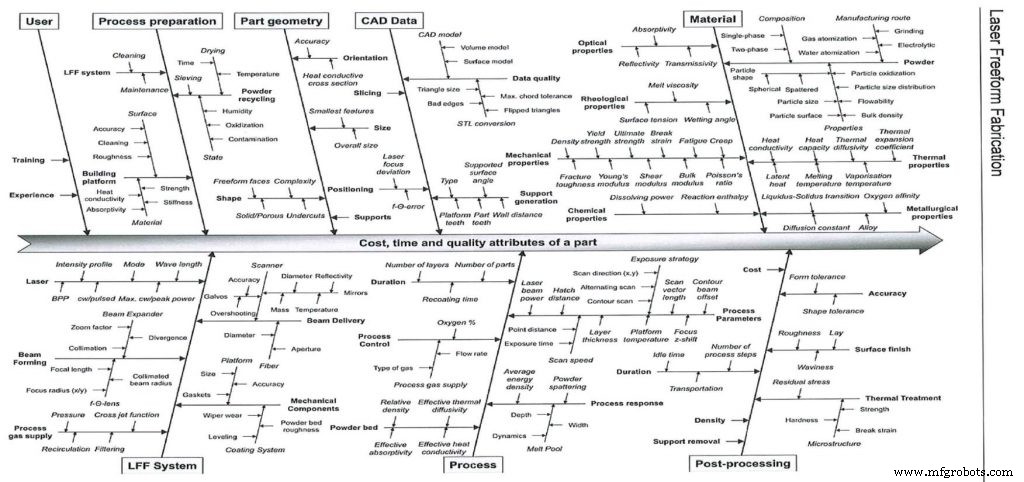
Lorsqu'il s'agit d'impression 3D métal - et de technologies de fusion sur lit de poudre en particulier - il existe un large éventail de variables qui peuvent affecter la forme et la structure d'une pièce. Ces variables couvrent l'ensemble du flux de production AM, de la conception à la préparation de la construction et au post-traitement.
Prenons le processus d'impression comme exemple. Ici, quelques-uns des paramètres déterminant le succès ou l'échec du processus incluent le chemin et l'intensité du laser et la vitesse de la lame de la coucheuse de l'imprimante. D'autres facteurs incluent la conception des structures de support et même des subtilités comme le nombre de fois que la poudre a été recyclée.
Bien que cette liste ne soit même pas près d'être exhaustive, chaque facteur a un impact sur le résultat d'une construction et d'un écart de quelque manière que ce soit pourrait affecter la qualité de la pièce finale.
Actuellement, un essai et une erreur est l'approche la plus courante pour traiter le large éventail de variables afin d'obtenir un processus qui produit reproductible les pièces. Cependant, cela peut impliquer de fabriquer plusieurs fois la pièce finale ainsi que des tests approfondis de la pièce elle-même.
Bien entendu, l'adoption de cette approche est un processus très coûteux et inefficace, et annule l'un des principaux avantages de la technologie :être capable de produire de petits lots de pièces de manière rentable.
Les entreprises doivent donc adopter une approche plus durable et réalisable pour le contrôle des processus et la qualification des pièces fabriquées de manière additive.
Solution :Développer un système de contrôle qualité en boucle fermée
Trois éléments doivent être réunis pour permettre un processus d'assurance qualité plus rapide, plus fiable et plus durable pour les pièces imprimées en 3D. Cela comprend la planification de la construction, la surveillance de la construction et le contrôle des commentaires.
- Planifier la construction
Une façon de mieux comprendre le processus d'impression est la simulation. À l'aide de la simulation, les ingénieurs peuvent tester le comportement d'une pièce dans un environnement numérique virtuel avant qu'une conception ne soit envoyée à l'impression.
La simulation du processus AM permet aux ingénieurs d'analyser les processus complexes qui se produisent pendant le processus d'impression.
Comme l'impression 3D métal est sujette à des problèmes tels que le gauchissement et la distorsion, la simulation offre des informations clés sur la façon dont une pièce se déformera pendant le processus d'impression, par exemple. Un autre exemple consiste à utiliser la simulation pour déterminer exactement comment le matériau va fondre et se solidifier.
Les ingénieurs peuvent ensuite utiliser ces données pour planifier la construction, en sélectionnant l'orientation des pièces et les stratégies d'assistance les plus efficaces.
Cela dit, les logiciels de simulation ont leurs limites. « Tous les logiciels de simulation d'aujourd'hui comportent un certain niveau d'hypothèses qui limitent la précision qu'ils peuvent fournir. C'est probablement le plus gros inconvénient à l'heure actuelle :ils ne peuvent pas être aussi précis que vous le souhaiteriez », a déclaré le technologue en chef d'ANSYS, Dave Conover, lors d'une récente interview avec AMFG.
Cependant, la technologie de simulation évolue rapidement, les éditeurs de logiciels continuant d'affiner leurs offres. En fin de compte, l'intégration d'un logiciel de simulation aux étapes de conception et de planification aidera à éliminer les essais et les erreurs, tout en réduisant considérablement les risques d'échec d'impression.
- Surveillance de la construction
Les systèmes de surveillance en cours de fabrication peuvent aider davantage le processus de qualification des pièces. Des capteurs et des caméras peuvent être utilisés pour mesurer plusieurs aspects de la construction en temps réel, ce qui permet de documenter le processus de construction et de garantir que les exigences sont respectées.
Avec les procédés AM sur lit de poudre, les caméras peuvent capturer la taille et la température du bain de fusion, ce qui a un impact direct sur la microstructure, les propriétés des matériaux, la finition de surface et les performances globales de la pièce.
Ingénieurs peut ensuite utiliser ces données pour prédire la probabilité de défauts, tels que le gauchissement ou la fissuration, et intervenir dans le processus bien avant que les défauts ne surviennent. Comme ces données sont documentées, cela peut aider à éviter les conditions de processus qui peuvent conduire à ces défauts à l'avenir.
Actuellement, il existe un nombre limité de technologies de surveillance en cours optimisées pour la FA.
Sigma Labs est une entreprise qui propose une solution pour l'assurance qualité en cours de fabrication AM. Son système d'assurance qualité PrintRite3D pour la fabrication additive associe les multi-capteurs et le matériel PrintRite3D SENSORPAK à un module logiciel PrintRite3D INSPECT.
Cette combinaison à multiples facettes, déposée sous le nom de technologie IPQA, permet d'optimiser les conditions du bain de fusion pendant le processus AM, en utilisant les données des capteurs et en établissant des métriques de qualité en cours de processus. À l'aide d'une analyse statistique des données de processus, des rapports sur la qualité des pièces peuvent être générés et utilisés pour valider la répétabilité.
À l'avenir, la société prévoit d'ajouter un module logiciel ANALYTICS, axé sur l'exploitation de l'analyse Big Data. Le module sera en mesure d'extraire des informations significatives et exploitables à partir des données collectées au cours des processus d'impression afin de simplifier davantage le contrôle qualité en cours de processus.
En ce qui concerne les imprimantes 3D elles-mêmes, certaines ont déjà une capacité de surveillance en cours de fabrication intégrée. Par exemple, le fabricant d'imprimantes 3D EOS propose la suite de surveillance EOSTATE. La solution matérielle et logicielle est basée sur quatre modules de surveillance différents, notamment System and Laser, PowderBed, MeltPool et Exposure OT (tomographie optique), qui peuvent capturer des données pertinentes pour la qualité en temps réel.
Avec EOSTATE Exposure OT, EOS prétend être le seul fabricant de systèmes de lit de poudre métallique à offrir à ses clients un outil d'assurance qualité intégrant la tomographie optique.
Ce système de surveillance utilise une caméra qui collecte les émissions lumineuses dans le spectre proche infrarouge, semblable à une caméra thermique. Il peut cartographier entièrement chaque pièce tout au long du processus de construction, couche par couche, quelles que soient sa géométrie et sa taille. Grâce à cette approche, les ingénieurs peuvent élargir la gamme de phénomènes détectables pertinents pour la qualité des pièces de FA.
MTU Aero Engines est une entreprise qui a déjà commencé à utiliser cette solution de surveillance dans ses lignes de production en série pour la FA. pièces de moteur d'avion.
- Fermer la boucle
La détection et la documentation des paramètres pendant le processus d'impression sont cruciales. Mais la capacité d'agir sur ces informations en temps réel - un processus connu sous le nom de contrôle de rétroaction - est ce qui rend cette approche encore plus efficace.
Le contrôle de rétroaction, également connu sous le nom de système en boucle fermée, fait référence à la capacité de détecter les écarts au cours du processus d'impression et d'ajuster automatiquement le système pour les compenser. Maintenir le contrôle du processus de fabrication permet aux fabricants d'obtenir des géométries, des finitions de surface et des propriétés des matériaux cohérentes qui sous-tendent la qualité.
Une entreprise qui a développé un processus de FA contrôlé par rétroaction est Velo3D. Après avoir levé plus de 92 millions de dollars de financement, Velo3D a émergé l'été dernier avec la sortie de sa solution AM en métal de bout en bout. Il comprend l'imprimante 3D Velo3D Sapphire, le logiciel de préparation d'impression Flow et ce que la société appelle la technologie Intelligent Fusion.
Avec ces éléments clés étroitement intégrés les uns aux autres, la technologie permet la simulation de processus thermique, la prédiction des performances d'impression et le traitement de contrôle en boucle fermée. En conséquence, le système Sapphire peut produire des pièces avec des géométries difficiles comme des surplombs avec pratiquement aucune structure de support, de manière répétée et cohérente.
Le logiciel Flow de Velo3D joue un rôle essentiel dans la mise en œuvre de ces avantages. Le logiciel exécute une simulation et une correction de pré-impression, optimisant la conception et ajustant la géométrie et l'orientation de la pièce. Cela aide à préparer le fichier, en équilibrant les éventuelles déformations, afin que la pièce sorte correctement. La métrologie de processus in situ accompagnée d'un contrôle du bain de fusion en boucle fermée fonctionne en tandem avec un logiciel, augmentant finalement le succès de la première partie à plus de 90 %.
Défi 3 :Réduire l'erreur humaine
L'erreur humaine est sans doute le plus grand facteur de risque pour s'assurer qu'une pièce imprimée en 3D répond à toutes les normes requises.
En effet, l'impression 3D nécessite encore plus d'interventions humaines que prévu, de la conception et du retrait des supports au post-traitement et à la vérification manuelle du respect des exigences à chaque étape.
Ce niveau d'intervention humaine augmente inévitablement le risque de compromission de la pièce finale.
Prenons l'exemple de la phase de post-production.
Une fois qu'un build est terminé, il devra être déballé et les différentes pièces qui ont été imprimées dans ce build devront être identifiées et inspectées avant d'être envoyées pour post-traitement.
L'ingénieur de production effectuant cette tâche devra généralement se référer à une feuille de travail imprimée, faisant essentiellement correspondre une image 2D à son équivalent physique et cochant manuellement une liste d'exigences.
Cette approche de l'inspection est non seulement chronophage, mais elle supprime également la visibilité du flux de travail de l'équation.
Pourtant, de nombreuses entreprises adoptant la FA ont du mal à transformer le manuel tâches impliquées dans un processus automatisé plus rapide, plus précis.
Étant donné que la réduction du risque d'erreur humaine est si importante pour garantir la qualité des pièces imprimées en 3D, l'un des moyens d'y parvenir consiste à utiliser des méthodes numériques pour automatiser autant d'étapes d'inspection que possible.
Solution :Mettre en œuvre un logiciel de workflow pour la fabrication additive
Le logiciel de workflow offre une plate-forme numérique centralisée pour aider les équipes de projet et de production à gérer leurs processus de production FA.
Dans le contexte de l'assurance qualité, les logiciels de workflow peuvent souvent fournir le cadre complet pour aider les entreprises à garantir que les exigences de toutes les pièces sont respectées.
De plus, les responsables de production peuvent utiliser un logiciel de workflow pour rendre le processus d'inspection des pièces sans papier et traçable. Au lieu d'inspecter manuellement chaque pièce, la fiche de travail en main, les pièces physiques peuvent être comparées à leurs homologues numériques en 3D.
Par exemple, l'outil de gestion de post-production d'AMFG fournit une visionneuse 3D, qui inclut toutes les données de la pièce, permettant aux utilisateurs d'inspecter une pièce et ses propriétés avec plus de précision.
L'outil permet aux utilisateurs de suivre le rapport entre les pièces réussies et celles qui échouent. Les pièces marquées comme ayant échoué sont automatiquement renvoyées dans la file d'attente de production interne de la plate-forme pour être reproduites. Le plus grand avantage de ceci est de permettre aux utilisateurs de suivre chaque action effectuée sur une pièce - ajoutant la traçabilité et la responsabilité au besoin de gestion de la qualité.
Existe-t-il des normes d'assurance qualité à l'échelle de l'industrie pour la FA ?
Jusqu'à présent, nous avons vu que comprendre comment qualifier les processus, les matériaux et mettre en œuvre des stratégies numériques est essentiel pour garantir que les entreprises peuvent bénéficier de l'impression 3D pour la production.
Les normes à l'échelle de l'industrie joueront un rôle clé dans ce processus. Avec la fabrication traditionnelle, les normes sont déjà monnaie courante, aidant les entreprises à garantir la qualité de leurs produits et à trouver un terrain d'entente. Bien sûr, la fabrication traditionnelle a eu des décennies, voire des siècles, pour développer des normes pertinentes.
L'impression 3D, en revanche, est encore un processus relativement nouveau et de nombreuses normes et certifications sont encore en développement. À l'avenir, l'industrie devra développer des méthodes d'essai, des protocoles et des données de référence pour réduire le coût et le temps de qualification des matériaux, des processus et des pièces de FA.
Heureusement, c'est un domaine qui évolue rapidement. L'année dernière encore, AMST International a publié sa norme F3303, qui décrit les moyens de qualifier les machines et les processus utilisés pour fabriquer des pièces par fusion laser ou par faisceau d'électrons sur lit de poudre. Il a également été noté qu'une norme supplémentaire pour prendre en charge la qualification des pièces, l'assurance qualité et le post-traitement des pièces de fusion sur lit de poudre est déjà en cours.
A côté d'ASTM International, le National Institute of Standards and Technology (NIST) travaille à l'élaboration de normes d'AQ pour l'industrie de la FA. Par exemple, le NIST a lancé le projet AM Part Qualification, axé sur « les mesures, les méthodes et les systèmes métrologiques nécessaires pour créer des mesures post-traitement robustes, développer une solide compréhension des performances mécaniques et qualifier les pièces AM ».
Garder un œil sur la qualité
Assurer la qualité des matériaux et le contrôle des processus sont essentiels pour produire des pièces métalliques de haute qualité constante avec l'impression 3D.
Aussi complexe que cela puisse paraître au premier abord, les fabricants peuvent être rassurés, car des solutions existent pour soutenir le processus d'assurance qualité, renforcées par le développement continu de normes à l'échelle de l'industrie.
Relever ces défis et mettre en œuvre de manière stratégique les bonnes solutions pour votre entreprise vous aidera de manière significative à profiter des avantages de l'impression 3D pour des applications exigeantes et de grande valeur.
impression en 3D
- Les poudres métalliques réfractaires devraient devenir des matières premières pour l'impression 3D
- Poudres métalliques réfractaires VS Technologie d'impression 3D
- Considération de ce que signifie la nouvelle technologie d'impression sur métal pour la FA
- Contrôle qualité en temps réel :quel système est fait pour vous ?
- Structures de support pour l'impression 3D avec du métal — une approche plus simple
- H.C. AMPERPRINT de Starck :un nouvel outil pour l'impression 3D métal
- 6 considérations de conception importantes pour l'impression 3D métal
- Conseils de conception pour l'impression 3D par frittage laser direct de métal
- Vue d'ensemble de la technologie :Quand devriez-vous vraiment opter pour l'impression 3D métal