Temps forts :Composites Convention 2019
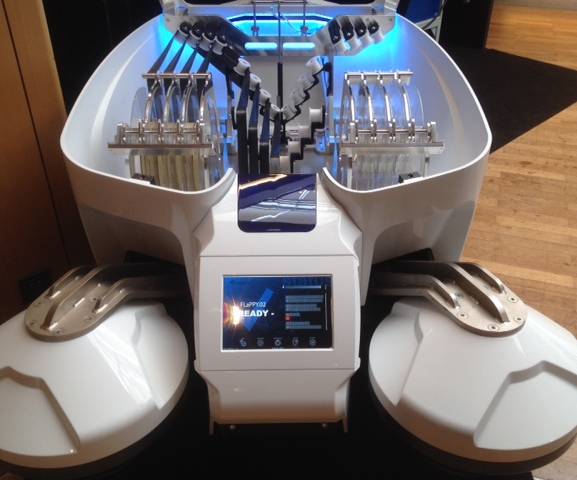
Le prototype de Flappybot (robot de production, de placement et d'assemblage autonome flexible) du DLR est un changement radical par rapport aux machines statiques volumineuses et coûteuses courantes dans la fabrication de grands composants aérospatiaux. Cette unité AFP autonome compacte est conçue pour « passer » directement sur le moule. Origine | DLR
Si l'industrie des composites veut continuer à croître et à améliorer sa compétitivité, elle doit exploiter les opportunités qu'offrent la numérisation et l'automatisation. Deux récentes conférences axées sur l'aérospatiale en Allemagne ont examiné ce que l'avenir de la fabrication de composites pourrait réserver.
Visite de l'usine du futur à Stade
Future Factory for Composites était le thème de la Convention Composites de cette année à Stade, en Allemagne, qui s'est tenue du 12 au 13 juin. Organisé conjointement par CFK Valley e.V. (Stade, Allemagne) et Carbon Composites e.V. (Augsbourg, Allemagne), l'événement a attiré une fréquentation record de près de 450 personnes. Une forte présence aux États-Unis résulte d'une collaboration avec l'Utah Advanced Materials and Manufacturing Initiative (UAMMI, Kaysville, Utah, États-Unis) en tant que réseau partenaire et les États-Unis en tant que pays partenaire.
Dans la présentation d'ouverture, intitulée « Numérisation :transition de la fabrication assistée par ordinateur à l'automatisation assistée par l'homme », le Dr Jan Stüve, directeur du Centre de technologie de production légère au Centre aérospatial allemand (Deutsches Zentrum für Luft- und Raumfahrt ; DLR ; Stade, Allemagne) a offert un avant-goût du programme à venir. Les futures technologies d'usine en cours de développement chez DLR comprennent plusieurs robots coopérants qui travaillent ensemble pour réduire le temps de production et des jumeaux numériques de machines qui permettent l'optimisation des processus. Un autre domaine clé concerne les robots mobiles autonomes pour des scénarios de production flexibles. Ceux-ci incluent le prototype FlappyBot, un compact unité de placement de fibres qui se déplace sur le moule. Stüve a mis en garde contre les dangers potentiels d'une automatisation excessive et a expliqué comment la numérisation devrait réimpliquer les humains dans le processus de fabrication.
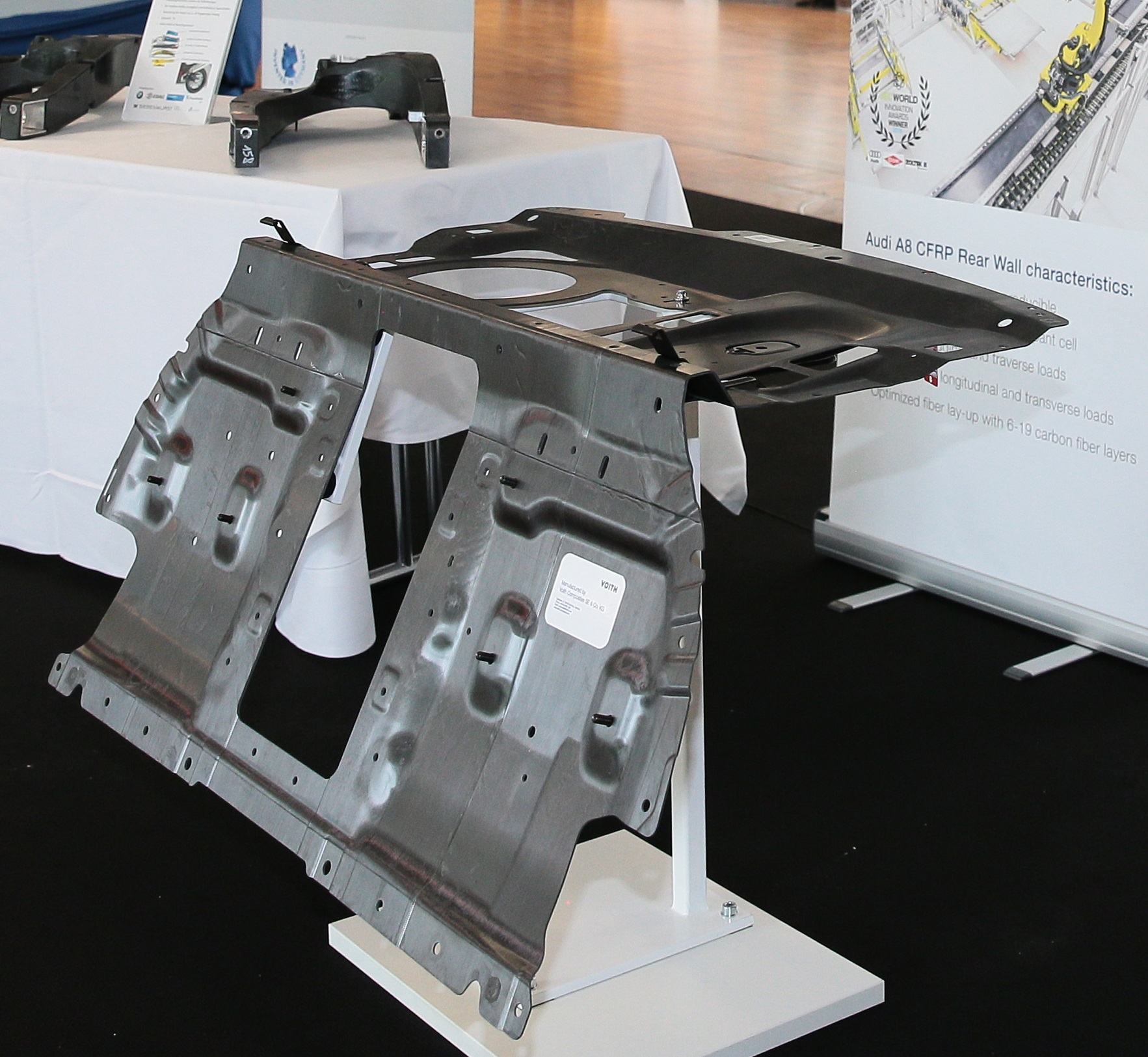
La paroi arrière de l'Audi A8 CFRP, le plus gros composant de l'habitacle, est fabriquée par Voith Composites dans le cadre d'un processus hautement automatisé permettant des volumes de production de 65 000 composants par an. Origine | CFK Vallée
Dans un deuxième discours, « Fabrication rapide et composites thermoplastiques - Tendances et technologies », le Dr Robert G. Bryant, ingénieur principal en matériaux au NASA Langley Research Center (Hampton, Virginie, États-Unis), a emmené les délégués loin des confins de la usine terrestre vers la construction dans l'espace. Une présence humaine à long terme dans l'espace nécessitera un abri et des plates-formes dans un premier temps. Le développement de fusées toujours plus grosses pour placer des structures de plus en plus complexes hors de la planète n'est pas économiquement viable. Les solutions nécessitent une fabrication à proximité ou sur site. L'utilisation d'un processus avancé de placement de bande (ATP) sans outil permettant la consolidation in situ de pièces composites thermoplastiques pourrait être la réponse. Dans cette nouvelle technique, deux robots ATP travaillent en vis-à-vis, l'un pour déposer le ruban thermoplastique préimprégné, l'autre faisant office d'outil. La fabrication sans outil pourrait réduire le coût de la fabrication aérospatiale, améliorer l'économie de l'exploration spatiale et profiter à d'autres secteurs du marché (en savoir plus dans "General Atomics Aeronautical développant un processus de composites thermoplastiques sans outil").
Durabilité
Les progrès de la fabrication doivent également s'accompagner de réductions de l'impact environnemental. Dans ce sens, lors de la session suivante, Jörg Spitzner, fondateur de Spitzner Engineers GmbH (Finkenwerder, Allemagne), a fait valoir que pour atteindre les objectifs climatiques, des technologies d'émissions négatives sont nécessaires. L'entreprise de Spitzner affirme que son concept d'éolienne breveté Blancair améliore à la fois l'efficacité de la turbine et élimine le CO2 de l'atmosphère. L'air est aspiré dans un module de filtrage monté sur la nacelle, où le CO2 est séparé pour le stockage et le recyclage dans la production de carburants synthétiques et d'autres applications. L'air purifié est libéré par des ouvertures dans les extrémités des pales du rotor. Une vidéo expliquant le concept est disponible sur le site Internet de Blancair.
Les organisateurs de la session ont également présenté un concept d'évaluation intelligente de l'éco-efficacité dans la production de composites (DLR) et des préimprégnés durcis à température ambiante hors autoclave avec une capacité de feu, de fumée et de toxicité (FST) (TCR Composites ; Ogden, Utah, États-Unis).
Autonomisation par la simulation
Pour le reste de la première journée de la conférence, l'attention s'est tournée vers la simulation.
Le Dr Lars Herbeck, directeur de la technologie chez Voith Composites (Garching, Allemagne), a expliqué comment la machine de placement automatique de fibres (AFP) de Voith Roving Applicator simplifie la chaîne de processus, permettant un processus de préformage automatisé efficace avec des temps de cycle réduits. Il a décrit la simulation structurelle et de processus effectuée pour la ligne de fabrication automatisée capable de produire 65 000 composants par an pour la paroi arrière arrière en plastique renforcé de fibres de carbone (CFRP) de l'Audi A8.
Mark Bludszuweit de MET Motoren- und Energietechnik GmbH (Rostock, Allemagne) a expliqué comment la simulation offre un aperçu de la meilleure façon de charger des pièces dans un autoclave, permettant une optimisation du processus de durcissement et une plus grande productivité. Un jumeau numérique développé pour le plus grand autoclave des installations du DLR à Stade peut fonctionner en parallèle avec le processus réel, ou plus rapidement pour offrir des prédictions du comportement des pièces.
D'autres sujets de développement de processus virtuels ont porté sur la modélisation des processus SMC (Groupe ESI ; Chartres-de-Bretagne, France) et la simulation de processus de panneaux sandwich pour comprendre les problèmes d'écrasement du noyau et de plissage du préimprégné dans l'autoclave (Airbus Helicopters ; Marignane, France).
En ce qui concerne la modélisation de la sécurité virtuelle, Jochen Rühl de Reichenbacher Hamuel GmbH (Dörfles-Esbach, Allemagne), qui fait partie de Scherdel Gruppe, a expliqué comment une approche basée sur la simulation pour gérer la poussière et les particules produites lors de l'usinage de pièces en PRFC a apporté des avantages à des clients tels que comme Airbus et Premium Aerotec (Augsbourg, Allemagne). Les simulations d'usinage et la visualisation des distributions de particules aident les fabricants à se conformer aux réglementations strictes en matière de santé et de sécurité et améliorent les résultats d'usinage, ainsi que les temps d'arrêt et la maintenance des machines, ce qui se traduit finalement par un coût par pièce inférieur.
La session de simulation a également présenté un projet parrainé par Boeing sur la modélisation des coûts virtuels de la fabrication de composites, prenant en compte les interactions complexes entre la conception, la production et la finance pour identifier les inducteurs de coûts (Massachusetts Institute of Technology ; Cambridge, Mass., États-Unis), et un concept de planification d'usine numérique basé sur la modélisation simulative des chaînes de valeur optimales des composites (Fraunhofer IGCV ; Augsbourg, Allemagne).
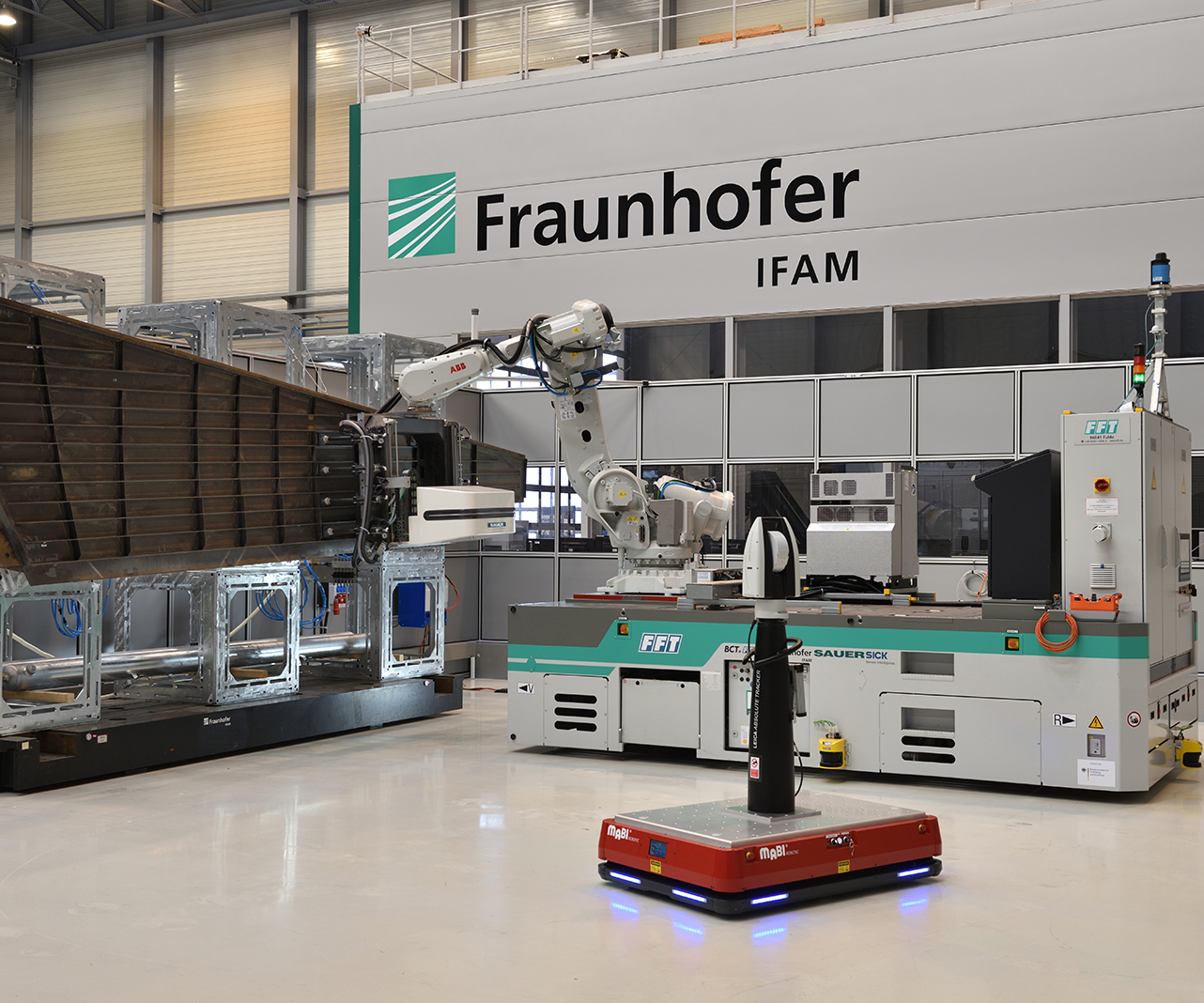
Le concept d'usinage mobile MBFast18 est composé d'un véhicule guidé automatisé, d'un robot et d'une machine CNC portable et offre une productivité accrue dans la fabrication de grandes pièces d'avion CFRP. Origine | Fraunhofer IFAM
Lauréats
Cette année, deux projets se sont partagés le CFK Valley Innovation Award et le prix de 7 500 €.
La première place (et 4 500 €) a été attribuée au projet de systèmes robotiques mobiles MBFast18, qui a développé un système d'usinage CNC mobile basé sur un véhicule à guidage automatisé (AGV) pour les pièces d'avions CFRP de grande taille.
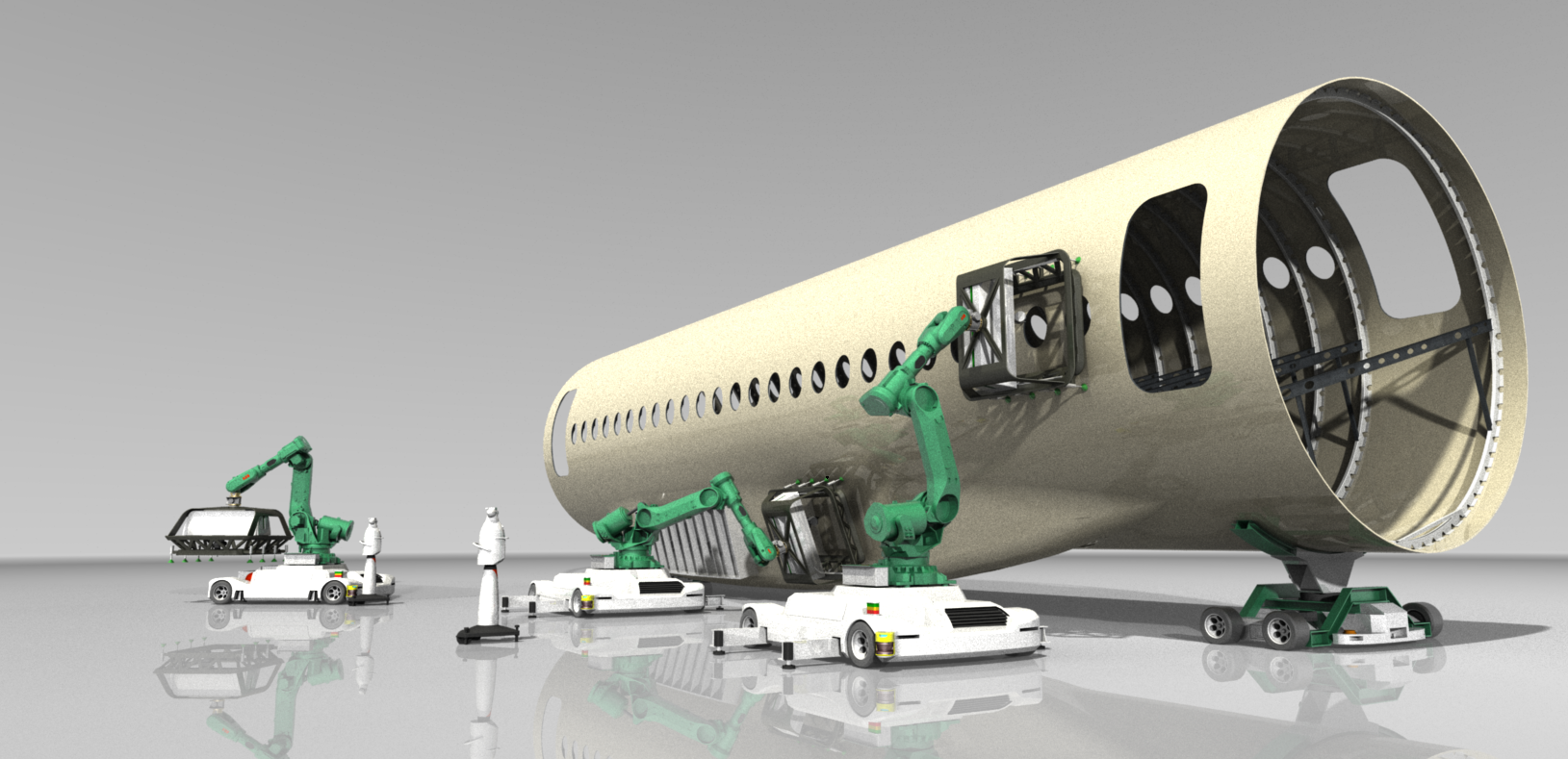
Origine | Fraunhofer IFAM
Par rapport aux systèmes d'usinage statiques coûteux d'aujourd'hui pour les grandes structures d'avions, les systèmes robotiques mobiles plus petits permettent une fabrication flexible et une productivité plus élevée.
Le système MBFast18 utilise une plate-forme autonome de 4,6 mètres de long construite par FFT Produktionssysteme GmbH &Co. KG (Fulda, Allemagne), des capteurs de navigation et de sécurité fournis par SICK AG (Waldkirch, Allemagne) et une machine CNC à 5 axes de SAUER /DMG MORI (Suhl et Bielefeld, Allemagne). Un laser tracker mobile développé par l'Institut Fraunhofer pour la technologie de fabrication et les matériaux avancés (IFAM; Stade, Allemagne) positionne le robot avec précision. L'unité de perçage, avec un espace de travail allant jusqu'à 0,5 mètre carré, est fixée au composant à l'aide de pinces à vide; les positions de perçage sont calculées et transmises à la machine à l'aide d'un logiciel développé par BCT GmbH (Dortmund, Allemagne). Ce concept est également applicable aux opérations de manutention et d'assemblage et à d'autres industries telles que l'énergie éolienne et ferroviaire.
Regardez une vidéo sur le projet MBFast18 :
La deuxième place est revenue à la start-up Hyconnect GmbH (Hambourg, Allemagne) pour sa technologie d'assemblage métal-composite FAUSST. La société cible initialement le secteur de la construction navale, où l'assemblage des composites au métal est un obstacle majeur à l'adoption plus répandue des composites. La solution FAUSST utilise un tissu hybride composé de fibres de verre et de métal tricotées en chaîne qui permet un assemblage mécanique solide des métaux et des composites. Le côté fibre métallique est joint à un profilé en acier qui peut être soudé à des structures métalliques, et l'autre côté est laminé au composant composite. On dit que la technologie brevetée accélère considérablement le processus de conception et de collage. Les premières applications prototypes sont actuellement en cours de test.
Regardez une introduction au processus d'adhésion FAUSST :
Activation grâce à l'automatisation
Le deuxième jour, le projet primé MBFast18 a été exploré plus en détail dans les présentations de Christoph Brillinger, chef de projet chez Fraunhofer IFAM, et du Dr Gregor Graßl de FFT, qui ont discuté des défis du développement de systèmes intelligents de contrôle de processus et d'usine pour les opérations multi-robots. . Jerome Berg, ingénieur du personnel chez Northrop Grumman Innovation Systems (Clearfield, Utah, États-Unis), a décrit la fabrication automatisée de longerons d'avions Airbus dans les installations de l'entreprise en Utah à l'aide d'un processus AFP développé en interne, et Uwe Lang d'Evonik Resource Efficiency GmbH (Darmstadt , Allemagne) a introduit la « Sandwich Technology 4.0 », une technologie de fabrication automatisée pour des taux de production élevés qui utilise le matériau d'âme en mousse ROHACELL de l'entreprise. Un processus de préformage hautement automatisé pour une trappe de train d'atterrissage avant d'avion a été démontré en collaboration avec le DLR et le centre technologique d'Airbus CTC GmbH (Stade, Allemagne).
Regardez une vidéo du processus de préformage :
Faisant un voyage dans la réalité virtuelle, Felix Hünecke, responsable du développement commercial chez ABSOLUTE Reality GmbH (Hambourg, Allemagne), a montré comment créer, éditer et compléter des modèles 3D de bâtiments avec des images, des documents et des vidéos pour créer des environnements virtuels qui peuvent être vu de n'importe où dans le monde. La société a réalisé une visite en 3D d'une salle de production du DLR à Stade.
Promenez-vous dans le hall de production du DLR :
Felix Schreiber, PDG du groupe ARK (Aix-la-Chapelle, Allemagne), a discuté des avantages en termes de processus et de coûts des données de machine structurées dans une ligne de production automatisée de moulage par transfert de résine (RTM), tandis que Sascha Backhaus de CTC GmbH a discuté de l'automatisation modulaire dans la fabrication de composites et de l'Hybr -Le projet iT, qui développe des équipes où les humains et les robots travaillent ensemble avec des systèmes d'assistance basés sur des logiciels.
Aucun événement sur la future usine ne pouvait négliger le sujet de l'intelligence artificielle (IA), et Amir Ben-Assa, CMO de Plataine (Waltham, Mass., États-Unis) a discuté des opportunités et des défis de la mise en œuvre de l'IA dans la fabrication de composites. Il a présenté des applications pratiques de l'IA, des alertes (par exemple, des retards de production ou des problèmes de qualité) aux recommandations (par exemple, une sélection de matériaux optimisée). Les assistants numériques basés sur l'IA sur Google Glass pourraient être une autre possibilité, offrant une interaction utilisateur « mains libres » avec l'IA sur le terrain de production et une présentation audio et visuelle des alertes en temps réel.
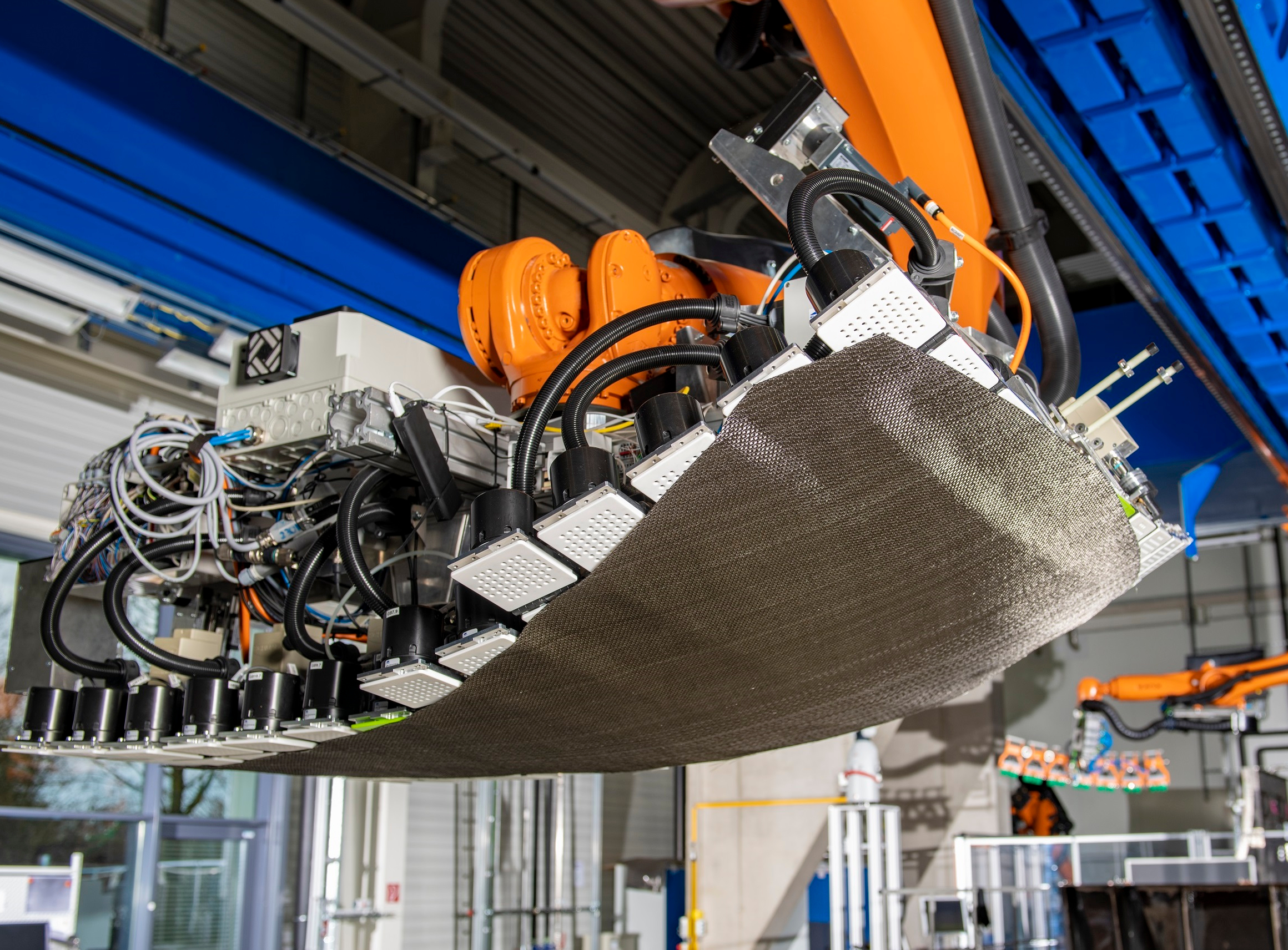
La cellule robotisée multifonctionnelle de ZLP Augsburg a été conçue pour permettre le développement de processus intégrés pour la fabrication de composants composites de grande taille à l'échelle industrielle. Origine | DLR
Autres sujets inclus :
- Détection par fibre optique pour la surveillance intelligente des processus dans les grandes structures composites (MT Aerospace AG ; Augsbourg, Allemagne );
- Un système de contrôle intelligent pour la fabrication automatisée de composites (National Composites Centre, Bristol, Royaume-Uni );
- Un système de contrôle qualité basé sur un modèle pour le thermoformage de petits composants (Faserinstitut Bremen e.V. ; FIBRE, Brême, Allemagne );
- Procédé de moulage par compression de thermoplastiques discontinus renforcés de fibres pour les applications aéronautiques, basé sur une automatisation flexible et adaptable à de grandes pièces (ACT Aerospace ; Gunnison, Utah, États-Unis );
- Un processus RTM isotherme offrant des temps de cycle réduits pour la production de pièces CFRP en grand volume (Airbus Helicopters)
- Production à grande échelle de profilés thermoplastiques complexes en fibre de carbone hautes performances pour jambes de force, tuyaux et arbres de transmission à l'aide de préformes de ruban presque en forme de filet et de formage par injection (herone GmbH ; Dresde, Allemagne). Apprenez-en plus sur Herone et ce procédé dans « Formage par injection pour des structures thermoplastiques unitisées hautes performances ».
10 ans de progrès à Augsbourg
Lors d'un événement séparé, le 5e colloque du DLR sur la technologie de production le 15 mai a vu près de 200 invités se rassembler dans son Centre de technologie de production légère (Zentrum für Leichtbauproduktionstechnologie, ZLP) à Augsbourg. L'événement a célébré le 10e anniversaire de ZLP à Augsbourg, où environ 60 employés se concentrent aujourd'hui sur l'automatisation et la numérisation de la production de composites.
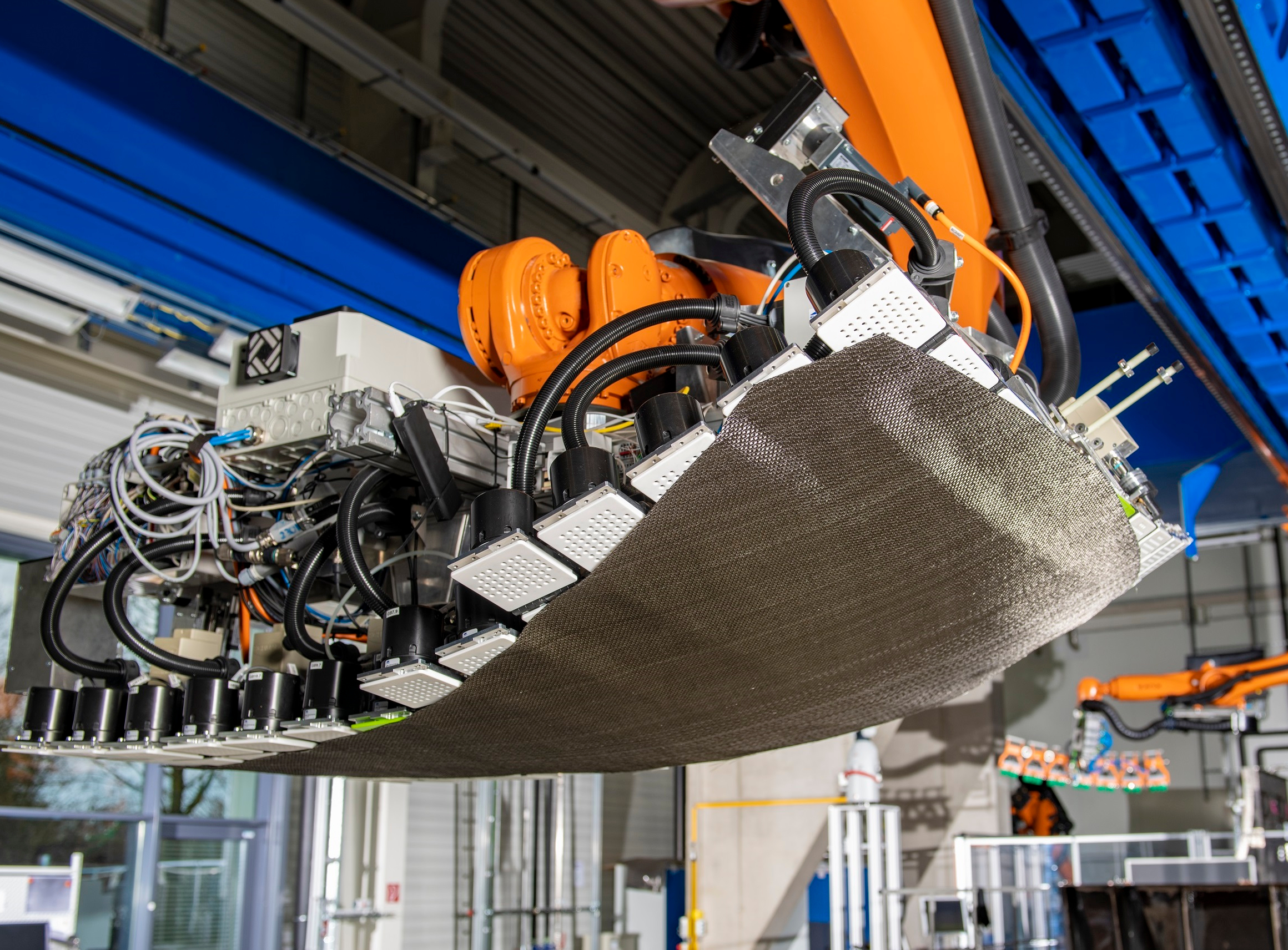
Une pince robotisée pour le drapage automatisé, faisant partie du processus de fabrication intégré de ZLP Augsburg pour les composants structurels à grande échelle. Origine | DLR
La journée a débuté par deux présentations de l'Université de la Colombie-Britannique (UBC ; Vancouver, Canada), qui a entamé une coopération avec le DLR en 2016. Le professeur Dr. Anoush Poursartip, co-directeur de l'initiative Digital Learning Factory de l'UBC, a présenté le concept d'une usine d'apprentissage des composites inspirée des hôpitaux universitaires de médecine. L'usine d'apprentissage des composites, qui sera située sur le campus Okanagan de l'UBC, sera conçue pour intégrer la recherche et l'éducation aux activités industrielles. Un jumeau numérique hébergé à l'UBC Vancouver combinera les données de l'usine physique avec une simulation pour optimiser les processus de production de composites aérospatiaux. Ensuite, le professeur Homayoun Najjaran de l'UBC et Marian Körber du DLR ont discuté de l'optimisation des processus de fabrication complexes dans un environnement virtuel et de la manière dont l'expertise de l'UBC dans les techniques d'apprentissage automatique et l'intelligence artificielle est utilisée pour réduire le temps et le coût du développement de systèmes robotiques au DLR. . Une méthode d'apprentissage en profondeur a été utilisée pour former la pince robotique de ZLP pour le drapage automatisé, un élément clé de la chaîne de processus automatisée de l'usine d'Augsbourg pour la fabrication de grandes pièces en PRFC. Le préhenseur, qui comprend 127 modules d'aspiration avec une force d'aspiration variable, reconnaît et prélève le matériau coupé; les modules prennent la géométrie requise pour le draper en position dans le moule.
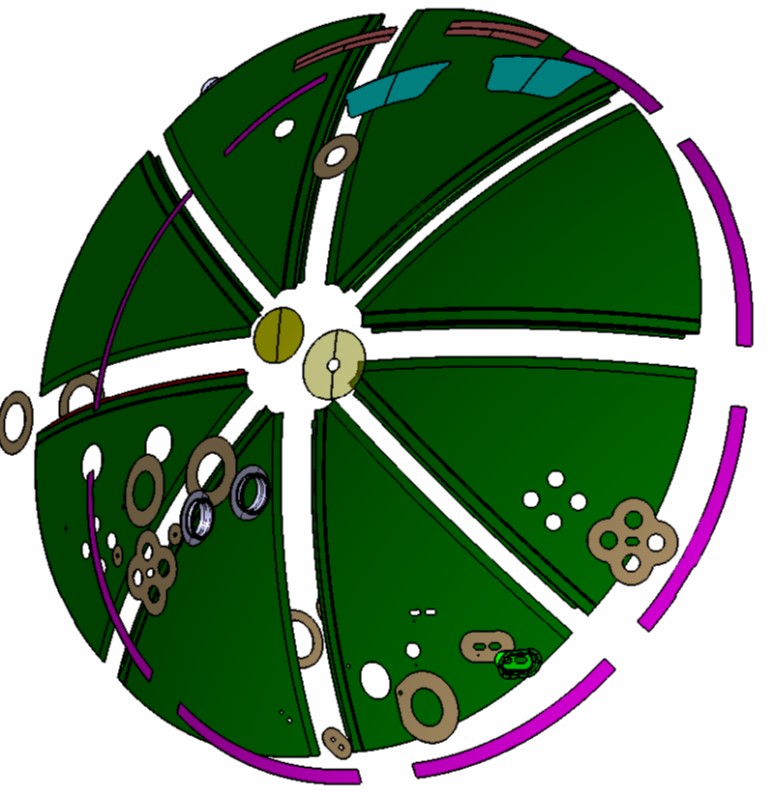
Les composants composites thermoplastiques pour la conception de la cloison à pression arrière de Premium Aerotec sont assemblés à l'aide d'une technique de soudage par résistance développée à ZLP Augsburg. Origine | Premium Aerotec
Les technologies thermoplastiques sont un autre objectif de ZLP Augsburg. Ralph Männich et Alexander Sänger de Premium Aerotec GmbH ont présenté un projet visant à développer la première cloison étanche arrière thermoplastique (RPB) au monde pour les avions monocouloirs. La société collabore avec ZLP Augsburg, Toray Advanced Composites et l'Institute for Composite Materials (IVW) sur une conception composée de huit segments CFRP avec des longerons intégrés assemblés à l'aide d'une technologie de soudage par résistance développée par ZLP. Des processus automatisés avec des temps de cycle courts permettent une production en grand volume. L'achèvement de la technologie (jusqu'au TRL 6) est prévu pour 2020 et la mise en œuvre est prévue pour 2021/2022. Au salon du Bourget en juin, Premium Aerotec a présenté un démonstrateur 1:1 pour un avion de la série Airbus A320. Par rapport aux cloisons étanches A320 actuelles constituées de composants en aluminium rivetés, la pièce thermoplastique offrirait les mêmes propriétés mécaniques avec un gain de poids de 10 à 15 % et une réduction de 50 % du temps de production. Dans l'exposé suivant, le Dr Stefan Jarka et Manuel Endraß du DLR ont poursuivi le thème du soudage thermoplastique, approfondissant les capacités d'assemblage et de CND de ZLP Augsburg, et son rôle dans le projet RPB.
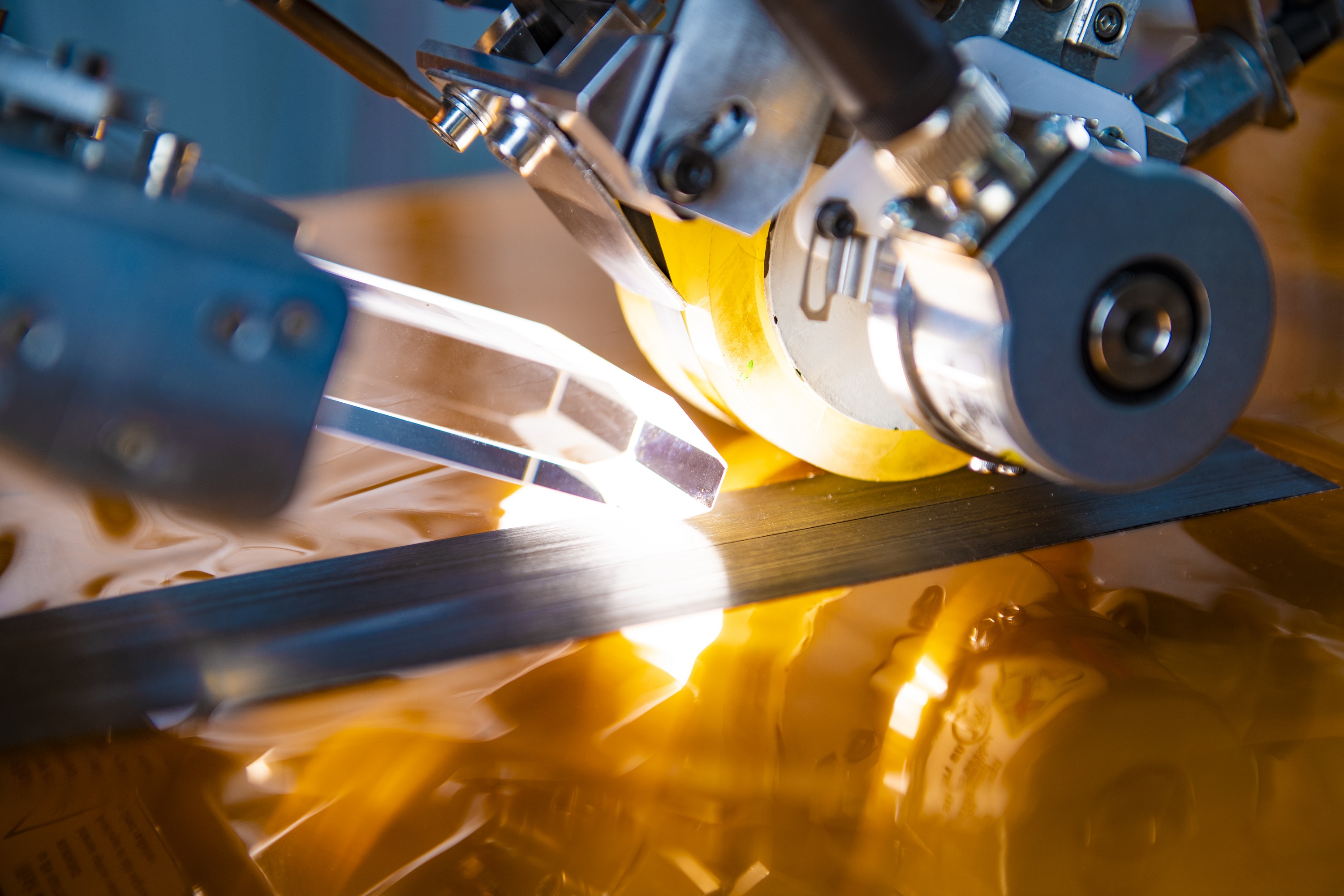
ZLP Augsburg étudie l'AFP in situ à base de lampe flash de composites thermoplastiques, une solution d'énergie pulsée qui élimine les enceintes de sécurité requises pour l'AFP à base de laser. Origine | DLR
Les composites thermoplastiques offrent également des opportunités dans les applications spatiales. Les présentations de Ralf Hartmond, MT Aerospace AG et Lars Brandt, chef de projet pour les applications spatiales chez DLR, ont décrit le développement d'un étage supérieur en thermoplastique renforcé de fibres de carbone pour la prochaine génération d'Ariane lance-roquettes. Brandt a détaillé les travaux du DLR sur le criblage des matériaux pour le réservoir d'hydrogène liquide (LH2 ) réservoir - où la fibre de carbone PEEK et le PAEK à bas point de fusion (LM) sont prometteurs - et le développement d'un procédé AFP composite thermoplastique in-situ pour permettre une approche de fabrication additive allégée. ZLP compare un nouveau procédé AFP in-situ assisté par lampe flash à l'AFP assistée par laser traditionnelle.
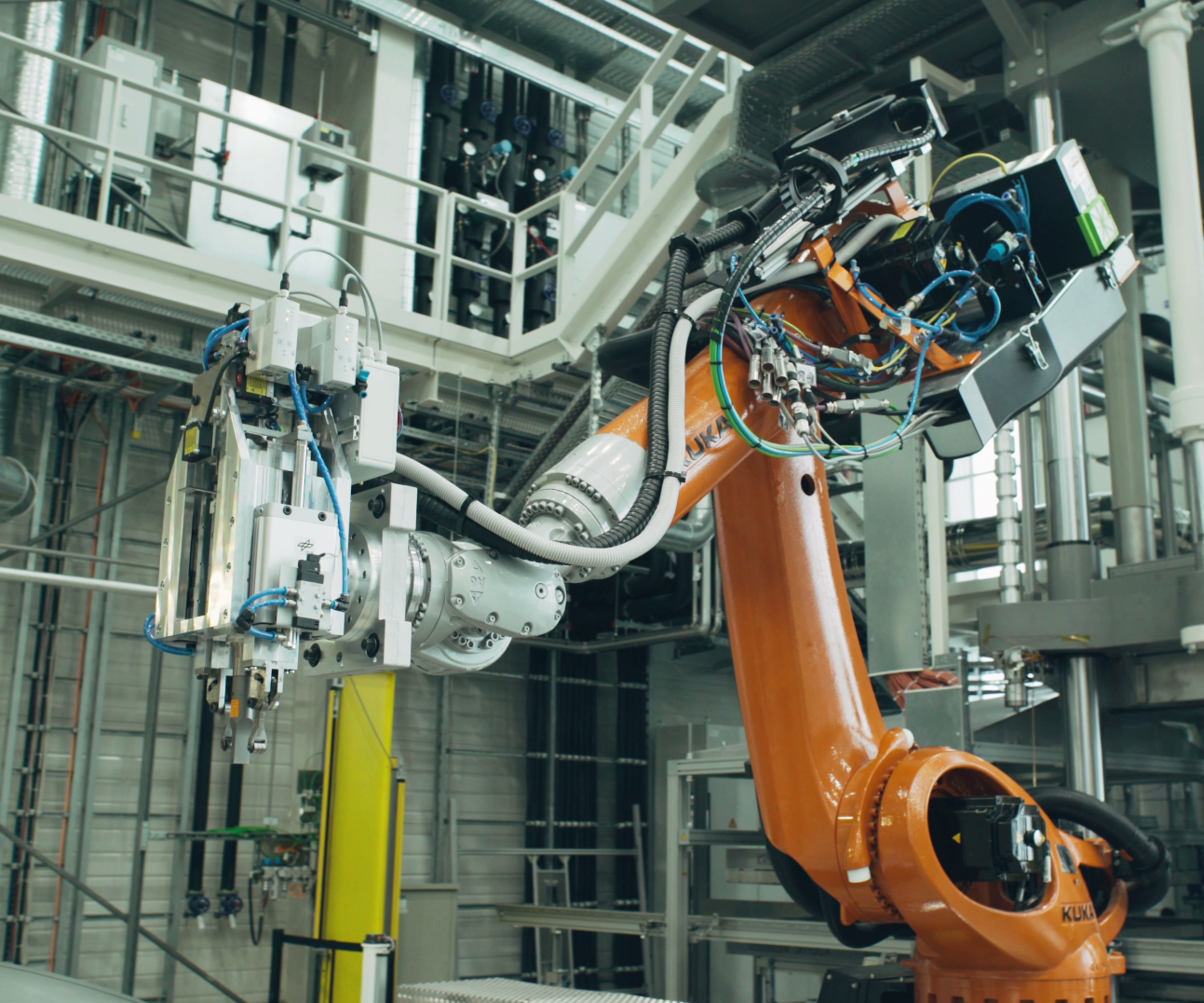
Les technologies d'assemblage seront la clé du succès de l'introduction des composites thermoplastiques dans les futures applications aérospatiales. ZLP à Augsbourg a développé un système de soudage par ultrasons continu basé sur un robot, composé d'un effecteur final monté sur un robot KUKA QUANTEC KR210 sur une piste linéaire de 7 m. Cela a été prouvé sur des composants comprenant un panneau de fuselage renforcé et une cloison de pression arrière. Origine | DLR
La journée s'est terminée par une allocution stimulante du professeur Michael Kupke, directeur de ZLP Augsburg, intitulée « Numérisation et production flexible ». Il a demandé si l'essor de l'économie des plateformes numériques présente des opportunités ou des risques pour les fabricants de composites, et a souligné que l'informatique devient une compétence clé et devrait être traitée comme un avantage concurrentiel à valeur ajoutée plutôt que comme un centre de coûts. Il a également déclaré qu'il y avait un changement de paradigme en cours, passant de la planification détaillée à l'auto-organisation (production allégée) et à l'automatisation combinée à la numérisation. L'IA, dit-il, rend possible une production autonome et flexible. Cependant, a conclu Kupke, il est essentiel de valoriser et d'intégrer les compétences humaines, qui sont vitales pour la prise de décision et l'amélioration des processus.
Résine
- 4 questions brûlantes pour la fabrication additive en 2019
- 25 jalons clés de la fabrication additive en 2019
- 3 prévisions de fabrication pour 2019
- En savoir plus sur JEC World 2019
- Aperçu du JEC World 2019 :SABIC
- Personnes dans les composites – janvier 2019
- La technologie d'automatisation met en avant la sécurité et la fabrication flexible
- 2019 :prévisions de fabrication
- Meilleures pratiques de marketing de fabrication pour 2019