Suppression des barrières pour alléger les navires avec des composites
Les composites de polymère renforcé de fibre de verre et de carbone (GFRP et CFRP) sont utilisés depuis des décennies pour construire des navires, y compris de nombreux chasseurs de mines de 40 à 60 mètres et des navires encore plus gros, notamment la Corvette de classe Visby de 72 mètres de long de la marine suédoise et le voilier de 75 mètres de long Mirabella V . Le yacht à moteur de 141 mètres Swift 141 (renommé Yas ) est une frégate hollandaise en acier reconstruite à l'aide de GFRP/CFRP dans des semelles sous le pont et une superstructure à trois ponts (voir « De la frégate au gigayacht de luxe »), y compris un joint de pont composite-acier.
Et pourtant, les composites sont rarement utilisés dans la construction navale. Cela est principalement dû à la réglementation sur la sécurité de la vie en mer (SOLAS) publiée par l'Organisation maritime internationale (OMI, Londres, Royaume-Uni), qui exigeait que les navires commerciaux soient construits en acier jusqu'à la MSC/Circ. 1002 a été délivré en 2002 autorisant des conceptions alternatives.
« Le règlement impose la réalisation d'une analyse de risque démontrant que la conception et la construction alternatives sont équivalentes à l'acier », explique Stéphane Paboeuf, responsable de la section Matériaux composites de la société de classification Bureau Veritas (BV, Nantes, France). "Ce processus est long, coûteux et la décision finale pourrait encore être négative." Ainsi, bien que les composites offrent de nombreux avantages pour la construction navale, les défis de la sécurité incendie et de la réglementation ont posé des barrières à l'utilisation.
Pendant ce temps, les propriétaires de navires, les exploitants et les constructeurs recherchent des solutions pour une durabilité améliorée, notamment un poids plus léger pour réduire la consommation de carburant, les émissions de gaz à effet de serre et le tirant d'eau des navires, ce dernier pour les voies navigables peu profondes. La résistance à la corrosion inhérente des composites pour réduire l'entretien est également attrayante.
En 2017, l'OMI a publié MSC.1/Circ., un nouvel ensemble de directives pour l'utilisation de composites FRP dans les navires commerciaux. À l'approche de l'évaluation de ces directives par l'OMI en 2021, une quantité incroyable d'activités est en cours. Deux consortiums européens, FIBRESHIP et RAMSSES, soutenus par le réseau européen de 378 membres pour les applications légères en mer (E-LASS), mènent cette vague de projets de démonstration, qui comprend des ponts composites, des gouvernails, des coques, des cabines modulaires et des superstructures, patch réparations d'assemblages soudés en acier et composite-acier. Ensemble, ils visent à surmonter les obstacles à la construction de navires composites légers en démontrant non seulement la résistance au feu et les performances structurelles des grandes structures et des navires entiers, mais également en développant de nouvelles voies pour les méthodes de certification et de production, de nouvelles technologies d'assemblage et des outils de conception. Ils partagent également des informations via des ateliers permanents, des référentiels de connaissances et des bases de données de matériaux/conception. Un nouveau marché s'ouvre peut-être pour les composites marins, mais quelles solutions cela nécessitera-t-il ?
FIBRESHIP et RAMSSES
FIBRESHIP et RAMSSES ont été lancés en juin 2017, financés par le programme Horizon 2020 de l'Union européenne. FIBRESHIP compte 18 membres et fonctionnera jusqu'en mai 2020, tandis que RAMSSES compte 36 membres et se termine en mai 2021. Les deux comprennent des entreprises de toute la chaîne d'approvisionnement couvrant des centres de R&D, des universités, des fournisseurs de matériaux et de technologies, des fabricants de pièces, des cabinets d'architecture et d'ingénierie de navires, chantiers navals, armateurs et sociétés de classification. Ces derniers sont chargés d'élaborer des règles spécifiques pour les constructions de navires individuels sur la base des directives générales de l'OMI. Ils sont autorisés par les États du pavillon (chaque navire porte le pavillon d'un pays) à auditer la construction des navires et à s'assurer que ces règles sont respectées. "Il est important que toutes les parties prenantes et les utilisateurs finaux soient impliqués", déclare Alfonso Jurado, responsable de la R&D chez Tecnicas y Servicios de Ingeniería (TSI, Madrid, Espagne) et coordinateur du projet FIBRESHIP.
« L'objectif principal de FIBRESHIP est de développer des capacités de conception et de production pour les grands navires (plus de 50 mètres de long) avec moins de poids », poursuit Jurado. « C'est aussi la principale motivation de mon entreprise. TSI conçoit la structure composite d'un navire de recherche sur la pêche (FRV) de 85 mètres de longueur hors tout (LOA), qui servira de démonstrateur et, jusqu'à présent, atteint une réduction de près de 70 % du poids structurel par rapport au navire de référence en acier. "C'est incroyable, offrant une réelle possibilité d'aide pour le secteur du transport maritime", dit-il. Une section de 20 tonnes de ce FRV, mesurant 11 x 11 x 8,6 mètres (voir l'image d'ouverture), a été construite par le chantier naval partenaire iXblue à La Ciotat, en France, et exposée au deuxième atelier public de FIBRESHIP en juin 2019 (voir l'article avec vidéo du démonstrateur en cours de fabrication).
Jurado explique que le FRV est le premier des trois cas de navires composites généraux que FIBRESHIP est en train de développer. Les deux suivants sont des porte-conteneurs de 260 mètres de longueur totale et un ROPAX de 204 mètres, ce dernier combinant la capacité de chargement d'un navire roulier et les installations de passagers d'un ferry. « Le FRV a été choisi comme démonstrateur car il est plus petit avec une structure marine plus conventionnelle, et donc le plus réalisable à construire dans un avenir proche », dit-il. « Les armateurs ont également montré un réel intérêt pour un tel navire. » Parallèlement, RAMSSES a 13 démonstrateurs en cours, dont 10 en composite, et poursuit également un navire tout composite.
Jurado note que les entreprises participant à ces projets voient le potentiel de ces nouvelles conceptions et de ces nouveaux produits légers à offrir un avantage concurrentiel à leurs entreprises ainsi qu'à l'industrie maritime de chaque pays. Mais les progrès ne seront pas garantis par les seuls grands manifestants. « Nous devons également avoir le soutien des autorités de régulation », ajoute-t-il. « Une première étape consiste à engager l'OMI et à adapter la réglementation SOLAS actuelle aux nouvelles exigences et demandes de l'industrie du transport maritime. Sans cela, nous ne pouvons pas avancer car les compagnies d'assurance ne souscriront pas les navires composites renforcés de fibres s'ils ne remplissent pas les exigences minimales et la certification de sécurité, par exemple. »
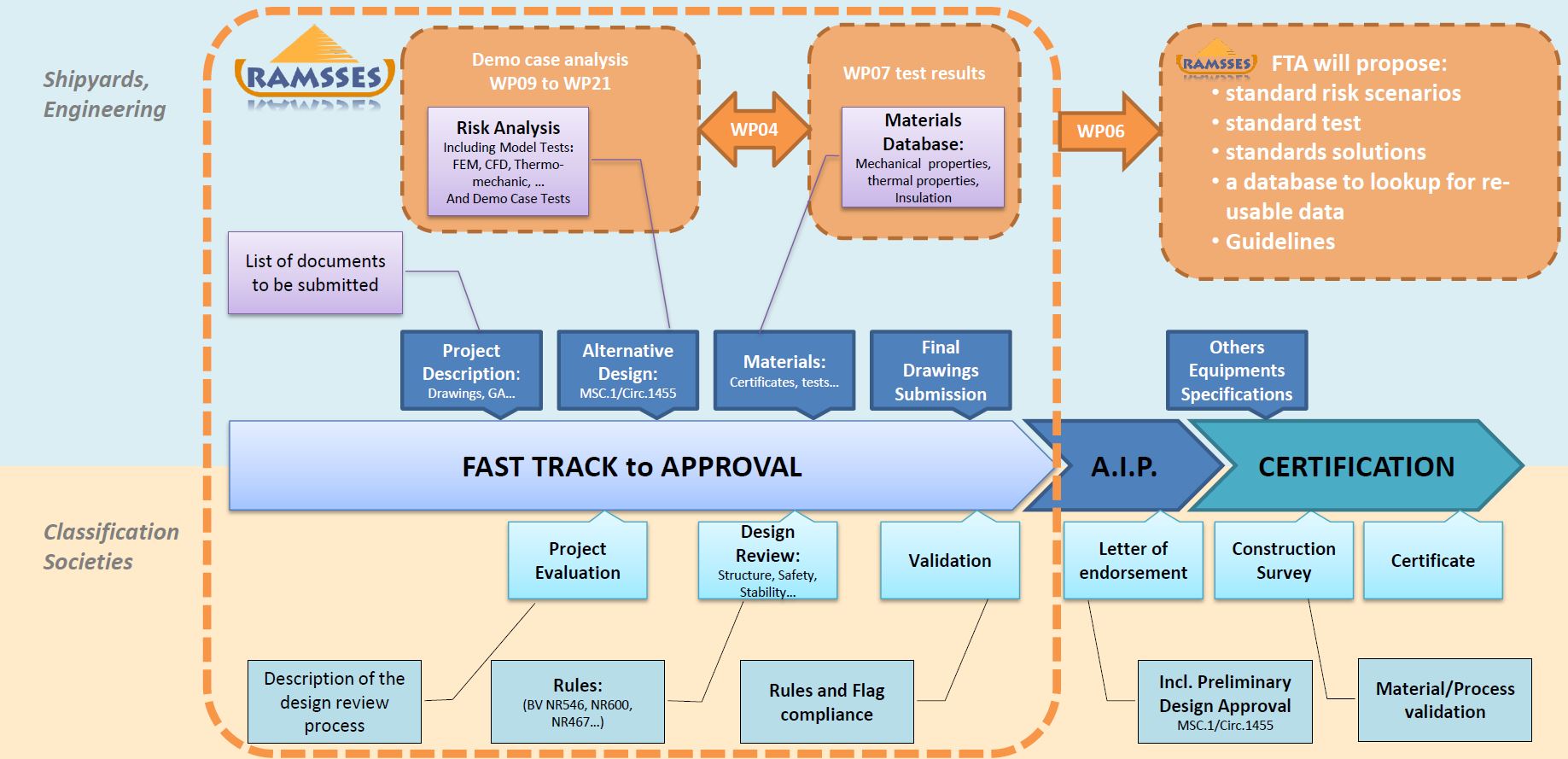
Proposition d'approche Fast Track to Approval (FTA) pour la certification des composites dans les navires commerciaux en cours de développement dans le cadre du projet RAMSSES, telle que présentée lors du séminaire E-LASS de juin 2019 (Vigo, Espagne). Origine | RAMSSES et Stéphane Paboeuf, Bureau Veritas
« FIBRESHIP poursuit une approche à long terme en développant de nouvelles règles, tandis que RAMSSES développe une approche à court terme en utilisant les règles et méthodes existantes », explique Paboeuf chez BV, qui est la seule société de classification partenaire de RAMSSES, et l'un des trois en FIBRESHIP aux côtés de Lloyd's Register (Londres, Royaume-Uni) et RINA (Gênes, Italie). « Dans RAMSSES, nous développons une procédure Fast Track to Approval (FTA) basée sur la réutilisation des données du projet pour standardiser les tests et fournir des conseils pour la conception et l'approbation. Cette procédure doit être simple et facilement lisible par les chantiers navals, les architectes navals et les fournisseurs. L'accélération par rapport au processus actuel viendra grâce aux supports développés dans les projets de démonstration RAMSSES, notamment :
- une base de données de solutions pré-approuvées et de résultats de tests de matériaux pour éviter les tests répétitifs,
- scénarios de risque d'incendie couvrant une gamme d'applications similaires pour limiter le nombre et l'étendue des évaluations des risques, et
- outils d'analyse et de modélisation, y compris des modèles numériques ou statistiques qui pourraient remplacer les tests physiques à l'avenir.
« Chez FIBRESHIP, nous travaillons avec Lloyd's Register et RINA pour développer un ensemble de règles prescriptives spécifiquement pour les grands navires construits avec des composites », poursuit Paboeuf. « Pour les performances structurelles, nous définissons de nouveaux coefficients de sécurité pour les charges locales et globales. RAMSSES et FIBRESHIP proposent également de remplacer les niveaux actuels de classement au feu tels que A60, B30 et B15 par une nouvelle convention REIxx, où R spécifie la résistance au feu (capacité portante au feu), E désigne l'intégrité (la prévention de la propagation des fumées et des flammes). ) et I définit l'isolation au feu. « L'objectif est de mieux aligner les classements au feu des structures avec les matériaux composites utilisés », explique Paboeuf.
En outre, les deux projets traitent également des évaluations des risques liés à la propagation des flammes, à la production de fumée et au risque d'incendie dans l'espace d'origine, mais aussi au niveau de la sécurité globale des navires. « Pour les performances au feu, nous développons une approche d'équivalence locale, qui traite de la sécurité incendie au niveau local en fonction des classements au feu des cloisons et autres divisions structurelles dans chaque espace du navire », explique Paboeuf. « La deuxième approche, l'équivalence globale, traite de l'incendie au niveau du navire, en prenant en compte tous les systèmes (protection incendie active et passive, détection, évacuation, etc.) qui impactent la sécurité incendie du navire dans son ensemble, et pas seulement chacun. espace divisé. »
« L'adoption plus large des composites dans la construction navale se fera étape par étape », dit-il. « Cela commencera par de petites pièces telles que les ponts et la superstructure, ou des équipements tels que les lignes d'arbres et les hélices, avant de passer à la construction de navires entiers, qui seront d'abord principalement des navires à usage spécial tels que des navires de recherche et d'essais sismiques et des navires à grande vitesse. patrouilleur. »

Fig. 1 navire composite RAMSSES de 80 mètres
Le chantier naval Damen (DSNS) développe un navire de type patrouilleur hauturier tout composite dans le cadre du projet RAMSSES. Son démonstrateur de section de coque pleine échelle de 6 mètres sur 6 mètres sur 3 sera construit en 2020 en utilisant l'infusion de résine en collaboration avec InfraCore Company (ICC) et Airborne International (AIR). Origine | Chantier Naval Damen et RAMSSES
Démonstrateurs de navires tout composite
En plus du FRV de 85 mètres présenté par FIBRESHIP, un navire de patrouille offshore de 80 mètres de long est en cours de développement au sein de RAMSSES pour être le premier navire SOLAS entièrement composite. Dirigé par Damen Shipyard Group (Gorinchem, Pays-Bas), ce travail fait avancer les résultats de son projet Bluenose démarré en 2014. Dans le cadre du module de travail RAMSSES 17, Damen dirige la démonstration d'un plein-mètre de 6 x 6 x 3 mètres. section de coque composite à l'échelle de ce navire réalisée par infusion sous vide, explique Matthias Krause, ingénieur R&D au Center of Maritime Technologies (CMT, Hambourg, Allemagne) et co-coordinateur du projet RAMSSES avec CETENA (Gênes, Italie). « Evonik a développé une nouvelle résine pour cette section de coque de démonstration et un outillage de 6 mètres de haut a été fabriqué. Damen travaille également avec Airborne International (La Haye, Pays-Bas), un fournisseur de l'industrie aéronautique qui a également construit de grandes structures infusées. Evonik (Essen, Allemagne) a expliqué son rôle pour améliorer la résistance aux chocs et le comportement à la fatigue de la coque infusée de fibre de verre/ester vinylique.
Un autre partenaire de ce démonstrateur est InfraCore Co. (Rotterdam, Pays-Bas), qui développe de nouvelles applications pour la technologie InfraCore utilisée par la société sœur FiberCore Europe (Rotterdam) dans plus de 1 000 ponts et écluses composites dans le monde. « Nous avons initialement rejoint Damen dans ce projet de construction d'un héliplateforme de 12 à 14 tonnes », explique Laurent Morel, responsable des opérations d'InfraCore. « Nous travaillons maintenant avec eux pour construire les ponts, les cloisons et la structure de la coque. Nous utiliserons à la fois l'infusion horizontale et verticale pour produire la section de coque en un seul coup. Jusqu'à présent, nous avons infusé à une hauteur de 9,8 mètres. Une fois terminé, ce démonstrateur sera testé pour les performances structurelles et au feu, les résultats et les leçons apprises étant intégrés aux nouveaux modules FTA de RAMSSES.
Plateaux légers
Les composites ont déjà été démontrés dans le premier porte-voitures roulant à roulettes utilisant un pont de chargement composite, conçu et construit par Uljanik Group (Pula, Croatie) dans le cadre du lot de travaux RAMSSES 14 (voir « Low weight on the high mers »), ainsi qu'un solarium léger pour un bateau de croisière fluviale de 110 mètres de long (voir « Un pont composite réduit le tirant d'eau d'un navire fluvial ») et un pont intermédiaire composite pour un transporteur de marchandises générales de 200 mètres de long. « Un pont entre les deux est un pont amovible que vous pouvez installer pour diviser la soute afin de faciliter différents types de cargaisons », explique Arnt Frode Brevik, directeur de Compocean (Sandvika, Norvège), un fournisseur de solutions composites issues du pétrole et du gaz. l'industrie.
« Nous travaillons avec Oshima Shipbuilding (Nagasaki, Japon) et DNV GL depuis plusieurs années pour développer un pont intermédiaire léger dans le but de réduire le poids de 50 % par rapport à l'acier », explique Brevik. Cela a abouti à un prototype GRP de 9 mètres sur 2 qui a été testé pour l'impact et les charges maximales, puis exposé à NOR-Shipping 2017.
Compocean a étendu ce développement à un nouveau projet avec Oshima, DNV GL et l'armateur Masterbulk Pte Ltd. testé jusqu'à fin 2021.
« Oshima cherchait à optimiser les articles pour réduire les coûts de carburant et de manutention », explique Brevik. « Bien qu'il n'y ait pas beaucoup d'entre-ponts par navire, c'est une partie facile pour commencer lors de l'introduction de nouveaux matériaux car cela ne fait pas partie de la structure principale du navire. » La conception est basée sur une plaque de fibre de verre imprégnée de résine polyester avec des renforts de chapeau en dessous. « Nous utilisons un mélange de couches de ±45 degrés, 0 degrés et 0 degrés/90 degrés pour toutes les pièces, mais dans des rapports différents. La structure du pont doit également intégrer de nombreux points d'arrimage pour sécuriser la cargaison. La plaque sera collée aux raidisseurs du chapeau à l'aide d'un adhésif structurel tandis que le boulonnage sera utilisé en combinaison avec le système d'arrimage. Un support d'extrémité en acier boulonné rejoindra le composite à la structure en acier du navire. "Nous poursuivrons également une conception avec des joints purement adhésifs à l'avenir", ajoute Brevik.

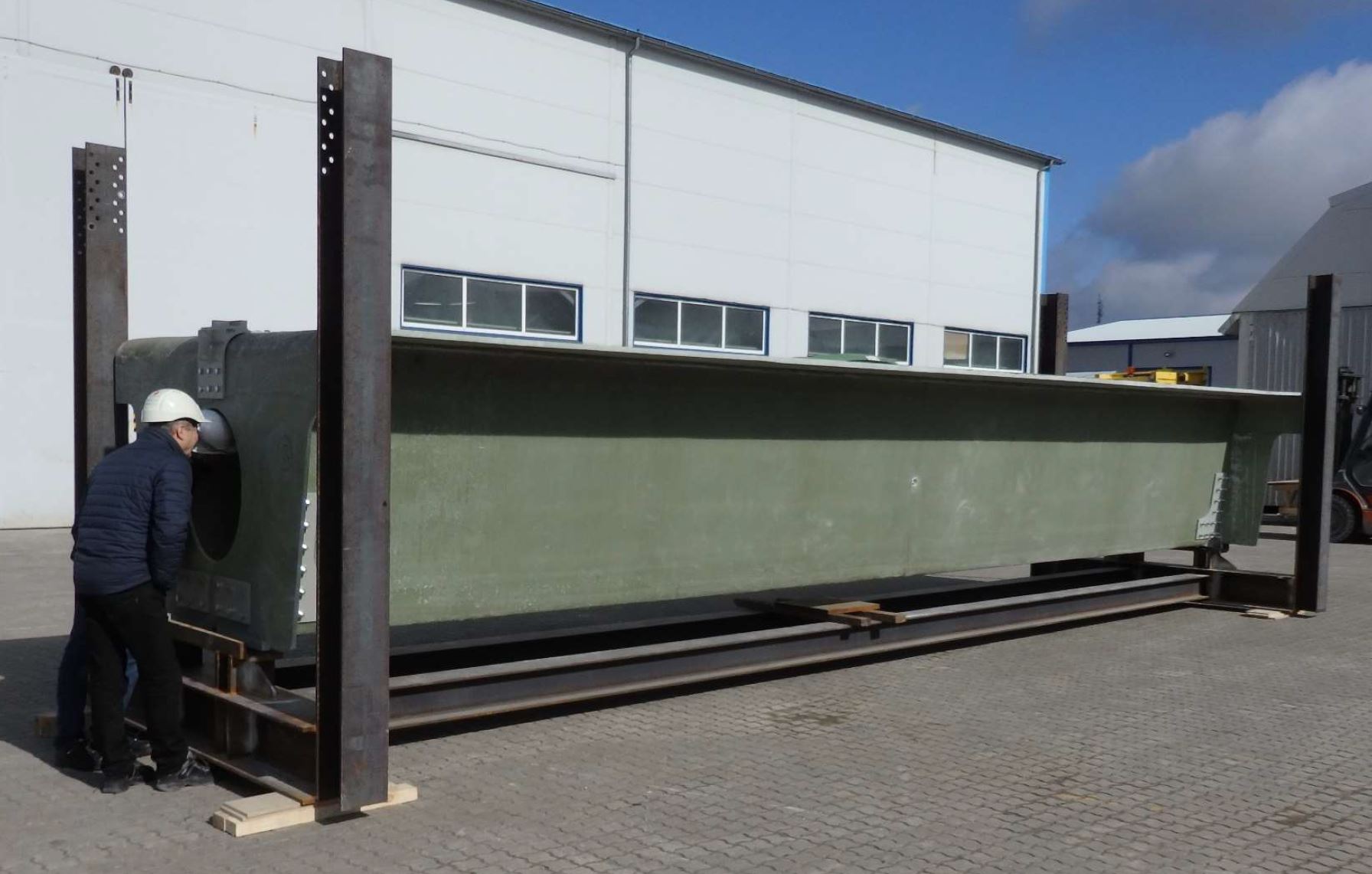
Fig. 2 ponts d'interpolation composites
La nouvelle conception de transporteur de marchandises générales à écoutilles ouvertes 65k d'Oshima Shipbuilding utilisera le prototype de pont d'interpolation composite de Compocean, qui permet d'économiser 50% de poids par rapport à l'acier et sera composé de plusieurs raidisseurs de chapeau FRP infusés (insert) liés à une plaque supérieure FRP avec des connexions boulonnées de le composite à la structure en acier du navire. Origine | Compocean et DNV GL
Après avoir reçu l'approbation finale de DNV GL pour la conception à grande échelle de l'entrepont, Compocean a produit les moules et commencé les tests de fabrication. "Le pont composite à grande échelle sera construit par un partenaire en Malaisie qui le transportera par barge jusqu'au navire", a déclaré Brevik. L'étape suivante consiste à viser une réduction de poids beaucoup plus importante, par exemple, des trappes composites au-dessus des ouvertures de cargaison (plaques plates au-dessus des « boîtes » vertes dans le rendu du navire ci-dessus). « Il y a sept grands panneaux d'écoutille sur ce type de transporteur », note-t-il. « Les faire approuver par DNV GL posera de nouveaux défis, mais le succès avec le pont interpolé aidera. »
Superstructure légère, cabines modulables
RAMSSES dispose de six lots de travaux axés sur les superstructures composites et les composants utilisés au-dessus du pont principal, la plupart avec des démonstrateurs et des résultats d'essais qui seront présentés en 2020. Le lot de travaux 16, dirigé par Naval Group (Paris, France), démontre un module de superstructure composite léger. joint à un tablier en acier. Le démonstrateur à terre représente un bloc standard pour un navire de type patrouilleur hauturier. « La construction navale en matériaux métalliques est basée sur la construction en blocs pour réduire les délais et les coûts », explique Jurado. « Construire de tels blocs à l'aide de composites pose des problèmes avec le besoin de grands moules ainsi que des techniques d'assemblage et des exigences de sécurité communes. Fibreship a étudié cela et a développé quelques recommandations sur l'assemblage de blocs à base de composite, y compris la séquence d'assemblage. Dans RAMSSES, Naval Group a étudié trois types de structures sandwich comprenant l'âme GF/polyester/balsa, l'âme en mousse FR époxy/PET et l'âme en mousse GF/polyester/3D renforcée de fibres. Elle développe également un système de surveillance de l'état de la structure (SHM) à l'intérieur des panneaux de joint et composites.
Le work package 18, mené par les Chantiers de l'Atlantique (Saint Nazaire, France) développe une solution modularisée pour les cabines passagers. « Ceux-ci sont généralement livrés sans plancher car ils sont soudés sur les ponts en acier du navire », explique Krause. « L'idée est de les fabriquer à partir de composites, pré-équipés de tous les systèmes auxiliaires tels que le chauffage et l'air, l'électricité, etc. En incluant un sol composite, ceux-ci pourraient être insérés dans un cadre en acier (comme un tiroir) plutôt que soudés sur un plate-forme en acier solide, économisant ainsi beaucoup de poids. Bien que le projet évalue les composites pour réduire le temps de production et d'assemblage des murs, des plafonds et des unités de salle de bain, car le remplacement du tablier en acier permettrait d'économiser environ 125 kilogrammes par mètre carré, les sols composites sont un objectif principal. Hutchinson (Paris, France) a proposé d'utiliser sa mousse composite renforcée de fibres minérales ZALTEX, qui résiste à des températures de -190°C à 1000°C.
Le lot de travaux 13, dirigé par le constructeur de navires de croisière Meyer Werft (Papenburg, Allemagne), vise également des processus d'assemblage efficaces, mais en ciblant les cloisons. . L'objectif est de construire deux démonstrateurs - un onshore, un offshore (essai en mer) - où des murs composites seront assemblés à des structures en acier puis soumis à 80 tests mécaniques. Le partenaire du projet InfraCore a effectué une analyse pour définir les exigences en matière d'isolation thermique et acoustique, de fréquence propre (vibration), de déformation et de largeur et hauteur maximales pour les murs composites. « On nous a demandé de développer des murs intérieurs et extérieurs multifonctionnels », explique Morel chez InfraCore. « Pour gagner du temps, de l'argent et du poids, nous devons intégrer une isolation et une bonne finition intérieure au panneau structurel léger. Il y a jusqu'à 6800 mètres carrés de ces murs sur chaque bateau de croisière. Nous avons la possibilité de les mettre à bord d'un bateau de croisière à la mi-2020, ce qui pourrait être les premiers murs composites approuvés SOLAS sur un bateau de croisière dans le monde. »
Dans le lot de travaux 10, Podcomp (Öjebyn, Suède) développe un panneau intérieur/extérieur alternatif utilisant des éléments biosourcés composites qui doivent être ignifuges et à un prix compétitif. Trois concepts sandwich basés sur le préimprégné GF/alcool polyfurfurylique (PFA) de Composites Evolution (Chesterfield, Royaume-Uni) et différents matériaux de noyau ont été examinés. Un seul concept a réussi les tests de calorimètre à cône et d'autres tests d'incendie effectués par les instituts de recherche RISE de Suède (Borås). Il est maintenant optimisé en termes de poids et de coût.
Après avoir essayé l'aluminium et le soudage par friction-malaxage, Baltic Workboats (Nasva, Estonie) avance maintenant avec les composites pour développer des panneaux pré-équipés et raidis pour le rouf/la superstructure des bateaux de travail en aluminium (work package 15). La conception des panneaux, la connexion avec d'autres panneaux et avec le reste de la structure du rouf, les procédures d'analyse structurelle et la solution d'isolation seront démontrées, ainsi que les techniques d'installation à bord.
Une autre solution pour la superstructure légère est en cours de développement par BaltiCo (Hohen Luckow, Allemagne), un fabricant d'équipements navals qui a une nouvelle start-up pour construire des bateaux complets en utilisant de la fibre de carbone placée par robot et drapée autour d'une structure en treillis. "Vous construisez le squelette de la structure que vous souhaitez produire, en plaçant une structure transversale ou des nervures en GFRP environ tous les demi-mètres, puis un robot enroule de la fibre de carbone autour d'elle", explique Krause. L'objectif est un système modulaire ultra-léger utilisant un processus hautement automatisé. La démonstration comprendra la production et l'assemblage de deux modules de coque et de pont autoportants dans un catamaran léger à énergie solaire non SOLAS.
Joints soudés FRP-acier
« Nous pensons que l'avenir de la construction navale réside dans la combinaison de composites FRP, d'acier et d'autres matériaux dans des structures hybrides », déclare le Dr Lars Molter, un vétéran de 10 ans chez CMT. « Nous avons examiné le collage, mais il n'existe pas de conception de joint standardisée que vous pouvez utiliser dans tous les navires et il n'y a pas de règles générales sur la façon d'appliquer le collage dans les navires SOLAS. De plus, vous devez contrôler l'environnement et le processus de liaison. Il note que cela est difficile au milieu du soudage et du coupage qui dominent généralement la construction des chantiers navals. « Nous avons demandé à DNV GL ce qu'ils approuveraient pour les joints de matériaux différents », explique Molter. « Ils ont dit que la structure primaire nécessiterait généralement une fixation mécanique ; le collage pur ne serait pas facilement certifié sans attaches redondantes. »
Molter et CMT ont répondu avec le projet FAUSST (Fiber and Steel Standard conjoint) financé par l'Allemagne, qui a développé un tissu tricoté hybride qui passe de 100 % de fibres de verre à 100 % de fibres d'acier. Ce dernier est soudé à un connecteur en acier (par exemple, une plaque plate, un profil rectangulaire, etc.), qui peut ensuite être facilement soudé dans la structure en acier d'un navire (Fig. 3). L'extrémité en fibre de verre est jointe à la structure composite par infusion de résine. "Cette conception de joint offre une inspection NDT à 100 % car vous pouvez utiliser l'UT (ultrasons) ou les rayons X sur la soudure", explique Molter. FAUSST a effectué des tests mécaniques, environnementaux et de fatigue sur ce type de joint et a également obtenu l'approbation de principe des sociétés de classification, mais il restait encore beaucoup à faire pour transformer la technologie en un produit commercial. Ainsi, Molter a quitté CMT et a fondé HYCONNECT GmbH (Hambourg, Allemagne) en 2018.
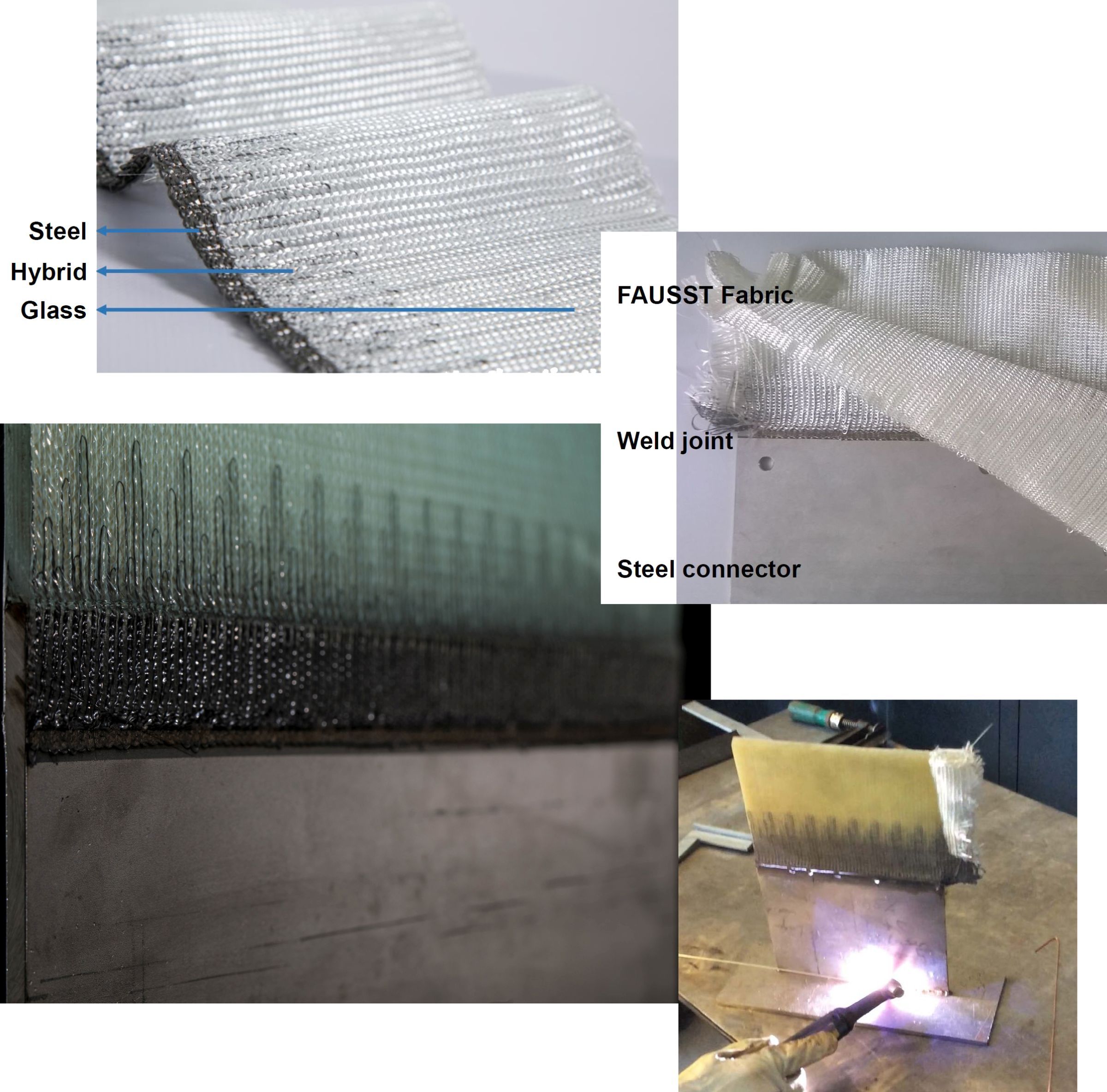
Fig. 3 Joint soudé acier-PRV HYCONNECT
Tissu hybride acier-verre FAUSST (en haut à gauche) est soudé à la presse à une plaque d'acier ou à un autre connecteur (en haut à droite) et peut ensuite être intégré dans une structure composite par infusion de résine (en bas à gauche) . De telles structures composites hybrides sont ensuite facilement soudées dans la charpente d'un navire en acier (en bas à droite) .
Origine | HYCONNEXION
« Nous avons rencontré des chantiers navals, DNV GL et BV et développons un produit qui peut être certifié », déclare Molter. « Vous commandez simplement vos pièces composites avec ce système de joint et vous pouvez ensuite les souder dans votre navire. C'est notre vision. Nous concevons le joint composite-acier puis livrons un produit dont le tissu est soudé à un connecteur en acier (plaque, profilé, etc.). »
Il explique que la conception commune et le tissu seront certifiés dans un système par étapes :« En appliquant plus de couches de tissu FAUSST, il y a une augmentation linéaire de la capacité de charge. » Par exemple, le produit de base pourrait être constitué de quatre couches de FAUSST avec une barre plate de 1 mètre soudée dessus, conçue pour une certaine charge de traction et de flexion. Then there would be some products available to the left (e.g., two-three layers total for a lower load rating) and right (e.g., six layers total for a higher load rating). “We are still finalizing these details, but the goal is a standardized and easy-to-use system,” notes Molter.
HYCONNECT has adapted the fabric technology to handle the difference in stiffness and coefficient of thermal expansion (CTE) between steel and composites; the use of knitted fibers for mechanical interlocking with unidirectional fibers for carrying load through the joint; and the technique required for high-quality press welding of the steel fibers to the steel connector (see "Connecting composites to steel”). “This solution is based on continuous testing,” says Molter. “Because FAUSST consists of standardized ready-made sub-products, it can be supplied quickly, within days.” Prototypes are currently being produced for selected customers, and HYCONNECT will begin full production in 2020.
Composite rudders
Ship rudders are also being developed as FRP-steel hybrids. As part of RAMSSES work package 12, Becker Marine Systems (BMS, Hamburg, Germany) is demonstrating a lightweight composite flap for a steel rudder designed for large container ships. Such rudders typically weigh more than 200 tons, says Jörg Mehldau, head of R&D at BMS. “By adding a hinged aft flap, you can significantly reduce the rudder area.” BMS pioneered this flap rudder, which dramatically reduces ship turning radius and improves course-keeping and maneuverability, enabling berthing without tugboat assistance. A composite flap not only reduces weight but also enables more functional shapes as well as more hydrodynamically- and load-optimized designs.
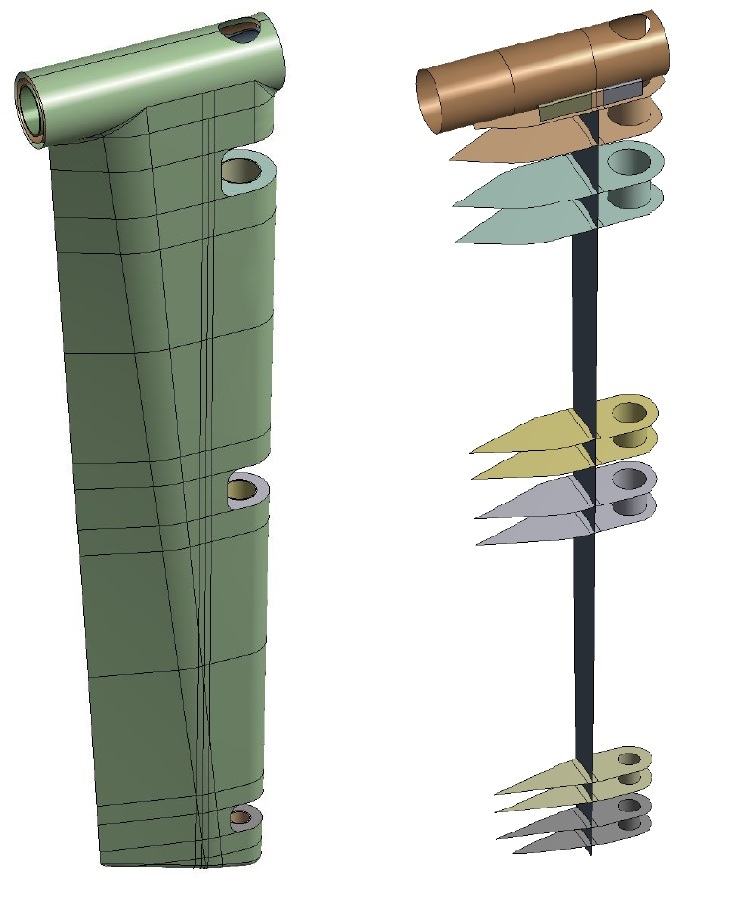
Fig. 4 Composite rudder flap
Becker Marine Systems is working with InfraCore to develop a lightweight, resin-infused rudder flap for the largest container ships. Measuring 11.8 meters long and 0.9 meter wide with a 2.9 meter chord, the full-scale flap must withstand 100 tons/m
2
of load. A 2-meter high demo will be tested 2Q 2020. Source| Becker Marine Systems
“The composite flap we are developing was inspired by the aviation industry,” notes Mehldau. For RAMSSES, the full-scale test case is aimed at one of the largest container ships (≈400 meters long), a flap measuring 11.8 longmeters and 0.9 meters wide with a chord of 2.9 meters (see Fig. 4). “We calculated the forces on this rudder and flap using formulas based on DNV GL rules for this ship’s type, weight and maximum speed,” says Mehldau. BMS then conducted preliminary design and engineering analysis, as well as trade studies for manufacturability and cost. “We first favored filament winding but it was too expensive,” he notes. “For each new ship hull, the rudder is a single design.” Thus, resin infusion was chosen, as was an alternative design from InfraCore. “It was the best for production flexibility, cost and structural performance combined,” Mehldau explains.
“To me, this was a natural fit for InfraCore because the composite lock gates we have built are very similar,” says Morel. He notes container ship rudders must withstand loads of roughly 100 tons per square meter with a surface area of 150 square meters. This matches well with InfraCore’s infusion-based technology used in bridge decks spanning up to 142 meters. Instead of bonding a high-density structural core to faceskins, InfraCore uses a low-density foam core only as a permanent formwork for multiple Z-shaped, two-flanged web structures. These are overlapped, faced with multiaxial fabrics and co-infused to form a robust construction. InfraCore will build a 1:6 scale demonstrator, using glass fiber and polyester resin materials already certified by DNV GL to keep costs low.
Morel notes that the reduced-weight InfraCore composite flap is cost-competitive, “because steel ship rudders are quite complicated to manufacture.” Mehldau agrees, “together with less maintenance and operational cost advantages, we see a successful business case.” The 2-meter -high demonstrator will be finished by 2Q 2020, followed by testing.
“We will test this using a lab test bench and air cushions, which can apply up to 8 bar of pressure equal to at least 80 Mpa of load,” says Mehldau. “We will measure strains and deflections to verify our simulations and perform a break load test.” A lab-scale demonstrator will also be tested via sea trials on a research ship in the Elbe River by CETENA (Genoa, Italy) which serves as project coordinator for RAMSSES along with CMT.
Forward momentum
“The outlook for composites in ships is good because many of the marine sector stakeholders have shown interest in FIBRESHIP, RAMSSES and other projects,” says Jurado. “The largest challenges are the need for new regulations, fire safety aspects, bonding techniques and reduction of shipbuilding costs.” For the latter, he cites automated manufacturing in shipyards as a key issue as well as mold construction and composite materials sourcing and storage. “Composites are already growing in ships,” says Krause at CMT, “but we started this work 20 years ago, so it is a slow process. However, we now have this critical mass and the industry is more connected via E-LASS.”
Jörg Bünker, head of R&D, application service for SAERTEX LEO FR products at SAERTEX (Saerbeck, Germany), agrees:“The drivers to reduce weight are strengthening. Within the next five to seven years, more composite materials will be sold into ships. This is the right time for more projects because IMO needs to see this interest and effort from the industry. Suppliers must show new solutions and shipyards must show where composites can be used, but no one can do it alone.”
Résine
- Recyclage :composites thermoplastiques renforcés de fibres continues avec polycarbonate recyclé
- Comment la technologie mobile supprime les obstacles au voyage
- TxV Aero Composites est conforme aux normes AS9100
- Mikrosam automatise les composites thermoplastiques avec un système de placement multi-robot sans outil
- Hexcel s'associe à Lavoisier Composites, Arkema
- Fabrication continue de fibres (CFM) avec des composites moi
- Sommet allégé :ciblage des opportunités de groupes motopropulseurs automobiles composites
- Ashland s'associe à Velox pour la distribution de composites en France
- Impression 3D de composites avec fibre continue