Prouvant le soudage LM PAEK pour le démonstrateur multifonctionnel de fuselage
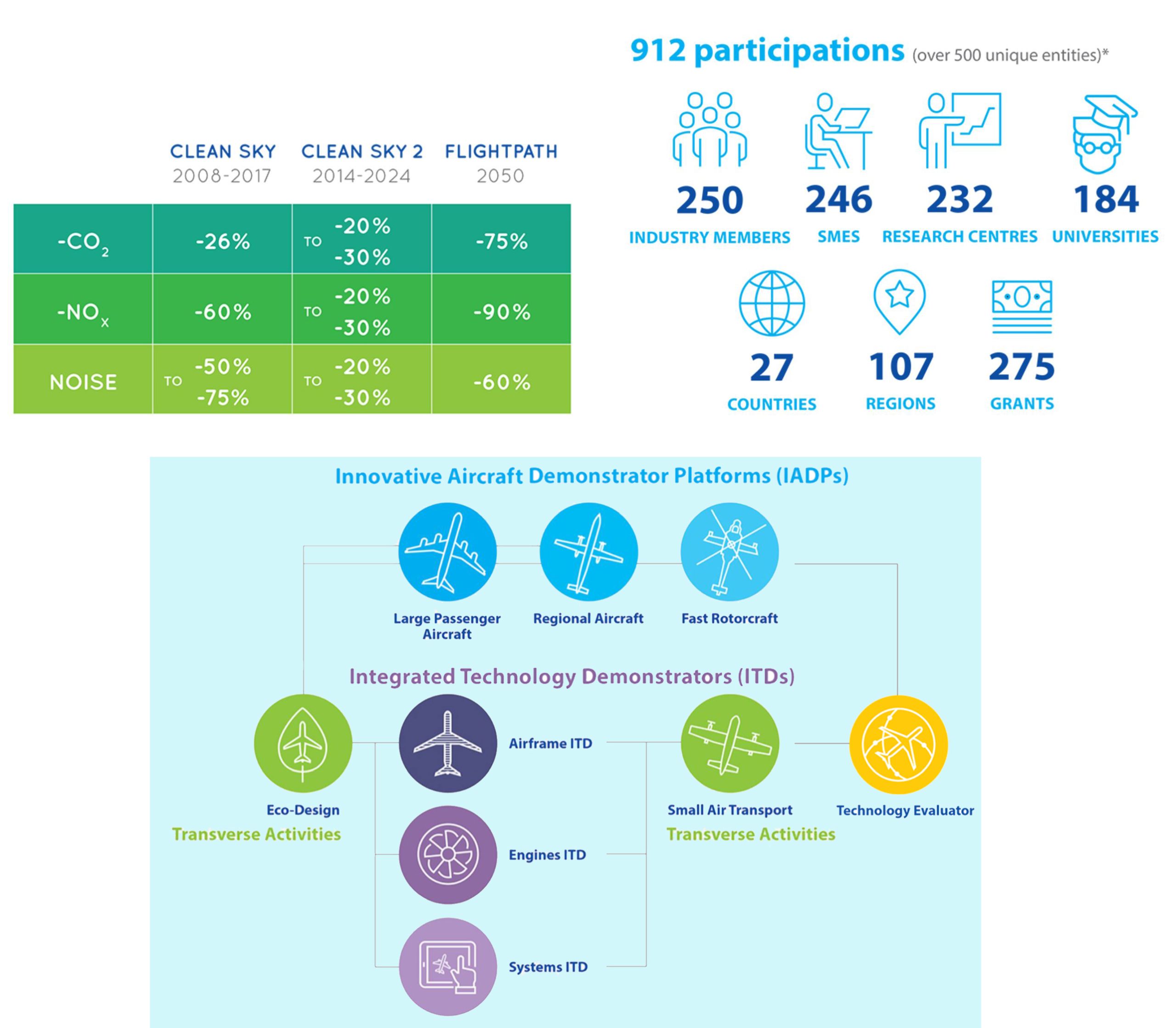
Ce type de recherche aéronautique a commencé avec le programme-cadre (PC) de la Commission européenne pour le financement de la R&D, couvrant le FP2 (1987-1991) au FP7 (2007-2013). Ces programmes ont contribué de manière substantielle à la maturation d'une grande variété de technologies jusqu'au niveau de maturité technologique (TRL) 6 et à leur mise en œuvre dans des avions tels que l'Airbus A350.
L'une des différences de Clean Sky 2 est son organisation autour de grands démonstrateurs. Le MFFD est l'une des trois sections de fuselage à grande échelle produites au sein de la plate-forme de démonstration d'avions innovants pour gros avions de ligne (LPA) (IADP) (voir le texte bleu en haut du carré bleu dans l'infographie ci-dessus) . Au sein du LPA IAPD, il existe trois plates-formes. Le MFFD se trouve au sein de la plate-forme 2 « Structure de cabine-système d'intégration physique innovante », qui comprend deux autres grands démonstrateurs.
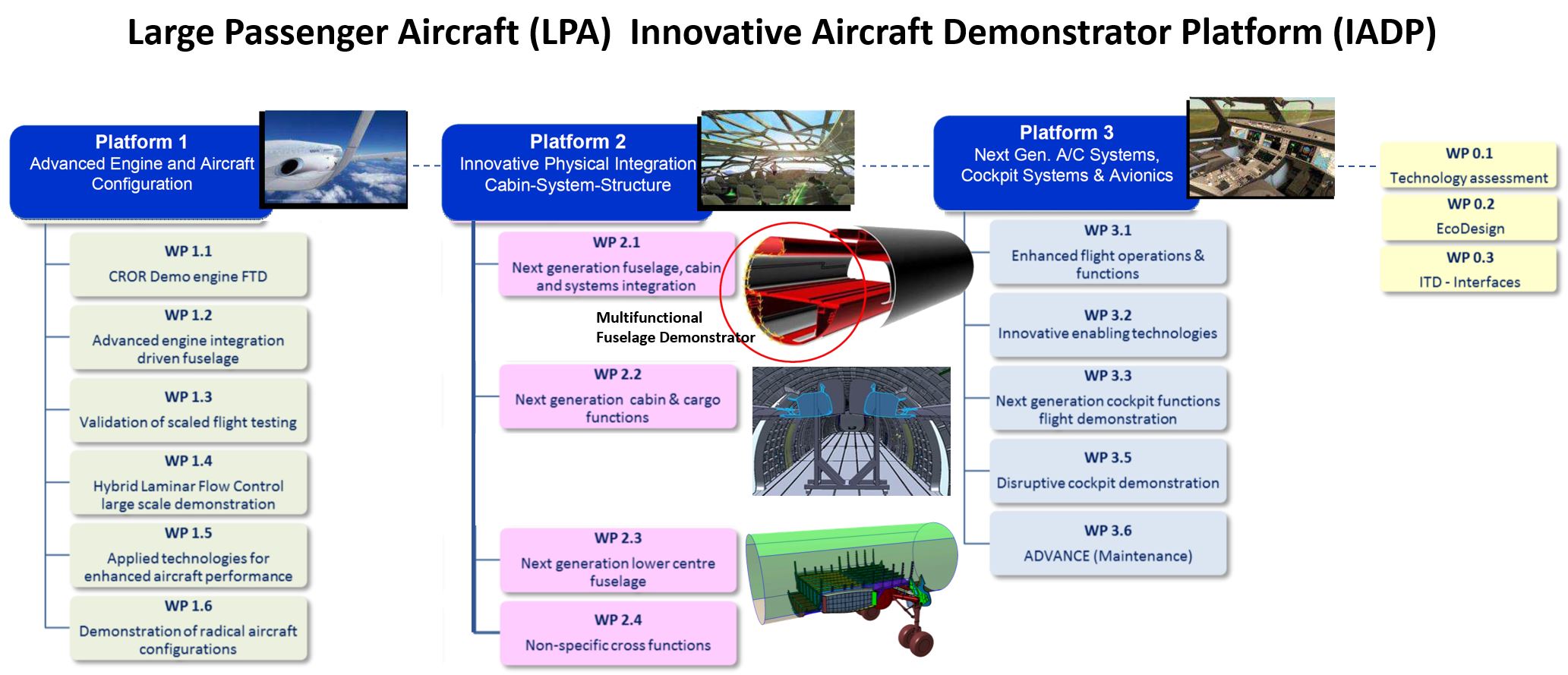
Pour comprendre ce que cela signifie, je reviens à quelque chose que les ingénieurs Airbus Airframe Research &Technology (R&T) de Getafe, en Espagne, m'ont dit alors que je recherchais des composites multifonctionnels en 2015. déchets de fabrication d'un cylindre structurel extérieur et d'un cylindre intérieur; nous voulons intégrer la cellule structurelle aux systèmes de cabine. J'ai eu du mal à visualiser ce que cela signifiait — jusqu'à ce que je voie un croquis du MFFD.
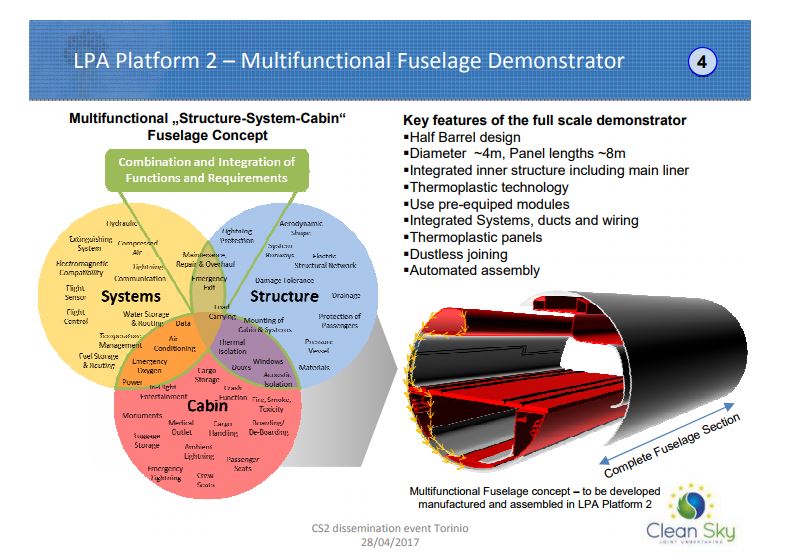
SOURCE | Diffusion de Clean Sky 2 (CS2) et "Démonstrateurs de composites thermoplastiques — Feuille de route de l'UE pour les futures cellules".
« La modularité, l'intégration et la création de plates-formes communes sont essentielles », déclare Ralf Herrmann, Airframe R&T Typique Fuselage chez Airbus Operations GmbH (Brême, Allemagne) et chef du programme MFFD. Je cite ici la page MFFD sur le site Web de Clean Sky 2:
Herrmann :"Nous savons depuis longtemps que les avantages de la réduction de poids et de la réduction des coûts récurrents dans la production d'avions - lors de l'utilisation de composites thermoplastiques — ne peut être atteint que par l'intégration de plusieurs disciplines. Cela signifie que se concentrer sur la structure seule ne peut pas tirer pleinement parti de la technologie des composites.
La polyvalence des thermoplastiques doit être appliquée en combinaison avec une approche de conception, selon Paolo Trinchieri, responsable du projet Clean Sky 2 :« Il est nécessaire de supprimer la séparation artificielle des fonctions au stade de la préconception de l'avion et de prévoir dès le départ un taux de production élevé de fabrication, d'assemblage et d'installation d'avions. »
Herrmann était auparavant chef de projet pour le projet FP7 MAAXIMUS (structure d'avions plus abordables grâce à un dimensionnement numérique étendu, intégré et mature). D'avril 2008 à septembre 2016, MAAXIMUS comprenait 60 partenaires et visait à démontrer le développement rapide et la validation du premier coup - en faisant mûrir simultanément des facilitateurs virtuels et physiques - d'un fuselage composite hautement optimisé pour obtenir une réduction de 50 % du temps d'assemblage de de grandes sections de fuselage, une réduction de 10 % des coûts récurrents, un poids structurel de 10 % en moins et un cycle de développement de 20 % plus court. Les objectifs du MFFD peuvent être vus comme une extension :
- Activer des taux de production de 70 à 100 avions/mois
- Réduire le poids du fuselage de 1 000 kg
- Réduire les coûts récurrents de 20 %.
Un élément clé est l'adhésion sans poussière (pas de trous, pas de fixations) via des composants composites thermoplastiques soudés. Herrmann explique que l'approche séquentielle actuelle de la fabrication d'avions - où la structure du fuselage doit être assez complète avant que les systèmes ainsi que les caractéristiques de la cabine et du fret puissent être installés - est chronophage et « sensible aux pannes ». Au lieu de cela, MFFD recherche des éléments structurels et des modules système pré-équipés et hautement intégrés qui peuvent être installés assez tôt, bien avant l'assemblage final.
Modification des joints longitudinaux et LM PAEK
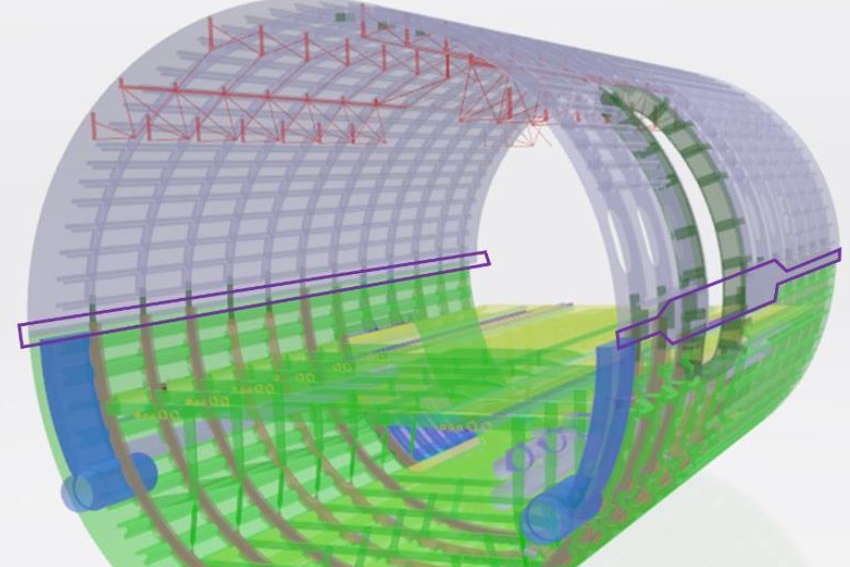
Les activités du projet MFFD ont commencé en 2017. Chaque année, il y a au moins un appel à propositions (AP) dans lequel les chefs de projet décrivent des sujets qui doivent être développés davantage. Comme on peut le voir dans l'image ci-dessous, la conception du joint en biais illustrée dans le CFP08 (avril 2018) a été remplacée par un joint longitudinal par le CFP09 (septembre 2018).
« Le joint de biais a présenté des problèmes d'accessibilité et de fixation des structures de plancher que nous avons réalisé qu'il serait difficile de surmonter dans le délai imparti », explique Herrmann. « Nous avons donc décidé de revenir à la conception conventionnelle afin de réduire le risque. Notre principal intérêt est de montrer comment intégrer tous les systèmes et éléments de cabine qui peuvent être installés avant l'assemblage des composants principaux (MCA). Ce sera également la première fois que ce matériau composite thermoplastique est appliqué dans des structures de fuselage primaires à grande échelle pour les gros avions de passagers. »
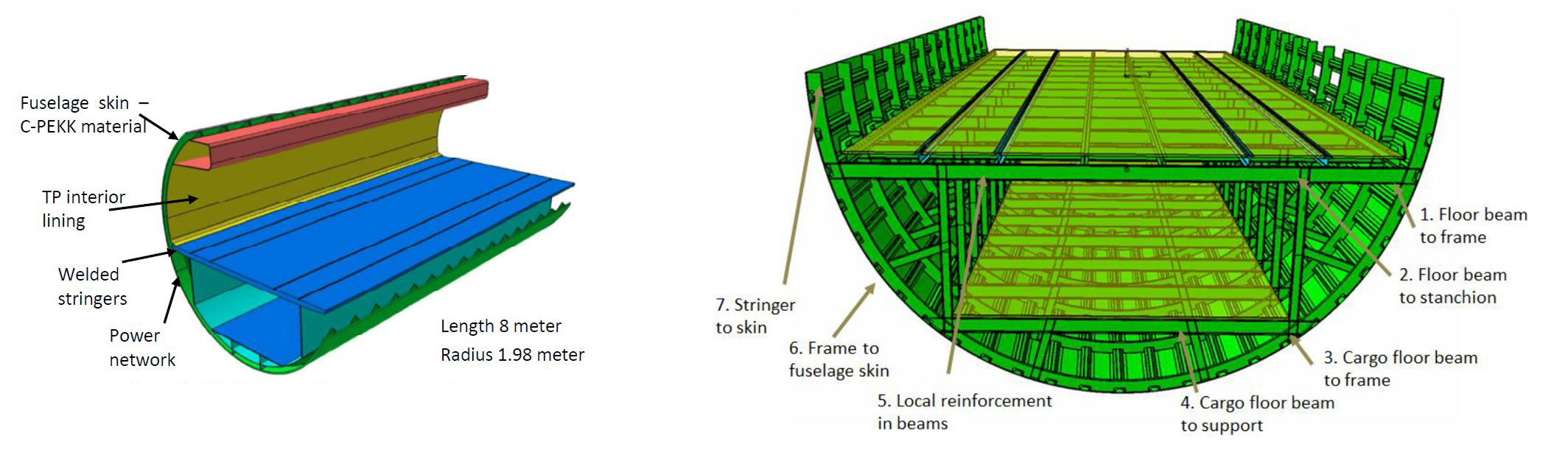
La conception du MFFD est passée d'une conception de joint en biais à un joint longitudinal plus conventionnel en 2018. SOURCE | CFP08 p.87 (gauche) et CFP09 p. 133 (à droite).
Un autre changement concerne le matériau de la matrice composite thermoplastique (TPC). Les sujets MFFD dans CFP08 et CFP09 font référence à la fibre de carbone/PEKK (polyéthercétonecétone), mais par CFP10 (mars 2019), le matériau de base a été décrit comme fibre de carbone et PAEK (polyaryléthercétone). PAEK est la famille globale de polymères au sein de laquelle résident PEEK, PEKK et LM PAEK.
Comme décrit dans mon blog sur PEEK contre PEKK contre PAEK, le fournisseur de matériaux Cetex TenCate, maintenant Toray Advanced Composites, produit les trois polymères sous forme de ruban renforcé de fibres de carbone et affirme que les propriétés sont fondamentalement les mêmes. Cependant, Cetex TC1225 CF/LM PAEK le ruban fond à 305 °C tandis que TC1320 CF/PEKK le ruban fond à 340°C . Et, selon Scott Unger, directeur technique mondial de Toray Advanced Composites, « LM PAEK a un bien meilleur débit… et peut également être traité à des vitesses plus élevées que le PEKK et le PEEK. » Le TC1225 coûte également moins cher.
Fuselage inférieur MFFD :projet SUPERBE
STUNNING est le nom du projet pour le développement et la fabrication de la moitié inférieure entièrement équipée du MFFD. Le projet vise à mûrir davantage :
- Processus d'assemblage automatisés
- Technologies de fabrication et d'assemblage thermoplastiques
- Technologies intégrées de conception et de développement de fabrication
- Développement d'architectures de systèmes électriques avancées.
Bas Veldman, chef de programme chez GKN Fokker (Hoogeveen, Pays-Bas) et chef de projet pour STUNNING, explique que le MFFD mesurera 8 mètres de long et 4 mètres de large avec un rayon de 2 à 2,5 mètres, ce qui est une échelle réelle pour un monocouloir. Avion de la famille A320. "C'est similaire à l'A321, qui n'est pas exactement circulaire mais à peu près en forme d'œuf (un peu plus haut que large)", ajoute-t-il.
La section inférieure du fuselage à 180° comprendra la coque inférieure du fuselage avec des longerons et des cadres soudés, la structure de la cabine et du plancher de chargement, ainsi que les principaux éléments intérieurs et systèmes. « Nous fournirons de grands modules pré-équipés pour un assemblage plug-and-play très rapide », déclare Veldman.
GKN Fokker est le partenaire principal de STUNNING et compte quatre divisions participantes, dont Aerostructures (Papendrecht, Pays-Bas), Fokker ELMO (Hoogerheide, Pays-Bas), GKN Fokker Engineering Romania (Bucarest) et GKN Fokker Technologies (Papendredcht, Pays-Bas). GKN Fokker ELMO est un fournisseur de faisceaux de câbles pour avions et de technologie de systèmes électriques. "Il est responsable de l'architecture des systèmes dans STUNNING et se concentrera sur l'optimisation du système électrique", explique Veldman, "et collabore avec le consortium CFP08 MISSION sur le développement d'un système de bus d'alimentation innovant."
« Diehl Aviation (Laupheim, Allemagne) est responsable de la structure intérieure, y compris les sous-systèmes et le sol, les panneaux latéraux et la manière dont ils sont assemblés, les interfaces des monuments et les multiports du système intelligent », poursuit Veldman. « NLR (Netherlands Aerospace Centre, Amsterdam) est responsable de la fabrication de la peau du fuselage et des longerons, et TU Delft aide à l'assemblage, sur la base de son expertise en soudage par ultrasons. » (Voir « Soudage de composites thermoplastiques » pour en savoir plus sur le soudage par ultrasons.)
Programme d'essais de soudage MECATESTERS
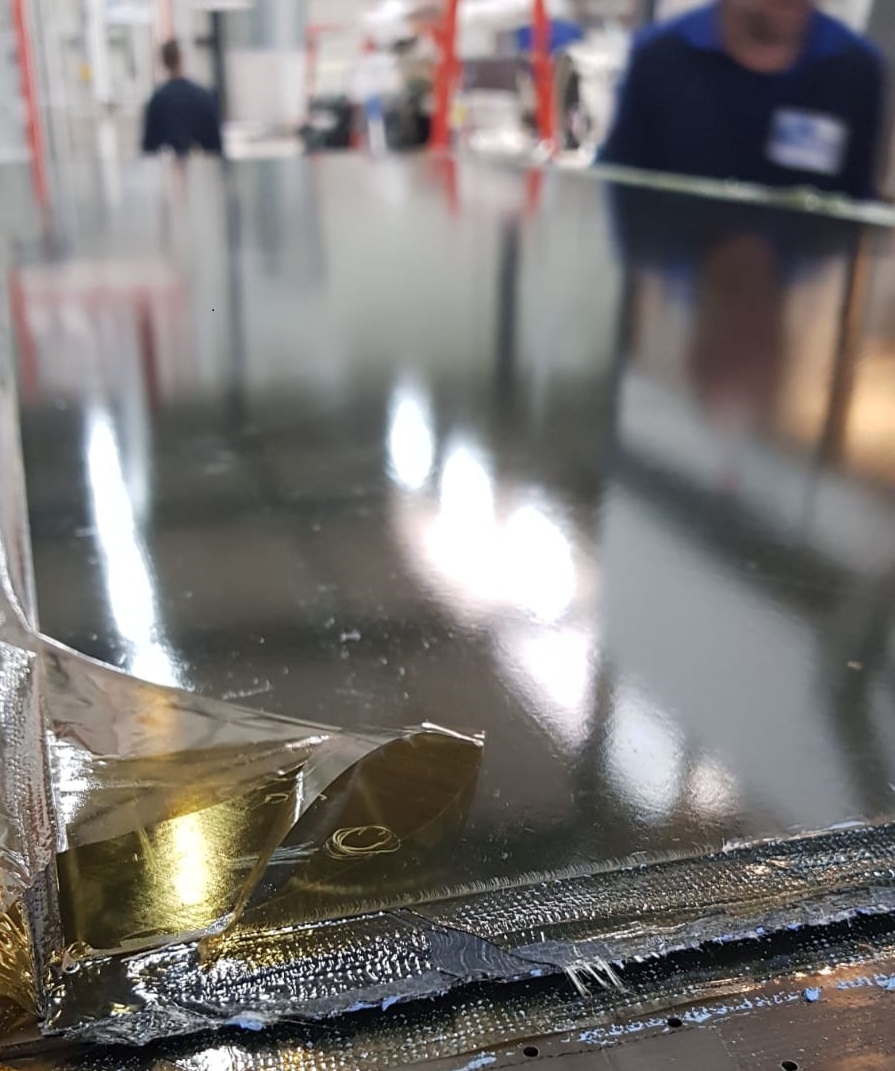
« STUNNING a lancé sept sujets CFP et cinq ont commencé à travailler, dont MAYA, MISSION, EMOTION, TCTool et MECATESTERS », a déclaré Veldman. Ce dernier est un vaste programme d'essais de soudage avec KVE Composites (La Haye, Pays-Bas) et Rescoll (Pessac, France) qui a débuté en avril 2019 pour une durée de 30 mois. Veldman explique que bien que KVE ait une longue histoire avec le soudage par induction de composites thermoplastiques de tissu et de ruban UD, les pièces soudées par induction volant à bord des avions à ce jour ont utilisé du tissu. « Dans STUNNING, nous établissons les meilleures pratiques avec les renforts UD et les matériaux LM PAEK, et comparons également le soudage par induction au soudage par conduction dans des conditions de charge et d'environnement typiques. Bien que le soudage par résistance et le soudage par ultrasons soient inclus dans d'autres lots de travaux MFFD et CFP (voir « Joindre les deux moitiés " ci-dessous), le soudage par induction et le soudage par conduction sont les deux seules techniques dans MECATESTERS.
Labordus chez KVE explique que pour les trois lots de travaux MECATESTERS (WP 1, 2 et 3), KVE fabriquera tous les stratifiés de test en utilisant du ruban en fibre de carbone TC1225 UD/LM PAEK durci à l'autoclave (voir « Premier stratifié Toray LM-PAEK pour projet Clean Sky MECATESTERS »). KVE préparera également des échantillons soudés par induction pour les tests, tandis que GKN Fokker produira des échantillons soudés par conduction et Rescoll effectuera tous les tests physiques. "Le nom Rescoll dérive de la recherche et du collage, qui est le mot français pour le collage", explique Labordus. "Ils sont connus pour leurs recherches sur tous les types de collage et offrent un laboratoire d'essais bien équipé pour les polymères et les composites, y compris les tests mécaniques, environnementaux, d'inflammabilité et tous les tests possibles pour se qualifier dans les industries aérospatiale, automobile, ferroviaire et autres."
Paramètres de processus et tests
« Nous commençons en fait avec le WP 2 pour définir les paramètres de processus, tels que les limites supérieure et inférieure pour la température et la pression du soudage par induction », explique Labordus. "Par exemple, nous avons un nominal pression que nous utilisons normalement, mais nous irons à des pressions plus basses jusqu'à ce que nous commencions à voir des défauts comme des vides, puis nous évaluerons ces propriétés de soudure pour établir la limite de pression inférieure. Les tests évalueront également la vitesse de soudage, qui affecte la vitesse de refroidissement et la cristallinité de la soudure, et potentiellement les propriétés mécaniques. Les mêmes paramètres seront étudiés chez Fokker pour le soudage par conduction.
Pour l'évaluation, le programme MECATESTERS effectuera plusieurs tests, notamment :
- Test de cisaillement selon ASTM D5868-01
- Test d'arrachement et de cisaillement sur coupons profilés en L
- GIC et GIIC selon ISO 15024 et ISO 15114, respectivement
(ce test de ténacité sera en fait terminé dans le WP 1)
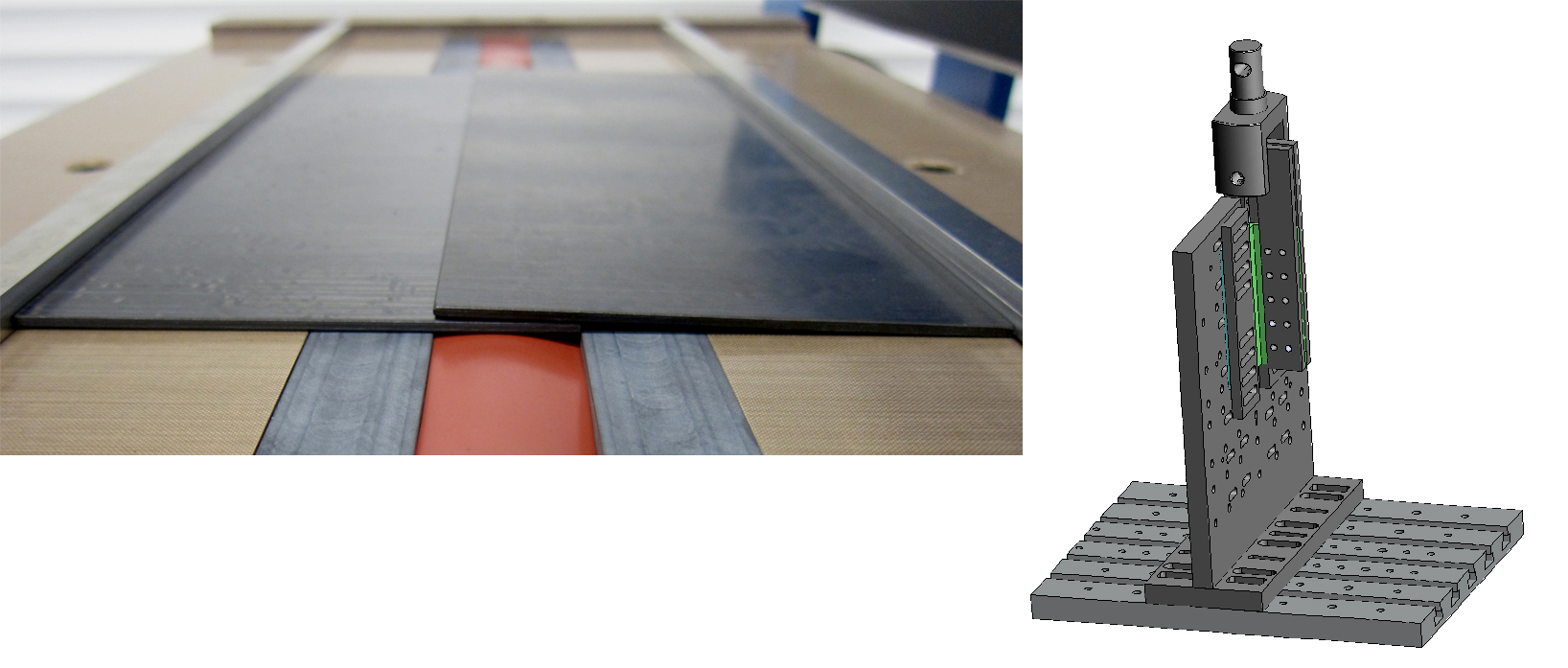
Coupon de cisaillement à un seul tour de ruban UD laminé prêt pour le soudage par induction (à gauche) et montage d'essai pour les tests combinés de cisaillement et de pelage du coupon de profilé en L soudé à l'aide d'un outil développé par Rescoll (à droite). SOURCE | KVE Composites, Rescoll.
« La méthode de test d'arrachement provient d'une norme interne développée par GKN Fokker », explique l'ingénieur de Rescoll Thomas Salat. « Le test d'arrachement des profils soudés est perpendiculaire à la peau pour la charge de pelage », note Labordus, « et parallèle à la peau pour la charge de cisaillement. Le pelage et le cisaillement sont les deux extrêmes, mais nous testerons également de nouvelles combinaisons de ceux-ci qui reflètent les conditions de charge pratiques en service. Ces tests seront effectués pour deux épaisseurs de stratifié distinctes dérivées de la conception du fuselage MFFD — 2,2 et 2,8 millimètres — à température ambiante (RT), à froid (-55 °C) et à haute température (80 °C) en utilisant une charge statique.
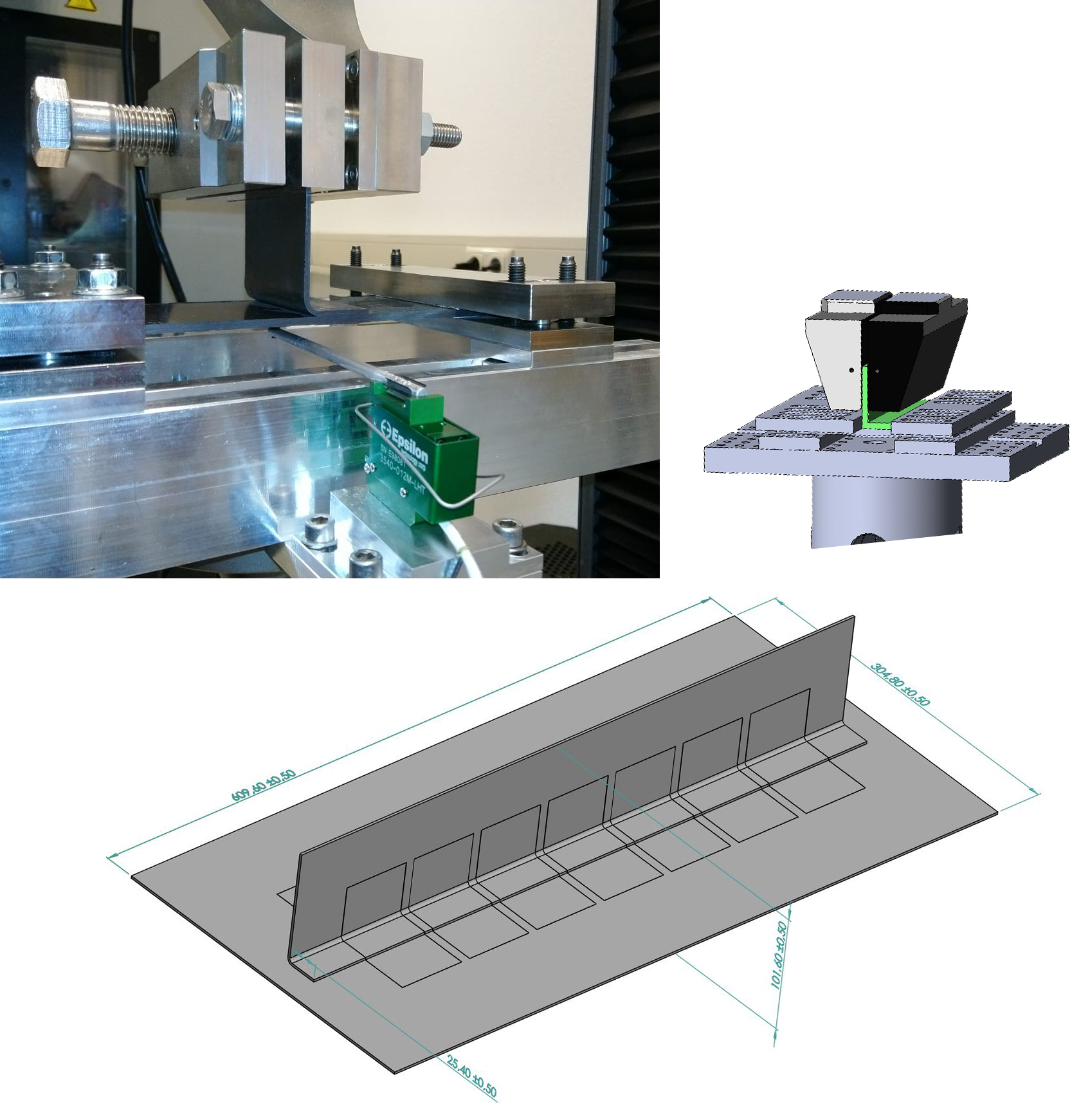
Tests d'arrachement sur coupons profilés en L chez KVE Composites (en haut à gauche). Dans MECATESTERS, ce type de test utilisera une pince et une configuration de test développées par Rescoll pour éliminer la déviation de la peau (en haut à droite). Les coupons d'essai seront découpés dans des panneaux soudés (en bas). SOURCE | Rescoll, KVE Composites.
Préparation de surface, vieillissement et fatigue
Le WP 1 commencera par des tests de ténacité. « Pour les tests de fissuration (GIC et GIIC), nous allons initier une fissure dans le composite et mesurer le comportement de cette fissure lorsqu'elle est chargée », explique Salat. « L'un est un test statique qui augmente la charge jusqu'à la défaillance. Nous ferons également un test dynamique où nous répétons la charge statique un million de fois, ce qui prend une à deux semaines. Nous verrons si la soudure composite peut résister à cette fatigue. Ce mode II est un nouveau type de test cyclique. Nous développons une méthode tirée d'un article technique publié par l'Université d'Europe et finalisons maintenant les paramètres. »
Toujours dans le WP 1, les paramètres de soudage établis dans le WP 2 seront utilisés pour examiner les effets de la préparation de surface ainsi que du vieillissement et de la fatigue. « Nous examinerons les contaminants de surface et leur impact sur la soudure », explique Labordus. « Nous étudierons également trois types différents d'agents de démoulage couramment utilisés dans le traitement des presses et des autoclaves ; types spécifiques de préparation de surface, y compris le ponçage, les abrasifs et le traitement au plasma ; et également l'utilisation d'un film de résine supplémentaire à la surface à souder. De plus, nous étudierons l'influence de l'orientation des fibres, par exemple plus/moins 45 degrés à l'interface de soudure. »
Rescoll utilisera également une chambre de conditionnement à 70 °C et 90 % d'humidité pour simuler le vieillissement en service, explique Salat. « Nous effectuerons ensuite les tests standard pour voir si cela affecte les performances de soudage. » Labordus ajoute qu'un nombre limité d'échantillons seront prélevés à 100 °C et 120 °C, « pour valider l'affirmation selon laquelle les composites thermoplastiques n'ont pas une forte chute au-dessus de 80 °C. »
En plus de l'essai de fissuration dynamique/GIIC, des essais de fatigue seront effectués en modes de cisaillement et d'arrachement à un seul tour. « Nous commencerons à 80 % de la charge de rupture statique et passerons à 50 ou 75 % de celle-ci en fatigue pendant un million de cycles », explique Labordus. « Nous ferons également d'autres tests, mais nous en discutons toujours », ajoute Salat.
Soudage sur des supports composés courts
Bien que les détails du WP 3 soient encore en cours de finalisation, il vise à étudier les soudures des supports moulés par compression fabriqués à partir de fibres courtes sur la peau du stratifié UD. « Nous allons à nouveau comparer les paramètres de processus et caractériser les propriétés mécaniques de la soudure », déclare Labordus, « mais nous travaillons toujours à définir la géométrie pour les tests. »
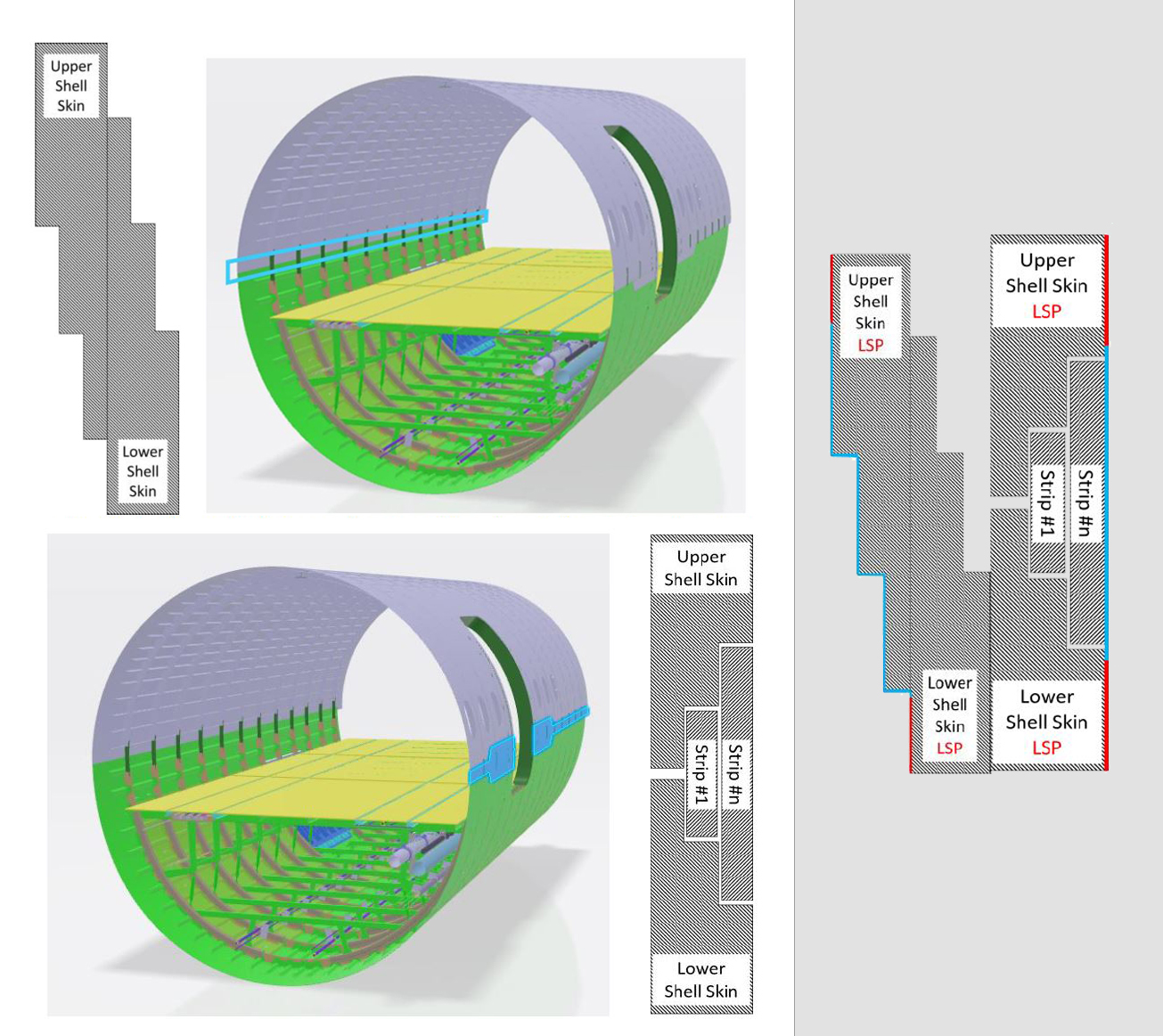
Longerons et clips soudés à un fuselage thermoplastique. SOURCE :Clean Sky 2 11 ème Appel à propositions JTI-CS2-2020-CfP11-LPA-02-35, « Caractéristiques innovantes d'arrêt du décollement pour les joints soudés thermoplastiques longs », Figure 2, p. 94.
Clips et supports soudés
Comme indiqué dans le sujet CFP10 JTI-CS2-2019-CfP10-LPA-02-31, tous les clips de cadre et supports de système pour le fuselage inférieur du MFFD seront fabriqués par moulage par injection de composés à fibres courtes fabriqués en réutilisant les déchets d'usine de le responsable du sujet GKN Fokker's production de stratifiés TPC à fibres continues. CF/PAEK est le matériau de base et le soudage est la méthode d'assemblage de base, bien que la méthode de soudage spécifique ne soit pas prescrite.
Selon le texte CFP10, le fuselage inférieur du MFFD aura 13 cadres et environ 36 longerons, nécessitant environ 500 clips de cadre (notez qu'il s'agit de structures primaires nécessitant des tests structurels et ce total comprend les clips utilisés pour les tests) et environ 270 supports de système (qui sont structures secondaires) réparties selon les types indiqués ci-dessous :20 supports de système (1), 120 supports de système (2), 50 supports de système (3) et 80 supports de système (4).
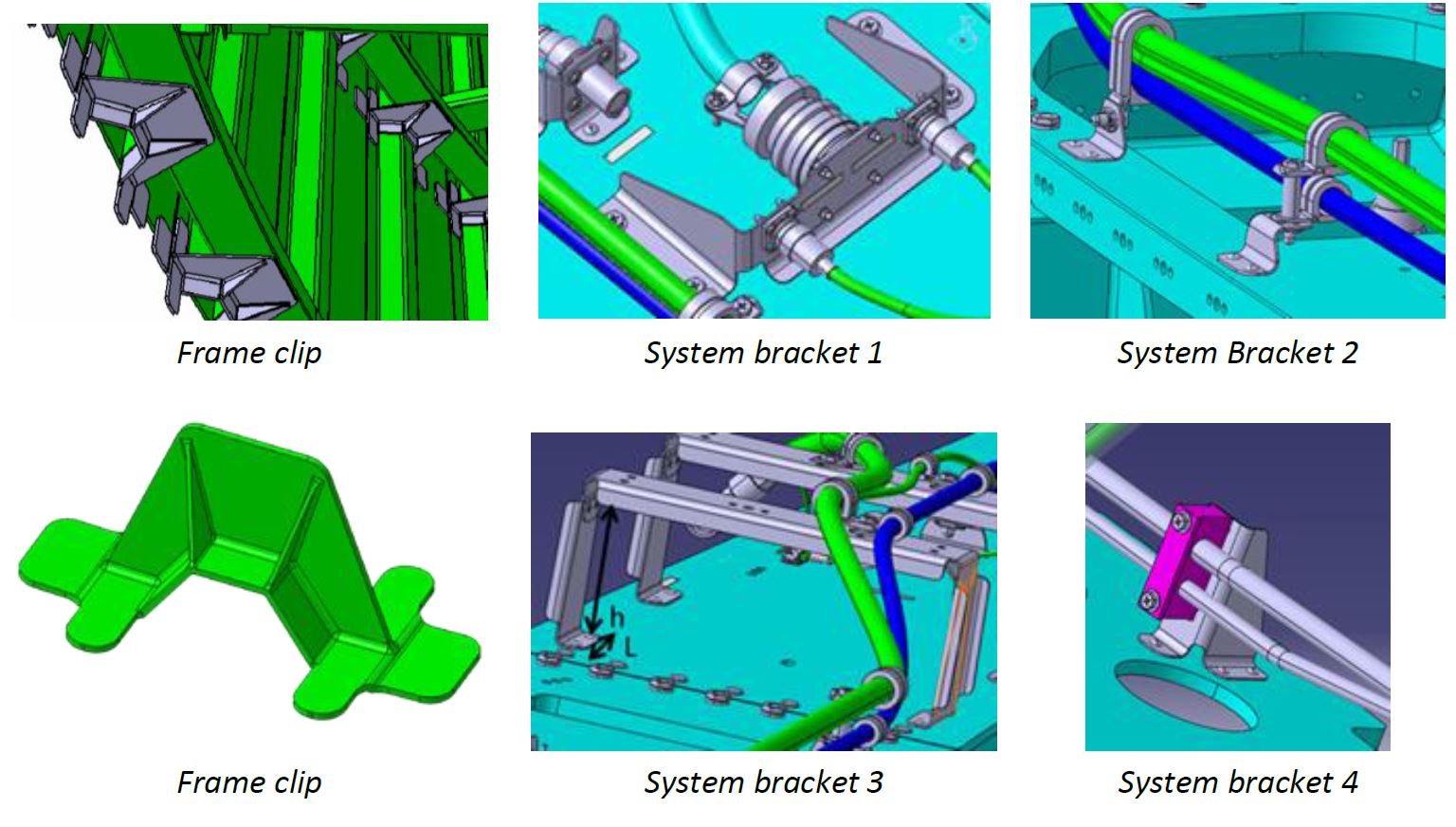
Exemples de pièces à livrer dans le sujet Clean Sky 2 JTI-CS2-2019-CfP10-LPA-02-31, Figure 2. SOURCE | Ciel propre 2 CFP10, p. 146.
Le CFP10 contient également le sujet du fuselage supérieur MFFD JTI-CS2-2019-CfP10-LPA-02-30, « Développement de systèmes de soudage innovants pour les joints structurels des composites à matrice thermoplastique » dirigé par Aernnova Composites Illescas (Illescas, Espagne). Prévu pour commencer après le 1er trimestre 2020, son objectif est de développer un système de soudage pour réaliser une liaison structurelle entre les pièces de renforcement (goussets, cales, ferrures) et les cadres structurels pour obtenir une structure d'encadrement de porte (DSS) hautement intégrée. J'espère donner plus de détails sur le fuselage supérieur du MFFD dans un futur blog. Pour l'instant, il suffit de comprendre pourquoi le work package 3 de MECATESTERS est important et combien sera réalisé une fois MECATESTERS, STUNNING et le MFFD terminés.
Rejoindre les deux moitiés
Une fois terminé, la moitié inférieure du MFFD ira à l'Institut Fraunhofer de technologie de fabrication et de matériaux avancés IFAM (Stade, Allemagne) pour être jointe à la moitié supérieure, explique Veldman. « Nous nous sommes engagés à livrer notre moitié du fuselage d'ici la fin 2021 », ajoute-t-il.
Comme indiqué ci-dessus, Ralf Herrmann chez Airbus est le chef de projet MMFD; ainsi, Airbus intègre les travaux de Fraunhofer IFAM et du consortium CFP07 MultiFAL (Multifunctional automation system for Fuselage Assembly Line) —pour développer des solutions à la myriade de défis.
Certains d'entre eux sont révélés dans deux sujets du 11 e Appel à propositions (novembre 2019), tous deux menés par Airbus pour débuter après le quatrième trimestre 2020 et intitulés « Outillage, équipements et auxiliaires pour la fermeture d'un joint cylindrique longitudinal : »
- JTI-CS2-2020-CfP11-LPA-02-33, " :Intégration de la sangle de serrage et continuité de la protection contre la foudre"
- JTI-CS2-2020-CfP11-LPA-02-34, " :Intégration du joint de chevauchement et de l'accouplement de cadre"
Écrit par Piet-Christof Woelcken, responsable de sujet chez Airbus Bremen et responsable du work package MFFD, les principaux défis de ces sujets incluent :
JTI-CS2-2020-CfP11-LPA-02-33
- Joint de sangle de crosse (Fig. 3 ci-dessous) :
- Le côté gauche du démonstrateur (dans le sens du vol) comprend le contour de porte passager. La variation de l'épaisseur de la peau dans cette zone nécessite une intégration de sangle de crosse étagée, joignant les peaux supérieure et inférieure.
- Compte tenu de la complexité du joint, soudage par conduction l'utilisation d'une plaque de pression chauffée est la technologie d'assemblage préférée.
- Continuité électrique de la protection contre la foudre (Fig. 4 ci-dessous) :
- La continuité électrique de la protection métallique contre la foudre (LSP) doit être réalisée à travers les deux joints longitudinaux à l'extérieur du fuselage.
- Il est prévu que la tête d'outillage fournie pour l'intégration de la sangle de crosse puisse être utilisée à cette fin.
JTI-CS2-2020-CfP11-LPA-02-34
- Joint de chevauchement (Fig. 2 ci-dessous) :
- Le joint de chevauchement de 8 mètres de long sur le côté droit des démonstrateurs (dans le sens du vol) relie les peaux supérieure et inférieure du fuselage. Dans une direction longitudinale, l'épaisseur de peau inférieure à 3 mm est constante dans la zone de soudage. Dans la direction circonférentielle, les peaux présentent une géométrie étagée pour des performances structurelles améliorées.
- Soudage par ultrasons est l'assemblage préféré afin d'atteindre un taux de production élevé.
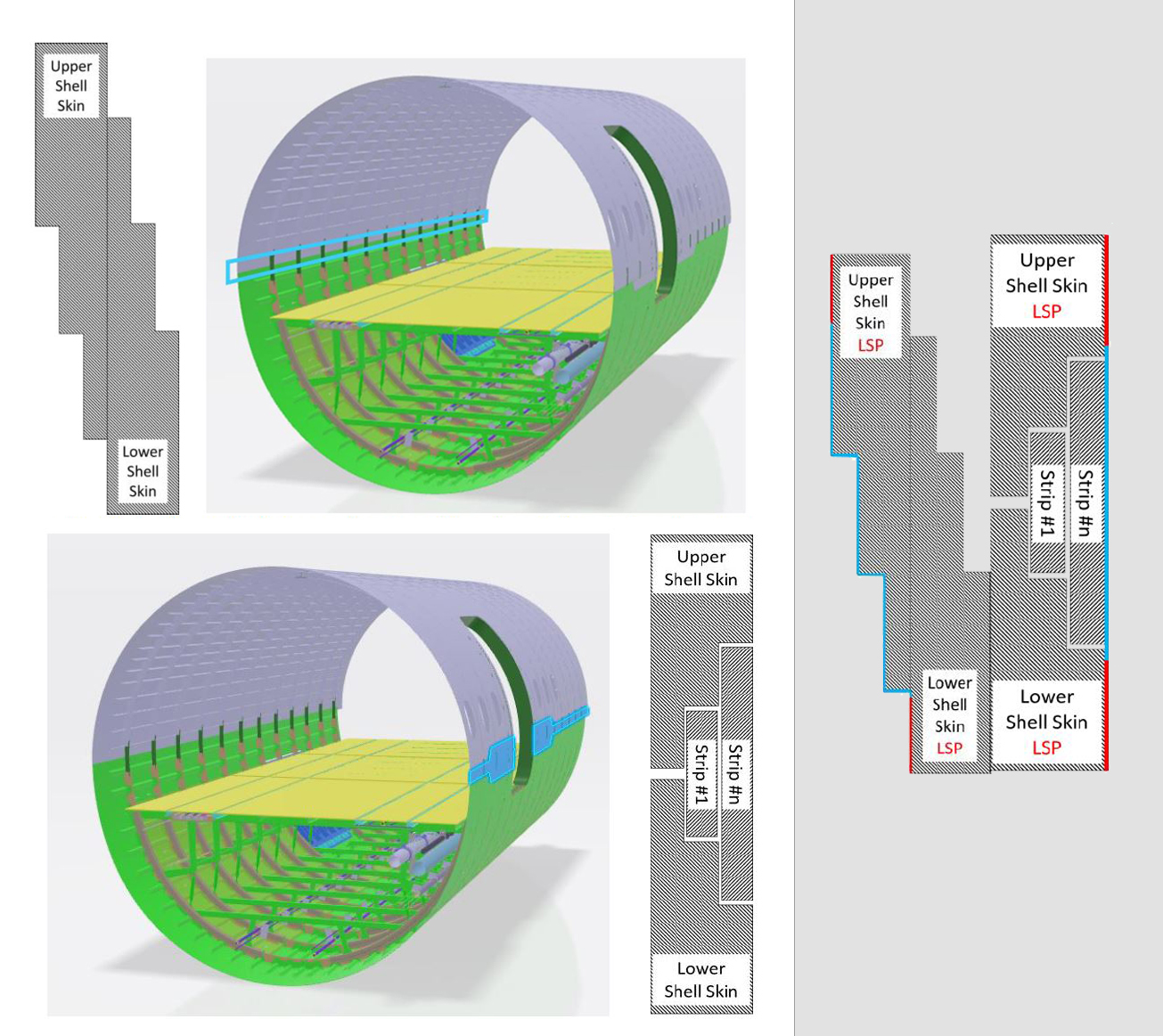
Fig. 2 (En haut à gauche) :Joint de chevauchement :Une approche par étapes a été adoptée dans la conception du joint de chevauchement. Notez que la coque inférieure se trouve sur le côté intérieur du fuselage. Fig. 3 (En bas à gauche) : Intégration de la sangle de bout à bout :un certain nombre de bandes superposées nécessitent une intégration à travers le joint étagé. Notez que la sangle de crosse se trouve à l'extérieur du fuselage. Fig. 4 (Droite) :La continuité électrique du LSP métallique doit être réalisée à travers les joints longitudinaux à l'extérieur du fuselage CFRP. Le rouge indique le LSP pré-équipé, le bleu indique le LSP à appliquer dans le cadre de ce sujet. SOURCE | Clean Sky 2 11 ème Appel à projets JTI-CS2-2020-CfP11-LPA-02-33 et -34, « Intégration de sangles et continuité de protection contre la foudre », pp. 78 et 86.
JTI-CS2-2020-CfP11-LPA-02-34
- Intégration du couplage du cadre (Fig. 5) :
- Joint de chevauchement :les accouplements de cadre sous le joint de chevauchement doivent lier structurellement les cadres de coque supérieur et inférieur.
- Sangle de crosse :les accouplements de cadre sous la sangle de crosse doivent lier structurellement les cadres supérieur et inférieur de la coque ainsi que se connecter à la peau.
- Soudage par résistance est la technologie privilégiée pour ce défi technique.
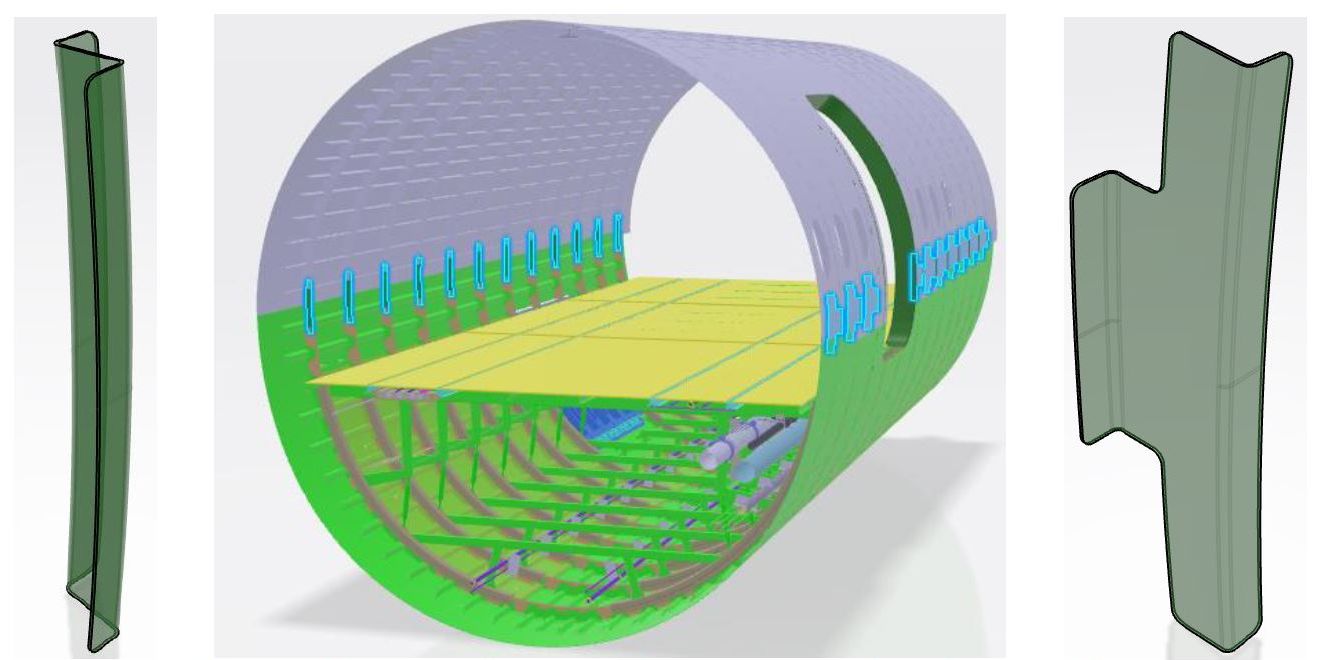
Intégration de couplage de cadre. Notez que les accouplements de châssis diffèrent d'un côté à l'autre dans le cadre de la démonstration technologique. SOURCE | Clean Sky 2 11 ème Appel à projets JTI-CS2-2020-CfP11-LPA-02-34, « Outillages, équipements et auxiliaires pour la fermeture d'un joint cylindrique longitudinal :intégration de joint de recouvrement et de couplage de cadre », Fig. 5, p. 86.
Méthodes de soudage, têtes d'outillage et tolérances
Herrmann explique que le soudage par conduction sera démontré du côté gauche via le joint bout à bout et le soudage par ultrasons du côté droit via le joint de chevauchement tandis que le soudage par résistance sera utilisé pour les accouplements de châssis. « MFFD démontrera de nombreuses approches techniques, ce n'est donc pas la même chose que la fabrication d'un vrai fuselage, mais est plutôt conçu comme un véhicule pour la démonstration et la maturation des technologies », ajoute-t-il.
Développement de têtes d'outillage de soudage
L'objectif de ces deux sujets écrits par Woelcken est de développer les têtes d'outillage nécessaires pour ces joints soudés. « Lorsque vous soudez deux pièces ensemble, vous devez appliquer de la chaleur et de la pression », explique-t-il. « Donc, cela est appliqué par la tête d'outillage pendant le soudage. Pour le procédé de soudage par conduction de type Fokker, vous appliquez activement de la chaleur et de la pression d'un côté et une pression passive d'un support est exercée de l'autre. Le joint bout à bout est un empilement de six rubans, et lors de l'assemblage, nous allons placer l'empilement et le chauffer pendant le soudage. Cependant, étant donné que le matériau du ruban LM PAEK UD est relativement nouveau dans le domaine du soudage, nous devons comprendre les conditions du processus et comment nous pouvons compenser les tolérances. Il faut donc définir les matériaux et l'épaisseur, ainsi que la géométrie de la tête d'outillage. »
« Notez que l'utilisation de ce type de joint bout à bout est un processus standard pour ce que nous faisons sur d'autres joints dans notre avion », souligne Woelcken. "Pour le MFFD, nous voulons laisser le fuselage supérieur et inférieur inchangé par rapport à cette pratique standard afin de minimiser la quantité de matériau que nous devons adapter."
Flexibilité dans les tolérances
Woelcken note que parce que les surfaces de soudage les plus hautes sont essentiellement fondues dans un liquide puis pressées ensemble, "cela donne beaucoup de flexibilité pour s'adapter aux tolérances". A noter, actuellement, avec thermoset ailes et fuselages en polymère renforcé de fibres de carbone (CFRP), ces problèmes de tolérance sont résolus en appliquant un adhésif de cale liquide. Bien que peu de gens veuillent en discuter publiquement, le problème général du calage dans les aérostructures composites a été largement reconnu et des initiatives pour le réduire et/ou l'éliminer ont été rendues publiques, comme la méthode d'assemblage Flexmont pour les empennages verticaux.
“ Nous espérons obtenir des avantages en matière de tolérances en utilisant des composites thermoplastiques », explique Woelcken, « en particulier en exploitant nos concepts de conception et en nous appuyant sur notre expérience avec le CFRP thermodurcissable et le soudage métallique. La clé sera la surveillance in situ pendant le chauffage et l'application de la pression. Il souligne que la chaleur est le paramètre numéro un. « Je suis surpris de la tolérance des procédés de soudage des composites thermoplastiques à la pression. Le principal défi est de contenir cette pression et de savoir comment elle diminue. Actuellement, nous surveillons la face arrière du joint soudé. »
Système d'usine d'assemblage automatisé Fraunhofer IFAM (en haut à gauche) avec les cotes au début du sujet de travail CFP07 (en haut à droite) est en cours de modification pour accueillir un fuselage à 360 ° pour le soudage des joints longitudinaux et circonférentiels du MFFD. SOURCE | Fraunhofer IFAM et cfk-valley.com, Clean Sky 2 7 ème Appel à projets, JTI-CS2-2017-CfP07-LPA-02-22, p. 76.
Automatisation d'assemblage
Dans le 7 e Appel à propositions, le sujet JTI-CS2-2017-CfP07-LPA-02-22, « Développement d'un système d'usine automatisé de grande taille pour les joints longitudinaux et circonférentiels du fuselage » est dirigé par Fraunhofer IFAM au sein du consortium MultiFAL. L'extrait ci-dessous met en lumière la manière dont les têtes d'outillage de soudage décrites ci-dessus, actuellement en cours de développement, pourraient être mises en œuvre :
« Pour réaliser le processus d'assemblage d'un fuselage thermoplastique, les tolérances deviennent un sujet majeur. The positioning and orientation of the fuselage shells, as well as resulting deformations caused by the welding process, need to stay within the tolerances. Comparable accuracies can be oriented to the state-of-the-art process of longitudinal joint. Here, the position error in each direction should be within 0.5 mm (in some exceptions up to 1 mm). … it can be assumed that a pre-load on the joint surface from both sides of approximately 1000N (independent of the welding technology) for a welding seam of 20 mm width is required by the automation system.”
Fraunhofer IFAM — which was also CTC Stade’s partner in developing the Flexmont VTP assembly process — describes its starting point:an in-house assembly plant system which can manipulate parts from 2 to 8 meters long and up to 6 meters high, including a 180° shell of a single-aisle aircraft. The system is enabled by a flexible arrangement of 10 cooperating hexapods (see “Reconfigurable Tooling:Revolutionizing composites manufacturing”), 24 linear units and modular rack elements. Vacuum grippers with 6-axis force and torque sensors adjust the pose and shape of the part, as required, to manage tolerances during assembly. The guidance and monitoring of these rapid, iterative adjustments is achieved through optical measuring devices.
According to the CFP07 text, Fraunhofer IFAM will modify this assembly plant system for holding a complete 360° fuselage, with work scheduled to begin in Q2 2018 and completed in 36 months.
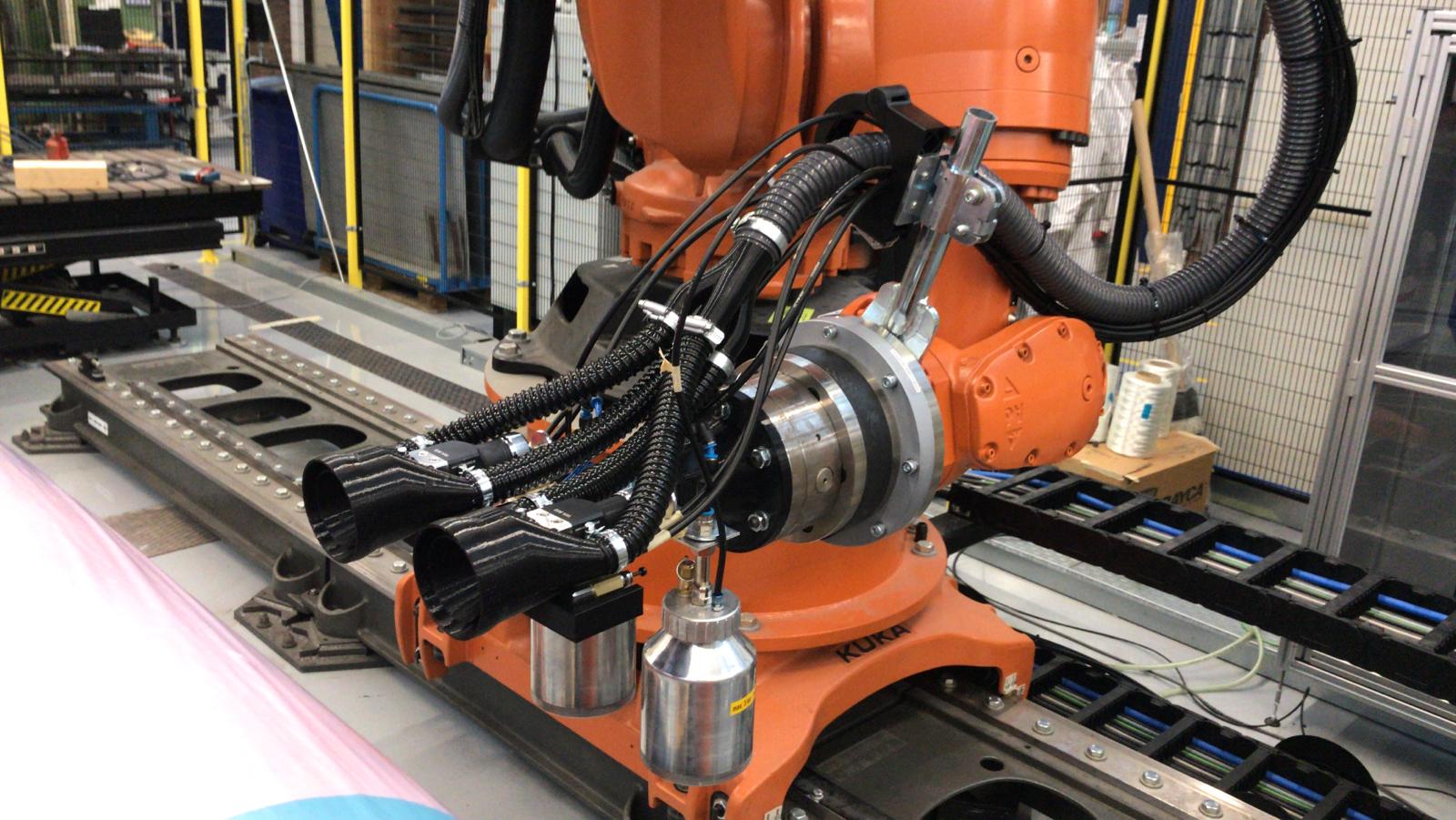
The STUNNING consortium is working with SAM|XL to develop automation for assembling the MFFD lower fuselage. SOURCE | samxl.com
Within STUNNING, activities are planned with the collaborative research center SAM|XL (Smart Advanced Manufacturing XL, Delft, Netherlands) to demonstrate automated welding techniques for assembling the lower fuselage. Specializing in automation for manufacturing large, lightweight composite structures, SAM|XL brings together TU Delft’s Aerospace Engineering group and Robotics Institute. GKN-Fokker is a major participant. One of the methods being investigated is sequential spot ultrasonic welding, which was proven in the Clean Sky 1 Eco Design project and TAPAS 2 as a fast and effective for connecting short fiber-reinforced brackets or clips to fuselage structures.
In her 2016 paper, titled “Smart ultrasonic welding of thermoplastic composites,” Villegas states that it is possible to scale up the ultrasonic welding process via sequential welding — that is, letting a continuous line of adjacent spot welds serve the same purpose as a continuous weld bead. Lab-scale sequential spot welding was used in the Clean Sky EcoDesign demonstrator’s TPC airframe panel, using flat energy directors to weld a CF/PEEK hinge and CF/PEKK clips to CF/PEEK C-frames (Fig. 6). Experimental comparisons with mechanically fastened joints in double-lap shear and pull-through tests showed promise. The process is further explored in 2018 papers {and 2019 papers} by Villegas’ TU Delft team member Tian Zhao {and in Villegas’ 2019 paper}.
— “Welding thermoplastic composites”, G. Gardiner, 2018.
The STUNNING consortium’s work with TU Delft and SAM|XL is adapting this technology to weld multiple system and semi-structural brackets, stiffening elements and stringers to the MFFD lower fuselage shell.
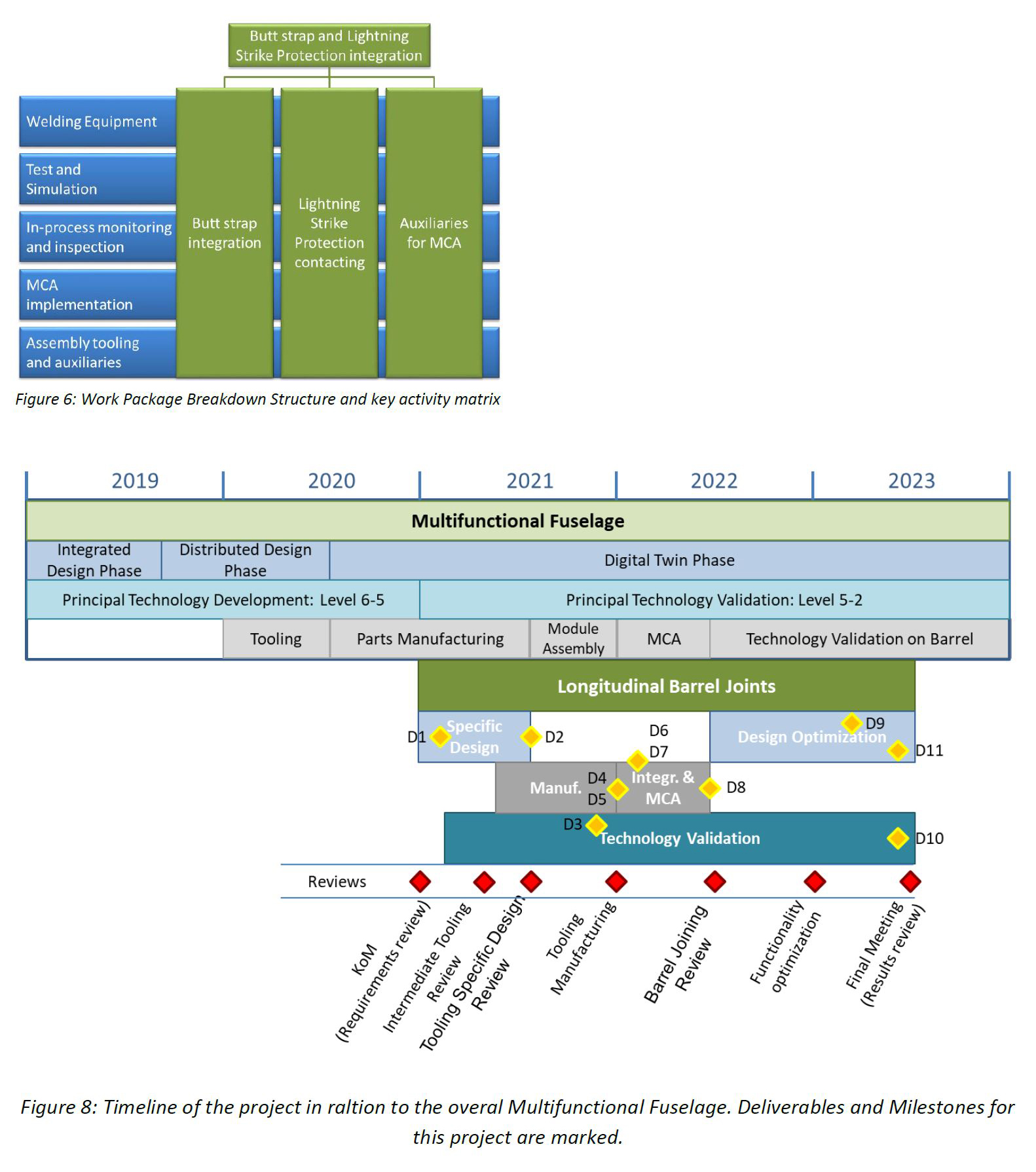
Work breakdown and timeline for MFFD assembly. SOURCE | Clean Sky 2 11 th Call for Proposals JTI-CS2-2020-CfP11-LPA-02-33, “Tooling, Equipment and Auxiliaries for the closure of a longitudinal Barrel Joint:Butt strap integration and Lightning Strike Protection continuity”, pp. 79 and 82.
Digital twin phase, 2020 and beyond
According to the Clean Sky website, the MFFD program reached an important milestone in Nov 2019 with the successful passing of its Critical Design Review (CDR). In the timeline above, the MFFD design enters a “Digital Twin Phase” in 2020-2021. Qu'est-ce que ça veut dire? “Though we have wrapped up the majority of the design phase, we are taking it a bit further by working with a specific lifecycle management approach,” explains Herrmann. “We are modeling imperfections and nonconformities from the NDT results and process parameters during component manufacturing. We want to combine this Industry 4.0 data with lifecycle management so that we continue to tailor the design according to what we are actually manufacturing. We want to see how far we can push this and what we can accomplish by the end of Clean Sky 2.”
For 2020, the chief agenda is manufacturing. “We hope to present various parts as they come together this year,” says Veldman. What will the largest challenge be for the STUNNING program? “Assembly,” he answers. “Not so much within STUNNING, but our lower fuselage has interfaces with the door surround structure, multiple Airbus-delivered components and the whole upper fuselage. Getting everything delivered at the right time and then bringing it all together will require a number of developments yet.”
That brings us to perhaps the biggest question:Will thermoplastic composites be used on the next aircraft entering production in 2030-35? “For sure, we want to try to use the technologies we are working on,” says Herrmann, “but I cannot say if or when thermoplastic composites will be on future aircraft. The most important part for us is that they are an enabler for dustless joining regarding ramping production to more than 70 aircraft per month. We have to show that it is feasible, not only with metallics but also with thermoplastic composites.”
“By the end of this project, we will have a more complete understanding of thermoplastic composite welding and will gain approval for its use in large primary aircraft structures,” says Salat. “If we can use this for future aircraft, we can achieve significant weight savings and improved sustainability.” But perhaps just as important is Clean Sky’s ability to bring Europe’s aviation research and innovation stakeholders closer together. “We have quarterly meetings where I sit with all of the LPA steering committee,” says Veldman. “I’m talking to the whole of the European aerospace industry, and it most certainly helps to open up opportunities for the future, not only for companies who can supply to us, but for a wide range of collaborations.”
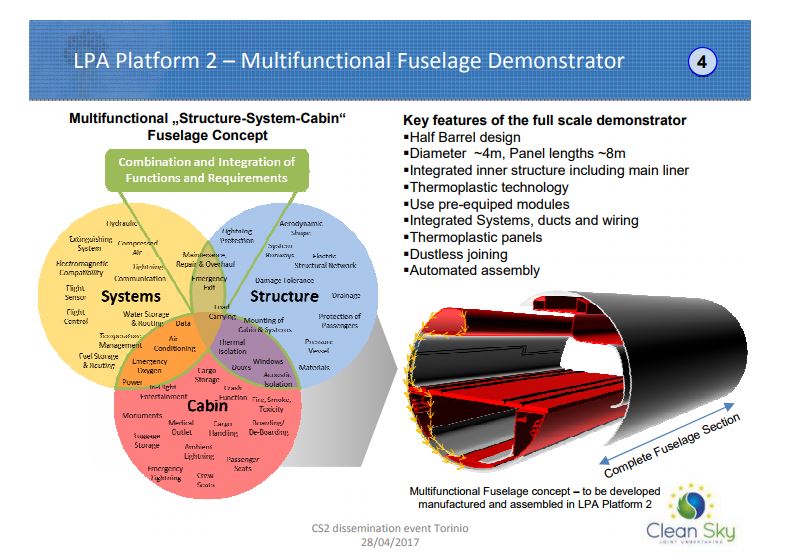
Résine
- 10 startups d'impression 3D à surveiller en 2020
- L'application en vedette :l'impression 3D pour les cabines d'avion
- Extraire la valeur des données pour l'IA
- 6 conseils de soudage pour l'entretien de l'usine
- Vous cherchez un plastique ultra résistant ? Découvrez FR-4 !
- Matériaux :composés et concentrés de qualité médicale pour le soudage laser
- Partenaire Victrex et Bond pour l'impression 3D de pièces PAEK
- La première section de fuselage composite pour le premier jet commercial composite
- Les meilleurs conseils pour souder l'aluminium