Kanfit fait face au COVID-19 et gère sa croissance à l'aide des systèmes Composites 4.0
Alors que je prépare un article sur la numérisation de la production de composites pour notre numéro de juillet, j'ai interviewé Shachar Fine, vice-président exécutif du développement commercial, du marketing et des ventes pour Kanfit Ltd. (Nof-Hagalil, Israël), un fabricant de composites diversifié et à forte croissance et de niveau aérospatial fournisseur. CW a brièvement mentionné l'utilisation de capteurs Bluetooth par Kanfit dans notre série 2018 de visites d'usines en Israël (voir « Un pionnier florissant de l'aérospatiale crée des affaires… »). Dans ce blog, j'explorerai plus en détail ce système basé sur l'intelligence artificielle (IA).
Faire face au COVID-19
Mais d'abord, Shachar Fine et moi avons brièvement discuté de la façon dont Kanfit gère le COVID-19 et maintient la production de composites. "Le gouvernement israélien a émis des directives selon lesquelles certaines entreprises" non essentielles " doivent fermer (par exemple, les gymnases, les salons, etc.)", explique-t-il, "mais celles définies comme" essentielles "(par exemple, COVID-19 et les fournitures de soins de santé, nourriture, etc.) peuvent travailler en tout cas tant que les employés restent à au moins deux mètres l'un de l'autre. L'industrie de la défense peut avoir jusqu'à 50 % de ses employés et l'industrie restante peut avoir jusqu'à 30 % de sa main-d'œuvre, tant que ces entreprises respectent l'exigence de distance. »
« Nous embauchons jusqu'à 50 % de nos employés par quart de travail et exécutons deux quarts de travail », déclare Fine. « Une troisième équipe ne s'est jamais justifiée car la productivité était tout simplement trop faible. Même maintenant, nous ne le ferons pas. Mais nous prolongeons certains de nos quarts de travail. Par exemple, dans les départements tels que l'usinage, où les employés surveillent principalement les équipements automatisés, nous effectuerons des quarts de travail de 12 heures. Mais pour les services où les travailleurs effectuent davantage de tâches manuelles, nous effectuerons des quarts de travail de 8 à 10 heures. » Il explique qu'il s'agit essentiellement d'aider à compenser la perte de productivité due à la distanciation sociale requise.
Fine a indiqué qu'il aimerait savoir comment les autres fabricants de composites s'adaptent. « Je suis sûr que je pourrais apprendre de ce que font les usines de composites dans d'autres parties du monde. Je fais partie d'un groupe de développement commercial sur WhatsApp ici en Israël et nous partageons des conseils sur la façon de poursuivre le développement commercial lorsque vous ne pouvez pas vous rencontrer ou voyager. Bien sûr, la priorité est de garder tout le monde en sécurité et en bonne santé. »
Bluetooth vs système RFID
Comme expliqué dans l'article de la tournée 2018, le système installé par Kanfit a été fourni par une start-up de Tel-Aviv, Trekeye. Le système comprend des balises Bluetooth (sans fil) qui sont attachées au voyageur de chaque pièce, c'est-à-dire le bon de travail qui voyage avec la pièce.
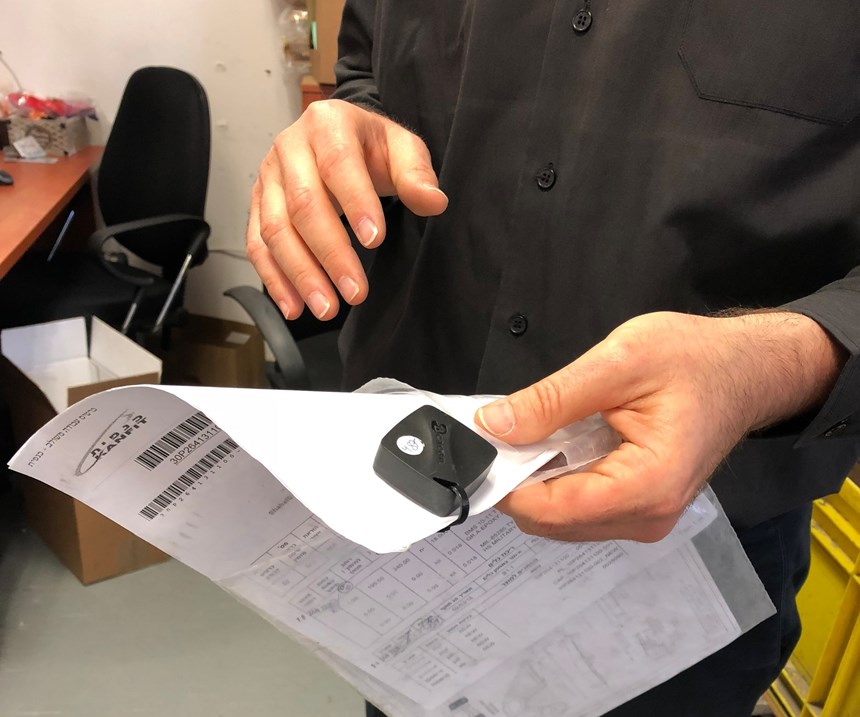
Lorsque le bon de travail d'une pièce est imprimé, l'étiquette y est attachée puis livrée à la production. Pour les pièces composites, les prochaines étapes pourraient inclure la découpe et la mise en kit automatisées de préimprégnés ou de renforts secs, le drapage, le préformage/le dégrossissage, le moulage par transfert de résine (RTM) ou l'ensachage sous vide et le durcissement à l'autoclave, le rognage, les tests non destructifs (CND) et la peinture. En règle générale, il y a plusieurs inspections entre ces étapes. La chaîne de processus pourrait également inclure l'assemblage de petites et grandes pièces métalliques dans des modules plus grands. La production de tels modules, y compris l'installation de divers systèmes (par exemple, le câblage, l'isolation, l'alimentation distribuée, etc.) est une tendance croissante pour les fournisseurs de niveau aérospatial. Une fois la chaîne de processus terminée et la pièce/l'assemblage prêt à être expédié, l'étiquette Bluetooth est retirée et réutilisée sur un nouveau bon de travail.
Fine explique que ce sont des balises, pas des capteurs. « Une étiquette ne détecte pas mais transmet simplement un signal », note-t-il. Dans ce cas, chacune des balises Bluetooth transmet son numéro de série toutes les 10 secondes. « Les antennes reçoivent ces signaux et triangulent la position de chaque balise », explique Fine. Le dernier composant du système est le logiciel, qui collecte les données, applique des algorithmes pour les analyser et répond par des alarmes et/ou des actions suggérées. Les balises Bluetooth sont alimentées par batterie, mais le logiciel alerte lorsque les batteries sont faibles en charge et que les batteries durent plus d'un an.
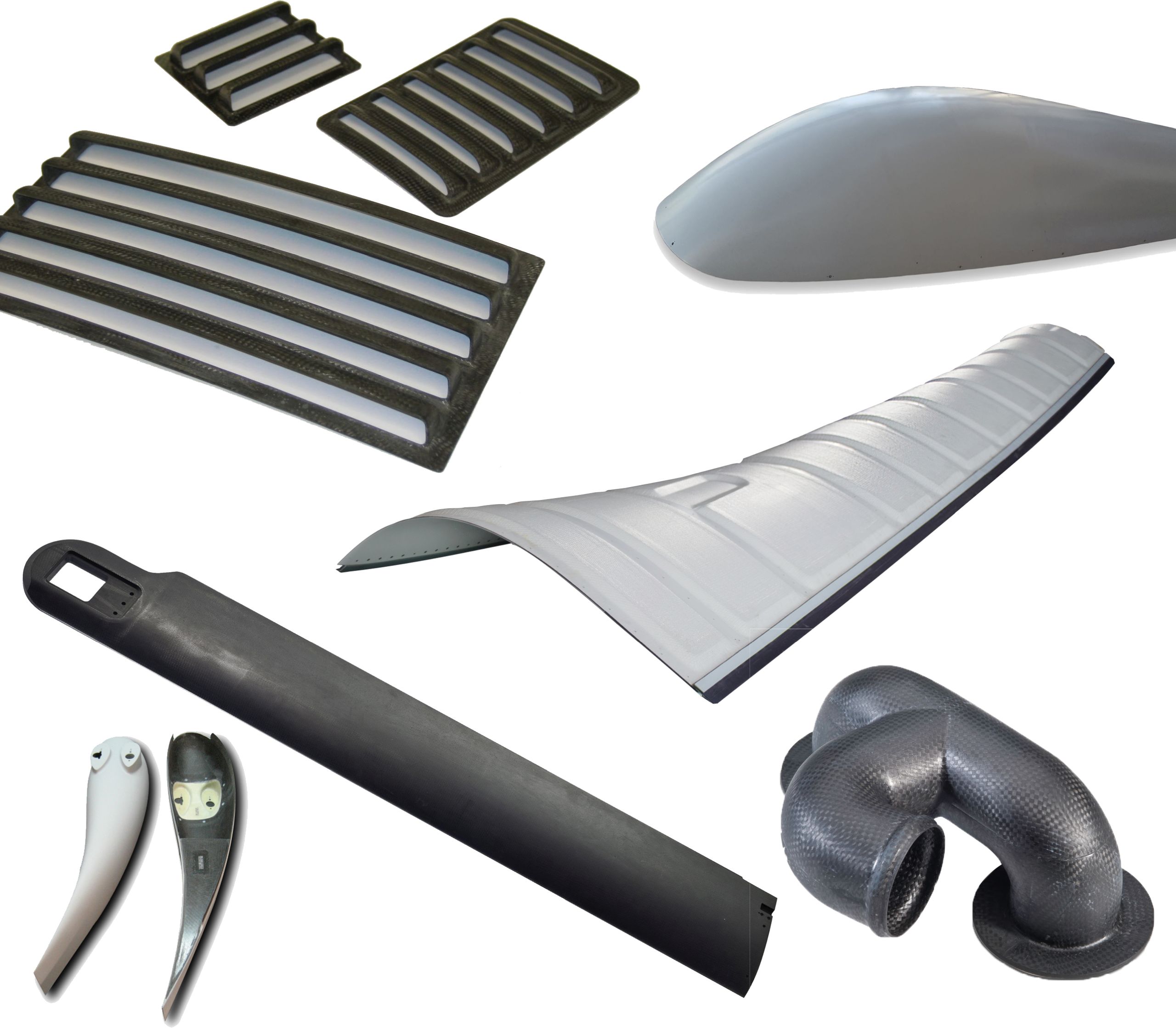
Kanfit a exploré l'utilisation d'étiquettes RFID, mais parce qu'elles utilisent des radiofréquences (champs électromagnétiques) pour transmettre des données, le métal interfère avec le signal. « Nous avons beaucoup de métal dans notre environnement de production », explique Fine. « Donc, vous devez penser à l'endroit où placer les antennes RFID dans le bâtiment afin que le signal de chaque étiquette soit toujours reçu. Si les étiquettes RFID ne s'enregistrent pas périodiquement, l'ensemble du flux de données est compromis. Avec nos balises Bluetooth, nous avons prouvé l'enregistrement à 100%. Nous les avons jetés avec des pièces métalliques et les avons placés près de différentes antennes. À chaque fois, le système a récupéré 100 % des balises."
Une autre différence, explique-t-il, est que les balises Bluetooth sont actives, envoyant un signal, tandis que les balises RFID sont généralement passives - leurs signaux ne sont captés que s'ils passent par une antenne située de manière appropriée. « Avec les balises Bluetooth, vous positionnez les antennes là où vous souhaitez que le système signale des pièces », explique Fine. "Il n'y a donc pas de contrainte technologique comme avec le système RFID. Vous pouvez placer les antennes sur un mur, un plafond ou un poste de travail. Où vous les placez et combien vous en utilisez dans une zone dépend de la résolution dont vous avez besoin. Pour Par exemple, dans une zone d'attente, une antenne au plafond est suffisante, mais dans une zone comportant plusieurs étapes de processus, vous aurez peut-être besoin de plusieurs antennes.
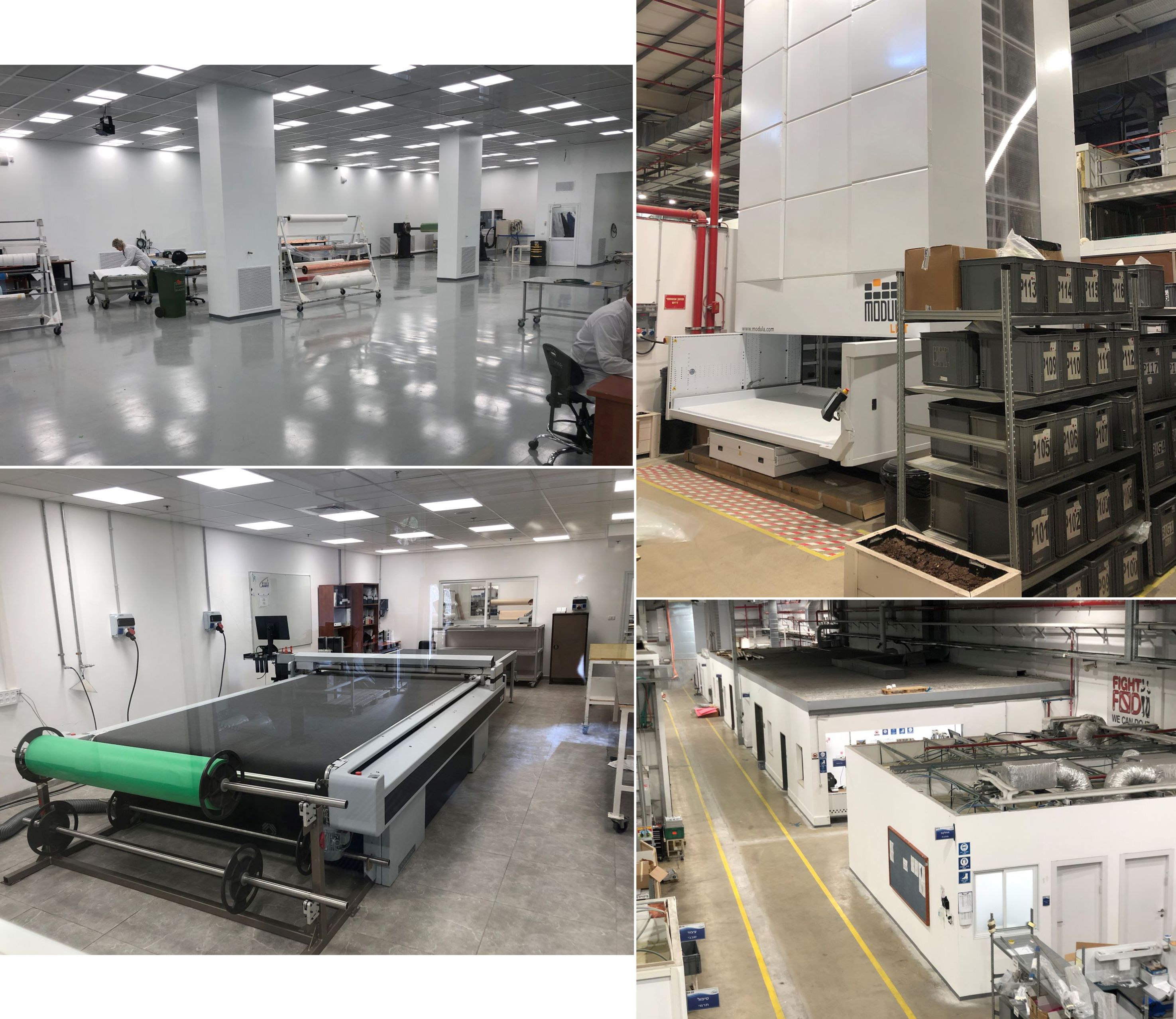
Un inconvénient du système Bluetooth Kanfit installé à partir de Trackeye est son coût. « Il y a beaucoup d'infrastructures », dit Fine, « et ces balises Bluetooth coûtent des dollars, pas des centimes comme les balises RFID. » Il y avait également un développement important nécessitant que les développeurs de Trekeye soient sur place. « Ils nous ont aidés à localiser les antennes afin que les informations que nous collections soient optimisées pour ce que nous essayions d'accomplir », explique-t-il. «Ils nous ont appris comment résoudre les problèmes de chevauchement des zones d'antennes afin que le système ne soit pas confus par une étiquette lue par deux antennes à la même intensité. C'était un processus."
Plans des parties et graphiques en spaghetti
Une fois le système installé et en cours d'exécution, les résultats qu'il a renvoyés comprenaient des cartes de pièces et des graphiques en spaghetti. « Notre service informatique avait la carte en ligne ouverte pour le système en permanence », explique Fine. « Lorsqu'un ouvrier cherchait une pièce, il se rendait au service informatique, localisait rapidement la pièce, puis allait la récupérer dans l'usine. C'était très facile de voir où étaient toutes les pièces. »
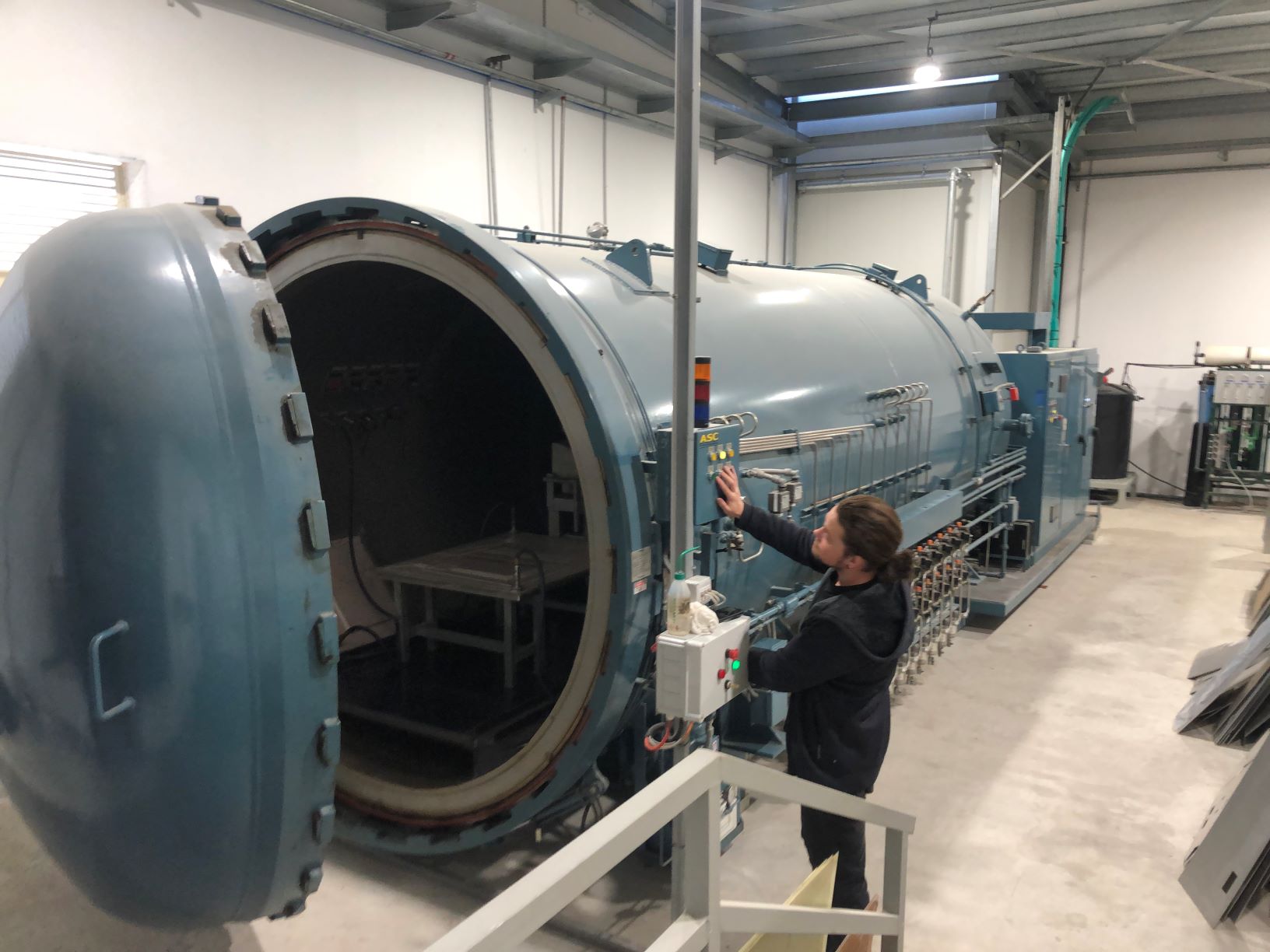
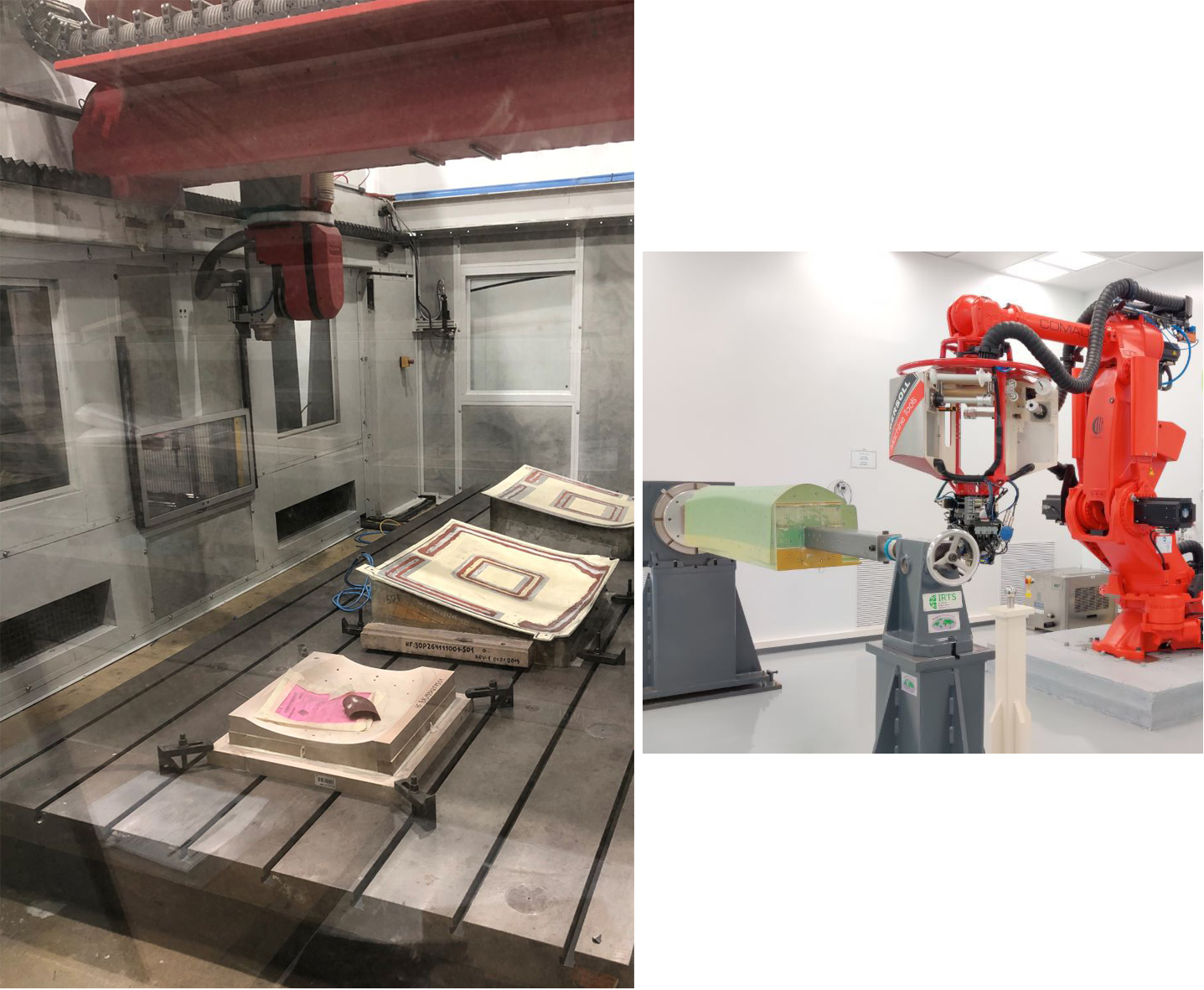
Il explique que Kanfit a des milliers de pièces partout dans l'atelier de production (3 000 bons de travail ouverts chaque minute), « et ce n'est pas une chaîne de montage standardisée. Le mélange de pièces en cours change et certaines pièces nécessitent des étapes différentes des autres. Par exemple, toutes les pièces ne sont pas autoclavées ou usinées. Quand vous voyez une pièce, vous ne savez pas toujours si elle est au bon endroit. Vous devez vérifier les documents de la pièce pour comprendre cela »
Le système Trekeye, cependant, fonctionnait étonnamment bien. « Même s'il ne s'agissait pas d'un système bon marché, le retour sur investissement (retour sur investissement) était très court », explique Fine. « Le système a une IA très avancée. Il n'a pas attendu qu'une pièce manque. Il enverrait un SMS (message texte) au gestionnaire que la partie "ABC" est allée à la mauvaise station. Il n'y avait pas d'attente. Le système alertait lorsqu'une pièce ne suivait pas son itinéraire normal."
Ces routes ou chemins partiels sont indiqués sur ce qu'on appelle des cartes en spaghetti. « Ceux-ci montrent les chemins des pièces à travers notre usine et nos chaînes de processus », explique Fine. « Nous commencions à voir des tendances. Par exemple, lorsque les ingénieurs créaient les bons de travail pour les pièces, ils mettaient en place des étapes d'inspection en fonction de leurs connaissances et de leur expérience. Les pièces seraient d'abord inspectées avant de passer à la station suivante. Les graphiques en spaghetti montreraient que vous pouvez modifier certaines actions et réduire la distance parcourue par les pièces. On verrait une partie aller-retour entre les départements pour de multiples actions. Nous nous asseyions ensuite avec l'ingénierie et nous demandions pourquoi cela va-t-il dans les deux sens ? Comment réduire de quatre fois à deux, par exemple ? C'est facile à voir dans le graphique mais difficile à voir dans les opérations quotidiennes réelles sur le terrain, et aussi quel est l'effet réel de ces allers-retours sur la production globale. Vous pouvez voir les étapes sous forme d'éléments de ligne au fur et à mesure que vous les écrivez dans le bon de travail, mais voir les chemins dans le graphique en spaghetti représente davantage de données et une visualisation de ces données qui a un impact réel. »
« Cela nous a également aidés alors que nous emménagions dans notre nouvelle installation plus grande », ajoute Fine. « L'une des leçons que nous avons apprises est de centraliser le service d'inspection dans la zone de production. Ainsi, au fil du temps, je suis sûr que l'IA continuera à nous aider à mieux localiser les machines et les stations, et même si nos pièces et nos opérations changent au fil du temps. Il peut également suivre les outils. »
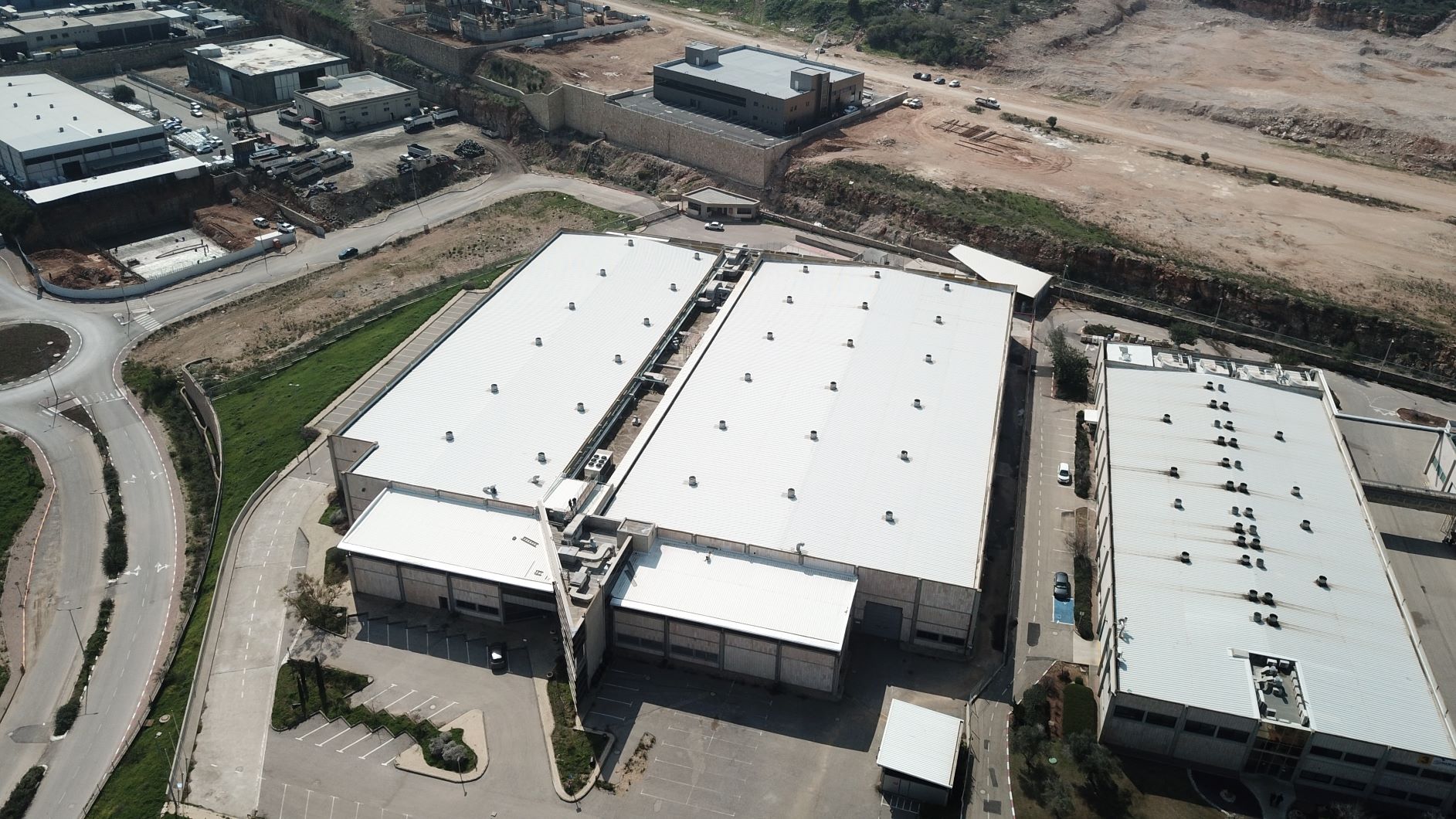
Un autre avantage est que Kanfit peut suivre le temps qu'une pièce passe à chaque station. "Bien que nous n'ayons pas encore mis en œuvre cela, cela pourrait réduire le temps que les employés passent à saisir ces données", note Fine. « Nous avons toujours un système ERP dans lequel les employés se rapportent, mais le système de balises Bluetooth a donné de meilleurs détails sur le moment où une pièce est entrée et a quitté une station, etc. »
Fine note que ces systèmes de surveillance des pièces et des outils ne remplacent pas l'ERP mais doivent être intégrés pour fonctionner avec lui. « Nous continuons à développer notre système ERP en interne car nous avons de gros clients et chacun d'entre eux a ses propres exigences. Nous devons donc beaucoup développer notre système afin de fournir toutes les informations souhaitées par chaque client. » Mais il voit la puissance de la technologie Bluetooth tag/AI pour améliorer ces systèmes, et l'avantage qu'il offre en termes d'efficacité supplémentaire.
Pas de saisie de données
Avez-vous dû saisir beaucoup de données pour chaque pièce lorsque vous avez créé le bon de travail et fixé le capteur ? "Non, c'est la partie la plus étonnante", dit Fine. « Il n'y a pas eu de saisie de données. C'est le système d'IA. Tout ce qu'il a reçu était les numéros de commande de travail. Ceux-ci comprennent des lettres et des chiffres, mais il y a une sorte de logique dans la façon dont nous les proposons et ce qu'ils signifient. L'IA doit avoir appris cela. Une fois qu'il a commencé à collecter des données, il a appris où les pièces devaient être. Par exemple, tous les bons de travail « ABC » portaient uniquement sur le métal et n'étaient jamais destinés au département des composites. Ainsi, lorsqu'une pièce métallique arrivait par erreur au département composites, le système s'alarme. Même les concepteurs de l'IA ont été surpris de la rapidité avec laquelle le système a appris. Nous avons initialement testé 100 pièces. Il a appris au sein de ce premier lot. »
Fine explique que c'est pour cela que le système a été conçu. Trekeye a commencé dans les hôpitaux, en travaillant avec une entreprise de maintenance d'appareils médicaux mobiles qui aidait à entretenir les brassards de tension artérielle, les thermomètres, les moniteurs, etc. Cette entreprise se plaignait de passer 80 % du temps du technicien de maintenance à rechercher les appareils nécessitant une maintenance. « Avec ce système en place, le technicien entrerait, se connecterait au système et verrait exactement où se trouvaient tous les appareils dans l’hôpital », explique Fine. « Un avantage supplémentaire était que le vol a diminué. Chaque fois que quelqu'un sortait avec un appareil, le système sonnait une alarme et un agent de sécurité était envoyé pour récupérer l'appareil."
Mise en œuvre future
Malheureusement, Trekeye n'a pas franchi l'étape critique de la « Vallée de la mort » en tant que startup et ne fonctionne plus. « Nous avons tout ce dont nous avons besoin pour faire fonctionner le système, à l'exception de quelqu'un pour le superviser », déclare Fine. « Pour ce type de système, vous ne pouvez pas simplement avoir un informaticien général. Vous avez besoin de quelqu'un de très compétent en IA. Nous venons également de finir d'emménager dans nos nouvelles installations et n'avons pas encore réinitialisé le système. » Il a cherché une autre entreprise faisant quelque chose de similaire, mais dit qu'il n'a encore rien trouvé qui réponde aux besoins de Kanfit. "Nous allons bientôt trouver un moyen de le remettre en service", ajoute-t-il.
Alors, quel est le vrai avantage ? « Premièrement, tout ce que vous ne pouvez pas mesurer, vous ne pouvez pas le gérer », déclare Fine. « Deuxièmement, la quantité de données dont nous disposons est si énorme, même pour nous en tant que petite usine, que nous avons dépassé le stade d’avoir une ou plusieurs personnes pour pouvoir traiter toutes ces données. Je ne peux même pas imaginer ce que cela doit être pour Boeing ou Airbus. Il faut que les machines se parlent maintenant. Laissez-les faire ce pour quoi ils sont bons et laissez-nous, les humains, avoir une vue d'ensemble et développer de nouvelles solutions basées sur ce qu'ils peuvent nous montrer."
Restez à l'écoute pour plus de blogs sur Composites 4.0 et CW article de fond de juillet.
Résine
- Comment concevoir des systèmes IoT industriels avec DDS et LabVIEW 2017
- Fabrication additive avec des composites dans l'aérospatiale et la défense
- Braskem s'associe à l'université pour une production de plastique durable utilisant la capture et l'utilisation du CO2
- Les systèmes ERP et MES peuvent-ils suivre l'IIoT ?
- Faire face au Black Friday 2020 et au "Crazy Thursday" des fabricants
- TxV Aero Composites est conforme aux normes AS9100
- Composites One et IACMI organisent un atelier de deux jours
- Impression 3D de composites avec fibre continue
- Associer l'IA et la robotique à plusieurs systèmes d'inspection