L'industrialisation de l'époxy thermoplastique
Cecence (Salisbury, Royaume-Uni) a été fondée en 2014 par trois fondateurs avec des décennies d'expérience dans les composites. Le directeur Mike Orange a une longue histoire dans le gréement et les mâts en polymère renforcé de fibres de carbone (CFRP) pour yachts. Responsable de l'innovation Humphrey Bunyan était auparavant responsable de l'innovation chez Future Fibres (Valence, Espagne). "Ils [Future Fibres] fabriquaient un gréement entièrement composite pour l'America's Cup et d'autres navires de course, ainsi que des attaches en CFRP pour maintenir les roues sur les voitures de Formule 1", explique Orange (voir "Composites de construction de yachts:Rigged for success"). « Nous avons compris les avantages du poids léger, mais nous nous sommes engagés avec d'autres secteurs qui n'avaient pas notre expérience et ont eu des difficultés avec les coûts, en intensifiant la fabrication et en respectant les réglementations en matière d'incendie. »
Ainsi, Cecence (prononcé « see-sense, comme dans le sens commun avec les composites en fibre de carbone) a été fondée pour se concentrer sur la résistance au feu, la fabrication industrialisée et la durabilité. Cela a abouti à des développements tels qu'un dossier de siège en composite de fibre de carbone/biorésine moulé par compression pour les avions de passagers qui ne pesait que 7,5 kilogrammes, une épaisseur de siège réduite à moins de 20 millimètres et un espace passager accru et confort, tout en répondant à toutes les exigences en matière d'incendie, de fumée et de toxicité (FST).
« Dans un projet précédent, Cecence avait développé une méthode de fabrication par presse à chaud qui a réduit le temps de cycle de 2,5 heures à 7 minutes pour un dossier de siège de classe économique utilisant des phénoliques à durcissement instantané développé avec le préimprégné britannique FTI (Somerset) », déclare Orange. Pour ce dernier dossier de siège décrit ci-dessus, qu'elle a développé avec Design Q (Redditch, Royaume-Uni), Cecence a élargi sa gamme FST en utilisant une résine préimprégnée d'alcool polyfurylique (PFA) développée par SHD Composites (Sleaford, Royaume-Uni). Le PFA est un polymère thermodurcissable dérivé de la biomasse qui se comporte comme un phénolique avec un excellent traitement de surface et une excellente durabilité (voir « Résister au feu sans le poids »). "Nous avons travaillé avec SHD Composites et poussé leur chimie pour un durcissement plus rapide", explique Orange. « Voilà ce que nous faisons :prendre des matériaux, des processus et des conceptions et les développer davantage afin que les produits composites puissent être fabriqués à grande échelle d'une manière commercialement viable mais durable. »
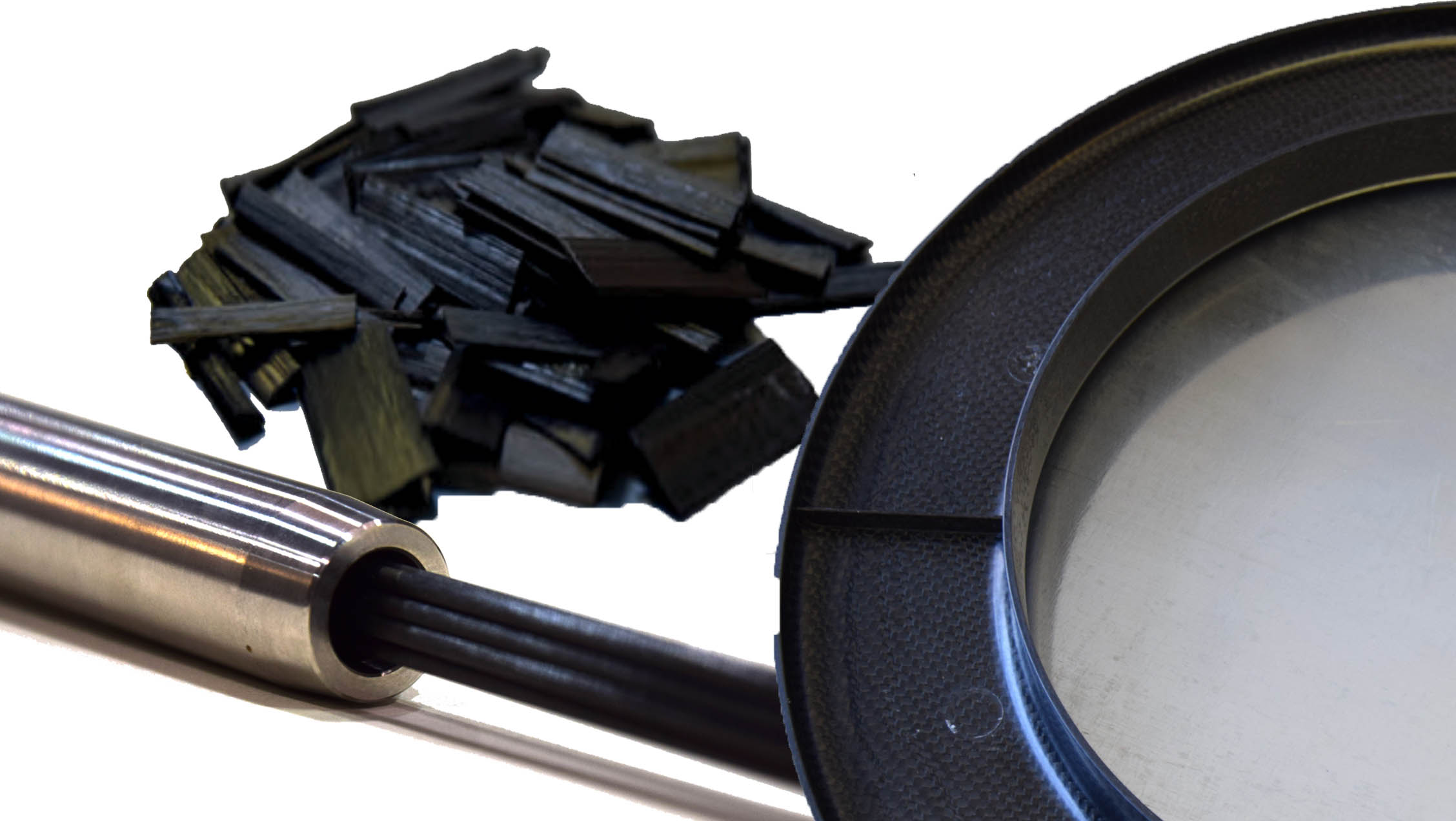
La vitesse de fabrication et la durabilité étaient des facteurs clés lorsque Cecence a rencontré un système de résine époxy thermoplastique il y a plusieurs années. "Ce thermoplastique avec des composants époxy à la fin de ses chaînes polymères était utilisé par une entreprise de textile qui n'a pas réalisé son potentiel dans les composites", explique Orange.
« Nous avons tout de suite compris les avantages d'un thermoplastique à faible viscosité qui pouvait très bien imprégner les fibres tout en permettant un époxy thermoformable », explique Humphrey Bunyan. Cecence a développé un préimprégné basé sur cette technologie époxy thermoplastique, puis une famille de produits sous la marque K_Series :K_Rod enroulable, K_Plate semi-imprégné de 0,25 à 1,98 millimètre d'épaisseur et K_Chip composé de moulage (Fig. 1). « Nous avons été en mesure de mouler à la presse des composants en moins de trois minutes », explique Orange, « et avons démontré une variante FR qui répond aux exigences FST pour les intérieurs d'avions. » Cecence a également utilisé le matériau pour développer un système d'équipement de ligne aérienne composite (COHLE) pour les lignes ferroviaires électriques qui réduit de moitié le nombre de pylônes/poteaux de support et le coût global d'installation et d'exploitation de 100 000 £ (124 200 $) par kilomètre.
Époxy thermoformable
"Avec les thermoplastiques typiques, vous avez un polymère matriciel à haute viscosité qui est difficile à forcer dans les fibres", explique Bunyan. « Ainsi, il est difficile d'obtenir une bonne imprégnation des câbles ou des tissus. Mais l'époxyde thermoformable K_Series a une très faible viscosité - 80 centipoises à 100°C. Cela nous permet de préimprégner des renforts de verre, de carbone et de fibres naturelles avec une excellente distribution résine-fibre et généralement une teneur en fibres de 60 % en poids. Nous pouvons également utiliser des fibres avec un ensimage pour l'époxy, qui n'est généralement pas compatible avec les thermoplastiques. Et pourtant, ce système est un véritable thermoplastique, permettant le reformage de pièces finies à 180-200°C sans réaction chimique ni dégagement de chaleur.
"Comme l'époxy, il adhère bien à la fibre, il n'y a donc pas de séparation de la fibre de la matrice, même si vous utilisez des pressions plus élevées pendant le moulage", note Orange. Cela fait référence à un problème qu'il a constaté avec les composés de polyamide (PA) et de polypropylène renforcés de fibres courtes. « Nous travaillions avec une couche de PA fondue sur un tissu par pressage à chaud pour faire une feuille plate. La matrice ne collait pas aux fibres, juste les entourant. Ainsi, lorsqu'il était pressé dans une pièce, vous obteniez un arrachement de la fibre. »
K_Plate, qui traite à 150-220°C, offre une température de service de 100°C pour des expositions courtes et une utilisation continue à 90°C. Les composés K_Chip de remorquage unidirectionnel hachés sont pressés à 240°C. « Le Tg [la température de transition vitreuse] et le début de la déformation thermique pour la série K_sont inférieurs à ceux des époxydes typiques, mais c'est aussi ce qui rend possible le reformage et le recyclage », explique Orange. Les processus K_Series sont également rapides. "Cecence a travaillé avec RocTool [Le Bourget du Lac, France] au JEC 2016 pour démontrer le thermoplastique le plus rapide qu'ils aient vu", dit-il, notant un temps de cycle de 2 minutes, 40 secondes pour un capot automobile. « Le temps de maintien n'était que de 25 secondes avant le refroidissement, en utilisant 8 à 9 bars de pression au-dessus de la membrane sous vide. Ils étaient également satisfaits de la finition des surfaces mates et brillantes [voir l'image d'ouverture], notant que notre matériau offrait la meilleure finition de tous ceux testés. "
De plus, les composants époxy des produits K_Series rendent les pièces composites faciles à peindre et à coller, sans les apprêts et préparations spéciaux requis pour les thermoplastiques traditionnels. « Vous pouvez les coller secondairement à l'aide d'adhésifs standard », ajoute Bunyan. « Vous obtenez également de bonnes propriétés de cisaillement interlaminaire et, dans l'ensemble, celles-ci créent des structures résistantes et absorbant l'énergie, grâce au thermoplastique. »
Caténaire CFRP pour chemins de fer électriques à moindre coût
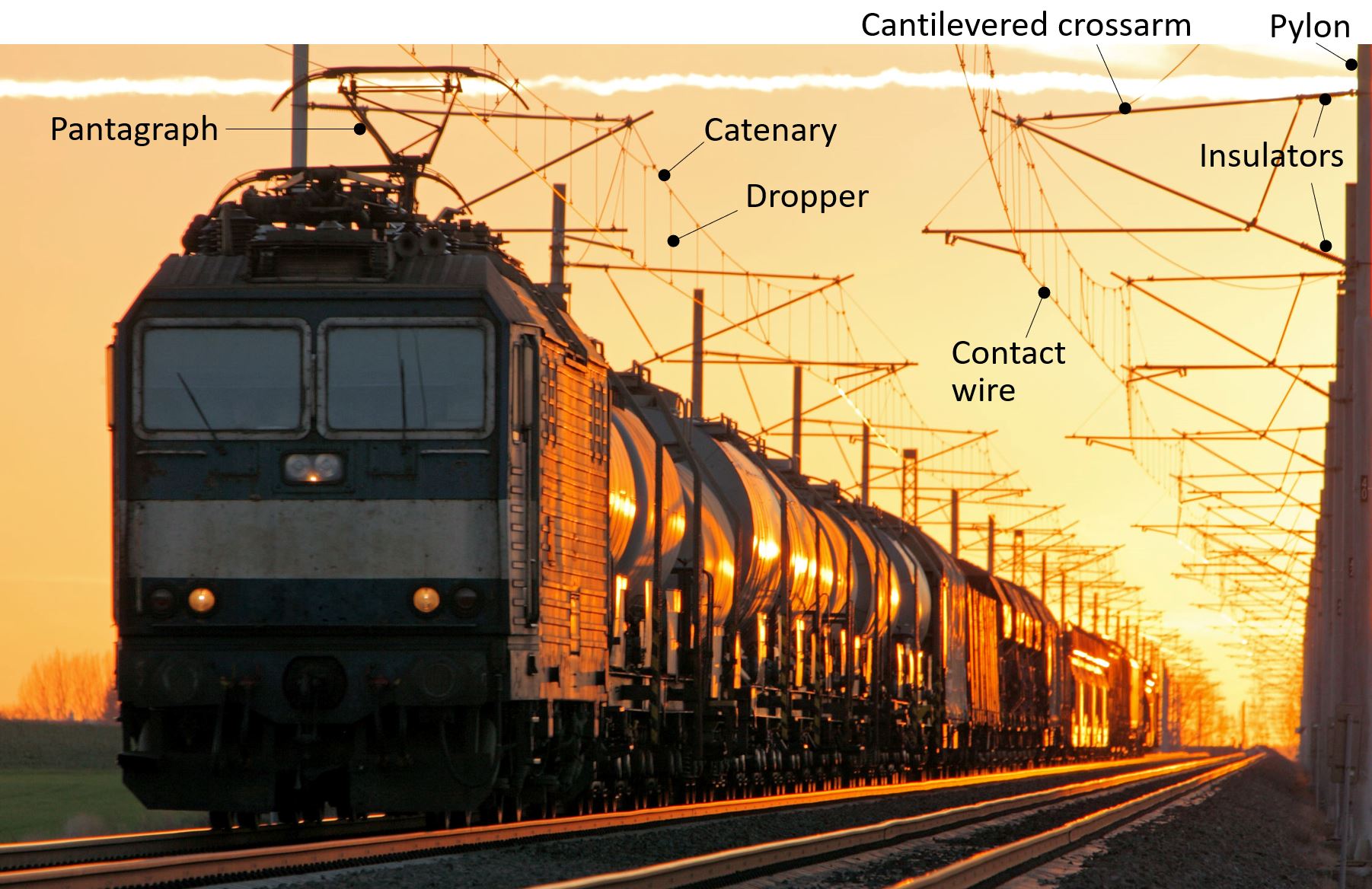
La double nature de cet époxy thermoplastique est illustrée dans un système d'équipement de ligne aérienne (OHLE) développé par Cecence à l'aide d'une caténaire CFRP fabriquée avec K_Rod. La caténaire et le fil de contact porteur de courant sont les deux fils principaux de l'OHLE d'un chemin de fer électrique (Fig. 2). L'électricité est livrée à la locomotive d'un train à travers un pantagraphe, qui s'étend du haut de la locomotive pour appuyer contre le fil de contact. « La caténaire agit comme un pont suspendu entre des pylônes (mâts, poteaux), qui sont espacés tous les 25 mètres le long des voies », explique Orange. Le fil de contact en cuivre est suspendu à la caténaire par des fils ou des compte-gouttes verticaux, un peu comme la chaussée est soutenue par des câbles dans un pont suspendu.
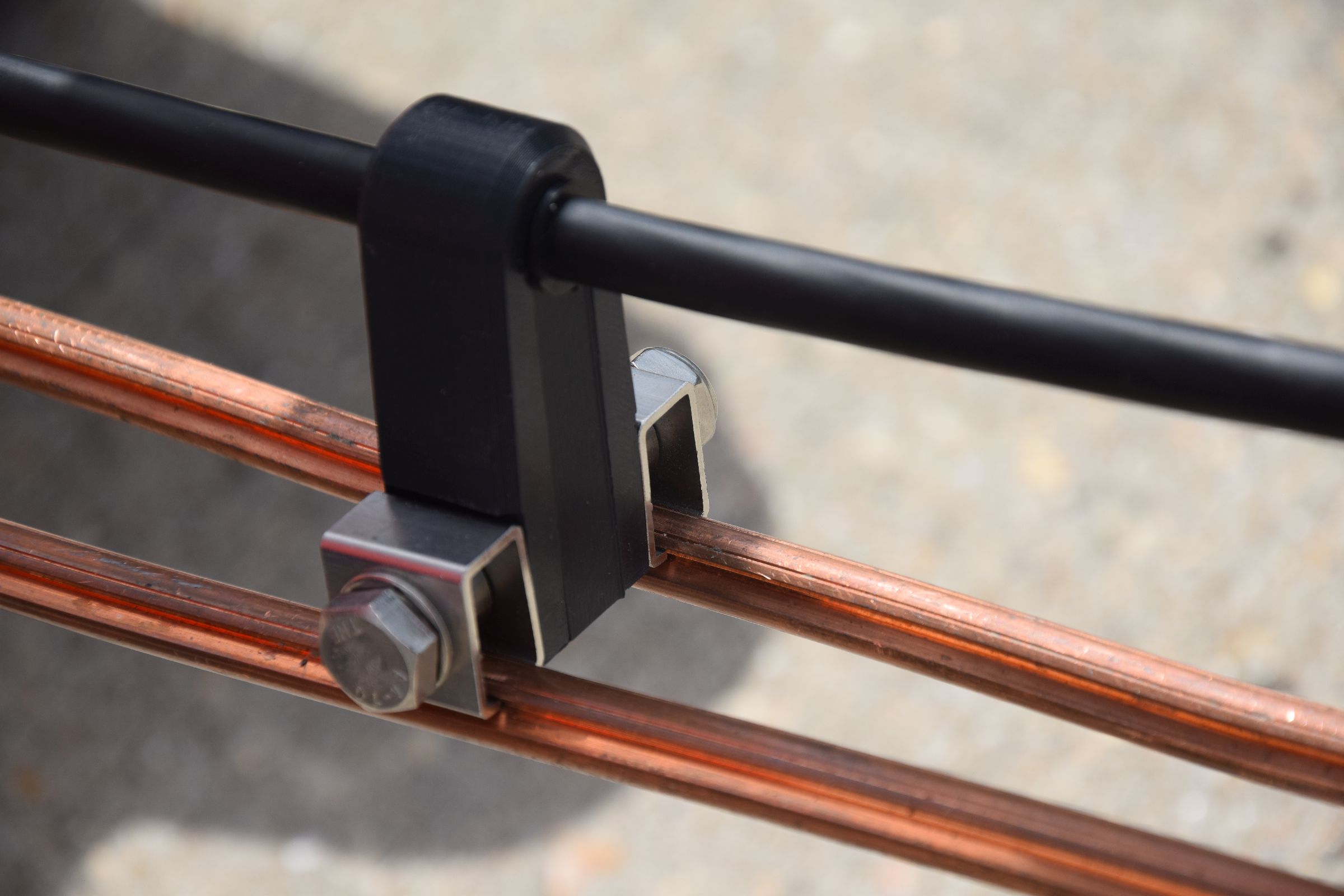
« En utilisant un câble de tension K_Rod comme caténaire, il ne peut s'asseoir qu'à 70 millimètres au-dessus du fil de contact en cuivre », souligne Orange (Fig. 3). "L'ensemble du système est plus compact avec un impact visuel beaucoup plus faible sur l'environnement." Les systèmes OHLE actuels utilisent des câbles caténaires en acier, qui changent de longueur avec le changement de température. « En été, ils s'étendent jusqu'à 400 millimètres par kilomètre », note-t-il. Pour contrer cet affaissement des lignes, des contrepoids en béton sur des poulies sont installés comme système de tension automatique, mais augmentent le coût global.
"Le poids de la ligne d'acier et son profil d'affaissement sont également la raison pour laquelle tant de poteaux sont nécessaires", note Orange. « Notre câble CFRP ne change de longueur que de 7 millimètres par kilomètre en été, car la dilatation thermique négligeable de la fibre de carbone crée un composite thermiquement stable. Il est également 80 % plus léger que le câble en acier, ne s'affaisse pas et permet d'espacer les pylônes de 50 mètres, ce qui réduit de moitié le nombre de pylônes nécessaires. Cela permet des économies supplémentaires car pour chaque pylône, il y a une traverse en porte-à-faux, soutenue par un câble de hauban.
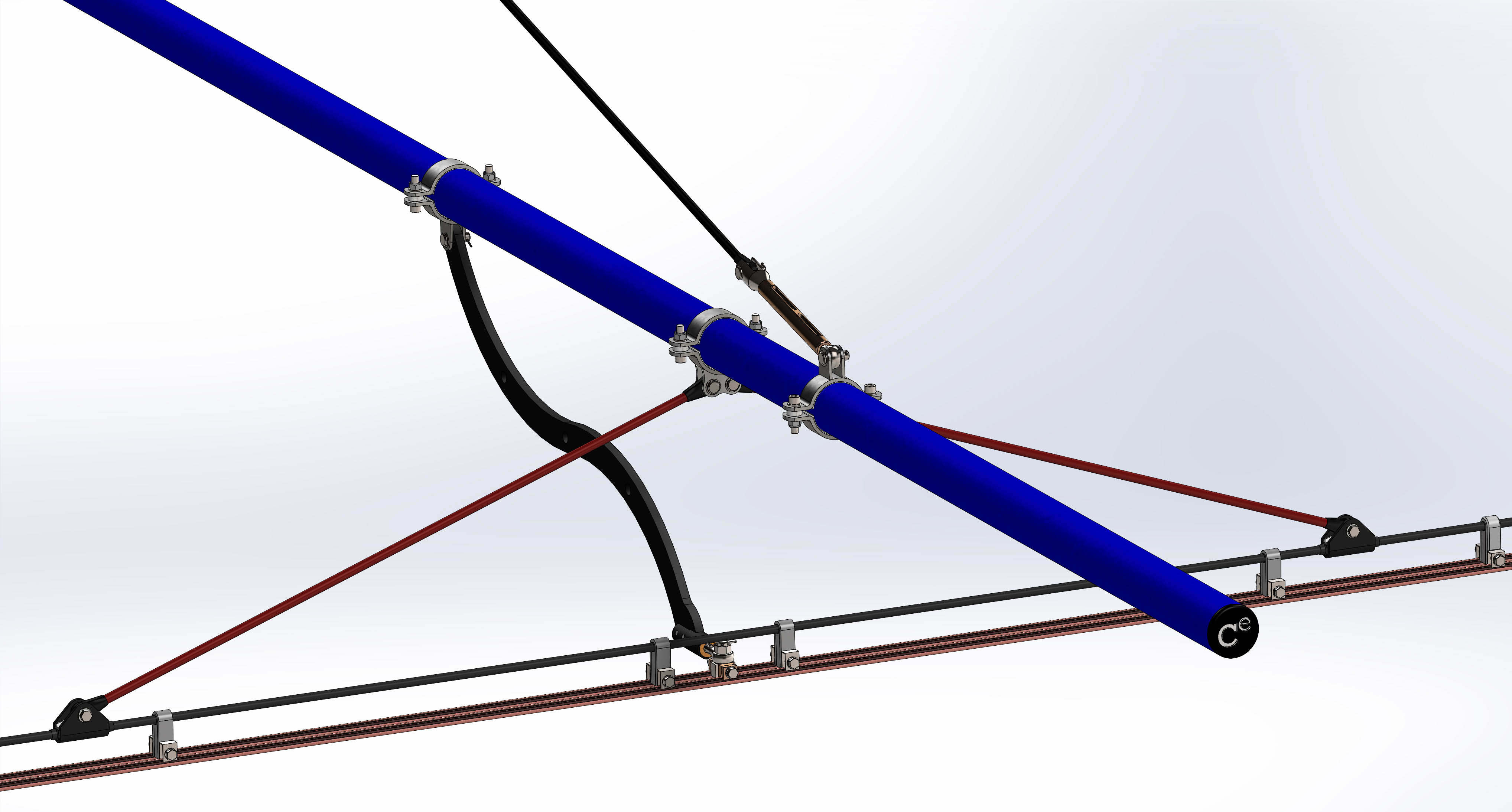
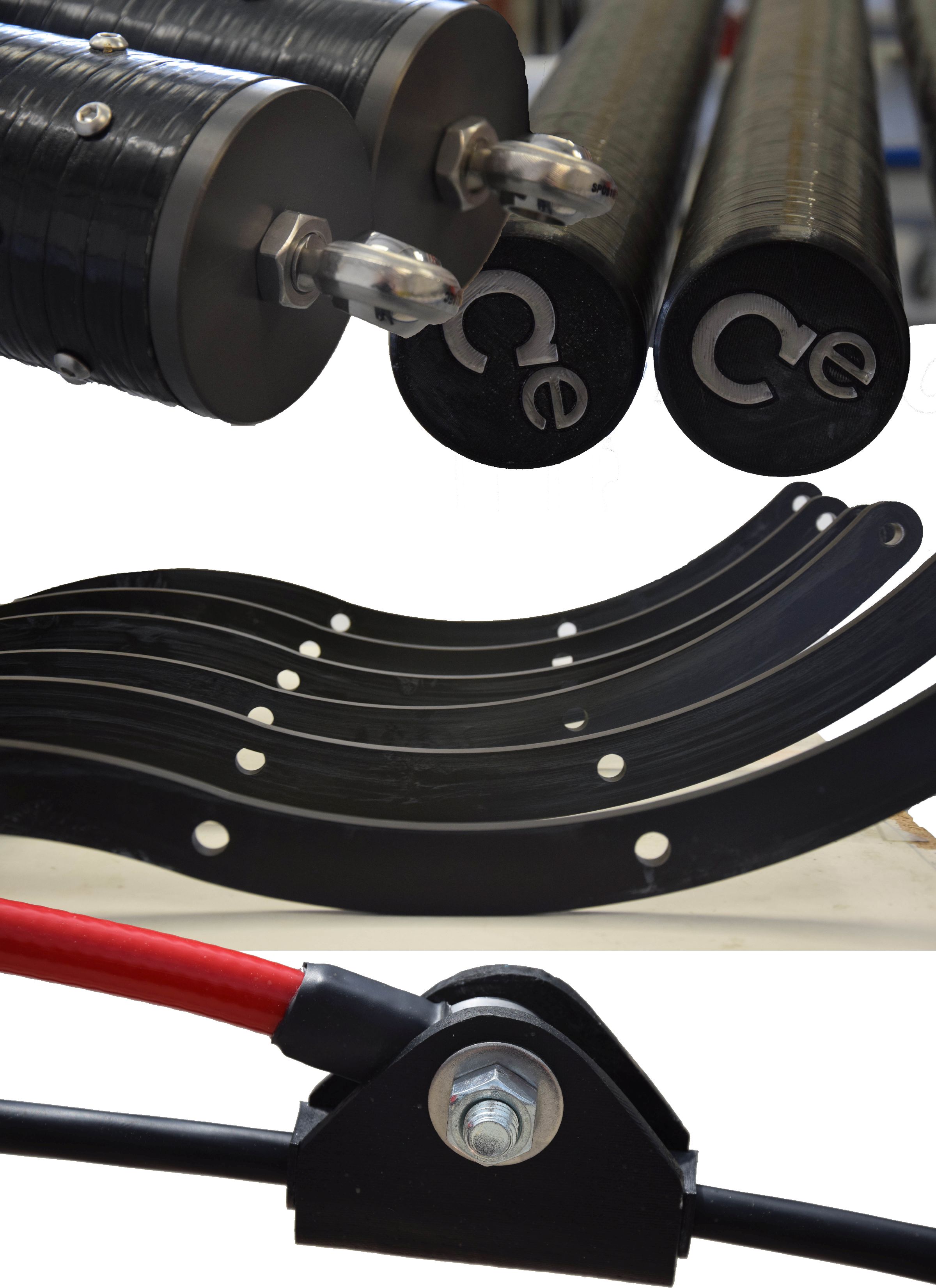
De plus, les systèmes OHLE conventionnels utilisent des composants entièrement métalliques, ce qui nécessite l'ajout d'isolants pour empêcher la conduction indésirable du courant électrique. « Le Cecence COHLE n'a pas besoin de tous les isolants car il utilise des poteaux et des traverses composites en fibre de verre non conducteur avec des haubans composites non conducteurs », explique Orange. « Nous utilisons également des compte-gouttes intermédiaires fabriqués à partir d'acide polylactique (PLA) imprimé en 3D. Contrairement à un système métallique, les poteaux n'ont pas besoin de peinture régulière et les composites résistants à la corrosion nécessitent moins d'entretien. »
« L'époxyde thermoplastique joue un rôle clé dans la caténaire CFRP », poursuit-il. «Cecence l'utilise à la fois dans le noyau K_Rod en fibre de carbone et dans la veste composite GF surtressée. Le résultat est un câble isolé léger, à haute résistance qui est enroulable et se lie bien lorsqu'il est collé dans une prise, résolvant le problème de terminaison normalement délicat pour les câbles composites en fibre de carbone. Grâce à l'incroyable transfert de charge du noyau dans la douille à travers la surtresse, nous n'avons pas besoin d'une longueur de douille énorme et ce système est facile, il est donc pratique à installer sur le terrain par les techniciens ferroviaires. »
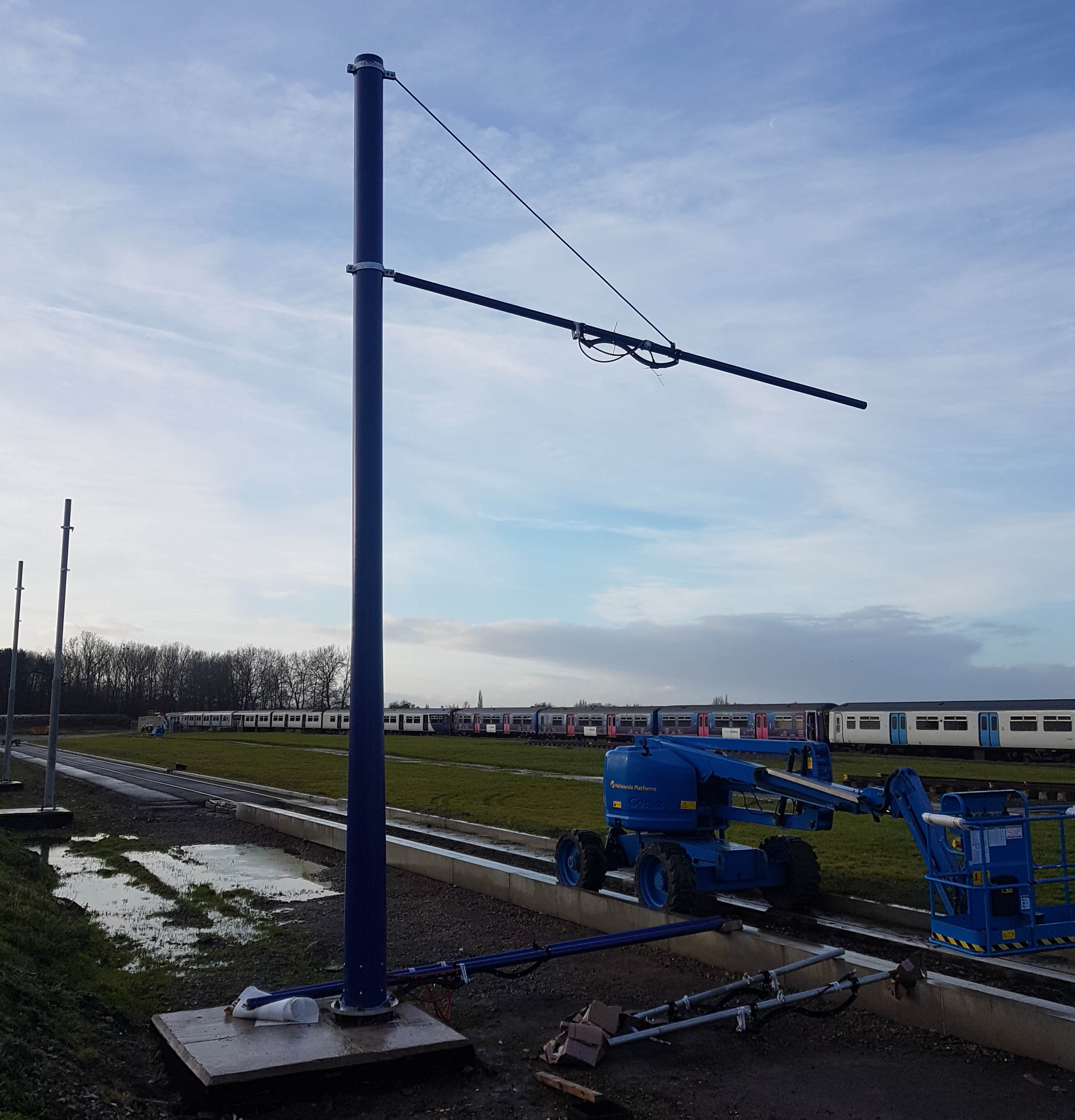
Même si le câble CFRP coûte trois fois celui d'une caténaire en acier, le coût global du système est réduit de 512 000 £ à 413 000 £ par kilomètre, explique Orange. Ces coûts, calculés avec la société multinationale d'ingénierie et d'infrastructure Atkins (Londres, Royaume-Uni), comprennent des économies d'exploitation/maintenance de 400 000 £ à 3,4 millions de livres sterling par kilomètre sur la durée de vie du système.
«Cecence a livré les composants du prototype en mai 2019», explique Orange, «et nos partenaires de développement avaient prévu de mettre en place les lignes électriques d'ici février 2020, mais cela a été retardé en raison de COVID-19. L'ensemble du système a été présenté à l'Advanced Engineering Show en 2019 et a remporté le Composites UK Innovation Award. »
Autres applications et développement de la série K
Au-delà de l'application OHLE, Cecence poursuit d'autres opportunités pour appliquer ses produits K_Series. «Cecence a également travaillé sur des projets où les câbles K_Rod ont été utilisés comme ancrages pour une falaise de pierre dans un projet de construction en Suisse», explique Orange. « Nos partenaires du projet devaient percer des trous de 80 mètres de profondeur dans la roche, insérer les câbles CFRP, puis les remplir de béton. Il y a eu des résultats de test étonnants, mais le partenaire académique n'a jamais été en contact avec l'industrie pour développer le projet au-delà de l'échelle du laboratoire . Nous poursuivons d'autres démonstrations, mais ce système est résistant à la corrosion et offre un bon transfert de charge. Il pourrait également être utilisé comme ancrage au sol pour divers systèmes de construction, tels que les bâtiments à l'épreuve des ouragans. »
Des vidéos sur YouTube et le site Web de Cecence démontrent la thermoformabilité de ses produits K_Plate. "Il y a également eu des discussions pour explorer les applications des profils aérodynamiques à géométrie variable/morphing avec une société aérospatiale britannique", a déclaré Orange. Cecence a démontré un matériau automobile rentable en utilisant K_Chip fabriqué avec des câbles composites hachés en tant que matériau hybride CF/GF/époxyde thermoplastique, maintenant un rapport de 2 : 1 entre le carbone et le verre, confirmé par des tests. ."
La société a également développé une série K_Series haute température avec un Tg de 250-300°C qui traite à 360-400°C. « Cela a été utilisé par un constructeur automobile qui souhaitait que les pièces en PRFC survivent à leur processus de peinture E-Coat à 180 °C », explique Orange. « Nous avons également le matériau K-FR, qui peut répondre aux exigences FST de combustion verticale, de dégagement de chaleur et de toxicité de la fumée des avions, et nous cherchons comment aider à amortir les vibrations pour réduire le bruit de la cabine des avions. Nous pouvons ajuster le thermoplastique et ajouter des couches de matériau élastomère pour obtenir une réduction significative du bruit. »
Samantha Bunyan, la troisième fondatrice de Cecence et sa responsable de l'engagement industriel, souligne que la recyclabilité est également un domaine clé de développement. Cecence fait partie du consortium ReDisCoveR Composites, exploité par le National Composites Center (Bristol, Royaume-Uni). Il a été créé en avril 2019 et poursuit 24 projets le long des quatre filières :recyclage, démontage, matériaux circulaires et réutilisation. « Au sein de ces projets, nous examinons le démontage des composants et démontrons la réelle recyclabilité des composites thermoplastiques », explique Bunyan. « L'industrie est enfin forcée de prouver la recyclabilité qu'il revendique depuis de nombreuses années. Cecence voit les avantages de pouvoir recycler les produits époxy thermoplastiques K_Series, mais il doit également démontrer les processus et la faisabilité économique pour cela. »
"Nous pensons qu'il y a beaucoup plus de place pour les composites durables dans les transports de masse, y compris les intérieurs d'avions, les sièges et les applications ferroviaires", déclare Orange, ajoutant que Cecence n'est pas seulement un partenaire dans le développement mais aussi dans la fabrication. « À ce jour, nous avons fabriqué 2 500 dossiers de siège en composite pour les avions de type A320 et nous étions sur la bonne voie pour produire les dossiers de siège les plus légers et les plus minces de l'industrie avant l'épidémie de COVID-19. Les déchets des sièges composites peuvent être réutilisés dans les repose-pieds et les accoudoirs. Le recyclage peut également être utilisé dans d'autres pièces auxiliaires utilisant actuellement des plastiques vierges. Tout cela peut contribuer à réduire la consommation de combustibles fossiles et les émissions, ainsi qu'à faciliter l'électrification et à accroître la durabilité. »
Dans les composites, note Samantha Bunyan, « la durabilité est triple :les matériaux, le traitement (rapide et à faible consommation d'énergie) et la chaîne d'approvisionnement. Nous perturbons tout cela, en travaillant avec des innovateurs du monde entier qui ne sont pas vus parce que la plupart des gens ne regardent que les grandes entreprises. Le monde a besoin de nouvelles solutions qui fonctionnent pour l'industrie. C'est ce que fait Cecence. »
Résine
- Fabrication de composites :la fabrication de matériaux composites
- Covestro intensifie ses investissements dans les composites thermoplastiques
- L'histoire de la résine époxy
- Composites thermoplastiques chez Oribi Composites :CW Trending, épisode 4
- Dépannage du thermoformage des composites thermoplastiques
- L'évolution des composites additifs
- Mar-Ball, Lattice Composites fusionnent pour étendre les capacités époxy
- Composites thermoplastiques :vue panoramique
- Soudage de composites thermoplastiques