Le processus sur mesure produit une pédale de frein composite toutes les minutes
Le groupe Tier 1 Boge Rubber &Plastics (Damme, Allemagne) produit ce qu'il dit être les pédales de frein tout composites les plus légères, les moins coûteuses et les plus solides au monde, et les premières de la production commerciale. Comme détaillé dans le FOD de janvier (voir « La structure composite thermoplastique remplace les métaux sur les pédales de frein critiques pour la sécurité »), le fournisseur produit actuellement un quart de million de pédales de frein par an pour quatre plates-formes de véhicules produites par des constructeurs automobiles allemands et le système pourrait produire jusqu'à 1 millions de pédales par an. Ceci est important car les pédales sont structurelles, doivent répondre aux mêmes exigences de performance rigoureuses que l'acier et l'aluminium en place, et les conceptions comportent trois types différents de composites thermoplastiques renforcés de verre.
Trois matériaux augmentent l'efficacité des fibres
Pour que les pédales restent légères, minces, rentables et capables de répondre aux spécifications OEM difficiles, Boge utilise une feuille organique de fibre de verre continue comme structure de coque pour supporter les charges principales de la pièce, qui peuvent atteindre 3 000 newtons. Les flans organosheet sont fournis prédécoupés à la taille, avec deux ou trois couches entièrement consolidées par le fournisseur Lanxess Deutschland GmbH (Cologne, Allemagne). Pour renforcer les principaux chemins de charge sur l'ébauche de feuille d'organo, Boge ajoute des bandes de rubans en fibre de verre unidirectionnels (UD) (fournis par Celanese Corp., Irving, Texas, États-Unis) dans des orientations et des couches basées sur des résultats de simulation par éléments finis. Pour ce faire, Boge utilise des logiciels qu'elle a modifiés et des fiches matières que l'entreprise a développées avec ses fournisseurs sur la base de courbes contrainte/déformation mesurées pour chaque matière dans des conditions de température et d'humidité spécifiées par les clients OEM. Pour ajouter une géométrie fonctionnelle, Boge utilise des composés de fibres de verre hachées surmoulées (de plusieurs fournisseurs) pour fournir des nervures structurelles et des caractéristiques de fixation.
Tous les matériaux comportent des matrices de polyamide 6 (PA6) noir précoloré, un polymère résistant largement utilisé dans l'industrie automobile. Si les spécifications OEM l'exigent, Boge a également la possibilité d'utiliser une matrice PA6/6 à température plus élevée et moins hygroscopique dans le composé de surmoulage, car les deux polymères sont suffisamment similaires pour se lier l'un à l'autre. En utilisant trois types différents de composites avec renfort de verre sous trois formes différentes, Boge est en mesure de placer la fibre précisément là où cela est nécessaire pour répondre aux exigences de performance tout en évitant la sur-ingénierie. L'effet de report de cette approche hybride-composite est qu'elle réduit l'utilisation de matériau, l'épaisseur de paroi nominale, le temps de cycle et le coût global des pièces.
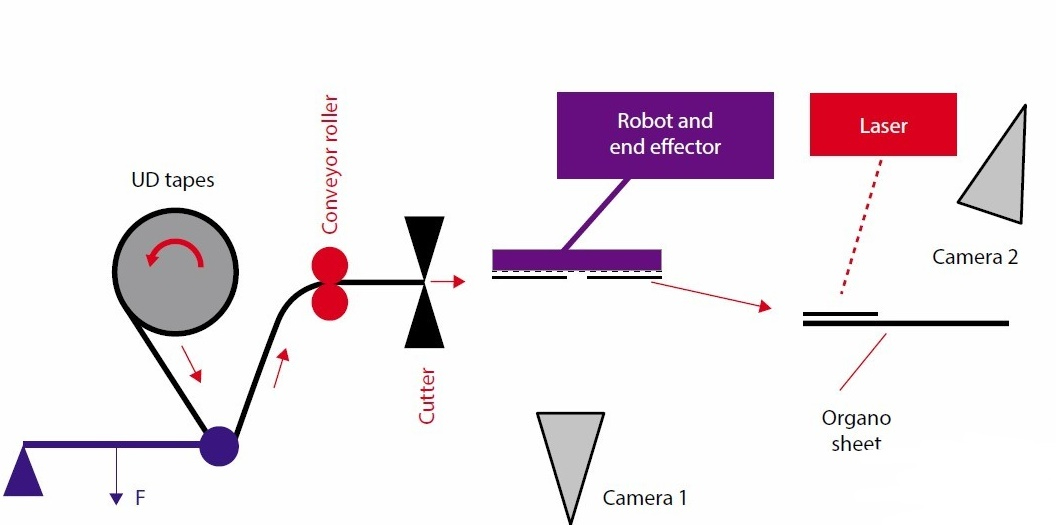
Étapes du processus et critères d'équipement
Partenariat avec le développeur d'automatisation/ligne d'assemblage M.A.i. GmbH &Co. KG (Kronach, Allemagne), Boge a développé un processus de production en trois étapes qui est rapide, efficace et produit des pièces de qualité vérifiée à des coûts abordables. Lors de la conception du processus et de l'équipement, l'équipe avait un certain nombre d'exigences. Premièrement, pour maintenir les coûts des pièces bas, les entreprises devaient maintenir le temps de cycle effectif total à environ 1 minute. Pour y parvenir, il faudrait une automatisation pour garantir que les matériaux se déplacent en douceur dans la cellule de fabrication.
Deuxièmement, alors que les flans organosheet sont fournis préempilés, entièrement consolidés et prédécoupés à la taille (contournés), les exigences de diverses conceptions de pédales signifiaient que l'équipe avait besoin de flexibilité pour couper, orienter et placer des bandes de ruban de différentes longueurs dans différents endroits et directions pour renforcer le principaux chemins de charge de la coque organosheet. Encore une fois, pour réduire les coûts, un processus de pose de bande sur mesure a été conçu pour offrir un niveau élevé de flexibilité et de contrôle, ainsi que la vitesse.
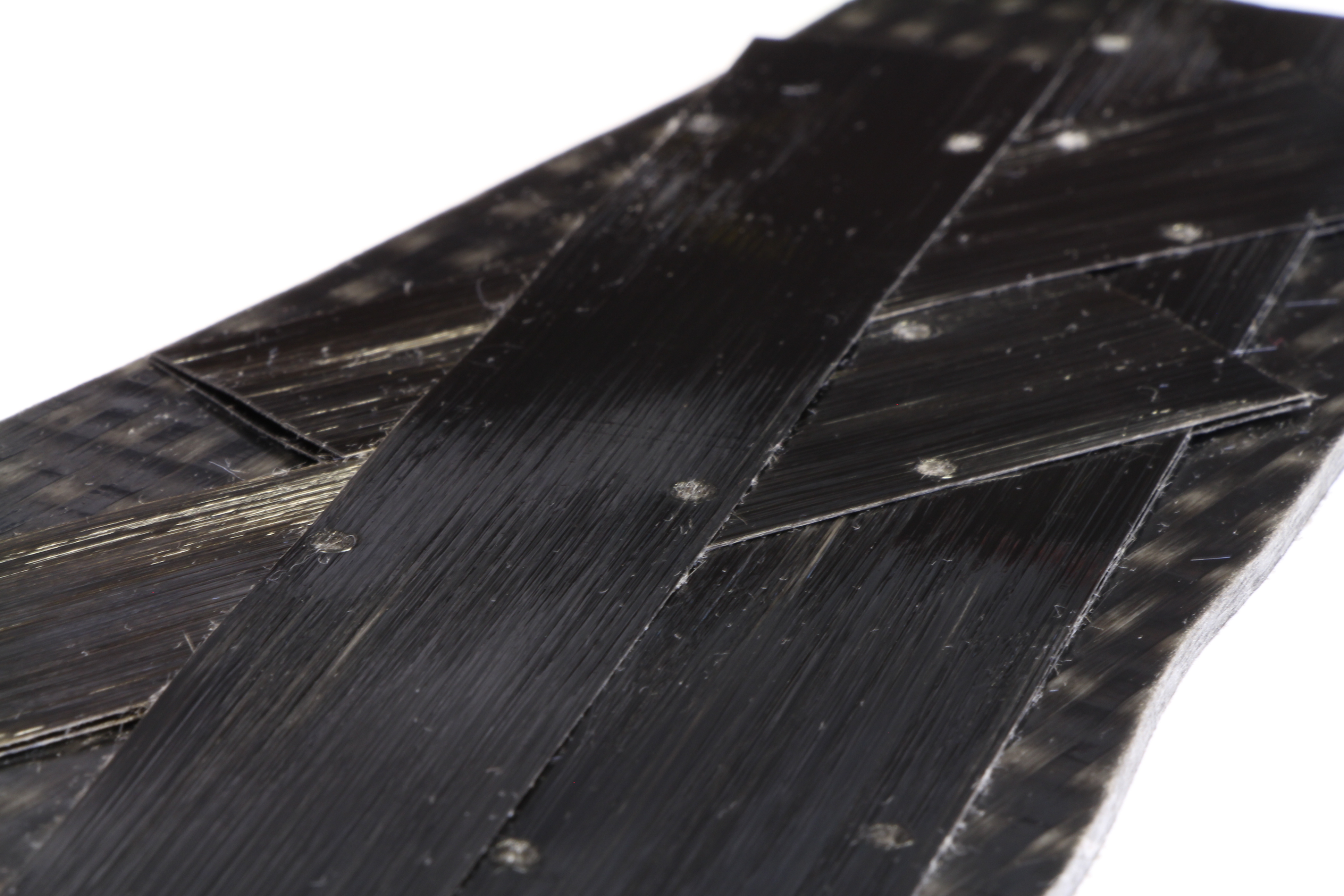
Au début du processus, la cellule de fabrication contient deux piles de prédécoupés flans organosheet dans des cassettes et quatre cantres de bandes UD à la fois. Tout d'abord, un robot prend un flan profilé d'organosheet et le déplace vers la surface de travail. En même temps, le ruban UD est sorti et coupé à la longueur requise. Les bandes sont ensuite placées sur un tapis sous vide qui les maintient en place au fur et à mesure que le convoyeur avance. Ensuite, un robot doté d'une unité de préhension et de placement rotative (effecteur final) prélève une bande à la fois de la bande d'aspiration et une caméra vérifie la qualité, la dimension et la position de chaque bande. Lorsque les quatre pièces ont été ramassées, le robot se déplace vers l'espace de travail et commence à placer une bande à la fois sur le flan d'organosheet à l'emplacement et à la position déterminés par la correction de position basée sur l'image. Lorsque chaque bande est positionnée, elle est empêchée de se déplacer par de multiples points de soudure créés par un laser. Pendant ce temps, davantage de bandes de ruban sont coupées et placées sur la courroie d'aspiration et le processus se répète jusqu'à ce que tous les rubans requis pour une conception de pédale de frein donnée soient empilés et cloués dans la bonne position sur la feuille organique.
Le système qui produit cette ébauche de fibre sur mesure est à 100 % à commande numérique, chaque aspect de l'opération étant entièrement programmable pour une flexibilité maximale. À chaque étape, des caméras ou d'autres capteurs, qui sont connectés au système de contrôle qualité (CQ) en ligne du système, détectent tous les bords et positions des bandes de ruban et de la coque organosheet et comparent les données géométriques de ces matériaux avec des paramètres connus pour s'assurer que chaque matériau est positionné là où il doit être.
Pour maintenir des vitesses de production élevées, le flan de fibres sur mesure passe ensuite à un four infrarouge pour chauffer les deux matériaux juste avant de draper/préformer/consolider les bandes sur la feuille organique. Un emballage spécial d'antioxydants dans les systèmes de ruban et de résine organo-feuille empêche les dommages thermiques. Ensuite, le flan chaud est rapidement déplacé dans la cavité de drapage/préformage où une haute pression est utilisée pour former le flan en une forme de canal en U tout en assurant une surface de haute qualité. Le système QC surveille à nouveau la consolidation et la qualité du préformage via le temps, la température et la pression.
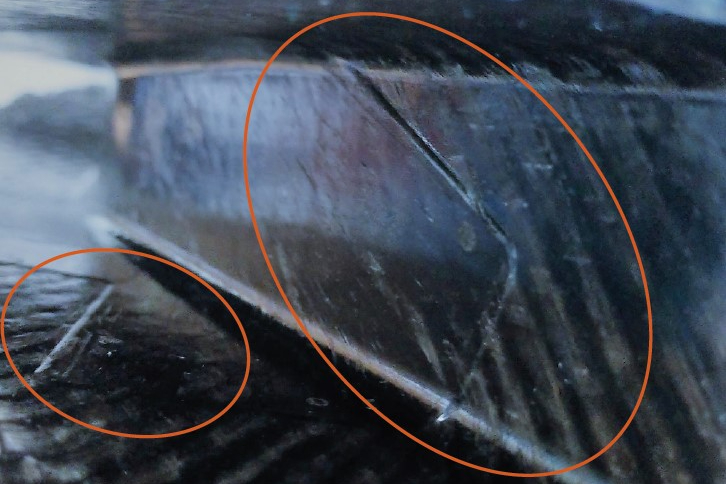
Enfin, la pièce encore chaude et drapée est transférée dans un moule d'injection où elle est surmoulée avec un composé de verre court/PA pour créer une géométrie supplémentaire telle qu'une structure de nervures complexe sur la face inférieure. Après le démoulage, une coupe rapide et automatisée et une inspection visuelle sont effectuées. Aucune peinture ou autre finition de surface n'est nécessaire. La taille finale de la pédale est d'environ 350 x 90 x 60 millimètres. Avant de quitter la cellule de fabrication, un code QR unique est apposé sur chaque pédale pour le relier aux données de fabrication et de matériaux de cette pédale dans le système qualité. Après assemblage, un test fonctionnel de la pédale dans son support et un contrôle robotique final sont effectués. En supposant que l'unité réussisse, un autre code QR est apposé sur l'ensemble de pédale de frein terminé pour fournir une traçabilité complète de chaque pédale et des composants supplémentaires avant l'expédition à l'OEM.
Étant donné que les pédales de frein sont des pièces critiques pour la sécurité et doivent répondre à des performances OEM exigeantes ainsi qu'à des exigences de qualité, Boge et ses partenaires ont intégré plusieurs mécanismes de sécurité intégrée dans le système de contrôle qualité conforme à l'industrie 4.0 pour vérifier rapidement et avec précision que les spécifications ont été respectées à chaque étape de le processus. Les données de contrôle qualité sont stockées et chaque pédale reçoit un numéro d'identification unique sous la forme d'un code QR pour assurer une traçabilité à 100 % du matériel, des quarts de travail et des conditions de processus impliqués dans la production de cette pièce.
Les pédales de frein tout composite produites par Boge pèsent environ la moitié du poids des pédales en métal. Ils améliorent également l'haptique de conduite pour les consommateurs, sont 100 % recyclables en fin de vie et satisfont ou dépassent les exigences de résistance de l'acier en place.
Résine
- Les méthodes de fabrication composite les plus populaires
- Première pédale de frein entièrement en plastique pour voiture de sport électrique à batterie
- Solvay augmente la capacité des composites thermoplastiques
- La roue en thermoplastique prend la route difficile
- Composite de bardage architectural dévoilé
- Fabriquer de meilleurs vélos en composite en Arkansas
- Comment fonctionne le processus CMC
- Les 4 choses critiques que tout opérateur de presse plieuse devrait savoir
- 4 choses que tout opérateur de presse plieuse devrait savoir pendant son sommeil