Fabrication de la moitié supérieure du démonstrateur multifonctionnel de fuselage (MFFD)
Ce blog fait suite à une présentation donnée par le Centre aérospatial allemand (DLR, Stuttgart et Augsbourg) au symposium TU Munich l'automne dernier et CW résumé de publié au cours de la même période, "Aller de l'avant sur le démonstrateur multifonctionnel de fuselage (MFFD)". Le projet a également été décrit dans une présentation donnée par Lars Larsen à 9h35 le jour 3 de l'ITHEC 2020 :« Process data-driven advancement of robot-based, continu ultrasonic Welding for the Dust-free Assembly of Future Fuselage Structures ».
Comme l'explique Larsen, « Le défi majeur est de montrer que les coûts de production peuvent être considérablement réduits en utilisant l'automatisation. » Pour la moitié supérieure du MFFD, cela inclut la consolidation in situ via la pose automatisée de ruban/le placement de fibres (ATL/AFP) pour éviter l'autoclave et le soudage sans poussière/sans poussière pour l'assemblage. « Cela devrait permettre de modifier la séquence des lignes d'assemblage des composants et finales à l'avenir », déclare Larsen, « permettant aux systèmes d'être intégrés avant Assemblée." En effet, contrairement à l'usinage des trous de fixation, le soudage ne produit ni copeaux ni débris susceptibles d'endommager les systèmes préinstallés tels que l'alimentation électrique distribuée, les aménagements intérieurs, etc.
Ce blog est basé sur mon entretien avec Sebastian Nowotny, responsable des technologies de conception et de fabrication de composants au DLR Institute of Structures and Design (BT, Stuttgart) et Frederic Fischer, responsable technique de la production de composites thermoplastiques au DLR Center for Lightweight Production Technology ( ZLP, Augsbourg). Fischer est également le chef de projet pour la moitié supérieure du MFFD chez DLR.
REMARQUE :Dans l'image ci-dessus, les limons formés par glissement font référence à un processus développé dans Clean Sky 2 par Applus+ Labaoratories (Barcelone, Espagne), voir mon blog de 2017 sur le formage glissant, et les clips pressés à chaud font référence à l'estampage, voir :
- Accélérer les composites thermoplastiques dans l'aérospatiale
- Temps de « clip » des composites thermoplastiques, travail sur des pièces petites mais cruciales
- À l'intérieur d'un foyer de composites thermoplastiques
Combiner structure, cabine et systèmes
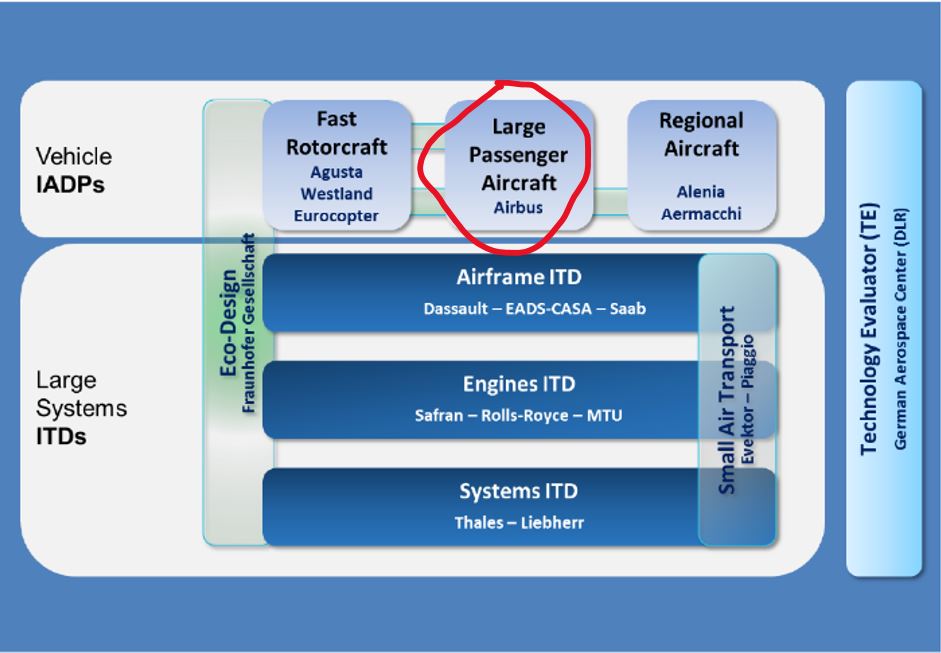
J'ai interrogé Nowotny sur l'histoire de la moitié supérieure du MFFD. « Lorsque Clean Sky 2 a démarré, le premier appel à propositions a été lancé », répond-il. « Je pense que nous avons commencé en 2015 et que nous avons remporté l'appel d'offres pour le projet appelé ICASUS, qui était un projet en co-partenariat pour le programme d'avions de grande capacité (LPA). L'accent a été mis sur la conception d'un fuselage multifonctionnel. À l'époque, ce n'était pas du composite thermoplastique. L'objectif principal était de combiner le fuselage, la cabine, les systèmes et la structure en un seul processus de conception. Donc, fondamentalement, le travail qui a été fait là-bas est ce qui est maintenant devenu le démonstrateur de fuselage multifonctionnel (MFFD) et est le support technologique de notre travail dans le projet de coque supérieure. »
ICASUS
Le projet ICASUS vise à développer des solutions multifonctionnelles et hautement intégrées pour la prochaine génération de fuselage multifonctionnel intégré à la cellule, à la cabine et aux systèmes. Aujourd'hui, le processus de fabrication et d'assemblage des avions monocouloirs repose sur des étapes séquentielles coûteuses et chronophages. L'assemblage des principaux composants (MCA) et la chaîne d'assemblage final (FAL) en particulier sont des goulots d'étranglement empêchant des processus plus rapides et accélérés. Pour cette raison, ICASUS développera un nouveau concept de fabrication et d'assemblage des futurs avions monocouloirs ciblant :
- Production à cadence élevée de 60 appareils/mois ;
- Réduction des coûts récurrents du fuselage de 1 million d'euros par rapport à la référence A321 ACF (« Advanced Cabin Flex » );
- Réduction du poids du fuselage d'une tonne métrique par rapport à l'A321 ACF.
L'approche consistera à combiner les disciplines autarciques à l'origine de la cabine/du fret, des systèmes et de la structure pour aboutir à la combinaison et à l'intégration les plus prometteuses des fonctions et exigences respectives. Ceci doit être réalisé en utilisant des matériaux de pointe et en appliquant des principes de conception innovants en combinaison avec l'architecture de système la plus avancée en combinaison avec la cabine de nouvelle génération.
Le moteur principal est de réduire considérablement la consommation de carburant en appliquant des systèmes légers et une architecture/intégration de système. Cela nécessite une procédure d'optimisation globale multidisciplinaire, ainsi que le développement et l'application d'une approche holistique de l'Industrie 4.0. La conception pour la fabrication automatisée, l'automatisation, la sensorisation, l'analyse des données et l'échange de données sécurisé doit être utilisée. Les principaux objectifs de la fabrication du MFFD comprennent la vérification de la production rentable et en grand volume de structures composites multifonctionnelles et la contribution aux concepts de certification pour les joints thermoplastiques CFRP (par exemple, le soudage).
Comment combiner la cabine du fuselage, les systèmes et la structure en un seul ? "Vous auriez toujours ces disciplines avec leurs exigences respectives, mais je pense que l'objectif principal est l'approche pour collaborer déjà à un stade précoce", explique Nowotny. « Il y a eu des règles strictes pour le processus de conception du fuselage des avions qui ont créé des restrictions et empêché une conception d'avion entièrement optimisée. L'idée initiale de combiner structure, cabine et systèmes était d'avoir un processus de conception qui rassemble ces trois aspects et essaie ensuite de trouver l'optimum global, pas seulement un d'abord pour la cabine, puis un pour la structure, puis un pour les systèmes. . Mais, bien sûr, il y a beaucoup de règles et ce n'est pas un processus facile car cela implique également une certification. »
"C'est un processus continu, dans le sens où une plate-forme numérique a été établie et tous les partenaires européens contribuent à cette conception numérique unique", a déclaré Fischer. « L'avancement de cette conception intégrée pour le MFFD est ce qui se passe depuis quelques années. Notre équipe livrera la moitié supérieure avec des dispositions pour la fixation de la cabine et du système. La vision est de révolutionner l'assemblage final en livrant des composants majeurs entièrement équipés. »
Bien que le DLR fasse déjà partie du projet de conception du MFFD, il n'a reçu le feu vert définitif pour le projet de fabrication qu'en 2019. Le consortium pour construire la moitié supérieure comprend Airbus en tant que chef de projet global du MFFD, Premium Aerotec (Augsbourg, Allemagne ) en tant que responsable de la conception industrielle et structurelle et fournisseur des cadres, Aernnova (Vitoria-Gasteiz, Espagne) pour produire les longerons et DLR en tant que responsable du développement de la technologie de drapage et de soudage. Au cours de l'année écoulée, déclare Fischer, « nous avons affiné la conception de la moitié supérieure pour garantir qu'elle peut être fabriquée avec les technologies sélectionnées. »
Consolidation in situ
Alors que la moitié inférieure du MFFD est produite à l'aide d'ATL et d'AFP suivis d'une consolidation à l'autoclave, la moitié supérieure utilisera une consolidation in situ pendant ATL/AFP. Pourquoi? « Pour tirer le meilleur parti du projet de recherche, nous avons choisi de remettre en question la ligne de base », explique Fischer, « et de profiter de l'opportunité d'utiliser une technologie en complément de la moitié inférieure. » Nowotny ajoute :« Nous avons montré qu'il s'agit d'une méthode de fabrication très prometteuse qui se concentre sur la production au plus juste en réduisant les étapes de fabrication. Mais je pense qu'il est clair qu'il n'y a pas une seule méthode de fabrication qui sert à tous les usages. Vous devez encore décider, au cas par cas, quel est le processus de fabrication optimal pour chaque pièce. »
Deux types de soudure
Un autre choix fait pour la moitié supérieure a été l'utilisation de deux technologies de soudage différentes. « Nous utilisons un soudage par ultrasons continu basé sur un robot pour les longerons, car, à notre avis, c'est la technologie la mieux adaptée pour les joints très longs, et en particulier pour la configuration des longerons », explique Fischer. Le soudage par résistance a été choisi pour l'intégration des cadres de fuselage. « Ces choix sont le résultat d'analyses intensives que nous avons eues au début du projet, en collaboration avec Premium Aerotec. Nous avons examiné les différents scénarios de soudage, ce qui devait être joint et où. »
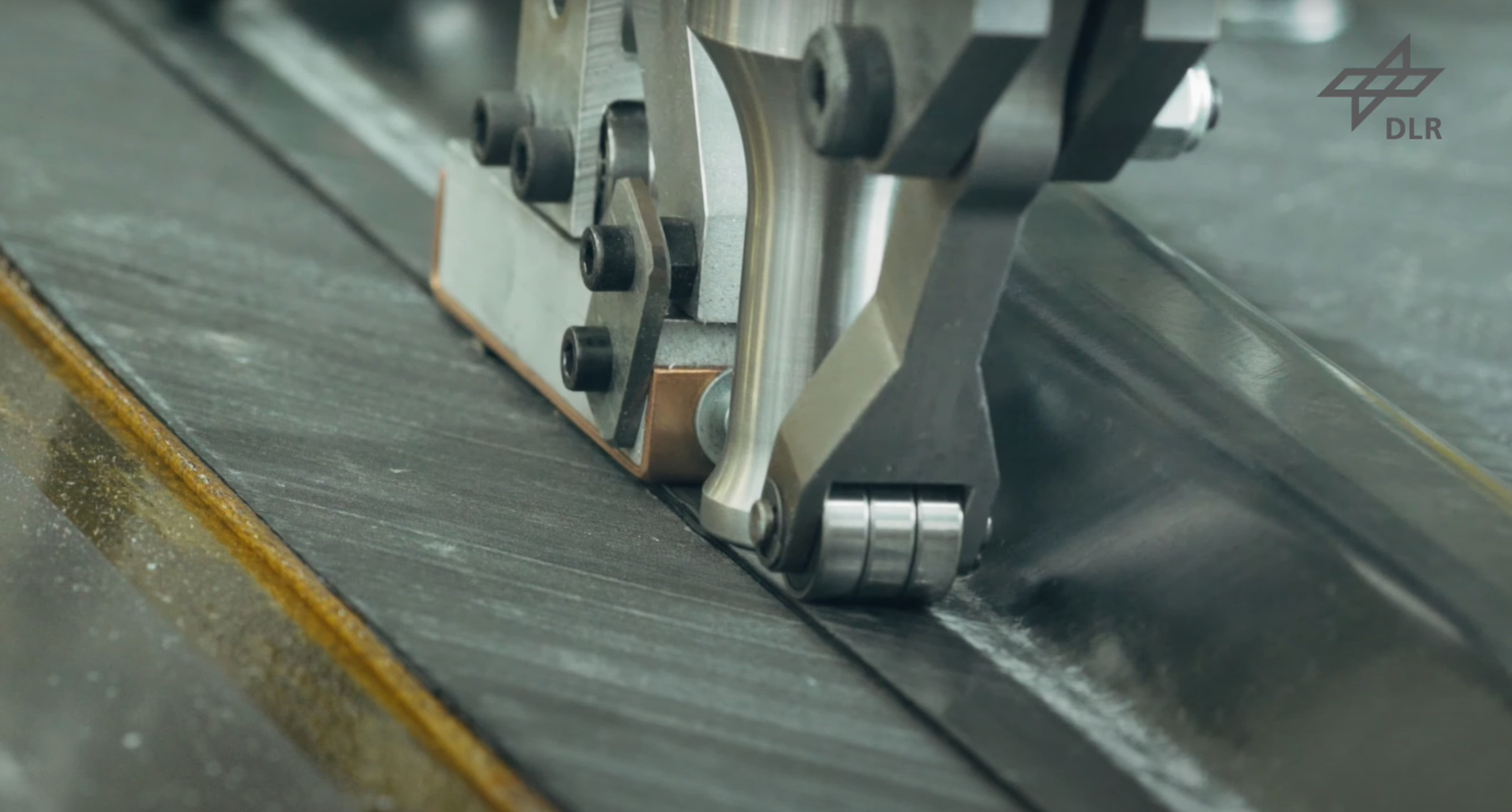
Le soudage continu par ultrasons développé par DLR utilise un robot industriel standard. L'effecteur d'extrémité de soudage comprend un rouleau de pré-roulage, une sonotrode de 25 millimètres de diamètre et une unité de compactage suivante. L'effecteur final est équipé de plusieurs capteurs, ce qui permet une surveillance du processus en ligne. En utilisant le robot comme manipulateur, comme le montre la vidéo ci-dessous, diverses géométries peuvent être soudées, telles qu'une cloison de pression arrière incurvée ou des longerons oméga sur une peau.
« Donc, nous avons deux processus avec une grande distinction », note Fischer. « L'un est un continu et l'autre est un discontinu traiter. Pour les joints de 8 mètres de long des longerons en Z, nous avons choisi le soudage continu par ultrasons. Et pour le cas d'utilisation très complexe - en termes d'accessibilité et de gestion des tolérances - de souder les brides attachées des cadres à la peau, nous avons choisi le soudage par résistance. Nous allons adapter et pré-équiper l'élément de soudage par résistance à la géométrie du cadre et disposer d'un outil de soudage en forme de pince qui se ferme pneumatiquement, entre en contact avec les éléments de soudage, puis déclenche le processus de soudage. »
Nowotny note que le soudage par résistance a la maturité la plus élevée et la résistance la plus élevée, ce qui correspond bien à la charge plus élevée observée dans les joints entre les cadres et les tasseaux. Il souligne que ce procédé soude le cadre à la peau et souder le taquet à la fois au cadre et au longeron.
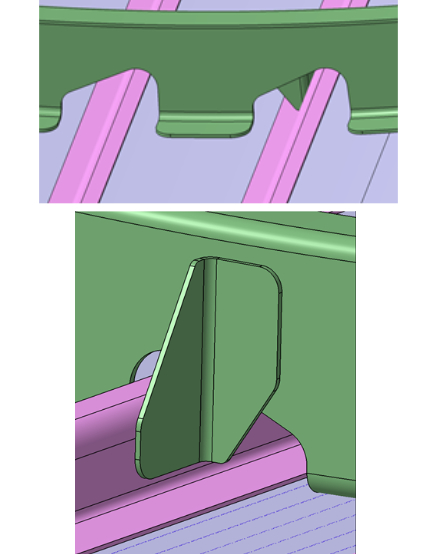
« Nous avons montré l'intégration de clips sur des pièces génériques au JEC 2017 », explique Fischer. Nowotny ajoute : « Et nous avons eu le projet HISYS avec le département haute portance d'Airbus Bremen en 2005-2008 pour le soudage par résistance avec du thermoplastique PEEK (polyétheréthercétone). Nous avons amené l'ensemble du processus de soudage des nervures dans la peau jusqu'à TRL 5. Ainsi, les bases du processus sont assez bien comprises, et nous pouvons maintenant nous concentrer principalement sur l'adaptation, l'automatisation et la robustesse du processus. »
“ L'un des principaux catalyseurs des différentes technologies de soudage, même si elles existent depuis longtemps, est de montrer qu'elles sont prêtes pour une application commerciale dans l'industrie », souligne Fischer, « y compris l'automatisation, la programmation et l'assurance qualité nécessaires. . L'une des questions clés que nous examinons est de savoir comment savoir que la soudure est bonne. Nous voulons nous assurer que nous avons les données de processus pour montrer que nous savons que la soudure fonctionnera à long terme et que nous ne demandons pas un contrôle CND ultérieur par ultrasons, ou une autre inspection globale de l'assemblage terminé. Ainsi, l'un de nos principaux objectifs dans ce projet est de développer l'assurance qualité industrielle. »
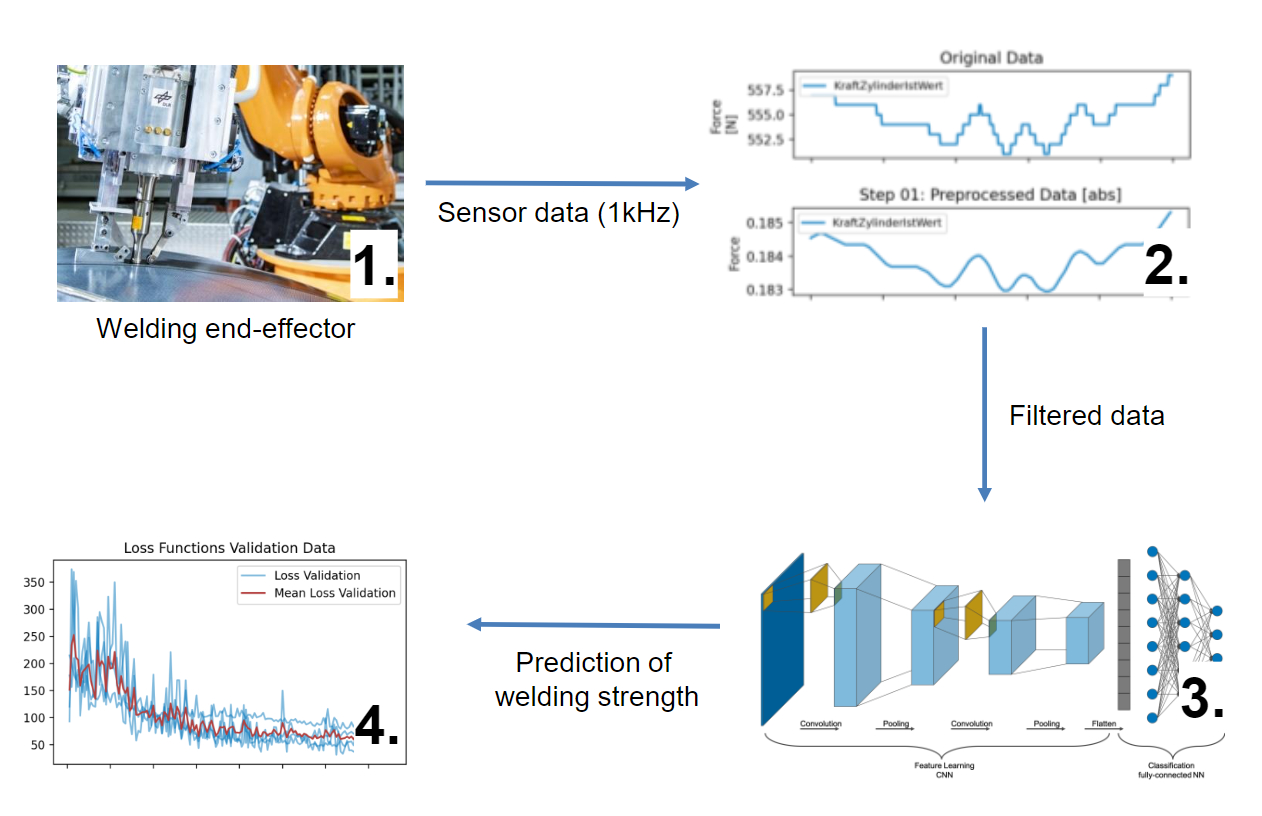
Pivot vers LM PAEK
Comme expliqué dans mon blog, « Proving out LM PAEK soudage for Multifunctional Fuselage Demonstrator », bien que le MFFD ait commencé avec de la fibre de carbone/PEKK (polyéthercétonecétone), lors du 10e appel à propositions (CFP10) en mars 2019, le matériau de base avait été passé à la fibre de carbone/PAEK (polyaryléthercétone). PAEK est la famille globale de polymères au sein de laquelle résident PEEK, PEKK et LM PAEK. Quelle est l'expérience de la moitié supérieure de l'équipe avec le LM PAEK ? « Nous l'avons déjà utilisé pour un certain nombre d'essais de fabrication », déclare Fischer. « Les performances du matériau sont assez prometteuses pour le soudage par ultrasons et par résistance. Pourtant, le matériel est en cours de développement et un processus d'échange commun en termes de leçons apprises et de développement de directives de traitement a été mis en place entre tous les partenaires européens et le fournisseur de matériel. »
“ Cependant », ajoute Nowotny, « je pense que c'est une bonne chose que nous ayons maintenant ces choix de matériaux, car il y a de nombreuses années, il n'y avait que Cytec APC-2, et rien d'autre. Surtout en Europe, parfois vous pouviez obtenir le matériel et parfois vous recevriez « non, désolé ». Maintenant, nous avons plusieurs fournisseurs de matériaux qui travaillent activement sur les matériaux, mais aussi pour les différents processus. Par exemple, Victrex, comme nous l'avons vu présenté lors du symposium TU Munich 2020, se penche désormais sur l'optimisation de la fabrication additive. Des travaux d'optimisation sont également en cours pour la consolidation in-situ de l'AFP, et certains pour la consolidation secondaire à l'aide d'un autoclave ainsi que divers procédés de fabrication hors autoclave (OOA). Il se passe donc beaucoup plus de choses maintenant, et cela augmente les chances d'obtenir un bon matériau pour chaque processus. »
Chronologie et prochaines étapes
« Nous avons essentiellement terminé le processus de conception et de fabrication d'un démonstrateur intermédiaire – un diamètre A320 avec deux baies de châssis et une largeur de 950 millimètres – et nous construirons cette demi-coque plus petite au début de l'année prochaine (2021) », déclare Fischer. . « En dehors de cela, nous avons commencé à acheter l'outillage pour la moitié supérieure à grande échelle, et nous intensifions nos technologies pour nous assurer que nous serons en mesure de produire la moitié supérieure à grande échelle à temps en 2022 ."
Qu'est-ce que cela implique? Un problème est les tolérances d'assemblage. « Les joints longitudinaux le long des côtés gauche et droit des moitiés supérieure et inférieure du fuselage sont conçus depuis un certain temps », explique Fischer. « À partir de là, nous avons certaines exigences et nous devons nous assurer que nos tolérances de production répondent à ces exigences. »
« L'histoire de base de ce que nous essayons de faire avec la coque supérieure est de démontrer les voies les plus efficaces pour la production de composites thermoplastiques et d'ouvrir une voie qui peut concurrencer l'aluminium pour les futurs avions », explique Fischer. Il note que DLR l'a déjà montré dans son travail avec Premium Aerotec pour développer une cloison de pression arrière thermoplastique soudée, montrée en 2018 et 2019 (voir aussi « Nouveaux horizons dans le soudage des composites thermoplastiques »). Le soudage et la production au plus juste sont des catalyseurs clés pour les thermoplastiques. Et maintenant, nous devons sortir ces technologies du laboratoire et les intégrer à l'industrie. Et pour que les industries croient qu'elles peuvent vraiment utiliser ces technologies de soudage, nous devons montrer qu'elles peuvent être automatisées, prévisibles et contrôlées pour la fiabilité dans des tâches de production réelles. Et c'est ce que nous faisons. »
Résine
- Les avantages de la fabrication à court terme
- Les matériaux organiques sont-ils l'avenir de la fabrication de plastique ?
- Comment choisir le meilleur fournisseur de fabrication de plastique
- Robots d'assemblage 101 :le quoi, où et comment des robots d'assemblage dans la fabrication
- Le rôle de la blockchain dans la fabrication
- Les 8 gaspillages du Lean Manufacturing
- En quoi consiste le processus de fabrication ?
- L'avenir de l'impression 3D dans la fabrication
- L'impression 3D est-elle l'avenir de la fabrication ?