Le projet Clean Sky 2 FRAMES fait progresser la simulation de chauffage du composite thermoplastique AFP avec une lampe flash au xénon
Crédit photo :Heraeus Noblelight et Compositadour
L'objectif principal du projet FRAMES de Clean Sky 2 (CS2), qui a débuté en juillet 2020, est de valider une approche de fabrication utilisée pour produire le démonstrateur arrière avancé fabriqué par le Centre aérospatial allemand (DLR) dans le cadre de la technologie CS2. plate-forme pour gros porteurs (LPA). Ce démonstrateur vise à apporter des solutions fiables et compétitives pour la simulation de l'échauffement lors du placement automatisé des fibres (AFP) pour réaliser une fabrication à cadence élevée de raidisseurs thermoplastiques et d'outillages auto-chauffés pour prendre en charge la co-consolidation d'un ensemble peau-raidisseur.
Pour plus de détails sur la manière dont FRAMES s'intègre dans les objectifs du projet Advanced Rear End Demonstrator, consultez la dernière section de cet article.
Modélisation thermique optique du chauffage par lampe flash au xénon système
L'AFP des composites thermoplastiques renforcés de fibres de carbone (CFRTP) s'est principalement appuyé sur le chauffage au laser pour atteindre les températures élevées nécessaires au traitement des matériaux matriciels thermoplastiques haute performance tels que PEEK (polyétheréthercétone), PEKK (polyéthercétonecétone) et LM-PAEK (bas point de fusion polyaryléthercétone). Cependant, une nouvelle technologie est apparue, basée sur une lampe flash au xénon pulsée. Dans cette méthode, des impulsions à haute énergie et de courte durée délivrées par une puissante source de chaleur à large bande sont collectées et délivrées par un guide de lumière à quartz. Placé près du point de pincement de la tête AFP, le guide de lumière à quartz façonne et positionne l'énergie lumineuse pour chauffer le substrat et les câbles entrants avant que la consolidation ne soit réalisée sous un rouleau de compactage. Il a été démontré que ce système de lampe flash au xénon correspond au temps de réponse rapide d'un laser et atteint les températures requises pour traiter les composites thermoplastiques.
Pendant le traitement AFP, l'impulsion de la lampe flash au xénon doit être contrôlée pour tenir compte des changements de vitesse et de géométrie et maintenir une température cible. Ceci est obtenu en faisant varier l'énergie, la durée et la fréquence des impulsions de la lampe flash. Pour optimiser ces paramètres, un modèle de simulation opto-thermique a été créé qui utilise des techniques de traçage de rayons optiques (calcul de l'angle de réfraction/réflexion à chaque surface) pour caractériser la source de la lampe flash, ainsi que l'analyse par éléments finis (FEA) pour prédire la température de traitement résultante. En utilisant ces outils de simulation, les essais et erreurs peuvent être évités; les paramètres d'impulsion peuvent être choisis pour atteindre une température de traitement souhaitée sans les essais physiques coûteux et longs.
Heraeus Noblelight (Cambridge, Royaume-Uni) dirige le développement du modèle thermique optique appliqué à son système de lampe flash Humm3. Le processus de création d'une simulation fiable implique la caractérisation optique de la source de la lampe flash au xénon à l'aide de mesures goniométriques (rotation autour d'un axe) et de mesures d'irradiance spectrale (énergie lumineuse reçue par la surface) qui sont ensuite utilisées pour déterminer les niveaux d'énergie spectrale, la distribution spatiale et l'efficacité énergétique électrique-radiative de la source.
Mesure de l'énergie spectrale
La figure 1 ci-dessous montre le montage expérimental conçu pour déterminer l'émission d'énergie d'une lampe flash au xénon par rapport à la longueur d'onde en utilisant des mesures d'irradiance spectrale. Dans ce système, la lumière de la lampe flash au xénon pénètre dans un détecteur à une distance prédéfinie (généralement de 0,5 à 1 mètre, à gauche ci-dessous). Cette lumière est ensuite transportée via un câble optique dans un système à double monochromateur (en bas à gauche ci-dessous) qui détermine l'intensité lumineuse à une longueur d'onde spécifique. Il en résulte un tracé spectral détaillé de l'irradiance de la source lumineuse - dans ce cas, la courbe d'émission entière de l'énergie lumineuse au xénon de la lampe flash Humm3 est mesurée (Fig. 2).
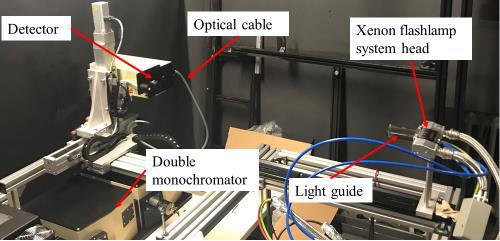
Fig. 1. Configuration de test à double monochromateur utilisée pour les mesures d'irradiance spectrale. La lumière de la lampe flash au xénon (en haut à droite) passe dans un détecteur (en haut à gauche) qui la transporte via un câble optique dans un double monochromateur qui mesure l'intensité lumineuse à une longueur d'onde spécifique. Cela permet un tracé détaillé à travers le spectre de l'énergie lumineuse émise par la lampe flash. Crédit photo :Heraeus Noblelight
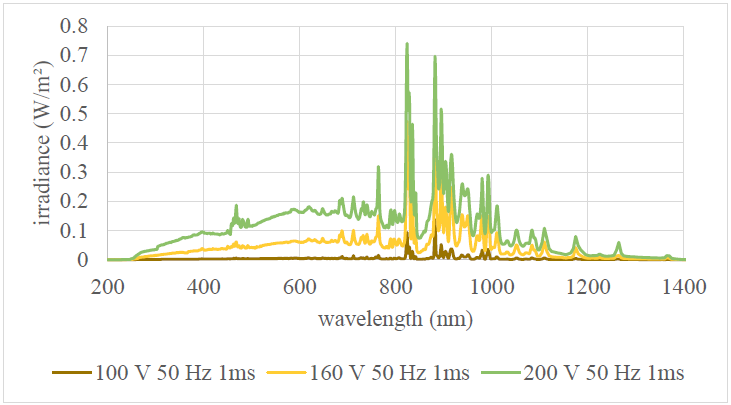
Fig. 2. Mesures d'irradiance spectrale de la lumière sortant de la lampe flash au xénon Humm3. Crédit photo :Heraeus Noblelight
Mesure de l'efficacité énergétique
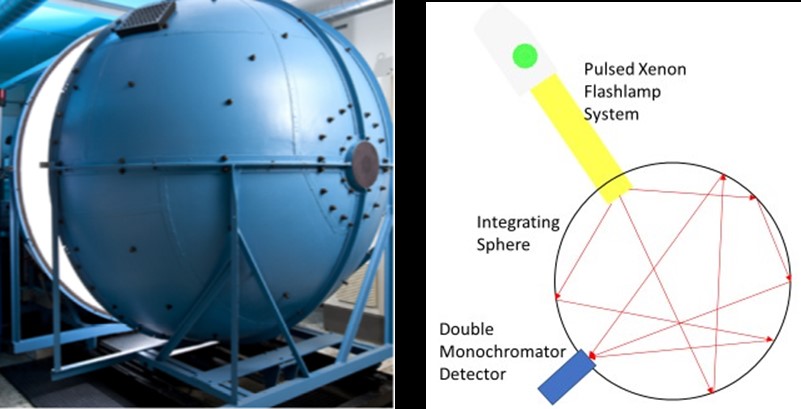
Fig. 3. Schéma de la sphère d'intégration utilisée pour les mesures spectrales de puissance radiante. Crédit photo :Heraeus Noblelight
L'efficacité du système a également été évaluée à l'aide d'une sphère d'intégration (Fig. 3) au laboratoire Heraeus à Hanau, en Allemagne, pour déterminer avec précision l'énergie spectrale sortant du guide de lumière Humm3 à différents niveaux de tension. La sphère présente une surface diffuse hautement réfléchissante qui dirige pratiquement toute l'énergie optique sortant de la tête de la lampe flash vers un détecteur à double monochromateur. En modulant l'énergie d'impulsion pour une durée et une fréquence d'impulsion données, la puissance optique moyenne sortant de la tête Humm3 est mesurée en fonction de la longueur d'onde pour une plage de tensions de lampe flash.
Analyser la distribution angulaire de l'énergie
La position de la tête de lampe flash par rapport au point de pincement de la tête AFP est également un aspect critique pour obtenir une superposition de composites de haute qualité. Parallèlement aux mesures de la puissance de sortie, la variation de l'intensité lumineuse de la lampe flash au xénon par rapport à son angle par rapport à la source a été mesurée. Toutes les mesures ont été normalisées pour étudier la distribution d'énergie angulaire plutôt que la puissance de sortie absolue à ce stade. Ces résultats ont été utilisés pour valider une simulation de lancer de rayons de la lampe flash pour prédire comment l'énergie des impulsions de la lampe flash est distribuée entre le substrat, le point de pincement et les câbles entrants.
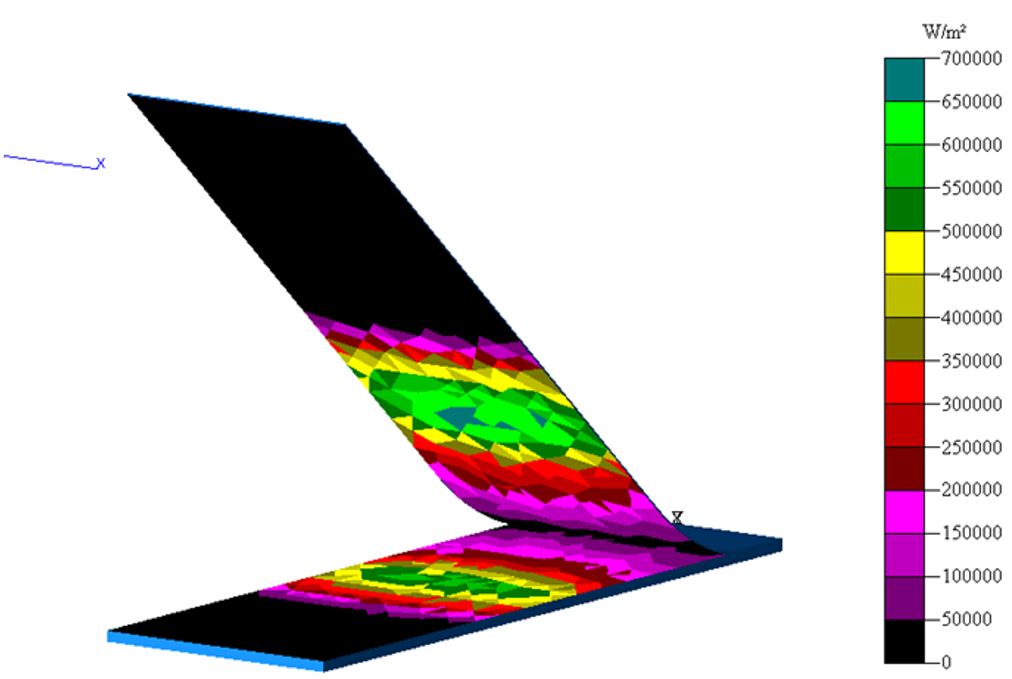
L'analyse par traçage de rayons optiques (Fig. 4) - réalisée à l'aide du logiciel TracePro (Lambda Research Corp., Littleton, Mass., États-Unis) - est ensuite détaillée pour calculer les profils d'éclairement énergétique de surface sur le câble composite et le substrat. Ces profils d'irradiance sont utilisés comme conditions aux limites d'entrée pour la simulation thermique. Le comportement optique et thermique des rubans LM-PAEK renforcés de fibres de carbone a également été caractérisé pour alimenter le modèle aux températures de traitement appropriées.
Validation via des essais physiques
En guise d'étape de validation, des essais physiques d'AFP ont été réalisés à Compositadour (Bayonne, France) pour montrer la capacité de la simulation à prédire les valeurs de température observées lors du dépôt réel d'AFP. La thermographie infrarouge et des thermocouples minces intégrés à l'intérieur des couches composites ont été utilisés pour mesurer les températures de traitement pendant les essais AFP. Les mesures semblent montrer un accord raisonnable avec les profils de température prévus dans la région pour fermer le point de pincement et également à travers l'épaisseur.
Mais ces mesures mettent aussi en évidence l'influence de l'outillage sur la gestion thermique des premiers plis. Au début du drapage, les premiers plis sont très proches de la surface de l'outil, ce qui peut servir de dissipateur thermique. Pour cette raison, un outillage chauffant a été utilisé. La température de l'outil a une forte influence sur la température du point de pincement AFP.
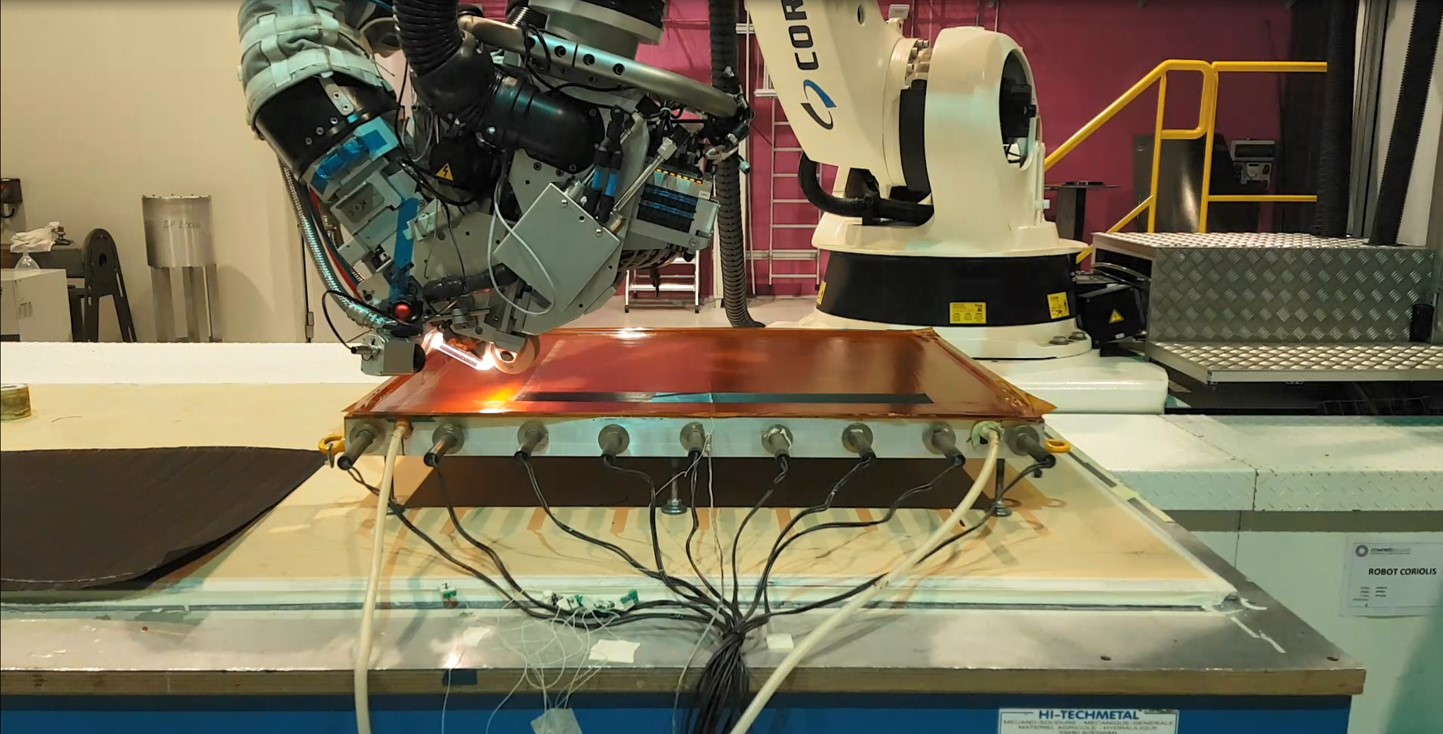
Au cours de cette phase de début de layup, les paramètres d'impulsion de la lampe flash au xénon doivent être ajustés pour maintenir la température du point de pincement constante. Mais une fois que peu de plis sont déposés, le drapage commence à devenir une sorte de couche isolante et l'influence de la température de l'outil diminue. À ce stade du processus, aucun réglage supplémentaire des paramètres d'impulsion n'est nécessaire.
Lors des essais de validation du projet FRAMES, des outillages chauffés ont été utilisés pour évaluer différentes températures de traitement au cours de l'AFP, explique Guillaume Fourage, ingénieur en chef des projets composites chez Compositadour. « L'approche de fabrication du démonstrateur arrière avancé n'est pas encore figée et nous évaluons différentes options pour le drapage de la peau dans le but de trouver le bon équilibre entre le temps de traitement, la consommation d'énergie et la qualité du drapage. La modification de la température de surface de l'outil nous oblige à ajuster les paramètres d'impulsion en conséquence pour atteindre la bonne température de point de pincement. Cela fait partie du plan de développement du modèle thermique optique et nous aide à augmenter la fiabilité et la robustesse de la simulation dans différentes conditions de drapage. »
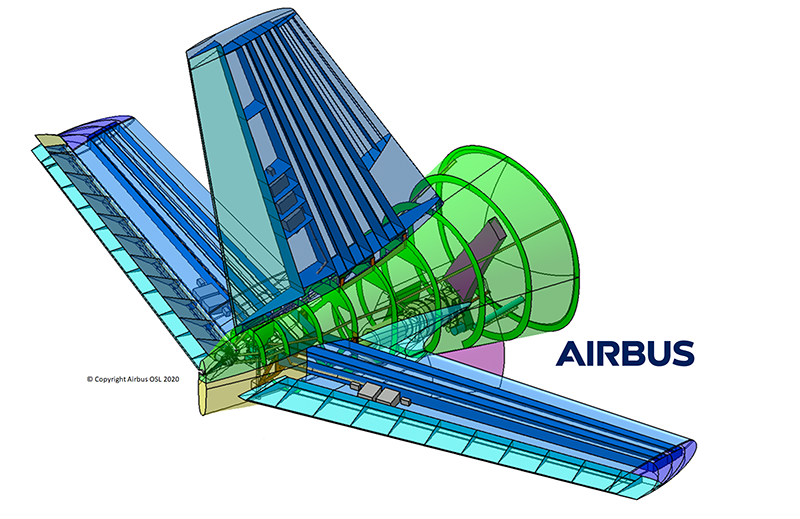
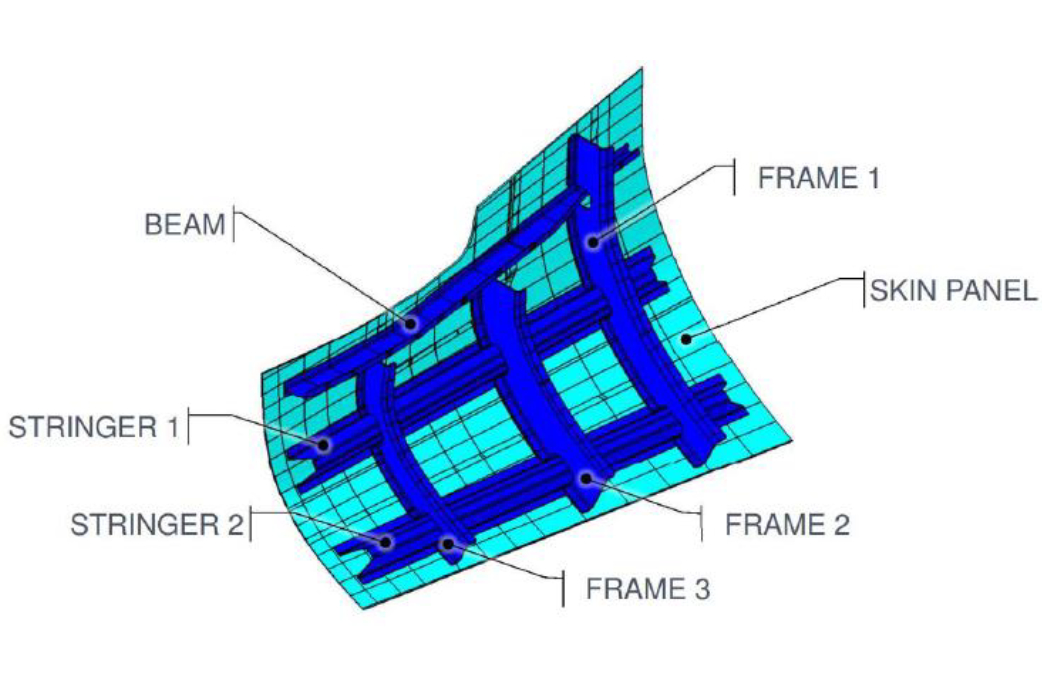
Démonstrateur d'extrémité arrière avancée (ARE) en composite thermoplastique pour Clean Sky 2. Crédit photo : (en haut) Airbus, (en bas) ESTIA-Compositadour
Ce modèle de simulation est maintenant adapté à la configuration finale du système de chauffage et de l'outillage qui sera utilisé pour fabriquer le démonstrateur Advanced Rear End (ARE) du composite thermoplastique CS2. Des pièces sont fabriquées en 2021 pour un assemblage en 2022 avec l'objectif d'atteindre le TRL 6 d'ici la fin du projet en 2023. En parallèle, un niveau de préparation à la fabrication (MRL) de 5/6 est poursuivi, pas seulement pour le démonstrateur ARE , mais aussi pour les procédés de fabrication associés et les outils en cours de développement. Les objectifs généraux du projet de démonstrateur ARE sont les suivants :réduire les coûts jusqu'à 20 %, le poids des composants jusqu'à 20 % et la consommation de carburant jusqu'à 1,5 %, ainsi qu'améliorer l'aérodynamisme conformément aux objectifs environnementaux de Clean Sky.
Ce projet a reçu un financement de l'entreprise commune (JU) Clean Sky 2 dans le cadre de la convention de subvention n° 886549. L'entreprise commune reçoit le soutien du programme de recherche et d'innovation Horizon 2020 de l'Union européenne et des membres de l'entreprise commune Clean Sky 2 autres que l'Union.
Pour plus d'informations, contactez Guillaume Fourage, [email protected]
Résine
- Recyclage :composites thermoplastiques renforcés de fibres continues avec polycarbonate recyclé
- Solvay augmente la capacité des composites thermoplastiques
- Contrôlez votre système d'éclairage avec votre voix
- Le projet Clean Sky 2 FUSINBUL développe des cloisons étanches à pression en fibre de carbone à grande échelle
- Clean Sky 2 publie les résultats du projet
- Le consortium cible des solutions pour les structures composites thermoplastiques en fibre de carbone
- Hexcel s'associe à Lavoisier Composites, Arkema
- Porte thermoplastique une première pour les composites automobiles
- Fabrication rapide d'ébauches composites sur mesure