Conception pour la fabrication automatisée de composites d'aérostructures de faible volume
La fabrication d'aérostructures composites pour avions commerciaux s'étend sur plus de 50 ans et n'a cessé de progresser de pièces plus petites à de très grandes structures primaires — fuselage, ailes, empennage, moteurs — développées au début des années 2000 pour le Boeing 787 et l'Airbus A350. La grande majorité de cette évolution dépendait de l'utilisation de préimprégnés en fibre de carbone/époxy durcis à l'autoclave, initialement posés à la main, puis, finalement, via le placement automatisé des fibres (AFP), la pose automatisée de ruban (ATL) et d'autres processus automatisés.
Ces technologies de matériaux et de processus (M&P) étaient adaptées aux gros porteurs 787 et A350 qui, avant la pandémie, avaient des taux de construction de 10 à 15 par mois. Cependant, alors que Boeing et Airbus se tournent vers l'avenir et envisagent d'appliquer des matériaux composites dans les structures primaires des avions monocouloirs qui devraient avoir des cadences de construction de 60 à 100 par mois, la conception et la fabrication et la fabrication privilégieront les cadences élevées, hors de -autoclave (OOA), processus hautement automatisés. Ces processus incluent, entre autres, le moulage par transfert de résine (RTM), le moulage par compression et l'infusion de résine liquide.
Mais même si la fabrication à cadence élevée dominera le secteur aérospatial commercial, la fabrication d'aérostructures composites à faible cadence Les avions, y compris les programmes d'avions régionaux et d'avions d'affaires, non seulement persisteront, mais pourront et devraient bénéficier de certaines des mêmes innovations en matière de coûts, de conception et de M&P qui seront déployées dans les programmes à haut débit.
C'est dans cette optique que le programme européen Clean Sky 2 a lancé OPTICOMS — Opti misé Com poser S structures pour petits aéronefs. OPTICOMS est un consortium dirigé par le fabricant aérospatial Israel Aerospace Industries (IAI, Lod, Israël) avec des partenaires qui fournissent des technologies d'automatisation innovantes, des matériaux, des logiciels, des outils et des machines. L'objectif d'OPTICOMS est d'évaluer une conception de caisson de voilure de production à faible taux qui comprend une fabrication automatisée, des structures intégrées, un traitement OOA, une grande liaison structurelle, des outils de fabrication et d'assemblage innovants, une surveillance de la santé structurelle des lignes de liaison et des tests virtuels.
Arnold Nathan, directeur de la R&D pour le groupe aviation à l'IAI et directeur d'OPTICOMS, déclare :« Chaque fois que nous essayons d'intégrer l'automatisation dans une [discussion] sur la fabrication de composites, nous entendons souvent nos clients dire : « L'automatisation, c'est bien, mais seulement quand vous avez un gros volume de production.' OPTICOMS a été mis en place pour savoir si vous pouvez justifier l'automatisation quand vous ne pas ont une production en grand volume. L'automatisation de la fabrication de composites peut-elle être compétitive et rentable pour les faibles volumes ?"
Conception des ailes
OPTICOMS est né d'une demande Clean Sky 2 émise par l'avionneur d'affaires italien Piaggio Aerospace (Gênes) pour le développement d'une aile alternative tout composite pour son P180 Avanti biturbopropulseur d'affaires à neuf passagers. Le caisson de l'aile mesure 6,8 mètres de long, 0,71 mètre de large à la racine et 0,28 mètre de large à l'extrémité. Piaggio, dit Nathan, était impatient d'évaluer une alternative au boîtier d'aile tout en métal - une alternative avec les mêmes dimensions, mais offrant un poids réduit (20%). En outre, le coût devrait être réduit de 20 à 30 % par rapport à la fabrication de caissons de voilure en composite conventionnel. IAI et ses partenaires ont remporté le contrat et ont commencé à travailler avec Piaggio en 2016.
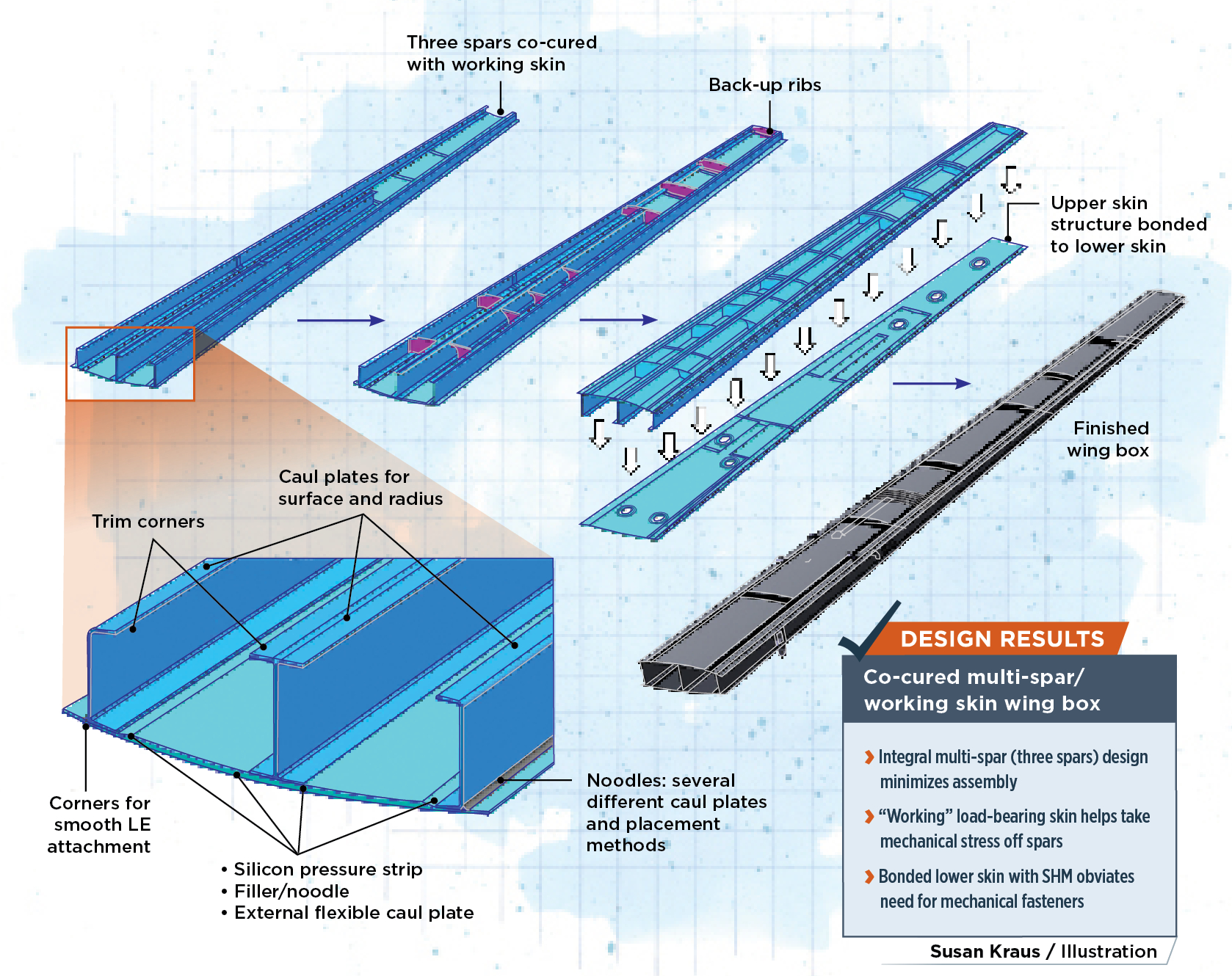
OPTICOMS est un programme en plusieurs parties conçu pour effectuer une série d'études commerciales très détaillées et minutieusement menées afin d'évaluer et de déterminer la conception optimale de l'aile, la combinaison de matériaux et le processus de fabrication OOA pour la fabrication automatisée d'un caisson d'aile tout composite à faible volume.
IAI et OPTICOMS, explique Nathan, ont décidé très tôt qu'ils se concentreraient sur et évalueraient l'utilisation de trois processus de fabrication fournis par trois partenaires :Coudes, France); placement automatisé de fibres (AFP) de câbles secs et préimprégnés, fournis par Coriolis Composites (Queven, France) ; et la technologie de placement automatisé de matière sèche (ADMP), fournie par Danobat (Elgoibar, Espagne). La sélection de ces technologies et partenaires serait essentielle pour guider l'IAI tout au long de ses études commerciales multivariantes.
Résultats de la conception
- La conception intégrale à plusieurs longerons (trois longerons) minimise l'assemblage
- La peau porteuse « de travail » aide à éliminer les contraintes mécaniques des longerons
- La peau inférieure collée avec SHM évite le besoin d'attaches mécaniques
La première étape de cette étude commerciale a été l'évaluation de la conception. Cet effort a été dirigé à l'IAI par Adam Sawday, ingénieur en conception structurelle pour les technologies avancées. Sawday dit que lui et IAI ont adopté une approche épurée de la conception de l'aile, étudiant plus de 18 concepts à travers une variété d'architectures. Les conceptions sont rapidement tombées dans l'une des deux catégories. Le premier emploie une peau « de travail » dans laquelle la peau du caisson de voilure devient une structure porteuse. La seconde utilise des peaux non fonctionnelles avec des semelles de longeron chargées. Au sein de ces catégories, les conceptions incluent un concept traditionnel avec des nervures, des longerons et deux longerons, ou, alternativement, l'utilisation de trois longerons - appelés longerons multiples - sans nervures ni longerons. Plusieurs concepts ont également envisagé l'utilisation d'une construction en panneaux sandwich qui produit une peau semi-travail.
« Notre mantra était de réduire les efforts de fabrication et d'assemblage », explique Sawday. "Et nous pensons que si vous pouvez développer une structure plus efficace et plus intégrale, vous obtiendrez une structure moins chère et plus légère."
Sawday dit que les conceptions ont été mesurées par rapport à une série de mesures pour évaluer leur capacité à atteindre les objectifs de coût et de poids du programme. Ces mesures comprennent :les coûts des matériaux, la complexité de la conception, les coûts de fabrication des composants, les coûts d'assemblage, les coûts des essais non destructifs (END), les coûts d'outillage et de gabarit, le poids, la résistance, le niveau de préparation technologique (TRL), les considérations écologiques, le profil de risque, la robustesse et fiabilité. Parmi ceux-ci, les critères les plus pondérés étaient le poids, les coûts de fabrication et d'assemblage, la complexité de la conception, le TRL et le profil de risque.
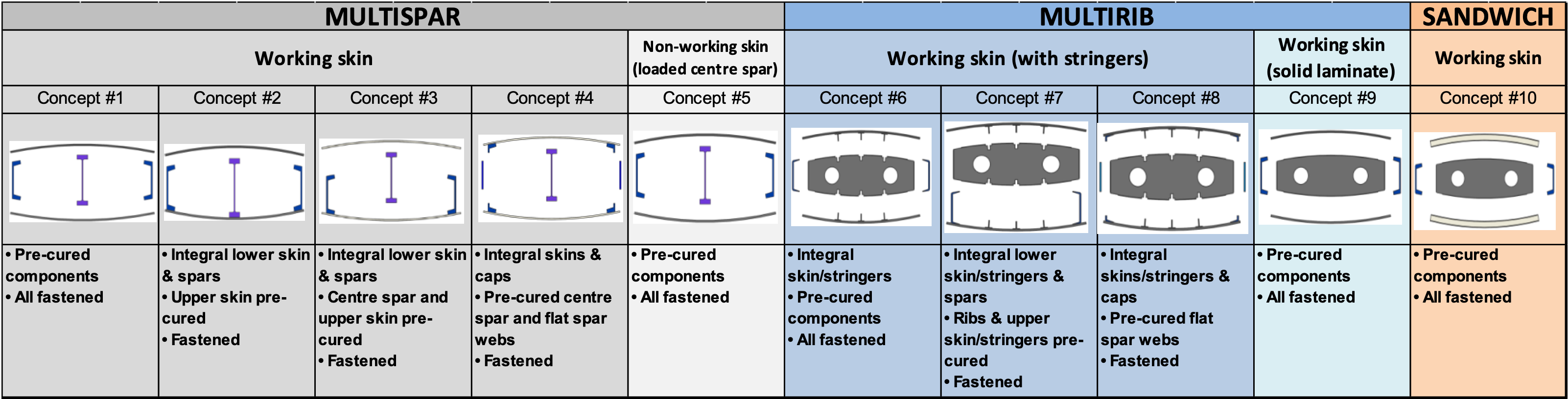
Sélection descendante jusqu'à la conception finale
Les données de cette évaluation ont aidé IAI à sélectionner les concepts de conception à 10 finalistes. Quatre étaient à plusieurs longerons/peau de travail, un était à plusieurs longerons/peau de travail avec longerons chargés, quatre étaient à plusieurs nervures/peau de travail avec longerons, un était à plusieurs nervures/peau de travail sans longerons et un était en sandwich structure/peau de travail sans longerons. Chaque conception offrait diverses combinaisons de pré-polymérisation, de co-polymérisation, de collage ou de fixation mécanique.
Pour arriver à la conception finale, il a fallu une autre série d'études commerciales utilisant bon nombre des mêmes critères que dans la première étude. Chaque conception a reçu une valeur commerciale, basée sur la façon dont elle répondait aux critères. "Nous avions cette grande table de compromis, et chaque option de conception avait une valeur, et cela nous a aidé à voir l'option la plus solide", explique Sawday.
Il y avait une conception, dès le départ, qui a toujours bien fonctionné dans les études commerciales et semblait susceptible de sortir en tête, note Sawday. Et il l'a fait. Surnommé en interne sous le nom de peau multi-spar/travail n ° 2, il comprend une peau supérieure hautement intégrée et co-polymérisée et trois longerons. Ceux-ci sont ensuite collés à une peau inférieure qui a des panneaux d'accès. Située sélectivement entre les longerons se trouve une série de nervures « de secours », conçues pour soutenir la peau, qui supporte la plupart des charges de flexion.
« Les structures les plus favorables que nous avons développées », explique Sawday, « étaient celles à longerons multiples, où la peau devient porteuse. Les longerons deviennent alors des structures plus simples et plus minces, et pas aussi lourdes que dans les conceptions d'ailes composites traditionnelles. Nous avons pensé que si nous pouvions simplement rendre ces espars très simples, avec une section transversale constante, cela éviterait beaucoup de maux de tête et beaucoup de ferraille. »
Sawday affirme que la conception intégrale collée à plusieurs longerons/peau de travail s'est avérée particulièrement prometteuse pour ses coûts d'assemblage réduits, son faible poids, sa facilité d'automatisation et son faible nombre global de pièces. La question demeurait cependant :quels matériaux et quels procédés de fabrication seraient les mieux adaptés pour donner vie à ce design ?
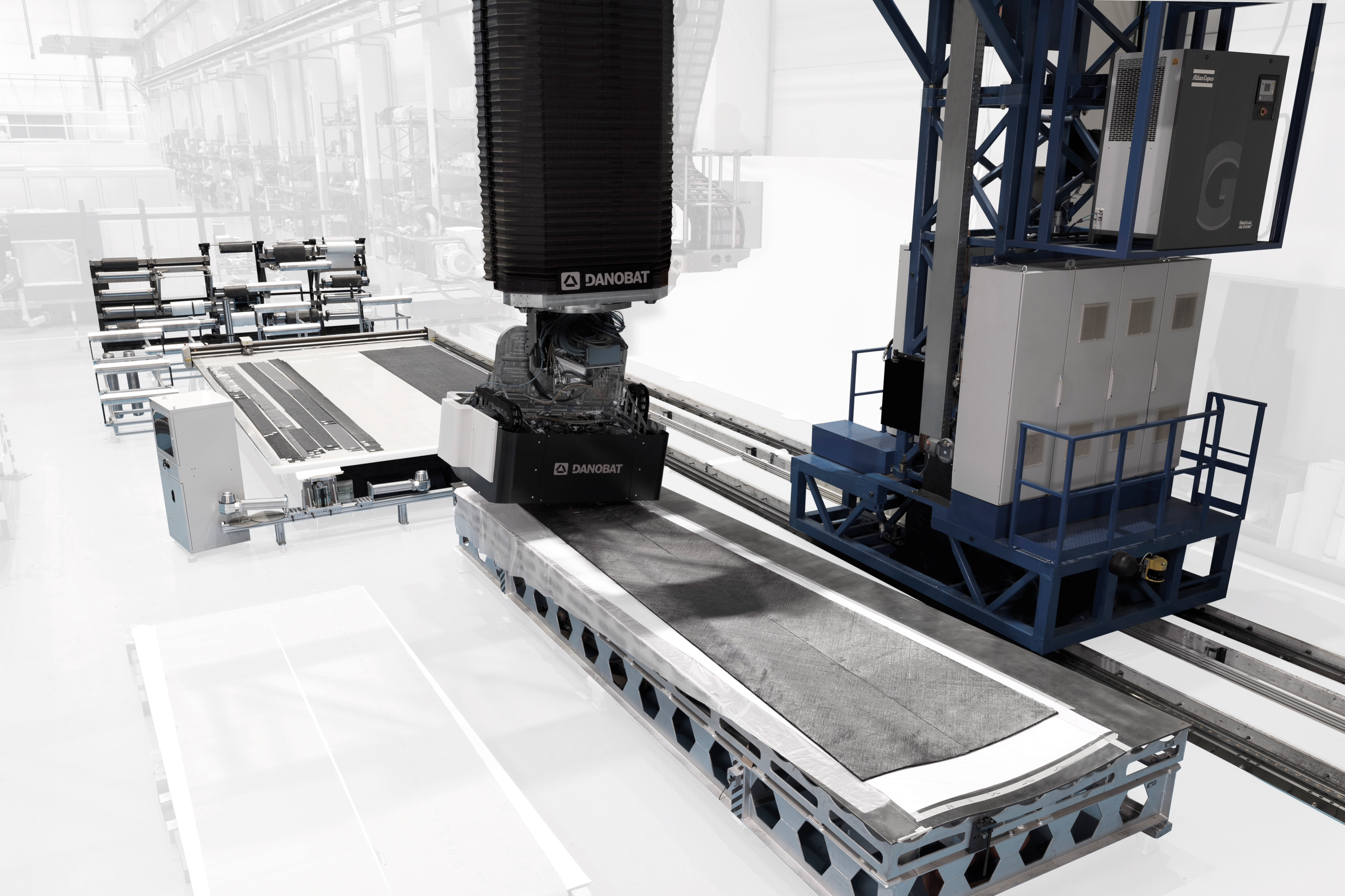
Études commerciales M&P
Tout d'abord, les études sur le commerce des matériaux. Celles-ci ont été réalisées à l'IAI par Yaniv Yurovitch, ingénieur en matériaux composites. Il dit qu'OPTICOMS a commencé à évaluer les préimprégnés en fibre de carbone OOA, les fibres de carbone sèches (rubans et tissus) et les résines sur la base des recommandations de Piaggio, de l'IAI et de partenaires technologiques. Le résultat a été une liste de 35 matériaux qualifiés et nouveaux.
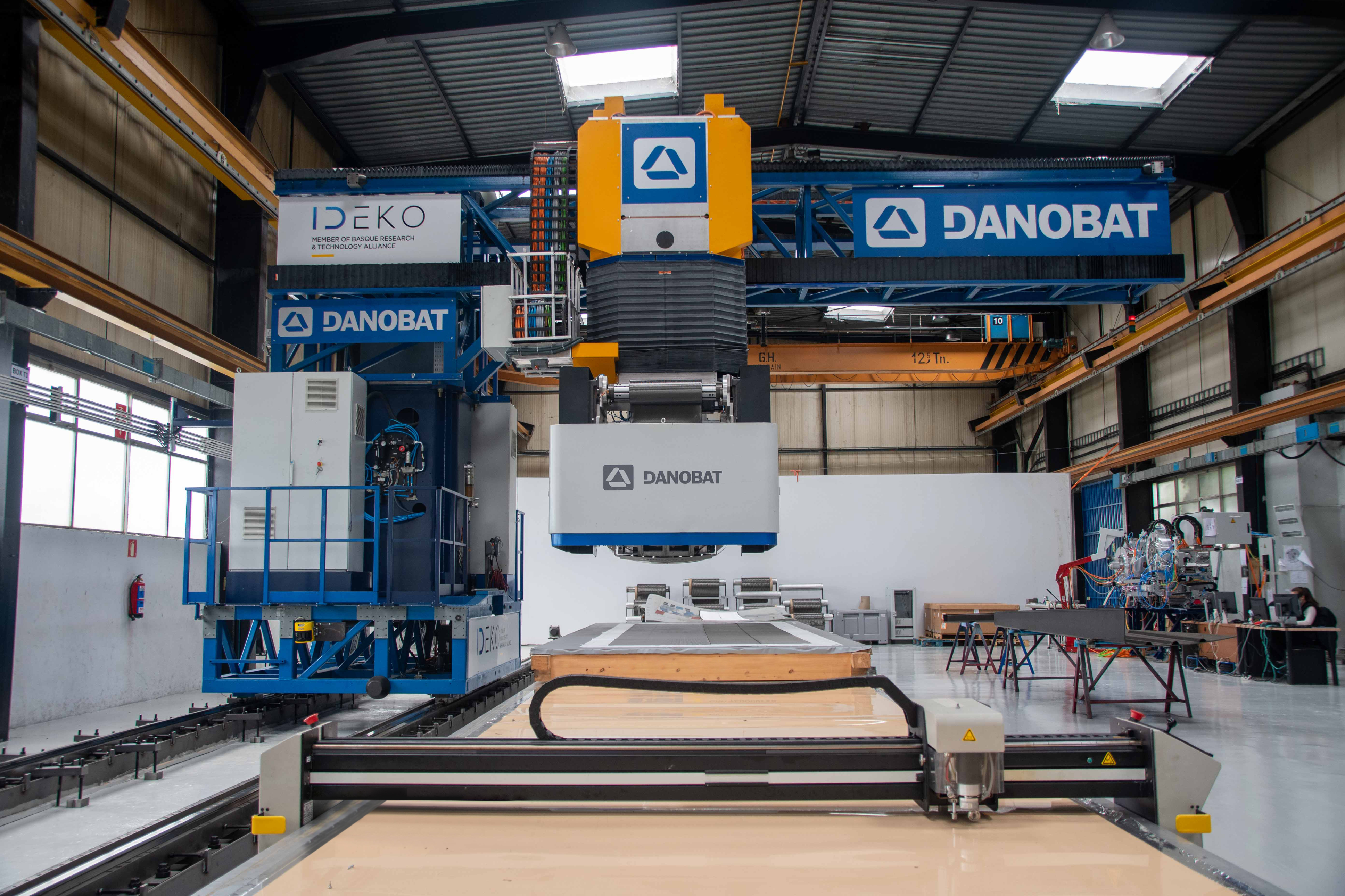
Ce premier groupe de matériaux a ensuite été criblé sur la base des paramètres les plus cruciaux pour le projet OPTICOMS :Coût, température de transition vitreuse (Tg ), la viscosité (pour l'infusion ou l'injection) et l'aptitude aux technologies de drapage automatisé. Cette évaluation a réduit la liste des matériaux de 35 à 20 préimprégnés, fibres sèches et résines.
Des échantillons de chacun de ces 20 matériaux ont été commandés; Yurovitch a ensuite fabriqué des coupons et effectué des tests mécaniques dans le cadre de la prochaine sélection. « C'était un très gros lot de travail », dit Yurovitch. « Cela nous a permis de prendre plus de décisions et de sélectionner les trois derniers matériaux. » Ces combinaisons fibre/résine sont :
- Toray Composites Materials America (Tacoma, Wash., États-Unis) 2510 fibre de carbone/préimprégné époxyde
- Les rubans UD en fibre de carbone HiTape d'Hexcel (Stamford, Connecticut, États-Unis), à utiliser avec la résine époxy HexFlow RTM6 d'Hexcel.
- Tissu en fibre de carbone sans sertissage (NCF) fourni par SAERTEX (Saerbeck, Allemagne), à combiner par infusion avec l'époxy durci PRISM EP2400 de Solvay Composite Materials (Alpharetta, Géorgie, États-Unis).
Cette liste favorise évidemment l'utilisation de fibres sèches, qui à son tour privilégie l'infusion comme procédé de fabrication. Nathan dit que cela est dû en partie au défi de gérer la durée de conservation du préimprégné dans un environnement à faible volume. « Lorsque vous parlez de production à faible volume, vous ne voulez vraiment pas transporter beaucoup de préimprégné et vous soucier de la gestion de la durée de conservation », dit-il. "La fibre sèche n'a pas ce problème."
Ces trois matériaux ont également été associés à un ou plusieurs des procédés de fabrication sélectionnés pour OPTICOMS :le préimprégné Toray correspond au pick-and-place et à l'AFP, le HiTape/RTM6 d'Hexcel correspond à l'AFP ainsi qu'au pick and place, et le SAERTEX NCF correspond au pick-and-place ou à ADMP.
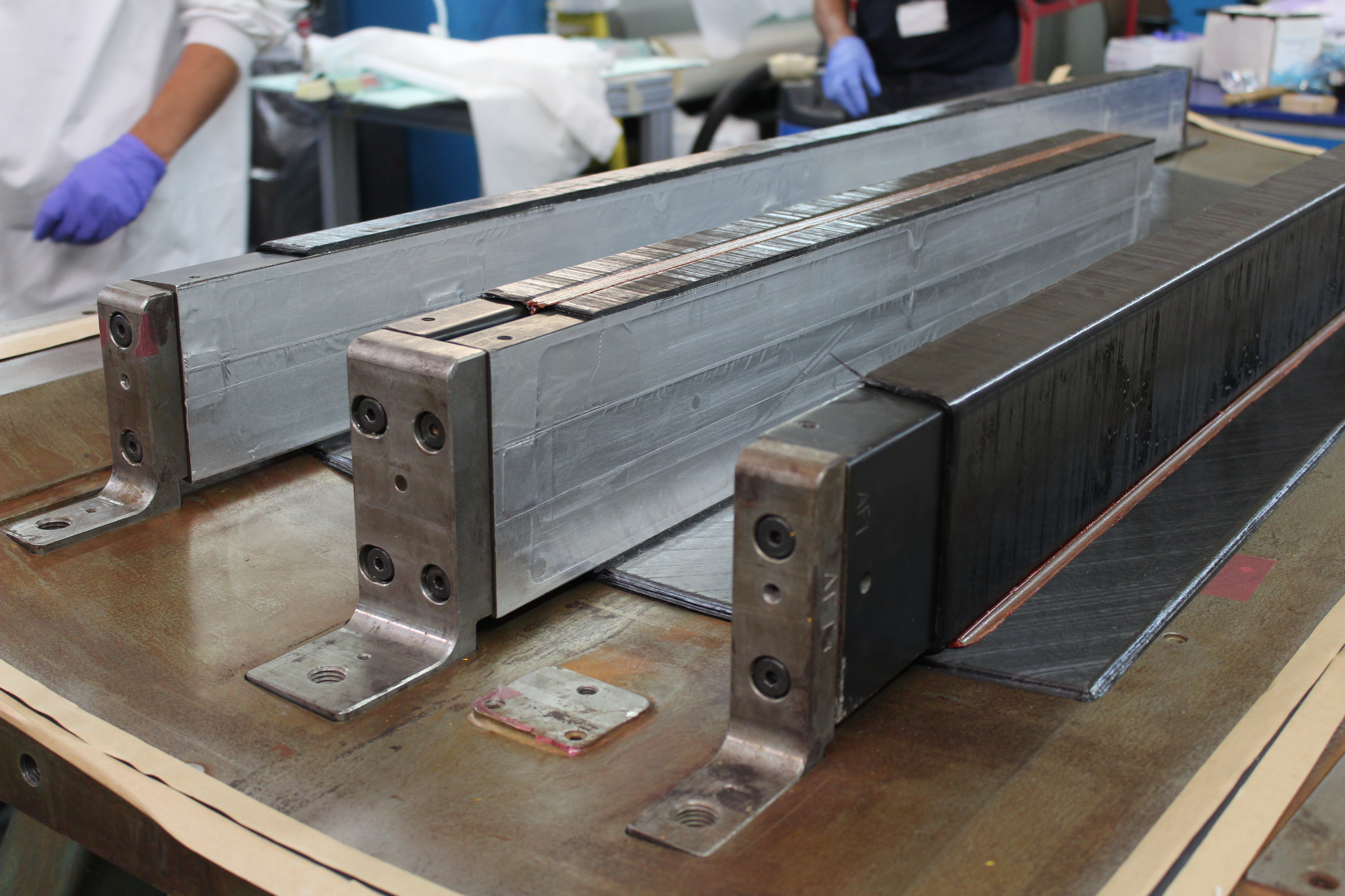
Les métiers autour des procédés de fabrication automatisés — qui sont les mieux adaptés à quel type de pièce — sont toujours exercés par IAI et OPTICOMS. Cependant, les résultats préliminaires, dit Nathan, orientent définitivement les technologies dans certaines directions. Par exemple, la technologie ADMP de Danobat, développée à l'origine pour le placement rapide de tissus larges dans la fabrication de pales d'éoliennes, s'est avérée tout aussi efficace dans OPTICOMS. La technologie a mûri pendant OPTICOMS et sa robustesse et sa fiabilité ont été améliorées, mais il s'agit toujours d'une technologie de drapage aérospatiale moins mature que l'AFP.
Inversement, l'AFP avec le système Coriolis, avec sa vaste expérience aérospatiale, est une technologie mature et précise, mais a des temps de préparation plus longs que l'ADMP et nécessite des inspections relativement fréquentes pour vérifier les anomalies. Coriolis a fait des progrès notables tout au long du projet OPTICOMS avec le développement d'une inspection en ligne et en temps réel du drapage pour faire face à ce défi, explique Nathan. Enfin, la technologie pick-and-place de TME, conçue pour automatiser le transfert des tissus coupés de la table de découpe au moule, semble être la plus efficace pour les pièces plus petites et discrètes, comme les nervures de renfort dans le multi-spar/travail conception de la peau.
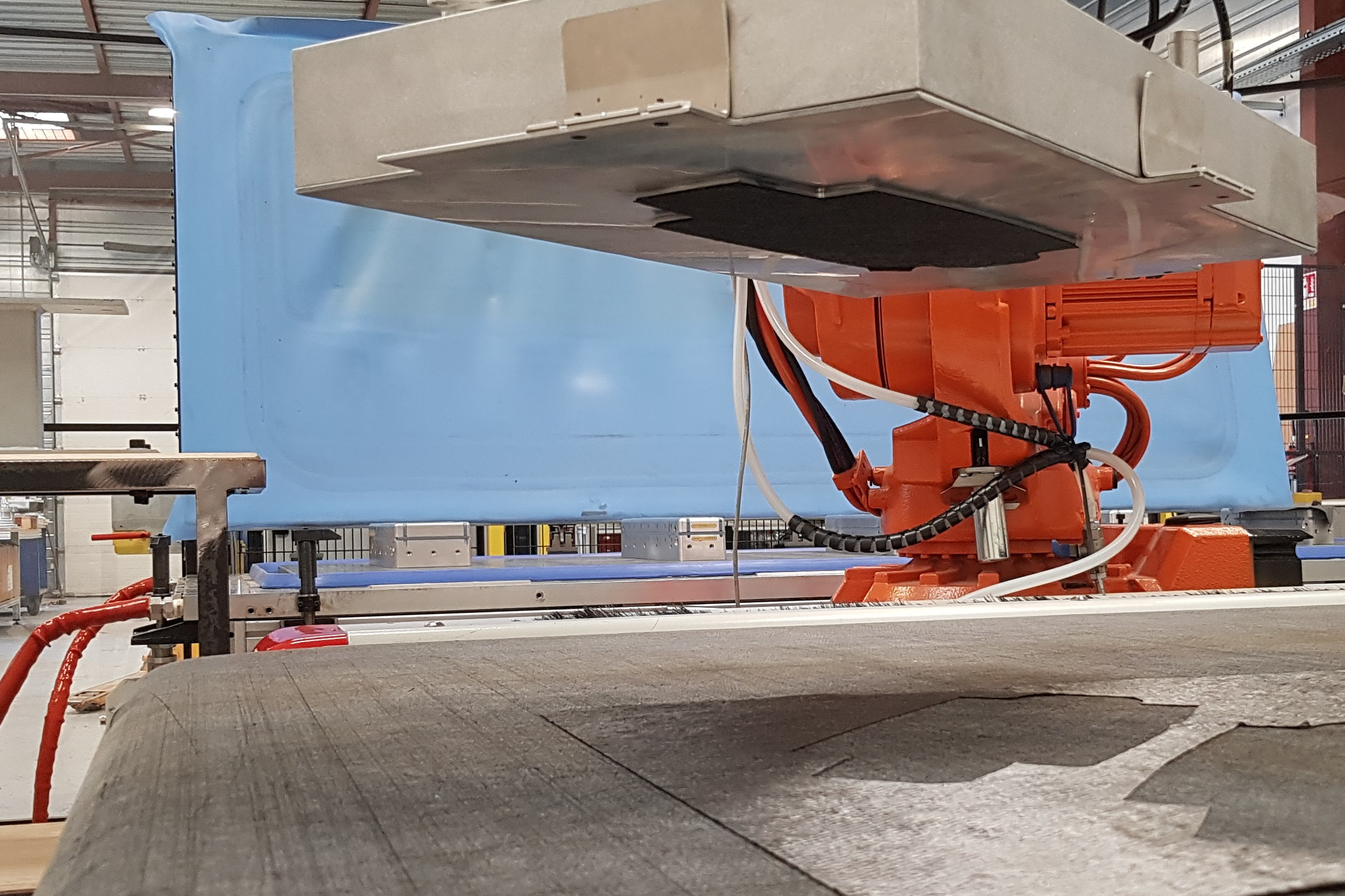
Prochaines étapes
OPTICOMS est en bonne voie pour atteindre les objectifs d'automatisation, d'économies de coûts et de poids fixés par le programme, déclare Nathan, bien qu'il reste encore plusieurs mois de travail à faire pour évaluer les processus de fabrication ainsi que les solutions d'assemblage.
« C'est un point important à propos d'OPTICOMS », explique-t-il. « Nous avons eu une solide sélection vers le bas de la conception. Nous avons eu une sélection de matériel. Nous avons eu une sélection descendante des processus. Tout cela demande du temps et des efforts. C'est l'un des aspects uniques du projet. »
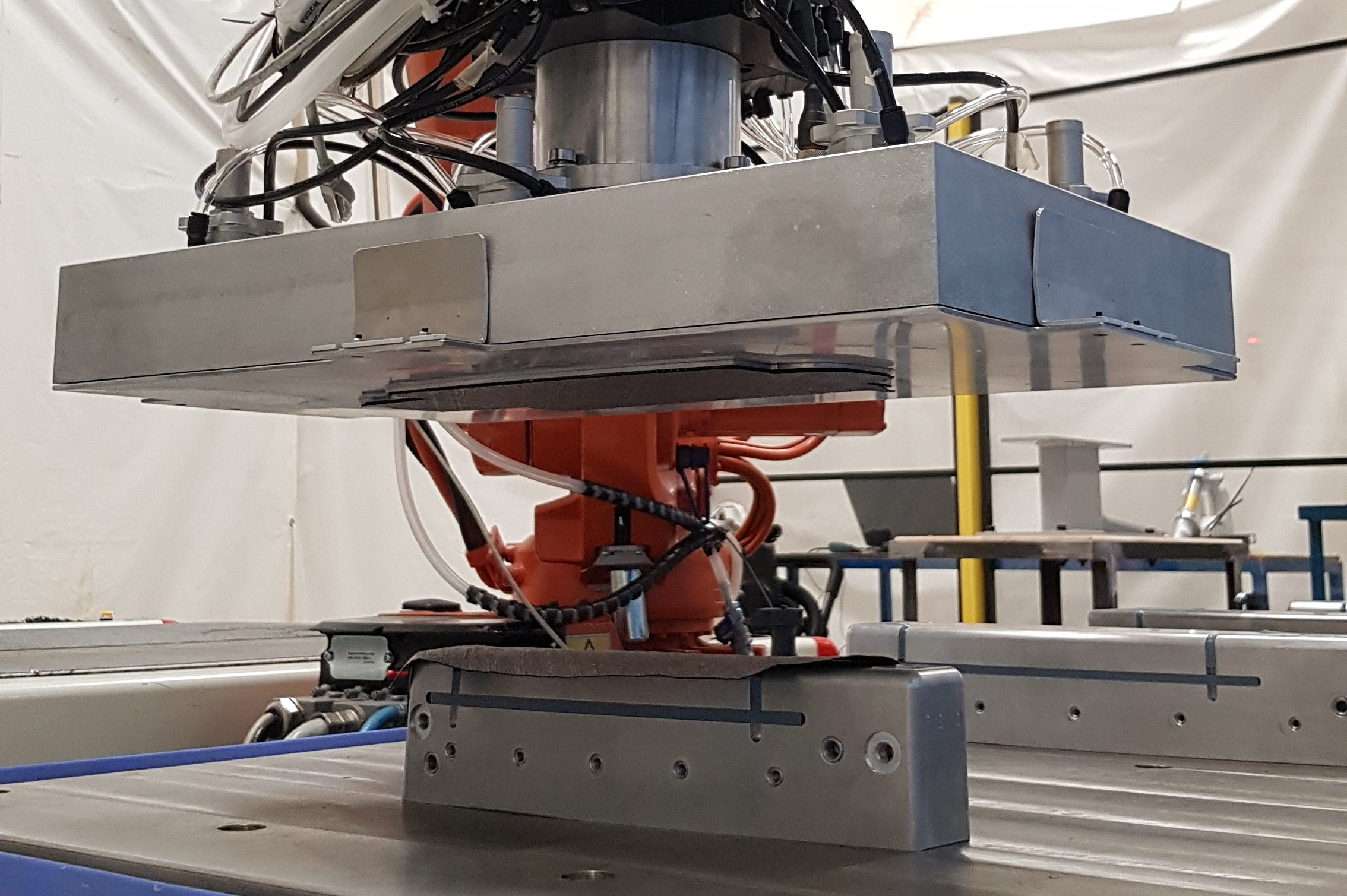
OPTICOMS a lancé trois appels à propositions (AP) pour des technologies et du matériel pour soutenir, assurer et améliorer les objectifs du projet. Les propositions retenues sont devenues des projets Clean Sky 2, associés et complémentaires au partenaire principal « mère » d'OPTICOMS, travaillant tous ensemble vers un objectif commun.
Le premier effort de ce développement est FITCoW, qui vise à développer un nouveau système d'outillage intégral en fibre de carbone pour le co-durcissement de la peau de travail et de trois longerons. La liste des objectifs de FITCoW est ambitieuse :réduction de 50 % du coût des pièces fabriquées, réduction des coûts d'outillage de 30 % (par rapport à l'alternative métallique), réduction de 20 % du temps de fabrication par rapport aux alternatives autoclave et OOA, réduction de 40 % des écarts de CTE par rapport à l'outillage Invar , 20% de réduction du temps de chauffage et de refroidissement et 40% de réduction du temps d'inspection grâce à de meilleures capacités de contrôle dimensionnel.
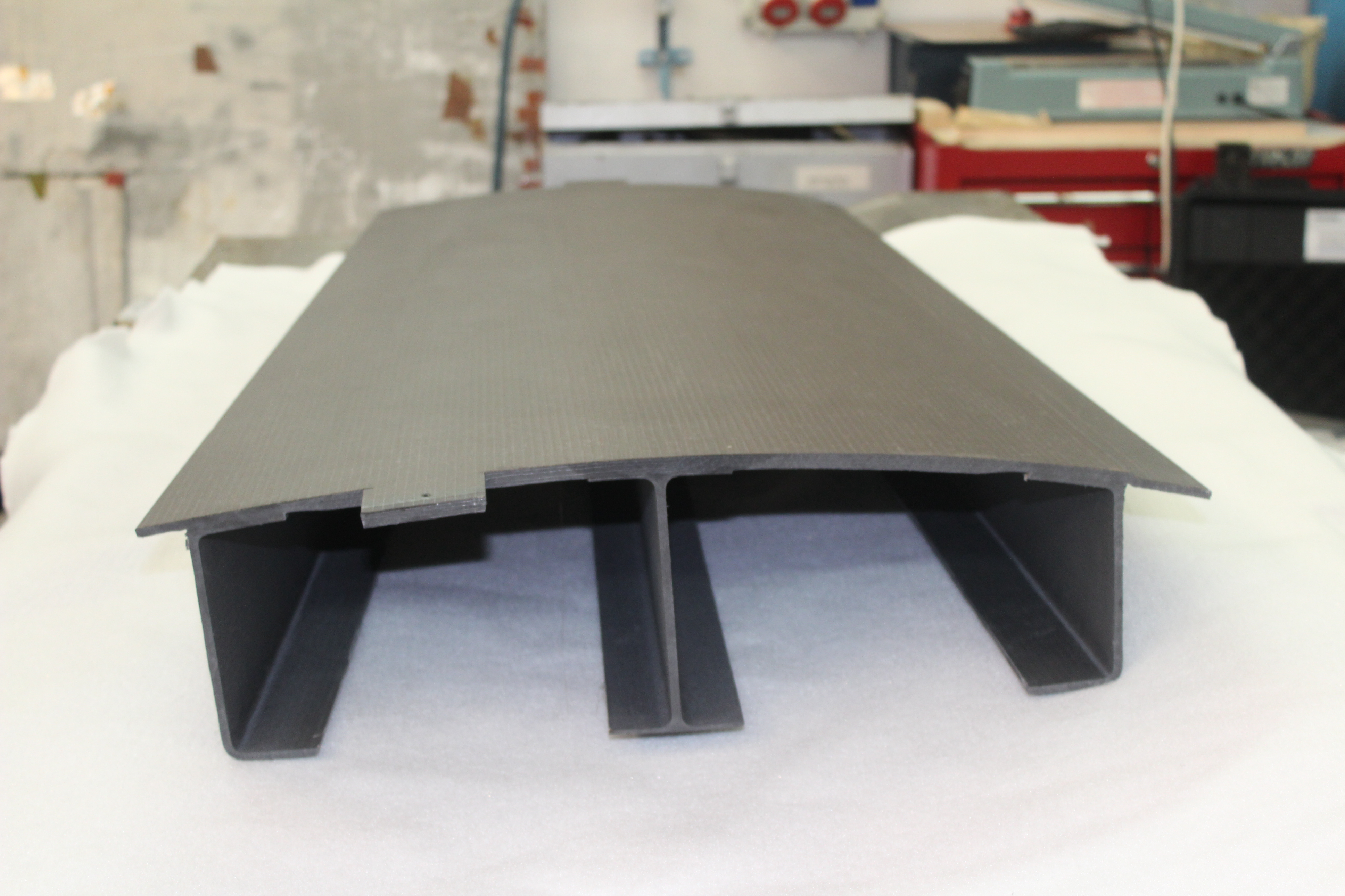
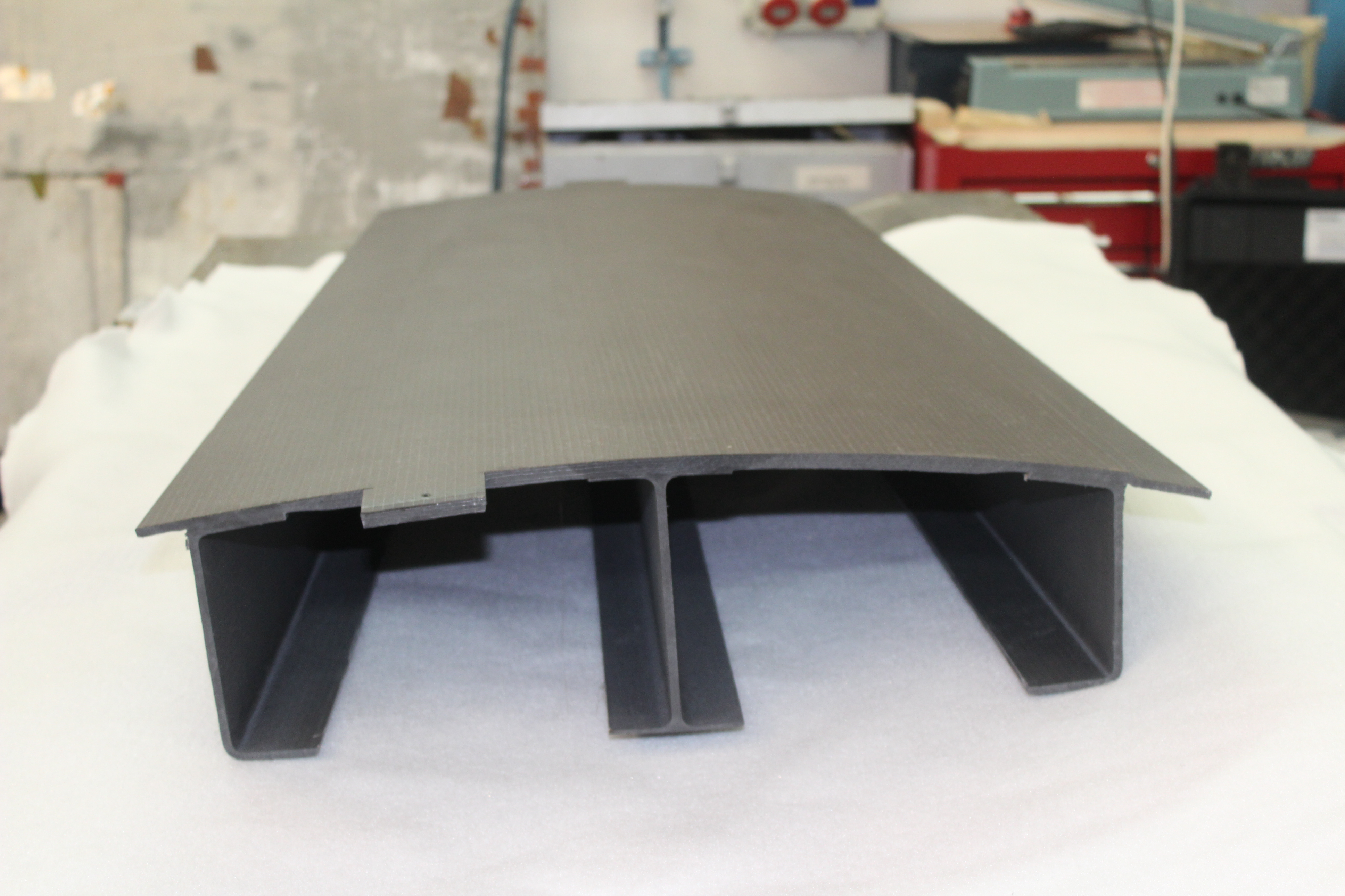
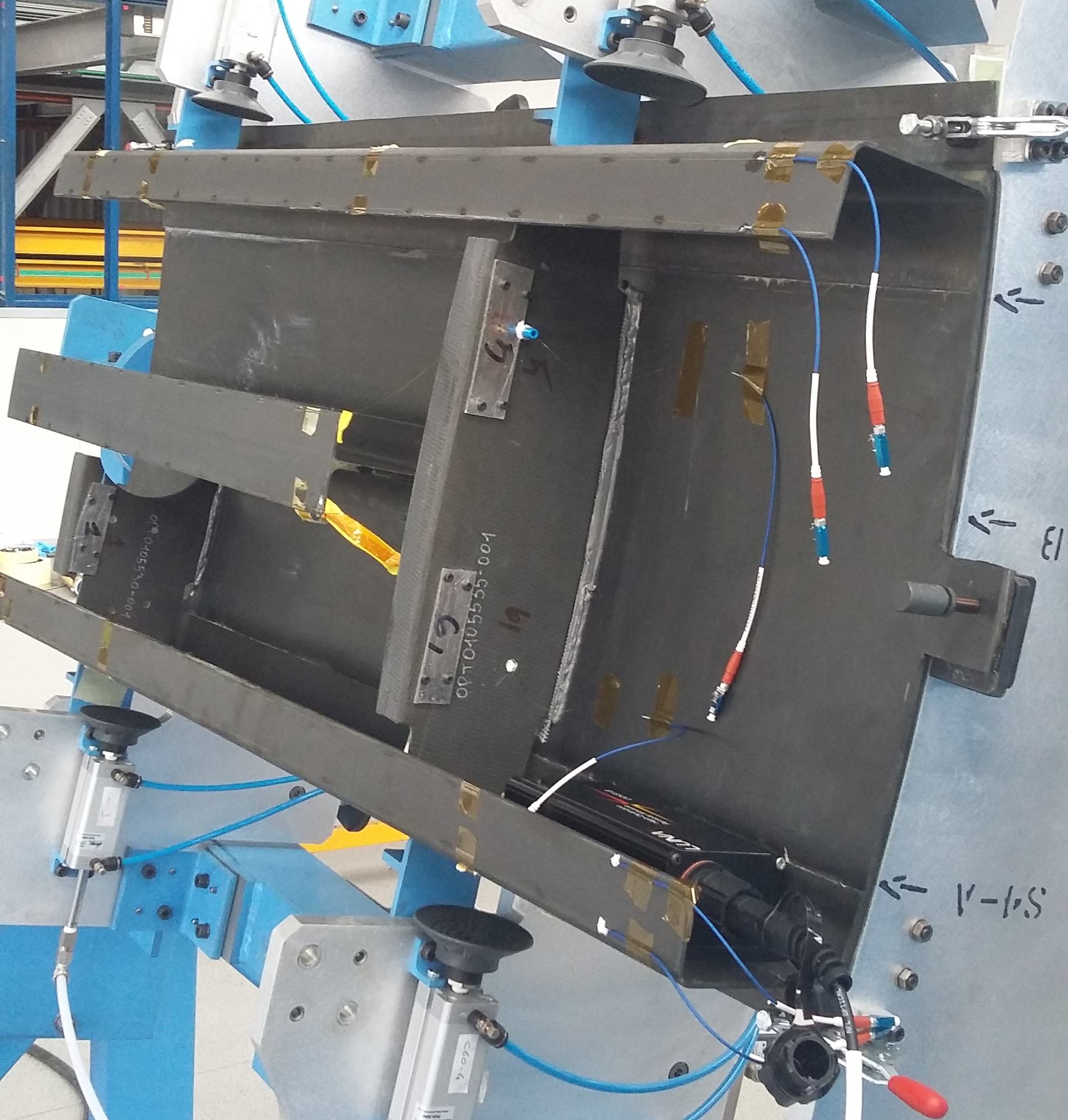
Pour lier la structure longeron/peau à la peau inférieure, le deuxième CFP a abouti à un autre projet OPTICOMS appelé WIBOND, pour développer un outil d'assemblage de liaison qui place l'adhésif, applique la pression appropriée et intègre des capteurs à fibre optique dans la ligne de liaison pour la santé structurelle suivi de la caution; CW rendra compte de cela et des autres technologies d'assemblage dans un article séparé qui sera publié en 2022.
Le troisième PCP a été lancé pour faire face au défi crucial des contraintes résiduelles qui provoquent un « ressort en place » de la structure longeron/peau. Ces déformations peuvent avoir des effets délétères sur le processus d'assemblage par collage. Le projet ELADINE a rejoint l'effort d'OPTICOMS pour développer un logiciel qui modélise et prédit l'anisotropie thermique, le retrait de polymérisation, l'interaction des pièces d'outils, l'écoulement et le compactage de la résine et les gradients de température à travers la structure.
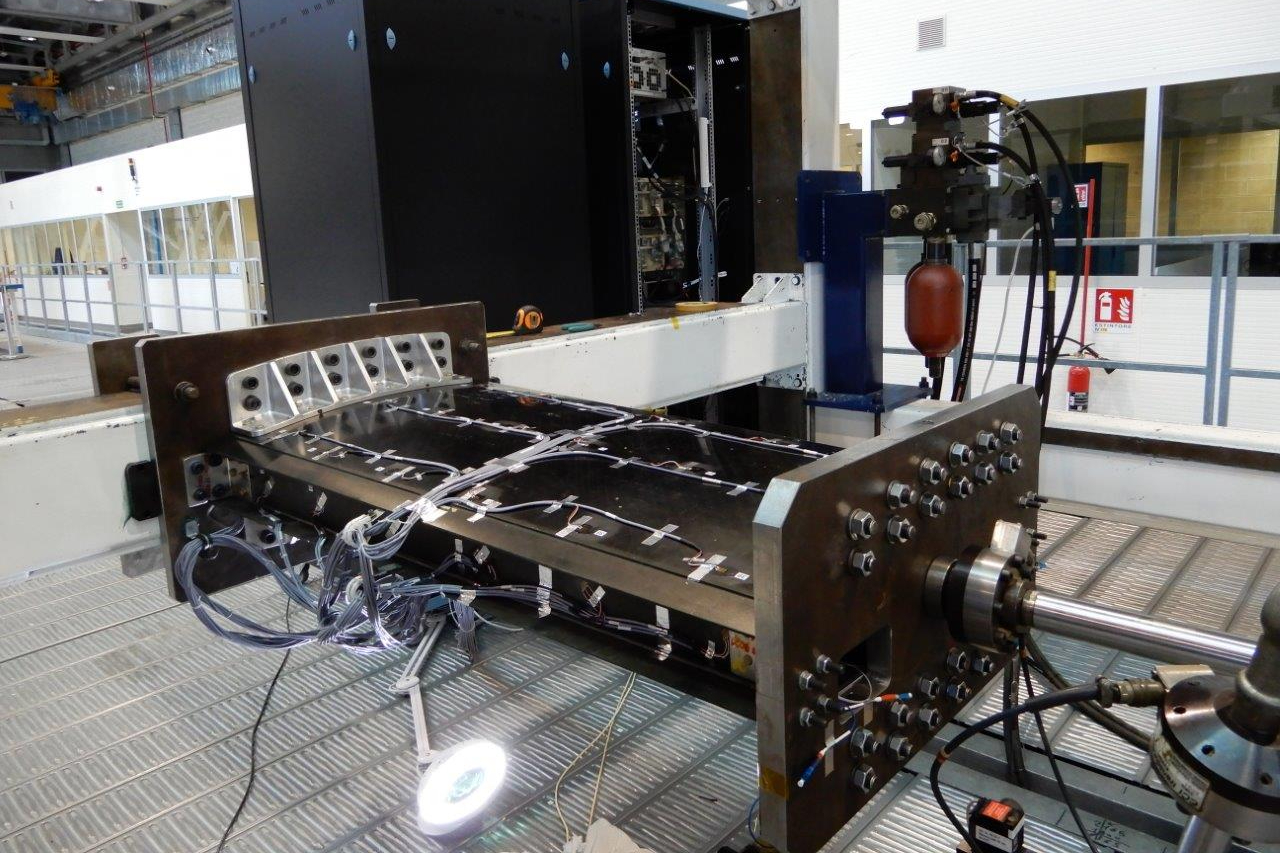
L'objectif principal d'IAI et d'OPTICOMS est de livrer d'ici le deuxième trimestre 2022 une aile de démonstration complète de 6,8 mètres à Piaggio pour des tests statiques et de fatigue. Ceci sera suivi d'une analyse des performances globales de l'aile et de la capacité de la conception, des matériaux et des processus à répondre aux critères du projet. Viendra ensuite une recommandation de Piaggio sur les prochaines étapes potentielles vers la commercialisation.
Au-delà de Piaggio, cependant, IAI espère que le caisson de voilure OPTICOMS pourrait trouver une application dans d'autres avions. "Bien que ce projet soit basé sur un avion spécifique", explique Sawday, "nous avons essayé de rendre la conception évolutive pour différentes épaisseurs et différentes tailles. Nous n'avons jamais perdu de vue le fait que cette technologie peut et doit être hautement adaptable. »
Résine
- Composites TPE ultra-légers pour chaussures
- Solvay composites sélectionnés pour catamaran de course
- Le collège communautaire ajoute de la flexibilité pour les étudiants avancés en fabrication de composites
- 4 erreurs courantes à éviter lors de la conception pour la fabrication
- Fabrication de PCB pour la 5G
- Répondre au grand besoin d'automatisation des composites
- Métaux pour la fabrication à grande diversité et à faible volume
- Qu'est-ce que la fabrication automatisée ?
- Évitez ces 4 erreurs courantes lors de la conception pour la fabrication