Fabrication de puces nanofluidiques en polydiméthylsiloxane par procédé de nanobroyage à pointe AFM
Résumé
Dans le domaine de la recherche actuelle, les dispositifs nanofluidiques à base de polydiméthylsiloxane (PDMS) sont largement utilisés dans les applications médicales, chimiques et biologiques. Dans le présent article, une nouvelle technique de nanobroyage (composée d'un système AFM et d'un actionneur piézoélectrique) a été proposée pour fabriquer des nanocanaux (avec des tailles contrôlables) sur des puces PDMS, et la taille des nanocanaux a été contrôlée par la tension et la fréquence d'entraînement entrées dans l'actionneur piézoélectrique. . De plus, des moules à microcanaux et nanocanaux ont été respectivement fabriqués par lithographie UV et nanofraisage à base de pointes AFM, et enfin, des dalles PDMS avec micro/nanocanaux ont été obtenues par processus de transfert. Les influences du rapport pondéral PDMS sur la taille des nanocanaux ont également été étudiées. Le processus de liaison des plaques de microcanaux et de nanocanaux a été mené sur un système d'alignement maison composé d'un microscope optique monoculaire et de platines de précision. De plus, les effets de la taille des nanocanaux sur les caractéristiques électriques de la solution de KCl (concentration de 1 µmM) ont été analysés. Par conséquent, on peut conclure que les dispositifs nanofluidiques PDMS avec plusieurs nanocanaux d'une profondeur inférieure à 100 nm peuvent être fabriqués de manière efficace et économique par la méthode proposée.
Contexte
En raison de leurs potentiels considérables dans les domaines chimiques, médicaux et biologiques, les systèmes micro/nanofluidiques sont largement utilisés dans l'analyse de l'ADN [1,2,3,4], la séparation cellulaire [5], la recherche sur les protéines [6,7,8], la sécurité alimentaire [9] et la surveillance environnementale [10]. Avec le développement rapide de la technologie de nanofabrication, la demande de dispositifs nanofluidiques avec une taille unidimensionnelle inférieure à 100 nm augmente continuellement [11]. Les puces nanofluidiques peuvent également être utilisées efficacement pour la détection de virus [12], la manipulation de nanoparticules [13] et l'étude de la diffusion d'ions [14]. Cependant, l'efficacité de détection et la sensibilité des puces nanofluidiques dépendent des dimensions et de la distribution des caractéristiques des nanocanaux. Il est indispensable de contrôler avec précision les dimensions des caractéristiques des nanocanaux pour une détection sans marqueur à base de nanofluidique. Comment fabriquer des nanocanaux avec des dimensions et une distribution de caractéristiques contrôlables est toujours un défi pour l'application dans le domaine nanofluidique.
Jusqu'à présent, il existe plusieurs méthodes qui peuvent être utilisées pour la fabrication de puces nanofluidiques. La gravure ionique réactive [15], la photolithographie conventionnelle [16], le traitement par faisceau à haute énergie [17], la lithographie interférentielle [18], la nanoimpression [19] et les technologies de gaufrage à chaud [20, 21] sont les plus couramment utilisées pour la fabrication de dispositifs nanofluidiques; cependant, toutes ces méthodes manifestent leurs propres limites. La gravure ionique réactive et la photolithographie conventionnelle sont les méthodes courantes pour la fabrication de canaux micro/nanofluidiques. Cependant, les dimensions latérales des canaux fabriqués dépendent de la longueur d'onde de la lumière incidente, ainsi les largeurs des canaux produits se trouvent souvent à l'échelle micrométrique, pas à l'échelle nanométrique [22]. En outre, il n'est pas pratique de changer les photomasques lorsque les micro/nanostructures fabriquées ont des caractéristiques différentes. La lithographie par faisceau d'ions focalisés (FIB) et la lithographie par faisceau d'électrons (EBL) sont toutes deux des méthodes de traitement de faisceau à haute énergie, qui peuvent facilement fabriquer une puce nanofluidique de haute précision avec des nanocanaux inférieurs à 100 nm. Cependant, l'investissement pour l'installation de fabrication est extrêmement élevé et l'exigence environnementale stricte est nécessaire [23]. La lithographie par interférence (IL) convient à la fabrication de structures périodiques simples sur une grande surface; cependant, il n'est pas adapté d'usiner un seul nanocanal [24, 25]. La résolution de traitement de la nanoimpression dépend des propriétés du modèle, le problème crucial pour cette approche est de savoir comment fabriquer le modèle avec des nanostructures de haute précision [26]. De plus, le moulage sacrificiel et la méthode basée sur le craquement sont également adoptés pour fabriquer des dispositifs à l'échelle micro/nano [27, 28] ; cependant, le contrôle précis de la taille des nanocanaux est très difficile dans ces approches. Ainsi, une approche de fabrication plus réalisable avec les propriétés de haute précision d'usinage, de facilité d'utilisation, de large plage de traitement et de faible exigence environnementale est exigée pour la fabrication d'un dispositif nanofluidique.
Ces dernières années, en raison de leurs hautes précisions d'usinage, les méthodes d'usinage d'ultra-précision, telles que le nanofraisage, le meulage de précision et le tournage d'ultra-précision, sont largement utilisées dans la fabrication de micro/nanostructures [29,30,31,32]. De plus, depuis l'invention du microscope à force atomique (AFM) en 1986, la nanofabrication à base de pointes AFM est une méthode puissante pour préparer des nanostructures [33]. Le nanograttage traditionnel basé sur la pointe possède certaines limites, telles qu'une largeur d'usinage limitée et une faible efficacité de fabrication. La largeur du nanocanal fabriqué par cette approche dépend de la géométrie de la pointe de l'AFM, ce qui signifie que les nanocanaux à largeur contrôlable sont inaccessibles. De plus, l'efficacité de fabrication du processus de nanograttage traditionnel à base de pointes est relativement faible, en particulier dans le cas de l'utilisation d'une alimentation dans le processus d'usinage pour agrandir la profondeur et la largeur de la nanostructure obtenue. En raison de ses avantages significatifs, tels que la taille d'usinage contrôlable et l'efficacité de fabrication élevée, le nano-fraisage à base de pointes est largement adopté pour fabriquer des nanocanaux. Gozen et al. [34, 35] ont fabriqué des nanostructures sur du polyméthacrylate de méthyle (PMMA) par un processus de nanobroyage. Zhang et al. [36,37,38] ont préparé des nanostructures tridimensionnelles en utilisant l'AFM et ont étudié les effets de différents paramètres d'usinage. Parc et al. [39] ont étudié le mécanisme du processus de nano-usinage et ont constaté que les intensités de la force de coupe étaient considérablement réduites; cependant, dans le système proposé, les installations d'usinage se sont avérées relativement compliquées et le processus d'enlèvement de matière n'a pas été étudié en détail. La relation entre les paramètres d'usinage, y compris la fréquence et la tension d'entraînement, et les dimensions des caractéristiques du nanocanal obtenu n'a pas été étudiée. De plus, leurs travaux ne se sont pas concentrés sur l'application des nanocanaux fabriqués. Par conséquent, des travaux supplémentaires sont nécessaires pour explorer le champ d'application de cette approche de nanofraisage basée sur la pointe AFM. Le polycarbonate (PC), en raison de son excellente usinabilité, est couramment utilisé pour la nanofabrication [40]; néanmoins, il est rarement sélectionné pour fabriquer des puces nanofluidiques. En revanche, le polydiméthylsiloxane (PDMS) est largement utilisé pour traiter les puces microfluidiques et nanofluidiques. Mata et al. [41] ont étudié les influences du rapport pondéral PDMS sur la contrainte de traction. Parc et al. [42] ont développé une nouvelle méthode pour améliorer la rigidité du PDMS. Les applications des puces nanofluidiques dans le domaine des tests sans étiquette dépendent principalement de la conductivité électrique des nanocanaux [43], ainsi les résultats de mesure sont souvent affectés par les tailles dimensionnelles des nanocanaux [44].
Par conséquent, afin de surmonter les inconvénients du processus de grattage traditionnel basé sur la pointe, l'approche de nano-fraisage est utilisée pour mener le processus de fabrication du nanocanal dans cette étude. De plus, la feuille de PC a été sélectionnée comme échantillon expérimental pour atténuer l'usure de la pointe ainsi que pour réduire les coûts de fabrication. En outre, la taille des nanocanaux sur la feuille de PC a été contrôlée par la tension et la fréquence d'entraînement entrées dans l'actionneur piézoélectrique. Les influences du rapport pondéral PDMS sur la taille des nanocanaux ont également été étudiées. De plus, afin de vérifier les effets de différentes tailles dimensionnelles sur la conductivité électrique des nanocanaux, le test de mesure de courant a été réalisé à l'aide d'une solution de KCl.
Méthodes
Configuration du système de nano-fraisage
Le système de nanobroyage à pointe AFM proposé consistait en un AFM commercial (Dimension Icon, Bruker Company, Allemagne) et un actionneur piézoélectrique (P-122.01, PI Company, Allemagne) (Fig. 1a). Les plages de déplacement de l'actionneur piézoélectrique dans les deux directions x et y étaient limitées à 1 m. De plus, l'actionneur piézoélectrique était entraîné par des signaux sinusoïdaux avec des tensions appropriées (générés à partir d'un dispositif générateur de signaux commercial (AFG1022 ; Tektronix, Inc., États-Unis)) sous l'amplification d'un amplificateur de signal (PZD350A ; TREK, Inc., États-Unis). Une feuille de PC a été fixée sur le support fait maison (en résine époxy) par une vis de fixation. L'opération de nano-usinage a été réalisée à l'aide d'une pointe pyramidale diamantée rectangulaire d'épaisseur 100µnm (DT-NCLR, Nanosensors, Suisse). Le cantilever de la pointe (constante d'élasticité normale de 68 N/m) était en silicium (Fig. 1b), et une pointe en silicium (rayon de 10 nm) (TESPA, Bruker Company, Allemagne) a été utilisée pour mesurer les rainures après usinage.
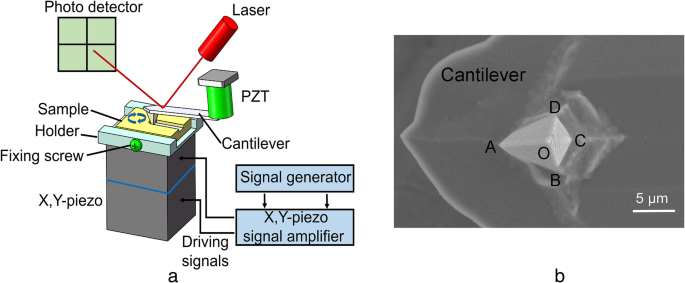
un Schéma de principe du système de nanobroyage. b Micrographie SEM de la pointe AFM diamantée
Fabrication de moules nanocanaux et microcanaux
La voie de fabrication des nanocanaux sur une puce PDMS est illustrée à la Fig. 2. Le système AFM et l'actionneur piézoélectrique ont été utilisés pour fabriquer des moules à nanocanaux (avec des tailles contrôlables) sur une feuille de PC. La feuille de PC (poids moléculaire de 35 000) d'une taille de 15 mm × 12 mm × 1 mm a été achetée auprès de Goodfellow. La moyenne et l'écart type de la rugosité de surface (Ra) de la feuille de PC ont été mesurés à 0,6 nm et 0,2 nm, respectivement (ces valeurs ont été obtenues en balayant une zone de 50 μm × 50 m de l'échantillon en mode de taraudage AFM). Afin de générer un mouvement circulaire, l'actionneur piézoélectrique était piloté par des signaux sinusoïdaux avec une différence de phase de 90° dans les directions x et y. Les largeurs des nanocanaux usinés dépendaient de l'amplitude du mouvement circulaire généré. La plage de la tension d'entraînement entrée à l'actionneur piézoélectrique a été réglée de 30 V à 150 V avec un espacement de 30 V, et en plus, deux fréquences de plongée de 100 Hz et 1500 Hz ont été sélectionnées. Lors de l'usinage le long de la direction bord avant, les matériaux sont expulsés en formation d'empilement et s'avèrent souvent être uniformément répartis des deux côtés d'un nanocanal [45], et cela aide à éviter toute fuite de puces nanofluidiques pendant le processus de liaison ; par conséquent, la direction d'usinage bord avant a été sélectionnée dans la présente étude. Des nanocanaux de 80 µm de longueur ont été fabriqués à l'aide du module Nanoman du système AFM. Tout processus d'usinage est affecté par la valeur de l'avance ; par conséquent, afin d'éliminer cette influence, la vitesse d'avance doit être modifiée avec la fréquence d'entraînement. Dans la présente étude, la valeur d'alimentation a été fixée à 10 nm, et les taux d'alimentation pour les fréquences 100 Hz et 1500 Hz ont été calculés comme 1 μm/s et 15 μm/s, respectivement. La charge normale de la pointe dépendait de la tension de sortie générée par le photodétecteur sensible à la position (PSD) ; ainsi, différentes charges normales utilisées dans notre étude ont été obtenues en fixant une tension relative (point de consigne). Selon nos travaux antérieurs [46], la charge normale d'usinage a été calculée par l'équation. (1) et la sensibilité a été mesurée à partir de la pente de la courbe force-distance obtenue [47].
$$ {F}_{\mathrm{N}}={V}_{\mathrm{setpoint}}\times sensibilité\times {K}_{\mathrm{N}} $$ (1)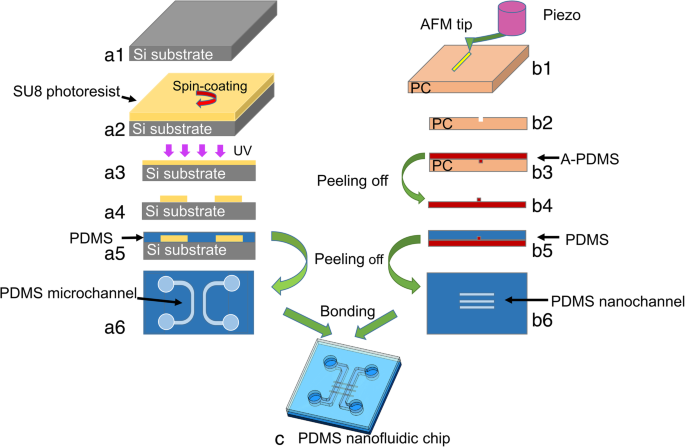
Organigramme de la fabrication de puces nanofluidiques :(a1)–(a6) Étapes de travail de la fabrication de microcanaux sur une puce PDMS ; (a1) Feuille de silicium utilisée pour le substrat de lithographie ; (a2) Revêtement par centrifugation de résine photosensible SU8 sur substrat Si ; (a3) Exposition de la couche SU8 à la lumière UV ; (a4) Obtention de microstructures convexes ; (a5) revêtement PDMS sur moule à microcanaux ; (a6) Puce PDMS finale avec microcanaux ; (b1)–(b2) Étapes de travail de la fabrication de nanocanaux sur une puce PDMS ; (b1) rayures de la pointe de l'AFM sur la feuille PC ; (b2) Moule à nanocanaux obtenu après grattage ; (b3) Revêtement A-PDMS sur moule à nanocanaux ; (b4) puce A-PDMS avec des nanostructures convexes ; (b5) Revêtement PDMS régulier sur le moule A-PDMS ; (b6) Puce PDMS finale avec nanocanaux ; (c) Puce nanofluidique PDMS après collage
Par conséquent, les charges normales pour le processus de nanobroyage ont été fixées à 17 N et 25 μN. De plus, à titre de comparaison, des moules à nanocanaux sur une feuille de PC ont également été fabriqués sans vibration, cette méthode est appelée grattage simple. Les charges normales pour le processus de grattage unique ont été fixées à 25 μN, 33 μN, 42 μN, 50 μN et 58 μN. Le diagramme schématique de la section transversale du moule à nanocanaux est affiché sur la figure 2 (b2).
Des moules à microcanaux ont été préparés par un procédé de lithographie UV. L'organigramme de la figure 2(a1–a4) décrit les détails de fonctionnement du processus de lithographie. La résine photosensible (SU-82015; MicroChem, USA) a été déposée par centrifugation sur substrat Si à 500 rps pendant 30 s et à 4000 rps pendant 120 s. Une paire de microcanaux en forme de « U » a formé la puce à microcanaux (Fig. 2(a6)), qui a été pontée par des nanocanaux pour former la puce nanofluidique finale. La largeur du microcanal était de 30 μm et le diamètre du réservoir était de 1 mm. De plus, la distance entre deux microcanaux en « U » était de 50 µm (Fichier complémentaire 1 :Figures S1 et S2).
Impression par transfert de microcanaux et nanocanaux
Le moule à microcanaux convexes (Fig. 2(a4)) et le moule à nanocanaux concave (Fig. 2(b2)) ont été transférés par PDMS (Sylgard 184, Dow Corining, USA) pour préparer la puce nanofluidique finale. La figure 2 (b3)–(b6) présente le processus technologique de transfert de moule par nanocanaux, qui consistait en deux étapes :le premier transfert et le deuxième transfert. Pour étudier les effets du rapport pondéral du monomère à l'agent de durcissement sur la taille des nanocanaux, trois rapports pondéraux différents de PDMS (A-PDMS) ont été utilisés au cours du premier et du deuxième processus de transfert. Les rapports pondéraux PDMS pour le premier processus d'impression par transfert ont été définis sur 9:1, 7:1 et 5:1, tandis que les valeurs pour le deuxième transfert ont été définies sur 10:1, 9:1 et 8:1. La figure 2 (a5) et (a6) affiche le processus de transfert du moule à microcanaux à l'aide d'une approche de transfert en une étape. Le rapport pondéral PDMS de 10:1 a été utilisé pour le transfert du microcanal convexe. Pendant tous les processus d'impression par transfert, un élastomère PDMS à deux composants a d'abord été uniformément agité, puis versé dans un boîtier pour préparer le moule. Le boîtier a ensuite été conservé dans un dessiccateur sous vide pendant 30 min et dégazé 2 à 3 fois pour éliminer toutes les bulles d'air piégées. Le moule préparé a été conservé dans un four chauffant à 80 °C pendant 4 h, et enfin, la réplique en PDMS a été délicatement décollée du moule.
Chip bonding
Les puces nanofluidiques préparées ont été liées par traitement oxygène-plasma (Zepto, Diener electronic, Allemagne) pendant une durée de 32 s sous une pression de chambre de 1,5 mbar et une puissance de chambre de 81 W (Fig. 2(c)). Les surfaces des microcanaux et des nanocanaux ont été nettoyées à l'aide de rubans adhésifs et les quatre réservoirs des puces à microcanaux en PDMS ont été perforés avant le collage. De l'eau déminéralisée a été utilisée pour garder les puces propres après le traitement au plasma, et les puces ont été maintenues alignées ensemble à l'aide d'un système d'alignement maison composé d'un support, d'un microscope monoculaire et d'une platine de précision unidimensionnelle (TSDT-401S ; SIGMAKOKI, Japon ) (Fig. 3a). Les détails du système d'alignement fait maison peuvent être trouvés dans l'ESI. Les puces ont ensuite été collées à une température de 95 °C pendant 20 min afin d'obtenir une puce micro/nanocanal fermée (Fig. 3b).
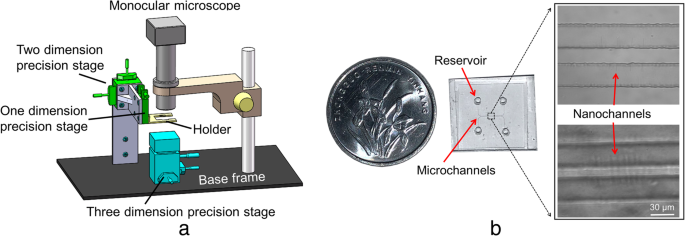
un Schéma de principe du système d'alignement maison et b puce nanofluidique
Résultats et discussion
Trajectoire rotative de l'actionneur piézoélectrique
L'actionneur piézoélectrique bidimensionnel est un composant essentiel pour effectuer un mouvement rotatif dans un système de nanofraisage à pointe AFM. Par conséquent, pour caractériser ses mouvements sous une gamme de tensions et de fréquences d'entraînement, des tests de grattage préliminaires ont été effectués. Sous le modèle de contact avec une plage de balayage de 0 nm, la pointe de l'AFM s'est d'abord approchée de la surface de la feuille de PC sous une charge normale donnée et est restée statique. La rotation de l'actionneur piézoélectrique bidimensionnel était contrôlée par une fréquence et une tension prédéfinies. Une fois le processus de grattage terminé, la pointe de l'AFM a été soulevée de la surface de la feuille de PC. Ainsi, l'amplitude de mouvement de l'actionneur piézoélectrique a été obtenue en fonction de la tension et de la fréquence d'entraînement. Les tensions d'entraînement ont été réglées dans la plage de 30 à 150 V avec un espacement de 30 V, tandis que les fréquences d'entraînement ont été réglées à 100 Hz et 1 500 Hz. La relation entre les amplitudes mesurées et les tensions de commande à deux fréquences de commande est affichée dans le fichier supplémentaire 1 :Figure S3. Il est évident que les valeurs d'amplitude d'usinage augmentaient avec l'augmentation des tensions d'entraînement, et la valeur de l'amplitude d'usinage à 1500 Hz était supérieure à celle de 100 Hz. Il a été constaté que les largeurs du nanocanal fabriqué par notre méthode proposée allaient de 350 nm à 690 nm.
Fabrication de moules nanocanaux sur feuille PC
Les relations entre la taille des nanocanaux et les paramètres d'usinage sous une seule rayure et nano-fraisage sont présentées sur les figures 4a et b, respectivement. Les largeurs et les profondeurs des nanocanaux usinés sont représentées par W 0 et D 0 , respectivement (Fig. 5a).
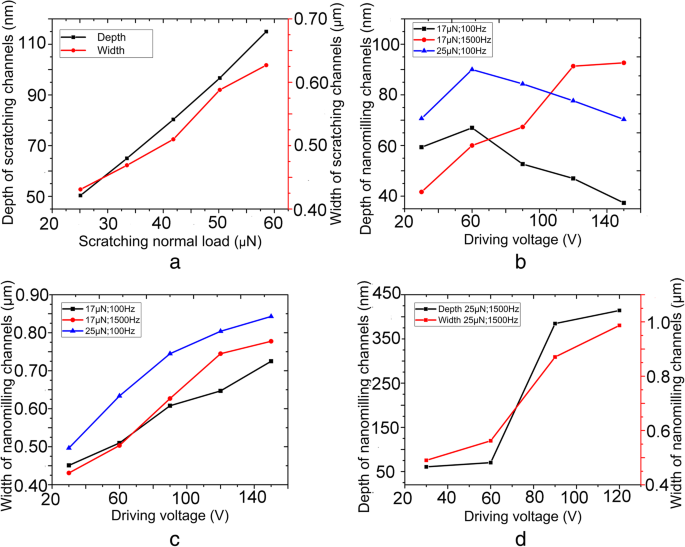
Relation entre la taille des nanocanaux usinés et les paramètres d'usinage :a les rayures simples avec des charges normales vont de 25 μN à 58 μN, b profondeur, et c largeur des canaux usinés lorsqu'ils sont fabriqués avec des charges normales de 17 μN, 25 μN et des fréquences d'entraînement de 100 Hz, 150 Hz, d la profondeur et la largeur des canaux usinés lorsqu'ils sont fabriqués avec une charge normale de 25 μN et une fréquence d'entraînement de 1500 Hz
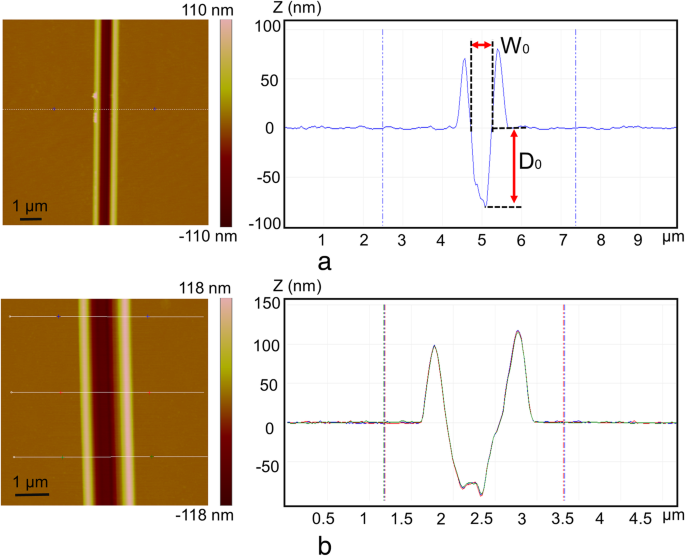
Images AFM typiques du nanocanal usiné avec différents paramètres d'usinage :a Grattage sous une charge normale de 42 μN. b Nanobroyage sous une charge normale de 25 N, une fréquence de 100 Hz et une tension d'entraînement de 60 V
Il est observable à partir de la figure 4a que les largeurs et les profondeurs des nanocanaux fabriqués augmentaient avec l'augmentation des charges normales. L'image AFM typique de grattage sous une charge normale de 42 μN est présentée sur la figure 5a. Il est à noter que des matériaux ont été expulsés du nanocanal pour former des empilements, qui étaient uniformément répartis des deux côtés du nanocanal. Parce que la forme de la pointe de l'AFM est symétrique à la surface qui a été formée par le bord « OA » pendant le processus d'usinage (Fig. 1b). Ainsi, les matériaux ont été expulsés uniformément par le bord avant de la pointe pendant le grattage du bord avant. Les figures 4b, c et d illustrent la relation entre la taille des nanocanaux usinés et la tension de commande. Il est évident à partir de la figure 4b que la profondeur du nanocanal a augmenté au début puis a commencé à diminuer sous une fréquence de 100 Hz avec des charges normales de 17 N et 25 μN. La feuille de PC utilisée dans notre étude était un polymère amorphe, qui présente un comportement élastique-viscoplastique en combinaison d'un écrouissage exponentiel à des niveaux de déformation élevés [48, 49]. La charge normale pendant l'usinage a été calculée par l'équation. (2), où \( \overrightarrow{n} \) et \( \overrightarrow{t} \) sont l'unité normale et l'unité tangente au vecteur de la ligne d'écoulement, respectivement, p et τ signifie la pression normale locale et la contrainte de cisaillement, respectivement, et \( \overrightarrow{z} \) est l'unité verticale [50].
$$ {F}_{\mathrm{N}}=p\cdot \int \overrightarrow{n}\cdot \overrightarrow{z} ds-\tau \cdot \int \overrightarrow{t}\cdot \overrightarrow{zds } $$ (2)Dans la présente étude, les tailles dimensionnelles des nanocanaux fabriqués ont été trouvées à l'échelle nanométrique, ainsi les valeurs de la pression normale locale et de la contrainte de cisaillement ont été supposées constantes. De plus, l'Éq. (2) a été converti en la forme simplifiée de l'équation. (3), où S n et S h sont respectivement les projections horizontales et verticales de l'interface entre la pointe AFM et l'échantillon.
$$ {F}_{\mathrm{N}}=p\cdot {S}_n-\tau \cdot {S}_h $$ (3)La relation entre S n et S h est exprimé dans l'équation. (4), où α et β sont respectivement les angles inclus entre la surface de la pointe et les plans vertical et horizontal.
$$ {S}_{\mathrm{n}}=\frac{S_{\mathrm{h}}}{\cos \alpha}\cdot \cos \beta $$ (4)La charge normale a été calculée par l'équation. (5).
$$ {F}_{\mathrm{N}}=\left(p\cdot \frac{\cos \beta }{\cos \alpha }-\tau \right)\cdot {S}_h $$ (5 )Il est évident d'après l'Éq. (1) que les valeurs de la charge normale étaient constantes pendant tout le processus d'usinage. Selon Briscoe et al. [51], la valeur de la vitesse de déformation moyenne a été calculée par l'Eq. (6), où V et w signifient respectivement la vitesse de la pointe et l'épaisseur des copeaux non coupés. La valeur maximale de l'épaisseur des copeaux non coupés a été trouvée comme ~ 10 nm.
$$ {}_{\varepsilon}^{\bullet }=\frac{\mathrm{d}\varepsilon }{\mathrm{d}t}\approx \frac{V}{w} $$ (6)De plus, les valeurs de vitesse de pointe ont été obtenues à partir de l'Eq. (7), où f est la fréquence du signal d'entrée.
$$ V=\pi \cdot {W}_o\cdot f $$ (7)Les valeurs du taux de déformation moyen à 100 Hz ont été trouvées dans la plage de 1,42 × 10 4 s -1 ~ 2,27 × 10 4 s -1 . Les valeurs de pression normale locale (p ) a commencé à augmenter avec l'augmentation des taux de déformation lorsque les taux de déformation variaient de 1,42 × 10 4 s -1 à 2,27 × 10 4 s -1 [52]. La valeur de τ était beaucoup plus petite que celle de p , cela signifie que la charge normale dépendait principalement de p . Par conséquent, afin de conserver les valeurs de charge normale (FN ) constante pendant tout le processus d'usinage, les valeurs de profondeur d'usinage doivent être plus petites à des tensions d'entraînement plus élevées. Cependant, la taille dimensionnelle finale du nanocanal fabriqué a été affectée par la récupération du matériau de l'échantillon. La récupération de l'échantillon diminuait avec l'augmentation des vitesses d'usinage dans la plage de 142 ~ 227 m/s [53] :ainsi, cela indique qu'une récupération élastique plus élevée s'est produite à 30 V. Par conséquent, la profondeur du nanocanal fabriqué à 30 V (~142 μm/s) était moins profonde que celle de 60 V (~161 μm/s). Fichier supplémentaire 1 :La figure S4 (a) et la figure 5b sont les images AFM typiques du nanocanal usiné à 100 Hz sous des charges normales de 17 N et 25 N, respectivement. Il est évident que l'empilement du côté droit du nanocanal est plus grand que le gauche. Le mouvement de rotation de l'échantillon pendant le processus de nanobroyage est dans le sens inverse des aiguilles d'une montre et l'angle de coupe de l'arête de coupe principale change avec la rotation. L'épaisseur des copeaux non coupés est trop petite pour former des copeaux au début et à la fin d'un cycle de processus de nanofraisage. L'épaisseur des copeaux non coupés au milieu d'un cycle de processus de nano-fraisage est relativement importante; cependant, le petit angle d'attaque contribue à la formation des carambolages. Ainsi, plus de matériaux sont poussés vers le côté droit du canal, et les empilements sont donc asymétriques. Les détails de la formation des empilements asymétriques peuvent être trouvés dans notre étude précédente [54].
Il est observable à partir des figures 4b et d que la profondeur du nanocanal a commencé à augmenter avec l'augmentation des tensions de commande à 1500 Hz sous des charges normales de 17 μN et 25 μN. La figure 4d montre que la profondeur des nanocanaux a fortement augmenté de 60 V (~ 2,64 mm/s) à 90 V (~ 4,10 mm/s) sous une charge normale de 25 μN. Selon Geng et al. [55], l'état d'enlèvement de matière est significativement affecté par la vitesse de coupe. Les matériaux ont été expulsés du nanocanal sous forme d'empilement pendant l'usinage à une vitesse de 2,64 mm/s, tandis que l'état d'enlèvement de matière est passé d'empilement à puce à 4,10 mm/s (Fichier supplémentaire 1 :Figure S4 (b)) . Par conséquent, l'augmentation de la profondeur d'usinage à 90 V (~4,10 mm/s) peut être attribuée au changement d'état d'enlèvement de matière. La largeur du nanocanal fabriqué a commencé à augmenter avec l'augmentation des tensions de commande. La figure 6 affiche le diagramme schématique de la trajectoire de la pointe AFM pendant le nanofraisage, les ellipses en pointillés, les ellipses noires pleines et les flèches bleues représentent respectivement le processus d'usinage fini, le processus d'usinage en cours et la direction du mouvement de la pointe AFM. La largeur (W 2 ) du canal usiné de la figure 6(b) était plus grand que celui (W 1 ) sur la figure 6(a). AS1 et AS2 (lignes rouges pleines) représentent la longueur de contact entre la section transversale de la pointe de l'AFM et le matériau de l'échantillon. La valeur de AS1 s'est avéré supérieur à celui de AS2 lorsque la largeur d'usinage "L 1 " était égal à " L 2. ”
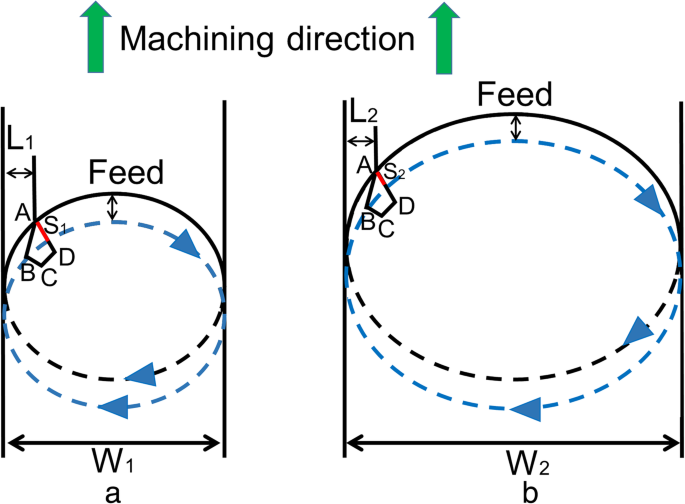
Représentation schématique de la trajectoire de la pointe de l'AFM pendant le processus de nanofraisage :la largeur usinée du nanocanal (a ) est plus petit que le nanocanal (b ), et les ellipses en pointillés, les ellipses noires pleines et les flèches bleues représentent respectivement le processus d'usinage terminé, le processus d'usinage en cours et la direction du mouvement de la pointe AFM
La valeur de Sh dans l'éq. (5) a été obtenu par l'équation. (8), où D et AS sont respectivement la profondeur du canal usiné et la longueur de contact entre la section transversale de la pointe AFM et le matériau de l'échantillon.
$$ {S}_h=\frac{1}{2}\cdot \left|D\left|\cdot \right|\; AS\droit| $$ (8)Par conséquent, l'éq. (5) a en outre été réécrit sous la forme de l'équation. (9).
$$ {F}_{\mathrm{N}}=\frac{1}{2}\cdot \left(p\cdot \frac{\cos \beta }{\cos \alpha }-\tau \right) \cdot \left|D\left|\cdot \right| AS\droit| $$ (9)Les valeurs de α et β ont été maintenus constants pendant tout le processus d'usinage. Les valeurs de taux de déformation à 1500 Hz ont été trouvées dans la plage de 2,03 × 10 5 ~3,66 × 10 5 s -1 ; par conséquent, on peut supposer que la pression normale locale (p ) a atteint sa valeur limite à 1500 Hz. De plus, la vitesse d'usinage n'a manifesté aucun effet sur la récupération de l'échantillon lors de l'usinage à 30–150 V (~ 2,03–3,66 mm/s) [53]; ainsi, les tailles dimensionnelles finales du nanocanal n'ont été déterminées que par les dimensions d'usinage. Les valeurs de AS2 (Fig. 6(b)) se sont avérés plus petits que ceux de AS1 (Fig. 6(a)) pour les plus grandes largeurs usinées, et selon l'Eq. (9), la valeur de D était plus grande pour une plus petite valeur de AS. Par conséquent, les valeurs de profondeur d'usinage augmentaient avec l'augmentation des tensions d'entraînement. Une image AFM typique du nanocanal fabriqué sous une charge normale de 25 μN, une tension de commande de 120 V et une fréquence de 1500 Hz est présentée dans le fichier supplémentaire 1 :Figure S4 (b). Il est à noter que les matériaux ont été retirés à la fois lors de la formation de puces et d'empilements, et que les matériaux expulsés ne se sont accumulés que d'un côté du nanocanal. De plus, les matériaux expulsés se sont accumulés dans la formation de copeaux au fond du nanocanal pendant l'usinage à 150 V sous une charge normale de 25 μN. Par conséquent, les données de taille du nanocanal fabriqué pendant l'usinage à une tension de 150 V et une fréquence de 1500 Hz (sous une charge normale de 25 μN) étaient vides sur la figure 4d.
Il est évident à partir de la figure 4c que la largeur des nanocanaux a commencé à augmenter avec l'augmentation des tensions de commande. De plus, lorsque les valeurs de charge normale et de tension de commande étaient maintenues constantes, la largeur du nanocanal fabriqué à une fréquence de 1500 Hz était plus large que celle de 100 Hz. De plus, la profondeur d'usinage du nanocanal fabriqué à 1500 Hz était plus profonde que celle de 100 Hz, et la taille de la section transversale de la pointe s'est avérée plus grande lors de l'usinage d'un nanocanal plus profond. Par conséquent, les nanocanaux ont été fabriqués plus larges lors de l'usinage plus profond.
Premier transfert de moules nanocanaux
Des nanocanaux usinés par une méthode de grattage unique sous des charges normales de 25 μN, 33 μN, 41 μN, 50 μN et 58 μN ont été appliqués au premier processus de transfert. De plus, des moules à nanocanaux fabriqués par nanobroyage à une fréquence de 100 Hz dans la plage de tension de commande de 30 à 150 V (avec un espacement de 30 V) ont également été utilisés dans le processus de transfert. Les nanocanaux (profondeur 80 nm et largeur 510 nm) usinés par la méthode de grattage simple ont été appelés « nanocanal I », tandis que les nanocanaux (profondeur 50 nm et largeur 610 nm, profondeur 90 nm et largeur 630 nm) fabriqués par nanobroyage étaient appelés «nanocanal II » et « nanocanal III », respectivement. Trois ratios de poids PDMS différents (5:1, 7:1 et 9:1) ont été utilisés dans le premier processus de transfert.
Les figures 7a et b révèlent les effets de différents rapports de poids PDMS sur la taille de la paroi sous une charge normale de 25 μN et une fréquence de 100 Hz, et la ligne en tirets noirs représente la taille originale du nanocanal avant le transfert. L'image AFM typique et la coupe transversale correspondante de la paroi obtenue à partir du nanocanal III à un rapport pondéral de 5:1 lors du premier transfert sont affichées sur les figures 7c et d, et cette paroi a été appelée « paroi III ». Les effets de différents rapports de poids PDMS sur la taille du mur sous un seul processus de grattage avec une charge normale de 17 N et une fréquence de 100 Hz ont été montrés dans ESI (voir Fichier supplémentaire 1 :Figures. S5, S6, S7 et S8 d'ESI pour les détails). Les parois obtenues à partir de « nanocanal I » et « nanocanal II » ont été appelées respectivement « paroi I » et « paroi II ». Il est évident que les hauteurs de tous les murs à différents rapports de poids de PDMS étaient approximativement les mêmes. The widths of the walls were larger than the original nanochannel width, and the width at the weight ratio of 5:1 was found to be the largest. Due to the thermal expansion of PC sheet, a small deviation was noticed between final wall size and original nanochannel size. It was also observed that the elasticity of PDMS increased as the PDMS weight ratio decreased from 5:1 to 7:1 [41, 42]. Hence, the wall obtained at the weight ratio of 5:1 was stiffer and its elastic recovery was smaller; thus, the width of the wall obtained at the weight ratio of 5:1 was the largest.
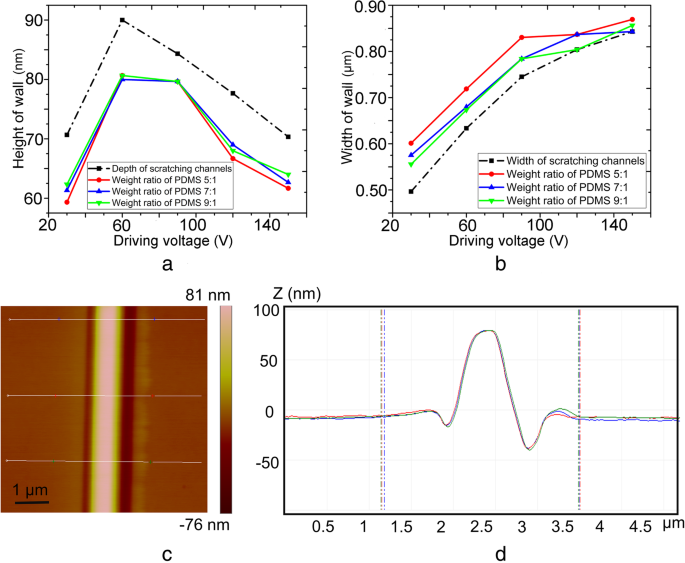
Relationship between a wall height, b wall width, and transfer parameters (various weight ratio of PDMS) during first transfer process, where the channel molds were fabricated with a normal load of 25 μN and a frequency of 100 Hz, and c typical AFM image and d corresponding cross-section of the wall obtained from nanochannel III at a weight ratio of 5:1
Second transfer of nanochannel molds
The final PDMS slabs with nanochannels were obtained during second transfer process based on the wall obtained at a weight ratio of 5:1 in the first transfer process. Three different PDMS weight ratios (10:1, 9:1, and 8:1) were used during second transfer process. Figure 8a and b present the relationship between nanochannel size obtained under a normal load of 25 μN and a frequency of 100 Hz and transfer parameters during second transfer. It is clear from Fig. 8a that the depths of the nanochannels were larger than the original machining size, moreover, the depth at 10:1 was found to be larger than other two ratios. Further, the widths of the wall were also larger than the original size, and the width at 10:1 was found to be the largest (Fig. 8b). Figure 8c and d present a typical AFM image and corresponding cross-section of the nanochannel (120 nm depth and 690 nm width) obtained from wall III at a weight ratio of 10:1 during second transfer, and it was termed as “nanochannel C.” The relationship between the nanochannel sizes obtained under single scratching process with a normal load of 25 μN and a frequency of 100 Hz and the transfer parameters during the second transfer process were shown in ESI (see Additional file 1:Figures. S9, S10, S11 and S12 of ESI for details), the nanochannels obtained from “wall I” and “wall II” were termed as “nanochannel A” and “nanochannel B”, respectively.
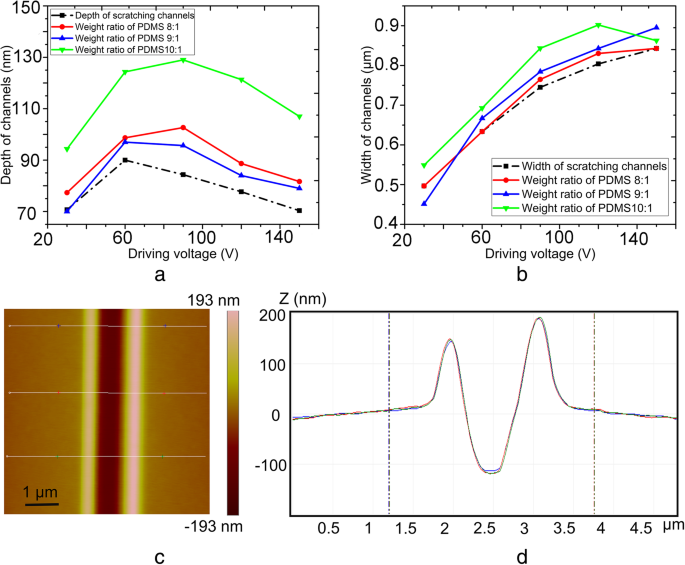
Relationship between a nanochannel height, b nanochannel width, and transfer parameters (various weight ratio of PDMS) during second transfer, where the channel molds were fabricated with a normal load of 25 μN and a frequency of 100 Hz, and c typical AFM image and d corresponding cross-section of the nanochannel obtained from wall III at a weight ratio of 10:1 during second transfer
The depths of nanochannels obtained from walls II and III were larger than the original machining size, whereas the depth obtained from wall I was smaller than the initial machining size. Furthermore, the changes in width were identical to the changes in depth. The aspect ratio of wall I was larger than those of walls II and III, thus each wall manifested different thermal expansion values. Hence, the changing trends of width and depth during second transfer were different though at the same PDMS weight ratio. The values of the depth and width of walls II and III at 9:1 and 8:1 were found to be closer to the original machining size compared with 10:1. Because the elastic recoveries of PDMS at 9:1and 8:1 are closer to 5:1 than 10:1, which indicates an almost similar recovery trend for PDMS at 9:1, 8:1, and 5:1.
Application of nanochannel devices in electric current measurement
Nanochannel devices are often used in the fields of single nanoparticle manipulation, electrokinetic transport phenomena, DNA analysis, and enzymatic reaction detection. The main working principle of nanofluidic chips depends on the variation in electric current; therefore, it is important to measure the electrical conductivities of nanochannel devices. The electrical conductance in a nanochannel can be estimated by Eq. (10) [56].
$$ G={10}^3N\;{}_Ae\frac{wh}{l}\sum {\mu}_i{c}_i+2{\mu}_e\frac{w}{l}{\delta}_n $$ (10)où μ i is the mobility of ion i , c i is the concentration of ion i , δ n is the effective surface charge inside the nanochannel, and NA and e signify Avogadro constant and electron charge, besides, w , h et l are the nanochannel width, height and length, respectively. It is obvious that the electrical conductance of a nanochannel is affected by the nanochannel feature dimensions and the solution concentration. The electric double layer (EDL) plays an important role in the nanochannel when the ratio of DEL thickness to the nanochannel height increases. The diffuse layer thickness of EDL is 3~5 times of the Debye length (λ D ), which can be expressed by Eq. (11) [57].
$$ {\lambda}_D=\sqrt{\frac{\varepsilon_0{\varepsilon}_r{k}_bT}{2{n}_{i\infty }{(ze)}^2}} $$ (11)où n i ∞ denotes ion density in the solution, ε o is the permittivity of vacuum, ε r is the dielectric constant of electrolyte solution, z is the valency of buffer solution (z = z + − z − = 1 for KCl), and kb et T are the Boltzmann constant and temperature, respectively. In the present study, three different nanofluidic chips were obtained after the completion of transfer process. Nanofluidic chips consisted of nanochannels A, B, and C were termed as nanofluidic chips A, B, and C, respectively. Each nanofluidic chip contained four nanochannels. The widths and the depths of nanofluidic chips A, B, and C were measured as 60 nm and 500 nm, 80 nm and 680 nm, and 120 nm and 690 nm, respectively. The effective length of nanochannels in all chips was calculated as 50 μm. As shown in Fig. 8, pile-ups distribute on the sides of the nanochannels A, B, and C. The pile-ups may fill into the nanochannels and lead to a failure of the preparation for the nanofluidic chips. Thus, in order to verify the reliability of the fabricated nanochannel devices, electrical conductivity measurement test was conducted. KCl with 1 mM concentration was as the electrolyte solution in our study, and the values of electrical current were measured by an electrometer (Model 6430, Keithley, USA). The schematic sketches of the measurements for electric current in microchannel and nanochannel are presented as the inset figures in Fig. 9a and b, respectively. The experiments were carried out under DC power (applied by an Ag electrode) with an increment of 2 V for 3-s duration. Figure 9a presents the measured I -V curves of microchannels in three different nanofluidic chips, and a linear relationship between current and voltage was observed. Moreover, as the effect of EDL in microchannels was negligible and the dimensional sizes of microchannels in different nanofluidic devices were identical, the values of current in different chips were nearly the same. It is evident from Fig. 9b that the values of current in different nanofluidic devices were distinct due to different nanochannel sizes. For KCl solution of 1 mM concentration, the value of λ D was about 10 nm, thus the diffuse layer thickness of EDL was found as 30~50 nm [57]. Consequently, EDL got overlapped along the depth (60 nm) of nanofluidic chip A; however, no overlapping was observed in nanofluidic chip C (depth of 120 nm). However, it was difficult to determine whether EDL got overlapped or not in nanofluidic chip B (depth of 80 nm). It assumes that the effective surface charges (δ n ) in all nanochannels are identical as the charge density of a surface is material property [58, 59]. The concentration of the ions in a nanochannel depends on the EDL field, the stronger the EDL field, the higher the ion concentration in the nanochanel [44]. In the present study, the EDL field in nanofluidic chip A is the strongest as the highest ratio of the DEL thickness to the nanochannel height, which signifies that the ion concentration in the nanochannel of nanofluidic chip A is the highest. Selon l'éq. (10), the nanochannel of nanofluidic chip A is more conductive due to the higher ion concentration. Hence, the value of electrical current in nanofluidic chip A was the largest, whereas nanofluidic chip C yielded the smallest value. In addition, at larger width sizes, EDLs did not overlap along the width directions of nanochannels. In nanofluidic chip B, when the value of applied electric field was lower than 25 V, a linear relationship was noticed between current and applied voltage; however, a limiting region appeared as the value of applied voltage increased and finally, became liner again as the electrical field increased further, this phenomenon belongs to ohmic-limiting-overlimiting current characteristic [60, 61]. The results of electrical current measurement revealed that the nanofluidic devices fabricated by the proposed method were effective, the pile-ups of the nanochannels A, B, and C had almost no influence on the performance of the nanofluidic devices.
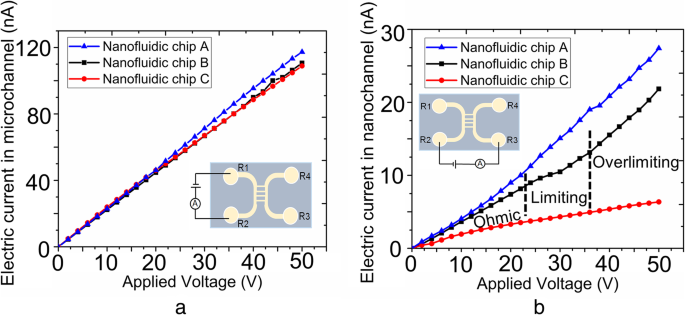
Electric current measurement results based on the fabricated nanochannel devices, the cross-section size (depth × width) of nanochannels for nanofluidic chip A, B, and C are 60 × 500 nm, 80 × 680 nm and 120 × 690 nm, respectively. un Current in microchannels. b Current in nanochannels. The insets display the schematic sketches of the measurements
Conclusions
In the present research, nanochannels with controllable sizes (sub-100-nm depth) were fabricated by AFM tip-based nanomilling, and for the first time, the machined nanochannels were applied to prepare nanofluidic devices. The multichannel nanofluidic devices were prepared in four steps:(1) fabrication of nanochannels by AFM tip and piezoelectric actuator, (2) fabrication of microchannels by lithography, (3) transfer of micro- and nanochannels, and (iv) bonding. Further, nanochannel sizes were controlled by changing the driving voltages and frequencies inputted to the actuator. The heights of the wall obtained during first transfer were smaller than the original machining size, whereas the widths were larger than the original machining size. The experiment results revealed that during second transfer process, nanochannel sizes affected PDMS weight ratios. Finally, micro-nanofluidic chips with three different nanochannel sizes were obtained by bonding a PDMS nanochannel chip on a PDMS microchannel chip. Moreover, the electrical current measurement experiment was conducted on the fabricated nanofluidic chips, and it was found that the values of current were affected by nanochannel sizes. Therefore, PDMS nanofluidic devices with multiple nanochannels of sub-100-nm depth can be efficiently and economically fabricated by the proposed method.
Compared with other fabrication approach, the proposed method for fabrication of the nanofluidic devices in the study is easy to use and low cost; besides, the nanochannels with controllable dimension size can be obtained easily. However, the commercial AFM system cannot equip with a large-scale high-precision stage due to the spatial limitation; thus, the maximum fabrication length of the nanochannel is confined as 80 μm. In addition, the tip wear cannot be neglected after long-term fabrication due to the high machining speed, which should be investigated in future work.
Abréviations
- AFM :
-
Microscope à force atomique
- DC :
-
Courant continu
- EDL:
-
Electric double layer
- KCL:
-
Potassium chloride
- PC :
-
Polycarbonate
- PDMS :
-
Polydiméthylsiloxane
- PSD:
-
Position-sensitive photodetector
Nanomatériaux
- Découpe :un cours accéléré sur ce processus de fabrication
- Blog :Comprendre le processus de fabrication du PDMS
- Les différentes façons dont le processus de finition ajoute de la valeur fonctionnelle aux projets de fabrication de métaux
- Utiliser une imprimante 3D pour améliorer votre processus de fabrication - Vidéo
- Votre guide du processus de cisaillement de la fabrication des métaux
- La fabrication de tuyaux de process nécessite une planification de routage imaginative
- La fabrication de la tuyauterie de procédé nécessite de respecter des spécifications précises
- Combien de temps votre processus de fabrication nécessite-t-il ?
- Les avantages du sablage pour votre projet de fabrication de métal sur mesure