Un guide du débutant pour la coulée de métal
Un aperçu de la coulée de métal dans une fonderie
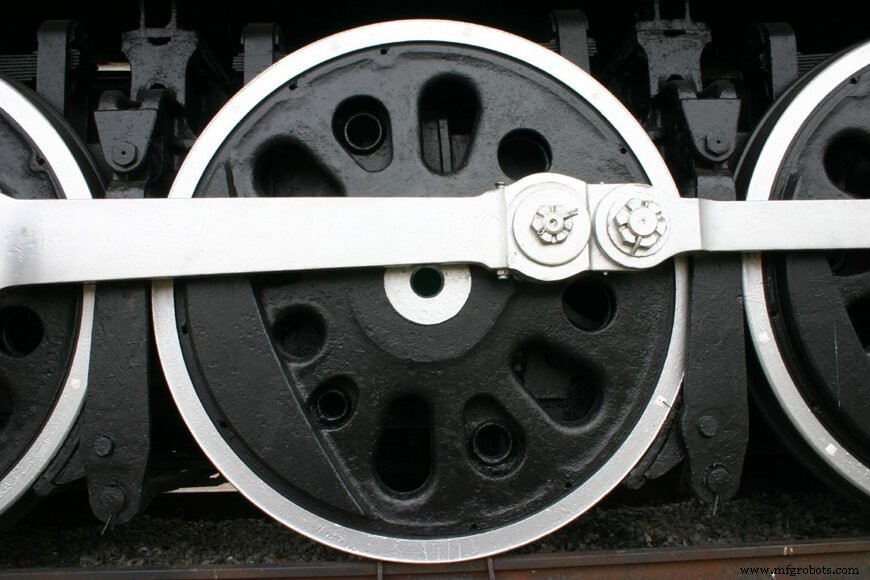
Nos vies sont remplies de produits en métal coulé. De nombreux objets métalliques que nous tenons pour acquis - roues de train, attelages de remorque, lampadaires, équipements industriels à grande échelle et même sculptures - sont coulés dans une fonderie. Le grand nombre d'applications différentes pour le métal coulé démontre sa polyvalence :le métal peut être coulé en composants métalliques durables et complexes avec un minimum d'usinage ou de soudage, réduisant ainsi le besoin de main-d'œuvre coûteuse. Plus important encore, les fonderies de moulage de métal sont devenues un important utilisateur de ferraille recyclée, prenant des objets métalliques obsolètes et les transformant en produits utiles.
Qu'est-ce que la coulée de métal ?
Le moulage est un processus qui crée des formes métalliques solides (moulages) en remplissant les vides dans les moules avec du métal liquide, puis en laissant l'objet refroidir. Les étapes de base impliquées dans la fabrication de pièces moulées sont la création de modèles, le moulage, la fusion et le coulage, le refroidissement, le décochage et le nettoyage, le traitement thermique et l'inspection.
Création de patrons
En termes de coulée, un « motif » est une réplique de l'objet à couler qui est utilisée pour façonner la cavité du moule. Ils peuvent être fabriqués à partir d'une large gamme de matériaux, y compris le bois, le métal ou le plastique. Le patronage est le processus de production de ces patrons. Parce que le modèle détermine la forme du moulage, un moulage ne peut pas être meilleur que le modèle à partir duquel il est fabriqué. Pour produire un moulage de qualité, il est essentiel que le modèle soit soigneusement conçu, construit et fini.
Les fonctions principales d'un motif sont de :
- façonner la cavité du moule
- s'adapter aux caractéristiques de la fonte métallique
- fournir des dimensions précises
- fournir un moyen d'amener le métal liquide dans le moule (le système de porte)
En se solidifiant, le métal a tendance à rétrécir et/ou à se déformer (à des degrés divers selon la fonte du métal). Le motif est conçu avec des tolérances de retrait et de distorsion intégrées pour compenser. Il doit également être construit avec une conicité dans les parois verticales, appelée ébauche, qui est nécessaire pour extraire le motif sans perturber les parois du moule.
Les moulages creux peuvent être créés à l'aide d'un noyau - un morceau supplémentaire de sable ou de métal qui façonne les trous internes et les passages d'un moulage. Chaque noyau est positionné dans le moule avant que le métal fondu ne soit coulé. Afin de maintenir chaque noyau en place, le motif comporte des évidements appelés impressions de noyau où le noyau peut être ancré en place.
Moulage
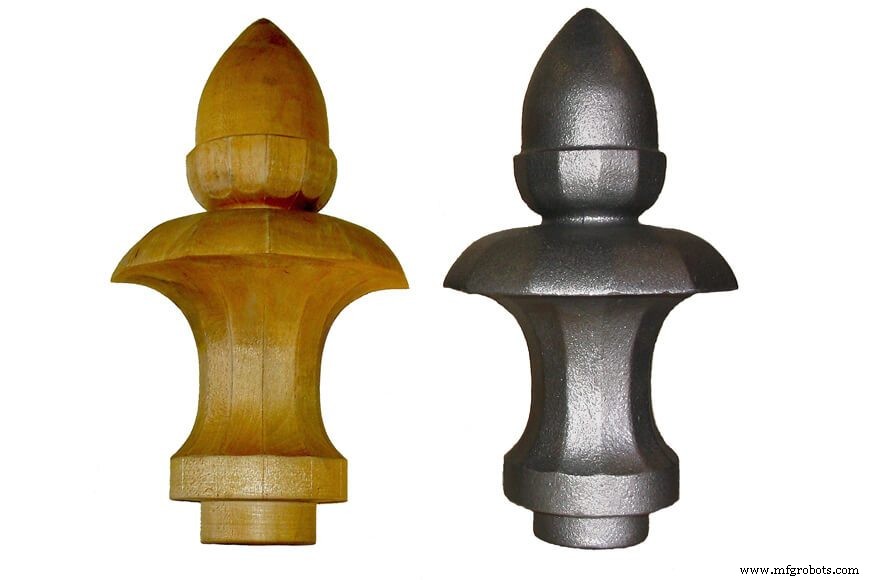
Le moulage est le processus de préparation d'un moule pour recevoir du métal en fusion. Il existe deux types distincts de processus de moulage :réutilisables et non réutilisables.
Comme son nom l'indique, les moules réutilisables peuvent être utilisés à plusieurs reprises. Le processus de coulée ne décompose pas le moule pendant le processus de solidification et de refroidissement du métal. Les moules réutilisables sont généralement en métal.
En revanche, les moules non réutilisables sont des objets temporaires qui sont détruits pendant le processus de solidification et de refroidissement du métal. La méthode de moulage non réutilisable la plus largement utilisée est le moulage au sable, un processus dans lequel du sable spécialement traité (sable « vert ») est enfoncé autour du modèle et placé dans un support (flacon). Le modèle est ensuite retiré, les noyaux sont mis en place et le système de porte est établi pour guider le métal en fusion dans le moule.
Chacune de ces catégories générales de méthodes de moulage comporte de nombreux sous-types spécialisés optimisés pour différents métaux de coulée et différents niveaux de complexité de modèle. Ces méthodes comprennent le coulage en neige fondante, le moulage sous pression, le moulage en coquille et le moulage à la cire perdue.
Faire fondre et verser
Il existe deux catégories de métaux à partir desquels les pièces moulées sont produites :ferreux (métaux contenant du fer) et non ferreux (métaux ne contenant pas de fer). Les alliages ferreux comprennent l'acier, la fonte malléable et la fonte grise. Les alliages non ferreux les plus couramment utilisés dans la fonderie sont l'aluminium et le cuivre, mais les alliages à base de magnésium, de nickel et de titane sont parfois utilisés pour des applications spécialisées.
Les métaux à fondre et à couler – généralement un mélange de ferraille recyclée et de métaux d'alliage – sont chargés pour « charger » le four. Une fois à l'intérieur du four, le métal est soumis à des températures extrêmement élevées jusqu'à ce que le point de fusion (souvent supérieur à 2500 degrés Fahrenheit [1370°C]) soit atteint. Des fours spécialisés sont nécessaires pour atteindre des températures aussi élevées.
Les deux principaux types de fours de fusion utilisés par les fonderies sont l'arc électrique et l'induction.
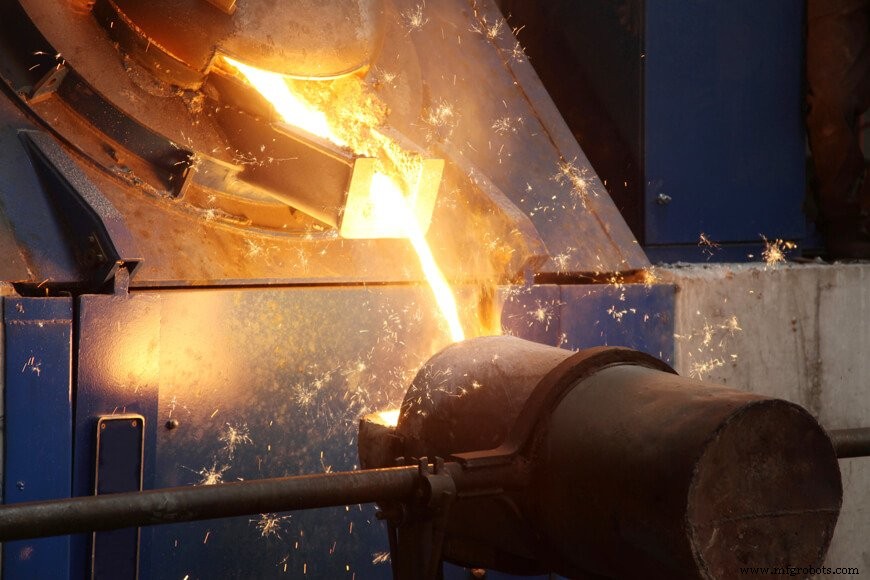
Le four à arc électrique fonctionne comme un processus de fusion par lots, produisant des lots de métal en fusion connus sous le nom de "chaleurs". Le métal est fondu en fournissant de l'énergie électrique à l'intérieur du four via des électrodes en graphite. L'énergie chimique supplémentaire est fournie par des brûleurs oxycombustibles et des lances à oxygène. De l'oxygène est injecté pour éliminer les impuretés et autres gaz dissous pendant le processus de fusion. Au fur et à mesure que le métal fond, des scories se forment et flottent au sommet du métal en fusion; le laitier, qui contient souvent des impuretés indésirables, est éliminé avant le soutirage (processus d'élimination du métal du four).
Un four à induction transfère l'énergie électrique par induction - une source électrique à haute tension provenant d'une bobine primaire induit une basse tension, un courant élevé dans la charge d'acier ou la bobine secondaire. Les fours à induction sont capables de fondre et d'allier une grande variété de métaux avec une perte de fusion minimale, mais en ce qui concerne l'affinage des métaux, ils sont moins capables que les fours à arc électrique.
En raison de leurs forces et faiblesses respectives, les fours à arc électrique sont plus largement utilisés pour la fusion des métaux ferreux, tandis que les fours à induction sont plus répandus dans les applications non ferreuses.
Solidification, éjection et nettoyage
Des creusets, des bras robotisés et des machines de coulée par gravité sont utilisés pour déplacer le métal en fusion d'un endroit à un autre. Des métallurgistes qualifiés verseront également du métal en fusion à l'aide de louches. Le métal en fusion est versé dans le moule à travers un système de portes et de colonnes montantes; le métal se refroidit et se solidifie, adopte en permanence la forme de l'intérieur du moule (vide), qu'il occupe. La pièce moulée est ensuite éjectée du moule ou retirée d'un moule en sable par décochage.
Les portes et les colonnes montantes qui livrent le métal en fusion à l'intérieur du moule se remplissent également de métal en fusion au cours du processus. Le métal dans le moule se solidifie avec le métal dans le système de porte et de colonne montante, formant une seule pièce. Immédiatement après l'éjection/le décochage, le métal de la porte et du système de cavalier est toujours attaché au corps de coulée principal. Cet excès de métal est éliminé lors du processus de nettoyage (un marteau à piquer ou une scie à ruban sont couramment utilisés). Un mélange de barils de culbutage, d'unités de jet d'air et de nettoyeurs haute pression est utilisé pour nettoyer tout sable ou tartre restant.
Le moulage résultant doit être de forme et de proportion identiques au motif d'origine, bien qu'il puisse être légèrement plus petit en raison du retrait du métal.
Traitement thermique et inspection
Certaines pièces moulées sont utilisées dans des applications industrielles exigeantes :elles peuvent avoir besoin de conserver leur forme exacte à des températures glaciales, de résister à la corrosion dans un environnement humide ou de supporter un poids immense. Le traitement thermique est utilisé pour modifier les propriétés physiques du métal selon les spécifications requises.
Le traitement thermique implique l'utilisation du chauffage et du refroidissement, souvent à des températures extrêmes, pour réduire les contraintes dans une pièce moulée et/ou modifier les propriétés physiques du métal. La température doit être contrôlée avec précision pour obtenir les propriétés physiques souhaitées.
Avant qu'un cycle de production de pièces moulées puisse être considéré comme terminé, ses propriétés physiques et son intégrité structurelle sont testées. Les méthodes de test qui nécessitent la destruction du moulage testé sont appelées tests destructifs, tandis que celles qui n'endommagent pas le moulage sont classées comme non destructives.
Les méthodes de test utilisées dépendent de l'exigence des spécifications. Pour certains produits purement esthétiques, seule une brève inspection visuelle de la précision dimensionnelle, des fissures et de la finition de surface est requise. D'autre part, si la pièce coulée doit fonctionner de manière industrielle, toutes ses propriétés physiques (ductilité, résistance à la traction, allongement, propriétés d'impact, dureté, etc.) peuvent être testées de manière exhaustive.
Durée de vie et recyclage
Une fois qu'une pièce moulée a passé l'inspection, elle est expédiée, vendue et mise en service. Les produits en métal coulé, en particulier ceux qui ont subi un traitement thermique, sont durables. Selon l'alliage métallique et l'application, leur durée de vie peut varier de quelques mois à plusieurs décennies. Une fois la durée de vie d'une coulée terminée, le cycle recommence. Il est collecté par un parc à ferraille, recyclé et refondu en un nouvel objet.
Vous souhaitez en savoir plus sur la production de moulage de métal sur mesure ? Une meilleure compréhension du processus de coulée de métal et de la manière de communiquer vos besoins à une fonderie de production vous aidera à garantir la réussite de votre projet de coulée.
Articles associés :
- Casting en profondeur :la vie d'une série de casting
- Conditions de fonderie
- Production d'acier moulé
- Fonte ductile contre fonte
- Traitement thermique
Métal
- Le guide du débutant sur les phoques à ressort
- Le guide du débutant sur les ressorts de compression
- Le guide du débutant sur les vis à double extrémité
- Le guide du débutant sur les extrémités du joug
- Le guide du débutant sur les charnières à fermeture automatique
- Le guide du débutant sur les ressorts de traction
- Un guide du débutant sur les aimants flexibles
- Normes des composants plastiques :Guide du débutant
- Qu'est-ce que le casting ? - Définition | Types de coulée