Les pièces hybrides surmoulées ouvrent de nouveaux marchés pour les composites
Complexité et force. Des composants tels que le support B pour les bacs de stockage d'avions présentent à la fois une grande complexité et une exigence de haute résistance - une combinaison pour laquelle la technique de surmoulage hybride est particulièrement adaptée. Source, toutes les images | Composites aérodynamiques TxV
Souvent, sur le marché de l'aérospatiale, un équipementier est prêt à payer plus pour un composant composite, sachant que l'investissement rapportera des dividendes en économies de carburant en raison de la légèreté du composant, d'une durée de vie plus longue en raison d'une usure moindre ou d'autres réductions des performances opérationnelles. et les frais d'entretien. Cette vision du « cycle de vie du produit » a ouvert de nombreux marchés et applications aux composites. Plus inhabituel est un composant composite dont le coût d'acquisition lui-même est inférieur à celui de la version métallique. Mais cela est en train de changer. Certains nouveaux processus automatisés de fabrication de composites commencent à faire pencher la balance en faveur des composites, parmi lesquels un processus de surmoulage hybride développé par TxV Aero Composites (Bristol, R.I., États-Unis).
Une coentreprise de Tri-Mack Plastics Manufacturing (Bristol, R.I., États-Unis) et Victrex (Thornton Cleveleys, Royaume-Uni), TxV a fait progresser sa technique de surmoulage hybride au point de devenir une production commerciale. La société s'est associée à SFS intec Aircraft Components (Althengstett, Allemagne) pour reconcevoir et produire commercialement un support de bac de stockage d'avion auparavant fabriqué à partir d'aluminium de qualité aérospatiale. Une réussite en soi, le support démontre également le potentiel du surmoulage hybride et du ruban unidirectionnel en fibre de carbone/polyaryléthercétone (PAEK) VICTREX AE 250 pour des économies de poids et de coûts dans de nombreuses applications aérospatiales - avantages obtenus en remplaçant un processus d'usinage soustractif des métaux par un processus composite dans lequel le matériau est ajouté, pas soustrait.
De la soustraction à l'addition
Les machinistes et les ateliers d'usinage qui produisent des composants métalliques sur des machines CNC se sont surnommés eux-mêmes des « fabricants de copeaux », pour la raison évidente que leurs processus coupent le matériau inutile des ébauches métalliques pour fabriquer des composants, créant ainsi des copeaux de ferraille. Ces copeaux représentent un aspect coûteux de l'usinage des métaux, qu'ils soient éliminés, envoyés à un recycleur ou retraités en interne. Dans le cas du support de bac de stockage suspendu de SFS intec, 60 à 70 % de l'aluminium devient de la ferraille au cours des différentes étapes de fraisage nécessaires à son usinage.
Ce taux de rebut élevé rend le coût des matières premières pour une version composite en forme de filet ou presque du support potentiellement inférieur au coût du matériau métallique. « Nous pouvons rivaliser avec l'aluminium moins cher (par livre) à cause des copeaux ; si le ratio achat/vol est de 8:1, la majeure partie de l'aluminium acheté devient de la ferraille », note Jonathan Sourkes, responsable principal des comptes de TxV. « Un autre facteur est le temps que chaque composant passe à être fraisé. Nous pouvons fabriquer des pièces [composites] en quelques minutes, pas en heures. »
Au-delà des coûts des matières premières, les versions composites de composants tels que le support - présentant une géométrie complexe et nécessitant des performances de charge élevées - n'ont pas été économiquement réalisables en utilisant les options de fabrication historiquement disponibles. D'une part, si les composants étaient fabriqués avec un renfort de fibres coupées à faible coût dans un processus à grande vitesse et à faible toucher comme le moulage par injection, le composant n'atteindrait pas des performances de charge suffisantes. D'un autre côté, s'il était fabriqué avec un renforcement en fibres continues plus porteuses via un processus à faible vitesse et à contact élevé, impliquant généralement un drapage manuel, la production serait trop lente et/ou imposerait des coûts de fabrication qui rendraient le produit final trop cher.
En raison de ces obstacles aux nouvelles applications composites de ce type, l'industrie des composites dans son ensemble a consacré des ressources importantes au développement de processus automatisés capables de produire de tels composants à des taux de production suffisamment élevés et avec une capacité de charge suffisante pour répondre aux besoins et aux spécifications des clients de l'aérospatiale. . En vue de la production commerciale de ces composants composites, TxV a vu le jour en 2017 spécifiquement pour accélérer l'adoption commerciale de procédés de fabrication innovants pour les applications composites à base de polycétone dans l'ensemble de l'industrie aérospatiale.
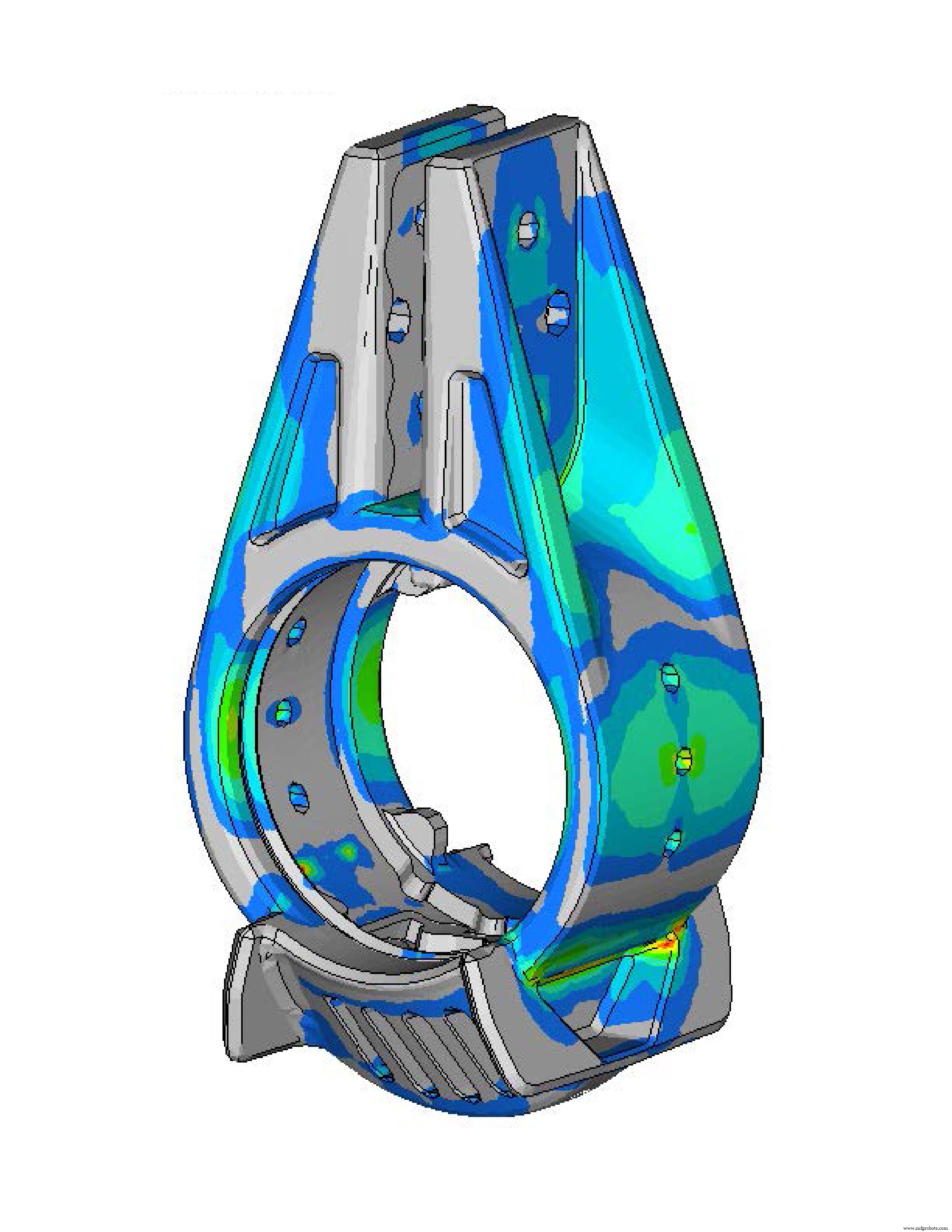
Prototypage virtuel. À l'aide de données exclusives développées pour caractériser la relation entre le stratifié et le surmoulage, TxV a itéré les couches et les orientations des plis sans avoir à fabriquer et à tester un prototype physique. Les itérations se poursuivent jusqu'à ce que les contraintes visibles, comme illustré ici, se situent dans la plage des cas de charge fournis.
La solution hybride surmoulée de TxV intègre deux avancées clés à l'état de l'art dans la fabrication de composants composites. Premièrement, il automatise la production des parties du composant qui nécessitent la résistance ou la rigidité d'un renforcement continu en fibres. Deuxièmement, il tire parti de la vitesse du moulage par injection pour compléter les géométries complexes du composant. Plus précisément, il produit un stratifié sur mesure pour gérer les charges, qui est ensuite surmoulé pour fonctionnaliser et créer des géométries de pièces finales. La technique hybride, selon Sascha Costabel, responsable de l'innovation chez SFS intec Aircraft Components, "est une bonne option pour les composants qui doivent résister à des niveaux élevés de contraintes mécaniques et des géométries qui nécessitent plusieurs étapes de traitement où l'usinage conventionnel est utilisé."
Le partenariat avec SFS intec a été un excellent choix, déclare Sourkes. « En tant que leader mondial des pièces jointes système, SFS fait toujours quelque chose de vraiment intéressant. Ils sont très innovants et prêts à investir dans les nouvelles technologies », note-t-il. SFS intec entretient également une relation solide avec ses clients aéronautiques, ajoute-t-il, et ils possèdent la capacité d'effectuer des processus de qualification - clé pour l'adoption par l'industrie aérospatiale d'un composant repensé.
Le support de bac de stockage d'avion, spécifiquement appelé « support B », a été choisi comme premier composant de fixation pour la refonte des composites, car il est représentatif des composants difficiles à concevoir et à produire. Après l'ingénierie collaborative, la conceptualisation et la conception des pièces et la modélisation des performances via un outil d'analyse par éléments finis (FEA) d'Altair (Troy, Michigan, États-Unis), l'équipe du projet a itéré à partir du premier article pour valider, tester et prouver le modèle. La conception pour la fabrication était au cœur du développement du support composite, qui tire parti des avantages de fabrication de la pose automatisée de ruban pour les éléments renforcés de fibres continues et du moulage par injection à grande vitesse pour les éléments renforcés de fibres coupées.
Supports du bâtiment B
Un aspect clé du processus de surmoulage hybride est l'utilisation de polymères distincts de la même classe. Le PAEK sert de résine de matrice pour les parties composites à fibres continues du support, tandis que le polyétheréthercétone (PEEK) est utilisé dans les zones surmoulées. VICTREX PAEK et PEEK offrent une résistance supérieure à la fatigue, aux produits chimiques et à la corrosion ; excellente résistance à la fumée, aux flammes et à la toxicité ; formabilité rapide; et la soudabilité. VICTREX AE 250, un PAEK à plus faible point de fusion (LM PAEK), offre une température de fusion de 40 degrés C inférieur à celui du PEEK. « Lorsque du PEEK fondu s'écoule sur la surface du composite LM PAEK, la température de fusion inférieure permet une fixation solide », explique Sourkes.
Les matières premières spécifiques pour le support B sont le ruban PAEK unidirectionnel renforcé de fibres de carbone VICTREX AE 250 (58% de fibres de carbone) dans des largeurs de deux pouces ; et VICTREX PEEK 150CA30 rempli de fibre de carbone court (30 % de fibre de carbone). Ces matériaux alimentent les cellules de travail de production de surmoulage hybride, qui créent les supports grâce au processus en plusieurs étapes suivant.
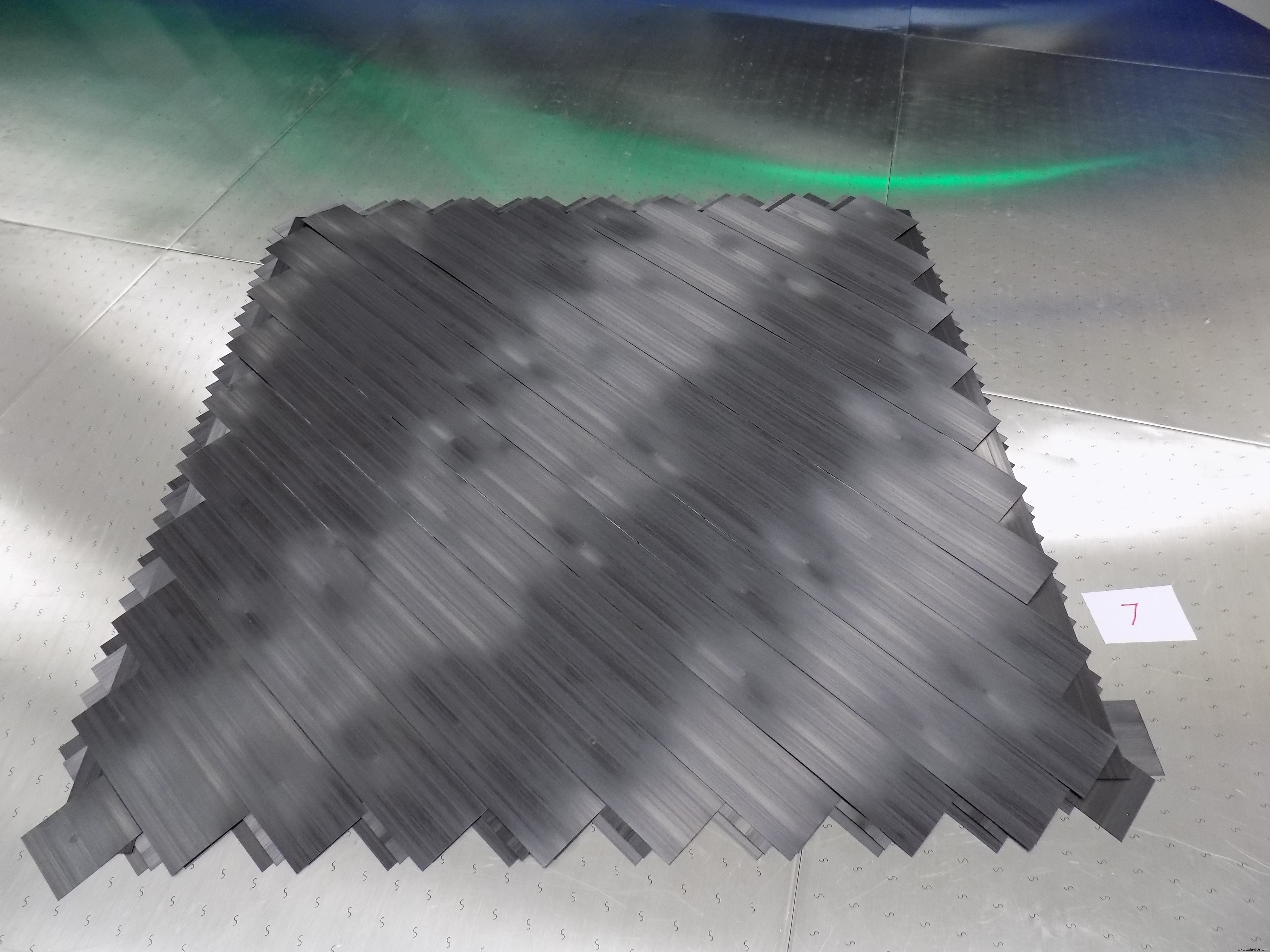
Étape 1. Un système de pose de ruban automatisé Dieffenbacher Fiberforge 2000 produit des découpes de stratifié sur mesure.
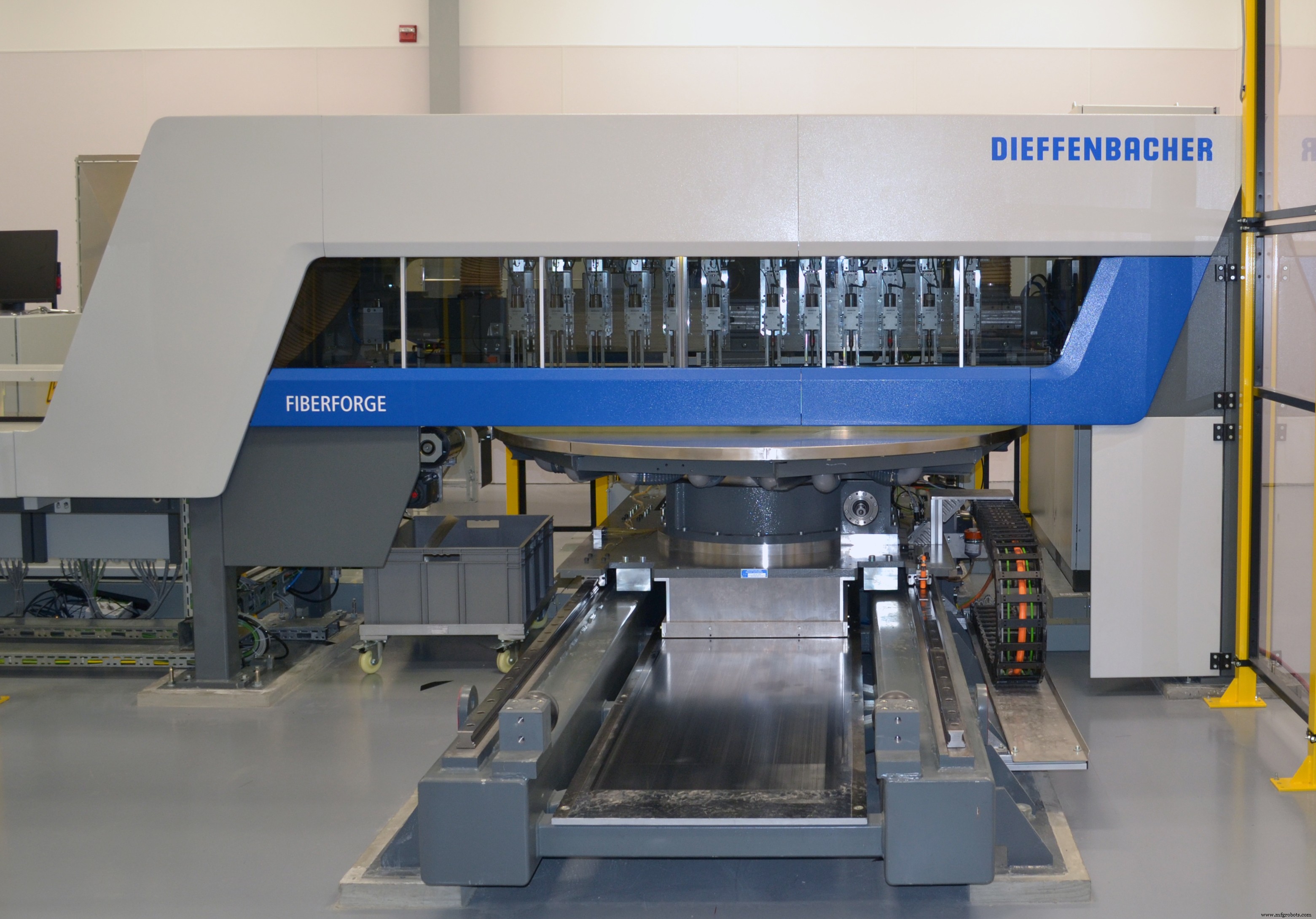
Tout d'abord, les rubans en fibre de carbone/PAEK sont posés dans un flan sur mesure à l'aide d'un système de pose de ruban Fiberforge 2000 de Dieffenbacher (Eppingen, Allemagne). « Cette machine est actuellement l'un des systèmes de pose de bandes les plus rapides au monde », atteste Sourkes. Il est équipé de robots pour charger et recharger les bobines de bande, afin qu'il puisse fonctionner sans interruption, minimisant ainsi le temps de contact manuel. La superposition est conçue de manière à minimiser les écarts entre les bandes. Chaque pli du flan sur mesure du support B est inspecté avant la pose du pli suivant. Le processus est effectué dans une zone à environnement contrôlé afin de minimiser le potentiel de corps étrangers et de débris (FOD).
Les ébauches sur mesure sont ensuite consolidées dans une cellule automatisée sur mesure qui nécessite une manipulation manuelle minimale pour charger et décharger les stratifiés. Dans la cellule, des plateaux chauffants assortis consolident par pression un panneau, éliminant ainsi les vides. Des plaques froides assorties refroidissent ensuite le panneau. Les deux jeux de plateaux, maintenus à température, sont beaucoup plus efficaces qu'une presse statique avec un seul jeu de plateaux. "Le résultat est un temps de cycle considérablement réduit mesuré en minutes par rapport aux heures", explique Sourkes.
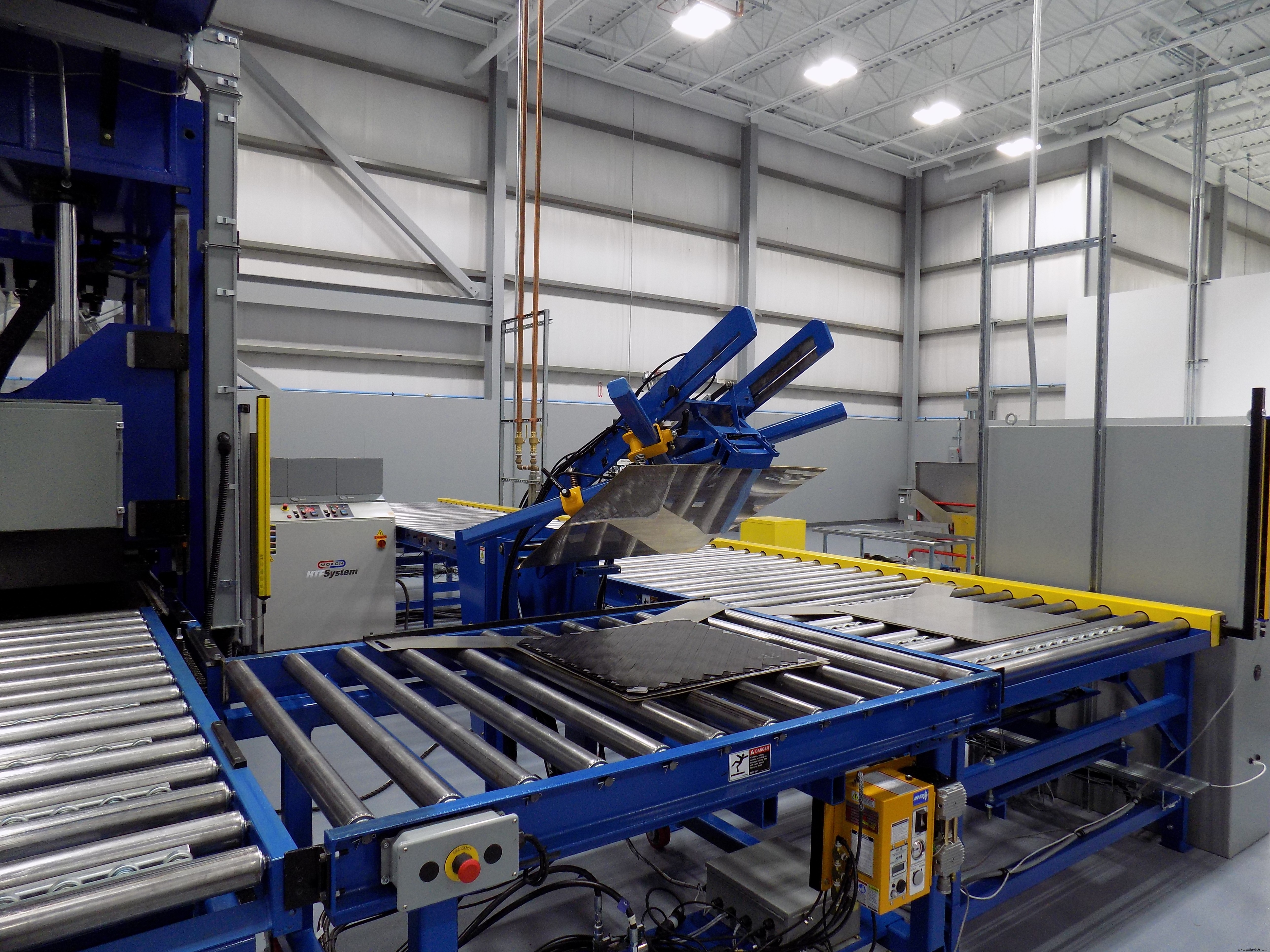
Étape 2. Les flans sur mesure sont consolidés dans une cellule de consolidation automatisée sur mesure, qui comprend deux ensembles de plateaux maintenus à température (un chaud, un froid) pour accélérer cette étape.
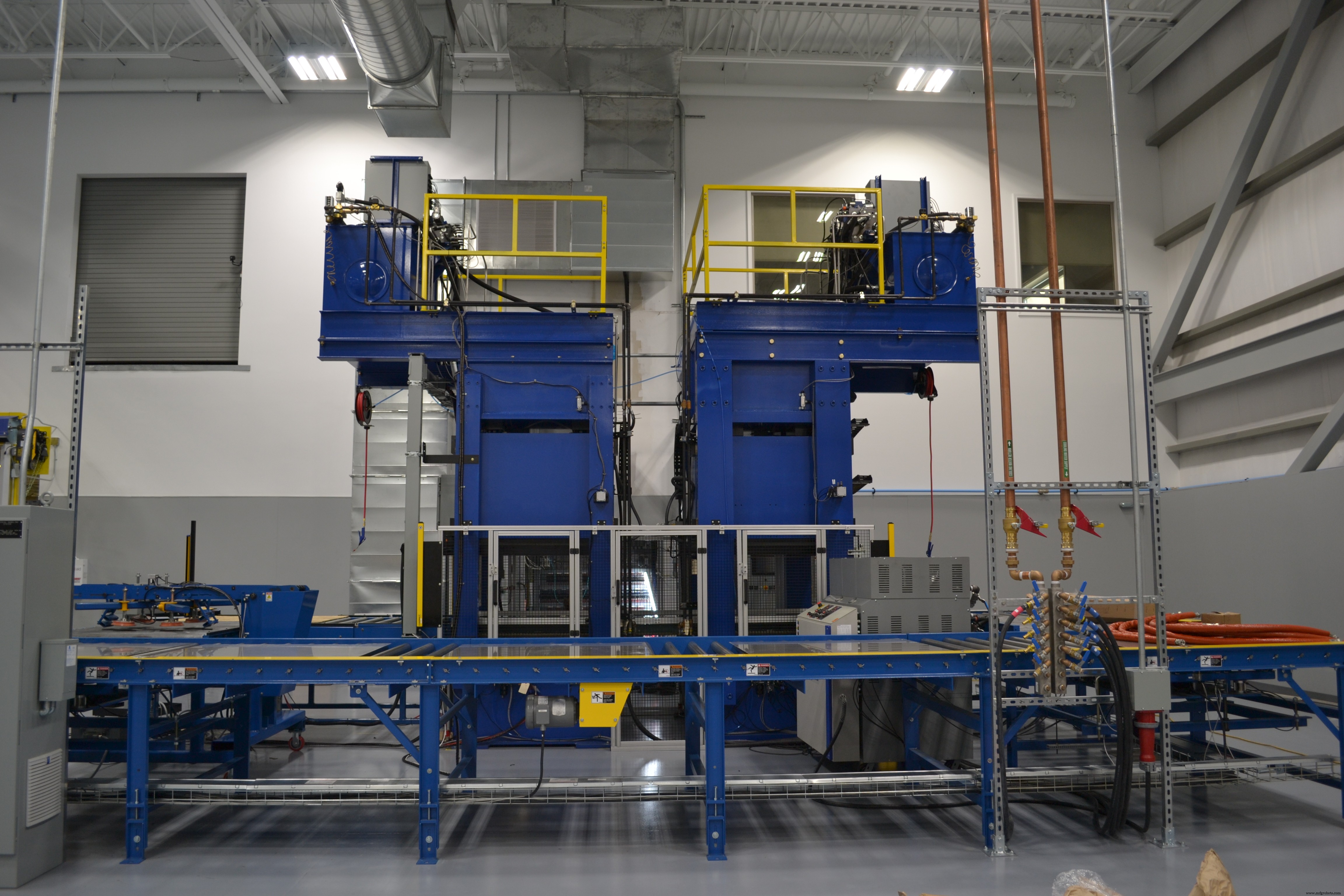
Les préformes stratifiées consolidées sont ensuite traitées dans une cellule de travail exclusive pour former la forme principale du support (étape 3). Les inserts finaux en fibre de carbone/PAEK sont ensuite découpés dans les ébauches formées à l'aide d'un cutter à jet d'eau Flow International (Kent, Wash., États-Unis) (étape 4)
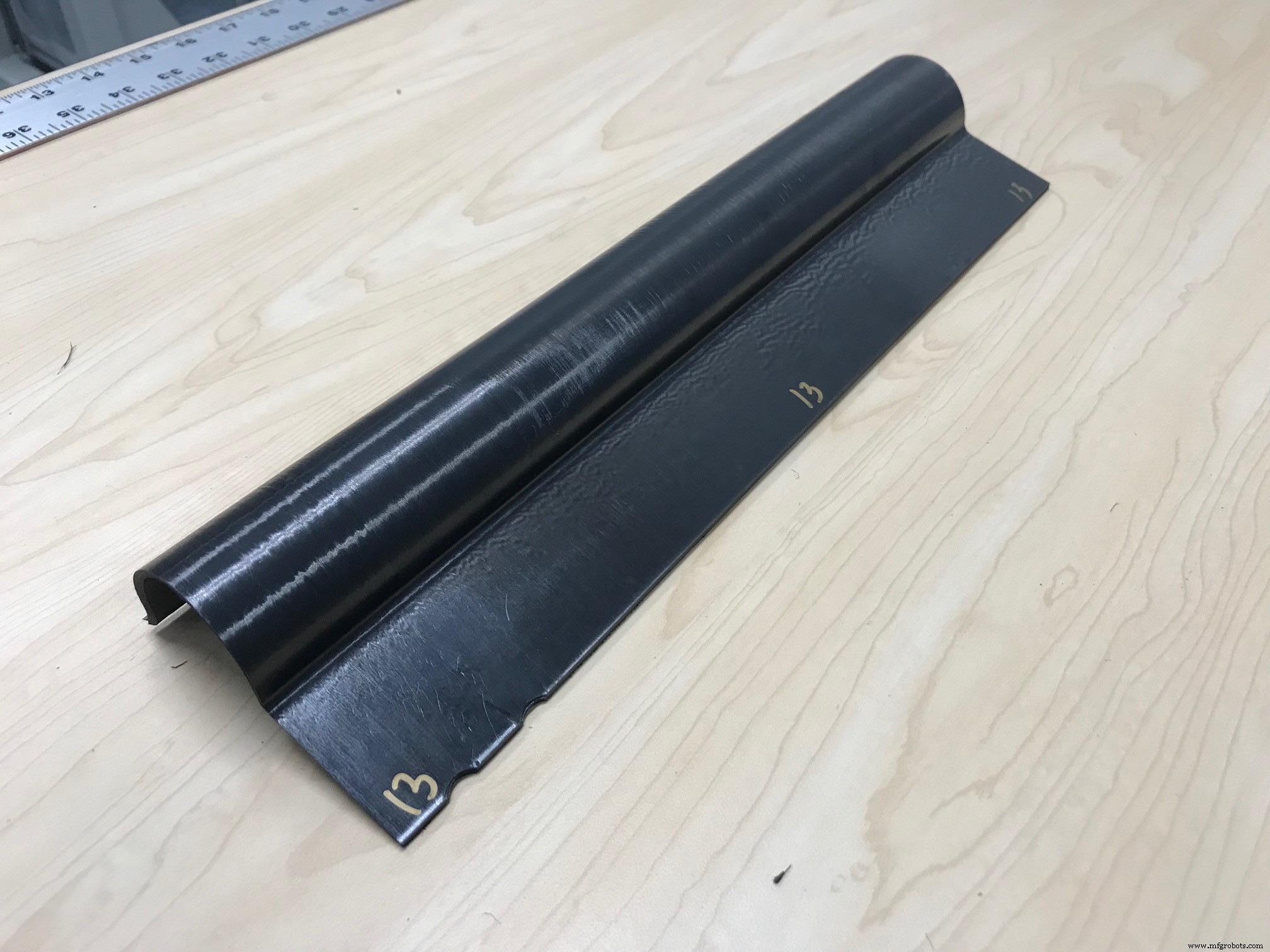
Étape 3. Une cellule de travail exclusive forme la forme principale du support.
En déterminant la taille du flan sur mesure, Sourkes souligne qu'un compromis doit être délibéré pour chaque projet. « Nous pouvons dimensionner le stratifié de manière à pouvoir extraire trois ou quatre rectangles à partir d'un seul carré vierge. En déposant un flan aussi grand que possible, puis en le découpant en préformes, vous maximisez le rapport achat/vol ; mais la découpe des préformes signifie plus de temps pour les opérations de découpe au jet d'eau. Dans le projet B bracket, chaque stratifié consolidé est découpé en plusieurs préformes
Vient ensuite l'étape de surmoulage, qui est réalisée avec une machine de moulage par injection à haute température Engel (Schwertberg, Autriche) (étape 5). Les inserts sont placés dans une cavité de moulage par injection qui est ensuite remplie de PEEK fondu. Les inserts sont placés dans une cavité de moulage par injection qui est remplie de PEEK fondu, qui fait fondre la couche supérieure des stratifiés VICTREX AE 250 pour créer un composant solide lié par fusion.
Si nécessaire, un composant est fini par usinage à la forme nette. "Bien que notre objectif soit de mouler des pièces proches du filet", admet Sourkes, "souvent, un niveau minimal d'usinage est nécessaire après coup pour nettoyer la géométrie du processus." L'usinage peut être effectué avec un jet d'eau ou un usinage CNC.
Résultats révolutionnaires
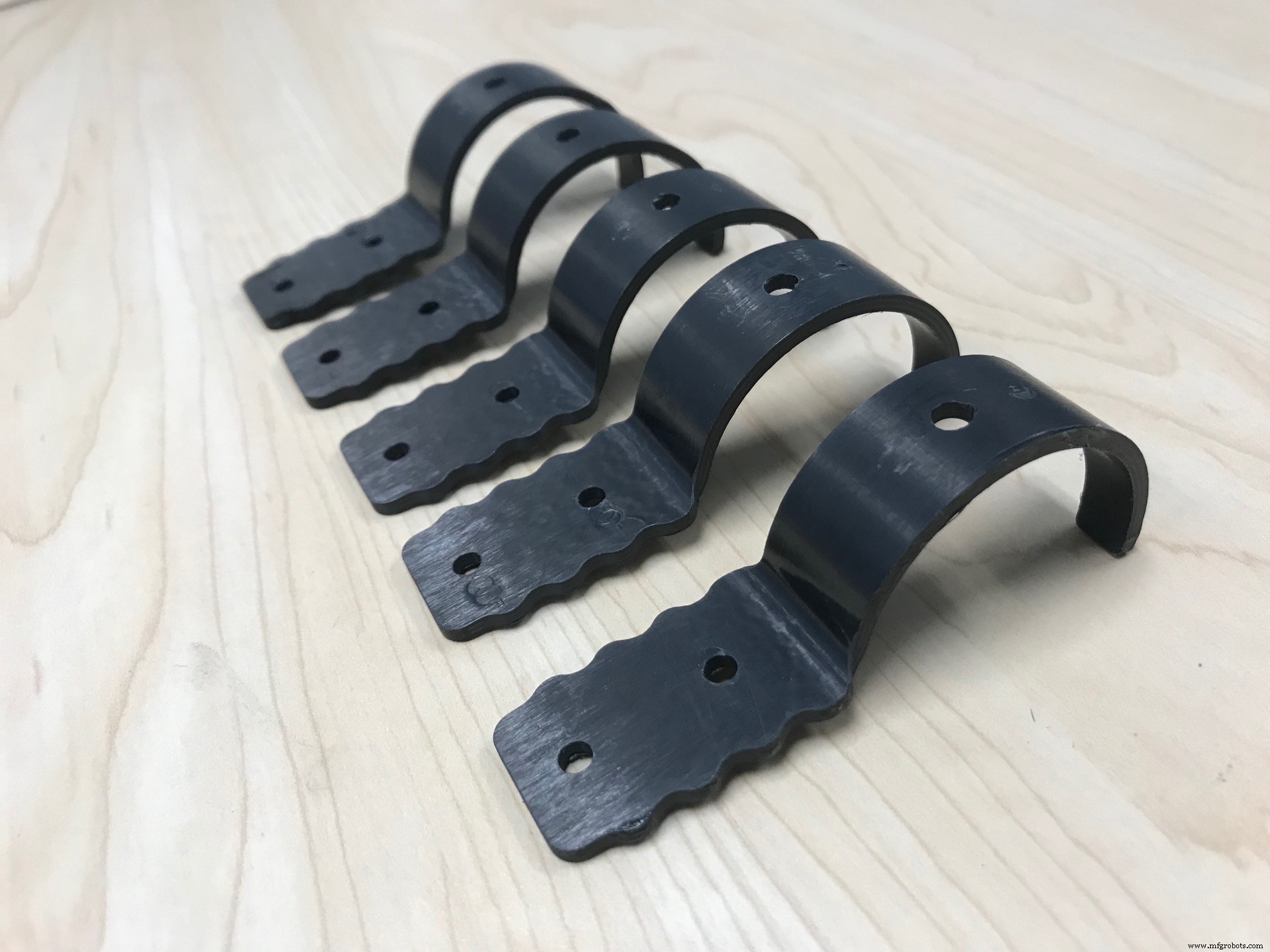
Étape 4. Une découpeuse au jet d'eau Flow International coupe les inserts en fibre de carbone/PAEK des flans formés. Deux de ces inserts sont utilisés dans chaque support.
Lors de la fabrication du support SFS intec, le processus de surmoulage hybride TxV atteint des temps de cycle de trois minutes et un rapport achat/vol de 1,06:1. « C'est l'utilisation efficace des matériaux et un processus de fabrication rapide qui nous permet de produire des pièces composites thermoplastiques à valeur ajoutée, et qui permet de réduire les coûts du système par rapport aux conceptions métalliques en place », souligne Sourkes. « Effectivement, nous remplaçons une matière première à moindre coût avec un rapport achat/vol élevé et un temps de traitement important par une solution matérielle hautement technique. » Le résultat est des économies de poids de l'ordre de 30 à 40 % et des économies de coûts de l'ordre de 20 à 30 % dans un remplacement similaire, c'est-à-dire une pièce de rechange qui suit les mêmes spécifications géométriques et opérationnelles que le composant existant. « Les économies de poids en particulier peuvent atteindre 60 % lorsque nous avons la possibilité de reconcevoir complètement un système de pièces», note-t-il.
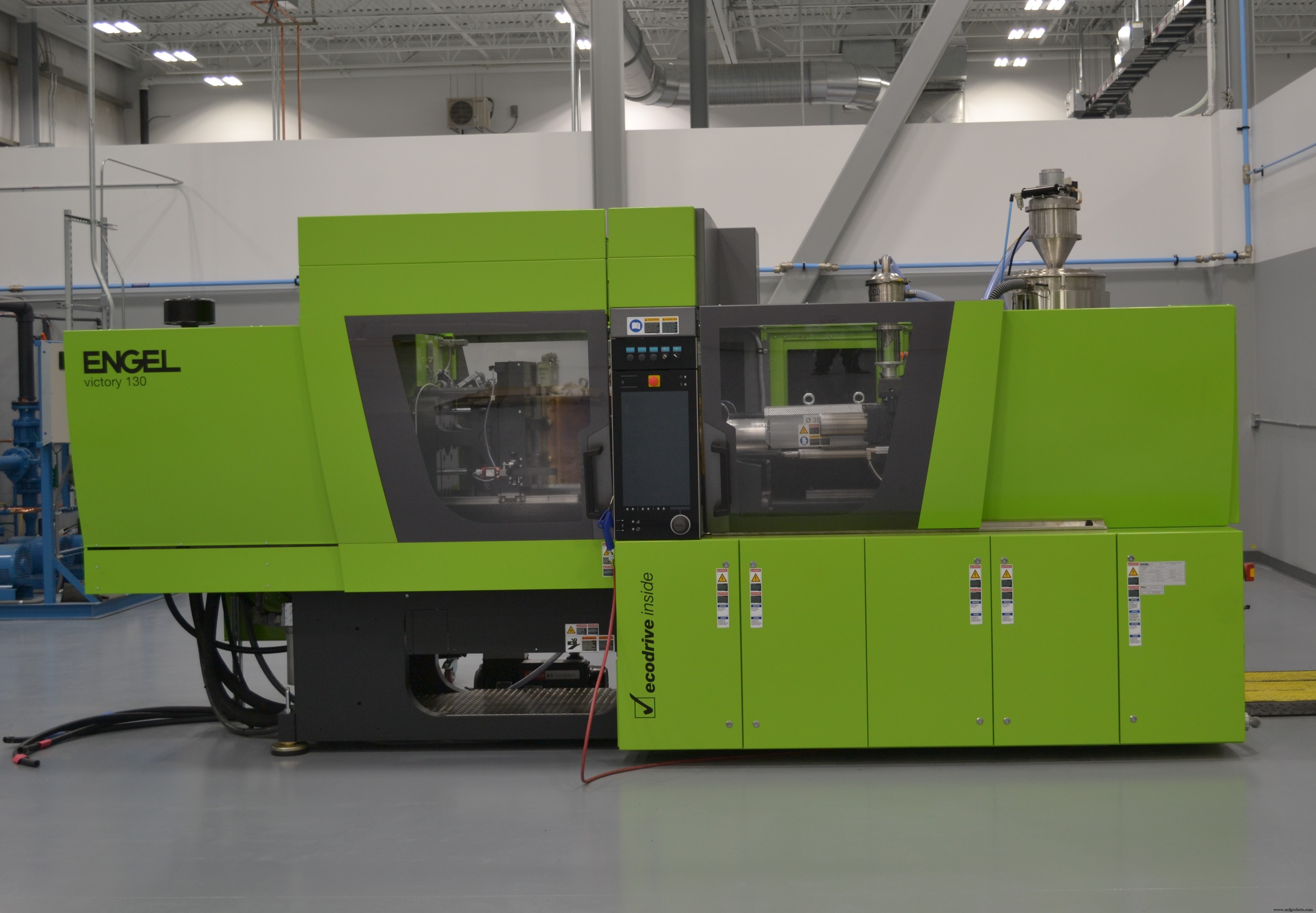
Étape 5. Une presse à injecter Engel optimisée pour le surmoulage hybride PEEK complète la pièce composite en surmoulant les inserts.
Le support en fibre de carbone/PAEK/PEEK a également consolidé le nombre de pièces :TxV et SFS ont convenu de surmouler par injection un nez d'écarteur sur le bas de la pièce dans la même opération que celle utilisée pour fonctionnaliser et ajouter d'autres fonctionnalités. Auparavant, le nez de l'écarteur était en PEEK puis maintenu en place par deux rivets. Ainsi, la consolidation se traduit à la fois par une réduction du nombre de pièces et par la suppression d'une étape d'assemblage.
L'expertise des deux sociétés qui ont lancé TxV a sans aucun doute permis le succès du surmoulage hybride. Sourkes explique qu'après avoir développé le matériau PAEK et la technologie de traitement, Victrex a d'abord exploré les opportunités avec des partenaires commerciaux existants. "Cependant, les entreprises possédant une expertise en moulage par injection n'avaient pas l'expertise nécessaire pour travailler avec des composites renforcés de fibres continues, et vice versa." Victrex et Tri-Mack se sont associés pendant plusieurs années avant de former TxV en 2017 et de construire le centre d'excellence des composites de polycétone spécialement conçu pour l'entreprise, qui est hautement automatisé et conçu pour la production en série à haut débit.
Lorsqu'on lui a demandé de comparer le processus et les résultats TxV avec une approche de fabrication conventionnelle, Sourkes note que le support B ne se prête pas aux approches de fabrication de composites standard. "Ce serait très difficile sans usiner le support à partir d'une billette composite - ce qui serait prohibitif", dit-il.
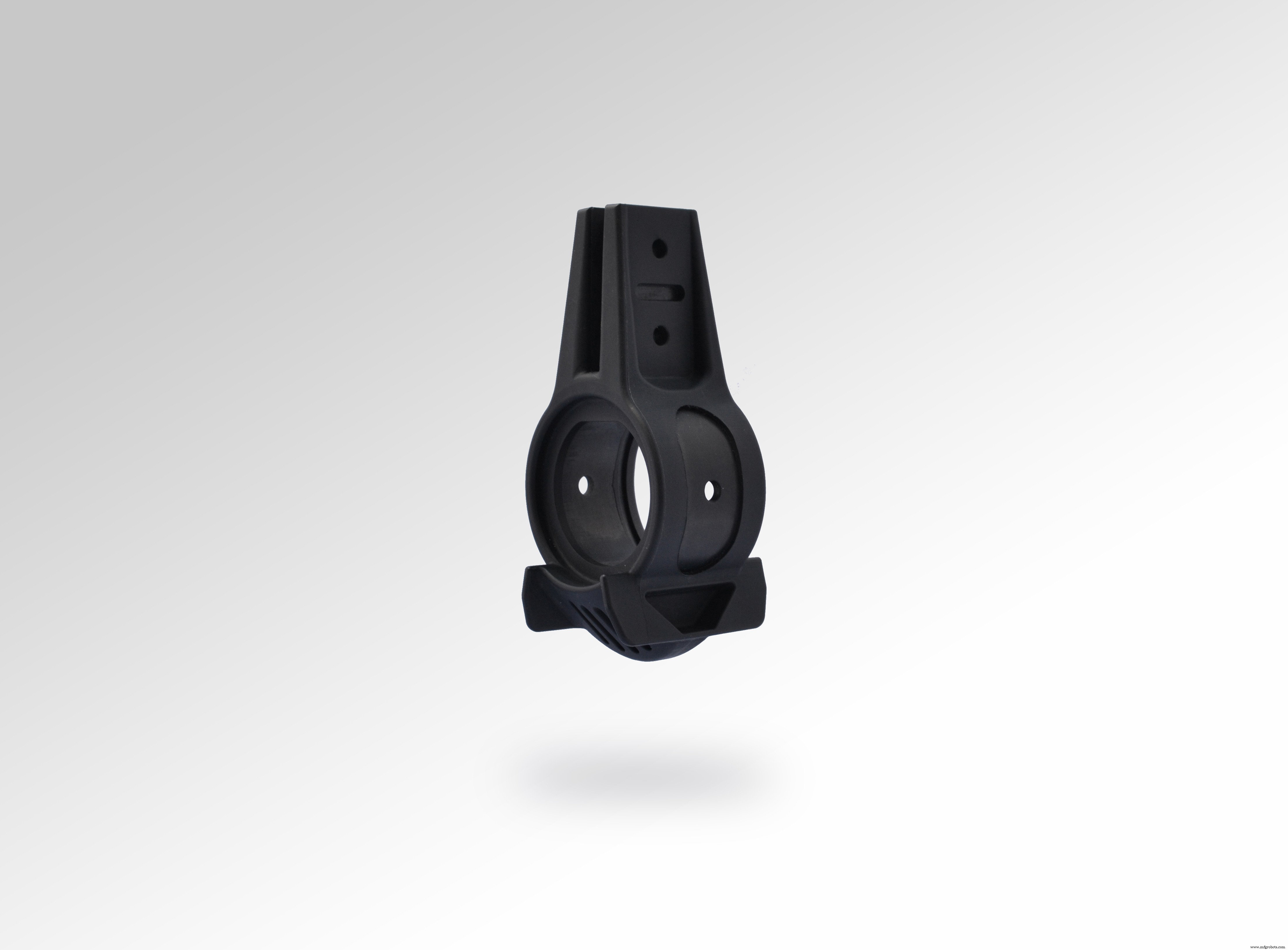
Étape 6. Le support B final est produit avec un temps de cycle de trois minutes, un rapport achat/vol de 1,06:1 et une économie de poids de 30 à 40 %.
Qualifiez-vous puis volez
Profitant de la capacité de SFS intec à exécuter la qualification, les deux sociétés ont procédé à la certification par « conception ponctuelle », ce qui signifie que seule cette géométrie de pièce particulière obtient l'approbation de vol. Les pièces ont été produites et soumises aux tests décrits dans le document de qualification. « Étant donné que la pièce est un support de bac supérieur, les charges opérationnelles sont assez facilement atteintes », note Sourkes. "Cependant, les exigences de performances vont au-delà de ces charges typiques et doivent couvrir certaines manœuvres de décollage et d'atterrissage extrêmes." En tant que CW est sous presse, le dossier de qualification a été soumis et attend l'approbation finale du dépositaire des spécifications. TxV et SFS intec s'attendent à ce que la pièce vole au début de 2020.
Une fois la tranche B qualifiée, TxV s'adaptera aux volumes de production. Alors que la société utilise sa ligne de surmoulage hybride existante pour produire ces supports, Sourkes souligne que la société a un double mandat :à la fois fabriquer des pièces avec la technologie et soutenir les fabricants de l'industrie intéressés à adopter eux-mêmes la technologie. En d'autres termes, les fabricants de composites peuvent adopter cette technique de fabrication dans leurs propres installations.
Les supports composites comme le produit SFS intec ont le potentiel de conquérir un marché assez important pour ce type de composants. Les avions commerciaux utilisent des milliers de supports et d'accessoires de système, ce qui représente une contribution significative aux coûts et au poids de l'avion dans son ensemble. « Nous sommes convaincus que les composants composites thermoplastiques joueront un rôle de plus en plus important dans la fabrication d'avions », anticipe Costabel.
fibre
- MMF #5 :Guide d'intégration de composants dans des pièces imprimées en 3D
- Une nouvelle façon révolutionnaire de fabriquer des pièces métalliques
- Présentation de notre nouveau matériau Markforged :Onyx
- AT&T et Tech Mahindra collaborent sur une nouvelle plateforme d'IA open source
- LANXESS met en service deux nouvelles lignes de production de composites thermoplastiques Tepex
- Nèos International établit un nouveau siège, une usine de composites au Royaume-Uni
- Comment fabriquer des composants mécaniques de précision
- Comprendre les composants de haute précision
- Finition des pièces et composants