Épisode 29 :John McQuilliam, Prodrive Composites
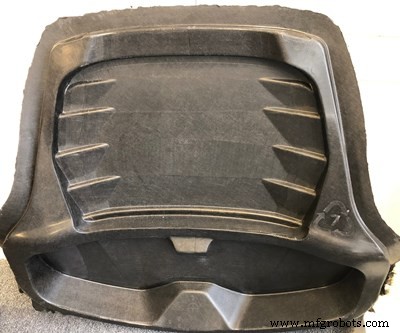
Exemple de pièce tertiaire réalisée selon le procédé P2T de ProDrive. CW photo | Scott François
Dans cet épisode de CWTalks, le rédacteur en chef de CW Scott Francis interviewe John McQuilliam, ingénieur en chef chez Prodrive Composites (Milton Keynes, Royaume-Uni), concepteur et fabricant de composites légers avancés pour un large éventail d'applications, notamment l'automobile, le sport automobile, l'aérospatiale, la marine, la défense et d'autres secteurs spécialisés.
John est un concepteur de voitures de Formule 1 du Royaume-Uni qui a travaillé avec de nombreuses sociétés de sport automobile. Il a rejoint Prodrive en 2017 en tant qu'ingénieur en chef de leur division composites. John discute du processus primaire à tertiaire (P2T) de l'entreprise, qui, selon l'entreprise, simplifie le recyclage et donne aux matériaux composites le potentiel de remplir trois durées de vie utiles ou plus.
Vous pouvez écouter l'intégralité des CW Talks interview ci-dessus ou visitez :
- Conversations CW :iTunes
- Conversations CW :Google Play
Extrait de l'épisode
CW : Salut, John, et bienvenue aux discussions sur CW, le podcast sur les composites. En mars, je crois, j'ai visité Prodrive Composites et j'ai pu voir un peu de votre processus P2T, qui signifie primaire à tertiaire.
JM : C'est vrai. La première étape est la fabrication du composant primaire, et c'est ce que nous réalisons actuellement la majorité des travaux. Ce sont donc des pièces qui nécessitent des fibres vierges, une résine spéciale ou un type particulier de résine thermodurcissable pour quelque raison que ce soit. Ce sont donc ce que j'appellerais des pièces composites traditionnelles... ce sont des pièces dont nous ne modifierions pas particulièrement la conception ou la fabrication, mais nous les modifierions certainement pour les rendre plus facilement recyclables.
CW : D'accord. Et ce sont généralement les pièces les plus performantes ?
JM : Oui. Ils seraient donc fabriqués en thermodurcissable… Ce que nous ferions, c'est simplement changer la conception de ceux-ci pour permettre aux déchets de fabrication des pièces et finalement la partie en fin de vie d'être recyclable afin que nous puissions réutiliser les fibres de carbone contenues au sein de ces parties. Le thermoplastique entre donc dans la deuxième étape... les étapes initiales peuvent être thermodurcissables ou thermoplastiques, mais l'important est que cela nous permette de récupérer les fibres. Donc, pour récupérer les fibres des pièces primaires, comme évoqué, nous changeons certainement les matériaux de conception en quelque chose dont il est plus facile de récupérer les fibres, donc ce dont nous parlons vraiment, c'est d'une utilisation accrue de tissus non frisés, plus les matériaux unidirectionnels, les choses où les déchets de production et le composant lorsqu'ils passent pour le processus de récupération des fibres donneront un meilleur rendement de fibres plus longues de haute qualité.
CW : Pouvez-vous décrire un peu le processus de récupération qui se produit pour ce composant principal et ensuite ce qui caractérise la partie secondaire résultante ?
JM : Oui. Ainsi, le processus de recyclage ou de valorisation des pièces primaires est un processus de type incinération. Ainsi, les déchets de préimprégné - les chutes de préimprégné - ou les pièces en fin de vie vont dans un four et toute la résine est brûlée, laissant les fibres de carbone derrière. Et ces fibres de carbone, grâce à une série de processus, sont transformées en un tapis non tissé d'épaisseur constante et d'orientation aléatoire, ce qui permet de former une plaque quasi-isotopique.
CW : Est-ce le processus qu'ELG [ELG Carbon Fibre] fait pour vous ? Gèrent-ils la pyrolyse ?
JM : Oui, ELG en fait cette partie. Donc, nous leur envoyons nos déchets et certaines pièces détachées, puis ils les transforment en l'un des précurseurs, l'une des pièces que nous utilisons pour fabriquer nos pièces secondaires.
CW : Pouvez-vous me parler un peu de ces pièces secondaires et de ce qui les caractérise ?
JM : Ainsi, les pièces secondaires, le renfort sont principalement constitués de fibres de carbone récupérées avec une utilisation discrète de fibres vierges si nécessaire dans certaines zones. Mais la majorité des renforts sont des fibres récupérées. Et puis on introduit un thermoplastique réactif. Il s'agit donc d'une résine liquide avec laquelle on infuse, disons, les renforts. Ensuite, il y a un type de processus de durcissement et nous obtenons un composant fini et son processus est effectué à des températures relativement basses, à la pression atmosphérique et nous obtenons ainsi un bon composant.
CW : Une partie de ce qui permet le P2T est ce système de résine que vous avez décrit comme une "résine plastique thermique réactive". Pouvez-vous expliquer un peu plus à nos auditeurs ce que vous entendez par là ?
JM : Ainsi, le thermoplastique réactif est à certains égards très similaire à une résine thermodurcissable. Nous le mélangeons donc juste avant de fabriquer le composant. Et il y a deux ou trois composants liquides qui vont au mélange. Chacun d'eux est un liquide. Et lorsqu'ils se combinent avec le temps et un peu de température, ils polymérisent en fait en un véritable thermoplastique. Et ce sont les propriétés thermoplastiques qui permettent un recyclage ultérieur. Et l'avantage qu'il s'agisse d'un thermoplastique réactif plutôt que d'un thermoplastique traditionnel est le fait que nous créons efficacement un thermoplastique en même temps que nous entourons les fibres de renforcement, c'est qu'il a une très faible viscosité, il peut donc être formé de manière traditionnelle normale. , devrait-on dire, des procédés de type thermodurcissable. Il n'a pas besoin de la température élevée et des pressions élevées que vous obtiendrez en injectant un thermoplastique fondu dans une préforme fibreuse ou en prenant un préimprégné thermoplastique où le thermoplastique et les fibres ont déjà été combinés, puis en les remontant à haute température et pression. , généralement dans des moules métalliques. Ainsi, nous évitons la complexité et le coût des outils de moulage requis pour traiter les thermoplastiques au-dessus du point de fusion et évitons les difficultés dues à la viscosité élevée du thermoplastique fondu avec distorsion et mouvement du renfort dans la cavité du moule.
CW : Et je suppose que cela se traduit par des économies de coûts, des gains de temps et signifie essentiellement beaucoup pour la production...
JM : Vous l'avez, oui. Ainsi, la méthode de production est similaire à ce que nous faisons dans l'industrie thermodurcissable traditionnelle, mais le coût de l'outillage est bien inférieur à celui requis pour le traitement d'un thermoplastique traditionnel. Et c'est un gros avantage pour la plupart de nos clients. Vous ne voulez pas faire l'investissement initial dans des outils de moulage thermoplastiques - ou des outils de moulage simplement pour les thermoplastiques.
CW : Considérez-vous cela comme un catalyseur pour une production plus importante ?
JM : Certes, nous pensons que c'est un catalyseur pour une production plus élevée. Les temps de cycle peuvent être plus courts que leur thermodurcissable traditionnel, car ils ne nécessitent pas de montée en température jusqu'à une température de traitement, une temporisation puis un nouveau refroidissement avant de pouvoir retourner le moule. Nous constatons donc des avantages de taux en utilisant ce processus par rapport à nos composants traditionnels durcis au four ou à l'autoclave.
CW : Et bien sûr, l'une des choses intéressantes est qu'à partir de là, vous pouvez à nouveau recycler cette partie secondaire. Alors qu'est-ce qui caractérise cette partie tertiaire dans le cycle de vie de ce matériau ?
JM : Je dirais donc que la partie secondaire, étant un véritable thermoplastique, peut être reformée en d'autres formes et serait généralement coupée en petits morceaux, puis placée dans la cavité entre le moule chauffant et pressée dans une nouvelle forme. Il sera donc possible de récupérer toutes les pièces secondaires redondantes, tous les déchets de production des pièces secondaires, et de les reformer en un autre composant en plastique renforcé de fibres ou en polymère renforcé de fibres.
CW : Et à partir de là, ces parties tertiaires ne sont pas forcément la fin du chemin pour ce matériau, même à cela...
JM : C'est exact... On pense donc que ces parties tertiaires, parce qu'elles sont thermoplastiques, peuvent être reformées, presque une infinité de fois. Le processus de découpe en palettes de moulage, devrions-nous dire en pièces de moulage, a un taux d'attrition sur la fibre… donc certaines propriétés mécaniques chuteraient, mais d'autres propriétés mécaniques telles que la rigidité, le taux de dilatation thermique et la distorsion la température serait plutôt bien conservée. Ainsi, vous obtenez toujours un composant renforcé de fibres de haute qualité - pas avec la résistance d'origine du composant en fibre continue ou même un composant en fibre relativement long - mais il y a certainement toujours les avantages en termes de rigidité, de dilatation thermique et de température de distorsion qui le rendent très intéressant retraiter les parties tertiaires encore une fois.
fibre
- Les 10 principales avancées de la technologie de fabrication des composites
- Hier et aujourd'hui :une brève histoire des matériaux composites
- Composites thermoplastiques chez Oribi Composites :CW Trending, épisode 4
- AMRC et Prodrive s'associent pour faire progresser la fabrication de composants composites recyclables
- Composites hautes performances en Israël
- Épisode 17 :Gino Francato, Sabic ; Arno van Mourik, Aéroporté; John OConnor, Siemens
- Épisode 26 :Achim Fischereder, Hexcel
- Semaine nationale des composites :durabilité
- Nèos International établit un nouveau siège, une usine de composites au Royaume-Uni