Traitements de surface courants des outils de moulage par injection et comment choisir le bon
Le processus de moulage par injection est assez complexe. Il implique plusieurs parties différentes travaillant ensemble pour produire un produit en plastique. Cependant, une partie qui se démarque est le moule lui-même, où l'on injecte le plastique fondu pour former la forme fixe et souhaitée du produit en plastique. Le moule est évidemment l'une des pièces fonctionnelles les plus importantes du moulage par injection, mais aussi l'une des plus coûteuses. Les dommages au moule représentent une obligation financière importante. Heureusement, c'est une obligation que vous pouvez éviter. Comment? Par un traitement approprié des moisissures. Ici, nous allons présenter quelques traitements de surface d'outils de moulage par injection.
Pourquoi le traitement des moules à injection est-il important ?
La réponse la plus simple à cette question est peut-être de réduire les coûts. Cela a du sens si l'on considère le coût des moules. Un seul moule peut coûter des centaines de milliers de dollars, et ce n'est que le coût d'achat. Ce coût peut et doit être évité, et le traitement de surface des outils de moulage par injection est un moyen d'y parvenir.
Les moules ne sont pas du tout faibles, généralement en acier trempé. Cependant, le processus d'injection de résines fondues à des températures et des pressions élevées finira par avoir des conséquences néfastes sur les moules d'injection. De nombreux matériaux thermoplastiques utilisés aujourd'hui sont également abrasifs et provoquent une abrasion et un frottement sur les surfaces du moule après de nombreux cycles d'injection. Il existe également un risque de corrosion et de fatigue après une utilisation continue.
Bien que le résultat final soit généralement un endommagement de l'outil de moulage, la qualité du travail produit par les moules affectés par la corrosion, le frottement, l'usure et l'abrasion est généralement inférieure à celle requise. L'écoulement du moule peut également souffrir sans un traitement approprié du moule. Tous ces éléments peuvent faire fuir les clients et les reconquérir est généralement difficile, même après le remplacement du moule. Cela met davantage l'accent sur la raison pour laquelle les mouleurs à injection doivent être formés au traitement des moules et aux différents outils de finition des moules.
Types de traitement de surface pour les outils de moulage par injection plastique
L'acier est dur, oui. Mais est-il assez difficile de protéger les moules à injection de l'usure après une exposition prolongée à de la résine fondue à haute température et pression ? Non, pas tout à fait. Différents traitements de surface peuvent offrir la protection supplémentaire indispensable. Nous en examinerons brièvement quelques-unes ci-dessous.
Placage
Le placage est l'une des solutions les plus courantes pour mouler l'usure, la déchirure et les abrasions. Il existe deux formes principales de placage - électrolytique et autocatalytique. La différence entre les deux provient de la présence ou non de courants électriques. Le placage électrolytique nécessite un courant électrique, contrairement au placage autocatalytique.
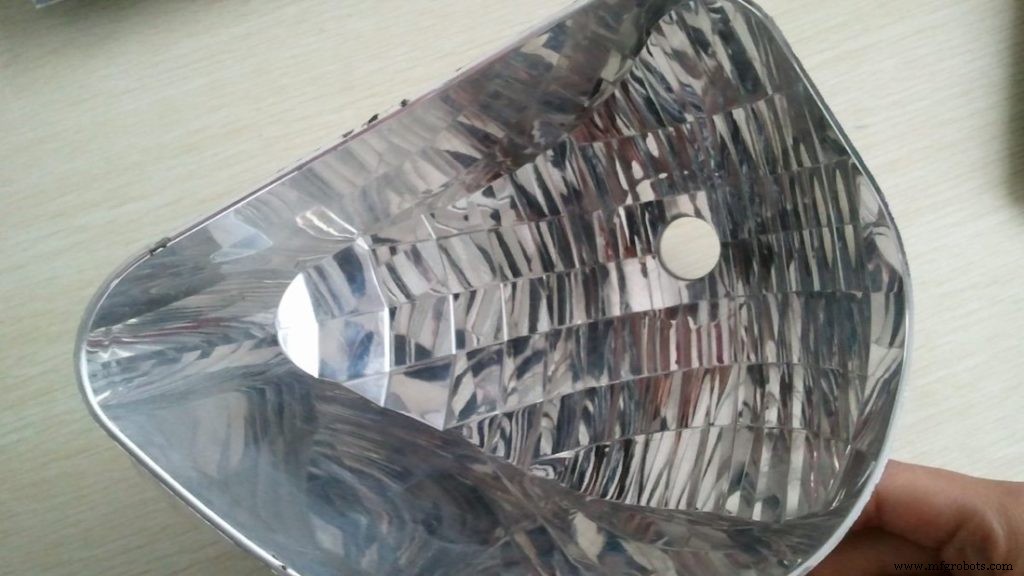
Le chromage et le nickelage autocatalytique sont les deux formes de placage les plus courantes pour les moules. Le chromage consiste à déposer par galvanoplastie une fine couche de chrome sur le moule. Le produit du chromage est le chrome. Contrairement au nickelage, le chromage nécessite l'utilisation d'une anode conforme qui pénètre dans la cavité du moule. Cela signifie que le chromage prendra plus de temps, en particulier pour les moules détaillés, et, par implication, peut coûter plus cher. Un autre inconvénient ici est que le chromage trop long peut empêcher un placage uniforme, en particulier dans les moules détaillés. La texture de la surface du moule est plus dure avec le chrome, ce qui les rend plus résistants à la rouille. Le chromage est généralement lisse et très fonctionnel.
Le nickelage autocatalytique est l'un des traitements de surface les plus polyvalents de tous les moules à injection. Le placage autocatalytique repose sur des réactions chimiques plutôt que sur le courant électrique. Il offre une protection contre la corrosion, les problèmes de lubrification, l'abrasion et même les attaques chimiques. Cette forme de placage ne nécessite pas d'anode, ce qui implique un placage plus uniforme que le chromage. Le nickel noir est l'un des nickelages autocatalytiques les plus identifiables.
Qu'il s'agisse de chrome ou de nickel, une chose que le placage assure est la durabilité. Le traitement des moules avec placage garantira que les moules durent pendant plus de cycles d'injection sans compromettre la qualité du produit.
Nitruration
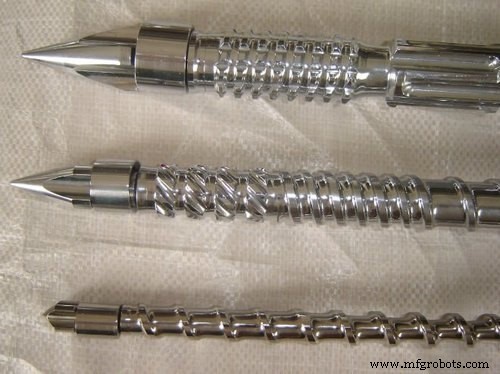
La nitruration est un processus de diffusion thermochimique. Avec la carburation, cette forme de traitement de moule est la pratique de traitement thermique la plus courante. Ce processus permet la diffusion d'atomes d'azote dans la surface du moule à basse température sans aucun changement dans la structure de phase de la surface du moule. Aucun changement de phase signifie une distorsion minimale de l'acier du moule.
Il existe différentes formes de nitruration, y compris la nitruration ionique, la nitruration en pack, la nitruration en bain de sel et la nitruration gazeuse, toutes dans le même but d'augmenter la texture et les performances de la surface de moulage.
Pour ce processus, les pièces du moule sont exposées à de l'azote actif entre 925 et 985F. Un bon contrôle de la température est essentiel au processus de nitruration pour une distorsion minimale de l'acier. De plus, les composants du moule à injection qui sont traités par nitruration sont généralement détendus avant l'usinage final pour garantir des changements de taille négligeables.
Au fil du temps, le processus de nitruration a été développé et amélioré, passant des techniques traditionnelles de nitruration gazeuse à une nitruration plus contrôlée utilisant un ordinateur pour contrôler les paramètres de nitruration.
La nitruration conduit au développement d'un boîtier moulé dur, mais les pièces qui doivent rester molles peuvent être masquées lors du processus de nitruration. Le boîtier moulé rigide le rendra résistant à l'usure et à l'abrasion.
Carburation
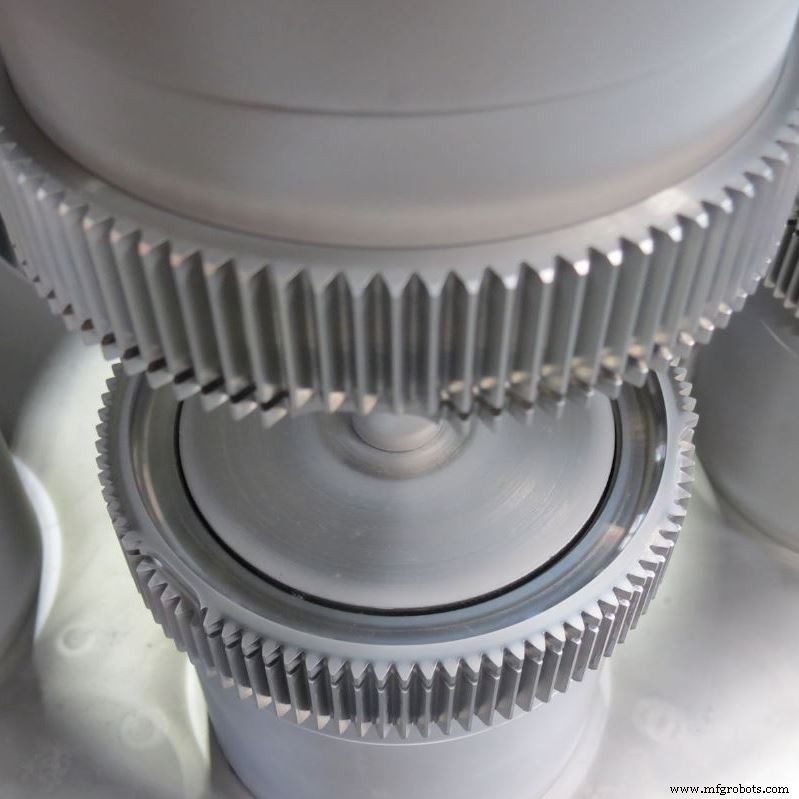
Une autre pratique de traitement des moisissures qui nécessite de la chaleur est la carburation. Ce processus est similaire à la nitruration. La principale différence est la diffusion des atomes de carbone dans la surface des composants du moule d'injection lors du traitement plutôt que des atomes d'azote lors de la nitruration.
La carburation conduit souvent à des moules résistants à l'usure et résistants. Ce procédé consiste à chauffer les composants du moule à injection dans un four à fosse. Ensuite, introduction des gaz de cémentation pour permettre la diffusion dans la surface du moule.
Comme pour la nitruration, il existe différentes formes de processus de cémentation, notamment la cémentation gazeuse, la cémentation sous vide, la cémentation par plasma pulsé et la cémentation à haute température.
La carburation est un meilleur traitement de surface de l'outil de moulage par injection que la nitruration pour les composants de moule plus lourds et plus chargés, comme les engrenages et les roulements de grande taille. Contrairement à la nitruration, la cémentation nécessite un traitement post-thermique. Cela est dû à la température nettement plus élevée à laquelle la carburation se produit.
Revêtement PVD
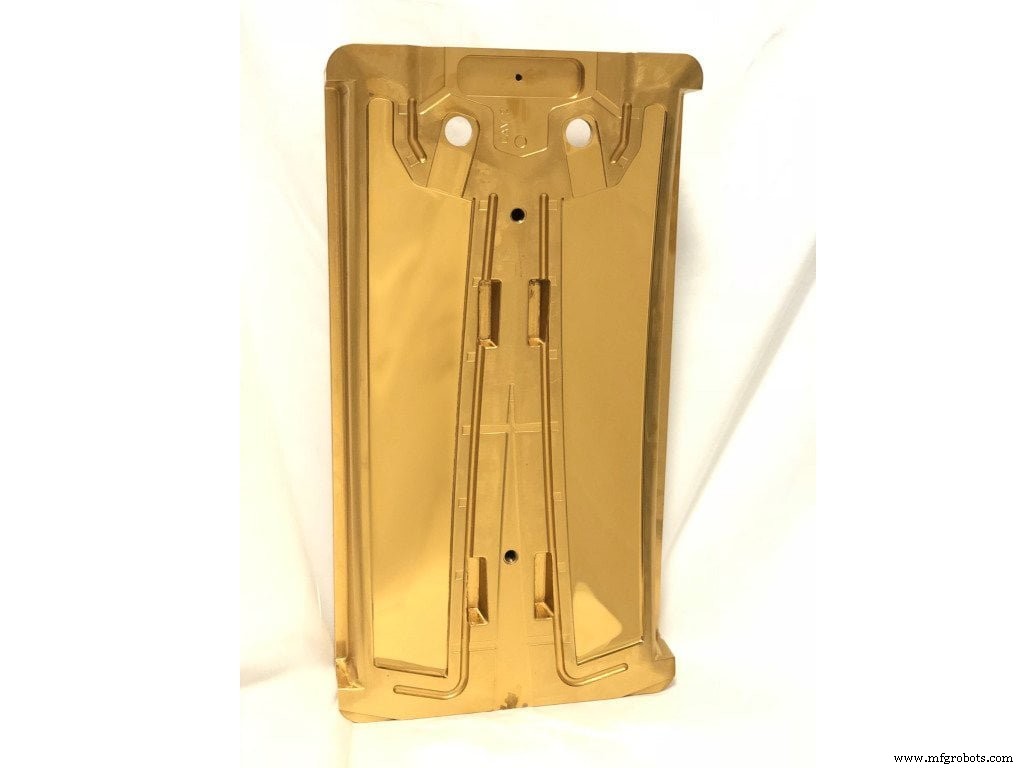
PVD est l'acronyme de Physical Vapor Deposition. Également connu sous le nom de revêtement en couche mince, ce type de traitement de moule est un processus dans lequel un matériau solide, appelé source, est vaporisé sous vide et déposé sur la surface d'un composant de moule. La source est généralement une tige en céramique ou en métal.
Les processus de revêtement PVD les plus courants sont l'évaporation et la pulvérisation. Avec l'évaporation, le processus utilise un arc cathodique ou une source de faisceau d'électrons. D'autre part, la pulvérisation implique l'utilisation de sources magnétiques améliorées.
Le principe de ce processus est la formation de surfaces de moule à haute densité en raison du bombardement du composant du moule avec des ions énergétiques chargés positivement. Le matériau source est conçu pour pulvériser dans le plasma, formant des liaisons solides avec la surface du moule, formant une fine couche adhésive.
Il est également possible de créer des compositions de revêtement composites en introduisant des gaz réactifs, comme l'oxygène et l'azote, dans la chambre à vide pendant le bombardement.
Le revêtement PVD aidera à améliorer la résistance du moule. Du fait que les couches formées sont également très fines, le revêtement a peu d'impact sur les dimensions finales des composants du moule. Le traitement de surface des outils de moulage par injection PVD est l'un des plus acceptables dans l'industrie aujourd'hui ; cependant, son utilisation est réservée aux matériaux qui peuvent résister à la très haute température que ce processus implique. Ce processus n'est pas non plus idéal pour les moules très détaillés avec beaucoup de pièces cachées.
Le revêtement PVD peut être fonctionnel ou décoratif, selon que l'accent est mis sur l'amélioration des performances globales ou sur l'amélioration de l'esthétique, respectivement. Le nitrure de titane (TiN) est un exemple de revêtement PVD fonctionnel, tandis qu'un film à base de Zr est un exemple de revêtement PVD décoratif.
Revêtement CVD
CVD est l'acronyme de Chemical Vapor Deposition. Le principe de ce revêtement est similaire à celui du PVD, la principale différence étant l'utilisation d'une réaction chimique pour produire le film mince qui recouvre le moule dans le revêtement CVD.
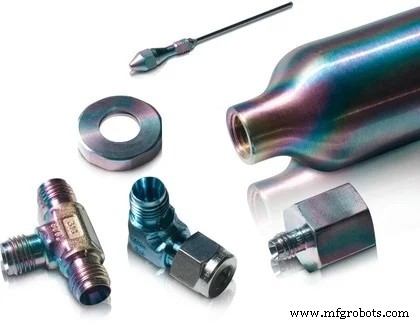
Le processus de revêtement CVD est généralement effectué dans un réacteur CVD. L'un des problèmes du revêtement PVD est la température élevée à laquelle il est réalisé; Eh bien, le revêtement CVD est effectué à des températures encore plus élevées (environ 1925F). Ceci, comme vous pouvez l'imaginer, limite ce traitement de moule aux composants qui peuvent résister à des températures élevées.
Le film mince formé dans ce processus de revêtement est dû aux réactions entre les phases gazeuses et la surface chaude du moule dans les réacteurs.
Comme le PVD, le revêtement CVD assure un moule robuste, résistant à l'usure et à l'abrasion. Le film formé est également très fin, généralement de l'ordre du nanomètre, ce qui garantit que les dimensions finales du moule ne sont pas modifiées de manière significative.
Le revêtement CVD est utile pour une large gamme de composants de moules, en particulier ceux qui impliquent de nombreux glissements. Cependant, en raison de la nature dépendante du gaz de ce processus, le masquage de certaines zones peut être difficile, voire impossible.
Il convient de noter que bon nombre de ces processus sont dûment pris en compte lors de l'outillage rapide. Et vous pouvez trouver les meilleurs services d'outillage rapide chez RapidDirect.
Considérations pour le traitement des moisissures
Il y a plusieurs facteurs à considérer avant d'appliquer les différents outils de finition de moule. En voici quelques-uns.
- Le type de composant ou de pièce de moule qui subit le processus de traitement du moule doit être bien examiné. Ne choisissez pas n'importe quel outil de finition de moule. Considérez plutôt la tolérance à la chaleur du composant du moule, car différents processus auront des impacts thermiques différents sur la surface du moule. De plus, la marge de manœuvre que vous pouvez vous permettre avec les changements de dimension finaux devrait entrer en jeu. Certains composants de moule nécessitent des films extrêmement fins tandis que d'autres peuvent recevoir des revêtements relativement épais.
- Le prix du traitement des moisissures est un autre facteur essentiel à prendre en compte. Les meilleurs processus coûtent généralement plus cher, mais il y a des moments où il est plus économique d'opter pour des options moins chères, en particulier lorsque le moule à injection n'est destiné qu'à une utilisation sporadique.
- Vous devez également vous assurer de la compatibilité du processus avec votre moule. Par exemple, certains procédés permettent le masquage; d'autres non. Ainsi, si le masquage de certains composants du moule est essentiel à votre traitement de moule, vous devez sélectionner des processus qui permettent le masquage. Le même principe s'applique à l'uniformité du revêtement.
Services de moulage par injection RapidDirect
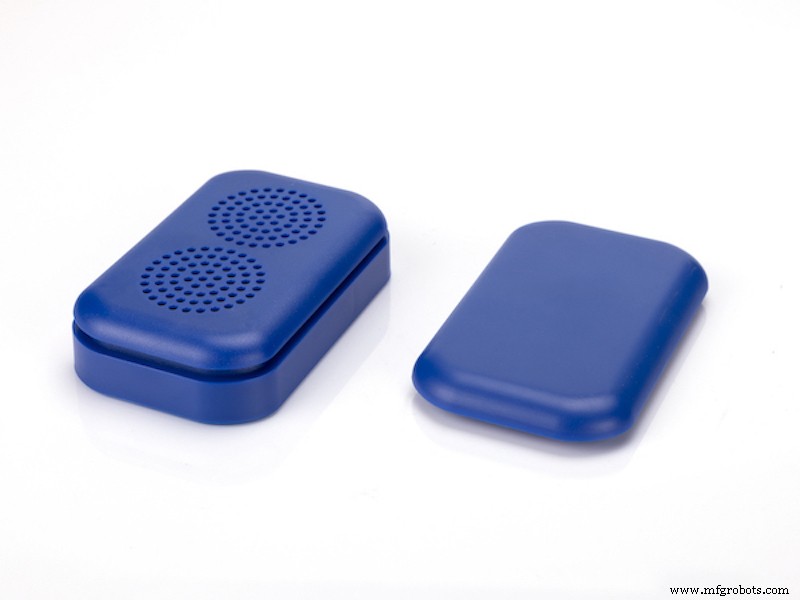
Chez RapidDirect, nous avons des tonnes d'expérience de notre côté dans la conception de moules à injection et le traitement de moules. Notre équipe d'experts est disponible et prête à vous aider avec tous vos problèmes de moulage par injection. Il y a plus. Nous offrons des services de moulage de la plus haute qualité, vous assurant que vous n'avez pas à vous soucier du bon traitement de surface, tout en maximisant le potentiel et la durée de vie de vos composants de moule.
Matériau composite
- Comment choisir les bons pieds de nivellement
- Comment choisir les bonnes glissières de tiroir
- 3 types d'ajustements et comment choisir le bon ?
- L'importance de la technique de moulage par injection
- Qu'est-ce qu'un compacteur et comment choisir le bon ?
- Acheter une grue :comment choisir la bonne
- Comment choisir la bonne fraise et la bonne programmation pour CNC ?
- Explication des termes courants du moulage par injection :multi-empreintes, famille, inserts, etc.
- Comment fonctionnent les ateliers d'usinage CNC et comment choisir le bon ?