La surveillance de l'état des machines maintient une usine en marche
En 1901, un brevet a été délivré à Ransom E. Olds pour l'idée d'une chaîne de montage en mouvement continu, qu'il a utilisée pour construire les premiers véhicules Oldsmobile. En 1913, Henry Ford améliore le concept en ajoutant des bandes transporteuses mobiles et avec ces deux innovations, le temps nécessaire pour assembler une voiture passe de 1½ journée à 1½ heure. L'usine d'assemblage moderne était née.
Au cours des quatre décennies suivantes, l'idée d'une chaîne de production mobile a été adoptée par de nombreuses industries, des radios aux rasoirs, des horloges aux berceaux, des clous aux journaux. Pendant la Seconde Guerre mondiale, les États-Unis ont construit 300 000 avions en utilisant des lignes de production mobiles. L'idée est devenue l'épine dorsale de la fabrication dans le monde entier et reste le principal moyen de fournir des produits aux marchés de masse.
Les outils et les machines utilisés pour effectuer les travaux d'assemblage sont la partie la plus critique de toute ligne. Dans les années 1950, la fiabilité des équipements d'usine devenait un élément important des opérations. Si une seule machine s'arrêtait de fonctionner, toute la ligne s'arrêterait jusqu'à ce que des réparations puissent être effectuées. L'inactivité des machines et des assembleurs a réduit l'efficacité et impacté les coûts. La maintenance est devenue importante.
Tout au long de la dernière moitié du 20e siècle, la plupart des opérations de maintenance en usine consistaient en une maintenance périodique programmée. Cela a amélioré la fiabilité et la durée de vie des machines, mais n'a rien fait pour aider les opérateurs de l'usine à prévoir et à éviter tout dysfonctionnement de l'équipement ou tout arrêt imprévu. Au cours des vingt dernières années, la surveillance de l'état des machines est devenue une partie importante des opérations en usine. Parfois appelées Smart Factory, Industrial IoT (IIoT) ou Industry 4.0, les usines ajoutent des capteurs et des systèmes analytiques qui surveillent la santé de l'équipement de fabrication.
La surveillance de l'état consiste à équiper l'équipement de capteurs capables d'identifier des changements paramétriques significatifs indiquant une panne ou une panne imminente. Ces systèmes recherchent deux choses. Premièrement :la machine fonctionne-t-elle en dehors de ses paramètres de conception, nécessitant une réponse rapide ? Deuxièmement :quelles sont les tendances à long terme des paramètres critiques pour prédire quand la machine devra être entretenue, réparée ou remplacée.
Moteurs électriques d'usine
L'une des machines les plus omniprésentes dans les usines est le moteur électrique. On estime qu'il y a aujourd'hui 300 millions de moteurs en fonctionnement dans les usines de fabrication du monde entier. Ils fournissent le pouvoir de fabriquer, d'assembler et de déplacer des produits dans une usine. La panne d'un seul moteur peut entraîner l'arrêt brutal d'une chaîne de production, ce qui coûte 10 000 dollars de l'heure. Les capteurs et les analyses de surveillance de l'état donnent un avertissement précoce des problèmes. Le traitement rapide de ces problèmes entraîne une réduction des coûts de maintenance, moins de perturbations dans le flux de processus et une sécurité améliorée pour les opérateurs de l'équipement.
La santé de n'importe quel moteur peut être déterminée en surveillant trois paramètres de fonctionnement :
-
Vibration — mesurée avec un accéléromètre.
-
Température — mesurée avec un capteur de température de type contact.
-
Courant — mesuré avec un capteur de courant de type inductif ou shunt.

Les accéléromètres fournissent des données sur la santé mécanique du moteur. Les capteurs de température fournissent des données sur la santé mécanique et électrique, et les capteurs de courant examinent la santé électrique. Les capteurs peuvent également fournir des données sur l'état de l'équipement et des outils attachés au moteur.
Accéléromètres
Tous les moteurs rotatifs ont une armature qui est suspendue par des roulements et tourne à différentes vitesses. Les armatures sont équilibrées pour ne pas vibrer lors de la rotation. Cependant, une armature déséquilibrée ou endommagée crée des vibrations qui peuvent affecter les roulements. Si les vibrations sont à des fréquences de résonance d'autres équipements fixés au moteur, les dommages peuvent être graves et rapides. La fréquence de vibration d'un moteur coïncide avec le régime du moteur et varie généralement de quelques Hz à 4 kHz. Les accéléromètres sont adaptés pour mesurer ces vibrations.
Les accéléromètres sont également utilisés comme microphones de contact qui écoutent le bruit à haute fréquence (grincement) des roulements où la lubrification a été épuisée. Ces fréquences vont de 5kHz à 15kHz. Les accéléromètres piézoélectriques fonctionnent bien car ils ont une large réponse en fréquence qui couvre les deux plages de fréquences avec un seul appareil.
Généralement, une transformée de Fourier rapide (FFT) est utilisée pour analyser le signal. Les données FFT montrent chaque bande de fréquence de vibration et son intensité. La figure 2 indique les fréquences et amplitudes de vibration naturelles d'un moteur type.
Les nouveaux moteurs ont des fréquences de vibration naturelles qui sont enregistrées et utilisées comme référence pour les comparer aux données prises plus tard dans la vie du moteur. Si ces mesures restent dans la même plage que les données d'origine, le moteur est en bonne santé. Si les fréquences ou les intensités commencent à changer avec le temps, cela indique une usure de certaines parties du moteur et une panne peut être imminente. Les réparations peuvent donc être planifiées avant qu'une panne ne se produise. Cela élimine les arrêts de ligne catastrophiques et améliore l'efficacité de la fabrication.

La figure 3 montre le capteur de vibrations modèle 8911 de l'unité commerciale TE Connectivity Sensors. Il contient un accéléromètre piézoélectrique et un microcontrôleur qui effectue une conversion FFT dans un format dont les clients ont besoin. De plus, ce capteur est alimenté par batterie et transmet les données sans fil sur les fréquences LoRa. Cela élimine le câblage dur. Le capteur peut être facilement monté sur un moteur avec un adhésif, un goujon de montage ou une base magnétique. Sans câblage et montage simple, le capteur peut passer du prêt à l'emploi au fonctionnement complet en très peu de temps et à très faible coût.
Capteurs de température
Les deux parties d'un moteur les plus touchées par les températures élevées sont les roulements et les enroulements du stator. Pour être efficaces, les capteurs qui mesurent ces paramètres doivent être en contact physique intime avec les pièces du moteur d'intérêt, de sorte que des conceptions uniques sont généralement nécessaires pour les applications motrices.
En fonctionnement, les roulements du moteur tournent généralement entre 60° et 70°C (140° et 160°F). Lorsqu'ils sont correctement chargés et lubrifiés, les roulements peuvent avoir une durée de vie extrêmement longue. Le problème le plus courant survient lorsque les lubrifiants disparaissent à cause de fuites ou échouent en raison d'une surchauffe ambiante. Ces modes de défaillance peuvent se produire sur des périodes de fonctionnement assez longues - des milliers d'heures. À mesure que le lubrifiant s'épuise, la température du roulement commence à augmenter et peut être facilement suivie à l'aide d'un capteur de température et d'un logiciel d'analyse.
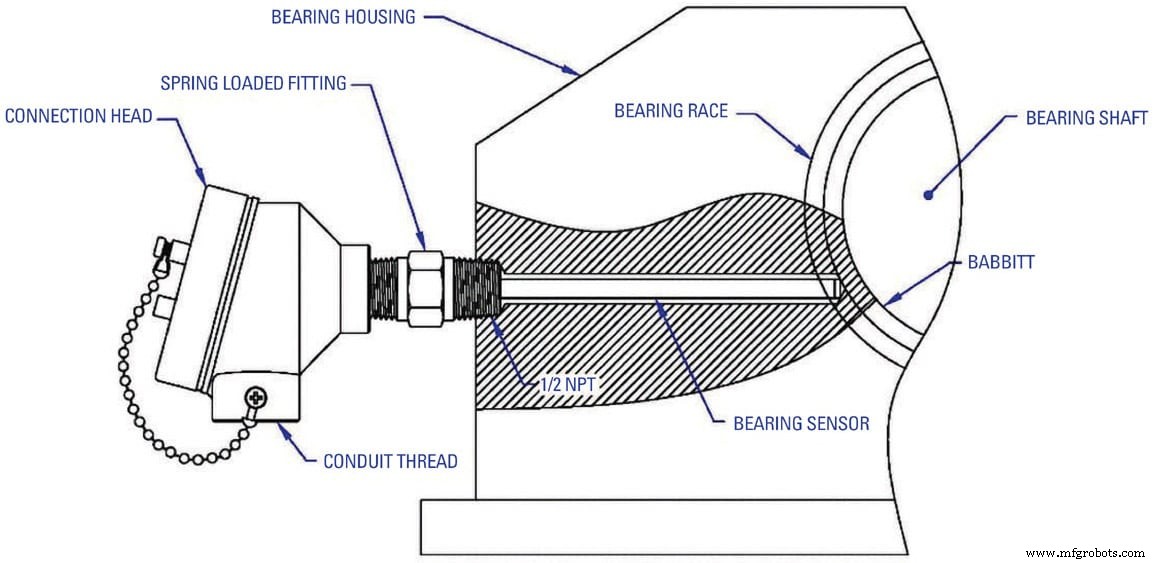
La figure 4 montre un capteur de température de type NTC ou RTD à ressort conçu pour être en contact direct avec une bague de roulement extérieure. Ce montage fournit les mesures de température les plus précises. Le boîtier de roulement doit avoir des caractéristiques conçues pour accueillir le capteur de température et fournir un accès proche au roulement.
Des capteurs de température sont également utilisés pour mesurer la température des enroulements électriques du stator. Ce sont les bobines qui génèrent les champs magnétiques pour propulser la rotation de l'armature. Si ces enroulements sont endommagés par un impact ou par la corrosion, la résistance du fil augmente et leur capacité à conduire le courant diminue. Cela provoque la chaleur des fils affectés. Ils peuvent atteindre des températures qui font fondre l'isolant et même provoquer un incendie.

Les figures 5a et 5b montrent des capteurs de température (unité commerciale TE Connectivity Sensors) intégrés dans les enroulements du stator d'un moteur. Les capteurs deviennent une partie permanente de l'appareil.
Comme pour les capteurs de vibration, la température de fonctionnement initiale est mesurée et enregistrée. Au fil du temps, les températures sont prises périodiquement et comparées à la ligne de base. Si les températures commencent à s'écarter de la normale, cela indique des problèmes mécaniques pour les roulements ou des problèmes électriques pour les enroulements du stator. Encore une fois, la maintenance peut être planifiée avant qu'une panne majeure ne se produise, évitant ainsi un arrêt inattendu de la ligne.
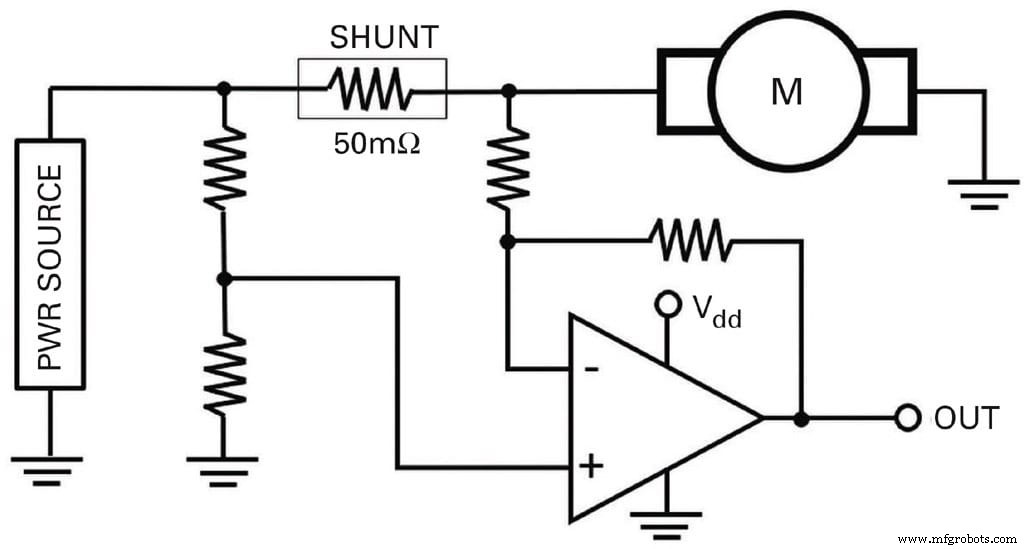
Capteurs de courant
Alors que les capteurs de vibration et de température peuvent signaler la santé physique d'un moteur, un capteur de courant peut vérifier sa santé électrique. Les capteurs de courant sont disponibles en deux configurations de base :conceptions shunt ou inductives. Chacun a ses avantages et ses inconvénients. La quantité de courant qu'un moteur consomme est affectée par de nombreux facteurs :la tension appliquée, la vitesse du moteur, la charge sur l'arbre du moteur et l'état des balais d'induit. Les courants hors plage peuvent signaler des problèmes de tension d'alimentation, des courts-circuits dans les enroulements du stator ou de l'induit, des balais usés ou des problèmes avec l'outillage attaché.

Un capteur de courant shunt est une résistance de puissance de très faible valeur placée en série avec la ligne d'alimentation électrique du moteur. La tension développée aux bornes de la résistance est proportionnelle au courant qui la traverse. En utilisant la loi d'Ohm (I =E/R) et connaissant les valeurs de tension et de résistance, le courant peut être calculé. Les shunts sont utilisés lorsqu'une très grande précision est requise ou pour les moteurs sans balais à haute fréquence. La figure 6 montre le schéma d'un capteur shunt.
Les capteurs de courant inductifs utilisent un anneau à haute permittivité autour du fil d'alimentation. Le courant traversant le fil induit un champ magnétique dans l'anneau (Bin). Un capteur à effet Hall intégré dans l'anneau mesure le champ magnétique et, à travers un amplificateur et une bobine enroulés autour de l'anneau, induit un champ magnétique inverse (BF) pour contrer Bin. La tension requise pour créer le champ BF est le signal de sortie. L'effet net des deux champs magnétiques apparaîtra comme un champ nul au niveau du capteur Hall. Plus le flux de courant dans le câble d'alimentation est élevé, plus la tension BF doit être élevée. (Voir Figure 7)
Au-delà du moteur

Souvent, l'équipement attaché au moteur peut également être surveillé pour la santé. La figure 8 montre un exemple de fraiseuse qui utilise une fraise rotative à plusieurs cannelures pour usiner une surface plane en une pièce à usiner. L'état de l'outil de coupe rotatif est très important pour la qualité de l'opération de coupe. Plus les cannelures de la fraise sont tranchantes, plus la coupe est précise et meilleure est la surface du travail fini. Au fur et à mesure que chaque cannelure effectue une coupe, le courant du moteur augmente pour fournir la puissance nécessaire. Les flûtes tranchantes nécessitent moins de puissance pour couper le métal. Les flûtes émoussées nécessitent plus de puissance.

En surveillant le courant du moteur de cette fraiseuse, il est possible de déterminer lesquelles des cannelures de l'outil de coupe sont tranchantes et lesquelles sont émoussées et doivent être affûtées.
Les contributions de la surveillance d'état à l'IIoT
Depuis l'invention de la chaîne de production et la révolution industrielle qu'elle a créée, de nombreuses innovations techniques ont fait progresser la fabrication. Les usines ont connu des gains de productivité moyens de 2,8 % par an au cours des 70 dernières années. Des technologies telles que les outils électriques, le moulage par injection, les équipements pick &place, les tests automatiques et la robotique y ont tous contribué. Aujourd'hui, la surveillance de l'état des machines s'ajoute à l'ensemble. Une surveillance de l'état réussie commence par des capteurs situés sur les machines de l'usine qui communiquent en permanence des données sur leur état et leur fonctionnement. En utilisant des analyses en temps réel, les opérateurs d'usine peuvent identifier les points problématiques et planifier les réparations et la maintenance nécessaires sans attendre les pannes catastrophiques. Cela apportera des gains de productivité à la fabrication. Cependant, tout commence par des capteurs.
Cet article a été écrit par Pete Smith, Sr. Manager, Sales and Marketing Support, TE Connectivity Sensor Solutions — TES (Schaffhouse, Suisse/Berwyn, PA). Pour plus d'informations, contactez M. Smith à Cette adresse e-mail est protégée contre les robots spammeurs. Vous devez activer Javascript pour le voir. ou visitez ici .
Capteur
- Le marché de la surveillance des conditions atteindra 3,9 milliards de dollars d'ici 2025
- Comment la surveillance des conditions améliore un programme PdM
- Le produit SKF Machine Condition Advisor remporte un prix
- L'usine de moteurs Honda bénéficie de la surveillance des machines
- Le périphérique SKF permet le diagnostic de l'état de la machine
- B&R présentera sa solution de maintenance conditionnelle à Agritechnica
- Surveillance de la santé des machines de l'usine
- Les pièges de la surveillance de l'état et le potentiel de maintenance en usine
- Suivi de l'état de votre équipement