Gear Manufacturing 101 :Un guide sur les processus de production d'engrenages
Le concept d'engrenages existe depuis un certain temps car ils font partie des composants mécaniques les plus anciens qui sont toujours d'actualité aujourd'hui. Que ce soit l'industrie automobile, le secteur aérospatial, n'importe quelle machinerie industrielle ou quelque chose de simple comme une horloge. Les engrenages sont nécessaires partout et peut-être aimeriez-vous en savoir plus sur la fabrication d'engrenages.
Donc, la question est de savoir comment les engrenages sont fabriqués.
Préface :processus de fabrication d'engrenages
Il n'y a pas de processus unique pour la fabrication d'engrenages car ils nécessitent différents processus selon le type et l'application.
Généralement, les engrenages fonctionnent dans des conditions très difficiles car la transmission de puissance (le but réel de l'engrenage) a plusieurs exigences. Premièrement, les engrenages doivent être en parfait état. Ensuite, ils doivent toujours être fiables, avoir des contraintes résiduelles minimales et peu ou pas de risque de propagation de fissures.
Naturellement, toutes ces exigences sont extrêmement difficiles à remplir. Cependant, personne ne peut nier leur importance. C'est pourquoi la production d'engrenages est un domaine hautement spécialisé avec des tolérances limitées et une marge d'erreur.
Cet article vous ramènera aux bases de la fabrication d'engrenages concernant les matériaux courants pour les engrenages industriels, les processus de préparation des engrenages et la manière dont les engrenages peuvent supporter toute cette charge sans tomber en panne.
Types d'engrenages courants et leurs applications
Avant de passer aux détails sur la taille des engrenages et les processus de fabrication, il est important de jeter un coup d'œil aux bases. Ce sont différents types d'engrenages et leur application et leurs avantages.
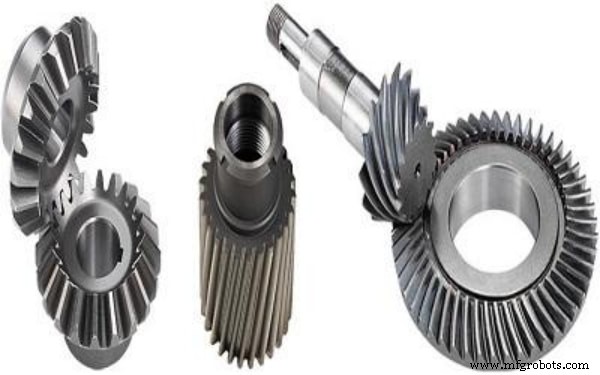
Votre application, vos paramètres de performance et de nombreux autres facteurs jouent un rôle important dans le type d'engrenages que vous utilisez. Il existe plusieurs façons de caractériser le type d'engrenage, mais la meilleure et la plus pertinente du point de vue de la fabrication d'engrenages est le profil de leurs dents.
Voici les 5 types d'engrenages que vous rencontrerez.
Pignons droits
Dessinez une image approximative de ce à quoi ressemble l'équipement dans votre esprit. Il y a de fortes chances que vous pensiez à un équipement avec des dents droites. C'est exactement à quoi ressemble un engrenage droit.
L'engrenage droit est le type d'engrenage le plus courant et a de multiples applications dans les centrales électriques, les composants aérospatiaux, les machines industrielles et bien plus encore. Les dents droites sont les plus simples à fabriquer et supportent des vitesses élevées et des charges élevées. Cependant, ils produisent beaucoup de bruit et ne conviennent pas aux applications nécessitant également un fonctionnement fluide.
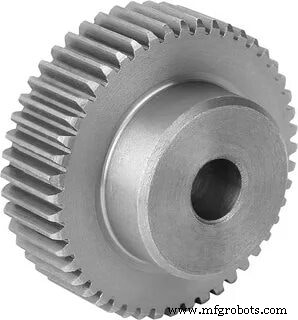
De plus, les engrenages droits peuvent s'accoupler avec d'autres engrenages du même type et des engrenages internes/externes. Vous trouverez des engrenages droits dans de nombreux mécanismes d'engrenage, comme une simple configuration à crémaillère/pignon ou un système d'engrenage planétaire.
Leur simplicité signifie qu'il est plus facile pour vous de faire. Par conséquent, il vous sera plus facile de maintenir la précision lors de la production d'engrenages. Les engrenages droits ont également peu ou pas de charge axiale, ils sont donc assez efficaces pour un train d'engrenages où vous souhaitez minimiser les pertes mécaniques.
Engrenages hélicoïdaux
Les engrenages hélicoïdaux sont assez similaires aux engrenages droits, mais ils sont livrés avec des dents qui sont tordues autour d'un corps cylindrique. Cette qualité leur permet de travailler facilement avec des arbres parallèles et non parallèles. Leur accouplement, cependant, ne fonctionne qu'avec d'autres engrenages hélicoïdaux du même angle d'hélice (l'angle de torsion du cylindre d'origine).
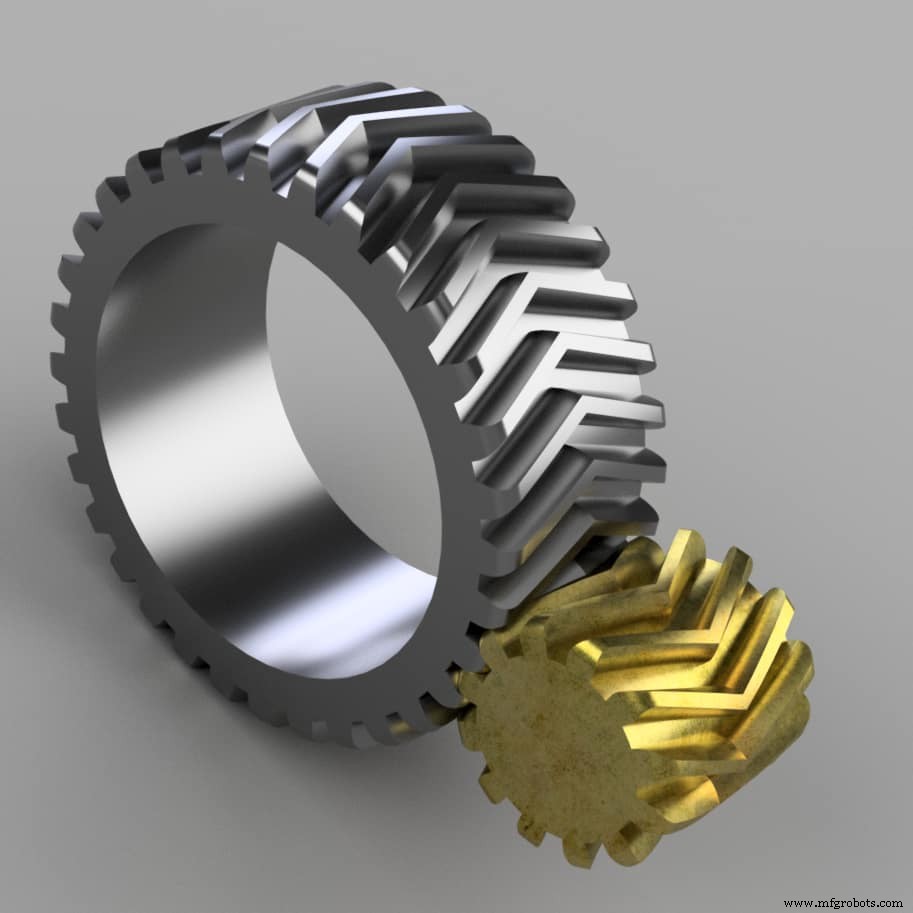
La plupart des applications des engrenages hélicoïdaux sont les mêmes que celles des engrenages droits. Cependant, les dents inclinées jouent un rôle énorme dans la réduction de la charge d'impact et la fluidité des opérations. Cela signifie également moins de bruit, mais au détriment de l'efficacité. Par rapport aux engrenages droits, un train d'engrenages hélicoïdaux aura plus de pertes et aura également besoin de paliers de butée en raison de sa forme.
Du point de vue de la fabrication, les engrenages hélicoïdaux sont plus résistants que les engrenages droits. Les angles d'hélice sont assez difficiles à reproduire avec une faible plage de tolérance acceptable. De plus, les coûts de fabrication puis l'ajout d'autres éléments axiaux les rendent adaptés à des opérations limitées.
Pignons coniques
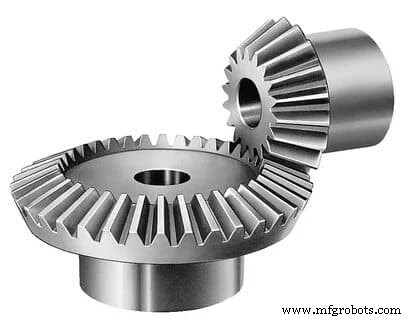
Les engrenages coniques ne sont pas vos engrenages cylindriques standard. Ils viennent sur une surface conique qui vous permet de changer le sens de la transmission sur des arbres qui se croisent. Généralement, les engrenages coniques fonctionnent avec 90 0 angles. Cependant, vous pouvez également les utiliser sur d'autres configurations.
Voici quelques types courants d'engrenages coniques que vous pouvez trouver dans une variété d'applications.
- Pignons coniques droits
- Pignons coniques en spirale
- Pignons d'onglet
- Pignons de couronne
- Engrenages hypoïdes
Engrenages à vis sans fin
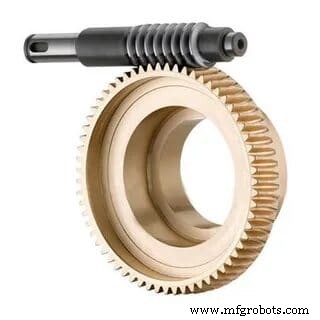
Le système d'engrenage à vis sans fin est une combinaison de deux composants. Une roue à vis sans fin et un engrenage en forme de vis. Ils sont principalement utilisés dans l'aérospatiale, les machines industrielles, les ascenseurs et la direction automobile.
La configuration de la roue à vis sans fin n'offre pas beaucoup de vitesse ou d'efficacité. Cependant, il offre une caractéristique unique requise pour les mécanismes autobloquants. Dans de nombreux cas, la vis sans fin peut faire tourner la roue, mais l'inverse ne peut pas se produire à cause des angles d'engrenage. De plus, une autre chose importante à noter est que les engrenages à vis sans fin ont beaucoup de friction et peuvent nécessiter une friction continue pour fonctionner correctement.
Crémaillère et pignon
Le système à crémaillère et pignon est une autre combinaison qui fonctionne principalement pour transférer le mouvement de rotation en linéaire et vice versa. Les dents d'engrenage peuvent s'accoupler avec des dents de type éperons et hélicoïdales, de sorte que vous pouvez travailler à la fois sur des axes parallèles et à un angle. Certaines des applications les plus courantes de ce système sont dans les systèmes automobiles, les balances et autres systèmes similaires.
Matériaux utilisés pour produire les engrenages
Il n'y a aucune restriction matérielle en ce qui concerne les engrenages. Les premiers étaient en bois et vous pouvez trouver différents engrenages en matériaux dans l'industrie. Des engrenages à grande échelle en acier ou en fer aux petits engrenages en plastique dans les jouets. Les combinaisons de matériaux sont infinies.
Néanmoins, les éléments suivants sont les plus couramment utilisés dans les processus de fabrication et de formage des engrenages :
- Fonte
- Acier
- Bronze
- Plastiques
Les engrenages ont des critères très spécifiques pour la sélection des matériaux. Selon l'application, le matériau que vous choisissez doit avoir la résistance à la traction et l'endurance appropriées.
De plus, le coefficient de frottement est une autre considération car les engrenages ont besoin d'un contact constant. Enfin, vous devez également sélectionner des matériaux faciles à traiter. Un matériau solide avec une faible fabricabilité sera plus difficile à gérer car la fabrication d'engrenages nécessite une précision et une exactitude extrêmes.
Les matériaux susmentionnés présentent l'équilibre parfait de ces propriétés pour leurs applications. C'est pourquoi vous les verrez couramment dans la plupart des engrenages que vous rencontrerez.
RapidDirect peut offrir tous ces matériaux utilisés dans le processus de fabrication des engrenages. Téléchargez votre fichier de conception pour obtenir un devis pour votre projet d'équipement.
Processus de fabrication d'engrenages courants
La production d'engrenages est assez compliquée en raison de la précision qu'elle exige. Aujourd'hui, la fabrication d'engrenages est une industrie en soi qui s'appuie sur de multiples processus, à la fois traditionnels et modernes, pour assurer le bon équilibre entre coût, qualité et opérations.
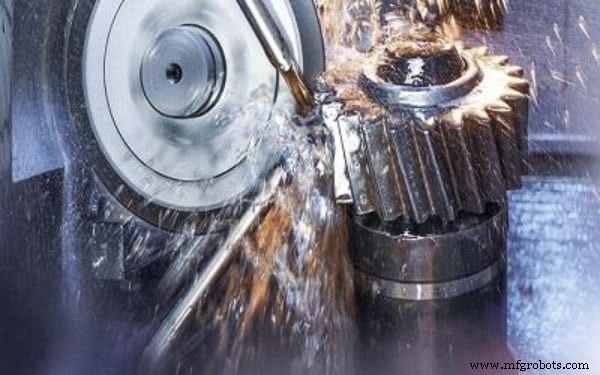
Voici une liste des processus courants de taillage et de fabrication d'engrenages, ainsi que leurs avantages et inconvénients apparents.
1 - Casting
Le moulage est un processus plus simple qui est principalement utilisé pour préparer des ébauches ou des cylindres pour les engrenages, tandis que les dents sont préparées par usinage. Cependant, il s'agit d'un processus de fabrication d'engrenages viable pour l'ensemble de nombreuses applications en raison de sa capacité de production de masse et de sa relative facilité.
Il existe cependant un domaine où la coulée est la méthode de fabrication la plus préférée dans l'industrie. C'est la production de très gros engrenages. Les méthodes d'usinage et autres méthodes de formation d'engrenages ne sont pas viables dans le cas de grands diamètres. Généralement, les engrenages plus gros sont presque toujours de type engrenage droit. Ainsi, leur relative simplicité fait du casting une très bonne option.
Parmi les types de méthodes de moulage les plus courants, le moulage en coquille, le moulage sous pression, le moulage au sable et le moulage en moule permanent sont les plus courants pour la production d'engrenages. D'autres méthodes ont une utilisation limitée dans certaines applications. Cependant, les éléments susmentionnés sont les plus courants dans l'industrie.
2 – Forger
Il s'agit d'un autre processus de formage qui peut vous donner à la fois des ébauches et des engrenages préparés en fonction de vos besoins. Le forgeage est tout à fait viable dans les cas où vous avez des engrenages relativement simples.
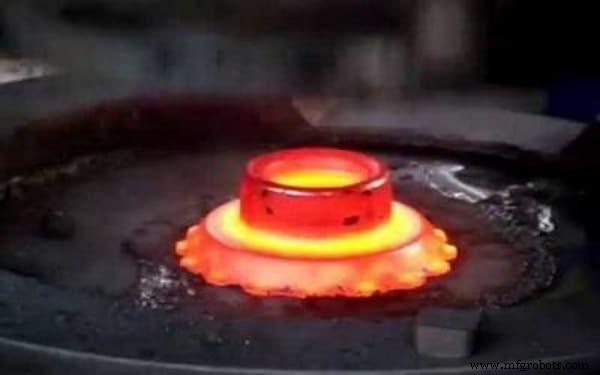
Théoriquement, le forgeage est un excellent processus de fabrication d'engrenages pour les applications lourdes pour une raison simple. Le forgeage nécessite un traitement thermique, ce qui signifie que l'engrenage résultant aurait de meilleures propriétés de fatigue. Cependant, la force énorme requise pour le processus de forgeage limite la taille et la finesse de ce processus.
Généralement, le forgeage fonctionne bien pour les engrenages de 6 à 10 pieds de diamètre. Selon le type de forgeage, par exemple le forgeage de précision, vous devrez peut-être ou non usiner les engrenages à la fin.
3 - Extrusion et étirage à froid
Il s'agit d'un autre processus de formation d'engrenages à la fois polyvalent et plus simple. En fait, l'extrusion nécessite moins d'outils, mais cela ne signifie pas que c'est le processus le plus économique.
L'extrusion, comme son nom l'indique, est le processus de passage d'un profilé métallique chauffé à travers une forme prédéterminée plus petite. En conséquence, vous obtenez une barre de la forme souhaitée avec une surface extérieure durcie et lisse.
Le processus d'étirage à froid est très similaire à l'extrusion. Il y a deux différences. L'extrusion pousse l'ébauche à travers une matrice, l'étirage la tire. L'autre différence est la température. L'étirage à froid ne chauffe pas la billette. Augmenter ainsi les propriétés mécaniques au détriment du coût.
4 - Métallurgie des poudres
La métallurgie des poudres est un procédé avancé qui a fait des progrès significatifs ces dernières années. Aujourd'hui, il est utilisé pour de multiples processus de fabrication, y compris la production d'engrenages.
Alors, comment fonctionne la métallurgie des poudres ? Vu de l'extérieur, c'est assez simple. Cependant, de nombreuses complexités sont impliquées.
Tout commence avec de la poudre métallique. La première étape consiste à prendre toute la poudre et à lui donner la forme finalisée que vous désirez. Une fois que vous avez terminé, l'étape suivante garantit que l'ensemble de la configuration est assez compact car il en résultera de meilleures propriétés mécaniques. Chauffez soigneusement l'ensemble de l'installation et vous avez terminé.
La métallurgie des poudres est extrêmement efficace, simple et viable pour de grandes quantités. Vous n'avez pas à vous soucier du post-traitement et le produit sera prêt à l'emploi. Cependant, les engrenages résultants ne peuvent pas supporter trop de charge et il existe également des limitations de taille.
De plus, le coût initial de toute installation de métallurgie des poudres est assez élevé, ce qui la rend non viable pour toute production à faible volume.
5 - Obturation
Le découpage est un processus très similaire à l'extrusion mais a des capacités tridimensionnelles limitées. Ce processus de formation d'engrenages utilise de la tôle pour créer la forme souhaitée à l'aide de plusieurs matrices. Vous pouvez produire différents types d'engrenages avec le processus de suppression. Cependant, les engrenages droits vous donnent les meilleurs résultats.
Aujourd'hui, le processus de découpage de la production d'engrenages est utilisé par plusieurs industries pour des applications légères. Par exemple, l'équipement de bureau, l'hydraulique, les petits dispositifs médicaux et d'autres applications nécessitant de faibles charges.
6 - Usinage d'engrenages
L'usinage est l'un des processus de fabrication d'engrenages les plus courants en raison de sa polyvalence. L'usinage traditionnel était assez courant pour la coupe et la fabrication d'engrenages, mais les progrès de l'usinage CNC ont propulsé sa popularité.
Les 4 méthodes de taille d'engrenage suivantes sont les plus courantes dans l'industrie.
Taillage
Le taillage utilise un dispositif de coupe conique appelé plaque de cuisson. La table de cuisson et la pièce à usiner tournent lorsque la table de cuisson tourne autour de l'ébauche d'engrenage. Jusqu'à présent, les engrenages droits et hélicoïdaux externes sont les seuls produits que vous pouvez créer à partir du taillage.
Le processus est assez polyvalent et rapide. Vous pouvez également augmenter vos taux de production en traitant plusieurs piles ensemble. Cependant, cela demande plus de compétences et de précision.
Mise en forme
Le façonnage est un processus avancé de coupe et de fabrication d'engrenages qui développe des engrenages que le taillage ne peut pas gérer. La fraise peut avoir n'importe quelle forme, comme un pignon, une crémaillère ou une forme à pointe unique. Il ressemble assez aux engrenages et fonctionne en coupant le blanc à la forme souhaitée. Vous pouvez créer des engrenages internes ou en grappe avec le processus de mise en forme.
Brocher
Le brochage est peut-être la méthode la plus rapide pour tailler les engrenages. Il s'appuie sur un outil multi-dents avec des fraises intégrées plus profondes que son prédécesseur. Cela se traduit par des coupes plus petites et incrémentielles qui sont plus faciles à réaliser et vous donnent rapidement la forme requise sans compromettre la précision.
Ce processus de fabrication d'engrenages est typique des engrenages internes, mais vous pouvez également l'utiliser pour fabriquer des dents externes. Pour cela, vous aurez besoin d'un outil spécialisé pour le brochage de pot qui vous permet de reproduire la même précision et efficacité.
Fraisage
Il s'agit d'une méthode de taille d'engrenage de base dans laquelle vous produisez des dents d'engrenage individuelles de manière séquentielle. Il est cependant assez polyvalent, surtout lorsqu'il s'agit d'une fraiseuse CNC. Bien que vous puissiez fabriquer n'importe quel type d'engrenage sur une fraiseuse, la précision de cette méthode laisse beaucoup à désirer. C'est pourquoi le fraisage n'est plus aussi courant qu'avant.
Cependant, les développements récents dans le domaine CNC et multi-axes ont changé la donne. La fabrication d'engrenages sur fraiseuses devient de plus en plus courante. Ainsi, les choses iront encore mieux avec le temps.
Post-traitement de fabrication d'engrenages
Selon la méthode de fabrication des engrenages que vous avez utilisée, vos engrenages auront besoin d'un post-traitement avant d'être prêts à 100 %. Ce post-traitement peut aller du traitement thermique pour améliorer les caractéristiques de fatigue à la correction dimensionnelle et à la finition de surface.
Voici les 5 processus de finition de surface les plus courants dans la production d'engrenages.
- Meulage : Comme son nom l'indique, le meulage est un processus de finition de surface courant qui vous donne une finition lisse sur toute la surface. Vous pouvez l'effectuer par intermittence ou en continu, et cela n'affectera pas les résultats.
- Rodage : Ce processus est destiné aux engrenages sensibles où vous avez besoin d'une précision extrême. Le rodage utilise de petites particules abrasives pour lisser une surface à des vitesses faibles ou moyennes.
- Affûtage : Il s'agit d'un autre processus courant qui polit la surface et la rend lisse. De plus, vous pouvez également corriger certaines erreurs mineures dans la géométrie de vos dents.
- Rasage : Ce processus élimine les couches extrêmement fines de la surface pour obtenir un profil lisse. Le rasage est généralement coûteux, il est donc rarement utilisé dans la production d'engrenages.
- Brunissage : Essentiellement, le brunissage est le processus d'utilisation de la compression pour lisser la surface.
Approchez RapidDirect pour les meilleurs services de fabrication d'engrenages
La fabrication d'engrenages est un domaine hautement spécialisé qui nécessite une précision et une exactitude extrêmes. Les engrenages sont un élément essentiel de tout système mécanique et même le plus petit défaut de fabrication peut avoir de nombreuses conséquences désastreuses. Par conséquent, vous devez faire attention au service que vous sélectionnez.
RapidDirect est un service certifié ISO avec l'équipe la plus expérimentée qui offre les meilleures performances au prix le plus compétitif. Nous offrons des services de pointe qui vous offrent le meilleur en matière de fabrication d'engrenages.
Des grands engrenages pour les machines industrielles aux plus petits composants pour toute application de niche, RapidDirect offre la bonne combinaison de compétences, d'expérience et de qualité dont vous avez besoin. Contactez-nous dès aujourd'hui et obtenez un devis initial en quelques heures.
commande numérique par ordinateur
- Fabrication vs production :en quoi ces processus diffèrent
- Processus de fabrication d'assemblage ou de formage :quelle est la différence ?
- La robotique et l'avenir de la production et du travail
- L'importance de la maintenance des équipements dans la fabrication
- Quels sont les processus de fabrication importants suivis dans différentes industries ? – II
- Quels sont les processus de fabrication importants suivis dans différentes industries ?
- 3 procédés de finition innovants utilisés dans la fabrication d'engrenages
- L'utilisation croissante de l'automatisation dans la fabrication
- L'impact de la fabrication additive sur la production industrielle