Obtenir de meilleurs résultats de fabrication additive dans la conception générative
Lire cet article en :Deutsch (Allemand)
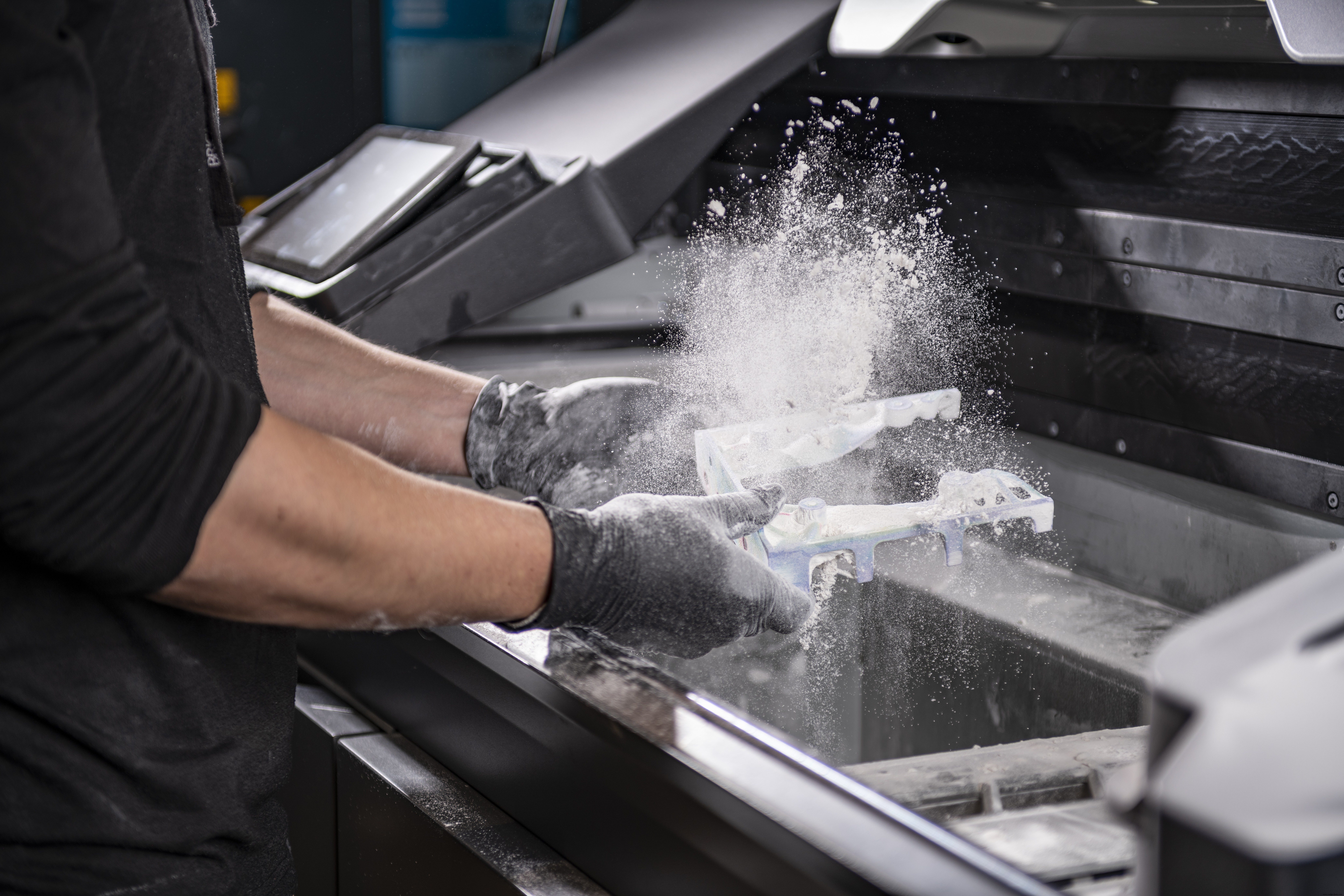
Dans le cadre de la mise à jour de décembre 2020 de Fusion 360, nous avons livré un cadeau caché juste à temps pour les fêtes :une nouvelle méthode pour générer des résultats de fabrication additive. En interne, nous appelons ce projet Additive 2.0, et il fait partie de notre aperçu Experimental Generative Solvers and Features. Cette nouvelle méthode devrait grandement améliorer la qualité de la forme et l'imprimabilité des résultats par rapport à ce que vous voyiez auparavant dans la conception générative. C'était un cadeau que beaucoup d'entre nous attendaient avec impatience, et mon équipe et moi aimerions « déballer » tout ce que nous avons livré.
Utilisation du nouvel algorithme Additive 2.0
Tout d'abord, vous devez activer notre aperçu des solveurs génératifs expérimentaux et des fonctionnalités à partir de vos préférences utilisateur.
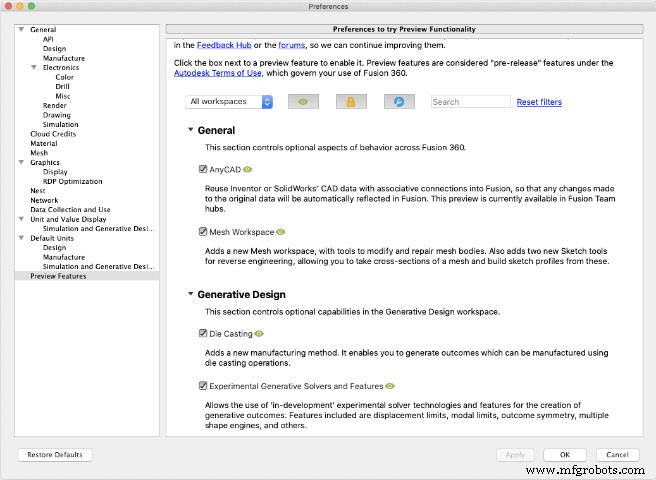
Avec l'aperçu activé, vous devrez activer les résultats alternatifs dans les paramètres de l'étude. À partir de là, configurez simplement votre étude comme d'habitude. Activez la contrainte de fabrication additive dans la boîte de dialogue Contraintes de fabrication, choisissez les orientations d'impression souhaitées et laissez nos solveurs s'occuper du reste.
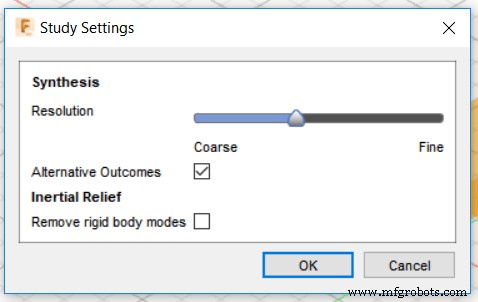
Une fois dans Explore, pour chaque ensemble de résultats additifs (où un ensemble équivaut à un matériau et une direction donnés), Additive 2.0 générera le deuxième résultat de chaque ensemble. Astuce rapide :la façon la plus simple de voir cela est de passer à la vue des propriétés, d'isoler la méthode de fabrication additive et de définir le menu déroulant Trier par sur Matériau.
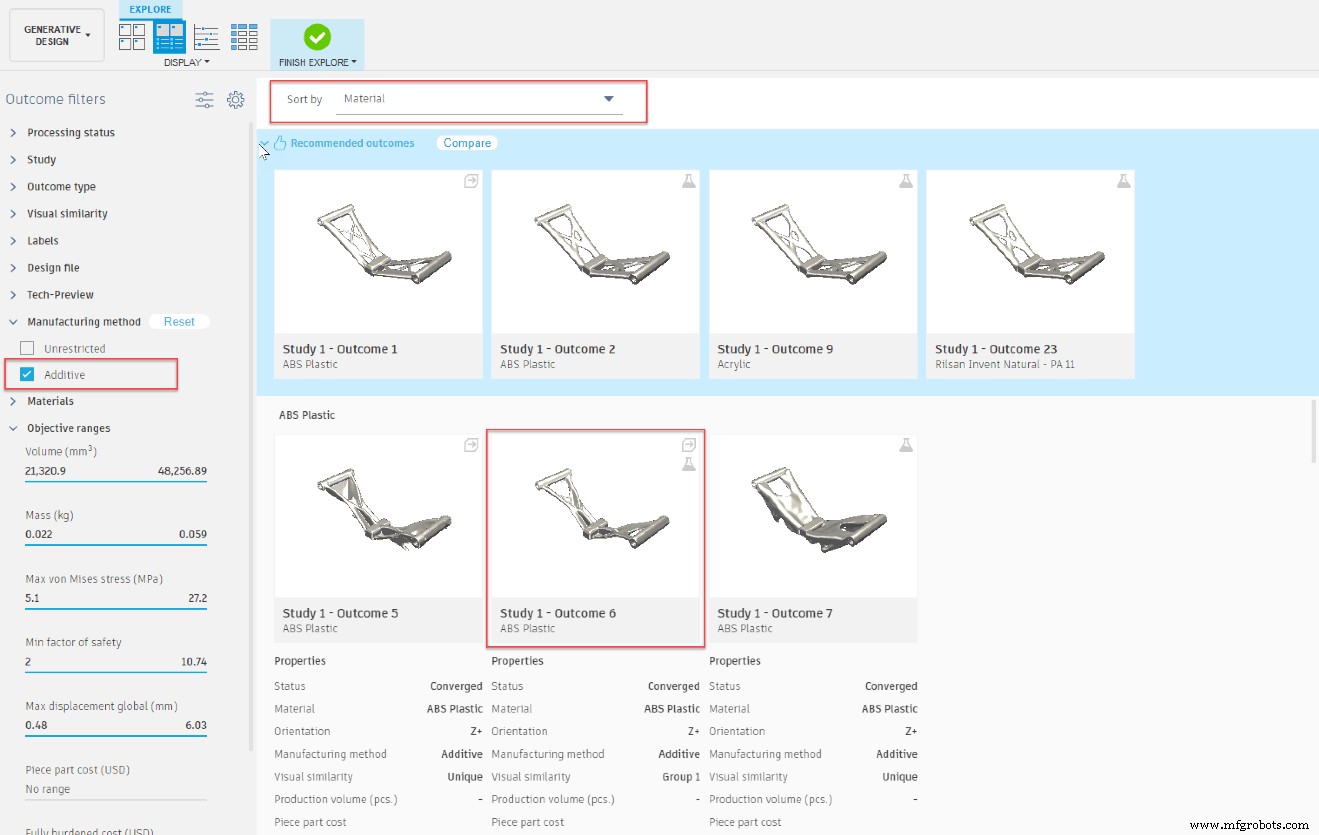
En quoi Additive 2.0 est-il meilleur ?
Notre approche initiale pour générer des résultats additifs laissait beaucoup à désirer en termes de qualité de forme dans de nombreux scénarios (beaucoup d'entre vous nous l'ont dit, et nous avons écouté !). Il était courant de voir des résultats avec des marches d'escalier prononcées et d'autres artefacts alors que nous essayions de répondre aux exigences de surplomb et d'être entièrement autonomes. Grâce à notre nouvelle approche, nos solveurs réussissent mieux à répondre aux exigences d'épaisseur minimale, à équilibrer la masse de conception et à minimiser le matériau de support. Cette nouvelle approche ne sacrifiera pas la qualité de la forme pour être entièrement autoportante.
Examinons quelques exemples qui démontrent l'impact de ces améliorations sur les résultats que nous créons.
Notre premier exemple est la configuration générative simple illustrée ci-dessous (les charges et les contraintes sont masquées). Nous avons l'intention de fabriquer cette pièce dans l'orientation illustrée à la figure 1 (ci-dessous), en remplaçant l'obstacle rouge par la plaque de construction.
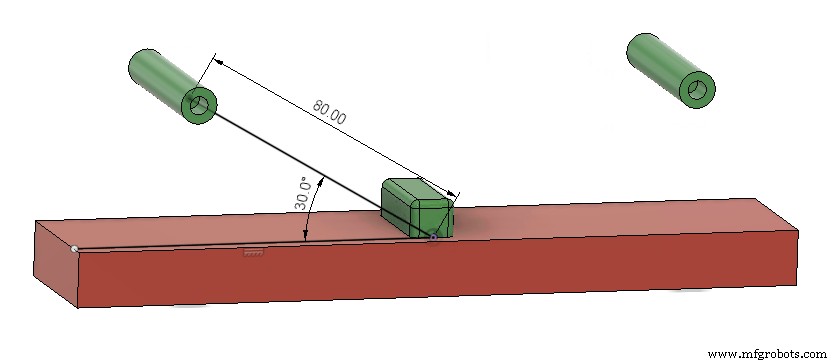
Cette configuration produit un résultat sans contrainte, comme le montre la figure 2 (ci-dessous), qui est difficile à fabriquer pour diverses raisons. Tout d'abord, une grande zone sous la géométrie de la pièce nécessite des structures de support (régions surlignées en rouge dans la seconde moitié de la figure). De plus, les éléments minces près du centre de la pièce sont fragiles et peuvent se casser lors du retrait du support. Bien que cette conception puisse être fabriquée de manière additive, elle est loin d'être optimisée.
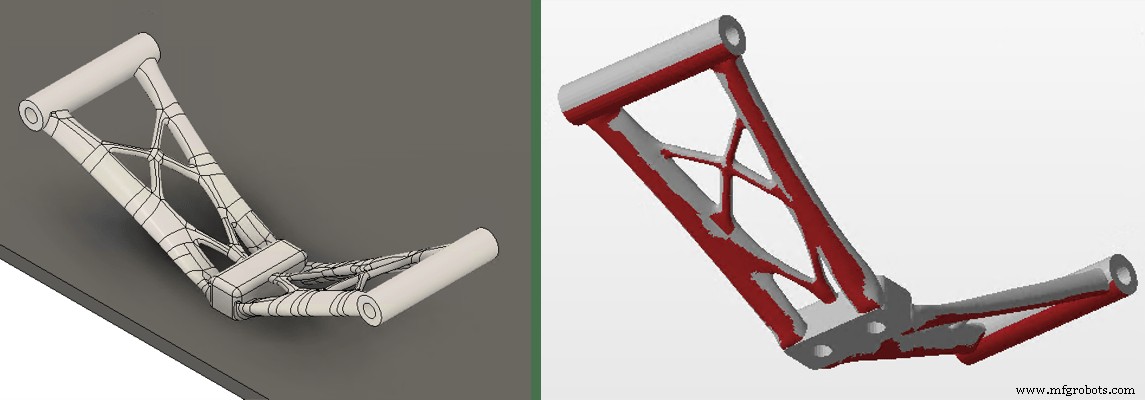
Lorsque nous commençons à regarder Additive 2.0 côte à côte avec nos contraintes additives existantes (Additive 1.0), les différences deviennent évidentes, comme le montre la figure 3 (ci-dessous). Dans les deux cas, nous avons configuré la contrainte additive avec un angle de porte-à-faux de 45 degrés et une épaisseur minimale de 3 mm.
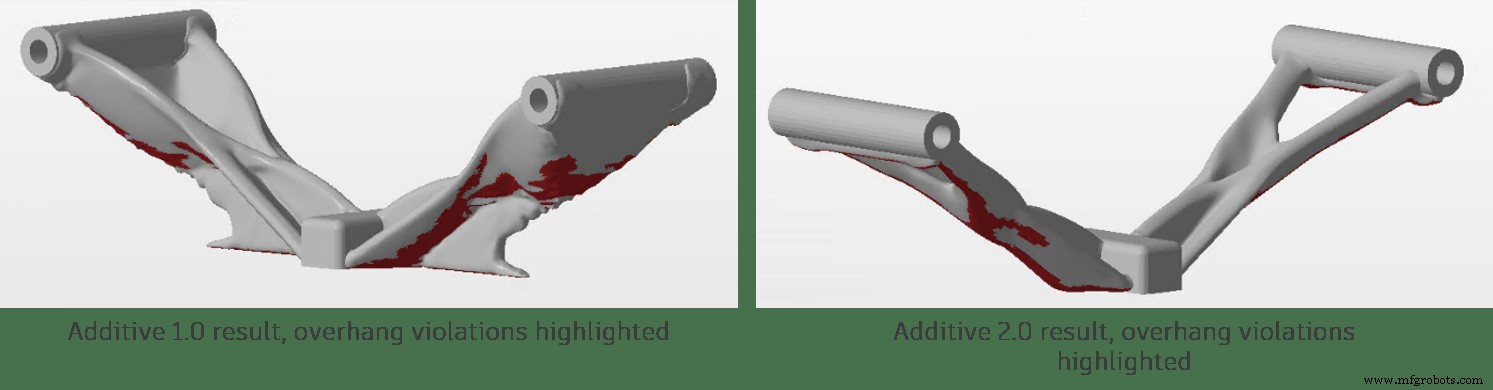
Dans les deux cas, la quantité de matériau de support nécessaire est réduite mais pas éliminée. Cependant, le résultat de l'additif 1.0, qui accumule du matériau à partir de la plaque de construction pour supporter l'ensemble de la structure, est 50 % plus lourd que le résultat sans contrainte. Il présente des artefacts en escalier qui étaient une gêne courante avec la solution de fabrication additive d'origine. L'additif 2.0 réduit également considérablement la quantité de matériau de support nécessaire, mais le fait avec des modifications plus subtiles de la géométrie et n'augmente la masse que de 11 % pour ce modèle. Les deux conceptions additives satisfont à la taille minimale de 3 mm, mais Additive 2.0 conserve une structure beaucoup plus proche de l'absence de restriction, fusionnant les poutres en treillis trop minces dans une structure organique plus épaisse. Les nouveaux résultats Additive 2.0 éliminent également une grande partie de la mauvaise qualité de surface dans le résultat d'origine.
En théorie, les nouvelles contraintes Additive 2.0 réduiront la zone supportée et élimineront les poutres minces avec une augmentation minimale de la masse globale de la pièce. Mais ces conceptions sont-elles réellement plus manufacturables ? Passons en revue le processus de préparation de l'impression et voyons.
Validation du processus d'impression
Exemple FFF
La figure 4 (ci-dessous) compare les résultats pour l'additif 1.0 et l'additif 2.0 avec le résultat original sans restriction. Chacun de ces résultats a été pris en compte dans le flux de travail FFF générique à l'aide de l'espace de travail additif Fusion 360. Les modèles ont été tranchés et post-traités à l'aide de Fusion 360 avant d'être imprimés sur une machine FFF de bureau. Chaque pièce a été post-traitée en utilisant les mêmes paramètres d'impression, la même machine et dans le même filament PLA. Les résultats présentés dans la figure 3 identifient clairement l'amélioration entre l'additif 2.0 et 1.0, avec une réduction significative de 41,3 % de la masse partielle. L'avantage d'Additive 2.0 par rapport à l'utilisation des contraintes illimitées est également mis en évidence, avec une réduction de 47,8 % du matériel de support requis.
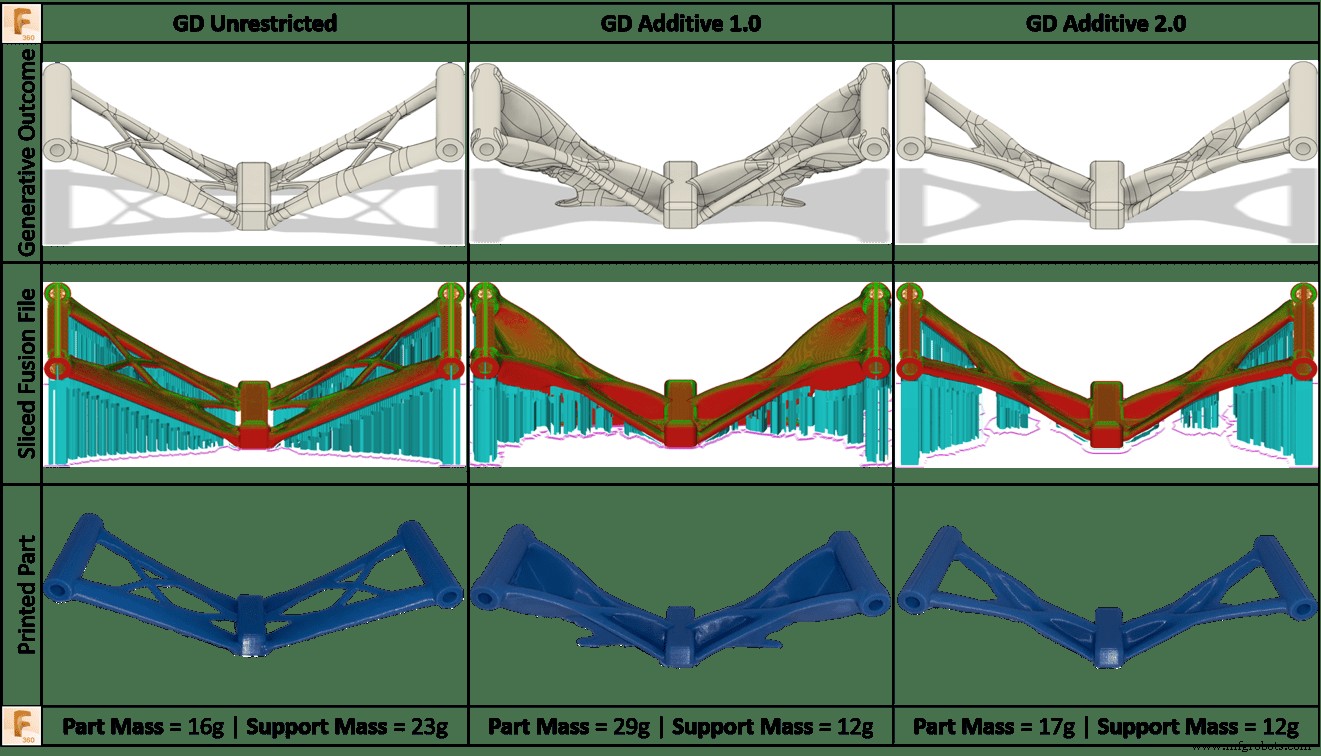
Exemple de SLA
La figure 5 (ci-dessous) compare les résultats pour l'additif 1.0 et l'additif 2.0 avec le résultat original sans restriction préparé pour l'impression dans un processus SLA. Chacun de ces résultats a été pris en compte dans le flux de travail SLA générique à l'aide de Netfabb. Semblable aux résultats ci-dessus, la figure 5 identifie clairement l'amélioration de l'additif 1.0 à 2.0. La masse des pièces et le matériau de support ont également nécessité ce processus.
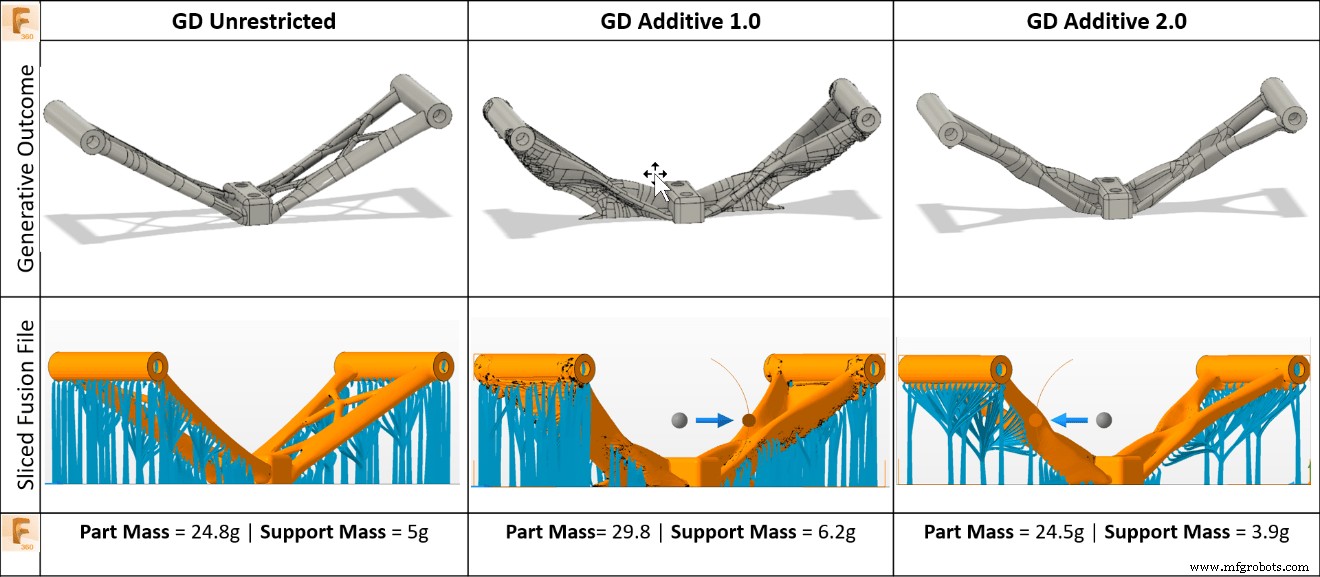
Exemple SLM
Regardons un autre exemple plus réel. L'exemple de problème de triple pince de moto dans les supports de formation en conception générative décrit la conception d'un composant structurel qui relie les tubes de fourche à la tige de direction d'une moto. Pour cet exemple, nous voulons fabriquer de manière additive le composant en aluminium en utilisant la fusion laser sélective (SLM).
Avant d'exécuter l'étude générative, nous avons sélectionné la direction de construction du composant. La hauteur de construction est un facteur de coût majeur, nous avons donc évité la direction +X. Nous savons par expérience que nous devrons combler la plupart des grands trous avec du matériau pendant l'impression, puis post-machiner pour obtenir la tolérance dont nous avons besoin. Une fois les trous remplis, l'orientation +Y entraînera un changement rapide de la section transversale sur la face supérieure de la pièce, ce qui provoque un refroidissement rapide d'une grande surface et peut entraîner des problèmes de construction. En conséquence, nous avons rejeté l'orientation +Y et opté pour la direction de construction +Z.
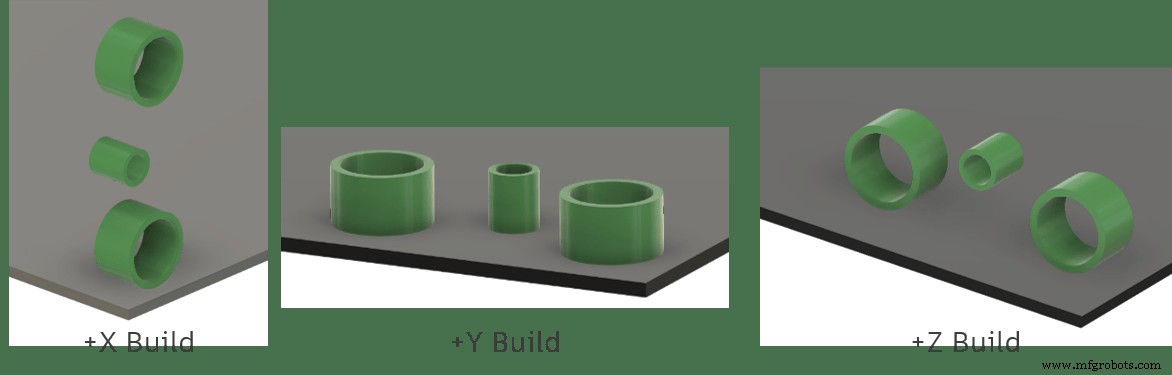
Nous avons sélectionné une taille d'élément minimale de 0,25 po (6,35 mm) pour garantir que toutes les poutres produites sont suffisamment grandes pour résister aux forces du retrait du support. L'angle de porte-à-faux a été fixé à 45°, conformément aux paramètres du processus SLM. Le résultat Additif 2.0 est illustré dans l'image ci-dessous.
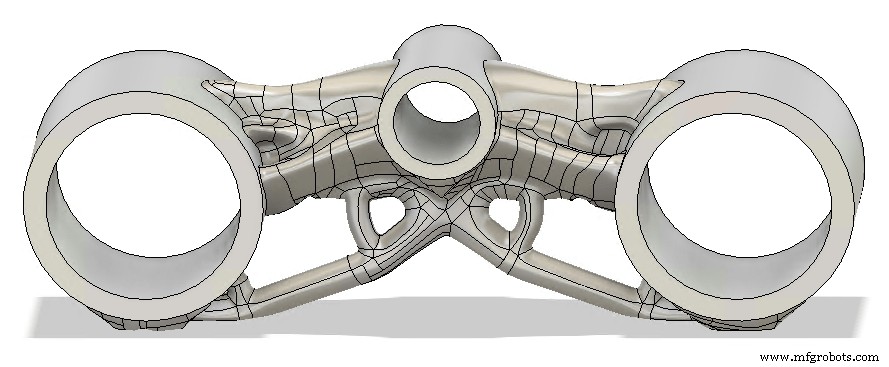
Normalement, nous ferions probablement des ajustements de conception à la forme organique à ce stade et validerions les performances de conception. Pour aujourd'hui, nous allons sauter ces étapes et passer directement à l'espace de travail de fabrication pour le préparer à l'impression.
Nous utiliserons un Renishaw AM250 pour fabriquer la conception, qui nécessite l'extension Additive Build Fusion. Tout d'abord, nous devons remplir les grands trous avec du matériau afin de pouvoir ensuite les usiner à la tolérance. Nous le ferons dans l'espace de travail de fabrication en créant un modèle de fabrication dans lequel nous presserons/tirerons les trous pour qu'ils aient un diamètre plus petit.
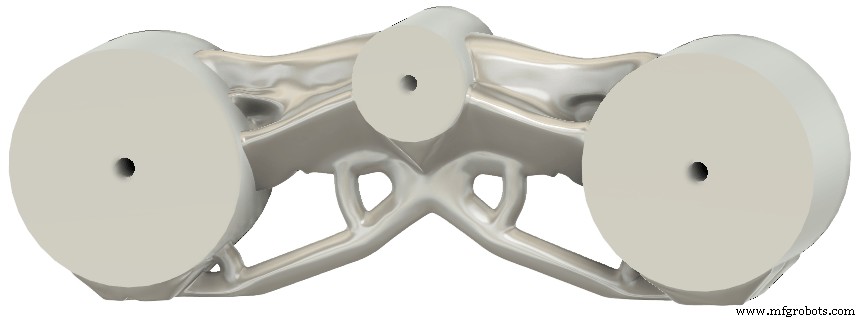
Nous allons maintenant créer une nouvelle configuration, en sélectionnant la machine Renishaw et notre géométrie modifiée. Après un petit travail avec la commande Déplacer, notre pièce est positionnée sur la plateforme de fabrication.
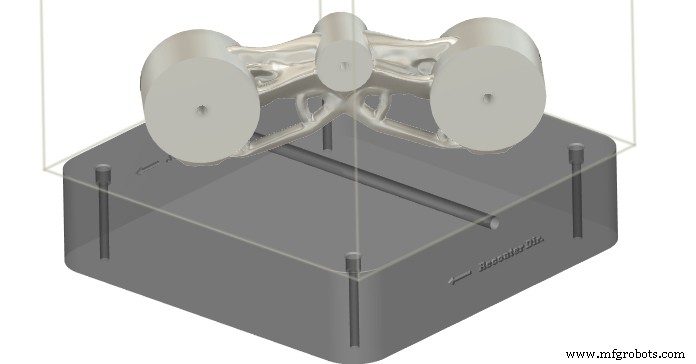
Nous allons maintenant utiliser la commande Volume Support pour générer du matériel de support.
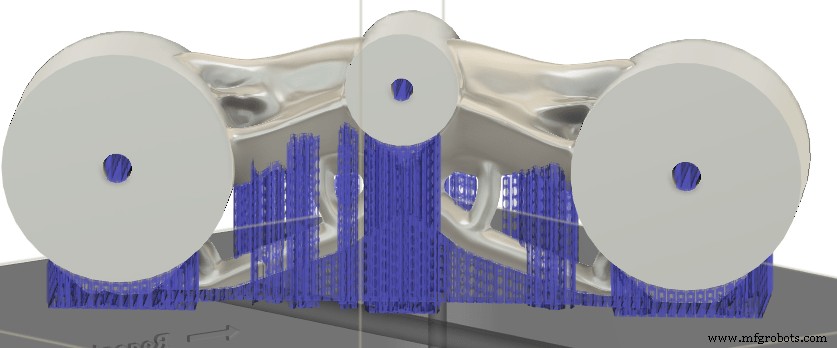
À ce stade, nous sommes prêts à simuler l'impression, puis à générer le g-code et à l'envoyer à la machine.
La figure 7 (ci-dessous) compare la conception Additive 2.0 avec les solutions de fabrication additive sans restriction et existantes, et nous constatons une tendance similaire à celle de l'exemple précédent. Les résultats de l'additif 1.0 sont plus lourds, nécessitent autant de support que la partie sans restriction et souffrent de problèmes de qualité de surface. L'additif 2.0 améliore la qualité de la forme, réduit le matériau de support requis et ramène la masse de la pièce à peu près égale au résultat sans restriction.
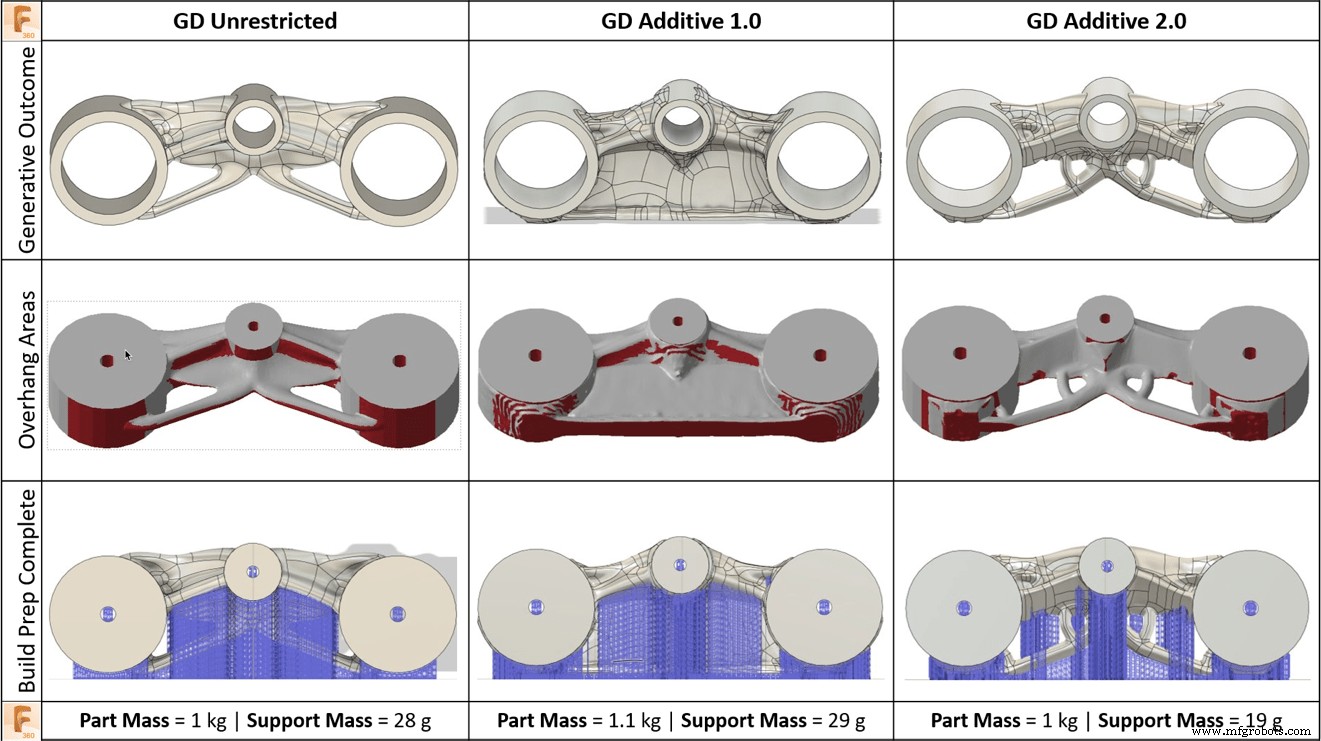
Essayez Additive 2.0 par vous-même
Nous espérons que vous êtes tout aussi enthousiasmés par ces améliorations de la fabrication additive que nous l'étions pour les apporter au produit. Bien que les images de ce blog racontent une belle histoire, nous voulions vous fournir les modèles que nous avons utilisés pour démontrer les améliorations, afin que vous ayez un aperçu par vous-mêmes. Ces modèles sont prêts à être exécutés, ouvrez-les et générez les études disponibles.
Configuration de la barre de tension en forme de V additive 2.0
Additif 2.0 Configuration de la triple pince de moto
Si vous avez des questions ou des commentaires sur nos nouvelles contraintes de fabrication additive, veuillez nous contacter à l'adresse [email protected]. Je tiens également à remercier chaleureusement une formidable équipe d'experts qui ont développé et validé cette solution, ainsi que Ben Weiss, Adam Day, Matt Oosthuizen et Divy Kishor Tiwary pour m'avoir aidé à rédiger ce billet de blog. Je vous souhaite à tous de joyeuses fêtes et une bonne année !

Technologie industrielle
- Fabrication additive vs fabrication soustractive
- Avantages de la fabrication additive
- 4 tendances d'automatisation prometteuses dans la fabrication additive
- Enquête sur les workflows de fabrication additive
- Conception pour la fabrication de PCB
- Tout compris avec additif
- Fabrication additive en électronique
- Comment tirer pleinement parti de la CAO dans le processus de fabrication additive
- Fabrication additive dans l'aérospatiale