Processus d'extrusion :définition, principe de fonctionnement, types, applications, avantages et inconvénients [Notes avec PDF]
Dans le domaine de l'ingénierie mécanique, le processus d'extrusion est largement utilisé par les ingénieurs pour former un objet qui a une section transversale fixe. Pour fabriquer l'objet, la matière première est poussée dans une matrice pour lui donner la forme souhaitée.
La fonction principale de ce processus est que les matériaux fragiles peuvent facilement être transformés en produit souhaité, car dans le cas de l'extrusion, seules les contraintes de cisaillement et de compression sont rencontrées dans le processus.
On peut affirmer que l'extrusion est un processus semi-continu ou même continu qui peut être utilisé pour former un matériau chaud ou même froid.
Qu'est-ce que l'extrusion ?
L'extrusion est un type d'opération de formage du métal où les matrices sont utilisées pour modifier la forme de la pièce métallique à l'aide d'une force externe de nature compressive. Par ce procédé, nous pouvons réaliser tout type de forme complexe assez facilement.
Principe de fonctionnement de l'extrusion :
La quantité de force requise dans le cas du processus d'extrusion est donnée par un plongeur ou un piston pour produire la force de compression. Voici le principe de fonctionnement du processus d'extrusion :
- Au début du processus, un lingot ou une billette de taille standard est développé par le fabricant.
- Ensuite, la billette est chauffée à une température plus élevée dans le cas du processus d'extrusion à chaud et elle est stockée pendant une longue période à température ambiante pour la pousser dans la presse.
- La billette est poussée par le piston monté dans la presse vers la matrice pour fournir la force de compression.
- La matrice est préalablement fabriquée à une forme requise pour développer le matériau à la forme souhaitée. Une force de compression élevée aide le matériau à obtenir la forme souhaitée.
- Enfin, le matériau est sorti de la presse et doit ensuite passer par le processus de finition afin d'améliorer ses propriétés mécaniques.
Types d'extrusion :
L'extrusion peut être globalement classée en deux types, l'un est l'extrusion à chaud un autre est Extrusion à froid . Ces catégories susmentionnées sont également subdivisées en catégories, elles sont les suivantes :
Extrusion à chaud
- Extrusion avant
- Extrusion arrière
Extrusion à froid
- Extrusion avant
- Extrusion hydrostatique
- Extrusion Hooker
- Extrusion arrière
- Extrusion par impact
- Forgeage par extrusion à froid
Plongeons donc dans ces catégories en détail.
Extrusion à chaud :
J'espère que vous êtes déjà assumé par le nom de ce type "Extrusion à chaud". Ici, dans ce processus, la pièce ou la billette est chauffée au-dessus de la température de recristallisation, puis elle est chargée dans le conteneur, puis le bélier exerce une force dessus.
Comme la pièce est déjà chauffée au-dessus de la température de recristallisation, elle s'écoule assez facilement à travers la matrice et est également remodelée de manière très précise et efficace.
Les matériaux couramment utilisés dans ce type d'extrusion sont le magnésium, le cuivre, l'acier, l'aluminium, le nickel, etc.
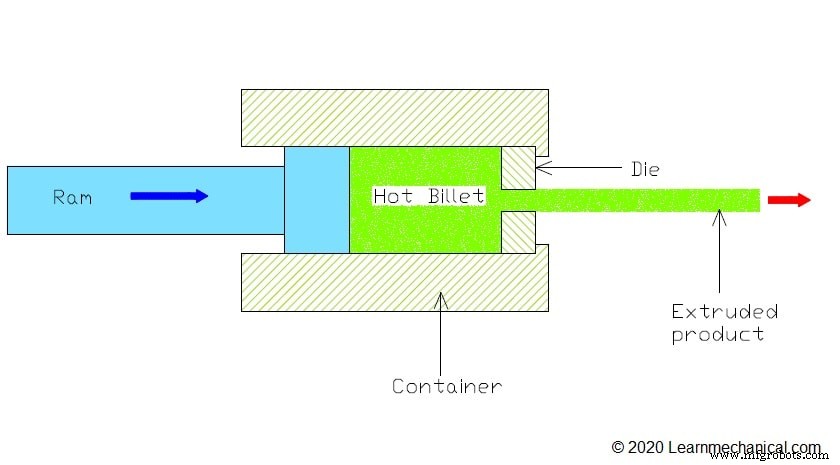
Extrusion à froid :
Dans ce processus, la pièce est maintenue à la température ambiante normale, ou vous pouvez dire en dessous de la température de recristallisation. Pour extruder n'importe quel produit par ce processus, il faut une énorme force.
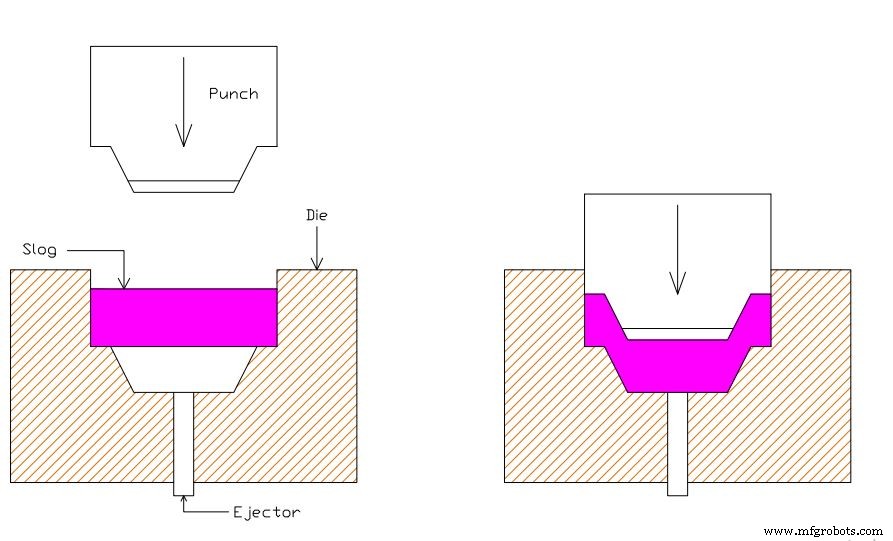
Extrusion indirecte :
Dans ce processus, la direction de la force appliquée par le vérin et la direction du métal extrudé sont du côté opposé. Ce type d'extrusion est également appelé extrusion arrière.
Le principal avantage de ce mode d'extrusion est qu'il réduit relativement le frottement. De plus, par ce procédé, nous pouvons extruder du métal d'un diamètre relativement inférieur.
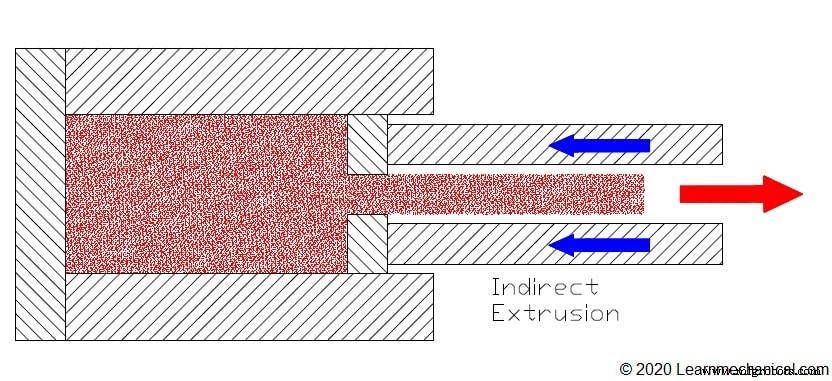
Extrusion directe :
Dans ce processus d'extrusion, la direction du piston et la direction du métal extrudé sont dans la même direction. Ce mode d'extrusion est également appelé extrusion vers l'avant.
Le principal avantage de ce procédé est que, grâce à ce type, nous pouvons extruder des pièces plus longues.
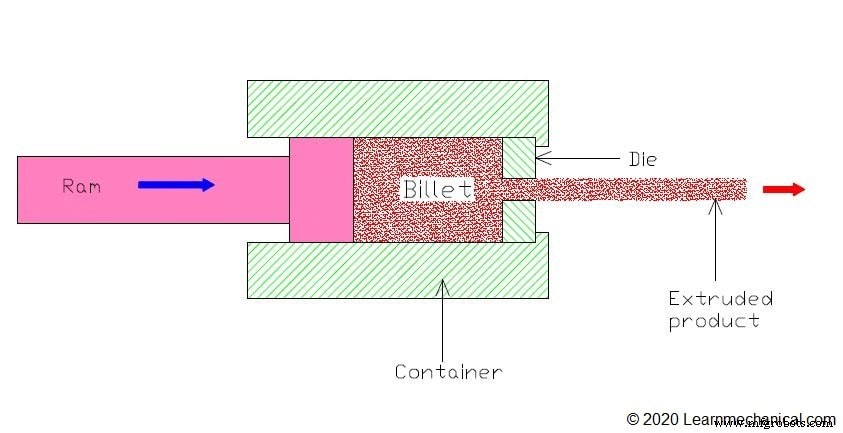
Extrusion hydrostatique :
Dans ce type d'extrusion, nous utilisons un fluide pour pressuriser la billette. Au 1er, une billette est chargée dans le conteneur, puis nous remplissons le conteneur avec du fluide généralement de l'huile de ricin, puis le conteneur est fermé sauf un côté du conteneur, qui contient un vérin et un piston.
Pour que l'opération reste fluide, la forme de la billette est maintenue conique afin qu'elle puisse facilement passer à travers la matrice.
Ainsi, lorsque nous démarrons la machine, le vérin exerce une forte pression sur le fluide, puis il est transféré à la billette. En raison du fluide sous haute pression, une déformation plastique se produit dans la billette et elle sort de l'autre côté de la matrice et prend la forme de la matrice.
Le principal avantage de ce processus est ici, très peu de force de friction entre en action car il n'y a pas de contact entre la paroi du conteneur et la billette.
L'extrusion hydrostatique se déroule généralement à température ambiante.
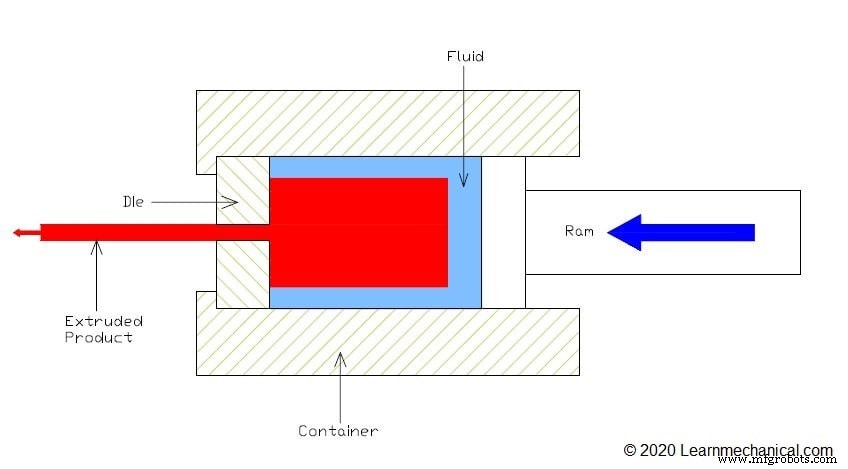
Extrusion Hooker :
Il s'agit d'un processus d'extrusion très populaire, par lequel des tubes en cuivre ou en aluminium sans soudure à paroi mince sont produits.
Au début, la billette ou l'ébauche est placée dans le conteneur, un poinçon exerce la force sur la pièce et transforme la pièce en forme de tasse.
À l'étape suivante, un poinçon plus long a de nouveau exercé la force dans la tasse et en a fait un long produit en forme de cylindre et l'épaisseur, comme d'habitude, a également diminué.
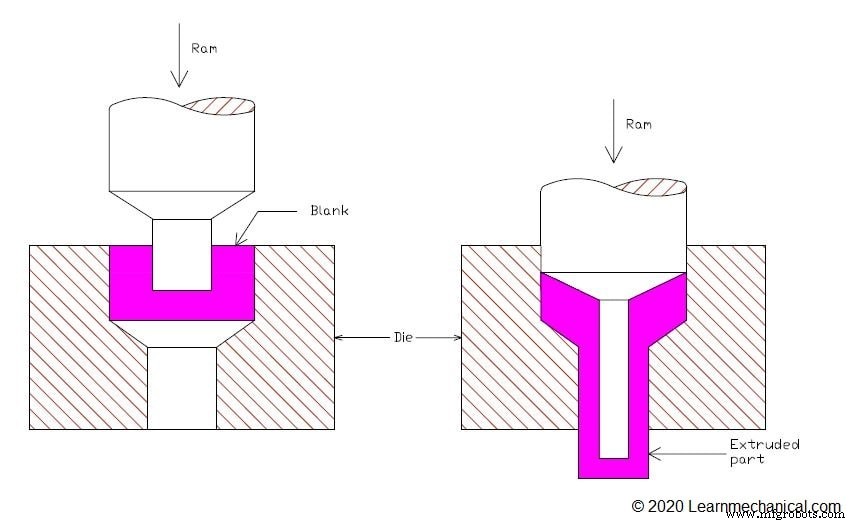
Extrusion par impact :
Ici, dans ce processus, un poinçon est frappé sur la pièce à très grande vitesse pour produire une charge d'impact. Il peut s'agir de n'importe quel type, comme avant, arrière et même les deux.
Cela se fait généralement à température ambiante, c'est-à-dire par extrusion à froid.
Si nous avons besoin de produits comme une tasse, un couvercle de dentifrice ou toute section creuse, nous effectuons généralement l'extrusion par impact arrière, qui est un processus d'extrusion par impact assez populaire.
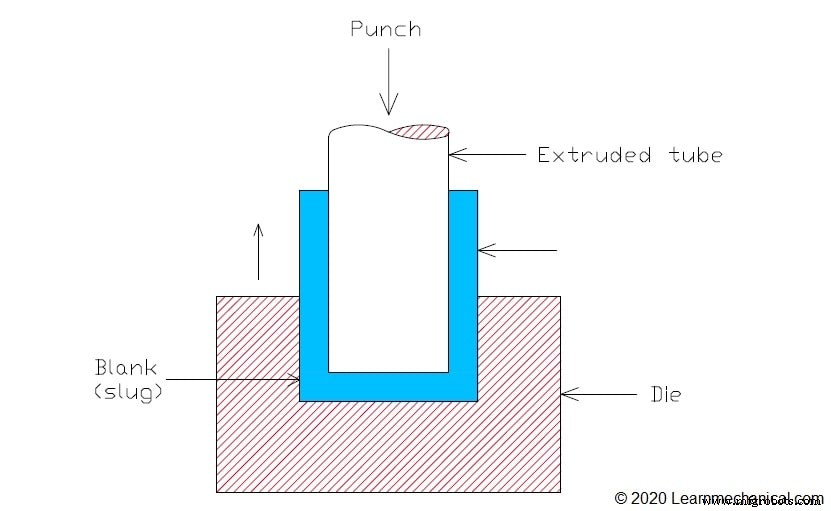
Forgeage par extrusion à froid :
Le forgeage par extrusion à froid est un processus d'extrusion à rebours. Le processus de forgeage par extrusion à froid est le même que celui de l'extrusion par impact. Dans ce processus, le mouvement du poinçon ou du vérin est un peu plus lent que l'extrusion par impact. Au fur et à mesure que la force appliquée à l'ébauche augmente progressivement, la longueur du produit extrudé est assez courte mais l'épaisseur est plus importante.
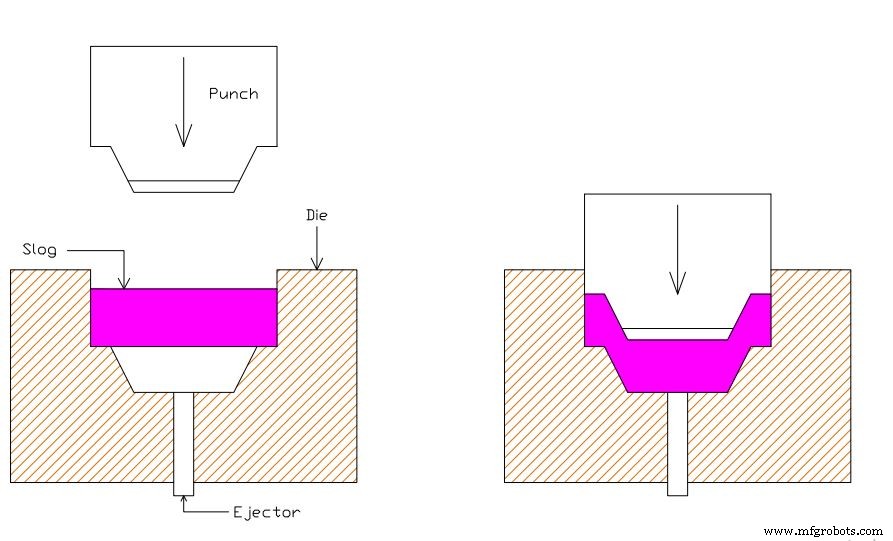
Applications du processus d'extrusion :
- Le processus d'extrusion est principalement utilisé dans la formation de tuyaux creux et il peut être utilisé dans l'industrie de la production. En dehors de cela, pour la fabrication d'aliments instantanés et de produits de type collations, le processus d'extrusion est envisagé par les fabricants. Dans le cas de la transformation des aliments, le processus d'extrusion est utilisé pour chauffer le produit et développer une phase liquide du produit. De plus, en cuisine, le processus d'extrusion est utilisé de nos jours et comprend le mélange, le cisaillement, la séparation, le refroidissement, le chauffage, etc. Pour éliminer l'humidité des produits et aussi pour encapsuler le matériau, le processus d'extrusion est également pris en compte par les producteurs.
- Cependant, pour développer des matériaux prêts à consommer, un processus d'extrusion à froid est utilisé . À titre d'exemple, les types de pâtes alimentaires sont fabriqués à l'aide d'un processus d'extrusion à froid. Ces types de produits incorporent une faible humidité grâce à laquelle le cycle de vie des produits est augmenté et il est également plus pratique de servir les clients.
- En outre, les produits pharmaceutiques sont également développés à l'aide du processus d'extrusion . Les filtres polymères, les produits nanoporeux sont formés par le processus d'extrusion. Le processus de fabrication des médicaments comporte un processus d'extrusion à chaud et à froid. Pour augmenter la solubilité des produits et la biodisponibilité, le procédé d'extrusion à chaud est utilisé. Dans ce processus, une pression, une chaleur et une agitation élevées sont prises en compte par les fabricants.
- En dehors de cela, dans le gros œuvre, le procédé d'extrusion d'aluminium est utilisé . Ce processus comprend les portes, les fenêtres, etc. Dans l'industrie automobile, le processus d'extrusion est également utilisé pour former le type de matériau souhaité en utilisant des matériaux fragiles.
- Enfin, on peut dire que le processus d'extrusion est largement utilisé pour fabriquer des matières plastiques .
Avantages du processus d'extrusion :
L'extrusion comprend plusieurs avantages qui sont les suivants ;
- Le processus d'extrusion est largement utilisé pour créer un profil complexe de matériaux en un minimum de temps par rapport à d'autres processus de formage des métaux.
- Le processus d'extrusion est très utile pour travailler avec des matériaux fragiles et ductiles.
- Les propriétés mécaniques qui peuvent être développées par le processus d'extrusion sont très précises et améliorent le cycle de vie des produits.
Inconvénients du processus d'extrusion :
Certains inconvénients de l'extrusion sont énumérés ci-dessous :
- La consommation de temps de ce processus est très élevée.
- Le coût d'installation au stade initial est également très élevé.
- La quantité de force de compression requise pour le processus d'extrusion est également très élevée, et en raison de laquelle l'opérateur doit s'assurer que le piston est correctement fixé dans la presse.
Conclusion :
Il s'agit donc du processus d'extrusion dans les détails.
J'espère que vous trouverez cet article intéressant.
Si c'est le cas, n'hésitez pas à partager cette ressource avec vos amis ou vos groupes de médias sociaux préférés. Votre part est vraiment appréciable.
Technologie industrielle
- Processus de rodage :définition, pièces ou construction, principe de fonctionnement, avantages, application [Notes avec PDF]
- Processus de rodage :définition, principe de fonctionnement, types, matériau, avantages, application [Notes avec PDF]
- Angle de coupe :définition, importance et types (positif, négatif, zéro) [Notes avec PDF]
- Mécanisme de retour rapide :définition, types, principe de fonctionnement, applications, avantages, inconvénients [Notes avec PDF]
- Soudage par faisceau d'électrons :définition, construction, fonctionnement, applications, avantages et inconvénients [Notes avec PDF]
- Soudage à l'arc plasma :principe, fonctionnement, équipements, types, application, avantages et inconvénients
- Procédé de soudage à l'état solide :principe, types, application, avantages et inconvénients
- Soudage par explosion :principe, fonctionnement, types, application, avantages et inconvénients
- Soudage par friction :principe, fonctionnement, types, application, avantages et inconvénients