Les jumeaux virtuels optimisent les opérations chez CenterLine
En science militaire, un « multiplicateur de force » est un système opérationnel qui utilise une stratégie pour accroître l'efficacité des armements existants. Nous pouvons utiliser l'idée comme une métaphore pour améliorer l'efficacité des systèmes d'information d'ingénierie et de fabrication, du concept initial au service client continu.
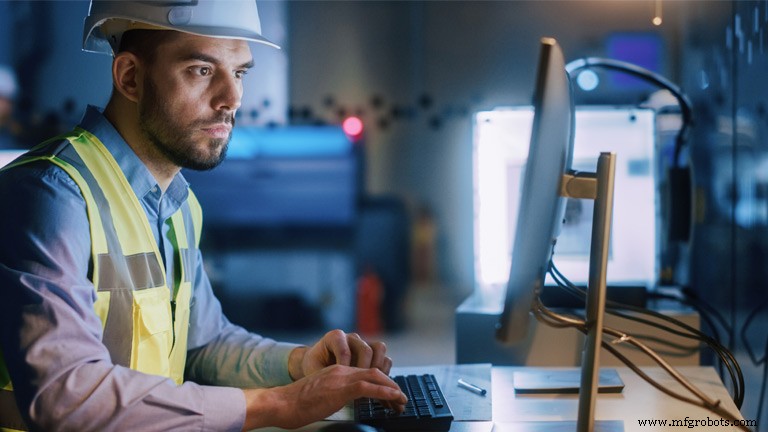
Les « armements » de l'automatisation industrielle sont représentés par une variété d'acronymes :CAO, CAE, PDM, PLM, SCM, MES, CMS, etc. Presque toutes les entreprises manufacturières disposent d'un certain niveau d'automatisation des processus, mais de nombreuses conversations sur les processus de fabrication se terminent par la phrase "alors nous copions les données de la nomenclature". C'est là que s'arrêtent les améliorations d'efficacité. Pour continuer notre métaphore initiale, les entreprises manufacturières possèdent les armements, mais il n'y a pas de stratégie primordiale pour en faire un multiplicateur de force industrielle.
Nous avons accès à de nombreuses solutions de création, de collecte et de gestion de données dans l'espace de fabrication qui informent divers aspects de ce qu'un produit devrait devenir et comment un processus de fabrication devrait travail, système par système. La prochaine étape consiste à passer du « devrait » au « fait ». La transformation des informations en intelligence en temps réel est le multiplicateur de force :les données de performances planifiées fournies par ces solutions peuvent devenir des informations sur les performances réelles en temps réel.
Cadres d'informations stratégiques
Le fil virtuel et le jumeau virtuel (ou jumeau numérique/thread) sont deux concepts connexes à la pointe de cette quête d'intelligence en temps réel. Pour rappel, un thread virtuel est la possibilité pour les utilisateurs d'améliorer des performances spécifiques en délivrant la bonne information aux bonnes personnes au bon moment. Pendant ce temps, un jumeau virtuel est une représentation visuelle constamment mise à jour d'un produit, d'un système ou d'un processus basé sur des données du monde réel.
Ces nouveaux cadres d'information conduisent à un nouveau modèle de processus dans lequel les données sont considérées à la fois comme faisant partie d'un fil virtuel et d'un jumeau virtuel. Dans l'ingénierie basée sur les modèles, par exemple, le thread et le jumeau représentent un cadre stratégique pour créer une valeur maximale dans l'entreprise. Les deux incluent les exigences telles que conçues ; dossiers de validation et d'étalonnage ; et données telles que construites, telles qu'exploitées et telles qu'entretenues.
Le thread virtuel et le jumeau virtuel sont des concepts, pas des produits ou des services spécifiques :vous ne pouvez pas courir chez votre intégrateur local et commander un thread virtuel. Au lieu de cela, ils fournissent des solutions qui aident les utilisateurs à créer des systèmes entièrement numériques dans lesquels chaque individu de l'organisation dispose de toutes les informations nécessaires dans un système facile d'accès et facile à partager.
La connectivité est l'objectif primordial. De nombreux problèmes liés aux données sont liés aux connexions et à l'accès, ce qui signifie que les entreprises doivent éliminer les inefficacités qui nuisent aux opérations de fabrication.
Combien de ces défis existent dans votre organisation ?
- Les modifications techniques n'atteignent pas l'atelier en temps opportun
- Manque de visibilité des fournisseurs
- Aucune norme ou contrôle sur la création d'instructions de travail
- Gestion et contrôle du contenu non synchronisé
- Le service marketing crée du contenu avec des informations de conception obsolètes
- Perte de productivité due à des informations inexactes et peu claires
- Manque d'accès aux données pour les bonnes personnes
Bien que bon nombre de ces problèmes ressemblent à des problèmes de technologie ou de méthodologie, ils ont toujours un impact sur les individus de l'opération en aval en entravant leur capacité à optimiser les flux de travail. Pour rendre les opérations plus efficaces, vous devez améliorer les systèmes utilisés, et non essayer de « réparer » les personnes qui les utilisent. Les systèmes entièrement numériques répondent aux besoins des membres de l'équipe en éliminant ces problèmes de connectivité et d'accès aux données.
Le fil virtuel
Le fil virtuel - le côté communications du nouveau cadre industriel - permet un flux de données connecté pour toutes les informations sur les actifs et les métadonnées associées. L'idée du fil virtuel est née dans la recherche aérospatiale il y a plus de 10 ans, lorsque des chercheurs du laboratoire de recherche de l'US Air Force à Wright-Patterson Air Force Base l'ont utilisé pour décrire l'assemblage piloté par modèle dans l'usine. Plusieurs threads s'étendent du modèle (la source de données commune) aux équipes de conception, d'approvisionnement, de test, de production, d'opérations sur le terrain et de soutien, ce qui signifie qu'il n'est pas nécessaire qu'un individu dans le thread demande des données ou réponde aux demandes de données avec une copie /coller l'e-mail. L'information est toujours "active" et toujours accessible, établissant une véritable ressource unique et une voie de communication pour toutes les parties, quel que soit le silo ou le flux de travail.
Le jumeau virtuel chez CenterLine
Avoir un accès permanent et en temps réel aux données des threads virtuels rend possible un jumeau virtuel. Les fils transmettent une vue complète du produit, combinant les détails de la nomenclature avec les données CAO/CAE pour une représentation visuelle, virtuelle et en temps réel. Il faut un flux bidirectionnel dans les threads virtuels pour activer un véritable jumeau virtuel, nécessitant une boucle de rétroaction où l'étalonnage, la validation, les données telles que construites et telles qu'utilisées mettent à jour le jumeau. Ensemble, le thread virtuel et le jumeau virtuel sont l'unification de la conception et des données.
Par exemple, l'entreprise canadienne de processus et de technologie d'automatisation industrielle CenterLine Limited (Windsor, Ontario), un producteur de chaînes de soudage et d'assemblage automatisées sur mesure, a dû faire face à des défis avec des configurations d'usine coûteuses, surtout si l'entreprise devait corriger des erreurs de conception ou faire face à des accidents opérationnels. entre les machines et les travailleurs humains dans des systèmes physiques déjà installés.
CenterLine a cherché à optimiser ses conceptions de cellules de travail robotisées et à surmonter ces défis grâce à la simulation numérique avant le déploiement d'équipements physiques dans les usines. Pour atteindre cet objectif, ils ont mis en œuvre la solution DELMIA sur la plate-forme 3DEXPERIENCE de Dassault Systèmes pour simuler virtuellement les produits, les processus et les opérations d'usine afin d'optimiser les mouvements de robot, l'aménagement de l'usine, le flux de matières et l'ergonomie.
Depuis la mise en œuvre de DELMIA pour chaque cellule de travail robotisée, CenterLine a réduit les problèmes liés à l'outillage et les retouches jusqu'à 90 % et le temps de programmation sur le terrain jusqu'à 75 %. Le temps gagné grâce à la simulation des trajectoires d'outils de soudage à l'arc robotisé a amélioré la productivité de 15 % et raccourci le délai de mise sur le marché pour la simulation et la conception de 15 à 20 %. En tant que source unique de vérité pour différentes données CAO, la plate-forme unifiée permet aux dirigeants de CenterLine de se concentrer sur les opérations quotidiennes au lieu de gérer les données et les produits
Lorsque tous les canaux de données sont connectés dans un cadre Virtual Thread/Virtual Twin, les membres de l'équipe sont unis dans une stratégie qui permet une meilleure utilisation des données existantes. En effet, les fabricants obtiennent finalement un nouveau multiplicateur de force pour la valeur de fabrication.
Système de contrôle d'automatisation
- Digital Twins :pourquoi les répliques virtuelles d'actifs créent une réelle valeur commerciale
- Comment collecter des données à partir de systèmes existants pour améliorer les opérations
- Rendre les données IoT significatives dans l'agriculture chez John Deere
- La précision des modèles de données numériques jumeaux est la clé du succès
- Comment les jumeaux numériques peuvent aider à améliorer les performances logistiques
- Ridecell lance la « première plateforme » pour convertir les données du véhicule en opérations automatisées
- Quelle est la durée de vie de l'outil ? Comment optimiser l'outillage avec les données machine
- Trois façons dont l'IA améliore les opérations de fabrication
- Pourquoi vos opérations d'entrepôt et d'usine ont besoin de l'IIoT