MMF #3 :Charnières de salon renforcées de fibres suffisamment solides pour tenir debout
MarkForged Mechanical Features [MMF] est une série d'articles de blog détaillant les meilleures pratiques pour la conception de pièces d'ingénierie traditionnelles courantes et de caractéristiques mécaniques pour l'impression 3D renforcée de composites avec les imprimantes MarkForged.
Une mauvaise résistance des pièces verticales est courante parmi les imprimantes 3D FFF (Fused Filament Fabrication), en particulier lorsqu'elles sont chargées en tension. Dans ces technologies d'impression 3D, la liaison le long de l'axe vertical est plus faible que la résistance du matériau constitutif car dans chaque partie, des centaines de couches adhèrent les unes aux autres le long de l'axe vertical, de sorte que la connexion entre chaque couche se comporte comme une couture ou un fissure lorsqu'il est chargé. La résistance dans le plan d'une couche est supérieure à l'adhérence intercouche car le plastique de chaque couche est déposé sous la forme d'un extrudat continu et présente les propriétés de résistance du matériau de la pièce lui-même. Sur le Mark Two, cette différence directionnelle de résistances (ou d'anisotropie) se produit également avec notre procédé de fabrication de filaments continus (CFF) - toutes les fibres composites avec lesquelles nous travaillons ont une résistance à la traction impressionnante, mais parce qu'elles sont posées le long de plans parallèles à la plaque de construction, cette force n'est pas directement traduite dans l'axe vertical. Une conception appropriée pour les pièces imprimées en 3D implique d'adapter la géométrie d'un composant de manière à ce qu'il soit principalement chargé dans le plan horizontal, et les pièces créées par une imprimante Markforged ne font pas exception. Cependant, avec quelques astuces de conception soignées dans votre manche, vous pouvez contourner ce problème et créer des pièces imprimées en 3D de qualité industrielle sur le Mark Two avec des propriétés beaucoup plus isotropes.
Si vous avez déjà manipulé nos matériaux, vous avez peut-être remarqué que notre nylon peut en fait être assez flexible par lui-même. Cela permet la conception de charnières vivantes ou de sections flexibles de composants pouvant former un joint ou une charnière sans aucun assemblage requis. En savoir plus sur la conception de charnières vivantes et d'éléments de flexion ici.
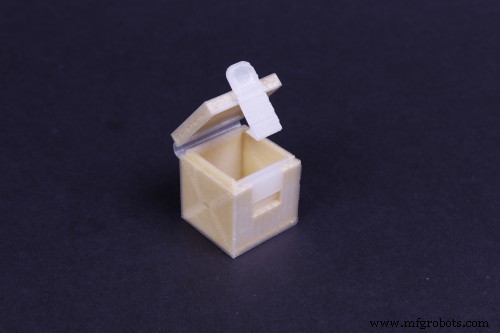
Alors que le renfort en fibre de l'imprimante Markforged peut considérablement rigidifier le nylon, vous pouvez utiliser du Kevlar® pour créer des charnières vivantes renforcées de fibres. Avec un peu d'origami renforcé de fibres, vous pouvez concevoir des pièces squelettées avec un minimum de matériau de support qui sont solides dans toutes les directions. Voici un exemple :
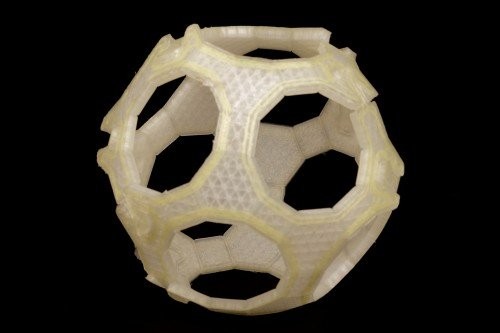
Une pièce comme celle-ci aurait pris un temps fou et du matériel de support pour imprimer comme indiqué, et cela aurait été assez faible le long de l'axe vertical, j'ai donc conçu pour l'imprimer comme ceci :
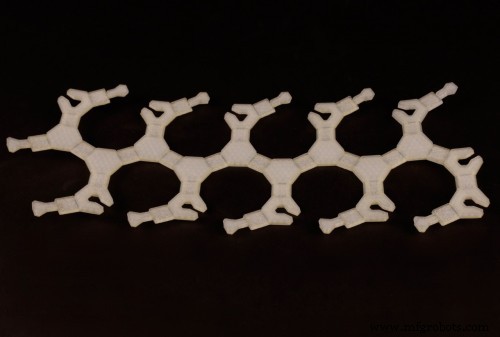
En regardant la disposition des fibres dans l'Eiger, vous ne verrez qu'une seule couche de Kevlar à motifs concentriques dans cette impression. J'ai choisi d'utiliser du Kevlar car, bien que la fibre de carbone et la fibre de verre soient plus solides, le Kevlar est le plus flexible des matériaux que nous proposons et conserve une grande partie de sa résistance à la traction même lorsqu'il est plié à des angles vifs. La fibre de carbone et la fibre de verre sont beaucoup plus rigides et se fractureront aux rayons de courbure que le Kevlar peut gérer sans problème. La seule couche de Kevlar offre suffisamment de force pour que cette balle puisse supporter quelques dizaines de livres, mais suffisamment de flexibilité pour que les articulations se plient bien.
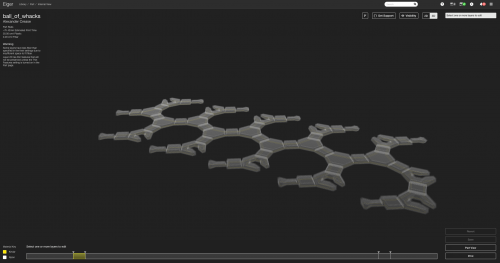
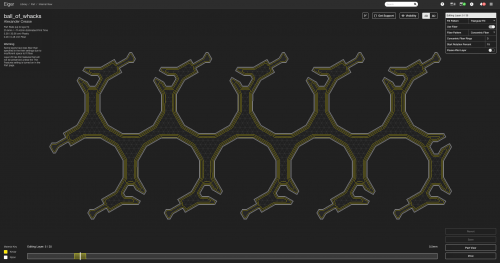
Après avoir conçu le polyèdre, j'ai augmenté les enjeux pour voir si je pouvais imprimer en 3D quelque chose de pliable suffisamment solide pour supporter mon poids corporel. J'ai décidé de rester simple et j'ai conçu un cube en Kevlar pliable dans Autodesk Fusion 360. J'avais besoin d'une méthode pour sécuriser les faces du cube ensemble et d'un joint pour connecter les faces qui n'étaient pas directement adjacentes. J'ai commencé par modéliser quatre faces du cube, chacune en tant que composant distinct, afin de pouvoir les manipuler dans l'environnement CAO pour simuler le comportement de pliage que je souhaitais pour mon assemblage. Pour sécuriser une connexion entre chaque face, j'ai conçu un joint à emboîtement de sorte que lorsque vous pliez chaque face dans la bonne orientation, la face s'enclenche et les emboîtements empêchent le cube de se déplier ou de se déformer.
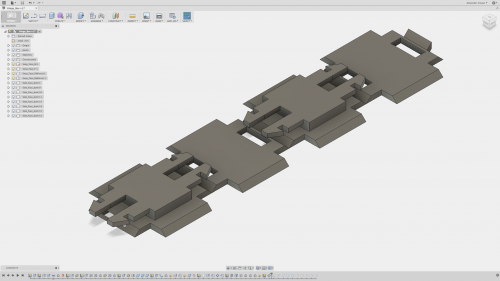
J'ai également ajouté une petite mortaise et un tenon sur les bords qui finiraient par se connecter une fois que la face la plus à gauche rejoint la face la plus à droite.
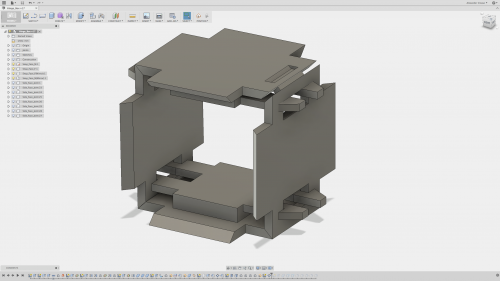
J'ai ensuite décidé d'essayer quelque chose d'intéressant avec les deux côtés restants de la boîte – sur chaque bord restant ouvert, j'ai conçu une section de chaque côté. Chaque section a une languette d'ajustement par torsion et une découpe pour la languette correspondante sur la section adjacente. Une fois la boîte pliée, ceux-ci peuvent tous être emboîtés pour former les deux côtés restants. Dans l'image ci-dessous, j'ai rendu l'une des pièces transparente pour montrer les chanfreins que j'ai ajoutés pour créer un joint en queue d'aronde qui dépend de la flexibilité du matériau à tordre en place.
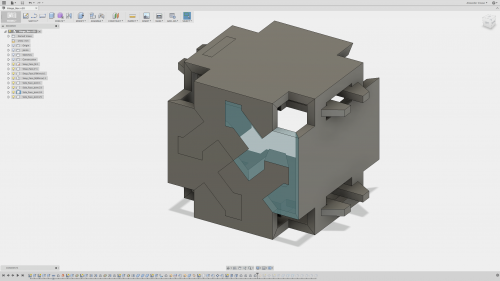
Une fois les géométries de chaque face gravées dans la pierre, j'ai «déplié» le cube en CAO de manière à ce que tous les corps soient à plat dans l'orientation dans laquelle je voulais que la pièce soit imprimée. Vous remarquerez dans l'image ci-dessous que chacun des composants se rencontrent le long de leurs bords - ils ne sont pas encore connectés. À ce stade, je devais encore combiner cela en une seule pièce unifiée en ajoutant les couches nécessaires pour créer la charnière vivante.
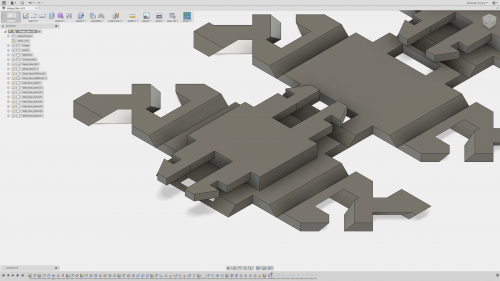
Pour ce faire, j'ai capturé les profils des faces inférieures de chaque composant et les ai extrudés de 0,875 mm, et j'ai combiné tous les corps séparés en un seul. Cela donne de l'épaisseur à la charnière vivante :l'épaisseur de 0,875 mm ajoute juste assez de matière pour qu'une seule couche de Kevlar s'adapte à l'intérieur et crée une charnière vivante renforcée de fibres. Notez ci-dessous que maintenant chaque bord où les composants séparés se rencontrent a maintenant une épaisseur.
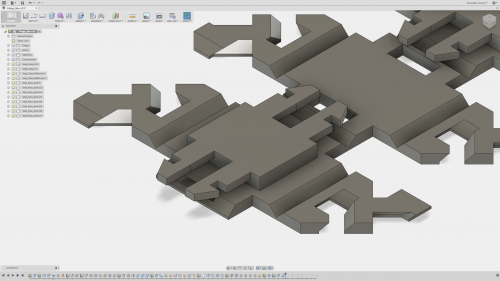
Et voici la vue complète de la pièce présentée et prête à imprimer :
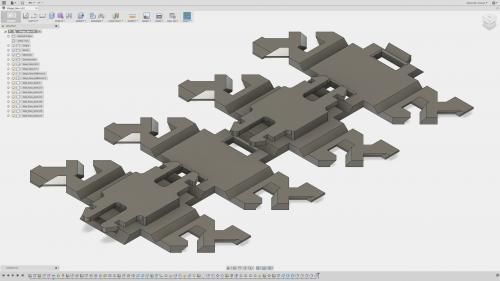
Dans l'Eiger, j'ai disposé des anneaux concentriques de fibres sur cette première couche de Kevlar pour créer et renforcer le joint. Pour renforcer le reste de la pièce, j'ai créé des panneaux sandwich en commençant sur chaque face au-dessus de cette première couche de Kevlar. Comme nous l'avons expliqué dans un article plus ancien, les panneaux sandwich sont fondamentaux pour les matériaux composites car ils offrent une résistance élevée avec un faible poids. Les panneaux sandwich renforcent chaque face du cube pour en faire des composants imprimés en 3D solides et rigides - gardez à l'esprit que chaque face n'a qu'environ 3 mm d'épaisseur. J'ai également pu installer du Kevlar dans les joints à encliquetage pour renforcer leurs petites caractéristiques, dont nous avons discuté dans un article précédent. Le GIF ci-dessous montre les premières couches, y compris la couche de charnière vivante renforcée de Kevlar (couche 5) et les couches inférieures du panneau sandwich (couches 6 à 8).
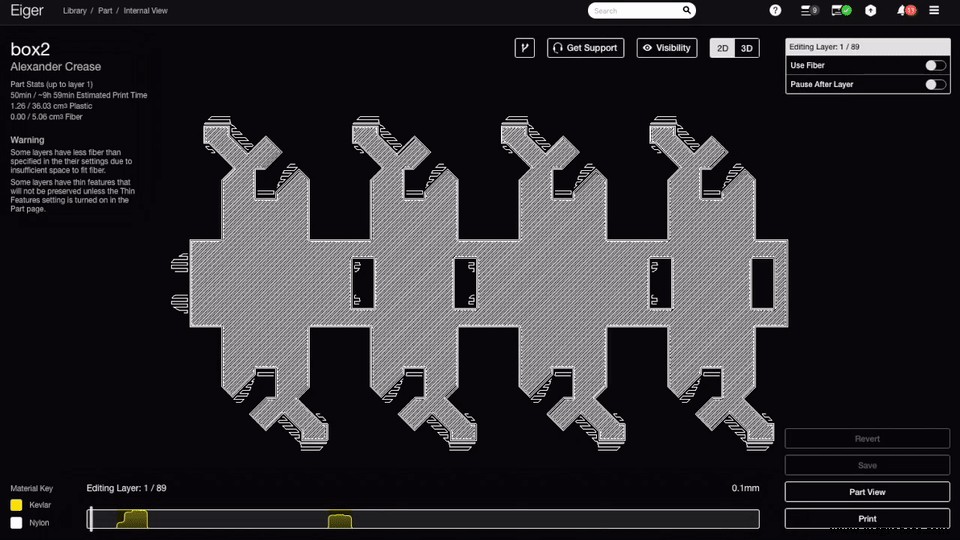
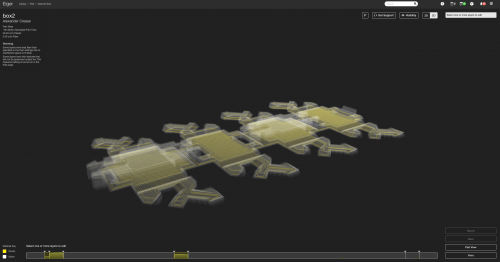
Après l'impression, j'ai tout assemblé et tordu dans les joints des panneaux latéraux, et j'ai fabriqué un cube pliable imprimé en 3D avec un renfort en Kevlar !
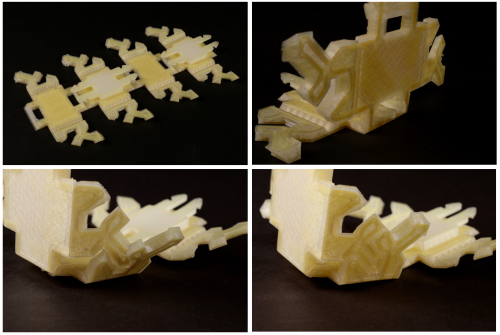
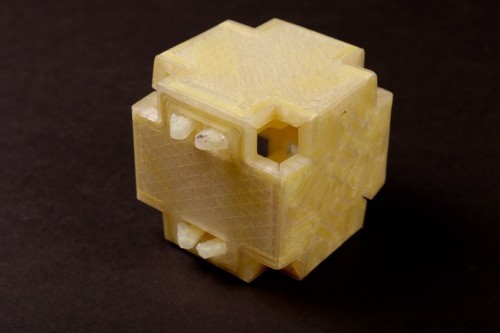
Chaque côté du cube fournit un renforcement substantiel à la fois en tension et en flexion, ce qui rend le cube dans son intégralité très difficile à comprimer et isométrique le long des trois axes principaux. J'ai pu y mettre tout le poids de mon corps (environ 130 lb) sans même une suggestion de déformation. Je suis une personne assez petite, alors j'ai fait un test beaucoup plus rigoureux. Je n'ai pas obtenu de très bonnes lectures, mais j'estimerais qu'il contenait environ 300 à 400 livres avant d'échouer. Voici ce qui s'est passé :
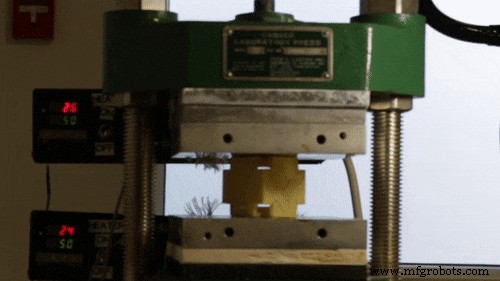
Ainsi, après quelques centaines de livres, la chose la plus surprenante était que la pièce ne s'est pas réellement cassée, tous les joints se sont détachés et le cube entier s'est aplati, donc avec un peu de redressement, il peut être ramené à sa forme d'origine. Ainsi, en créant des structures pliables avec des charnières vivantes renforcées de fibres, vous pouvez créer des pièces imprimées en 3D très solides dans toutes les directions.
Vous voulez l'imprimer vous-même ? Téléchargez le fichier STL ou .mfp !
Vous voulez tester la force par vous-même ? Commandez un échantillon gratuit ici !
impression en 3D
- Que sont les charnières à deux volets ?
- 5 avantages à choisir des charnières en aluminium
- Une introduction aux charnières continues
- La technologie laser existante est suffisamment puissante pour attirer les extraterrestres à 20 000 années-lumière
- Mon premier mini routeur CNC personnalisé — Il doit être assez solide
- Ferro-Titanit® U
- DIFENDER 400
- Comprendre la résistance à la compression
- Comment concevoir des charnières mobiles imprimées en 3D