Stratasys Insight – Fonctionnalités Anti-Part Curl que vous devez connaître
Est-il déraisonnable d'attendre la perfection de l'impression 3D ? C'est vrai, mais les utilisateurs finaux blâment rapidement les machines.
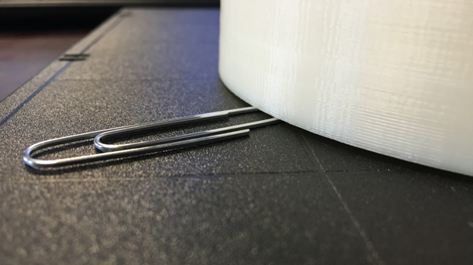
Permettez-moi de commencer par préciser que je ne suis pas ingénieur plastique, mais je sais que les thermoplastiques ont une température de transition vitreuse, ce qui signifie qu'ils deviendront liquides et se solidifieront à nouveau à certaines températures. C'est la raison pour laquelle certains articles en plastique peuvent être fondus et réutilisés à plusieurs reprises. Comme vous le savez peut-être déjà, c'est exactement ainsi que fonctionne la technologie FDM :les matériaux sont chauffés jusqu'à leur transition vitreuse, extrudés, puis se solidifient à nouveau. Le processus est assez simple, mais il y a évidemment beaucoup plus à prendre en compte.
Alors que les thermoplastiques, tels que l'ABS, ont des taux de retrait relativement faibles, nous constatons toujours des problèmes de distorsion et de gondolage en raison des caractéristiques du matériau, en particulier lors de l'impression de grandes géométries avec des sections transversales épaisses. Cela peut être accrédité aux taux de refroidissement différentiels des matériaux. Les surfaces extérieures ont tendance à se refroidir plus rapidement, tandis que la masse intérieure reste plus chaude, ce qui peut entraîner des résultats indésirables.
Il n'y a rien de plus frustrant et décourageant que de supprimer une version de 25, 50 ou 100 heures pour constater qu'une certaine géométrie s'est déformée bien au-delà de la tolérance. Ces étapes de traitement négligées mais rapides et faciles, dans le logiciel Insight de Stratasys, peuvent aider à réduire ce chagrin.
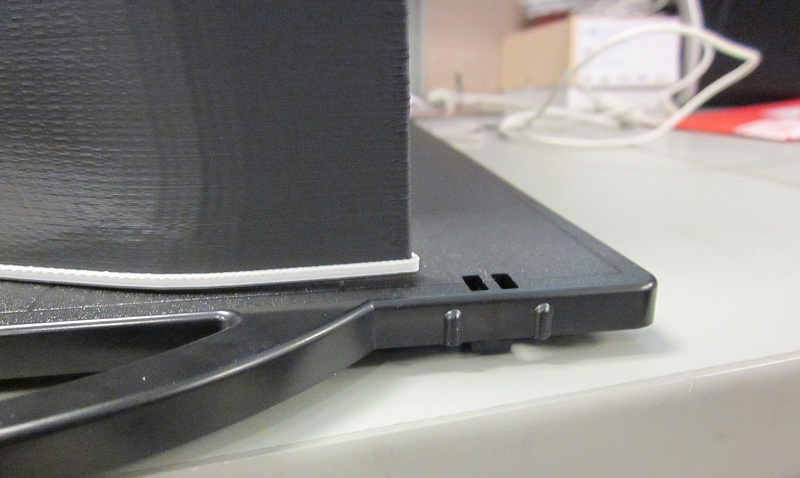
Option 1 :Donnez au modèle une base plus grande
L'augmentation de la géométrie de base permettra une plus grande surface de liaison avec la fondation. Cela sert également de dissipateur de chaleur.
Ces contrôles sont accessibles sous le Support menu en sélectionnant Configuration puis en cliquant sur l'icône des paramètres de paramètres avancés. L'une de ces valeurs ou les deux peuvent être modifiées selon les besoins.
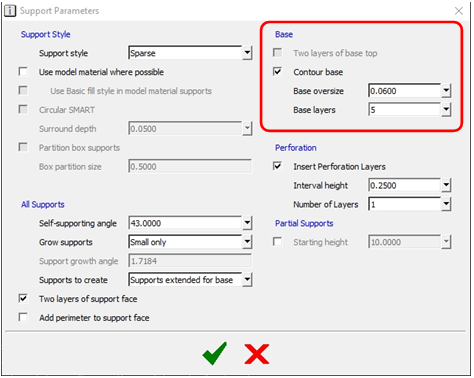
Base surdimensionnée – Considérez cela comme l'empreinte de la base de support. Le réglage fait référence à la dimension autour du périmètre entre la pièce et le support. La valeur par défaut est 0,050", mais elle peut être augmentée jusqu'à un maximum de 0,5". Les couches bleues et blanches, dans les images ci-dessous, représentent les couches de base (matériau de support).
Couches de base – Ce paramètre simple contrôle l'épaisseur ou le nombre de couches de base. La valeur par défaut est 5 couches et la liste déroulante vous donnera le choix entre 5, 10 et 15 ; Cependant, vous pouvez également saisir une hauteur de couche de votre choix, même si nous n'avons pas rencontré de situation nécessitant plus de 15 couches.
Le paramètre de surdimensionnement de base par défaut de 0,050" (illustré ci-dessous) maintient fermement l'empreinte du modèle.
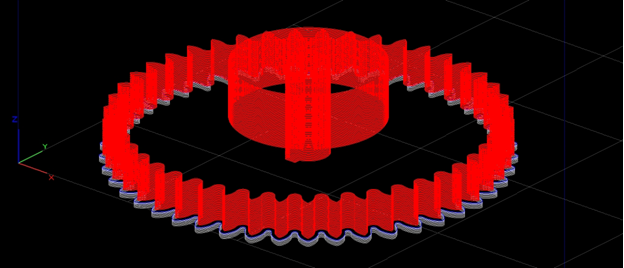
Montré ci-dessous, le surdimensionnement de base est réglé au maximum de 0,5". Vous remarquerez que la surface de la base a augmenté d'environ 16 %, ce qui fournit une base plus large pour se lier au plateau et évacue une partie de la chaleur de la grande section transversale.
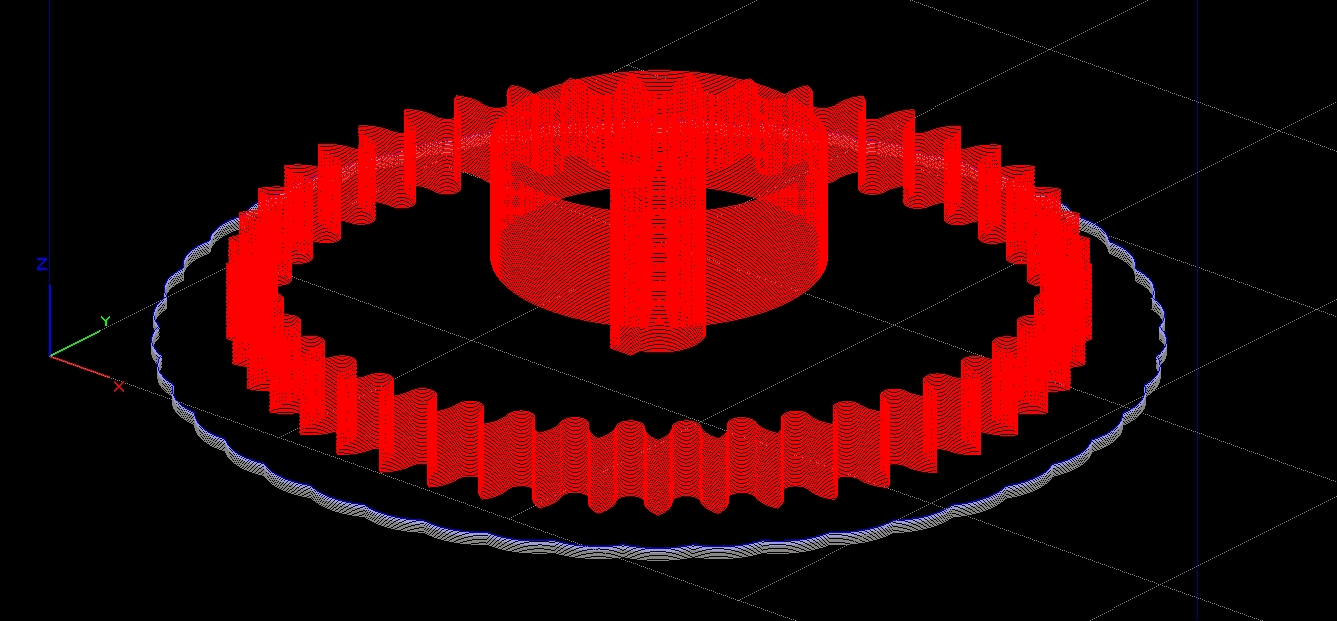
Ci-dessous, j'ai défini le paramètre sur 15 couches de base avec le surdimensionnement de base de 0,5". L'utilisation de combinaisons de ces options produit souvent les meilleurs résultats.
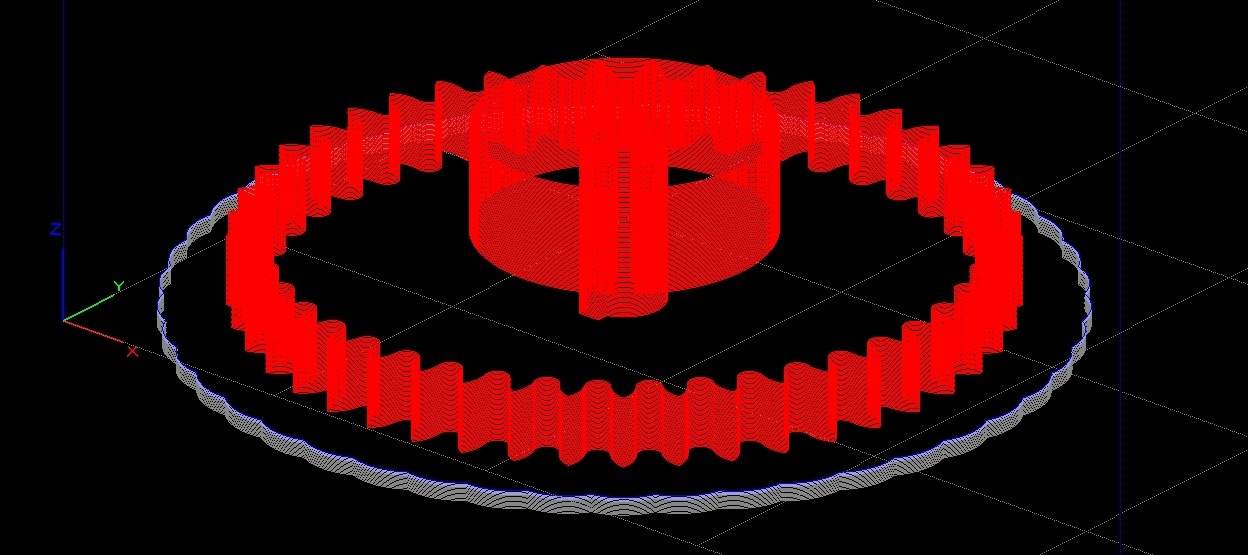
Option 2 :Supprimer les perforations (Supports de rupture)
Ce paramètre fait référence aux paramètres de prise en charge, qui ajoutent des couches de modèle uniques à des intervalles spécifiques dans les colonnes de prise en charge. Insight l'activera automatiquement lorsqu'un matériau avec support de rupture est utilisé. L'intention de conception des perforations est d'aider à retirer les supports. Mais voici le hic :si la géométrie a de grandes zones de support, elles peuvent s'enrouler et se séparer au niveau de ces perforations. Ainsi, le retrait des couches de perforation aidera à réduire le gondolage des pièces, mais rendra plus difficile le retrait des supports.
Ces contrôles sont également accessibles sous le Support menu en sélectionnant Configuration puis en cliquant sur l'icône des paramètres de paramètres avancés. Les commandes sont juste en dessous des commandes de la base de support. Décochez la case et le tour est joué !
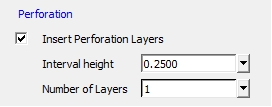
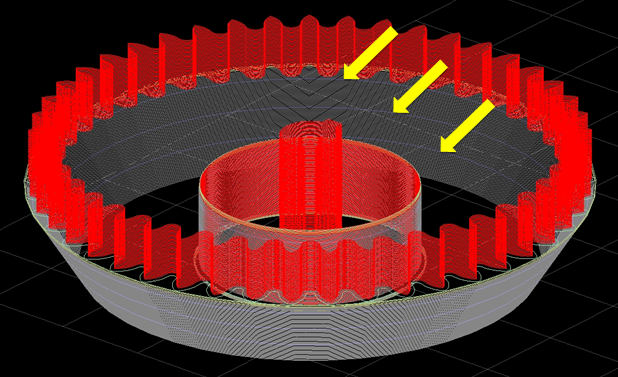
L'exemple ci-dessus montre les lignes de calque de perforation par défaut (bleu clair).
Option 3 : ajouter des colonnes d'ancrage
Colonne d'ancrage – Cette fonction peut créer des colonnes de matériau de modèle qui relient et fixent la surface inférieure du modèle directement au substrat via le support de base. La mise en garde est que ces fonctionnalités supplémentaires devront ultérieurement être supprimées mécaniquement. Gardez cela à l'esprit si la surface inférieure de la pièce est critique.
Le placement et la quantité sont entièrement personnalisables, mais dépendront de la géométrie. De toute évidence, vous voudrez vous concentrer sur les zones de la construction qui ont pu avoir des problèmes dans le passé.
Avant de générer des supports, commencez le processus en accédant au Support Menu et sélectionnez Colonne d'ancrage .
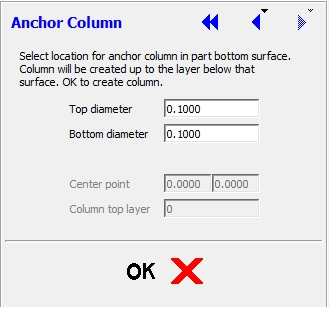
Dans la vue de dessus, sélectionnez le point central souhaité et cliquez sur OK. Insight ajoutera un contour circulaire, qui localise la colonne d'ancrage. Une fois que vous avez confirmé le placement et créé des supports, descendez dans les couches de support de base et remarquez les colonnes d'ancrage. Ce processus peut être répété pour autant de colonnes d'ancrage supplémentaires que nécessaire.
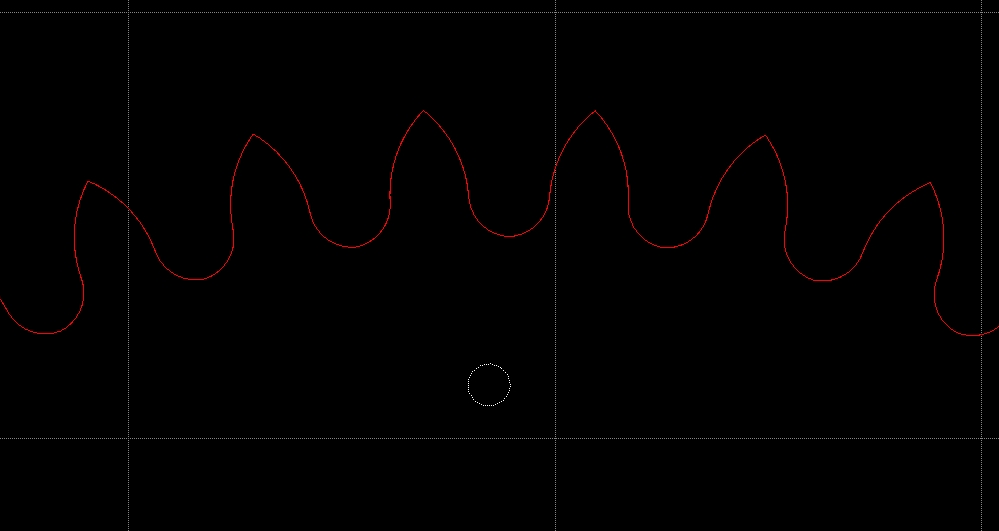
Une fois les supports et les parcours d'outils générés, vous remarquerez la colonne dans toute sa splendeur.
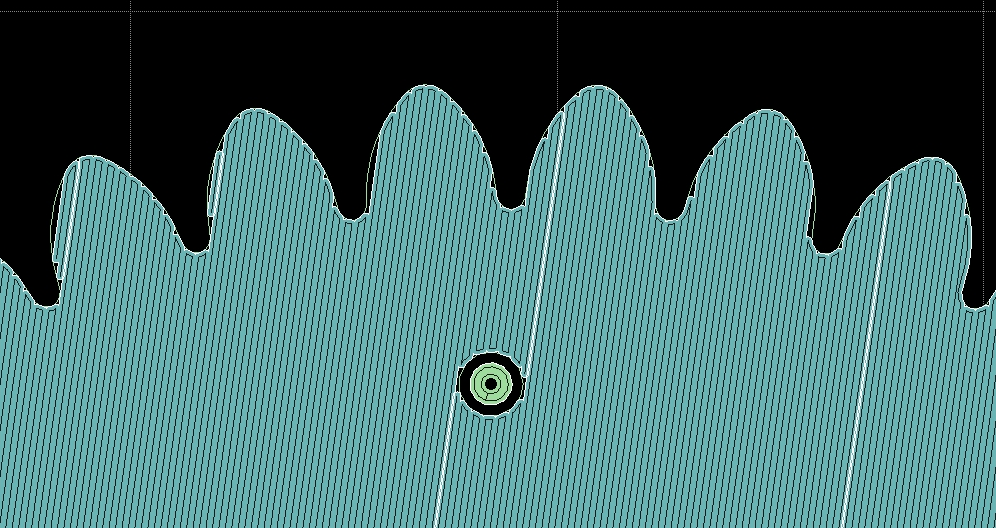
Comme je l'ai mentionné plus tôt, l'utilisation de combinaisons de ces options produira les résultats les plus favorables. Dans une application récente, notre client a combiné les deux paramètres de l'option 1 et a ajouté plusieurs colonnes d'ancrage. Ils ont pu réduire la courbure des pièces de 0,020" à 0,009" ; ce qui était bien dans leur tolérance.
Si vous rencontrez une boucle partielle, même après avoir utilisé ces options, nous pouvons fournir une assistance supplémentaire pour les applications et une formation avancée Insight. Veuillez nous contacter pour plus d'informations.
Bon traitement !
Tags :Colonnes d'ancrage, Technologie FDM, Insight Software, Thermoplastiques, Parcours d'outils
impression en 3D
- 5 types courants de poignées en T :ce que vous devez savoir
- Une introduction aux pinces à orteils :ce que vous devez savoir
- Structures de support d'impression 3D :les éléments clés que vous devez savoir
- Les 5 principales erreurs de fichier STL à connaître avant d'imprimer
- 7 bibliothèques React que vous devriez connaître
- Revêtement d'embrayage :tout ce que vous devez savoir
- Ce que vous devez savoir sur le moulage de métal
- Termes de base du jet d'eau que vous devez connaître
- Qu'est-ce que le moletage ? Voici ce que vous devez savoir