Une introduction à la fabrication additive à l'arc métallique [Mise à jour 2020]
La fabrication additive filaire (WAAM) est l'une des technologies d'impression 3D métalliques les moins connues, mais qui recèle un potentiel énorme pour les applications d'impression 3D à grande échelle dans plusieurs secteurs.
Ce guide se concentrera sur le fonctionnement de WAAM, ses avantages et ses limites, ainsi que sur les principales entreprises WAAM et les applications réussies.
Comment fonctionne la fabrication additive Wire Arc ?
WAAM est une variante d'une technologie de dépôt direct d'énergie et utilise un procédé de soudage à l'arc pour imprimer en 3D des pièces métalliques.
Contrairement aux procédés AM de poudre métallique plus courants, WAAM fonctionne en faisant fondre un fil métallique en utilisant un arc électrique comme source de chaleur.
Le processus est contrôlé par un bras robotisé et le la forme est construite sur un matériau de substrat (une plaque de base) dans lequel la pièce peut être découpée une fois terminée.
Le fil, une fois fondu, est extrudé sous forme de billes sur le substrat. Au fur et à mesure que les perles se collent, elles créent une couche de matériau métallique. Le processus est ensuite répété, couche par couche jusqu'à ce que la pièce métallique soit terminée.
Vous pouvez voir le processus en action ici :
Matériaux
WAAM peut travailler avec une large gamme de métaux, à condition qu'ils soient sous forme de fil. Cette liste comprend l'acier inoxydable, les alliages à base de nickel, les alliages de titane et les alliages d'aluminium. Tout métal pouvant être soudé peut également être utilisé avec WAAM.
Les avantages de la fabrication additive Wire Arc
La possibilité d'imprimer en 3D de grandes pièces métalliques
WAAM est particulièrement adapté à la fabrication de pièces métalliques de grande envergure. Cela contraste avec les technologies AM en métal par fusion sur lit de poudre (PBF), qui produisent généralement des composants haute définition plus petits.
Contrairement aux machines PBF AM, qui ont une enveloppe de construction limitée, le bras robotique d'une machine WAAM a plus de liberté de mouvement, ce qui signifie que la taille d'un composant n'est pas limitée par l'espace, mais seulement par la distance que le bras robotique peut atteindre. Cela permet la production de pièces plus grandes, ce qui ne serait pas possible avec les processus PBF.
Processus et matériaux moins chers
En termes de coût des matériaux, le fil de soudure utilisé dans le processus d'impression WAAM est nettement moins cher que la poudre métallique utilisée dans le métal PBF.
C'est parce que la technologie WAAM est basée sur le soudage, un procédé bien établi technologie de fabrication en soi. Le matériel WAAM comprend généralement un équipement de soudage standard, qui est moins cher que de nombreuses imprimantes 3D métalliques disponibles sur le marché.
De plus, le fil est généralement plus facile à manipuler que la poudre, qui nécessite un équipement de protection spécialisé. utiliser.
Pièces de haute qualité
Les pièces produites avec WAAM sont particulièrement remarquables pour leur haute densité et leurs propriétés mécaniques élevées, comparables aux pièces fabriquées avec des méthodes de fabrication traditionnelles.
Comme la matière première du fil est un matériau d'entrée 100 pour cent dense, il y a une porosité négligeable induite dans le processus de fabrication, conduisant à une pièce finale très dense.
Il convient aux opérations de réparation
WAAM est également une bonne option pour les opérations de réparation et de maintenance de composants spécifiques tels que les aubes de turbine, ainsi que les moules et les matrices.
Les éléments usés ou les pièces endommagées peuvent être réparés avec WAAM en déposant un nouveau matériau à sa surface. Cela peut entraîner des économies importantes car il élimine le besoin de produire une nouvelle pièce à partir de zéro.
Les limites de WAAM
Contraintes et distorsions résiduelles
L'un des défis associés à WAAM est la gestion de la chaleur.
Le processus d'impression implique des températures élevées, provoquant l'accumulation de contraintes résiduelles - un problème couramment rencontré avec l'impression 3D métallique. Comme les contraintes résiduelles peuvent souvent entraîner des déformations dans un composant, le refroidissement doit être pris en compte dans le processus.
Certains matériaux nécessitent un blindage
Lors de l'utilisation de certains matériaux, comme le titane, un blindage est nécessaire pour créer une atmosphère inerte afin de garantir les bonnes conditions de construction.
Cela signifie que le processus doit avoir lieu dans une chambre à gaz inerte. Cependant, la chambre à gaz inerte limite la taille des pièces qui peuvent être produites avec cette technologie et l'installation d'une telle chambre augmentera le coût de l'équipement.
Basse résolution
WAAM produit généralement des pièces de forme presque nette avec une mauvaise finition de surface. La surface d'une pièce doit donc être finie par usinage.
Acteurs clés WAAM et applications technologiques
WAAM3D
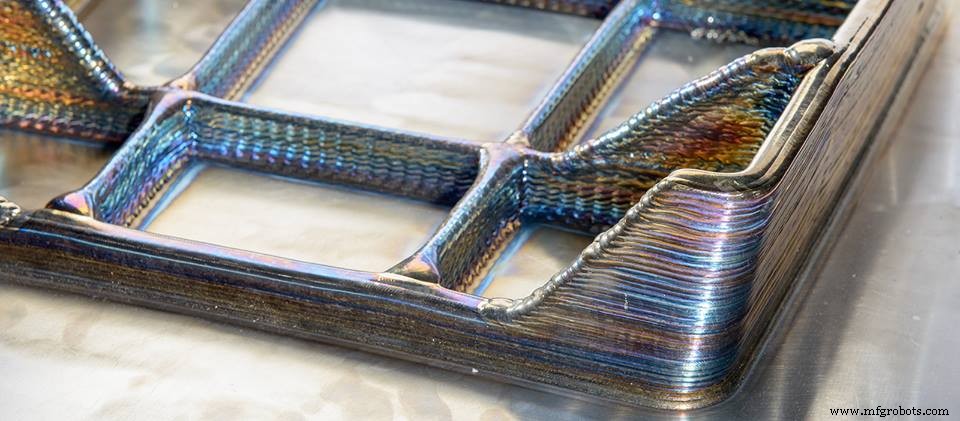
En 2020, le marché WAAM reste restreint, avec une poignée d'entreprises développant activement cette technologie d'impression 3D métal.
WAAM3D est peut-être l'un des noms les moins connus dans le domaine, mais la société a mené de nombreuses recherches avant de commercialiser sa technologie.
WAAM3D a été fondée en 2018 pour commercialiser la propriété intellectuelle de l'Université de Cranfield dans le domaine de WAAM.
Selon l'entreprise, le manque de chaîne d'approvisionnement - à savoir les outils logiciels, le matériel conçu par WAAM, les matières premières, la formation et les services - a entravé l'adoption industrielle méritée des processus WAAM, malgré ses avantages commerciaux prouvés .
La société vise à créer une telle chaîne d'approvisionnement et à promouvoir l'utilisation de WAAM dans les secteurs de l'aérospatiale et de la défense, du pétrole et du gaz, de l'énergie et du nucléaire.
Jusqu'à présent, WAAM3D a publié plusieurs applications réussies de sa technologie.
L'un est un cadre arrière pour le chasseur Eurofighter Typhoon de BAE Systems. La pièce en titane, qui mesure 2,5 mx 1,5 m de surface plane, supporte les deux moteurs Eurojet EJ200 capables de produire 60 kN (13 500 lbf) de poussée sèche.
Une autre pièce en titane, une pression de 1 m de long navire, a été fabriqué pour Thales Alenia Space. En utilisant WAAM pour fabriquer ce composant, l'équipe a économisé plus de 200 kg de matériau par article et a pu consolider deux parties du navire en une seule.
De plus, la production de la pièce aurait pris plusieurs jours - une réduction significative du délai, car la pièce prend généralement plusieurs mois à produire.
Plus tôt cette année, WAAM3D a terminé son premier tour de financement de série A qui devrait amener l'entreprise à commercialiser la technologie WAAM.
AML3D
L'Université de Cranfield a inspiré la fondation d'une autre entreprise :AML3D. Le directeur général d'AML3D, Andrew Sales, a étudié à Cranfield et, fasciné par le potentiel de la technologie, a fondé un bureau de service WAAM en Australie en 2014.
En 2019, la société a obtenu la certification de l'organisme d'accréditation mondial de l'industrie du transport maritime, Registre du Lloyd's. Une fois la certification en place, AML3D a livré sa première pièce à un client maritime :un jeu de bagues d'usure en acier inoxydable martensitique.
Les pièces sont traditionnellement forgées et nécessitent une étape supplémentaire de post-traitement thermique. Ce processus augmente le délai d'exécution total jusqu'à six à huit semaines. Ces articles à long délai de livraison doivent être conservés dans un inventaire physique ou remplacés prématurément.
En utilisant WAAM, AML3D a pu fabriquer les anneaux pour le même coût, tout en réduisant le délai de livraison à quelques jours seulement. Il s'agit d'une amélioration critique pour les navires qui restent à quai pendant un temps limité.
Afin de développer davantage ses capacités, la société envisage maintenant de lancer une usine de production à Singapour à court terme. Ceci est motivé par la demande de la plaque tournante maritime de Singapour, car l'emplacement est une plaque tournante stratégique pour les routes de navigation commerciale.
Ramlab
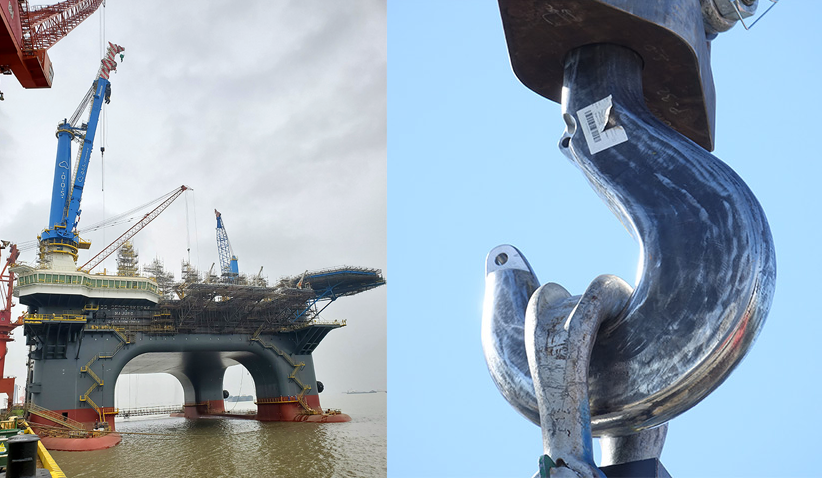
Dans la même veine, le laboratoire de fabrication additive du port de Rotterdam (RAMLAB) utilise WAAM pour accélérer la production de pièces marines. L’entreprise a fait sensation en 2017 en imprimant en 3D un prototype grandeur nature de l’hélice de navire approuvée de première classe au monde.
Le "WAAMpeller" utilise 298 couches d'alliage nickel aluminium bronze et pèse 400 kg. La partie a été achevée en sept mois — démontrant le potentiel de WAAM pour optimiser la production des futurs composants de navires.
En 2018, Ramlab, en collaboration avec Huisman Equipment, a lancé un autre projet d'impression 3D d'un grand crochet de grue, pesant près de 1000 kg. Huisman Equipment a poussé ce projet encore plus loin et a imprimé en 3D, certifié et installé un crochet WAAM de 36 000 kg, spécialement conçu pour être utilisé dans les opérations de levage offshore.
MX3D
L'une des premières applications qui a ouvert la technologie WAAM au monde était un pont en acier imprimé en 3D, développé par la start-up néerlandaise MX3D.
Le projet de pont, qui a débuté en 2018, a duré plus d'un an mais a servi de vitrine du potentiel de l'impression 3D métal à grande échelle.
Plus récemment, l'équipe MX3D a utilisé sa technologie pour imprimer en 3D un cadre de vélo en aluminium. Le cadre à l'allure futuriste a été conçu à l'aide d'un logiciel de conception générative et imprimé en 3D en deux parties en moins de 24 heures, mettant en valeur la vitesse d'impression élevée de la technologie WAAM de MX3D. MX3D a également développé une « configuration de montage intelligente », qui permettrait, semble-t-il, de préparer facilement tout cadre WAAM personnalisé pour la conduite.
Gefertec
L'entreprise allemande Gefertec est un autre acteur sur la scène WAAM. En 2017, elle a dévoilé sa technologie de fabrication 3DMP®, qui fait partie de la série de machines GTarc AM de Gefertec.
Le plus grand système comprend un système à 3 axes pour la production de pièces jusqu'à 3 m3 avec un maximum masse de 3000kg.
Ce qui est intéressant avec les machines Gefertec, c'est qu'elles peuvent être intégrées à un système de fraisage. Cela signifie qu'il est possible de créer un système hybride, où la technologie 3DMP® est utilisée pour créer une pièce, qui est ensuite immédiatement finie avec l'usinage.
Un exemple d'utilisation de la technologie de Gefertec consiste à imprimer en 3D un couvercle de roulement d'essieu en métal pour une locomotive. Ce modèle de locomotive a été mis en service dans les années 60 et 70, il peut donc être difficile de se procurer des pièces de rechange, qui ne sont souvent plus disponibles.
En conséquence, la livraison du composant prendrait traditionnellement jusqu'à neuf mois, et pendant ce temps, la locomotive serait hors service, entraînant des coûts élevés.
Gefertec's Une imprimante 3D a été utilisée pour produire cette pièce de rechange, et le projet, de la conception initiale à l'ingénierie inverse et à la production, a été achevé en deux mois. Bien qu'il s'agissait de la première production d'une pièce, avec un processus établi en place, il est possible de réduire encore plus le délai, potentiellement à quelques semaines seulement.
WAAM - l'option viable pour la fabrication additive métallique à grande échelle
Avec une technologie relativement nouvelle comme WAAM, le développement des applications prend du temps et les avantages se font sentir dans l'ensemble de l'industrie. Cependant, nous constatons une augmentation de la demande de grands composants métalliques imprimés en 3D, ce qui suggère que l'adoption de WAAM va s'accélérer.
En fin de compte, il est clair que WAAM transforme la façon dont les grandes pièces métalliques sont produites, offrant aux entreprises la possibilité d'une méthode de production plus rapide et plus rentable.
impression en 3D
- Fabrication additive vs fabrication soustractive
- Avantages de la fabrication additive
- Enquête sur les workflows de fabrication additive
- Entretien d'experts :Nanci Hardwick, PDG de MELD Manufacturing, sur la réalisation du potentiel de la fabrication additive métallique
- Fabrication additive métallique :5 questions à poser à un fournisseur potentiel de poudre métallique
- Épisode 3 du podcast sur la fabrication additive
- Fabrication additive dans les applications grand public
- Fabrication additive en électronique
- Fabrication additive dans l'aérospatiale