Impression 3D de moules CFRP pour flaperon RTM, exosquelettes et plus encore
Crédit photo :Chaire TU Munich des composites de carbone (LCC) et QPoint Composite
La Chaire de Carbon Composites (Lehrstuhl für Carbon Composites ou LCC) a été créée en 2009 dans le département de génie mécanique de l'Université technique de Munich (TUM, Munich, Allemagne) avec un financement de SGL Carbon (Wiesbaden, Allemagne). Sa mission est d'effectuer de la R&D sur des matériaux, des procédés et des applications en polymère renforcé de fibres de carbone (CFRP), y compris des projets de simulation et de test. Une « chaire » dans le système universitaire allemand est la plus petite unité comprenant un professeur et son équipe. L'équipe du LCC est dirigée par le Prof. Dr. -Ing. Klaus Drechsler et emploie actuellement 30 chercheurs à temps plein. Bien que le financement de SGL ait pris fin en 2016, le LCC a maintenu son leadership dans la R&D sur les composites, qui comprend la construction du moule pour la moitié inférieure du Multifunctional Fuselage Demonstrator (MFFD), voir l'encadré ci-dessous, et comprend désormais également l'impression 3D/additif fabrication.
Ce blog a commencé lorsque CEAD (Delft, Pays-Bas) m'a informé que LCC avait acheté l'un de ses systèmes flexbot AM basés sur une extrudeuse pour l'impression 3D à l'aide d'un bras robotisé. Mon entretien ultérieur avec Patrick Consul, chercheur au LCC, a cependant révélé un trésor de projets, dont COMBO3D, au sein de Clean Sky 2, pour imprimer en 3D un moule RTM en composite thermoplastique pour la production d'un flaperon d'avion en composite thermodurcissable, et EMOTION pour produire l'outil. pour mouler la moitié inférieure du démonstrateur de fuselage multifonctionnel en composite thermoplastique (MFFD) de Clean Sky 2 ainsi qu'un outil partiel secondaire pour démontrer comment le même fuselage pourrait être produit par consolidation directe in situ (hors autoclave). J'ai trouvé toute la discussion sur la façon dont TUM a atteint ce point et où elle se dirige pour être intéressante.
Moitié inférieure MMFD
Voir mon blog de février 2020 :"Proving out LM PAEK Welding for Multifunctional Fuselage Demonstrator". Cet encadré est tiré de l'article de février 2020, « Développement d'un démonstrateur de fuselage multifonctionnel » par Bas Veldman, responsable de programme pour le MFFD chez GKN Fokker (Hoogeveen, Pays-Bas).
La coque de la moitié inférieure du MFFD est constituée d'une peau thermoplastique, rigidifiée par des longerons soudés, des clips et des cadres. Le processus de fabrication à démontrer comprend trois étapes clés :
- Le ruban préimprégné pour la grande peau du démonstrateur est posé sur une table plate et inclinée par la machine AFP laser existante de NLR.
- Les layups sont transportés de manière robotique avec des ventouses vers un moule de consolidation femelle et y sont drapés sans chauffage.
- Après mise sous vide, la peau est consolidée en autoclave.
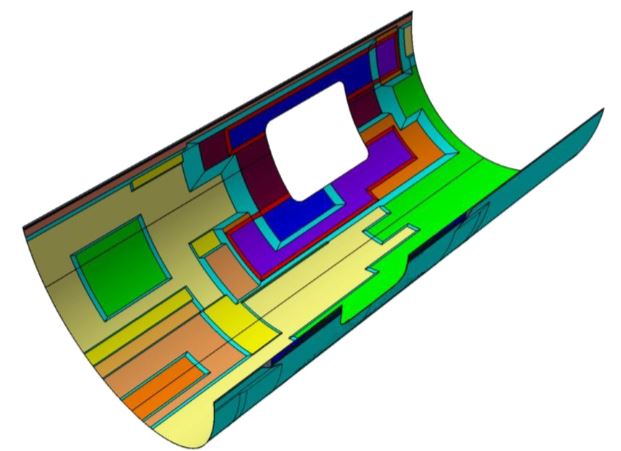
L'utilisation d'un moule de consolidation femelle offre une surface (plate) beaucoup plus simple que pour un outil mâle tout en contrôlant directement les contraintes aérodynamiques sur la qualité de la surface externe de la peau.
Le projet MFFD fait également appel au hors autoclave processus à étudier — en commençant parallèlement au grand démonstrateur de fuselage multifonctionnel — dans un démonstrateur ultérieur de plus petite taille. En particulier, composite thermoplastique in-situ une fabrication dans laquelle la consolidation est réalisée pendant le drapage, sera considérée, car elle peut éliminer complètement l'étape d'autoclave, et donc réduire la fabrication à une procédure en une seule étape.
Enhanced Mold for Thermoplastic Fuselage in and out of Autoclave Consolidation, ou EMOTION (https://cordis.europa.eu/project/id/864474), est le projet Clean Sky 2 pour la production de l'outillage de coque inférieure MFFD. « Cela semble simple », explique Patrick Consul du coordinateur du projet, TU Munich, « mais c'est en fait assez difficile car il doit être chauffé à 400 °C. C'est bien au-dessus de la plage de température dans laquelle l'Invar36 n'a pas de CTE [coefficient de dilatation thermique] significatif. » L'invar est couramment utilisé pour les outils de moulage composites en raison de sa faible expansion pendant les cycles de durcissement à haute température. Cependant, le CTE de l'Invar augmente avec la température. « Le défi », note le consul, « sera de contrôler la dilatation thermique pendant le chauffage et le refroidissement pour le moule de 8 mètres sur 4 mètres et la peau du fuselage pendant le durcissement. »
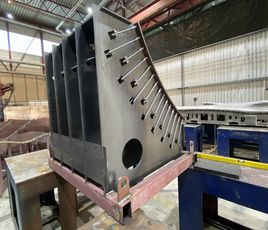
Progression en fabrication additive
« Nous sommes 8 à 9 personnes à travailler sur la fabrication additive au sein du LCC », précise le Consul. Il commence l'histoire de ce travail avec l'achat par le LCC d'une machine de placement de ruban composite thermoplastique assistée par laser à l'AFPT (Dörth, Allemagne) en 2012. Il a ensuite ajouté une machine Coriolis Composites (Quéven, France) pour permettre le placement automatisé des fibres (AFP ) de préimprégnés thermodurcissables. Les premières imprimantes de bureau à filament ont été achetées en 2017. « J'ai également rejoint en 2017 pour aider au développement de nouvelles applications et projets de recherche, y compris la rédaction de propositions, par exemple, pour Clean Sky 2. » Il explique que les projets Clean Sky 2 sont attribués sur la base de propositions soumises aux responsables thématiques en réponse à des appels à propositions (CFP) rendus publics. LCC a réussi ses propositions pour le projet CFP08 COMBO3D et le projet CFP09 EMOTION. Les deux sont discutés ci-dessous.
«Nous avons quelques autres projets, certains portant sur l'impression 3D avec des renforts en fibres continues», explique Consul. « D'autres utilisent une tête d'impression intégrée au laser pour préchauffer le substrat composite afin d'imprimer sur des pièces CFRP déjà consolidées ou pour augmenter la résistance au cisaillement interlaminaire (ILSS) entre les couches imprimées. Un autre projet explore les applications d'outillage, par exemple, où vous avez un faible nombre de pièces composites spécialisées. "
« Ces projets sont soutenus en permanence par des simulations numériques afin de prédire le comportement des pièces fabriquées en additif pendant et après le processus d'impression », poursuit-il. « Le LCC est également impliqué dans un projet avec l'Imperial College de Londres qui vise à fabriquer des exosquelettes à l'aide de CFRP imprimés en 3D. Un autre projet étudie les structures en treillis afin d'optimiser les propriétés des pièces imprimées en 3D en termes de rigidité, de résistance ou d'absorption d'énergie. »
Progression dans les imprimantes

« Nous avons commencé par utiliser une simple imprimante 3D basée sur le FDM (fused depositionmodeling) d'Apium (Karlsruhe, Allemagne) pour imprimer des montages de test spécialisés nécessitant une rigidité élevée », explique Consul. « L'imprimante mesurait 3 mètres de long sur 1 mètre de large avec une sortie de matériau élevée pour réduire le temps d'impression. Bien qu'il ne puisse pas utiliser de fibre continue, il était bien conçu pour l'impression avec du PEEK, du PEKK et du PEEK renforcé de fibres de carbone haché. Il utilisait non seulement un lit chauffant, mais également une plaque chauffante autour de la tête d'impression, ce qui aidait à produire une répartition homogène de la température dans les impressions, réduisant ainsi le stress thermique et assurant la cristallisation.
« Nous avons également eu une imprimante Markforged (Cambridge, Mass., États-Unis) pendant un certain temps, puis nous avons obtenu une Anisoprint [Esch-sur-Alzette, Luxembourg] », explique le consul. Bien que l'imprimante Markforged ait activé le FDM avec fibre continue, l'équipe LCC a choisi de ne pas le conserver. « Le problème que nous avions était que le système était très fermé », explique le consul. « Le logiciel de découpage de Markforged était trop difficile à utiliser pour la recherche car il limitait considérablement ce que nous pouvions faire. Nous ne pouvions imprimer qu'une couche de matériau à fibres continues, puis une couche de filament thermoplastique court renforcé de fibres sur le dessus. Le slicer qui génère le code n'accepterait pas le G-code de notre part. Donc, il n'y avait aucun moyen de dire à la machine de l'imprimer comme nous le voulions avec de la fibre continue dans chaque couche, etc. »
Interrogé à ce sujet, Markforged explique que ses systèmes n'ont jamais été destinés à être utilisés pour la recherche, mais plutôt conçus pour être simples et robustes pour une utilisation généralisée dans la fabrication de pièces, en utilisant un cheminement de fibre basé sur des règles et nécessitant peu d'efforts et de temps pour configurer la trancheuse. . C'est Le logiciel Eiger permet aux utilisateurs de configurer les couches individuellement, et Markforged accueille les commentaires et donne la priorité à l'amélioration de l'expérience utilisateur pour ses clients.
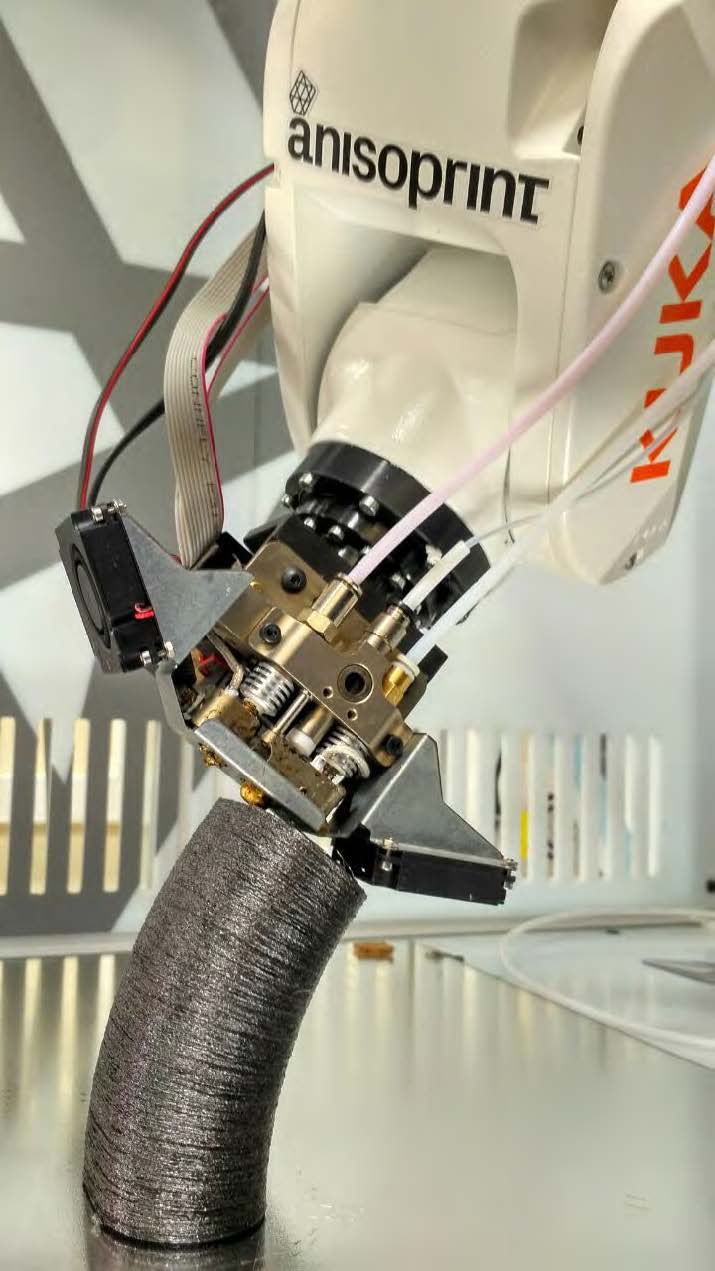
« Anisoprint, qui utilise un slicer de code G complètement ouvert, nous a donné un meilleur accès au processus », explique Consul. « Elle est également capable d'imprimer de la fibre de carbone continue et pas seulement en couches 2D, mais aussi hors plan, en courbes 3D. Nous avons une tête d'impression Anisoprint pour un petit robot Kuka, capable de produire des pièces de 1 mètre sur 1 mètre, ce qui est plus grand que la plupart des ordinateurs de bureau, mais petit pour un système de robot."
Mais qu'en est-il de la double matrice d'Anisoprint matériaux thermodurcissables-thermoplastiques (TS-TP) ? Comme expliqué dans mon blog 2019 sur Anisoprint « … il imprègne d'abord le renforcement de fibres continues avec un thermodur polymère, puis l'extrude dans le filament thermoplastique fondu pendant l'impression. Le consul répond que l'adhérence entre le filament TS et le TP est plutôt bonne. « Lors de nos premiers essais, nous pouvions obtenir un contenu en volume de fibres plus élevé par rapport à l'imprimante Markforged, mais c'était parce que nous pouvions modifier le code G. La tête d'impression Anisoprint pousse le filament TS dans le TP puis le pose. Nous prévoyons d'utiliser cette imprimante pour les pièces d'exosquelette. C'est un moyen facile d'intégrer des fibres plus résistantes."
Imprimantes à granulés extrudés
La progression suivante était vers une imprimante à grande échelle, d'abord avec un TP renforcé de fibres courtes, puis un TP à fibre continue. « Nous avons d'abord développé une extrudeuse montée sur un robot, puis notre intérêt pour la machine CEAD a rapidement suivi. Nous espérons intégrer la fibre continue dans ces deux systèmes l'année prochaine. »
Mais pourquoi aviez-vous besoin de la machine CEAD si vous aviez déjà une extrudeuse sur un bras robotisé ? « L'extrudeuse initiale était la version bêta d'une extrudeuse à granulés Dyze Pulsar, qui produit un maximum d'environ 2 kg/h et environ 1 kg/h avec les PAEK, mais elle a du mal avec plus de 20 % de charge en fibre de carbone », explique Consul. « Cependant, le rendement moyen est inférieur car le robot accélère et décélère souvent pendant l'impression. Pour COMBO3D, les premières moitiés de moules à petite échelle nécessitaient déjà au moins 36 kilogrammes, il nous a donc fallu environ 48 heures pour imprimer une seule moitié. Nous devions également toujours avoir quelqu'un avec, car des erreurs, comme une ligne d'alimentation de matériau bloquée ou un gauchissement des pièces, pouvaient se produire à tout moment. »
Parce que le démonstrateur final COMBO3D est environ 10 fois plus grand que les pièces initiales à petite échelle, il n'était pas possible de l'imprimer à l'aide de ce premier système d'extrusion, explique Consul. « De plus, certains des matériaux que Victrex nous a fournis avaient une viscosité plus élevée et cette première extrudeuse ne pouvait pas fournir suffisamment de couple pour extruder ces polymères. Avec l'imprimante CEAD, nous avons un rendement maximum d'environ 12,5 kg/h, et après quelques heures d'essais, nous avons eu un rendement moyen stable d'environ 5-6 kg/h. Cela nous a permis d'imprimer le moule à petite échelle de moitié en moins de 8 heures et nous permet d'utiliser des teneurs en fibres plus élevées pour réduire le gauchissement, rendant le processus global plus facile à contrôler. »
« Alors que le Pulsar nous a déjà permis d'utiliser des granulés, d'obtenir un rendement de matière élevé et de tirer parti des degrés de liberté d'un robot », poursuit-il, « l'imprimante CEAD étend nos capacités vers des pièces plus grandes, des teneurs en fibres plus élevées et une plus large gamme de polymères . Le Pulsar comble le fossé entre nos imprimantes à filament et le CEAD, non seulement en termes de sortie, mais également en termes de taille de buse et de détails résultants des impressions. »
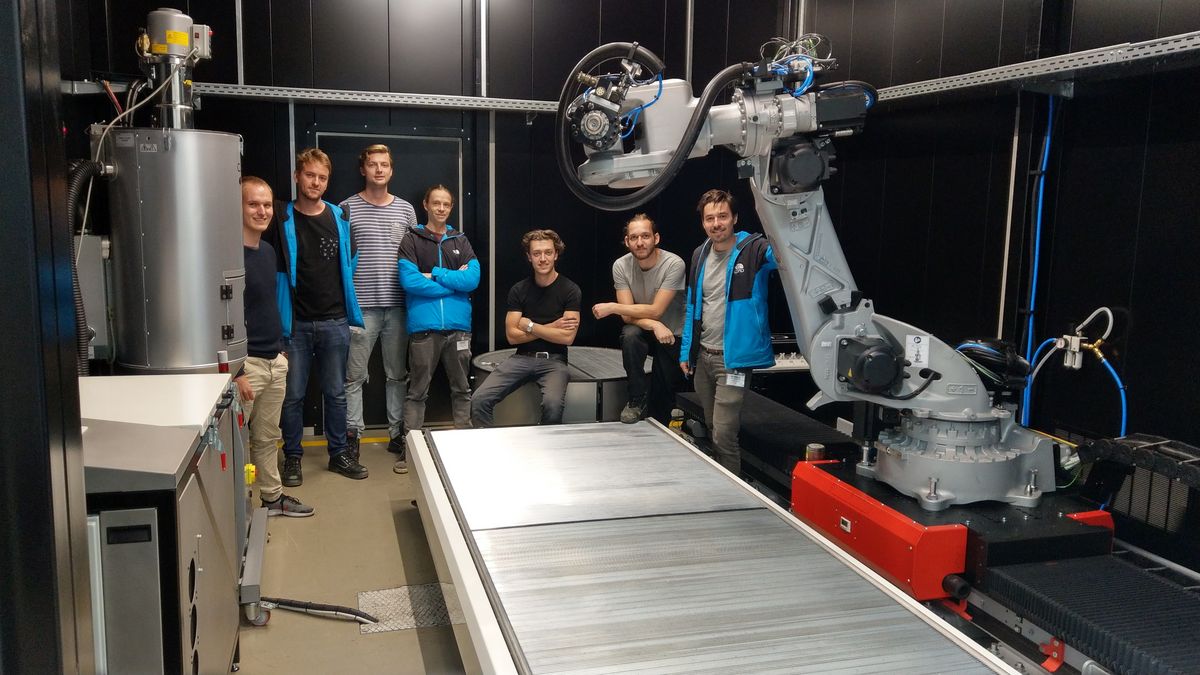
Données techniques du CEAD AM Flexbot :
- Données techniques AM Flexbot :
- Impressions par extrusion à base de granulés jusqu'à 12,5 kg/h (non renforcés et renforcés de fibres courtes)
- Traitement de matériaux jusqu'à 450 °C
- Volume de construction 3000 x 1200 x 1700 millimètres
- Construire une plaque sur une table rotative ou une table plate (chauffable)
- Reprise au moyen d'une tête de fraisage.
COMBO3D
L'objectif de ce projet Clean Sky 2 est d'imprimer en 3D un moule pour produire un flaperon composite de démonstration (1,5 mètres sur 3) pour un gros avion de ligne, faisant partie du Work Package A-3.1 :Aile multidisciplinaire pour haute et basse vitesse. L'objectif de l'utilisation de la fabrication additive est de raccourcir les délais de production d'outils. Le projet a débuté en janvier 2019 et se terminera en mars 2021. Les partenaires incluent Alpex Technologies (Mils bei Hall, Autriche), le spécialiste des métaux légers Leichtmetallkompetenzzentrum Ranshofen (Ranshofen, Autriche) et Victrex (Thornton Cleveleys, Royaume-Uni), fournisseur du thermoplastique haute performance polyaryléthercétone (PAEK).
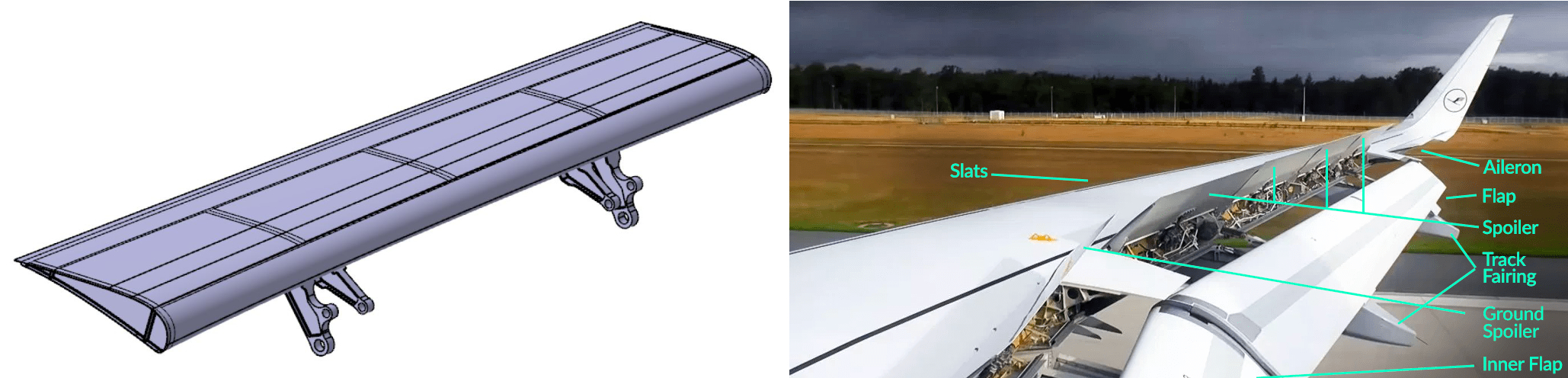
Un autre élément clé du projet consiste à démontrer que ce flaperon en fibre de carbone/époxy peut être fabriqué avec un moulage par transfert de résine (RTM) au lieu d'un préimprégné durci à l'autoclave. La pièce RTM durcira aux mêmes 180°C que les pièces de l'autoclave. Pour assurer la stabilité thermique, l'outil sera imprimé avec du PAEK court renforcé de fibres de carbone, qui a une température de fusion de 305°C.
Afin de raccourcir le cycle de durcissement, le moule imprimé en 3D intégrera un contrôle actif de la température. « Nous devons pouvoir chauffer et refroidir le moule plus rapidement par rapport à l'autoclave », note Consul. «Nous utiliserons un maillage d'éléments chauffants électriques à 3 millimètres sous la surface du moule et intégrerons également des canaux imprimés pour l'huile ou l'air chauffés à 6 millimètres sous la surface du moule. De cette façon, nous pouvons chauffer la surface du moule très rapidement mais également utiliser les canaux pour chauffer dans tout le volume de l'outil. Nous visons une vitesse de chauffage et de refroidissement 50 % plus rapide que l'autoclave et nous sommes convaincus que nous pouvons atteindre une vitesse au moins 30 % plus rapide."
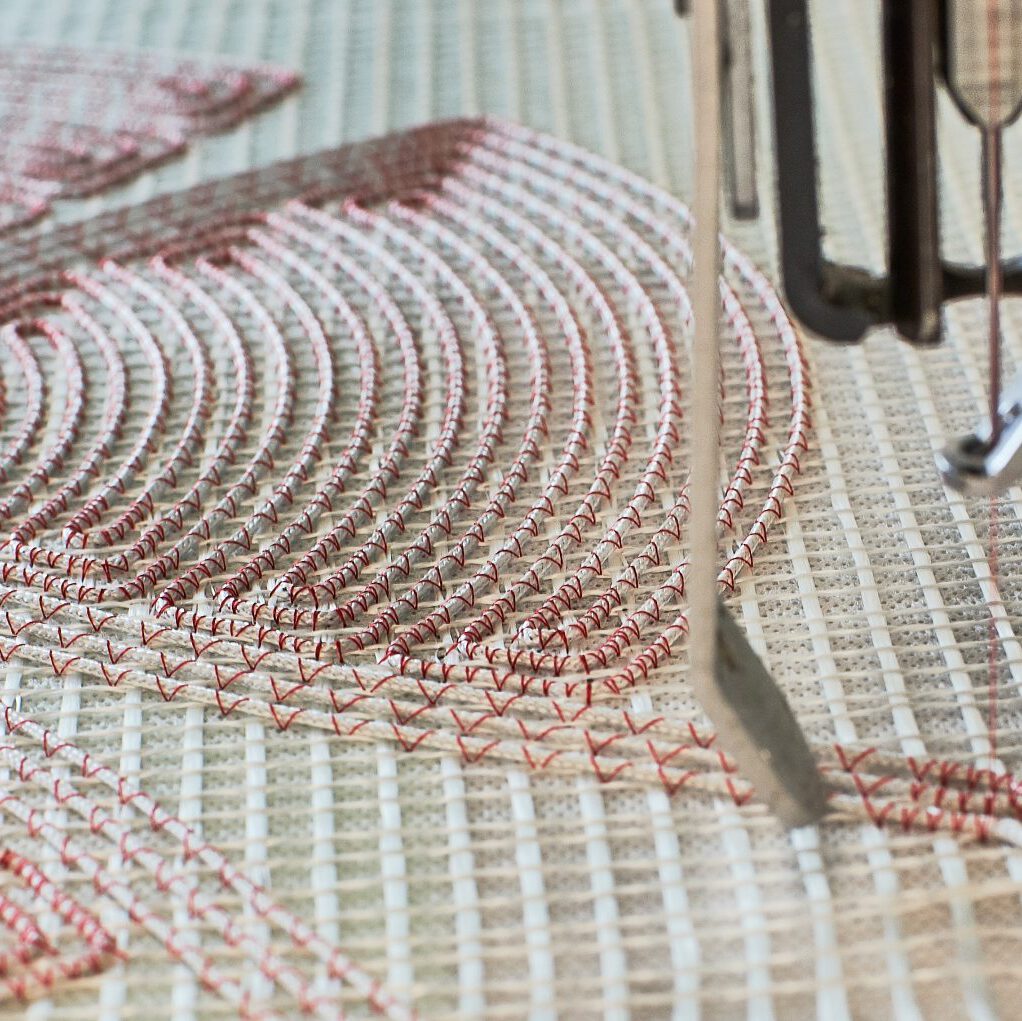
Quels sont les éléments chauffants à intégrer dans l'impression 3D ? "Nous avons utilisé le placement de fibres sur mesure (TFP) de mèches de carbone sur un textile en fibre de verre comme éléments chauffants pour réaliser différentes zones de chauffage dans un moule en CFRP pour une pale de rotor d'hélicoptère", explique Consul. « C'était pour un projet Clean Sky 1 que nous avons réalisé en collaboration avec QPoint Composite (Dresde, Allemagne). Nous allons travailler avec un concept similaire sur le moule COMBO3D. »
L'ensemble du développement de l'outil imprimé est soutenu par la simulation. La conception de l'outil sera optimisée en mettant en œuvre le système de chauffage et de refroidissement dans une simulation thermique. Le processus de fabrication sera également simulé, soutenant le processus d'impression en générant des connaissances sur la distribution de la température pendant l'impression et en la corrélant avec la planification du chemin.
Installation de la machine CEAD et avancement du projet
« Le système CEAD a été livré très rapidement – de la commande à l'installation, il n'a fallu que 6 mois », explique Consul. « À ce moment-là, nous avions terminé les tests de matériaux, conçu l'outillage des plaques et commencé à imprimer de petites pièces. Nous craignions que cela prenne beaucoup de temps pour que le processus fonctionne correctement avec le CEAD AM Flexbot, mais cela a bien fonctionné avec les premiers essais. »
Outillage de plaque ? "C'est un petit moule, intégrant déjà des canaux de refroidissement et des éléments chauffants pour produire des plaques CFRP pour les tests de coupons", explique-t-il. "Ces tests visaient à garantir que la qualité de notre moule CFRP RTM imprimé en 3D sera comparable au CFRP actuel que Saab produit avec son processus d'autoclave."
Malheureusement, le projet a été interrompu par COVID-19, « mais maintenant tout va bien et nous rattrapons notre retard », explique le consul. Et qu'en est-il de l'utilisation du PAEK pour le moule imprimé en 3D ? « Le seul problème actuellement est que la Tg [température de transition vitreuse] pour le PAEK est de 130 à 140 °C, ce qui est inférieur à la cure de 180 °C pour la partie de démonstration », note le consul. « Donc, nous devons encore voir combien de cycles nous pouvons effectuer à la température de durcissement avant que le fluage ne se produise ou que la surface ne soit endommagée. »
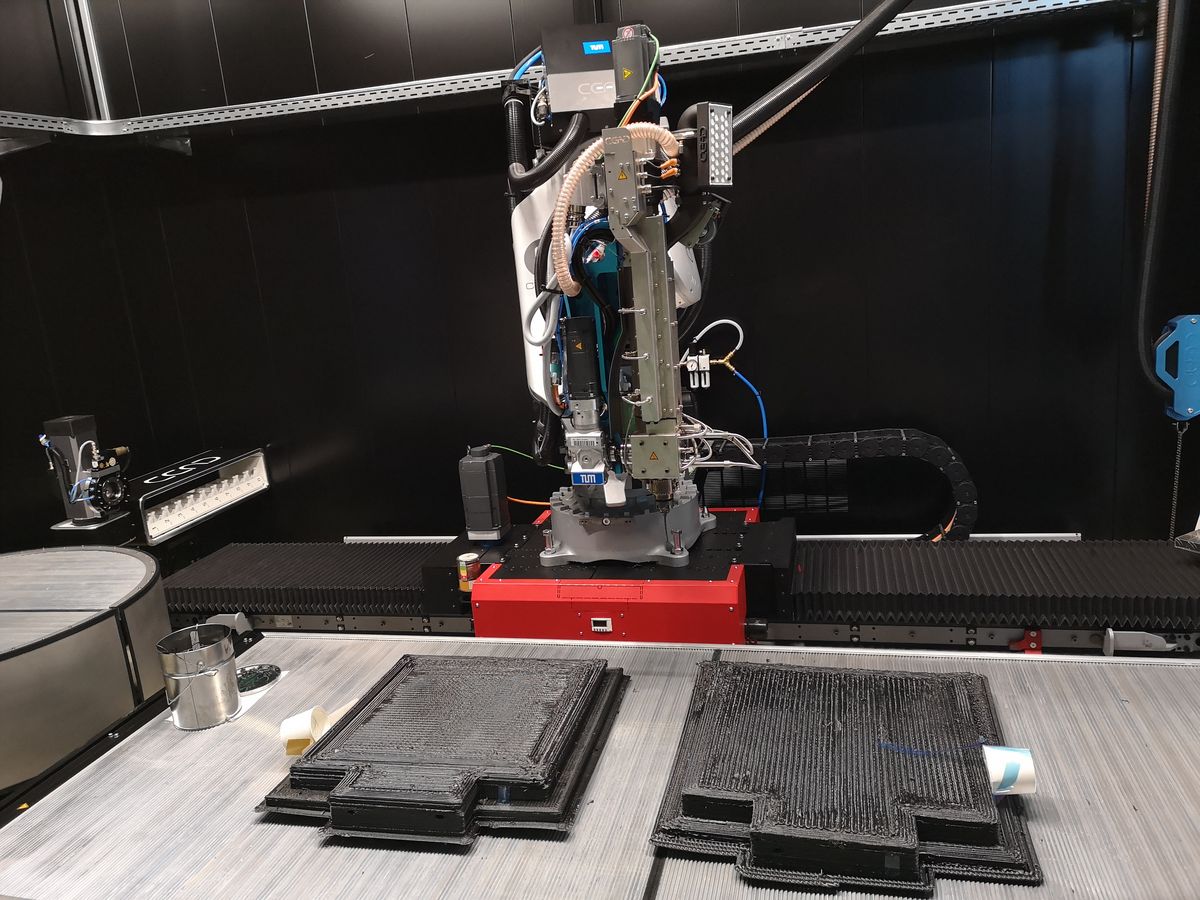
Machine CEAD dans d'autres projets ?
"Nous postulons à un projet d'outillage aérospatial qui démarre l'année prochaine avec GKN Aerospace Deutschland (Munich) en utilisant la machine CEAD et le polyéthersulfone (PESU)", a déclaré le consul. [Remarque :GKN en Allemagne fabrique des volets d'aile composites pour l'A330 et l'A350 ainsi que des ailerons pour la famille d'avions d'affaires Bombardier Global.] « CEAD fera partie de ce responsable du développement de la machine pour les fibres de carbone continues. Nous prévoyons également d'utiliser la machine CEAD en interne pour fabriquer des prototypes de moules pour RTM qui, autrement, auraient été sous-traités. Cela nous donne un avantage en accélérant le travail. »
Le consul note que PESU a une Tg plus élevée que PAEK. « Il est également amorphe, pas semi-cristallin, il devrait donc être plus facile à imprimer, bien que la résistance au fluage puisse être un problème. Ce que nous essayons de faire, c'est d'éviter le PEI (polyétherimide). Dans le passé, nous avons examiné la question du collage du PEI sur la résine époxy. Le RTM6 [époxy pour RTM] dissout le PEI, ce qui entraîne une bonne adhérence entre les deux. C'est exactement ce que vous ne voulez pas dans les moules imprimés en 3D qui doivent libérer les pièces, ne pas s'y coller. »
Futurs composites industriels (et volants) imprimés en 3D
En discutant de certains des autres projets que LCC poursuit dans le domaine de la fabrication additive, je demande à Consul ce qui a retenu le CFRP dans les exosquelettes ? "Parce que les exosquelettes doivent être adaptés à chaque porteur, les pièces sont spécialisées donc le volume n'est pas important", répond-il. « Notre projet vise à permettre la production de composants d'exosquelette des membres inférieurs spécifiques au patient pour permettre la production d'un exosquelette spécifique au patient en moins de 24 heures. Ces exosquelettes soutiendront la réadaptation des patients victimes d'un AVC en fonction de leurs profils biophysiques et de leurs besoins de réadaptation médicale uniques. » (Voir l'article CW, « L'exosquelette C-FREX dépend du CFRP… »)
« Les gens pensent que l'impression 3D peut imprimer n'importe quelle pièce, mais vous devez d'abord avoir de l'expérience avec l'impression 3D et les composites. Par exemple, il y a souvent des problèmes d'adhérence couche à couche et d'anisotropie qui doivent être compris. Les pièces composites imprimées en 3D ne seront pas de la même conception que celles actuellement fabriquées en plastique et en métal. »
Il note qu'il y a encore des problèmes à surmonter pour l'utilisation de composites imprimés en 3D pour la production de pièces d'avions hautes performances, par exemple :comment concevez-vous ces pièces pour la fabrication additive ? Comment identifier les pièces où la fabrication additive ajoute de la valeur ? « L'outillage aérospatial est le principal domaine d'applications que notre équipe étudie en ce moment », explique Consul. « L'impression 3D du moule s'adapte bien. Ces moules doivent résister aux mêmes conditions de durcissement que les pièces, mais il y a moins de risque associé aux moules par rapport aux pièces volantes. Un bon exemple est celui des raidisseurs de nervures pour les ailes, où il y a un grand nombre de pièces différentes mais peu de cycles par pièce. C'est donc un bon moyen de générer de l'expérience avec la technologie. Il est trop tôt pour essayer des pièces structurelles qui voleront. Nous visons cela à long terme, mais les outils d'impression nous permettront d'obtenir un processus d'impression 3D suffisamment stable avec des propriétés de haute performance et également de développer la capacité de prédire avec précision ces pièces et processus en simulation. »
Résine
- Solutions d'impression 3D pour les sociétés pétrolières et gazières
- DSM et Nedcam vont développer de nouvelles applications pour l'impression 3D grand format
- Maîtres de couleur acétal pour l'automobile et plus basés sur des transporteurs à faibles émissions
- Automatisation pour IML et Stack Molds
- Partenaire Victrex et Bond pour l'impression 3D de pièces PAEK
- Conseils pour les moules d'impression 3D
- Conseils pour l'usinage CNC du titane :Aéronautique et plus
- Formlabs contribue à rendre l'impression 3D plus accessible aux PME
- SIGRABOND® Chemical CFRP pour composants et assemblages