Barre d'armature composite pour future infrastructure
Dans le monde entier, les structures en béton sont attaquées comme jamais auparavant. Non seulement le trafic a augmenté sur les routes, les ponts et les viaducs, mais le changement climatique a augmenté les événements météorologiques extrêmes, notamment les tempêtes violentes et les pluies torrentielles qui entraînent des crues soudaines et d'autres événements destructeurs. Sous de telles contraintes, le béton peut se fissurer. Cela permet une détérioration rapide dans des environnements agressifs en raison de l'exposition à des éléments tels que l'eau salée, qui est corrosive pour les barres d'armature en acier.
« Les fissures créent des chemins pour que les agents des environnements agressifs atteignent l'acier d'armature et/ou de précontrainte et commencent le processus d'oxydation corrosive », explique le site Web d'innovation des structures du Florida Dept. of Transportation (FDOT, Tallahassee, Floride, États-Unis). « Une approche innovante pour lutter contre ce problème majeur consiste à remplacer les barres et torons d'acier traditionnels par un polymère renforcé de fibres (FRP). » FDOT a été un leader dans l'utilisation et les tests de barres d'armature en FRP, ainsi que dans le développement de normes de conception et d'utilisation, comme celles publiées par l'American Concrete Institute (ACI, Farmington Hills, Michigan, États-Unis). Bien que les barres d'armature composites soient principalement fabriquées avec de la fibre de verre (GFRP ou GRP), des produits ont également été développés à partir de basalte (BFRP) ou de fibre de carbone (CFRP).
« Avec une longue et coûteuse histoire de corrosion dans le monde entier, l'acier n'est plus considéré comme une option rentable dans les environnements agressifs », déclare Nick Crofts, PDG du fabricant de barres d'armature GFRP Mateenbar (Dubaï, Émirats arabes unis et Concord, Caroline du Nord, États-Unis). fournisseur pour le plus grand projet de barres d'armature GFRP au monde. Ce projet est le canal d'atténuation des inondations de 23 kilomètres de long et jusqu'à 80 mètres de large à Jizan, en Arabie saoudite. Bien que les barres d'armature en GFRP existent depuis 30 à 40 ans, selon Crofts, des projets clés comme le Jizan Flood Channel les propulsent maintenant dans les infrastructures grand public. Cette croissance justifie déjà les nouvelles usines de Mateenbar en Arabie saoudite et aux États-Unis.
Technologie pionnière des barres d'armature GFRP
La barre d'armature Mateenbar GFRP a été développée par Pultron Composites (Gisborne, Nouvelle-Zélande), un pionnier et spécialiste de la technologie de pultrusion et de l'innovation de produits. Mateenbar relève les défis uniques du marché des barres d'armature, qui exige non seulement un volume élevé et des prix bas, mais exige également que le produit soit spécifié par les architectes et/ou les ingénieurs du projet. Ainsi, la première usine de Mateenbar en 2008 a été construite à proximité de clients potentiels et de sociétés d'ingénierie de projet à Dubaï, aux Émirats arabes unis, une région connue pour ses grands projets d'infrastructure et son utilisation pionnière des composites dans la construction. Pultron reste un partenaire stratégique de Mateenbar et un fournisseur clé de technologies sur mesure et de développement de produits.
Étapes de fabrication
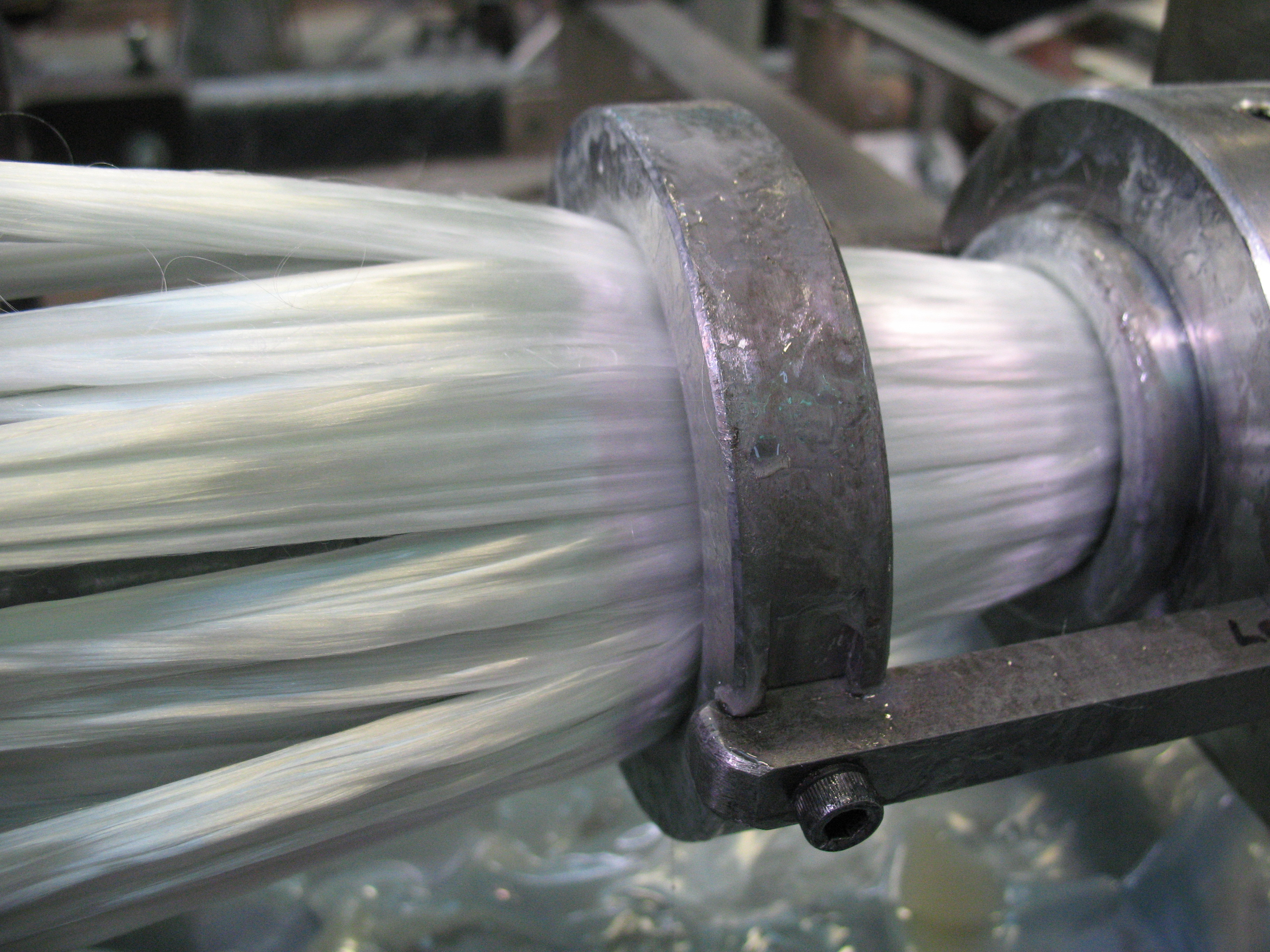
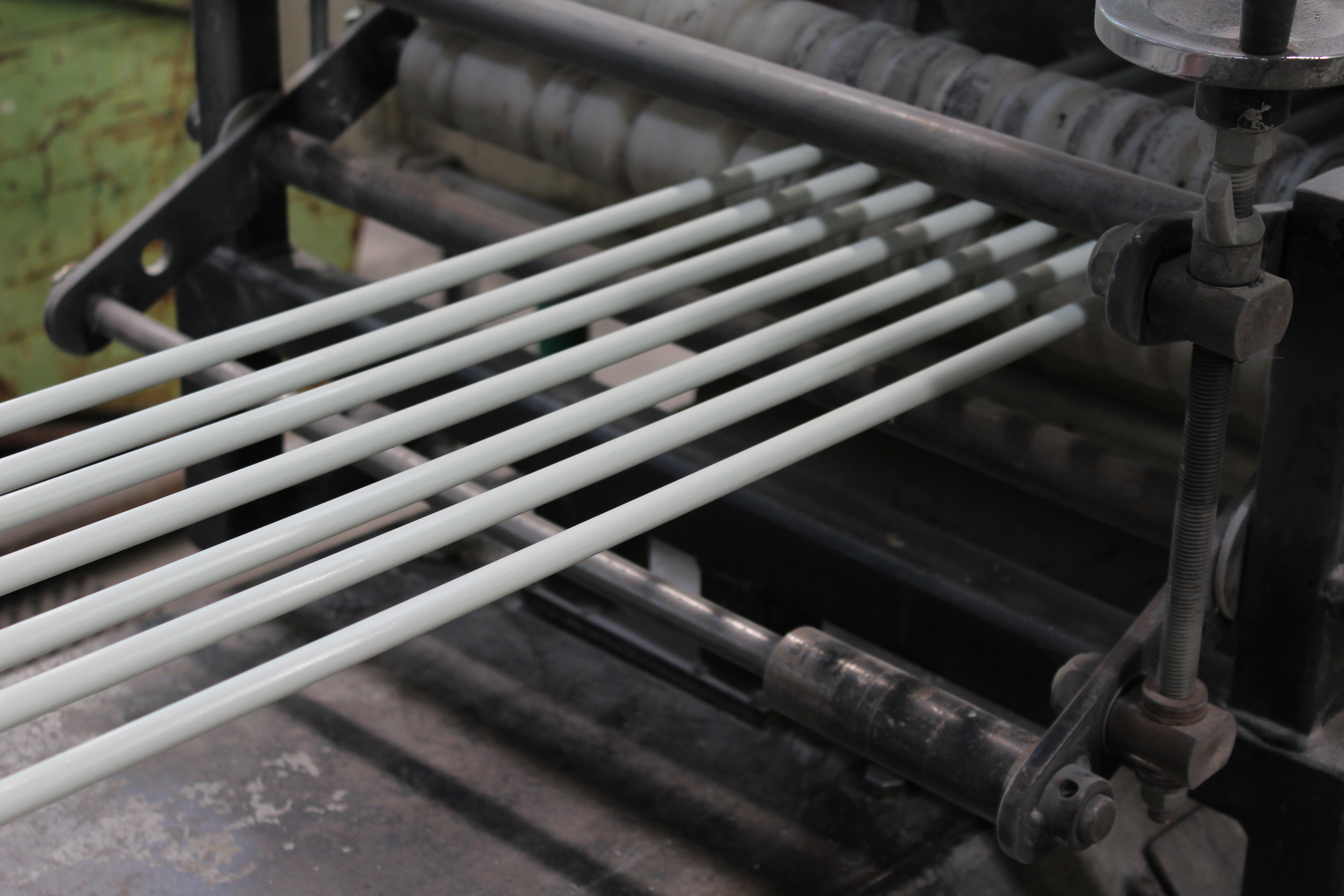
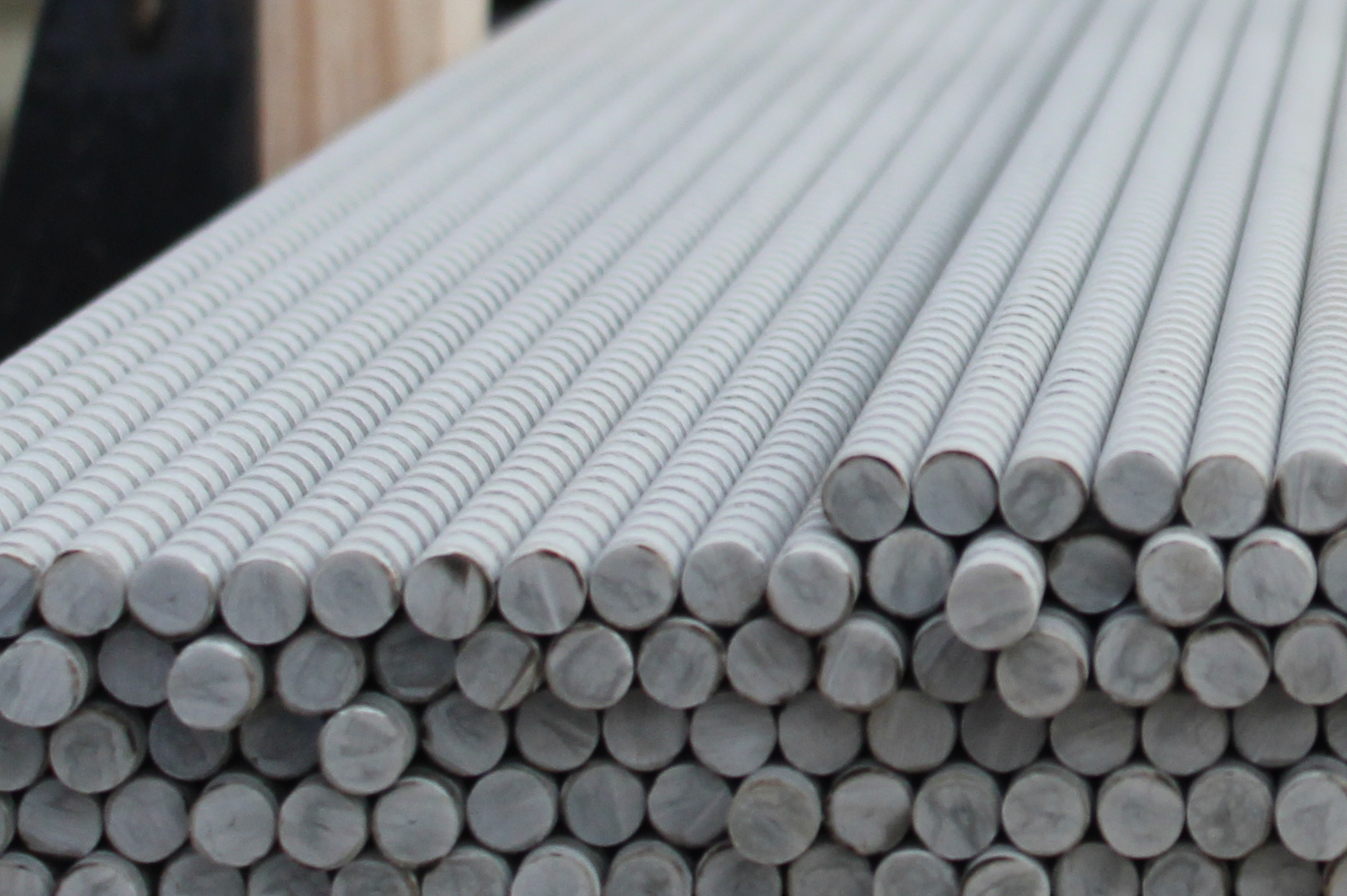
L'usine de Mattenbar utilise la technologie de pointe de Pultron pour produire des barres d'armature pultrudées très cohérentes à haut débit sans émissions de composés organiques volatils (COV). « Nous injectons de la résine et polymérisons à l'intérieur la matrice de pultrusion en acier d'ingénierie », explique Crofts.
« Cette barre d'armature est un produit d'ingénierie avec des performances dimensionnelles supérieures à ±1 % », ajoute-t-il. « Il n'y a aucune excuse pour voir de la résine sur le sol ou de la poussière dans l'air. La fibre utilisée est du verre ECR résistant à la corrosion d'Owens Corning (Toledo, Ohio, États-Unis) et la résine est notre propre variante d'un ester vinylique à dorsale époxy. Il maximise la ténacité, la résistance et la durabilité, et est de loin supérieur à une épine dorsale en polyester avec des terminaisons en époxy. »
Les tiges rondes pultrudées sont ensuite usinées pour créer un profil en spirale qui permet une adhérence porteuse à l'intérieur du béton. « C'est aussi une opération fermée », souligne Crofts, « utilisant des cabines d'usinage équipées de systèmes de filtration d'air Donaldson (Bloomington, Minn., États-Unis). Nous appliquons ensuite un film de résine à l'extérieur pour améliorer la prise en main. Les barres d'armature de Mateenbar sont produites dans des longueurs allant jusqu'à 80 pieds, coupées à la longueur requise. "Il est typique de voir des longueurs de 40 pieds pour la plupart des projets d'infrastructure et de construction", explique Crofts.
« Notre barre d'armature droite moyenne a un diamètre de 0,75 pouce, avec un module de traction de 8 700 ksi (60 GPa) en fibre de verre de 11 600 ksi (80-GPa) ; ainsi, la teneur en fibres est très élevée — plus de 80 % en poids. Il n'y a aucun moyen de le plier, c'est pourquoi notre barre d'armature pliée en GFRP est fabriquée à l'aide d'un processus et d'une résine différents, avec une technologie exclusive. »
Le plus grand projet de barres d'armature GFRP au monde
Jizan (également orthographié Jazan) est la capitale de la région de Jizan, située dans le coin sud-ouest de l'Arabie saoudite, au nord de la frontière avec le Yémen. Des crues soudaines catastrophiques se produisent lors de fortes pluies périodiques en raison du ruissellement des montagnes voisines. Le canal de drainage des eaux pluviales en béton armé de 23 km de long a été construit pour protéger une grande zone industrielle qui comprend une raffinerie de pétrole pour Saudi Aramco (Dhahran, Arabie saoudite).
Jusqu'à la pandémie de COVID-19, Saudi Aramco était la plus grande entreprise au monde en termes de chiffre d'affaires. Il gère toutes les activités pétrolières et dérivés du Royaume et représente également 10 % de toutes les constructions en Arabie saoudite. « Saudi Aramco s'est rendu compte qu'un pourcentage énorme de son budget annuel était consacré au remplacement de structures en béton », explique Crofts. « La salinité élevée du sable de la région et le delta élevé de température du jour à la nuit provoquent une fissuration plus rapide du béton. Saudi Aramco a commencé à rechercher des technologies alternatives et, en tant que membres de l'ACI, ils ont tiré leur stratégie des normes de barres d'armature FRP développées, les adaptant et les affinant davantage en tant que normes Saudi Aramco. L'entreprise a ensuite imposé l'utilisation de barres d'armature en GFRP dans certains environnements très corrosifs. »
Saudi Aramco a lancé un appel d'offres pour le projet de canal d'inondation de Jizan, puis a sélectionné trois fournisseurs de barres d'armature en PRV. Mateenbar a remporté 50% du contrat. « Nous avons attendu plusieurs mois pendant que le projet se préparait », se souvient Crofts, « et puis, soudainement, tous les matériaux étaient nécessaires immédiatement. L'usine de Dubaï a démarré à plein régime en l'espace d'une semaine et a produit près de 6 000 kilomètres de barres d'armature en PRV en sept mois. »
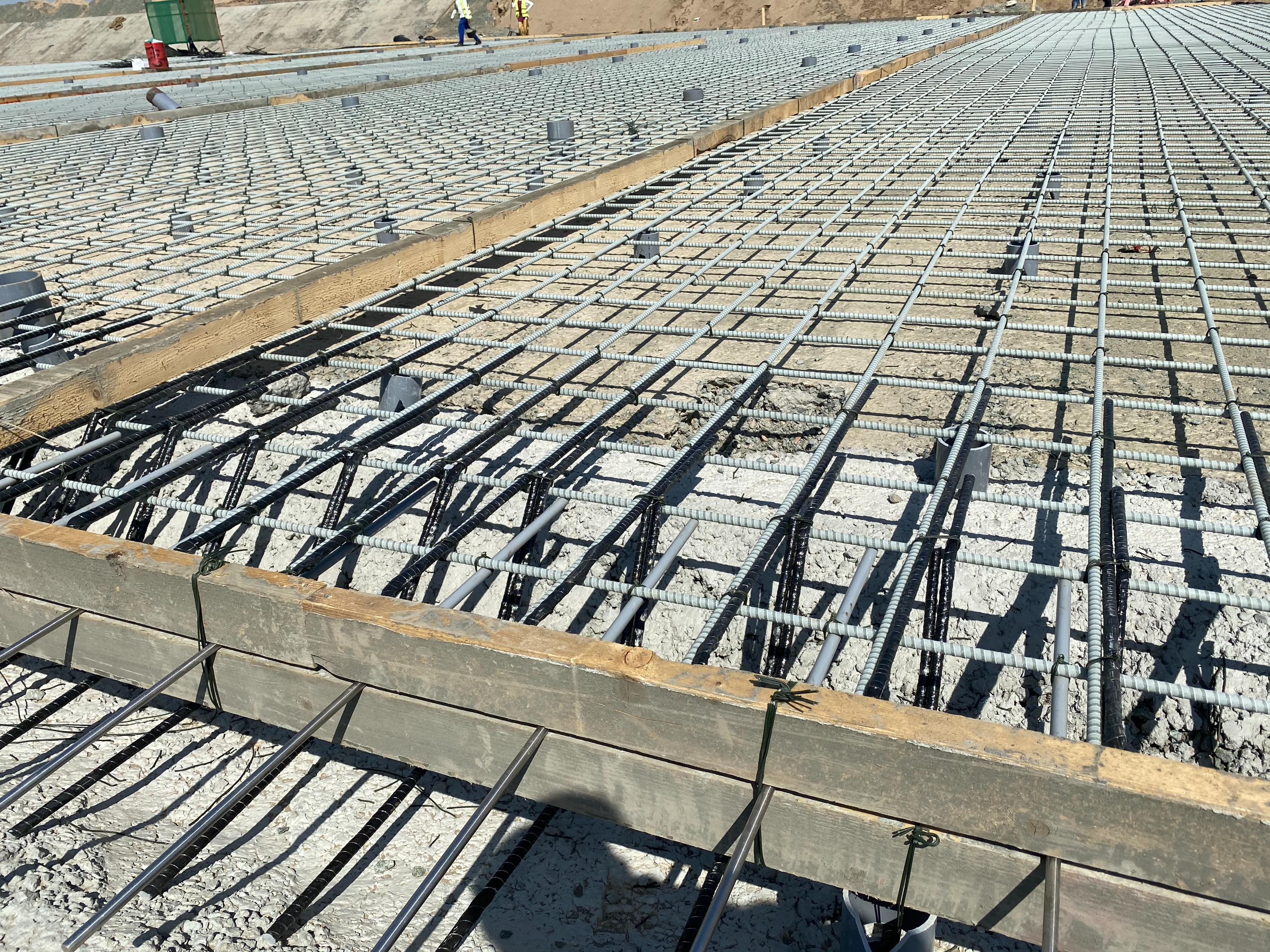
Une fois livrées, les barres d'armature ont été installées par l'entrepreneur du projet, Al Yamama Group (Dammam, Arabie saoudite). « Nous pensions avoir besoin de beaucoup d'aide lors de l'installation, mais ce n'était pas nécessaire », explique Crofts. « Ils l'ont trouvée beaucoup plus rapide à installer que les barres d'armature en acier. » Avec un poids de 25 % de celui des barres d'armature en acier, les barres d'armature GRFP permettent de manipuler de plus grandes longueurs avec moins de personnes et sont plus faciles à déplacer et à positionner. « Il y a également moins de tuyaux de positionnement nécessaires », ajoute-t-il. "Ces sections rondes de tuyau sont utilisées pour soutenir la barre d'armature à la bonne hauteur dans le béton."
Une fois la barre d'armature placée, attachée avec des fils d'acier inoxydable et inspectée, elle est prête pour le béton à couler sur le dessus. L'équipe d'installation des barres d'armature s'est déplacée si rapidement, note Crofts, qu'elle était en fait à un kilomètre du canal de 40 à 80 mètres de large avant de se rendre compte que les opérations de coulage du béton ne pouvaient pas suivre. « Alors, ils se sont arrêtés et ont laissé le béton rattraper son retard », ajoute-t-il. «C'est important car si de fortes pluies arrivent, les inondations remplissent le canal de sable. Cela s'est produit à plusieurs reprises, causant des retards, mais soulignant également l'importance de ce canal de drainage. »
Après avoir coulé le béton sur la barre d'armature, l'équipe d'installation le tasse et le comprime pour éliminer les bulles d'air, puis il durcit au cours des jours et des semaines suivants. « Il n'y a aucune différence entre le GFRP et les barres d'armature en acier pour ces marches », explique Crofts. « Nous avons terminé de fournir les barres d'armature en janvier 2020 et le canal vient d'être terminé. »
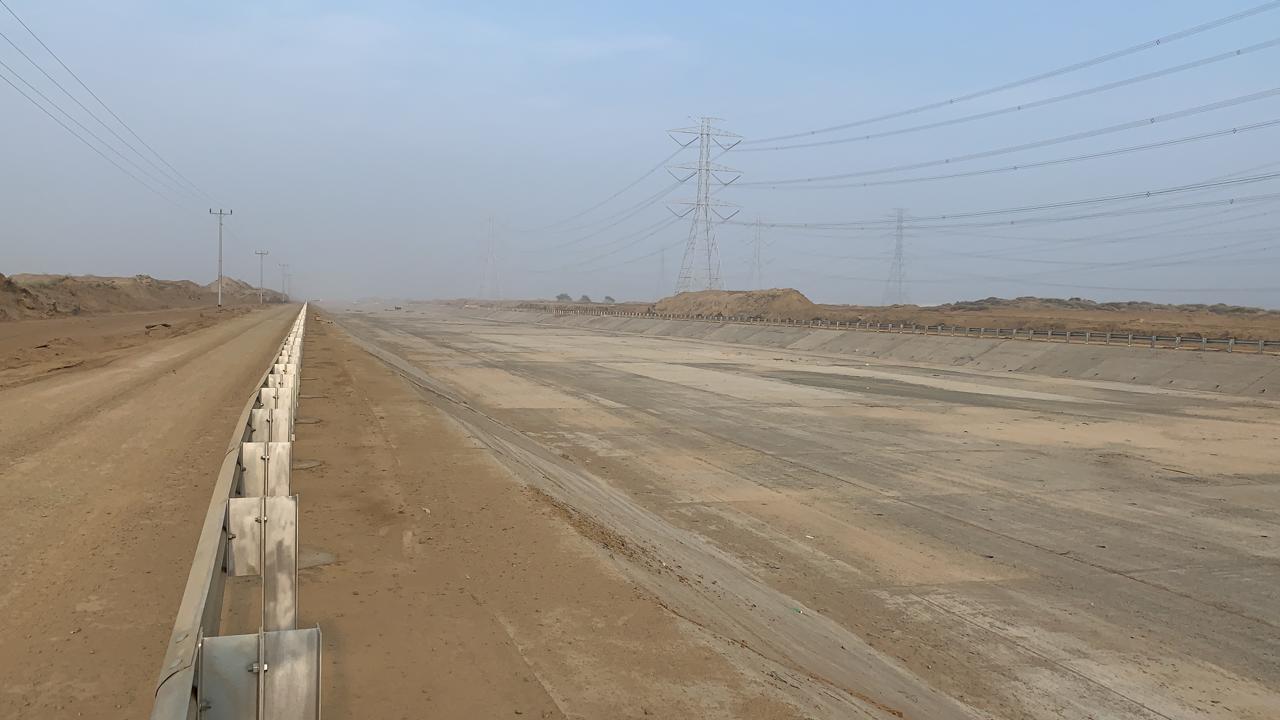
Conception, coût et avenir GFRP
Crofts souligne que les barres d'armature en PRV ne remplacent pas directement l'acier. « Les barres d'armature en PRV ont des propriétés différentes de celles des barres d'armature en acier. Ces différences doivent être prises en compte dans la conception. Ainsi, alors que le béton armé d'acier serait généralement conçu selon l'ACI 318, cela ne conviendrait pas aux barres d'armature GFRP, qui s'appuient plutôt sur le guide de conception ACI 440. À titre d'exemple, les barres d'armature en GFRP ont une résistance à la traction plus élevée que l'acier, mais un module de traction inférieur. Il est également élastique jusqu'à l'échec. Crofts note que dans une conception en acier, la quantité de barres d'armature serait généralement déterminée par la résistance à la traction. Cependant, pour le GFRP, le module est généralement le facteur qui détermine la quantité de barres d'armature requise. Répondre à cette exigence se traduit généralement par une structure qui dépassera les exigences de résistance ultime. Il garantit également un mode de défaillance souhaitable dans la structure renforcée de barres d'armature GFRP.
Une autre considération est la production de coudes et de formes. Crofts note que le rapport entre les barres d'armature coudées et droites dans les projets est, en moyenne, d'environ 30 %. Avec des barres d'armature en acier, cette fabrication est souvent réalisée sur place. « Les barres courbées Mateenbar sont produites dans notre usine à environnement contrôlé et livrées directement sur site sans étapes de fabrication intermédiaires », explique-t-il. « Cela peut être un défi du point de vue de l'approvisionnement car les besoins changent d'une semaine à l'autre. Nous avons constaté que la flexibilité et le fait d'avoir une usine située dans la même région sont très importants. »
« Le coût des barres d'armature en GFRP est 3 à 4 fois plus élevé que celui de l'acier s'il est calculé en dollars par livre », explique Crofts, « car notre produit est un quart de la densité. La mesure appropriée est en dollars par pied, car les barres d'armature sont en fait spécifiées et achetées en tant que fraction du volume de béton. Lorsque vous mesurez son coût en volume, les barres d'armature en PRV sont compétitives par rapport à l'acier. »
« Jizan a été le premier méga-projet à ne pas autoriser l'acier », explique Crofts. « Ils avaient une équipe pour concevoir les structures requises avec une durée de vie de plus de 100 ans. Plusieurs producteurs de barres d'armature en GFRP cherchent à s'implanter en Arabie saoudite à mesure que la demande augmente. » Mateenbar y construit également une nouvelle usine, ainsi qu'une autre à Concord, en Caroline du Nord, aux États-Unis, pour desservir l'Amérique du Nord, qui est le deuxième marché après le Moyen-Orient. Les deux nouvelles usines sont des installations modernes de 100 000 carrés, utilisant la technologie de pultrusion avancée de Pultron. Pour les deux, l'équipement a été livré en octobre 2020 et la production devrait commencer au début de 2021.
Alors que la demande de barres d'armature GFRP augmente au Moyen-Orient, le marché en Amérique du Nord continue de mûrir. « Actuellement, les plus grandes applications de barres d'armature GFRP en Amérique du Nord sont les digues et les ponts le long de la côte ou là où les routes sont fortement salées », explique Croft. « Cependant, les DOT et les propriétaires d'actifs cherchent maintenant à améliorer les coûts tout au long de la durée de vie des structures [CW est d'accord, voir « Le rôle croissant des composites dans les infrastructures »], ce qui inclut la réduction du besoin d'entretien et la construction d'infrastructures à la fois durables et durables. Les ingénieurs-conseils et les utilisateurs finaux voient la valeur de la technologie des barres d'armature GFRP et les producteurs de barres d'armature GFRP coopèrent sur les normes de qualité et de performance. Il existe également des utilisateurs de premier plan, tels que le FDOT, qui font la promotion de la technologie et aident d'autres DOT, ce qui a contribué à diffuser les connaissances. »
Crofts note que FDOT a récemment organisé un webinaire sur la conception en béton armé GFRP avec 200 participants. Dans un autre webinaire, le Dr Antonio Nanni, l'un des principaux chercheurs de l'Université de Miami (Miami, Floride, États-Unis) travaillant avec FDOT, a déclaré :« Les barres d'armature en FRP sont prêtes pour les heures de grande écoute ». Cela a été prouvé, dit Crofts. « Le travail consiste maintenant à ce que davantage d'entreprises le spécifient et que les entrepreneurs l'utilisent. »
Résine
- Préparer un avenir autonome
- Pour les transactions futures, nous faisons confiance à la blockchain
- UAMMI, Impossible Objects fabrique des pièces composites pour l'U.S. Air Force
- Impossible Objects s'associe à BASF pour l'impression 3D composite
- INEOS Styrolution va construire un site de production pour le composite thermoplastique StyLight
- Techsil lance un adhésif époxy transparent pour substrats composites
- SABIC lance un panneau composite pour le bâtiment et la construction
- Rhodes Interform fabrique une presse composite pour AMRC
- La première section de fuselage composite pour le premier jet commercial composite