La conception du hayon met à l'épreuve l'enroulement filamentaire modifié
Les hayons élévateurs pour automobiles, ou les portes de hayon arrière, passent lentement des métaux aux composites depuis des décennies. Bien que ce n'est qu'en 2013 que le premier hayon entièrement en plastique/composite, sans la structure de support en métal, a été commercialisé, la plupart des hayons comportent encore aujourd'hui ce composant de support sur lequel les peaux extérieures et les panneaux intérieurs sont fixés, en particulier sur les plus grands et plus lourds sport- véhicules utilitaires (VUS) et véhicules utilitaires multisegments (VUM) avec des portes arrière plus grandes.
Cependant, quelle pourrait bien être la prochaine évolution des hayons élévateurs en composite a fait ses débuts en 2019 sur la Toyota Supra voiture de sport de Toyota Motor Corp. (Toyota City, Japon). Un cadre composite enroulé de filaments a remplacé un cadre métallique et offrirait une rigidité et une résistance supérieures à un poids inférieur à celui des structures métalliques traditionnelles, avec une plus grande flexibilité de conception, en particulier dans les espaces d'emballage restreints. Il semblerait que le processus d'enroulement filamentaire ait été modifié à un point tel que, à mesure que l'intérêt augmente et que les applications prolifèrent, il peut atteindre les objectifs de vitesse et de coût de la production de véhicules en plus grand volume. C'est ainsi que le design et la technologie sont nés.
Fabrication trilatérale
Magna International Inc. (Aurora, Ontario, Canada) est un intégrateur de niveau 1 en Amérique du Nord, mais en Europe, sa filiale Magna Steyr AG &Co. KG (Graz, Autriche) conçoit et assemble également des voitures complètes pour les équipementiers nécessitant une fabrication supplémentaire. capacité.
Récemment, Magna a participé à un programme intéressant impliquant les constructeurs automobiles Toyota et BMW AG (Munich, Allemagne), qui travaillent en coopération sur des projets de conception et de fabrication depuis 2013. Pour son dernier effort, Toyota cherchait à relancer sa Supra plaque signalétique et s'était associé à BMW pour fournir la conception et le réglage du véhicule et d'une voiture sœur, la Z4 à 2 places de BMW . Les deux véhicules partagent les systèmes de moteur, de suspension et de direction. Magna Steyr assemblerait les deux voitures à Graz et fournirait la Supra avec sièges, panneaux de carrosserie, loquets de porte et hayons élévateurs. Bien qu'il y ait beaucoup d'innovations sur les deux voitures, le hayon intégré dans la Supra C'est là que l'innovation dans la conception des composites est la plus apparente.
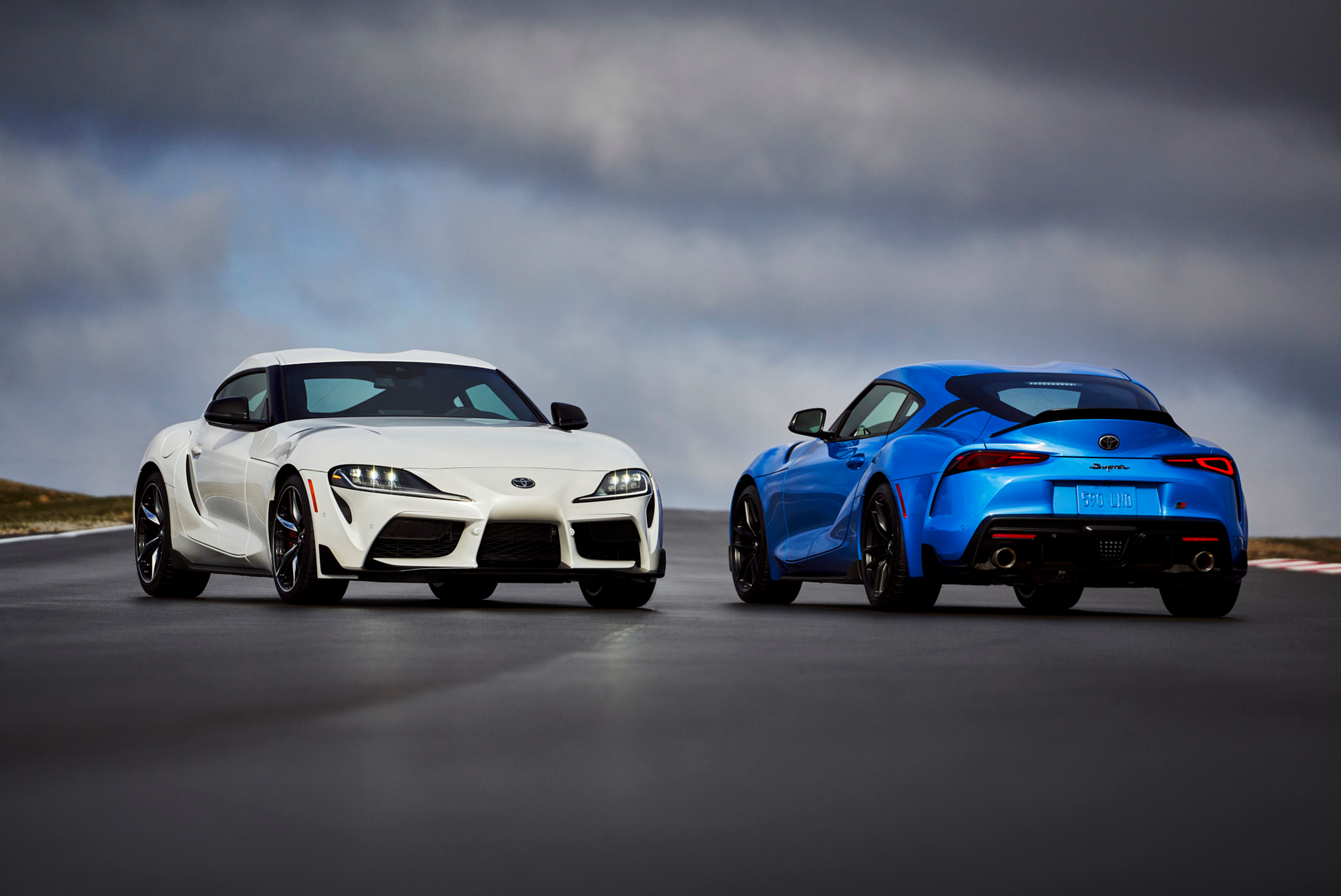
Manchester de Bohême
Des années avant l'implication de Magna dans le 2020 année modèle Supra, son exploitation à Liberec, en République tchèque, avait exploré les technologies des cadres spatiaux composites pour un certain nombre d'applications potentielles. Par chance, la région a une riche tradition en tant que centre textile de premier plan et était autrefois connue sous le nom de « Manchester of Bohemia ». L'équipe de Liberec recherchait une architecture technologique prenant en charge des charges élevées, une masse globale réduite, conservant des tolérances dimensionnelles strictes et pouvant être produite dans un processus avec une répétabilité et une reproductibilité élevées (R&R) pour répondre aux exigences de performances et de fabrication des constructeurs automobiles européens.
« Nous avons conclu que nous avions besoin d'un produit thermodurcissable avec une stabilité thermique et dimensionnelle élevée », se souvient Riad Chaaya, directeur mondial de la ligne de produits Magna - hayons élévateurs en composite. « Nous savions également que nous avions besoin d'une forme fermée avec la capacité de produire des sections transversales de formes et d'épaisseurs variables - nécessaires pour optimiser les performances mécaniques, l'espace d'emballage, la masse et le coût - qui pourraient être produites dans un processus capable de fabriquer 150 000 pièces par an. Nous avons examiné de nombreuses technologies, notamment le moulage par soufflage, le tressage et l'enroulement filamentaire, mais aucune ne répondait vraiment à nos besoins. Après de nombreux essais, nous avons sélectionné l'enroulement filamentaire comme le mieux adapté à ce que nous voulions, car il nous permettait de contrôler les orientations et le nombre de filaments pour extraire le module le plus élevé au poids le plus faible. »
Malgré de nombreux avantages, on craignait que l'enroulement filamentaire ne soit trop lent pour la production automobile conventionnelle. De plus, l'équipe avait besoin d'une méthode pour commencer et terminer le processus de bobinage afin de créer un cadre de forme fermée. Heureusement, alors que l'équipe n'avait aucune histoire avec l'enroulement filamentaire, l'héritage de Liberec en matière de fabrication de textiles signifiait que la communauté locale était pleine d'experts en mèches et en enroulement de filaments.
« Heureusement pour nous, ces experts ont eu la passion de ressusciter leur savoir-faire traditionnel pour nous aider à l'appliquer de nouvelles façons pour répondre aux besoins automobiles de grand volume », ajoute le Dr-Ing. Josef Půta, leader technologique de Magna Exteriors - République tchèque.
« Parce que le bobinage filamentaire traditionnel était trop lent pour nos besoins, nos partenaires et nous avons examiné de nombreuses façons de le faire fonctionner plus rapidement », se souvient Lukáš Strouhal, responsable de l'industrialisation, Magna Liberec. « Nous avons envisagé des moyens d'accélérer chaque étape du processus et de faire les choses très différemment. Bien que nous ne puissions pas en dire trop sur comment nous l'avons fait, nous pouvons dire que nous avons obtenu d'énormes améliorations en termes de vitesse, de sorte que notre processus modifié puisse devenir « digne de l'automobile ». »
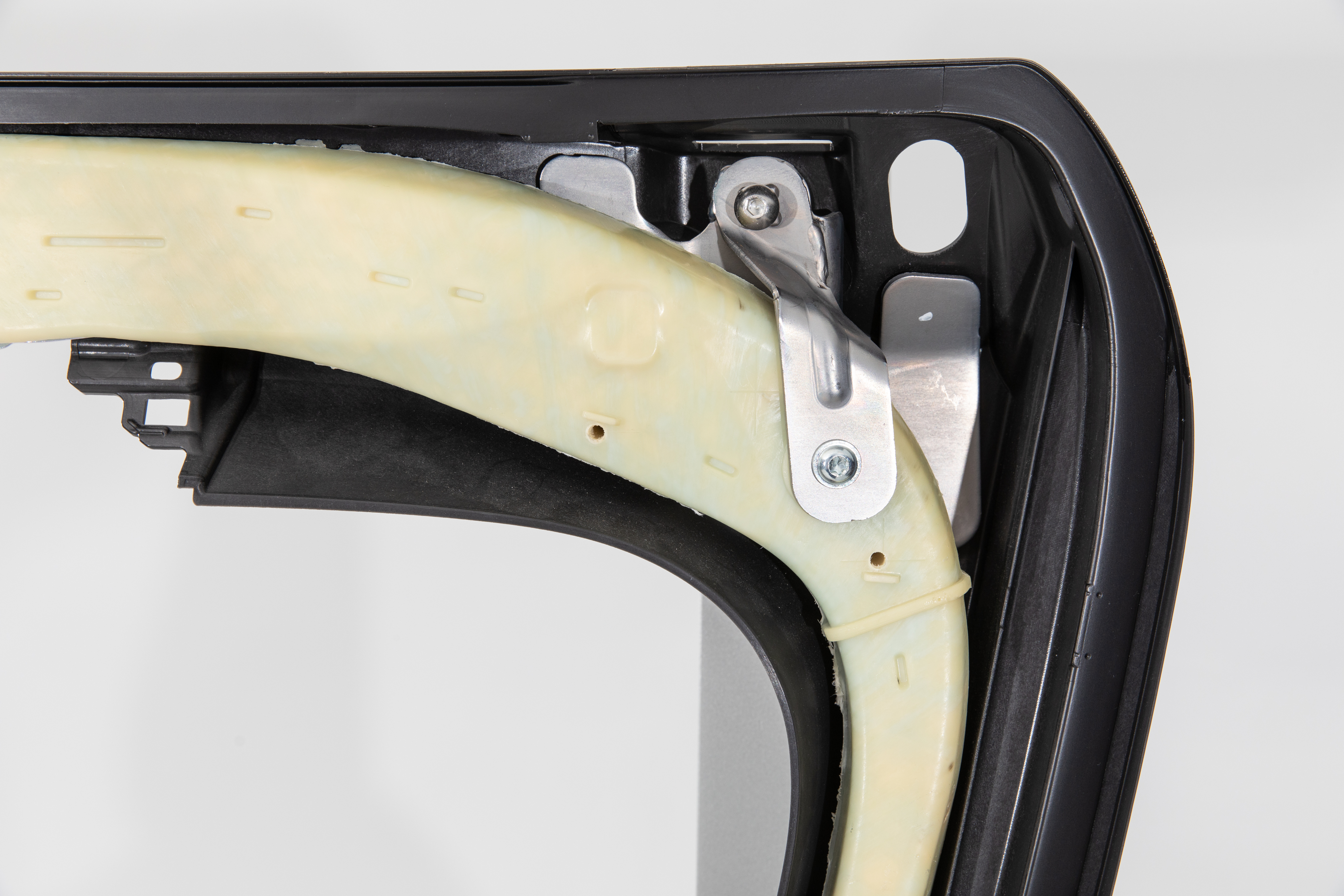
Magna et ses partenaires ont exploré de nombreux systèmes de résine, notamment l'époxyde, le polyuréthane (PUR) et un mélange PUR/ester vinylique, ainsi qu'une variété de renforts, du verre au carbone en passant par les fibres de basalte. Le système final comprend du PUR et des fibres de verre, qui offrent le meilleur équilibre entre l'efficacité des fibres, les performances, le coût et la vitesse de production.
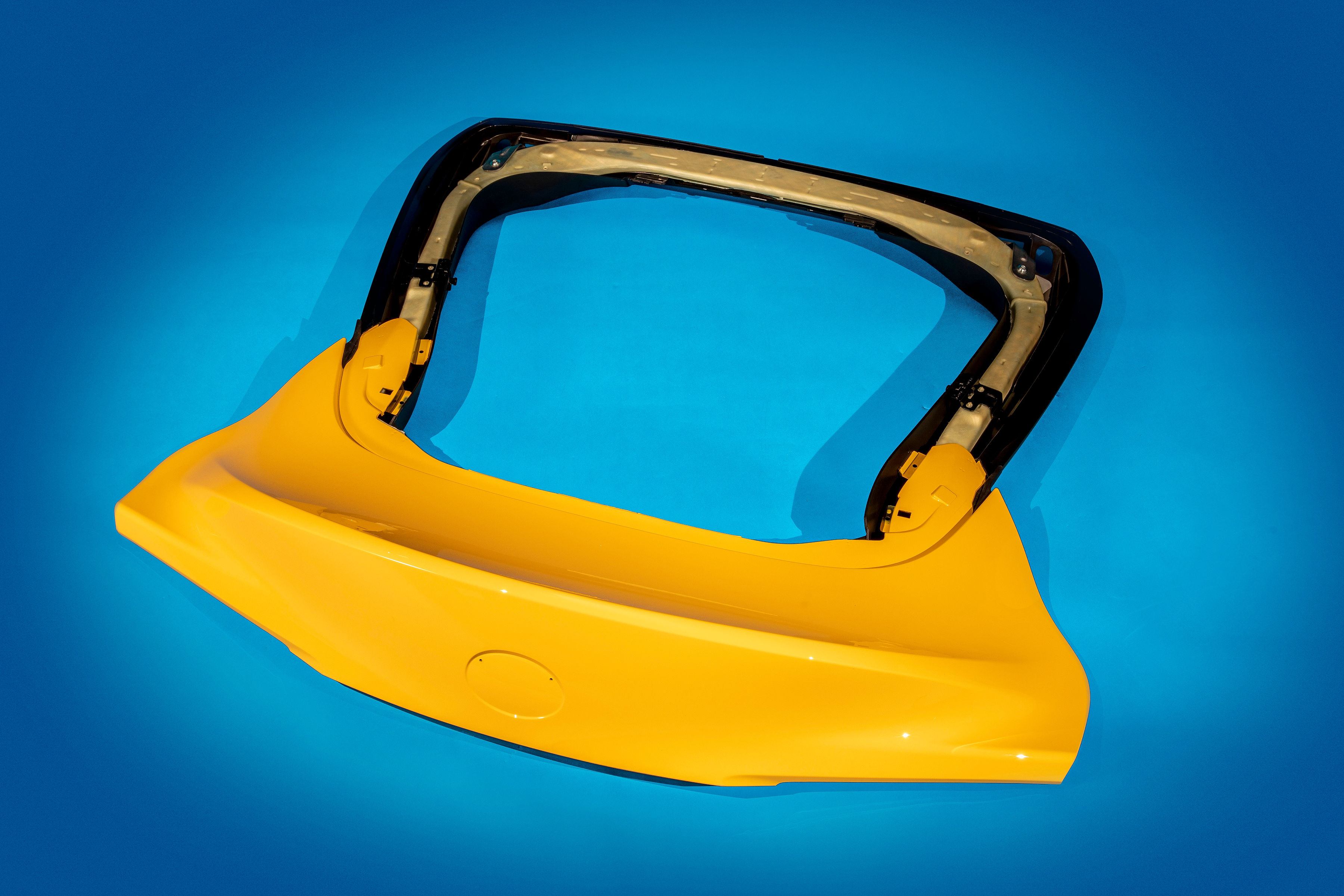
Le cadre spatial générique enroulé de filaments de Magna est produit en trois étapes, chacune soigneusement optimisée pour la vitesse. Tout d'abord, un noyau PUR cellulaire rigide est produit par moulage par injection-réaction (RIM); deuxièmement, ce noyau, qui fonctionne comme un mandrin, est enroulé avec de la fibre de verre; et troisièmement, cette structure enroulée est ensuite infusée de PUR et consolidée dans le processus de moulage par transfert de résine à haute pression (HP-RTM). Des précautions sont prises pour s'assurer que le noyau ne s'effondre pas pendant l'infusion/la consolidation. Půta explique que beaucoup de travail a été consacré à la spécification des types de mèches, d'encollages et de résines utilisés - nécessitant un travail étroit avec les fournisseurs sur les modifications de matériaux - ainsi qu'à déterminer le nombre d'enroulements et l'orientation des filaments dans chaque couche. Sans surprise, la société a délivré de nombreux brevets couvrant tout, de la conception à la production de noyaux, en passant par la machine d'enroulement de filaments, ainsi que d'autres secrets commerciaux qu'ils détiennent.
« Nous avons apporté de multiples innovations à chaque étape du processus et à chaque produit », explique Strouhal. « Vous pourriez déchirer l'un de nos cadres, voir les formes et les géométries utilisées, et vous vous demanderiez toujours pourquoi et comment nous avons fait cela. »
Bien que l'équipe de Magna Liberec n'ait pas développé sa technologie spatiale pour une application particulière, elle était sur le point d'avoir une opportunité intéressante de l'utiliser.
hayon élévateur difficile
Magna fabrique depuis longtemps des hayons élévateurs pour véhicules de tourisme. L'entreprise aurait construit les premiers hayons élévateurs entièrement en oléfine en Amérique du Nord et en Europe pour la BMW i3 2013 citadine électrique, et conçu et construit un hayon élévateur tout oléfine de nouvelle génération pour la Jeep 2019 Cherokee de FCA NA LLC (Auburn Hills, Michigan, États-Unis) SUV. Étant donné que la production de hayons élévateurs était un livrable pour la Supra programme, Magna s'est non seulement inspiré du travail effectué à Liberec, mais aussi de sa longue histoire de conversion de structures métalliques de hayons élévateurs en composites et en plastiques.
« La Supra hayon élévateur a offert un certain nombre de défis immédiats », se souvient Chaaya. « Premièrement, l'espace de l'emballage était très limité, ce qui signifie que les tolérances étaient très serrées et que les valeurs de coefficient de dilatation thermique linéaire doivent être soigneusement gérées pour que les hayons élévateurs s'ouvrent et se ferment librement. Deuxièmement, la forme de cette porte était encore plus difficile. Toyota voulait non seulement un hayon plus léger, mais ils avaient des exigences de style très spécifiques pour la façon dont l'arrière du véhicule était drapé. Troisièmement, avec les volumes de construction projetés du véhicule, l'outillage pour obtenir cette forme en métaux serait très coûteux. En fait, nous avons conclu que le cadre du hayon ne pouvait pas être fabriqué en une seule pièce de métal tout en répondant aux exigences de conception et de performance de Toyota. Cela signifiait que le cadre spatial devait être fabriqué à partir de composites et, plus précisément, de composites thermodurcissables. »
La peau extérieure serait un panneau TPO peint et moulé par injection renforcé de talc pour gérer la forme agressive, tandis que le panneau intérieur serait en polypropylène à verre long (PP); les deux seraient joints au cadre avec un adhésif structurel PUR 2K. Chaaya ajoute que beaucoup de travail a été fait pour optimiser le cadre de l'espace et compléter le hayon élévateur pour répondre aux exigences de charge de torsion. L'un des premiers défis consistait à trouver un moyen de simuler avec précision les propriétés des matériaux pour obtenir une corrélation précise entre les résultats prédits et mesurés.
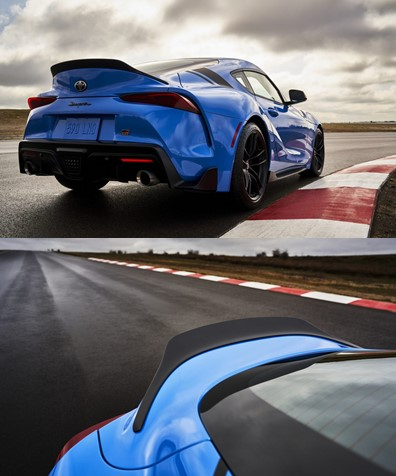
"Ce fut un combat difficile pour obtenir une bonne corrélation avec nos modèles de matériaux, car nous devions simuler chaque couche d'enroulement et incorporer la forme, les rayons et les exigences d'enroulement elles-mêmes", ajoute-t-il. « Bien que nous ayons commencé à perdre 20 %, après de nombreux réglages et déterminé la meilleure façon d'améliorer notre rigidité, nos prévisions finales étaient très proches. Sur un si grand cadre, nous avons également réussi à maintenir des tolérances dimensionnelles à 1 millimètre. »
Beaucoup d'avantages
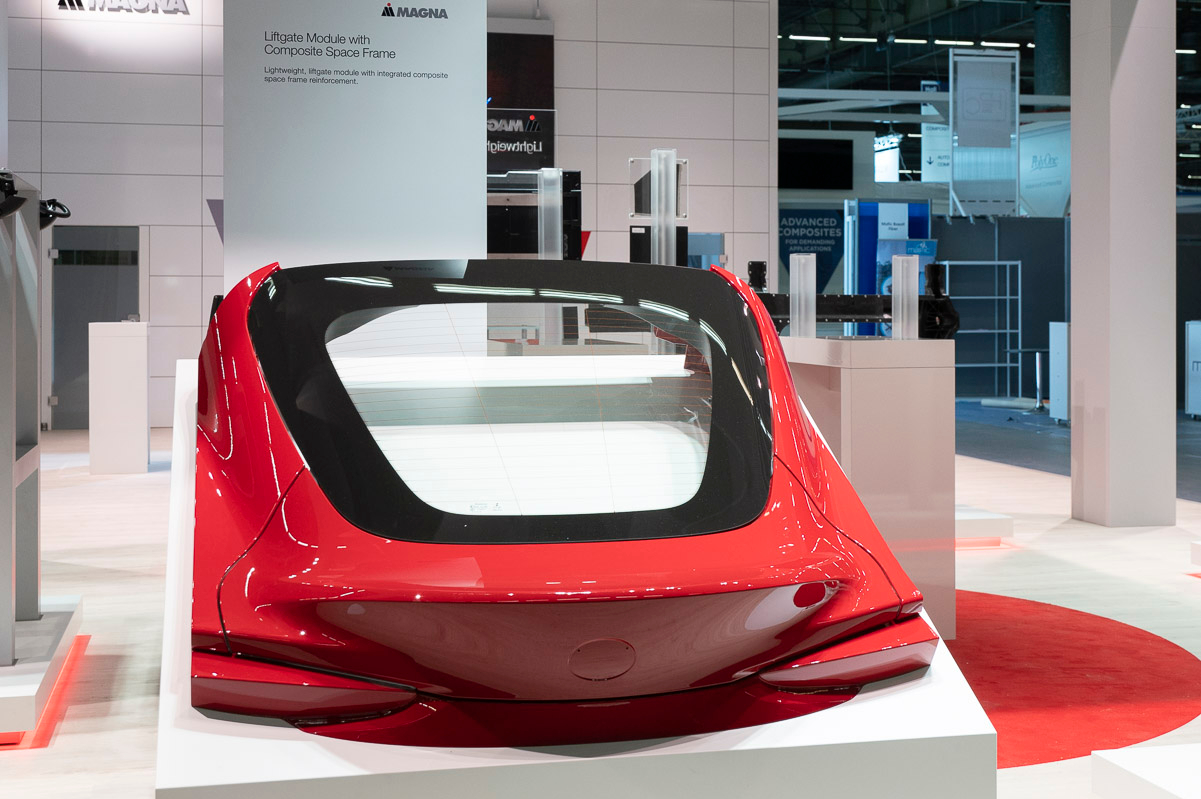
Le cadre final en forme de beignet présente des diamètres et des épaisseurs de paroi variables, mais a un diamètre nominal de 50 à 60 millimètres. À part un petit support dans le coin et des fixations dures comme des loquets et des charnières, ainsi qu'une feuille pour mettre à la terre les antennes intégrées, l'ensemble du cadre - qui mesure 104 x 111 centimètres - est entièrement composite. Même les supports « d'oreille », utilisés pour connecter le panneau de garniture intérieure à la moitié inférieure du hayon, sont composites et fabriqués via HP-RTM. Bien que le cadre composite soit 10 % plus léger qu'un cadre métallique comparable, les effets de décomposition de la masse signifient que le hayon complet est environ 20 à 25 % plus léger qu'un hayon métallique. Des hayons élévateurs plus légers nécessitent moins d'efforts pour les consommateurs pour ouvrir/fermer, sont plus faciles à installer pour un travailleur pendant l'assemblage du véhicule, économisent du carburant pendant la durée d'utilisation du véhicule et fournissent ce que Strouhal décrit comme «un son solide incroyable» lorsque le hayon se ferme. Le système composite a également éliminé les étapes telles que les bords ourlés et les points de soudure/joints requis avec les hayons élévateurs en métal.
Chaaya laisse entendre que son entreprise a un autre projet automobile majeur à enroulement filamentaire en cours. Il dit également que Magna voit d'autres utilisations de la technologie au-delà des hayons élévateurs. « Portes, couvercles de coffre, capots, FEM (modules frontaux) et même des véhicules autonomes — comme un bus composé d'un cadre en verre — pourrait utiliser un tel cadre spatial », ajoute-t-il. « Et il n’aurait même pas besoin d’être caché. Si nous utilisions un tissage en fibre de carbone, ce serait un signe de prestige de laisser cette belle surface exposée et de ne pas cacher le cadre à l'intérieur. »
Résine
- Le guide du débutant pour la fabrication de filaments fondus (FFF)
- Le rôle de la conception assistée par ordinateur (CAO) dans l'impression 3D
- La Triode
- Le design industriel à l'ère de l'IoT
- Optimisation de la ligne d'alimentation RF dans la conception de PCB
- Les nouvelles technologies et les marchés à World of Filament événement Winding
- Enrouleur de filament Roth pour faciliter les grandes réductions de poids/coût d'Ariane 6
- Les avantages du prototypage de PCB
- Connaître l'importance de la nomenclature dans la conception de circuits imprimés