Conception d'aubes de turbines hydroélectriques propulsées par des composites
Le terme « énergie hydroélectrique » évoque souvent d'immenses opérations entraînées par des infrastructures construites à cet effet telles que des systèmes de barrage et de grandes turbines avec des aubes de turbine à hélice traditionnellement métalliques. Cependant, de nombreuses régions manquent de nouvelles capacités pour les grandes centrales hydroélectriques de grande puissance. Dans le même temps, la demande pour une production d'énergie renouvelable plus importante et à moindre coût continue de croître.
Le département américain de l'Énergie (DOE), dans son rapport 2018 "Hydropower Vision" décrivant l'état actuel de l'énergie hydroélectrique aux États-Unis et ses objectifs pour l'avenir, a prédit que la croissance du marché hydroélectrique américain - de 101 gigawatts (GW) de la capacité énergétique en 2018 à une capacité potentielle de près de 150 GW en 2050 - nécessiterait de nouvelles technologies de pointe qui peuvent fournir plus d'énergie à moindre coût.
Selon Darren Wren, directeur général de Kinetic NRG (Gold Coast, Australie), une solution potentielle pourrait être de plus petits générateurs hydroélectriques capturant l'énergie inexploitée des systèmes d'eau à faible débit comme les canaux d'irrigation et les ruisseaux. Fondée en 2016 par le regretté fondateur Paul Camilleri, Kinetic NRG est une société d'énergie renouvelable à financement privé axée sur le développement de nouvelles technologies de production hydroélectrique pour fournir une électricité fiable et à faible coût.
La première technologie de l'entreprise s'appelle le système de générateur d'énergie hydrocinétique (HEG), qui mesure 1,5 mètre de diamètre avec une puissance allant jusqu'à 30 kilowatts (kW) à partir de débits d'eau de 2,0 mètres par seconde. Cette production en fait un « micro » système hydroélectrique selon des organismes de classification tels que le DOE des États-Unis, qui définit les micro-systèmes comme ceux d'une capacité allant jusqu'à 100 kW. Destiné à une utilisation directe dans les rivières, les canaux d'irrigation ou les canaux de fuite acheminant l'eau des barrages existants, le HEG est conçu pour l'hydroélectricité à faible chute - ce qui signifie que la « chute », ou la distance entre la ligne d'eau et la turbine, est inférieure à 20 mètres.
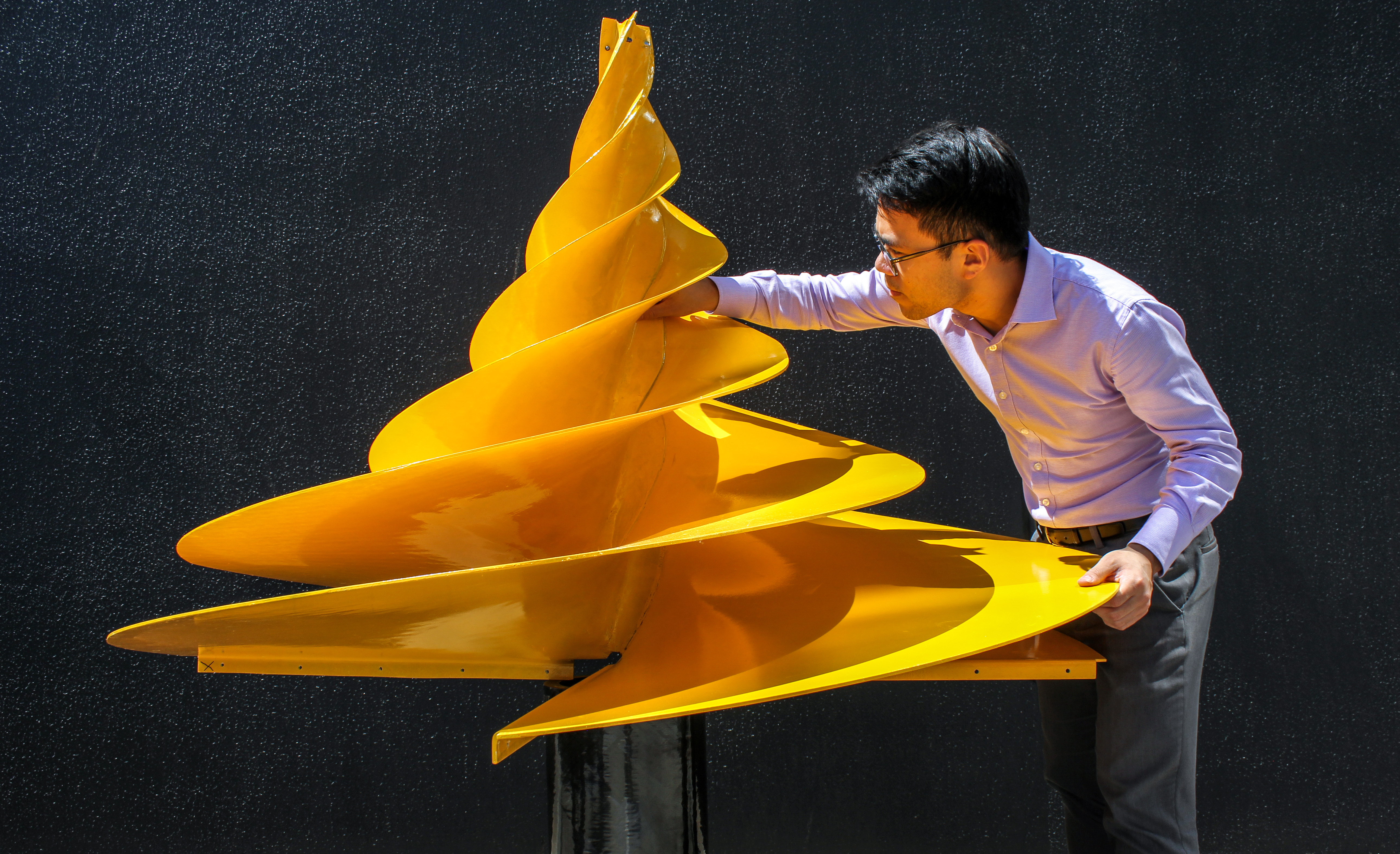
Le développement du HEG et de sa pale de turbine en spirale est en cours depuis environ cinq ans, dit Wren. «Ça a été tout un voyage. La conception que nous avons maintenant est venue littéralement d'essais et d'erreurs. »
Concevoir une lame modulaire et manufacturable
Les premiers modèles de lame spirale à petite échelle de Kinetic NRG ont été formés à partir de métal, mais lorsque le moment est venu de fabriquer le prototype à grande échelle de 1,5 mètre de diamètre, « nous avons en fait constaté que nous ne pouvions pas le faire », explique Wren. Le concept était de commencer avec un morceau de métal plat, puis de former ou de forger un ensemble de spirales rayonnant à partir du centre. "Nous ne pouvions tout simplement pas trouver un moyen d'accéder à certains points de la pièce pour créer la force dont nous avions besoin", explique-t-il.
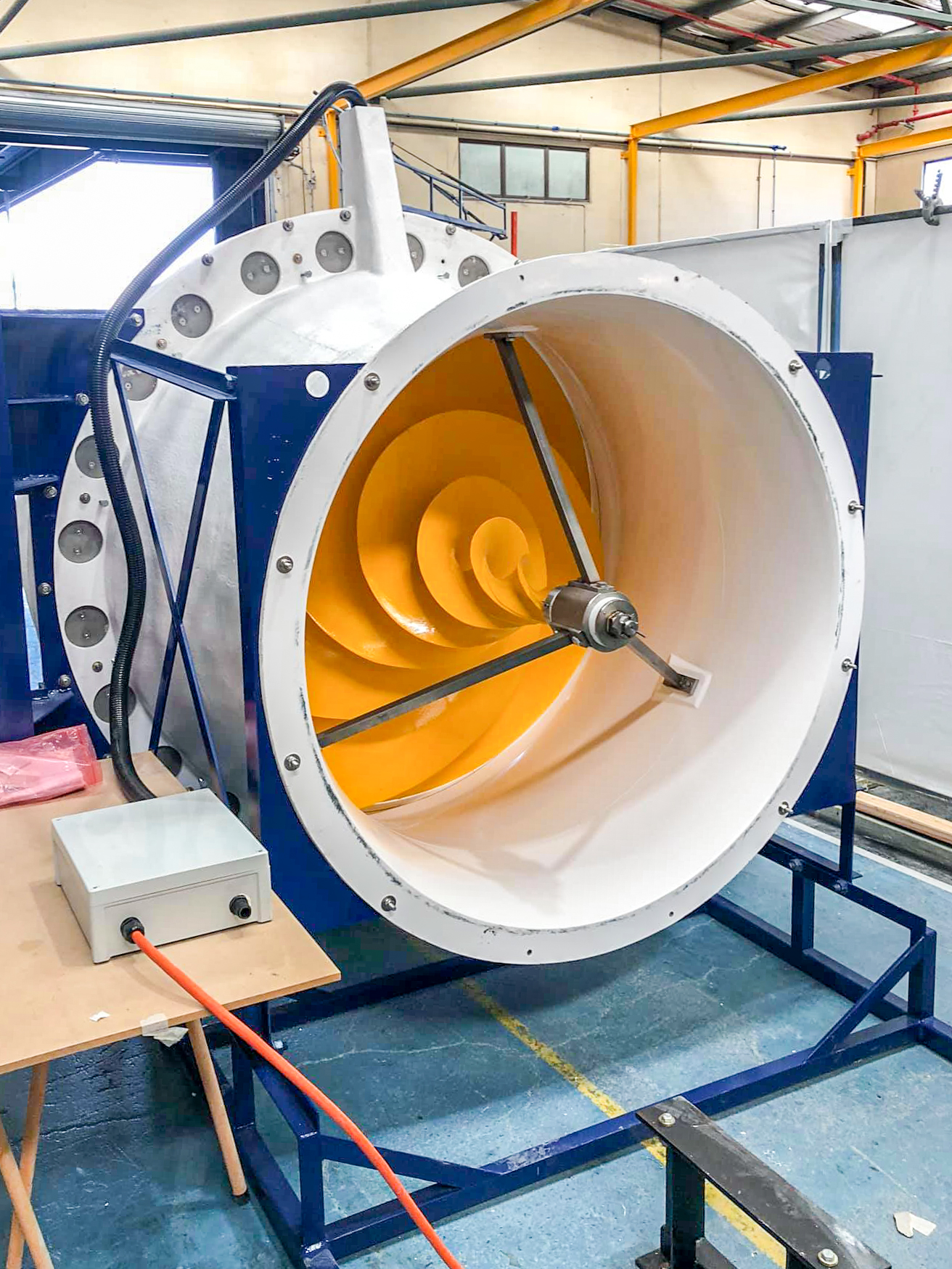
La société a finalement abandonné ses efforts métalliques, mais pas la conception elle-même. Wren dit que Kinetic NRG s'est associé à une université locale pour explorer des techniques de fabrication et des matériaux alternatifs tels que le nylon ou la céramique, et a commencé à discuter avec des sociétés d'impression 3D pour voir si la fabrication additive pouvait être une option viable. Pourtant, aucune solution ne s'est présentée qui a fourni la bonne combinaison d'aptitude à la fabrication et de propriétés mécaniques. Enfin, après un voyage de trois ans, Kinetic NRG a été présenté via une connexion de réseau d'approvisionnement à l'équipe de la société d'ingénierie Advanced Composite Structures Australia (ACS-A, Melbourne), spécialisée dans la conception et la fabrication de produits à faible volume et à haute valeur ajoutée. -ajout de composants composites pour une variété de marchés finaux.
Wren appelle ce qui s'est passé ensuite "une réunion d'esprits", expliquant que Kinetic NRG a travaillé avec Paul Falzon, directeur général d'ACS-A, et son équipe sur diverses méthodes pour fabriquer et concevoir la pièce en utilisant des matériaux composites - des matériaux que ACS-A connaissait. par expérience serait en mesure de répondre aux exigences de forme, de poids et de rigidité nécessaires à Kinetic NRG.
La forme innovante de la lame était le principal défi de conception du projet, avec des exigences mécaniques pour la lame basées, selon Wren, sur les normes établies par le DOE des États-Unis et la Commission électrotechnique internationale. Les autres composants du système (transmission, gestion de l'alimentation, communication, etc.) sont des produits standard du commerce qui sont connus pour répondre à toutes les réglementations nécessaires.
Selon Falzon, ACS-A a d'abord évalué les tentatives métalliques de conception de la lame, puis a déterminé comment obtenir la forme, les tolérances dimensionnelles et le poids requis de la lame. La pale devait également pouvoir résister aux environnements aquatiques et être suffisamment rigide pour supporter l'arbre en acier de la turbine sur lequel elle est fixée. L'équipe ACS-A a commencé avec la conception métallique d'origine et a « inversé » une lame composite en fibre de verre pour correspondre à la rigidité d'origine, explique Falzon. Cependant, certaines modifications de conception ont dû être apportées lors du passage d'une structure métallique soudée à un stratifié composite. Comme l'explique Falzon, « Nous avons pris du recul et nous avons demandé : « D'accord, si nous voulons tirer pleinement parti des matériaux composites, à quoi ressemble cette chose ? » »
Après plusieurs itérations et discussions, la conception actuelle qui a pris forme comprend quatre lames composites identiques qui s'emboîtent pour former la forme finale en spirale. "La lame composite est en fait plus épaisse que la conception en acier, mais plus légère en raison de la densité plus faible des matériaux avec lesquels nous travaillons", explique Falzon. "Être plus épais signifie également que nous obtenons beaucoup plus de rigidité en flexion par rapport à la conception en acier, donc vous obtenez en fait un produit beaucoup plus rigide dans l'ensemble."
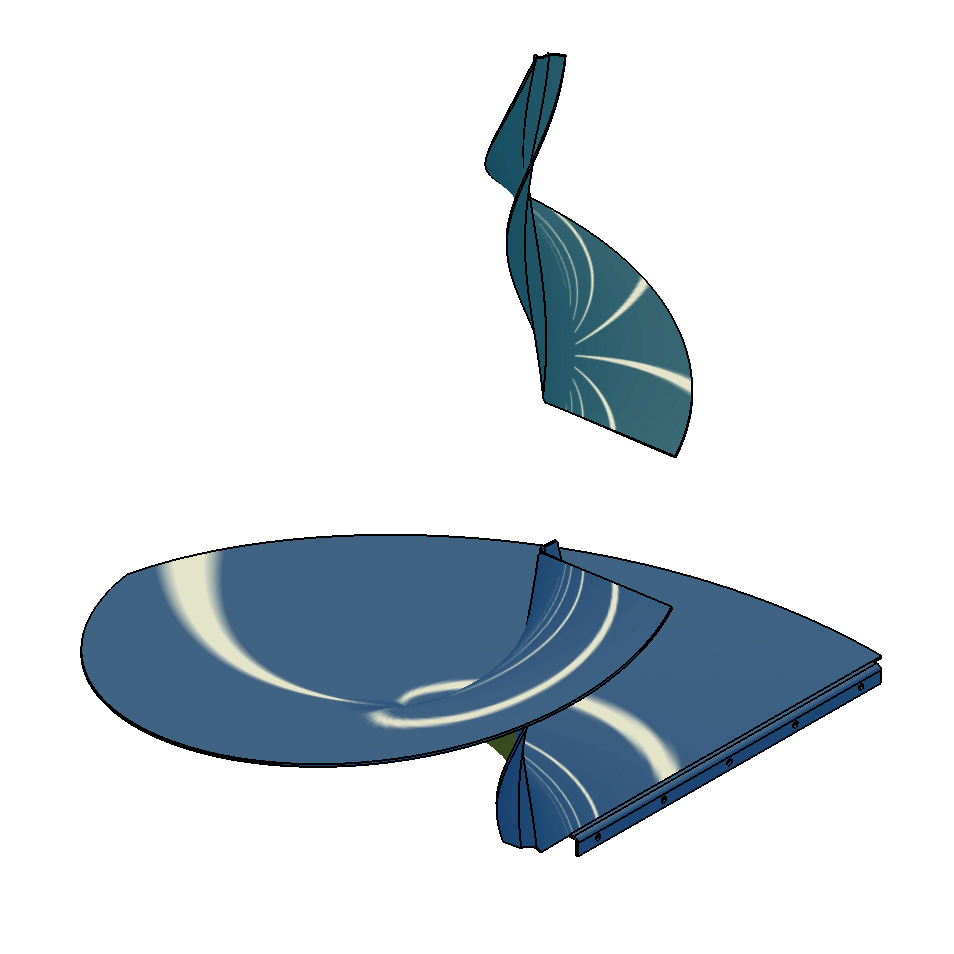
Outillage inversé
Le développement de la forme de l'outillage, dit Falzon, a été la partie la plus difficile du processus. L'équipe ACS-A a évalué la forme de l'ensemble de pales d'origine à l'aide du logiciel CATIA de Dassault Systèmes (Waltham, Mass., États-Unis). Cela a conduit au développement des surfaces des pales et à la conception de concepts d'outillage. « Lorsque vous regardez les pièces telles qu'elles sont aujourd'hui, elles sont en fait fabriquées à l'envers. Le modèle de lame a dû être inversé pour créer l'outillage, et c'est bizarre jusqu'à ce que vous voyiez l'outillage réel quand il arrive. C'est assez complexe », dit Falzon. Il explique que l'outillage a dû être inversé « pour garantir que nous puissions obtenir la finition de surface requise du côté de la lame exposé au flux d'eau » et pour garantir que chacun des composants de la lame fabriqués puisse être démoulé en une seule pièce. L'outillage devait également être précis :les composants des aubes imbriquées devaient pouvoir s'aligner exactement une fois assemblés, les uns avec les autres et avec l'arbre central de la turbine. Pour le prototype, l'outillage, fourni par Sykes Australia (Sydney), a été fabriqué à partir d'une pâte d'outillage à faible coût déposée sur un support en mousse, puis usinée CNC à la forme finale.
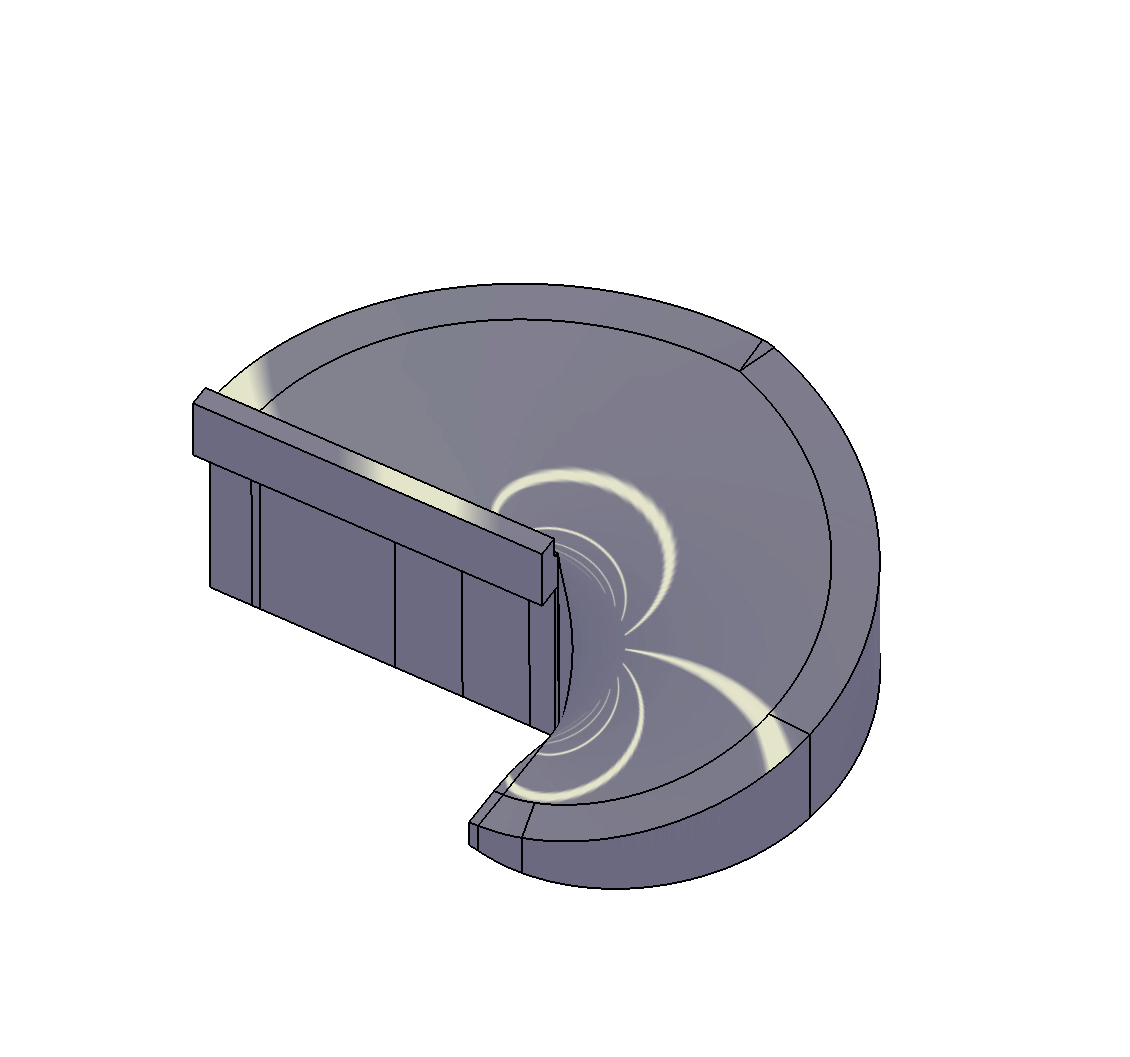
Une fois l'outillage développé, le prototype de lame actuel à grande échelle a été construit à partir de tissu en fibre de verre sans sertissage (NCF) et de résine époxy, fabriqué par drapage à la main et durci à température ambiante, suivi d'une post-polymérisation dans un four à température élevée et application d'une peinture de qualité marine. Les matériaux ont été sélectionnés, note Falzon, pour répondre aux exigences structurelles et financières de la pièce. Les sous-composants imbriqués sont liés par adhésif - choisis plutôt qu'une fixation mécanique pour un meilleur contrôle et une précision dimensionnelle lors de l'assemblage. "Le vrai truc", dit-il, "est de s'assurer que les pales peuvent s'emboîter, mais une fois que nous avons tout stratifié et collé ensemble, il forme un assemblage très rigide qui atteint les performances de forme structurelle et hydrodynamique nécessaires."
L'analyse numérique de la rigidité de la structure et d'autres propriétés mécaniques a été réalisée à l'aide d'outils de MSC Software (Newport Beach, Californie, États-Unis). "Ce système est beaucoup plus efficace, plus léger et capable de faire plus de travail que la conception d'origine", ajoute Falzon.
Propulser vers la production commerciale
Selon Wren, l'objectif de production initial de Kinetic NRG sera de 950 unités sur une période de trois ans, puis passera à plusieurs milliers par an. Les clients potentiels, dit Wren, peuvent inclure des particuliers et des entreprises, des compagnies d'électricité et des municipalités - un large éventail, soulignant la polyvalence du concept HEG. Les systèmes peuvent être installés en tant que « mini centrales hydroélectriques » dans les canaux d'irrigation, ou placés en aval des générateurs hydroélectriques existants pour générer de l'électricité à partir d'un écoulement sous-utilisé, ou en tant qu'alimentation supplémentaire pour les communautés ou les entreprises éloignées, dit-il.
Actuellement, le prototype HEG à grande échelle est en cours d'essais mécaniques dans l'eau ; pendant ce temps, les processus de fabrication à grande échelle sont évalués pour la production commerciale.
ACS-A prévoit de continuer à affiner la conception de la pale, selon les besoins, en fonction des résultats des tests mécaniques et des exigences pour une fabrication la plus rentable possible. Plus précisément, Falzon indique que l'ACS-A explore les processus de préformage automatisés "afin que nous puissions obtenir la bonne forme avec un minimum de travail manuel", suivis d'un moulage par transfert de résine léger (L-RTM) ou d'un autre processus à plus grande vitesse.
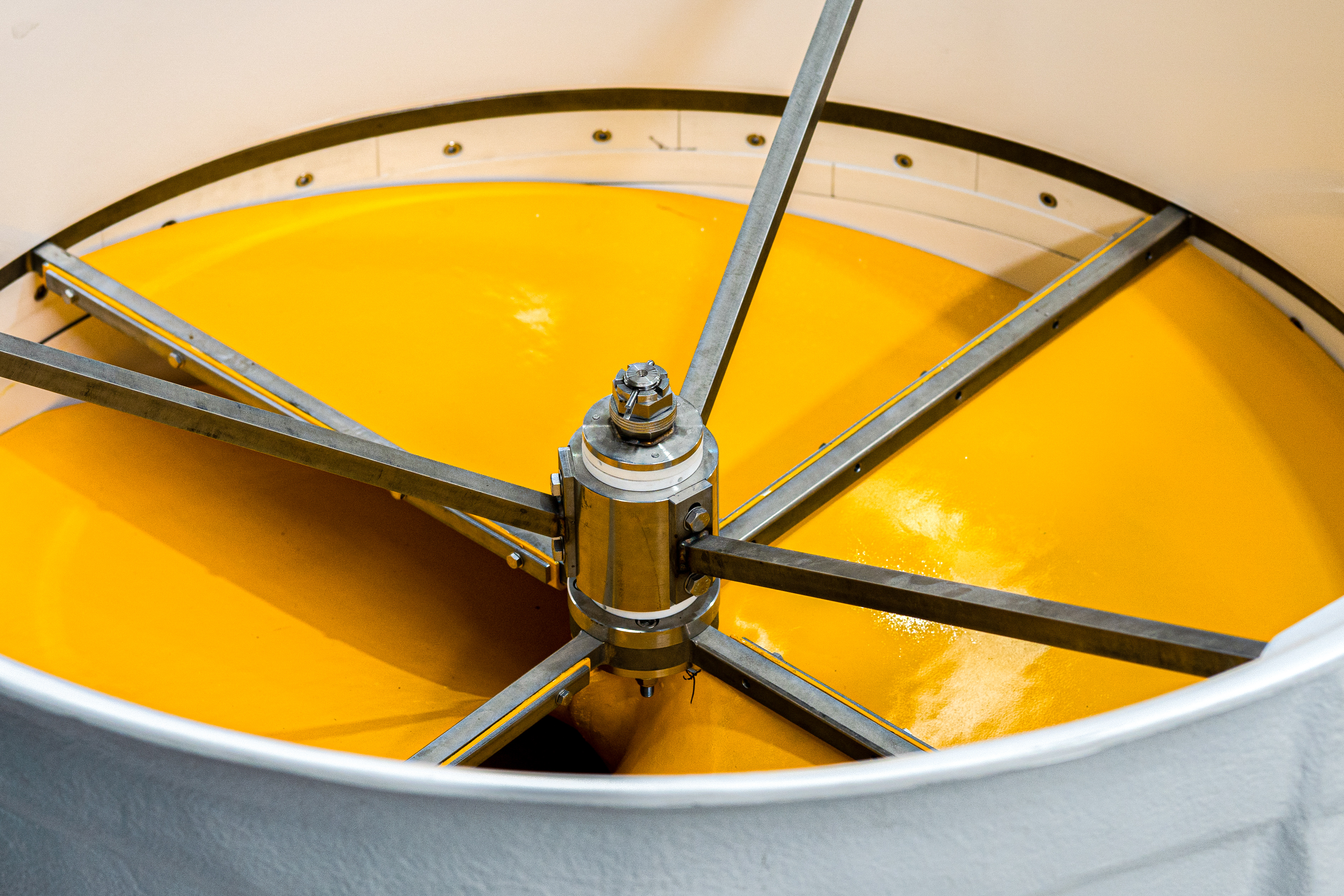
Les méthodes d'assemblage des turbines sont également en cours d'évaluation, l'objectif étant, selon Wren, que les sous-composants des pales soient produits de manière modulaire et assemblés localement, afin d'éviter les coûts et les défis liés à l'expédition d'unités entières à grande échelle tout en créant des opportunités d'emploi local et en réduisant les coûts d'installation. . Pour rendre cela possible, ACS-A peut également avoir besoin de modifier la manière dont les lames s'emboîtent et le nombre de sous-composants dans chaque assemblage. "Nous aurons toujours les pales complètes dans leur forme d'origine, ce sera toujours un élément clé", dit Wren, "mais nous pouvons changer l'endroit où les transitions se produisent afin de créer la même forme en moins de composants pour plus de facilité assemblage sur site."
Les deux sociétés évaluent également la conversion des composants métalliques de la turbine en composites, afin de réduire le poids de l'ensemble global. "Nous utiliserons du verre le cas échéant et de la fibre de carbone le cas échéant, mais en fin de compte, nous devons atteindre un prix pour la technologie afin de rendre le coût de production d'énergie pour le système compétitif", a déclaré Falzon.
Alors que le processus de conception et de fabrication approche de l'optimisation, le prochain défi sera, selon Wren, d'obtenir les bons partenariats d'investissement et de fabrication pour atteindre les volumes commerciaux.
Résine
- La conception de référence de badge intelligent comprend un SoC Bluetooth
- Relever les défis de conception des compteurs d'énergie CC de précision
- Megger fait un don au programme d'énergie éolienne d'Iowa Lakes
- Considérations et contraintes relatives à la conception du système de transport d'énergie
- CompositesWorld SourceBook 2022
- Initiative CETEC mise en place pour commercialiser une technologie permettant la recyclabilité complète des pales d'éoliennes en composite
- Continuous Composites, Siemens Energy applique des matériaux hautes performances pour les groupes électrogènes
- Composites hautes performances en Israël
- Comprendre l'énergie hydroélectrique