La fabrication additive ajoute de la polyvalence aux grandes structures marines
La capacité de construire rapidement différentes itérations de pièces - sans avoir à développer ou à acheter un outillage dédié coûteux - est la raison pour laquelle la fabrication additive (AM) est si souvent utilisée dans le prototypage de pièces. Cependant, à mesure que les matériaux et les technologies d'impression continuent de s'améliorer, de plus en plus d'entreprises sont en mesure d'étendre la vitesse et la polyvalence de la FA aux pièces d'utilisation finale, en particulier pour les applications à court terme ou uniques où la capacité de produire rapidement de nouvelles conceptions est un atout. .
Récemment, deux sociétés ont démontré que les technologies de FA composites peuvent être des solutions pour la personnalisation de grandes structures marines telles que les véhicules sous-marins autonomes (AUV) et les bateaux à moteur.
Impression 3D grand format pour une production AUV personnalisable
Les véhicules sous-marins autonomes sont un type de véhicule robotique sans pilote capable de voyager sous l'eau sans connexion physique à un bateau ou télécommande d'un opérateur humain, et sont souvent équipés de caméras ou de capteurs pour divers cas d'utilisation dans la défense, la recherche océanique ou les applications d'enquête offshore. En règle générale, les coques extérieures des AUV comprennent soit un grand récipient sous pression en métal, soit elles sont construites en plastique thermoformé ou en composites. Les deux options, cependant, nécessitent le développement et l'achat d'un outillage dédié, ce qui peut être coûteux et limite la quantité de personnalisation qui peut être adaptée pour les clients AUV. Le fabricant d'AUV Dive Technologies (Quincy, Mass., États-Unis) a découvert que l'impression 3D composite résout bon nombre des limitations de la fabrication traditionnelle.
En 2018, les co-fondateurs de Dive Technologies, Bill Lebo, Jerry Sgobbo et Sam Russo, ont décidé de créer leur propre entreprise pour concevoir et lancer un nouvel AUV plus performant qui répond aux demandes des clients en matière de longue endurance et de grande capacité de charge utile.
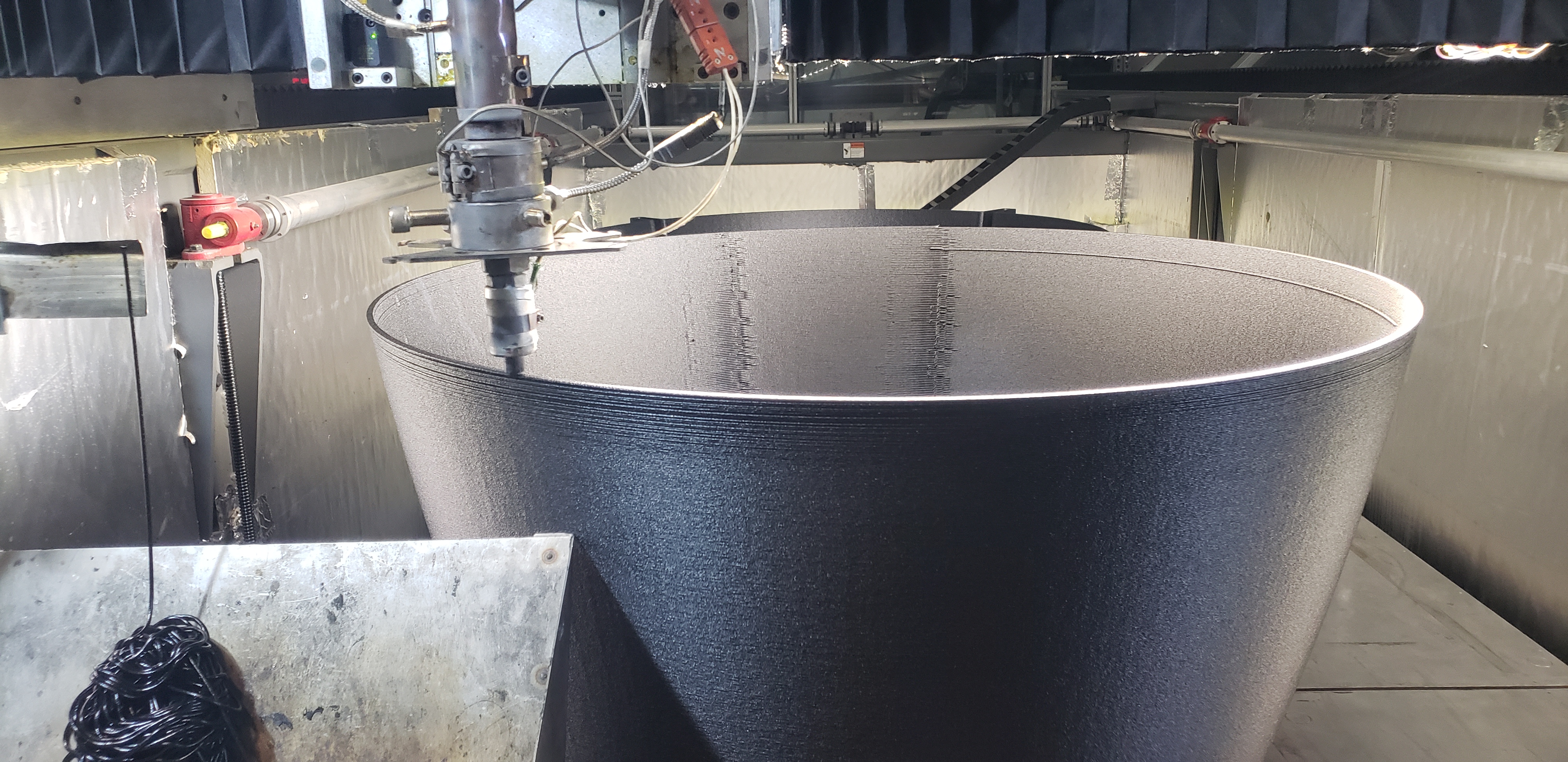
Ce qu'eux et leur équipe ont développé est le DIVE-LD, un AUV commercial de 19 pieds de long et 4 pieds de diamètre capable de plonger à 6 000 mètres et de parcourir jusqu'à 500 miles, transportant une charge utile allant jusqu'à 1 mètre cube. À l'origine, l'équipe supposait que la structure finale de son véhicule utiliserait des plastiques thermoformés pour la coque extérieure. Pour explorer et tester la conception, Dive Technologies a discuté avec le Oak Ridge National Laboratory (ORNL, Oak Ridge, Tenn., États-Unis) de l'utilisation de l'impression 3D pour le prototypage rapide. Grâce à ORNL, l'équipe Dive a été présentée au spécialiste de la fabrication additive grand format (LFAM) Additive Engineering Solutions (AES, Akron, Ohio, États-Unis), et a commencé à travailler avec l'équipe AES sur un processus de fabrication pour ses formes de coque AUV.
Au cours du travail sur les prototypes imprimés en 3D, cependant, Dive Technologies a réalisé le potentiel de LFAM pour produire rapidement des finis composants, pas seulement des prototypes. Non seulement les composants prototypes imprimés en 3D répondaient mieux aux exigences des pièces que prévu, mais l'adoption de la FA pour les véhicules de production permettrait également d'économiser les coûts d'outillage, permettrait à Dive de produire des produits finis plus rapidement qu'en utilisant les méthodes traditionnelles et permettrait un nouveau niveau plus élevé de personnalisation rapide pour clients.
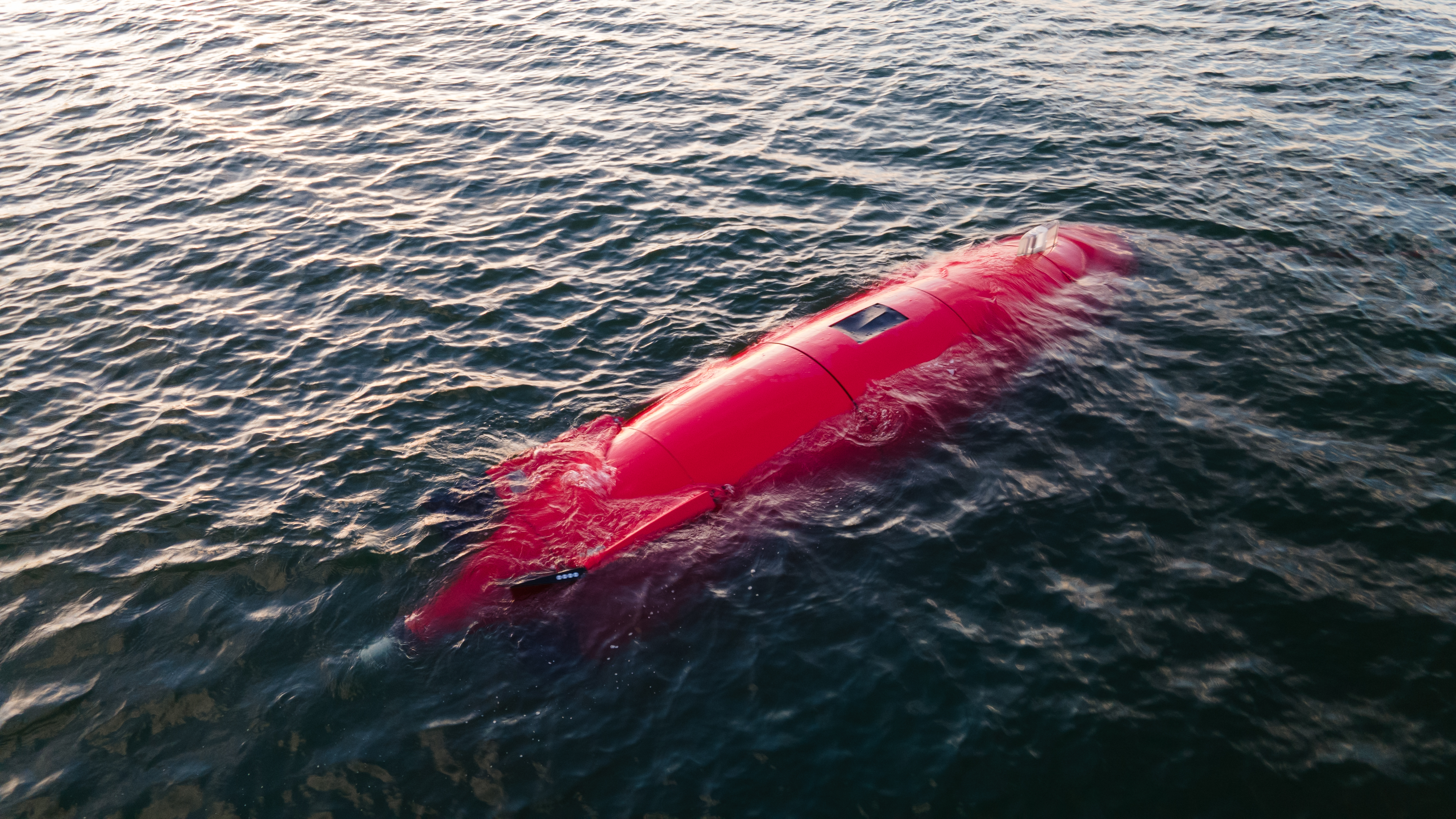
La coque extérieure du DIVE-LD comprend neuf carénages en forme de tube imprimés à l'aide de l'une des quatre imprimantes 3D AES de Cincinnati Inc. (Cincinnati, Ohio, États-Unis) Big Area Additive Manufacturing (BAAM). Ces carénages sont imprimés à partir d'ABS chargé de fibres hachées fourni par Sabic (Riyad, Arabie saoudite). Selon le co-fondateur et vice-président d'AES, Andrew Bader, AES peut imprimer toutes les pièces d'une coque complète en moins de deux jours. Une fois livrés à Dive, les carénages imprimés en 3D sont fixés mécaniquement à l'aide de quatre attaches par carénage et revêtus pour produire une surface extérieure lisse et hydrodynamique. Après des tests initiaux réussis en 2020, Dive construit les premiers véhicules clients ce printemps et livrera la première commande en juin 2021.
Selon Russo, la FA est devenue un élément essentiel de la proposition de valeur de Dive Technologies pour les futurs véhicules et produits. Le partenariat avec Dive est également un grand pas pour l'impression 3D AES et composite. Bader ajoute : « Habituellement, lorsque les gens pensent à l'impression 3D, ils pensent aux prototypes, aux montages et à l'outillage, ce qui montre de quoi d'autre l'impression 3D est capable. »
Pour en savoir plus sur Dive Technologies et AES, lisez « L'impression 3D grand format permet une production rapide et sans outil pour les AUV. »
AM à fibre continue et automatisation pour une conception polyvalente de bateaux à moteur
Depuis le brevetage de son procédé de fabrication de fibres continues (CFM) en 2015, Moi Composites (Milan, Italie) a exploré une gamme d'applications pour sa technologie CFM d'impression 3D à fibres continues basée sur le dépôt. Les caractéristiques de CFM incluent le logiciel de conception personnalisé de Moi Composites, l'utilisation de bras robotiques, le durcissement UV et la fabrication « hybride » - une stratification composite plus traditionnelle sur un noyau structurel imprimé en 3D. Récemment, la société a démontré sa technologie CFM en tant que solution pour une conception de structures marines plus rentable, plus rapide et plus innovante, grâce à un bateau à moteur de démonstration appelé MAMBO.
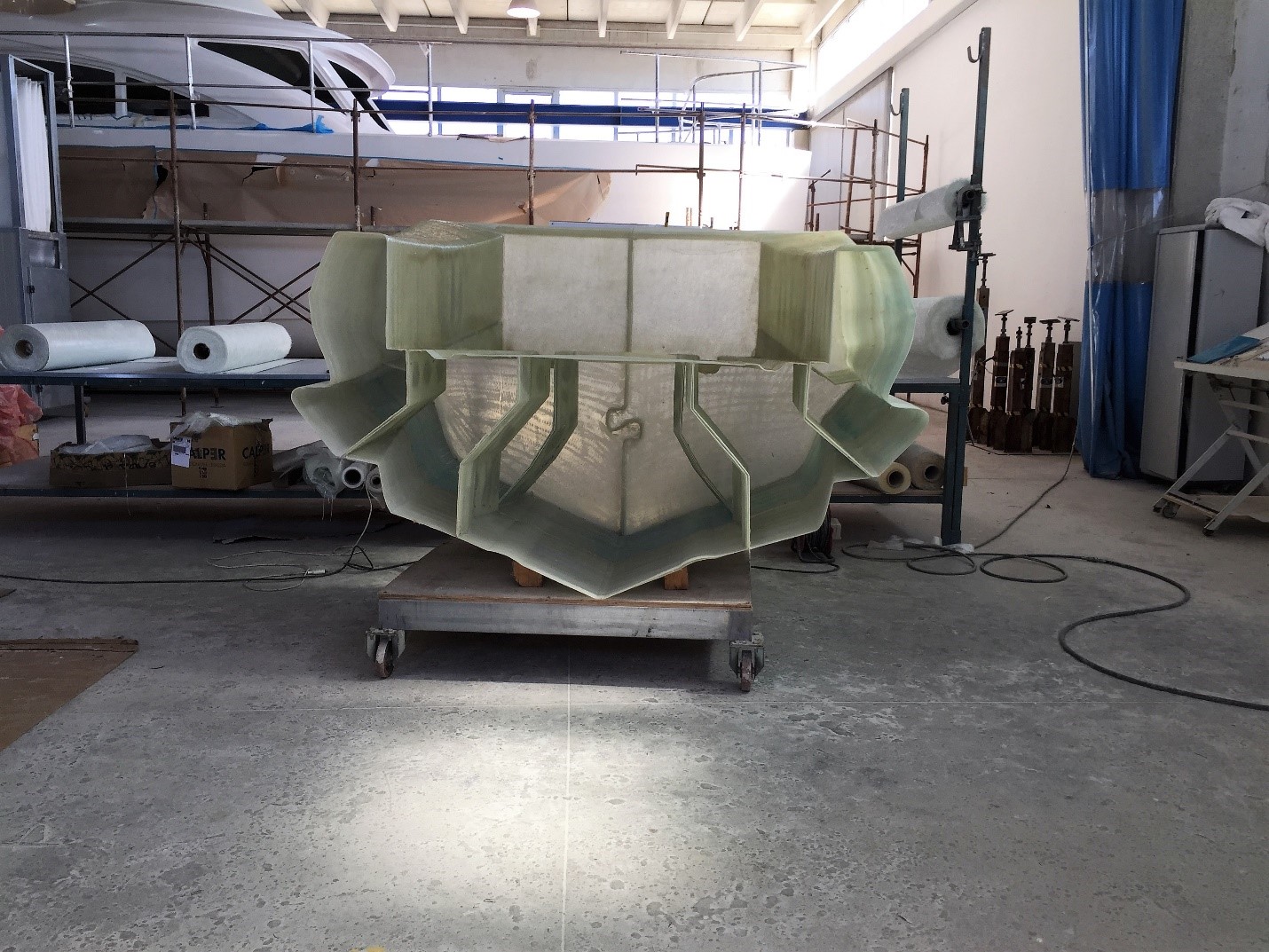
Selon Gabriele Natale, co-fondateur de Moi Composites, lui et son co-fondateur Michele Tonizzo ont assisté au salon nautique de Gênes en 2017 et ont réalisé que les coûts d'outillage et les procédés traditionnels d'infusion de fibre de verre utilisés pour de nombreuses coques de bateaux limitent la capacité des concepteurs de bateaux à explorer de nouvelles et des conceptions plus complexes. Reconnaissant que leur technologie d'impression 3D à fibre continue sans moule pourrait être une solution habilitante, Natale a déclaré :« À partir de là, nous avons commencé à élaborer un plan et à rencontrer des partenaires de l'industrie maritime. »
Le bateau MAMBO résultant mesure 6,5 mètres de long sur 2,5 mètres de large, avec un poids à sec d'environ 800 kilogrammes, équipé d'un système de navigation, d'un sol en liège, de sièges en cuir blanc et d'un moteur de 115 chevaux. Moi Composites a travaillé avec le studio d'ingénierie de conception marine MICAD (Lecce, Italie) sur le concept de conception structurelle du bateau, qui combine des formes organiques dans ses éléments structurels inspirés du célèbre catamaran Arcidiavolo de Sonny Levi. Autodesk (San Rafael, Californie, États-Unis) Fusion 360 CAD et les logiciels de fabrication additive NETFABB ont été utilisés dans la conception et l'analyse dynamique des fluides des composants.
La coque et le pont du bateau, imprimés à partir de verre E unidirectionnel fourni par Owens Corning (Toledo, Ohio, États-Unis) et de résine vinylester, ont été conçus pour être fabriqués en 50 sections individuelles de différentes tailles. La moitié des sections ont été imprimées dans l'usine de Moi Composites à Milan et l'autre moitié dans l'usine de fabrication avancée (ACF) du partenaire Autodesk à Birmingham. La technologie d'impression 3D CFM de Moi Composites et les robots doubles Kuka (Augsbourg, Allemagne) ont été utilisés dans les deux installations. Selon Dominique Müller, directeur de recherche au sein de l'équipe de fabrication additive d'Autodesk, le système CFM du centre technologique d'Autodesk a permis d'imprimer rapidement le bateau et a également permis à Autodesk de mieux connaître la technologie que Moi pilotait à distance à l'aide du logiciel Autodesk. . Le temps d'impression total pour tous les composants était d'environ deux mois.
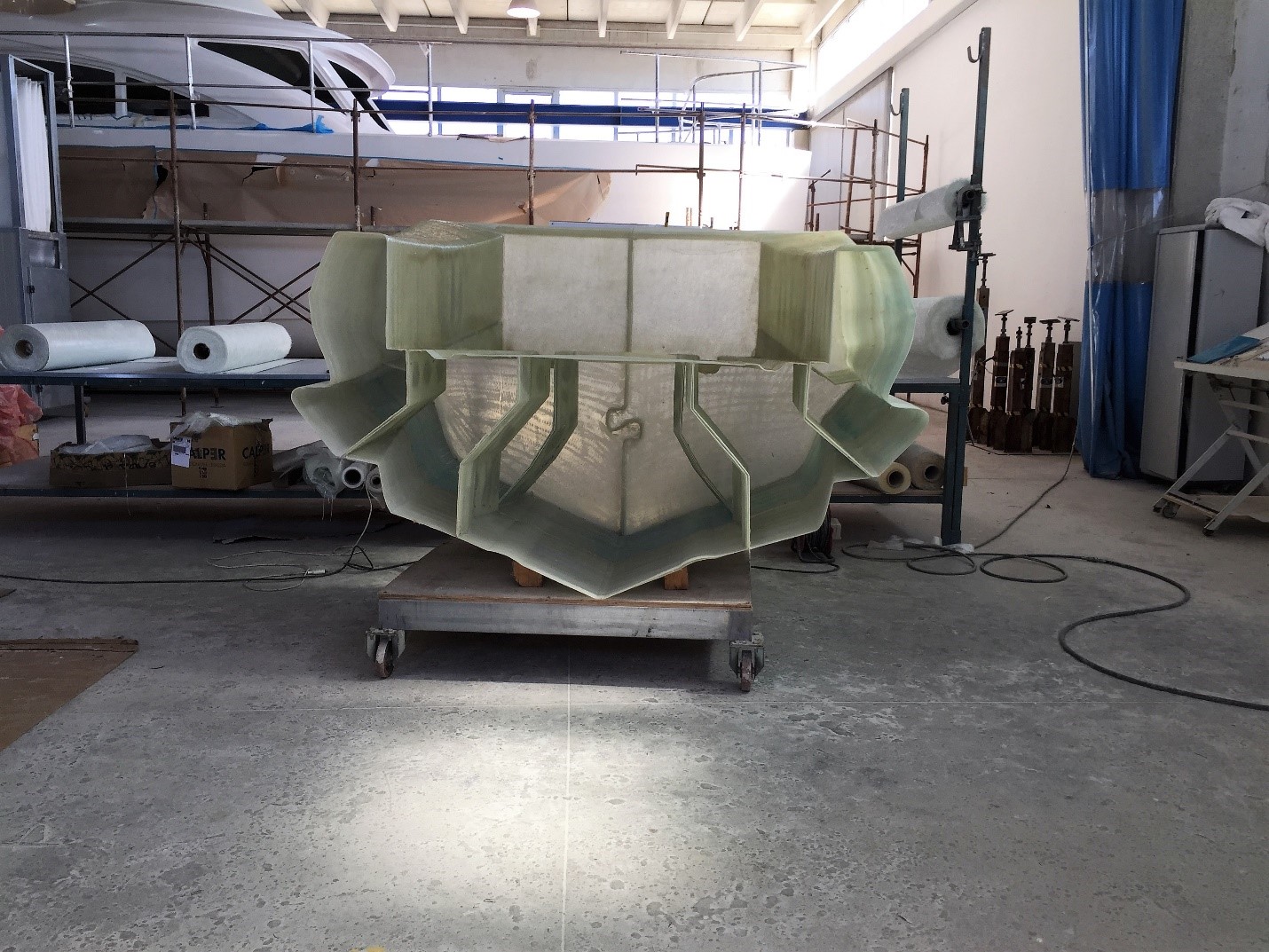
Les pièces imprimées ont été expédiées au chantier naval Catmarine à Miggiano, en Italie, où elles ont été reconstituées et collées. Dans un processus de fabrication hybride similaire à celui que Moi a utilisé avec des prothèses et d'autres pièces, la coque entière a ensuite été laminée à la main avec une couche supplémentaire de fibre de verre/polyester recouverte de mousse PVC, qui, selon Natale, varie en épaisseur le long de la structure. Une fois la coque et le pont entièrement assemblés, poncés et enduits de gel, les partenaires de Moi Composites ont équipé le bateau de systèmes de propulsion, de navigation et d'autres pour compléter le bateau.
Les premiers essais en mer et tests de stabilité ont été effectués à l'automne 2020, le MAMBO atteignant jusqu'à 26 nœuds ; Moi Composites prévoit de poursuivre les essais en mer à l'été 2021 en vue de la certification du bateau.

« La fabrication additive, la numérisation et l'automatisation peuvent accélérer la création de nouveaux concepts et de projets futuristes, car pour chaque bateau que vous souhaitez concevoir, vous devez créer un nouveau moule. Grâce à cette technologie, vous pouvez facilement modifier votre modèle 3D et l'imprimer à nouveau. C'est parfait, en particulier pour les bateaux de courte durée ou ponctuels », explique Natale.
Pour en savoir plus sur MAMBO, lisez « MAMBO teste les eaux pour l'impression 3D de grandes structures marines. »
Résine
- 5 processus courants de fabrication additive
- Fabrication additive vs fabrication soustractive
- Avantages de la fabrication additive
- Henkel propose une plate-forme de matériaux pour la fabrication additive
- Le NCAMP lance le premier programme de qualification pour la fabrication additive
- Les thermoplastiques durables et la fabrication additive forment une alliance au Colorado
- 5 technologies perturbant la fabrication
- Fabrication additive en électronique
- Fabrication additive dans l'aérospatiale