Le meulage par pincement double rugueux réduit de moitié le temps de cycle
Le « besoin de rapidité » de la fabrication est plus vrai aujourd'hui que par le passé, car les clients exigent une rotation plus rapide des produits. Et si un fabricant ne peut pas s'adapter, le client trouvera une autre entreprise qui le fera. Par conséquent, de nombreux ateliers d'usinage inventent des processus ou investissent dans de nouveaux équipements plus efficaces pour permettre
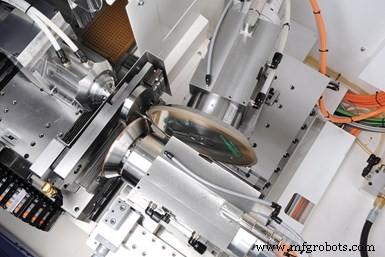
Le processus de meulage par pincement cylindrique à double ébauche est illustré sur les deux photos. Cependant, la photo du haut montre la roue positionnée à 10 degrés. Ici, la roue se déplace presque en ligne avec l'axe de la pièce. La meule peut meuler plus efficacement si elle avance dans le matériau dans un tel mouvement axial. Cependant, à 90 degrés (photo du bas), la roue peut effectuer des mouvements pour les angles arrière et les évidements, mais plus de vibrations seront introduites par rapport à la position à 10 degrés. Selon Rollomatic, la position à 10 degrés doit être utilisée si le profil le permet. Crédits photos :Rollomatic Inc.
production plus rapide.
Cela vaut également pour les fabricants d'outillage. Un processus qui peut les aider à le faire est un processus de meulage par pincement alternatif appelé meulage cylindrique par pincement à double ébauche. Non seulement le nouveau processus de meulage réduit de moitié le temps de cycle par rapport au meulage par pincement traditionnel, mais il génère également moins de chaleur et est un processus plus silencieux, pour ne citer que quelques avantages.
Cette méthode de meulage par pincement à double ébauche a été conçue par Rollomatic Inc. spécifiquement pour la préparation des ébauches d'outils de coupe en carbure et de fraises à rainures en T. Le processus a été intégré dans la rectifieuse à pincer/peler ShapeSmart NP50 de la société, qui a été initialement développée en 1996.
La méthode diffère du meulage par pincement traditionnel qui utilise une meule d'ébauche principale pour enlever la majeure partie du matériau, qui est ensuite suivie de près par une meule de finition opposée pour fournir une finition fine. Les deux meules s'opposent lors du meulage simultané, contrecarrant ainsi leur pression sur la pièce. A l'inverse, lors de la rectification par pincement à double dégrossissage, les deux stations de rectification sont équipées de meules diamantées avec une granulométrie pour la rectification dégrossissante. Ces deux meules d'ébauche fonctionnent de manière synchrone, mais la meule d'attaque effectue la majeure partie de l'enlèvement de matière. L'autre roue nettoie le matériau laissé par la première roue. La distance de retardement de la deuxième meule dépend de la position le long du profil car le processus de double ébauche a été spécifiquement développé pour le rétreint des ébauches d'outils.
Les broches de meulage jouent également un rôle important dans le processus. Les broches à entraînement direct synchrone du NP50 ont chacune une puissance maximale de 19 ch avec un moteur synchrone qui fournit une vitesse constante pendant le fonctionnement. La courbe de couple est également très efficace, selon Rollomatic. La force de rotation du moteur synchrone n'est pas réduite avec un régime plus élevé.
Les broches synchrones efficaces de la machine sont également avantageuses car elles ne fonctionnent qu'avec une consommation électrique de 35 % ou moins. En conséquence, ils ne dégagent aucune chaleur dans la machine ou dans le processus de broyage. On dit également qu'ils fonctionnent beaucoup plus silencieusement, même sous charge, par rapport à leur homologue à moteur à induction.
Exemple
Rollomatic suggère que cette méthode de meulage convient le mieux aux pièces en carbure et en acier trempé. On dit que la dureté et la résistance à la chaleur de ces matériaux en font les meilleurs choix pour la broyabilité.
Par exemple, sur un essai de production de 100 pièces d'ébauche en carbure monobloc avec un diamètre de tige de 5/8 de pouce, un diamètre de col de 0,400 pouce et une longueur de col de 2,25 pouces, le meulage par pincement à double ébauche a réduit le temps de cycle à 5 minutes et 5 secondes, par rapport à un temps de cycle d'environ 10 minutes avec la rectification par pincement d'ébauche/finition conventionnelle, selon l'entreprise.
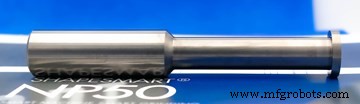
Cette ébauche de rainure en T en carbure monobloc a été rectifiée en utilisant la technologie de meulage à double pincement. Lors d'un test de production dans la machine de meulage par pincement/pelage ShapeSmart NP50 utilisant un meulage par pincement à double ébauche, le temps de cycle sans chargement/déchargement était de 5 min. et 5 secondes.
Finitions acceptables, répétabilité améliorée
Le meulage par pincement à double dégrossissage peut obtenir une finition de surface de 12 à 32 micropouces par rapport à 1,2 micropouces avec une meule diamantée de finition.
Le processus reproductible de cette méthode de broyage est un autre avantage. Selon Rollomatic, un opérateur peut mettre en place un travail de meulage sans avoir à composer continuellement et méticuleusement des avances et des vitesses optimales.
La répétabilité de la technologie permet également la production de lots longs sans qu'il soit nécessaire de redresser fréquemment les meules. Selon la société, les meules d'ébauche ont généralement une meilleure rétention des coins que les meules de finition à grain plus fin.
Avec tous les avantages d'efficacité qu'offre la rectification par pincement à double ébauche, il existe encore plus de capacités disponibles sur la rectifieuse NP50 qui améliorent la productivité.
Bien que la machine offre cette technologie de meulage par pincement à double dégrossissage, le meulage par pincement de dégrossissage et de finition peut toujours être effectué sur la machine. De plus, des options telles que la mesure des pièces et les unités de chargement automatique sont disponibles.
Si la mesure de pièces en cours de fabrication est importante pour une application, Rollomatic propose une jauge de diamètre Marposs en option sur la machine. L'unité mesure le diamètre à un endroit le long de l'axe de l'outil, et le retour signale à la machine d'effectuer une compensation automatique de la position de la roue. Selon l'entreprise, cette correction est utile en cas de changements de température ambiante et d'usure des meules. La jauge peut également être utilisée pour palper des méplats et prérégler la position circulaire de la pièce en fonction de la surface plane.
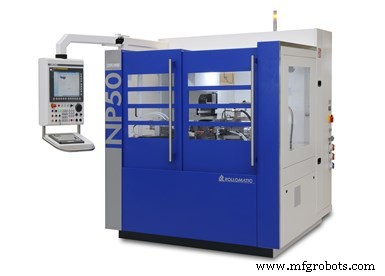
La rectifieuse par pincement/pelage ShapeSmart NP50 effectue non seulement le broyage par pincement/pelage traditionnel, mais a également été mise à niveau pour utiliser la technologie de broyage par pincement à double rugosité. Le meulage à double pincement grossier réduit de moitié le temps de cycle, améliore la finition de surface et produit également moins de chaleur et de bruit.
Des unités de chargement automatisées peuvent également être intégrées dans la machine NP50 standard. Un chargeur d'outils automatique à trois axes et à grande vitesse a été développé par la société avec une vitesse de configuration rapide à l'esprit. Il utilise des cassettes pré-calibrées et une conception de pince qui permet de maintenir différents diamètres sans avoir à réinitialiser les positions de la pince.
Rollomatique | rollomatic.ch/fr
Équipement industriel
- La rentabilité de la fabrication grâce à des outils de coupe bien entretenus
- Théorie de la meule | Métaux | Secteurs | Métallurgie
- La tourelle de travail final réduit le temps de cycle
- Job Shop réduit le temps de traitement de 60 %
- Utilisation du tournage dur pour réduire le temps de meulage
- Le mandrin CNC à double broche réduit le temps de production
- Comment améliorer le temps de cycle dans l'usinage automobile
- Temps de cycle vs. Takt Time :pourquoi les différences sont importantes
- Calcul du temps de cycle d'usinage CNC