Qu'est-ce qu'un motif dans le moulage au sable? Processus de moulage en fonderie
Dans l'industrie métallurgique, le modèle de moulage est une réplique qui a une forme et des dimensions similaires à celles du moulage. Les modèles de moulage sont utilisés pour presser dans le moule en sable pour créer la cavité creuse qui permet au métal en fusion d'être versé et de former le moulage.
Dans la fonderie de moulage au sable (quelle que soit la fonte, l'aluminium ou l'acier), un ensemble de modèles comprend le modèle, la tête de fraisage du système de porte, la colonne montante et la plaque de modèle.
Le matériau, la conception et la structure du motif ont un effet considérable sur la qualité des produits. De même, le coût de fonctionnement et de fabrication de modèles peut être bien pris en compte dans les dépenses de moulage .
Matériaux de modèle de moulage dans la coulée de métal
Conseils pour choisir les matériaux des motifs
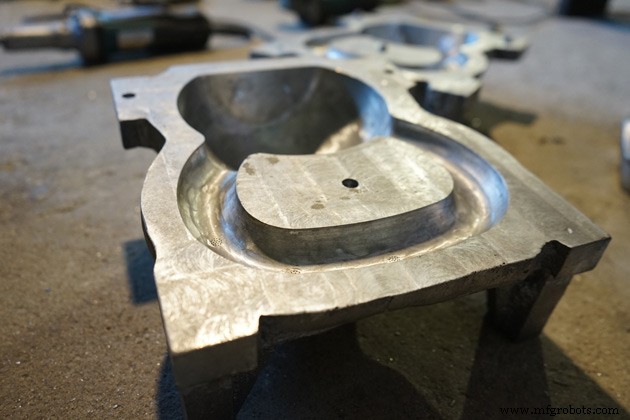
– Robuste et durable :choisissez les matériaux de motifs qui durent longtemps, ne se déforment pas et ne changent pas de forme pendant le processus de coulée.
– Anti-abrasion et résistance à l'eau :il est essentiel de choisir des matériaux résistants à l'eau et à la corrosion pour protéger les motifs de moulage de la rouille et de la dégradation.
– Facile à former :insensible aux changements de température et d'humidité.
– Faible coût et poids réduit :cela assure un équilibre entre coût et profit pour votre fonderie.
Choisissez le matériau pour la création de patrons
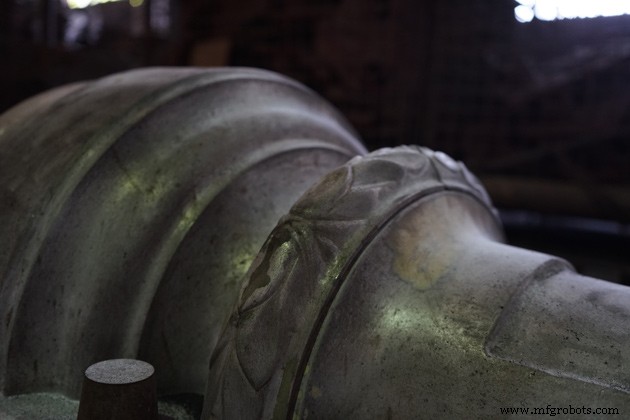
Pour garantir ces critères ci-dessus et dépendre de l'industrie spécifique, les matériaux de modèle doivent être considérés avec leur flexibilité . Le métal, le bois et le plastique sont les matériaux prioritaires dans le processus de modélisme.
- Motifs métalliques :Les motifs en métal assureront la dureté et seront faciles à façonner. Néanmoins, la faiblesse des modèles en métal est qu'il est facile à rouiller et présente une masse importante . De plus, le matériau à motif métallique nécessite également des appareils avancés et est difficile à réparer, ce qui entraîne un coût plus élevé en comparaison globale .
Il existe des métaux couramment utilisés dans le processus de fabrication de modèles, tels que la fer grise, l'acier, l'aluminium et le magnésium . Chacun de ces matériaux de modèle a une propriété de retrait différente.
- Motifs en bois :est un matériau de modèle très populaire en raison de sa disponibilité et de sa petite masse . De plus, le bois peut être formé facilement avec un coût beaucoup moins cher que les modèles en métal. Cependant, l'inconvénient du motif en bois est facile à absorber l'humidité et à se déformer .
- Modèles en plastique :Le plastique et la fibre de verre sont des tendances de nos jours car leur plus grand avantage est la masse légère , étanche et résistant aux produits chimiques . De plus, la finition de surface du plastique est excellente brillance . Pourtant, ce matériau par contre est facile à craquer tout en faisant face à de fortes chocs ou vibrations pendant le processus de coulée.
- Autres matériaux :La cire et le plâtre de Paris sont également utilisés comme matériaux de modèle pour le processus de moulage, mais ils ne sont que préférables dans la technique de moulage de précision .
Types de modèle de coulée dans le travail des métaux
Il existe une gamme de types de modèles dans la coulée de métal et chaque type convient à des exigences de coulée spécifiques. Ici, VIC trie les 3 principaux types de modèles de coulée que l'on trouve principalement dans la fonderie de métaux.
1. Patrons d'une seule pièce
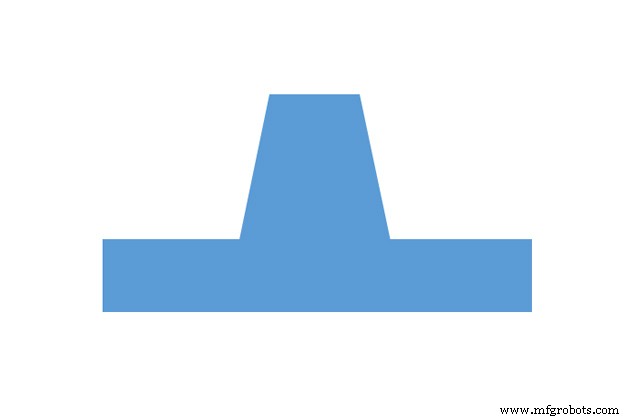
Le patron d'une seule pièce est le type de patron le moins cher . Ce tri est souvent utilisé dans le cas où le moulage est simple, la surface est plane et le volume de production est faible ainsi que dans le développement de prototypes.
2. Motifs divisés ou en deux parties
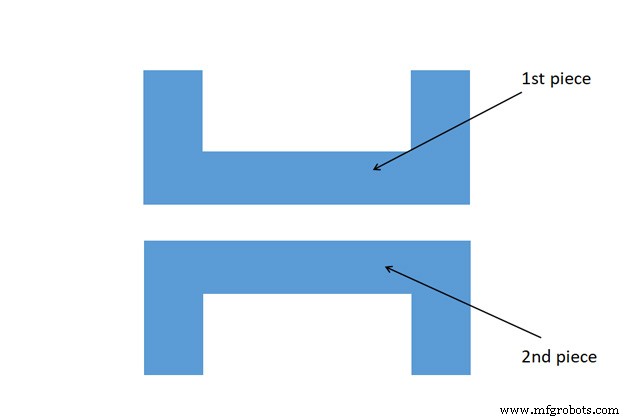
Le modèle en deux pièces est courant dans le moulage d'objets complexes . Ce type de motif est divisé en plans de séparation et la position du plan est déterminée par la forme du moulage.
Le patron est divisé en deux parties, l'une des parties est moulé en drag et l'autre est moulé en chape . La partie de chape a toujours des goujons qui correspond aux trous faits avec précision dans la partie traînée du motif.
3. Motifs segmentés ou multi-pièces
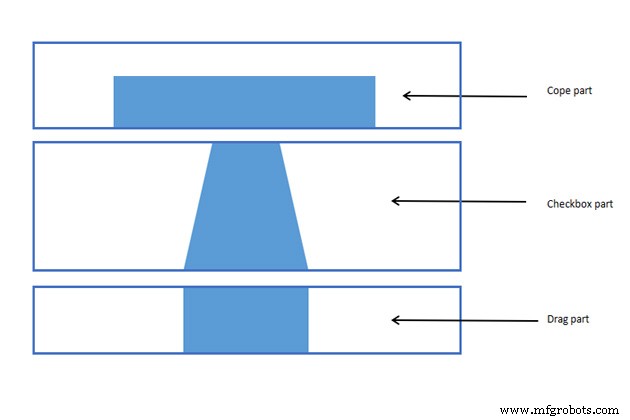
Le modèle multi-pièces préfère couler des pièces de moulage super compliquées qui sont impossibles à réaliser par d'autres méthodes de modélisme. Ce modèle comporte trois parties :partie supérieure, centrale et inférieure.
La partie supérieure est la partie de l'adaptation , la partie inférieure est partie glisser et celui du milieu est la partie case à cocher . Il est utilisé dans divers types de joints tels que le joint à onglet, le joint à cheville.
Processus de fabrication de modèles de moulage en fonderie
1. Conception de motifs
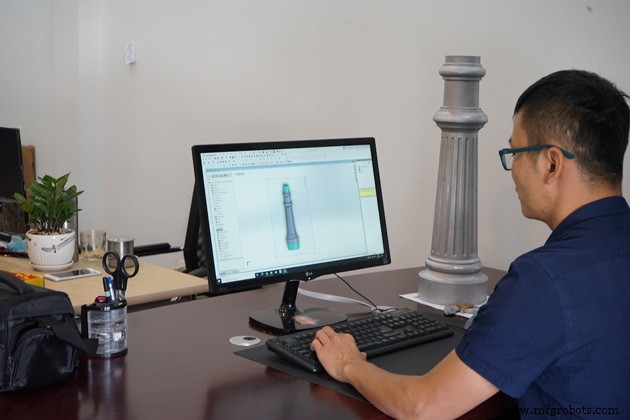
Le service technique travaillant sur le modélisme de fonderie doit examiner attentivement le dessin de moulage pour concevoir un modèle aussi serré et efficace que prévu.
Les points les plus importants doivent être pris en compte, y compris le plan de séparation , forme et dimension du casting et noyau , plus matériau du motif .
Étape 1 :Décidez du plan de séparation
Habituellement, le plan de séparation coïncide avec la ligne du moule de séparation.
Si le motif est de type à pièces fendues ou à plusieurs pièces, les parties supérieure et inférieure doivent être clairement définies même lorsque la surface de séparation est symétrique .
Étape 2 :déterminez la forme et la dimension du support d'impression central.
Le support d'impression de base est utilisé pour supporter l'impression de base à fixer dans le moule.
La tolérance du support d'impression de base affectera directement la tolérance dimensionnelle à l'intérieur du moule. Par conséquent, il doit tenir compte de la forme d'impression du noyau, de l'écart entre le noyau et le motif ainsi que du processus d'assemblage du motif pour concevoir exactement le support d'impression du noyau .
Étape 3 :Déterminer les dimensions et la tolérance du motif
Avec le modèle a des plans de séparation, chaque pièce a une dimension différente et une fois ces pièces assemblées, elles doivent être respectivement avec la dimension de coulée.
Si le motif est en métal, lorsqu'il est condensé, il rétrécira . Par conséquent, si vous prenez la taille correcte du dessin de moulage comme modèle, la taille du moulage sera considérablement plus petite. Pour résoudre ce problème, la cavité du moule doit être agrandie et la taille du motif doit être supérieure à la taille de coulée d'une proportion de retrait du métal. Ceci est déterminé sur la base des allocations de modèle .
Étape 4 :Déterminer les matériaux du motif
- Modèle en bois :Si le motif est petit, il peut être en bois massif. Si le motif est plus grand et plus compliqué, il doit être en bois coupé. Pour représenter un dessin de modèle en bois, vous pouvez dessiner des vues et des coupes complètes, ou utiliser des symboles de pièces de puzzle pour gagner du temps et faciliter la lecture.
- Motif métallique :Applicable à la production de masse ou à la commande à volume élevé. Si le volume du motif est important, il est conseillé de réaliser le motif avec du métal creux interne pour réduire le poids et économiser les coûts de matériaux. Si le motif est petit, choisissez du métal solide.
Étape 5 :Localisation lors de l'assemblage du motif
Pour les échantillons circulaires avec un plan de séparation perpendiculaire à l'arbre centrifuge, une seule goupille est nécessaire.
Pour les autres types, utilisez 2 ou 3 goupilles cylindriques.
En principe, plus la distance entre les goupilles est grande, plus le positionnement est précis. La structure de goupille et de trou doit être de taille raisonnable pour faciliter le retrait et le démontage . Pour les motifs avec des plans divisés, les goujons de la partie de grugeage doivent correspondre aux trous faits avec précision de la partie de traînée.
De plus, sur le dessin du motif, il est nécessaire de spécifier le lissé de la surface et la couleur de peinture des parties du motif.
2. Allocations de modèle de moulage
Les tolérances de modèle reflètent les propriétés du métal coulé. Lorsque le modèle est réalisé, certaines tolérances doivent être accordées sur les tailles spécifiées dans le dessin du composant fini afin qu'un moulage avec la spécification particulière puisse être effectué.
Il existe des indemnités comme suit :
Solidification par retrait (ou allocation de contraction)
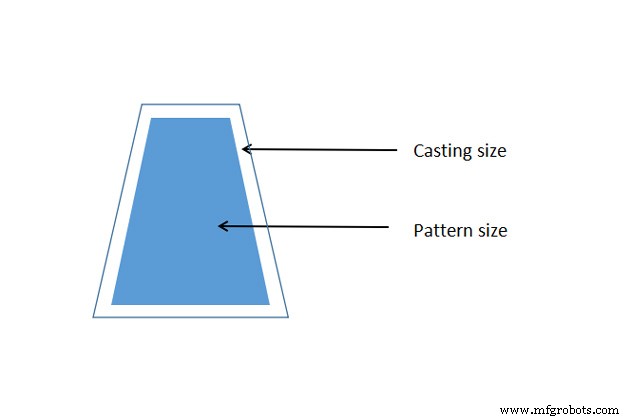
La plupart des métaux ont un retrait pendant le refroidissement, qui est la transition de liquide à solide (appelé retrait liquide) et refroidissement sous forme solide (appelée contraction linéaire).
Le retrait d'un liquide est une diminution de volume lors de la solidification (du liquide au solide). Le retrait liquide est pris en compte par les colonnes montantes, qui alimentent le métal liquide à la coulée, sont fournies dans le moule.
Le retrait solide est une réduction de taille tout en réduisant la chaleur lorsque la coulée de métal est à l'état solide. Pour tenir compte de cela, une marge de retrait est prévue sur les patrons.
Le taux et le niveau de retrait dépendent du matériau. Le tableau suivant montre les taux de retrait pour différents métaux.
Matériel | Rétrécissement |
Fer gris | 1 % |
Acier | 2 % |
Cuivre/Aluminium | 1,5 % |
Fer blanc | 1,5 % |
Magnésium | 1,6 % |
Remarque :Le rétrécissement dépend également de la taille du matériau, plus la taille est longue, plus le rétrécissement est élevé.
Essentiellement, le processus de création de patrons formule de rétrécissement est :
Taille du motif =taille du moulage + retrait du métal
Cependant, lors de l'enregistrement sur le dessin, il est toujours nécessaire de prendre des données en fonction du dessin de coulée. Lors de la fabrication de modèles, utilisez des rapports de taille en fonction des différents alliages coulés.
Allocation de tirant d'eau ou de réduction
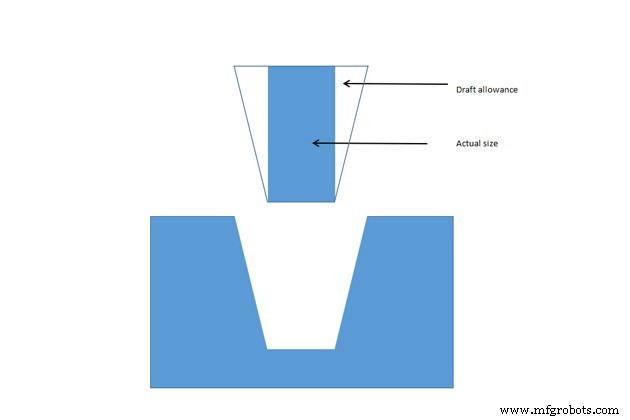
Lorsque le motif est retiré du moule en sable, les parois du moule peuvent être frottées avec le motif, ce qui déchire et endommage le motif. Pour éviter cela, une conicité sur toutes les surfaces verticales du motif doit être créée, c'est ce qu'on appelle la dépouillement d'épaisseur .
Ici, au moment où le soulèvement du motif commence, toutes ses surfaces sont éloignées de la surface du sable. Par conséquent, le motif peut être supprimé sans endommager la cavité du moule.
Le dépouille d'angle est créé pour toutes les faces du motif, qui sont parallèles à la direction de dessin pour faciliter le processus de retrait. Selon la taille des faces extérieures, la valeur de la dépouille d'angle est comprise entre 0,5 et 3 degrés.
Matériel | Hauteur de la surface donnée (pouces) | Angle de dépouille (surface externe) | Angle de dépouille (surface interne) |
Bois | |||
Métal, plastique |
Allocation de finition ou d'usinage
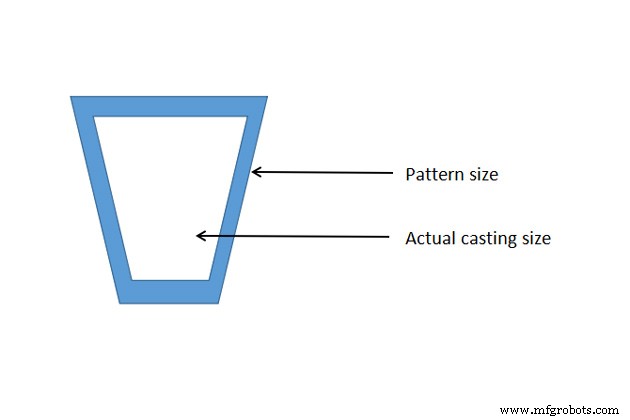
La surface de la pièce moulée collectée n'est généralement pas de taille correcte, de sorte qu'un usinage, tel que le tournage ou le meulage, doit être effectué pour améliorer la qualité de la finition de surface.
Étant donné que l'usinage enlève une quantité de métal de la pièce coulée, une quantité de métal appelée surépaisseur d'usinage doit être compensé. La surépaisseur d'usinage est influencée par la méthode de moulage, la taille du moulage, le matériau de moulage et la possibilité de finition du moulage.
Métal | Dimension (pouce) | Allocation (pouces) |
Fonte | Jusqu'à 12 12 à 20 20 à 40 | |
Acier coulé | Jusqu'à 6 6 à 20 20 à 40 | |
Non ferreux | Jusqu'à 8 8 à 12 12 à 40 |
Allocation de distorsion ou de carrossage
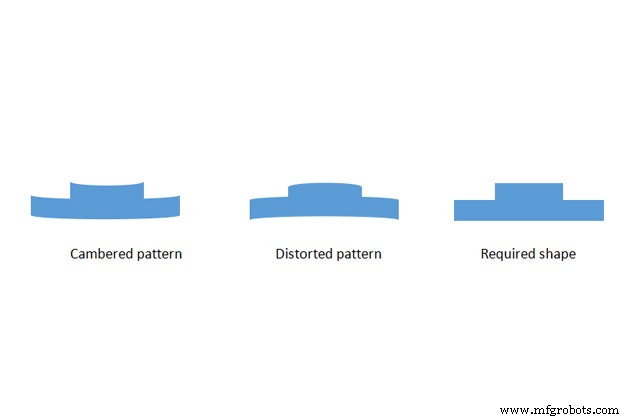
Lors de la solidification, si la pièce moulée a la forme L, U, V, T, … ou est plus fine que la longueur, elle aura tendance à se déformer dans les plans verticaux .
La raison à l'origine de ce problème est que les contraintes internes se sont développées dans le métal solide. Ces contraintes internes sont causées par le refroidissement inégal des différentes parties du moulage, ce qui provoque des conflits de condensation , cela s'appelle allocation de distorsion ou allocation de carrossage .
Le remède à cette situation consiste à modifier la conception du moulage dans le sens d'une déformation initiale du motif dans la direction opposée. Le degré de déformation à corriger est évalué en fonction de l'expérience du modéliste.
Allocation de frappe ou de secousse
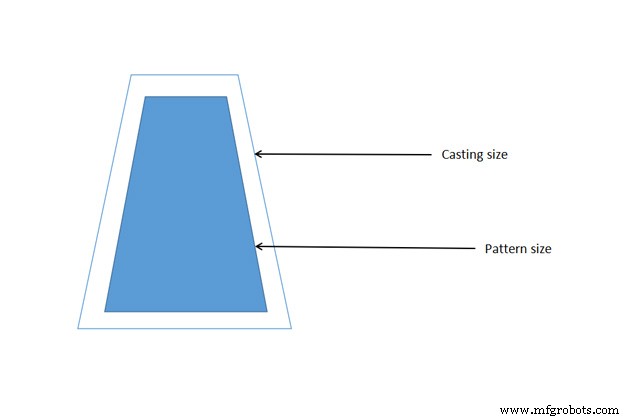
Lors du processus de retrait du motif du moule en sable, avec de grands motifs ou une coulée de haute précision, il est nécessaire de rapper autour de la surface verticale du motif pour élargir la cavité du moule, puis ramasser le motif plus facilement. Elle ne s'appliquait qu'aux cotes parallèles au plan de séparation .
Pour compenser cela, nous devons réduire la taille du motif d'origine. Il n'y a pas de formule standard pour calculer cette allocation car cela dépend beaucoup du travailleur.
Core et impression de base
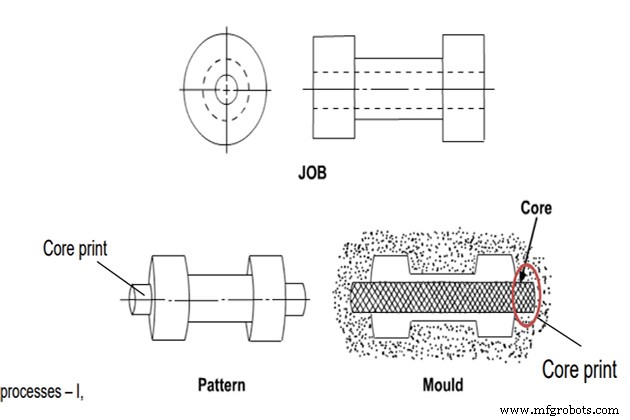
Un noyau est utilisé pour créer des trous ou des évidements dans un moulage . Le noyau est généralement constitué de sable vert ou sec.
L'impression du noyau est fournie dans le moule pour localiser, positionner et soutenir le noyau . Le noyau de sable restera à cette position lorsque le métal en fusion sera versé dans le moule.
Le noyau doit être placé horizontalement, verticalement ou suspendu à l'intérieur de la cavité du moule. Cependant, le noyau ne peut pas s'auto-accrocher à l'intérieur de la cavité du moule sans aucun support. L'impression de base est préparée à l'aide de projections sur le motif . Mais le problème est qu'en enlevant le motif, le moule s'abîme à cause de la présence de ces projections. Par conséquent, le modèle divisé est utilisé pour le processus de moulage dans lequel le noyau est utilisé.
L'impression du noyau doit être de taille et de forme appropriées pour supporter le poids du noyau et la flottabilité du métal en fusion qui l'entoure pendant la coulée.
3. Modélisme
Concevoir un système de porte
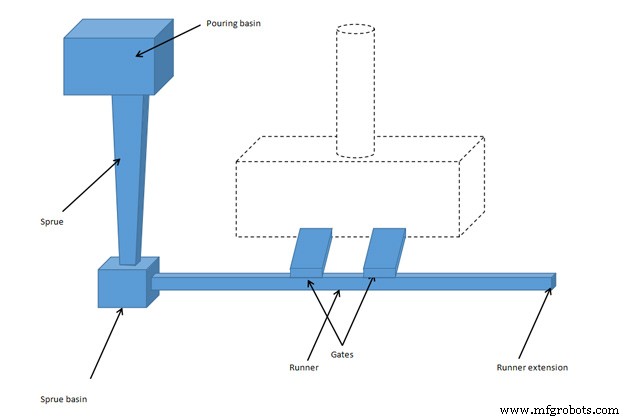
Chaque modèle comprendra un système de porte pour verser le métal liquide dans la cavité du moule . Le système de gating est très important car il régule la vitesse à laquelle le métal est coulé dans le moule. Si la vitesse est trop rapide, cela peut provoquer la corrosion du moule, si elle est trop lente, le métal peut refroidir avant de remplir la cavité.
Ce système de porte se compose des parties connectées suivantes :
- Tasse verseuse :est une entrée en forme de cône dans le moule. Il aide à contrôler la turbulence du flux de métal et stabilise le débit, ainsi que sépare les scories pendant la coulée.
- Carottes :un entonnoir qui conduit le métal en fusion d'une tasse de coulée dans la carotte conique, puis à travers le canal, entrant dans les portes l'une après l'autre.
- Portail :est la fin du chemin, c'est là que commence Mold Cavity.
Il existe deux types de portails :le grand portail et le petit portail. De grandes grilles sont utilisées pour refroidir rapidement le métal et des grilles plus petites sont utilisées pour un refroidissement lent. Selon l'exigence sur le taux de condensation de la coulée, une porte raisonnable est utilisée.
- Riser :Est une cavité de métal en fusion et fait partie du moule prévu pour compenser le retrait du métal car il réduit la température et aide à prévenir les trous. La colonne montante est l'endroit où le métal liquide se refroidit lentement. En fonction de la colonne montante, le travailleur saura si la matrice est remplie ou non.
Si le moulage a des trous dans la conception, le noyau doit être placé dans le moule pour déterminer la position où le métal ne coulera pas.
Parfois, il est possible de placer des frissons sur la surface du motif avant la coulée pour refroidir localement afin de déterminer l'ordre de refroidissement des métaux liquides. Les frissons peuvent être facilement récupérés et réutilisés car ce ne sont que des morceaux de métal qui ont une température beaucoup plus froide et qui ne collent pas au moulage.
Les systèmes de portes peuvent être conçus manuellement ou à l'aide de logiciels automatisés.
Les détails sur la conception du système Gating :https://vietnamcastiron.com/gating-system/
Création de patrons
Comme mentionné, les motifs sont disponibles dans une variété de matériaux différents, notamment le bois, le métal, le plastique et la cire. Les matériaux à motifs en bois et en métal sont couramment utilisés pour le moulage au sable , tandis que la cire est couramment utilisée pour le moulage de précision .
Les motifs ont une complexité différente, selon la taille, la forme et la quantité requise.
Dans le moulage de précision, lorsque chaque modèle de cire est détruit pendant le moulage, un modèle de cire est nécessaire pour chaque moulage et ces modèles de cire sont créés dans le moule. La cire est remplie dans ces moules, et après refroidissement, le moule est séparé et le modèle en cire monobloc est extrait.
Pour le moulage au sable, le motif est normalement fabriqué à partir d'un motif en métal ou en bois. Si une haute précision est requise, elle sera traitée par une machine CNC .
Résumé
Ainsi, VIC a répondu à toutes les questions sur la façon de faire un modèle de coulée dans l'industrie métallurgique et les notes dans le processus de fabrication de modèles.
La finition et la taille de la coulée dépendent beaucoup du modèle de coulée et, par conséquent, déterminent le succès de la qualité du produit coulé. Par conséquent, le modélisme est un métier qui nécessite de l'expérience ainsi qu'un haut niveau d'expertise de travail.
Veuillez suivre la série de blogs sur le casting avec VIC pour mettre à jour vos connaissances sur l'industrie du casting. N'hésitez pas non plus à nous envoyer un e-mail si vous recherchez un fabricant OEM / ODM dans l'industrie du moulage via :[email protected].
Processus de fabrication
- Le processus en 6 étapes du moulage en coquille
- Qu'est-ce que la coulée de métal ? - Définition, types et processus
- Moulage au sable et moulage sous pression :quelles sont les différences ?
- Qu'est-ce que le moulage au sable ?
- Quand choisir le processus de moulage au sable de résine
- Qu'est-ce qu'une Fonderie ?
- Qu'est-ce que le casting CI ?
- Qu'est-ce que le sable de moulage?
- Comprendre le processus de moulage au sable