20 Unité 3 : Mouvement de la machine du centre de fraisage vertical
OBJECTIF
Après avoir terminé cette unité, vous devriez être en mesure de :
- Comprendre le mouvement de la machine du centre de fraisage vertical.
- Comprendre la position d'origine de la machine.
- Comprendre les coordonnées de la machine CNC.
- Comprendre le système de coordonnées de travail.
- Comprendre les décalages de la machine et de l'outil.
- Définissez le décalage de longueur d'outil pour chaque outil.
Mouvement de la machine VMC
Les machines CNC utilisent un système de coordonnées cartésien 3D. La figure 10. montre un centre de fraisage vertical (VMC) typique. Les pièces à usiner sont fixées sur la table de la machine. Cette table se déplace dans le plan XY. Lorsque l'opérateur fait face à la machine, l'axe X déplace la table de gauche à droite. L'axe Y déplace la table d'avant en arrière. La colonne de la machine saisit et fait tourner l'outil. La colonne contrôle l'axe Z et se déplace de haut en bas.
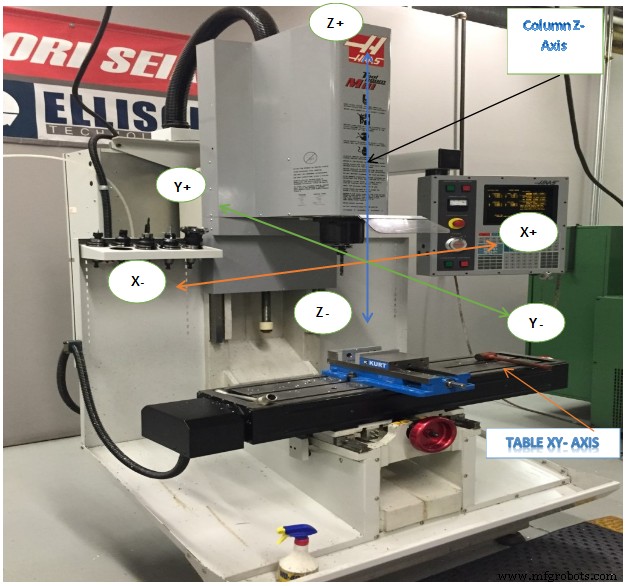
Figure 1. Mouvement de la machine VMC
Coordonnées de la machine CNC
Le système de coordonnées de la machine CNC est illustré à la figure 11. Le point de contrôle du système de coordonnées de la machine est défini comme la face centrale de la broche de la machine. Le point d'origine du système de coordonnées de la machine est appelé Machine Home. Il s'agit de la position de la face centrale de la broche de la machine lorsque l'axe Z est complètement rétracté et que la table est déplacée vers ses limites près du coin arrière gauche.
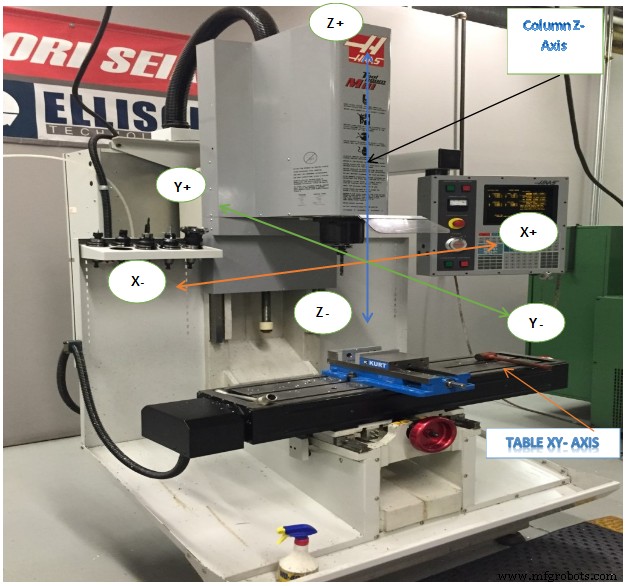
Figure 2. Système de coordonnées de la machine VMC (à la position d'origine )
Comme le montre la figure 12, lorsque vous travaillez avec une CNC, pensez, travaillez et écrivez toujours des programmes CNC en termes de mouvement d'outil, et non de mouvement de table. Par exemple, l'augmentation des valeurs de coordonnées +X déplace l'outil vers la droite par rapport à la table (bien que la table se déplace en fait vers la gauche). De même, l'augmentation des valeurs de coordonnée +Y déplace l'outil vers l'arrière de la machine (la table se déplace vers l'opérateur). L'augmentation des commandes +Z déplace l'outil vers le haut (loin de la table).
À propos de la position d'origine de la machine
Lorsqu'une machine CNC est allumée pour la première fois, elle ne sait pas où sont positionnés les axes dans l'espace de travail. La position d'origine est trouvée par la séquence de redémarrage à la mise sous tension initiée par l'opérateur en appuyant sur un bouton de la commande de la machine après avoir mis la commande sous tension.
La séquence Power On Restart entraîne simplement les trois axes lentement vers leurs limites extrêmes (-X, +Y, +Z). Lorsque chaque axe atteint sa limite mécanique, un micro-interrupteur est activé. Cela signale à la commande que la position d'origine de cet axe est atteinte. Une fois que les trois axes ont cessé de bouger, la machine est dite « homée ». Les coordonnées de la machine sont ensuite en relation avec cette position d'origine.
Système de coordonnées de travail
Évidemment, il serait difficile d'écrire un programme CNC en relation avec les coordonnées de la machine. La position d'origine est éloignée de la table, de sorte que les valeurs du programme CNC seraient importantes et n'auraient pas de relation facilement reconnaissable avec le modèle de pièce. Pour faciliter la programmation et la configuration de la CNC, un système de coordonnées de travail (WCS) est établi pour chaque programme CNC.
Le WCS est un point sélectionné par le programmeur CNC sur la pièce, le brut ou le montage. Bien que le WCS puisse être identique à l'origine de la pièce en CAO, ce n'est pas obligatoire. Bien qu'il puisse être situé n'importe où dans l'enveloppe de la machine, sa sélection nécessite une attention particulière.
- L'emplacement du WCS doit pouvoir être trouvé par des moyens mécaniques tels qu'un détecteur de bord, un indicateur coaxial ou une sonde de pièce.
- Il doit être localisé avec une grande précision :généralement plus ou moins 0,001 pouce ou moins.
- Il doit être répétable :les pièces doivent être placées exactement dans la même position à chaque fois.
- Il doit tenir compte de la façon dont la pièce sera tournée et déplacée lorsque les différents côtés de la pièce sont usinés.
Par exemple, la figure 13 montre une pièce serrée dans un étau. Les dimensions extérieures de la pièce ont déjà été fraisées sur une machine manuelle avant d'être réglées sur la machine CNC.
La CNC est utilisée pour faire les trous, les poches et la fente dans cette pièce. Le WCS est situé dans le coin supérieur gauche du bloc. Ce coin se trouve facilement à l'aide d'un Edge Finder ou Probe.
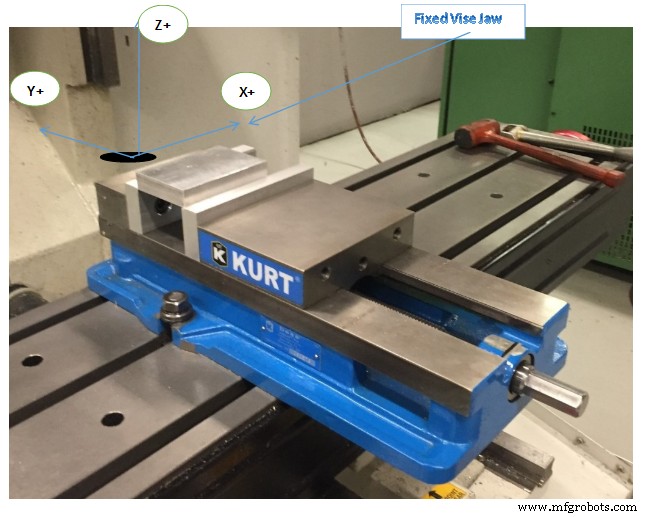
Figure 3. Système de coordonnées de travail (WCS)
Décalages de la machine et de l'outil
Décalages machine :
Parce qu'il est difficile de placer un étau exactement dans la même position sur la machine à chaque fois, la distance entre la maison et le WCS n'est généralement pas connue tant que l'étau n'est pas réglé et aligné avec la machine. Il est préférable de configurer la machine après l'écriture complète du programme, car il est coûteux de laisser une machine CNC inactive en attendant que la programmation CNC soit effectuée. En outre, le programmeur peut changer d'avis au cours du processus CAM, rendant obsolète toute configuration pré-planifiée.
Pour compliquer davantage les choses, différents outils sortent de la broche de la machine de différentes longueurs, également une valeur difficile à déterminer à l'avance. Par exemple, une longue fraise en bout s'étend plus loin de la face de la broche qu'un foret de longueur tronquée. Si l'outil s'use ou se casse et doit être remplacé, il est presque impossible de le régler à la longueur exacte hors du porte-outil à chaque fois.
Par conséquent, il doit exister un moyen de relier le système de coordonnées machine au WCS de la pièce et de prendre en compte les différentes longueurs d'outil. Ceci est fait en utilisant machineTool et Fixture Offsets. Il existe de nombreux décalages disponibles sur les machines CNC. Comprendre leur fonctionnement et les utiliser correctement ensemble est essentiel pour un usinage CNC réussi.
Décalage de pièce XY :
Les décalages de fixation permettent à la commande CNC de connaître la distance entre la position d'origine de la machine et le WCS de la pièce. En conjonction avec les décalages d'outil, les décalages de montage permettent d'écrire des programmes en relation avec le WCS au lieu des coordonnées de la machine. Ils facilitent les réglages car l'emplacement exact de la pièce dans l'enveloppe de la machine n'a pas besoin d'être connu avant l'écriture du programme CNC.
Tant que la pièce est positionnée là où l'outil peut atteindre toutes les opérations d'usinage, elle peut être située n'importe où dans l'enveloppe de la machine. Une fois que les valeurs de décalage du dispositif sont trouvées, entrées dans la commande et activées par le programme CNC, la commande CNC travaille en arrière-plan pour traduire les coordonnées du programme en coordonnées WCS.
Remarquez dans la figure 14 comment les décalages de pièce (+X, -Y) sont utilisés pour déplacer l'axe de la broche de la machine directement sur le WCS.
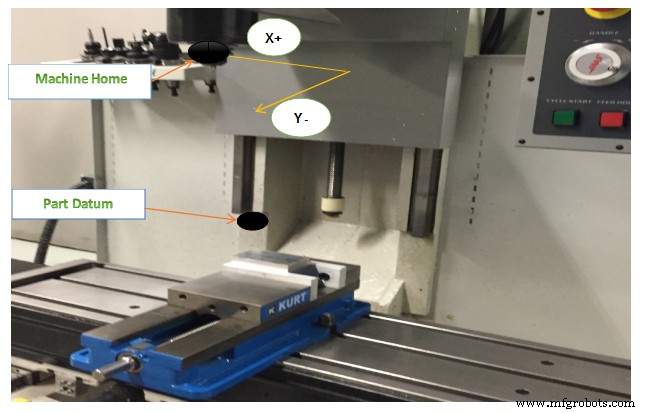
Figure 4 :le décalage de la pièce déplace la machine vers le WCS
Décalage de pièce Z
La valeur Part Offset Z est combinée avec le décalage de longueur d'outil pour indiquer à la machine comment décaler la référence Z de l'origine de la pièce au zéro Z de la pièce, en tenant compte de la longueur de l'outil. Fixture Offset Z peut ou non être utilisé, selon la configuration et le fonctionnement de la machine.
Décalage de longueur d'outil (TLO)
Chaque outil chargé dans la machine a une longueur différente. En fait, si un outil est remplacé en raison de l'usure ou de la casse, la durée de son remplacement changera probablement car il est presque impossible de placer un nouvel outil dans le porte-outil exactement au même endroit que l'ancien. La machine CNC a besoin d'un moyen de savoir jusqu'où chaque outil s'étend de la broche à la pointe. Ceci est accompli en utilisant un décalage de longueur d'outil (TLO).
Dans son utilisation la plus simple, le TLO est trouvé en déplaçant la broche avec l'outil de la position Z d'origine de la machine à la position Z-zéro de la pièce, comme illustré à l'extrême gauche de la Figure 17 ci-dessous. L'outil est piloté manuellement par rapport au point zéro pièce Z et la distance parcourue est mesurée. Cette valeur est entrée dans le registre TLO pour cet outil. Les problèmes avec cette méthode incluent la nécessité de fraiser la pièce à la bonne profondeur avant de régler les outils. De plus, si la référence Z est coupée (typique des pièces surfacées en 3D), il est impossible de définir la référence si un outil se brise ou s'use et doit être remplacé. Tous les outils doivent être réinitialisés chaque fois qu'un nouveau travail est configuré. Lorsque cette méthode est utilisée, le Fixture Offset Z n'est pas utilisé, mais mis à zéro.
La méthode montrée au centre est bien meilleure et utilisée dans ce livre. Tous les outils sont réglés sur une position Z connue, comme le haut d'un bloc de précision 1-2-3 reposant sur la table de la machine. Cela facilite la réinitialisation des outils s'ils sont usés ou cassés.
Une sonde d'outil est très similaire à la méthode de bloc 1-2-3, sauf que la machine utilise un cycle spécial pour trouver automatiquement le TLO. Il le fait en abaissant lentement l'outil jusqu'à ce que la pointe touche la sonde, puis met à jour le registre TLO. Cette méthode est rapide, sûre et précise mais nécessite que la machine soit équipée d'un palpeur d'outil. De plus, les sondes d'outil sont chères, il faut donc veiller à ne jamais planter l'outil dans la sonde.
Les 2e et 3e méthodes exigent également que la distance entre la position de réglage de l'outil (le haut du bloc 1-2-3 ou du palpeur d'outil) et la référence de la pièce soit trouvée et entrée dans le décalage de fixation Z. La machine ajoute les deux valeurs ensemble pour déterminer la correction totale de la longueur d'outil. Une méthode pour ce faire est incluse dans.
3 façons de définir le décalage de longueur d'outil
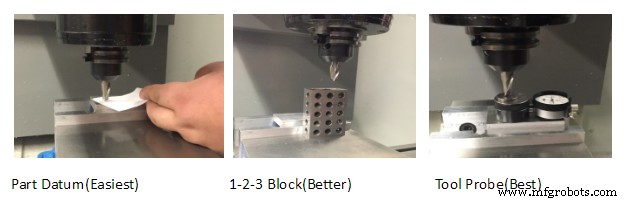
Figure 5. Façons de définir le TLO
TEST UNITAIRE
1. Expliquez la position initiale de la machine.
2. Sur le centre de fraisage vertical (VMC), l'axe X déplace la table dans quelle direction.
3. Sur le centre de fraisage vertical (VMC), l'axe Y déplace la table dans quelle direction.
4. Sur le centre de fraisage vertical (VMC), l'axe Z déplace la table dans quelle direction.
5. Veuillez énumérer 3 façons de définir les décalages de longueur d'outil.
Technologie industrielle
- Fonctionnalités du centre d'usinage vertical pour améliorer la productivité
- Les principales raisons d'acheter un centre d'usinage vertical
- Définition, processus et types de fraiseuses
- Caractéristiques du centre de tournage vertical déplacement, broche inversée
- Le centre de tournage vertical ajoute une capacité de taillage d'engrenages
- Centre de tournage vertical à quatre axes pour la production d'arbres
- 1 Fraiseuses
- 22 Unité 5 :Opération CNC
- Fraiseuse verticale CNC