Robot Company crée un logiciel adapté à l'industrie 4.0
FANUC a concrétisé l'une des promesses de l'Industrie 4.0, celle de la maintenance prédictive des équipements d'usine, avec sa solution Zero Down Time IoT. ZDT peut être appliqué à n'importe quel bras robotique FANUC et à leurs périphériques.
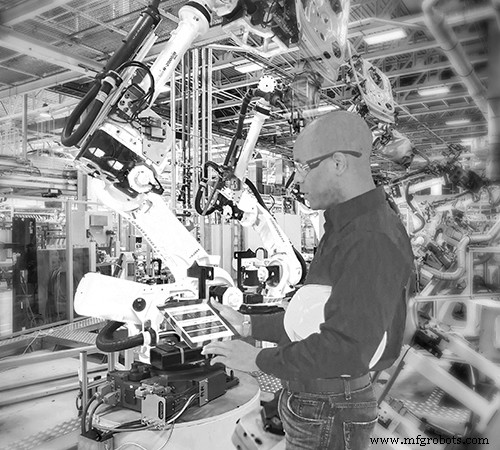
Pour faciliter le reste de l'automatisation dans une usine, plus tard cette année, la société de robotique mettra à disposition le système Intelligent Edge Link and Drive (FIELD) de FANUC, une plate-forme gratuite et open source que les développeurs tiers pourront utiliser pour écrire des applications qui collectera et analysera les données d'autres équipements automatisés.
Fabrication intelligente s'est entretenu avec Joe Gazzarato, directeur technique de ZDT chez FANUC America, pour en savoir plus.
Joe, qu'est-ce que ZDT ?
"ZDT" signifie "Zero Down Time". Avec des fabricants qui fonctionnent constamment maintenant, 24/7/365, essayant de répondre à la demande, tout temps d'arrêt inattendu peut leur coûter la production. Avec ZDT, nous surveillons la santé mécanique, du système et des processus de nos robots pour éliminer les temps d'arrêt imprévus.
Nous avons plus de 21 000 robots connectés à ZDT sur plus de 100 sites clients dans 16 pays différents.
Nous surveillons ces robots et si un problème est prédit par nos analyses, notre système ZDT informera le client et notre équipe de service afin que nous puissions résoudre le problème avant qu'un temps d'arrêt inattendu ne se produise. Nous avons déjà permis à nos clients d'économiser plus de 85 millions de dollars en identifiant les problèmes qui, selon nous, auraient entraîné des temps d'arrêt inattendus.
Comment avez-vous accompli cela ?
Nous travaillons sur ZDT depuis un peu plus de quatre ans maintenant. Nous avons commencé avec seulement 500 robots, avec 50 robots sur chacun des 10 emplacements.
Nous avons créé un logiciel pour nos robots qui produit des messages contenant des données importantes. Ces robots envoient leurs messages à un collecteur de données qui se trouve à l'intérieur de l'usine du client. Les données ZDT
Le travail du collecteur consiste à crypter et à envoyer les messages sortants vers notre centre de données dans le cloud où ils sont stockés et automatiquement analysés à l'aide de programmes qui ont été écrits par nos ingénieurs.
Si l'une des analyses détermine qu'il y a un problème, des e-mails sont envoyés au client et à notre équipe de service et l'un de nos techniciens de service appelle le client pour s'assurer qu'il comprend ce que signifie l'alerte, comment la confirmer et comment y remédier. De plus, si le client a besoin d'aide, le technicien peut faire en sorte que des pièces ou une assistance soient envoyées sur le site afin que nous puissions résoudre le problème avant qu'un temps d'arrêt ne se produise.
Quelles technologies spécifiques rendent ZDT possible ?
Le collecteur de données ZDT a des exigences de bande passante très faibles. Certaines autres implémentations autour du Big Data diffuseront des données en continu à un rythme de quelques millisecondes. ZDT n'est pas conçu comme ça. Nous collectons moins de 500 mégaoctets de données du robot en un an. De plus, le collecteur de données peut fonctionner sur un petit ordinateur. Il ne nécessite pas beaucoup de ressources informatiques.
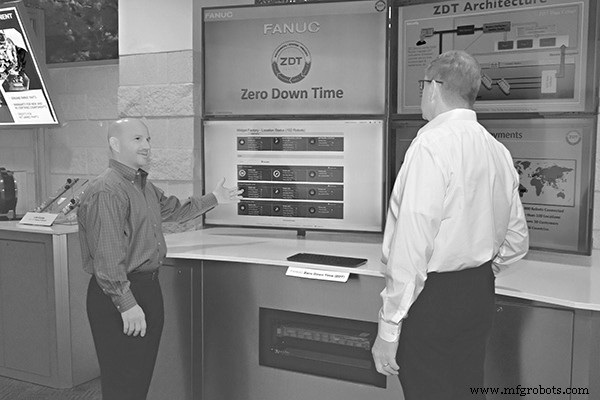
Une autre clé est notre infrastructure cloud. Les outils que nous utilisons pour ingérer et stocker les données à des fins d'analyse sont vraiment importants. Nous nous assurons que les données sont organisées de manière à ce qu'elles soient sécurisées lorsqu'elles sont stockées et efficaces pour une utilisation par nos programmes d'analyse.
Nos analyses sont probablement l'une des parties les plus importantes de ZDT et la clé de notre succès jusqu'à présent. Ils sont écrits par les mêmes ingénieurs qui développent notre logiciel de contrôleur de robot. Les ingénieurs FANUC avec des années d'expérience en robotique ont écrit les programmes analytiques qui examinent les données que nous avons collectées. Leur expertise dans l'écriture de logiciels robotiques les a aidés à devenir très doués pour écrire les analyses à partir des données produites par nos robots.
Existe-t-il d'autres utilisations des données que vous collectez dans le cadre du processus ZDT ?
ZDT fait aussi beaucoup d'autres choses. Nous avons créé de nombreuses fonctions pour aider les clients à augmenter leur productivité, à optimiser leurs ressources de maintenance, à réduire leurs efforts d'assistance et à prolonger la durée de vie de leurs robots.
Un bon exemple est notre analyse de changement de processus. Une expérience commune pour beaucoup d'entre nous qui ont travaillé avec des équipements d'automatisation est de se présenter sur le chantier et de constater que votre système ne fonctionne pas ou qu'il fait quelque chose de différent de ce qu'il faisait la veille. Et vous demandez autour de vous et obtenez la même réponse. "Je n'y ai pas touché" ou "Personne n'a rien changé". Sans ZDT, les gens doivent alors effectuer leur propre analyse pour déterminer ce qui a changé.
Avec ZDT, nos clients savent avec certitude si l'un de leurs robots a été modifié, car nous enregistrons chaque jour toutes sortes de données provenant des robots. Lorsqu'un robot est modifié, ils sauront exactement quel programme ou paramètre a été modifié, ainsi que la date et l'heure auxquelles cela s'est produit, afin qu'ils puissent probablement déterminer qui a effectué le changement, et ils connaissent également la valeur d'origine. Tout cela permet au client de remettre très facilement les choses très rapidement.
Mes données sont-elles sécurisées ?
Le collecteur de données ZDT, qui peut être bloqué par le pare-feu du client, crypte les données lorsqu'elles sont envoyées à notre centre de données, et il s'agit d'un service sortant uniquement.
Pensez également à ZDT en lecture seule. Nous ne pouvons voir que les informations collectées par les robots. Nous ne pouvons rien changer.
Lorsque FANUC affirme que les utilisateurs de ZDT peuvent accéder aux informations de diagnostic dans toute l'entreprise, cela fait-il référence aux robots et non aux autres équipements de l'usine ?
Généralement, mais nous avons en fait conçu ZDT pour que les clients puissent suivre certains de leurs équipements périphériques.
Disons que l'ensemble de vêtements d'un robot comprend des conduites d'air externes et des câbles électriques qui transportent l'alimentation jusqu'à l'extrémité de l'outillage du bras. Vous pouvez associer l'usure de l'emballage de la robe aux données du robot. Par exemple, après que le robot s'est déplacé de tant de milliers de degrés ou s'est tordu le poignet tant de milliers de fois, ZDT peut informer le client que la condition a été remplie et il peut envoyer quelqu'un pour inspecter l'emballage de la robe.
Sans ZDT, vous pouvez effectuer une maintenance périodique, mais avec ZDT, vous l'inspecterez en fonction de l'utilisation du robot. Ainsi, les clients optimisent l'utilisation de leurs ressources de maintenance et effectuent la maintenance quand c'est nécessaire et pas seulement en raison du temps calendaire qui s'est écoulé.
De plus, bien que ZDT ne collecte pas de données provenant d'autres équipements, FANUC se prépare à publier plus tard cette année une technologie conçue précisément pour cela.
Comment décririez-vous le système FIELD ?
FIELD est une plateforme que nous lançons aux États-Unis cette année. Il est conçu pour collecter des données à partir de n'importe quel composant activé par le réseau, y compris les robots, les contrôleurs de soudage, les automates programmables et les capteurs, et pas nécessairement les équipements FANUC. Tout appareil connecté au réseau dans une installation peut partager ses données avec le système FIELD, qui fonctionnera en interne dans l'usine.
FANUC met à disposition des kits de développement de logiciels afin que des tiers puissent écrire des applications qui accèdent à ces données et faire des choses qui apportent de la valeur au client. ZDT est un exemple de la valeur que FANUC fournit grâce à l'utilisation de ce type de données, mais nous pensons qu'il existe des millions de possibilités pour ce que les gens peuvent faire avec les données des équipements de fabrication. Le système FIELD est conçu pour permettre à d'autres entreprises de développer leurs propres applications et de les vendre aux fabricants.
Deux serveurs différents sont disponibles pour le système FIELD. L'un, le FIELD Base Pro, peut connecter jusqu'à 30 appareils. Nous prenons également en charge un serveur informatique unifié de Cisco qui peut prendre en charge jusqu'à 150 connexions d'appareils. Ils peuvent être regroupés afin que les informations puissent être partagées entre les serveurs.
Il existe de nombreuses plates-formes IoT différentes, mais le système FIELD de FANUC est unique pour plusieurs avantages qu'il offre.
- Il fonctionne à l'intérieur de l'usine. D'autres fonctionnent dans le cloud, comme le fait ZDT. Étant donné que les applications FIELD fonctionneront à l'intérieur de l'usine, les applications peuvent être beaucoup plus réactives. Ils obtiennent leurs données en temps quasi réel et peuvent les analyser et prendre des décisions très rapidement. Ils ne dépendent pas non plus d'une connexion Internet.
- FANUC a rendu la plate-forme FIELD entièrement ouverte. Il y aura une association de partenaires du système FIELD où les personnes qui souhaitent écrire des applications ou intégrer le système FIELD dans leurs systèmes ou avec leurs appareils pourront le faire. Être membre est gratuit.
- Le système peut se connecter à n'importe quel appareil compatible réseau. De nombreuses autres plates-formes existantes ne prennent en charge que très peu de protocoles ou quelques protocoles standard, mais FANUC inclut également la possibilité pour les fabricants d'appareils d'écrire leur propre protocole. Donc, s'il n'y a pas de pilote existant pour connecter votre appareil au système FIELD, vous pouvez en créer un. Et ce kit de développement est disponible gratuitement pour les fabricants d'appareils.
L'idée est de créer cette communauté d'appareils et de développeurs d'applications pour développer les capacités de fabrication.
Système de contrôle d'automatisation
- Solutions logicielles pour l'industrie 4.0 :qui sait mieux que les utilisateurs ?
- GE va lancer une société IIoT de 1,2 milliard de dollars
- Sepro lance des applications pour améliorer le logiciel de robot
- Collaborative Robot Marketplace ajoute un logiciel de surveillance
- L'essor du robot :investir dans l'automatisation disruptive
- Le logiciel B&R utilise mieux le potentiel des robots
- Mitsubishi Electric va acquérir la société américaine de logiciels Iconics
- Le logiciel IHM moderne propulse l'industrie 4.0
- Epson crée un robot autonome à deux bras pour la fabrication de haute technologie