Piloter l'usine numérique avec des données MES en temps réel
Avec la poussée vers une usine entièrement numérique, les logiciels de systèmes d'exécution de fabrication (MES) n'ont jamais été aussi essentiels pour les fabricants de tous bords. En utilisant les dernières solutions de systèmes d'exécution de fabrication à réponse rapide dans les opérations de fabrication, les constructeurs peuvent obtenir des mises à jour rapides sur les données opérationnelles urgentes qui peuvent aider à améliorer les processus d'usine et rapprocher l'usine numérique de la réalité.
Au fur et à mesure que la convergence des systèmes logiciels de fabrication et d'entreprise progresse, de plus en plus de fabricants réalisent les gains qu'offre une usine numérique, avec des performances de données en temps réel ou en temps quasi réel offrant beaucoup plus d'informations sur la fabrication que celles dont ils disposaient dans le passé. passé. Les fabricants prennent de plus en plus au sérieux la mise en œuvre de l'infrastructure nécessaire aux solutions de fabrication intelligentes et à l'Internet industriel des objets (IIoT), et le plus souvent, les systèmes MES basés sur le cloud sont au cœur de ces technologies.
« La tendance est à la convergence des systèmes d'entreprise pour obtenir une analyse approfondie du fonctionnement des équipements et des systèmes. Nous voyons des fournisseurs de données unir leurs forces », a déclaré Pete Tecos, vice-président exécutif de 5ME (Cincinnati), notant le récent partenariat de 5ME avec SmartWare qui associe les solutions Freedom Smart Manufacturing et les plates-formes Bigfoot CMMS (système de gestion de la maintenance informatisée) de Smartware. "Plus nous collectons des données et les partageons rapidement entre différents systèmes, plus nous avons une meilleure vue sur les opérations globales."
L'impact du cloud
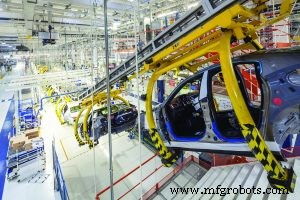
Alors que de plus en plus d'entreprises commencent à adopter la technologie de fabrication basée sur le cloud, les capacités des solutions MES, de la gestion des ressources d'entreprise (ERP) et des systèmes de collecte de données en atelier se fondent de manière plus transparente, travaillant de concert pour rendre les efforts de l'IIoT et de l'industrie 4.0 plus efficaces sur le magasin sol.
"Il permet la poursuite du" Saint Graal de la fabrication ":une analyse système complète en temps réel grâce au partage de données", a déclaré Tecos. "Les ajustements et/ou les corrections sont effectués plus rapidement et perturbent moins les opérations de fabrication."
Les solutions logicielles de fabrication d'aujourd'hui offrent une multitude d'outils pour suivre les mesures clés de l'usine, y compris l'efficacité globale de l'équipement (OEE) et bien d'autres, pour l'entreprise de fabrication, et ces systèmes enrichis s'intègrent bien alors que les développeurs de ces solutions s'associent pour répondre aux demandes. de l'IoT/IIoT.
« Fondamentalement, vous commencez au niveau de l'usine en interface avec les actifs et une variété de systèmes de fabrication, puis fournissez une couche de visualisation [OEE cockpit] pour afficher les performances et les KPI », a déclaré Tecos. « Enfin, poussez les informations en temps réel vers l'amont dans l'espace des systèmes d'entreprise [ERP, MES, GMAO, systèmes qualité]. Si tous ces systèmes fonctionnent en symbiose plutôt qu'en silos, vous pouvez orienter les opérations vers une fabrication adaptative hautement efficace grâce à l'échange d'intelligence opérationnelle en temps réel - c'est le Saint Graal."
La compatibilité avec d'autres plates-formes est essentielle, a ajouté Tecos. « La facilité d'utilisation, les capacités de collecte de données et la polyvalence avec les types de machines sont également importantes. Notre logiciel présente les données sous plusieurs angles et les classe en trois catégories :fréquence, durée et monétisation. Nous examinons les corrélations entre celles-ci, en prenant essentiellement les données de fréquence et de durée pour créer une vue monétisée
des opérations."
Les résultats de certains clients 5ME sont impressionnants. Après avoir installé les systèmes eLog de 5ME, l'usine Caterpillar d'East Peoria, dans l'Illinois, a réduit de moitié la durée moyenne des retards et a amélioré les temps de cycle des machines de 30 % sur les machines sur lesquelles Freedom eLog a été installé, ce qui s'est élevé à 1,2 million de dollars. augmentation de la valeur ajoutée. L'entreprise a indiqué qu'elle avait trouvé que les données électroniques "basées sur des faits" étaient bien meilleures, plus précises et moins émotionnelles que le système papier/processus manuel qui était utilisé auparavant.
Prendre la vue d'entreprise
Les systèmes MES ne sont plus des systèmes autonomes, a noté Stephen Brown, vice-président, pratiques de fabrication, Amériques, Siemens PLM Software (Plano, TX). « Le MES fait partie d'une infrastructure informatique d'entreprise interconnectée. La valeur du MES est désormais définie par la manière dont le système MES s'intègre dans la chaîne de valeur globale, à la fois en amont du développement de produits et de l'ingénierie de production, et en aval de l'automatisation », a-t-il déclaré.
« Les clients souhaitent numériser l'intégralité de la chaîne de valeur, de la conception du produit à la planification de la production, l'ingénierie de la production, l'exécution de la production, puis les services. Nous appelons cela l'entreprise numérique », a déclaré Brown. « Plus précisément, nous utilisons l'expression Digital Twin. Nous aidons nos clients à créer un jumeau numérique non seulement du produit, mais également du processus de production, de l'usine et de l'équipement de production. Nos clients utilisent ensuite le jumeau numérique pour simuler complètement le produit et son processus de fabrication avant de s'engager à dépenser de l'argent pour les prototypes, l'outillage et les actifs physiques."
Ces facteurs permettent une innovation rapide, a-t-il noté. « Il ne s'agit pas simplement de gérer les opérations de fabrication. Il s'agit de créer un processus de fabrication flexible, réactif et prévisible, capable de répondre aux nouvelles exigences des produits."
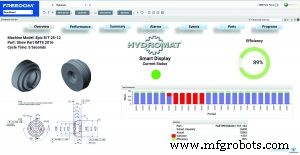
Une fois en production, et lorsqu'ils sont liés à l'automatisation, les clients de Siemens peuvent prendre des décisions en utilisant les données en temps réel de l'atelier, a déclaré Brown. "Les exemples incluent la disponibilité ou le temps de fonctionnement en temps réel de la machine qui peut être utilisé par le logiciel de planification de la production pour optimiser les horaires, et les problèmes de qualité identifiés pendant la production qui peuvent être communiqués en temps quasi réel à l'ingénierie pour la disposition des pièces, ce qui est particulièrement important dans aérospatiale », a déclaré Brown. "Enfin, ajoutez une couche d'IoT et d'analyse de données avec Mindsphere, et nous fermons la boucle dans l'entreprise numérique.
Siemens gère le processus d'innovation et de changement avec son Teamcenter PLM, créant un jumeau numérique du produit et du processus de fabrication, a déclaré Brown. "Nous intégrons ensuite notre portefeuille MOM [manufacturing operations management], en envoyant les données nécessaires sur le produit, la fabrication et la qualité à l'atelier, puis utilisons Mindsphere pour l'IoT et l'analyse de données volumineuses pour capturer les données telles que construites, en retournant des informations sur le produit. et la conception de processus pour une amélioration continue.”
Accélération pour l'IIoT
Les fabricants cherchent davantage à tirer parti du Big Data et du boom de l'IoT/IIoT ainsi que de la mobilité dans le cloud, a déclaré Eric Green, vice-président de Dassault Systèmes-Delmia. "Tout cela affecte les fabricants aujourd'hui, mais jusqu'à ce qu'il y ait une analyse de rentabilisation définitive, ils en sont encore à un stade exploratoire", a-t-il déclaré.
«Avec certaines des technologies spécifiquement autour de l'IIoT et de l'IoT, ils découvrent et comprennent encore quelles sont les opportunités. Si vous pensez à l'IIoT, les fabricants font le précurseur depuis de nombreuses années », a noté Green. « L'IIoT propose une nouvelle génération, une nouvelle évolution. Mais nous avons des clients qui ont des équipements qui ont plus de 20 ans, et ces nouvelles technologies doivent être en mesure de soutenir les investissements dans les équipements existants."
La clé pour les fabricants sera de trouver où et comment ils peuvent appliquer l'innovation, a-t-il ajouté. "En tant que consommateurs, chacun de nous crée une expérience, avec les automobiles que nous conduisons, les smartphones et les appareils intelligents que nous avons. Cela a un effet sur la façon dont les entreprises accèdent au marché. Cela oblige ces fabricants à être plus efficaces ou à être plus innovants."
Pour des développeurs comme Dassault, l'objectif est de commercialiser rapidement et efficacement de nouveaux produits passionnants, a-t-il noté. "Si vous envisagez de mettre de nouveaux produits sur le marché, de la conception du produit à la fabrication et au consommateur, la plate-forme d'innovation nécessite de pouvoir collaborer rapidement pour mettre la conception sur le marché." Cela va au-delà de l'ERP, a-t-il ajouté, pour devenir une plate-forme d'innovation commerciale. Des applications telles que MOM, la gestion des opérations de fabrication, qui accompagnent le produit de la conception à la fabrication via une approche collaborative basée sur un modèle, peuvent accélérer la livraison des lancements de produits.
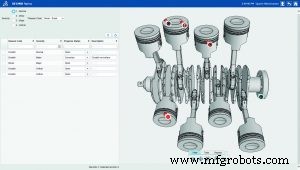
"Pour nous, en tant qu'organisation, nous considérons cela comme une priorité clé", a déclaré Green. « MOM est un ensemble de fonctionnalités plus large que MES, impliquant plusieurs sites, un ensemble et une portée plus larges et un contrôle des stocks plus large. Ce que vous voyez, c'est que différentes organisations ont élargi leur champ d'action pour inclure MOM, et cela est lié à l'innovation que nous proposons."
Donner à l'utilisateur une capacité en temps quasi réel est un avantage clé. "La valeur est là parce que nous avons une visibilité globale, s'il y a des changements, ces changements peuvent être propagés et les erreurs sont éliminées."
Le logiciel Delmia-Apriso permet la continuité numérique, de l'ingénierie à tous les aspects de la fabrication, a déclaré Green. "C'est la capacité d'utiliser un monde virtuel pour optimiser différents scénarios, comme la combinaison de modèles", a-t-il déclaré. « En combinant le modèle et la date d'exécution du monde réel avec le monde virtuel de l'ingénierie, nous utilisons la simulation ou l'optimisation pour évaluer l'impact des changements sur la base de données d'usine réelles, avant de déployer les changements dans l'usine. Le logiciel Delmia Apriso aide les utilisateurs à fournir une visibilité et un contrôle des opérations globales afin d'optimiser l'exécution de la production, des stocks et de la qualité."
Le portefeuille Siemens MOM comprend le MES, la qualité, la planification avancée et l'intelligence de fabrication. "Avec ces applications sont associées des solutions de conception et de simulation d'usines de fabrication, notre portefeuille Tecnomatix, puis bien sûr l'IoT et l'analyse de données avec Mindsphere", a ajouté Brown. « Nous prenons la nomenclature d'ingénierie et la transformons en nomenclature de fabrication, puis en nomenclature de processus. C'est là que MES prend le relais.
"Nous créons des instructions de travail pour chaque étape, y compris les étapes de qualité et d'inspection, et pouvons ensuite envoyer ces instructions à l'opérateur lorsqu'une pièce spécifique est présentée à l'opérateur au poste de travail", a déclaré Brown. Ou nous pouvons envoyer un code spécifique à une cellule de travail robotique en fonction de la pièce présentée à cette cellule de travail. Dans le monde de la personnalisation de masse, où la taille des lots se rapproche de l'unité, nous sommes en mesure d'atteindre des temps de cycle et des coûts historiquement observés uniquement avec une automatisation stricte et de très grandes séries."
Siemens a également ajouté une nouvelle application Automation Gateway pour le Simatic IT MES UAF 2.1 qui offre une connectivité OPC et une connectivité directe aux contrôleurs Siemens S7, a déclaré Brown. L'application configure les objets de nœud d'automatisation composés de propriétés connectées aux balises du système d'automatisation. "Automation Gateway comprend un service maintenant la connexion avec les systèmes d'automatisation, synchronisant les données d'automatisation", a-t-il déclaré. "Les données d'automatisation sont exposées à la commande de l'application UA pour la lecture et l'écriture, et l'application peut s'abonner aux événements de modification des données d'automatisation via la gestion des signaux."
Plus d'analyses de machines
À mesure que la demande d'analyse augmente, de plus en plus de choix abondent, comme les nouvelles solutions d'analyse de machines que Rockwell Automation (Milwaukee) a annoncées l'automne dernier lors de son Rockwell Automation Fair. Ces systèmes comprenaient FactoryTalk Analytics for Devices de Rockwell et une application basée sur le cloud FactoryTalk for Machines pour les constructeurs d'équipements, ainsi que des analyses de système et d'entreprise.
L'analyse complète les systèmes MES et ERP et aide les fabricants à exploiter les données en plein essor provenant des capteurs connectés via l'IIoT. "Les gens continuent de parler d'Industrie 4.0 et de fabrication intelligente", a déclaré Todd Montpas, directeur commercial, Logiciels d'information, Rockwell Automation. "Ce qui les intéresse vraiment, c'est de savoir si la technologie a des extensions pour les performances de la machine, et ce qu'ils demandent vraiment, ce sont toutes ces capacités au niveau de l'exécution. Nous devons nous assurer qu'ils ont des processus qui fonctionnent."
De nombreux clients sont intéressés par les systèmes basés sur le cloud, a-t-il ajouté, notant que certains clients majeurs s'intéressent au cloud Azure de Microsoft. "Ce que nous essayons de faire, c'est d'avoir une approche très évolutive, avec une exécution évolutive, mais intégrée dans une stratégie d'analyse évolutive ; en y plaçant un capteur, vous pouvez obtenir des analyses en temps réel que vous effectuez au niveau de la machine et un apprentissage automatique pour prédire les pannes. »
À Hannover Messe, GE Digital (Boston) a dévoilé en avril sa nouvelle solution Plant Applications MES visant à améliorer ses offres pour les industries de fabrication hybrides pour les processus de production hautement automatisés. Cette nouvelle version offre aux clients une nouvelle interface utilisateur, utilisant la conception UX avancée de GE, pour mieux permettre au personnel d'exploitation d'analyser l'efficacité de l'équipement et d'identifier les causes profondes des temps d'arrêt.
"L'une des choses intéressantes que je vois aujourd'hui est que de nombreux clients cherchent à" se préparer "pour l'IoT industriel", a déclaré Matthew Wells, vice-président, Digital Product Management, GE Digital. « Il évolue mais il s'installe dans un concept de cloud hybride. C'est MES avec un Big E [soulignant l'exécution] ; ils veulent que cela continue de fonctionner sur place. Ce que l'IdO industriel et le cloud offrent est un moyen de compléter cela."
Les temps de réponse et le besoin d'une fiabilité de plus de 99 % pour les opérations de fabrication ont empêché les fabricants de se précipiter vers le cloud, a noté Wells. « Est-ce qu'une fiabilité de 99 % est suffisante ? De nombreux clients n'accepteront pas ce risque pour leurs usines de fabrication », a-t-il déclaré. "Ce que le cloud offre vraiment, c'est un moyen de plonger plus profondément dans les données. Dans le cloud, vous pouvez stocker l'historique et faire du machine learning. Lorsque vous disposez du cloud, vous pouvez accéder à de grandes quantités de données, ce qui augmente l'efficacité de vos analyses."
L'accès à plusieurs téraoctets de données à tout moment dans le cloud permet aux fabricants de tirer pleinement parti du jumeau numérique, a ajouté Wells, qui est la principale attraction de l'IIoT. "Le Digital Twin est un ensemble d'analyses qui modélise essentiellement le comportement des machines qui fonctionnent constamment en arrière-plan, en ajustant les données", a déclaré Wells. "C'est vraiment là que commence la valeur de l'IdO industriel. C'est un marché émergent qui se développe rapidement."
Système de contrôle d'automatisation
- L'usine numérique :la fabrication intelligente propulse l'industrie 4.0
- L'importance de l'IIoT dans une usine intelligente
- 5 minutes avec PwC sur l'IA et le Big Data dans le secteur manufacturier
- Surmonter les goulots d'étranglement :la puissance de l'analyse dans le secteur manufacturier
- Censornet :assurer l'avenir de l'industrie manufacturière
- GE Digital :transformer la fabrication avec Smart MES
- Relever le défi de la fabrication grâce aux données et à l'IA
- GE Digital :informations opérationnelles avec données et analyses
- L'essor des plateformes numériques dans le secteur manufacturier