Choisir la bonne presse
La technologie de la presse, qu'elle soit mécanique, hydraulique ou servo, joue de nombreux rôles
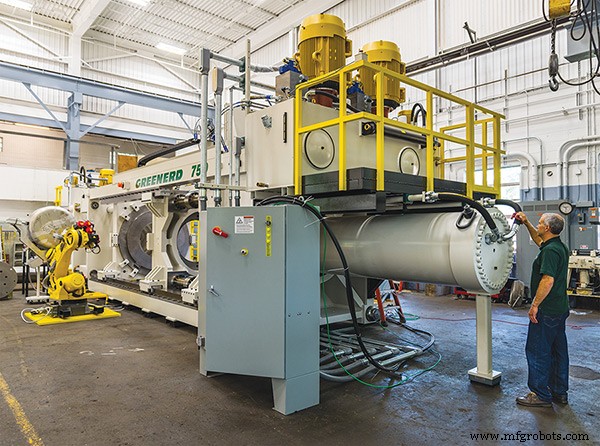
Il y a du choix dans les presses, ce qui est une bonne chose. Le débat n'est pas de savoir lequel est le meilleur, mais lequel convient le mieux pour le travail à accomplir. Il existe des compromis en termes de coût, de fonction et de qualité entre les principaux types de presses que l'on peut choisir.
C'est un débat amical, et les cartes sont sur la table aux yeux de tous.
Examen rapide de la technologie
Selon Stephanie Price, ingénieur d'application senior chez Promess Inc, Brighton, Michigan, de nombreuses personnes dans l'industrie n'apprécient pas pleinement les avantages de la technologie des servopresses. À l'inverse, Mike Josefiak, ingénieur en mécanique chez Greenerd Press &Machine, Nashua, N.H., fait valoir qu'une presse hydraulique est la meilleure solution pour certaines applications. Et Jim Landowski, vice-président de Komatsu America Industries LLC, basé à Chicago, vous dirait qu'il existe encore des situations dans lesquelles une presse mécanique traditionnelle convient.
Une presse mécanique convertit le mouvement de rotation d'un volant d'inertie en mouvement linéaire du vérin pressant contre la pièce. Comme Landowski l'a décrit, vous pouvez « imaginer le cercle, avec zéro en haut et 180 en bas. Une presse mécanique passe de zéro à 180 et revient à zéro, ou 360, en un mouvement continu. Le trait n'a pas de force en haut et une force maximale en bas, donc "selon la matrice, vous pouvez commencer à pousser le matériau à 160 degrés environ. Mais quand il arrive à 180, la pièce est finie, car votre toboggan remonte."
Comme Bob Southwell, vice-président exécutif d'AIDA-America, Corp. Dayton, Ohio, l'a expliqué, la plupart des servopresses sont des versions du même arrangement, "sauf que vous alimentez une transmission mécanique avec un servomoteur, par rapport à un volant d'inertie avec un mécanisme de frein d'embrayage. Une presse mécanique a une course fixe et une vitesse constante. Mais "ajoutez-y un servomoteur, et maintenant vous pouvez programmer le profil de mouvement. Vous pouvez ralentir, faire une pause, effectuer un réamorçage rapide et faire diverses choses qui n'auraient jamais été possibles avec une presse mécanique standard. Il existe également une version à entraînement direct (servomoteur à vis à billes), avec de meilleures caractéristiques de couple que l'hybride servo-mécanique.
Une presse hydraulique combine un ensemble de pompes, de vannes et de tuyaux pour engager le vérin avec un fluide sous pression. Bien que cette approche présente des avantages, elle n'inclut pas le type de contrôle de mouvement décrit ci-dessus. Ainsi, une servo-presse offre des capacités supplémentaires et résout un certain nombre de problèmes qui surviennent avec les presses mécaniques ou hydrauliques pures.
Nouveaux matériaux, nouveaux défis
Landowski a observé que l'évolution vers des alliages avancés provoquée par l'allégement de l'automobile et d'autres facteurs stimule la demande de servo-presses. Comme il l'a dit, "pensez à l'acier comme un liquide, il doit couler... Vous ne travaillez pas le matériau, vous travaillez avec le matériau."
Les matériaux plus durs nécessitent des ajustements précis de la vitesse du bélier afin "de laisser le matériau s'écouler correctement, sinon il devient comme de la tire et commence à se désagréger". Par exemple, a-t-il dit, la formation d'une coupelle dans un alliage dur peut nécessiter un ralentissement de 30 à 15 IPM sur une course de 3" (76,2 mm), à un taux de changement précis et peut-être variable.
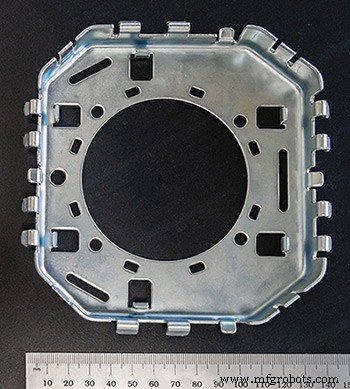
Seul un asservissement pourrait gérer cela, étant donné que les ajustements se font en quelques millisecondes.
Le principal avantage d'un servo, a déclaré Landowski, est la flexibilité de travailler avec différents métaux en composant le flux de matériaux. "C'est pourquoi nous avons des gens qui viennent essayer diverses options. Je peux faire une bonne ou une mauvaise partie simplement en changeant la vitesse de la diapositive. »
Southwell était d'accord et a indiqué que ces défis matériels ont entraîné une part de marché des servopresses d'environ 80 % dans la fabrication automobile nord-américaine. « Les aciers et les aluminiums à haute et ultra-haute résistance sont beaucoup plus difficiles à former que les matériaux d'il y a dix à quinze ans. Et la capacité d'un servo à ajuster le profil de formage s'est avérée extrêmement bénéfique pour la clientèle. »
Josefiak de Greenerd a convenu que la servocommande a un avantage en termes de temps de réponse par rapport à l'hydraulique, dans laquelle la réponse est atténuée, mais a déclaré qu'il n'avait pas «vu de nombreuses applications où ce niveau de contrôle dans le profil de mouvement a un impact matériel sur le fait que vous fassiez ou non un bon produit." Mais il a reconnu que « le réamorçage est un bon exemple d'une fonction d'asservissement uniquement. Aller au fond puis re-frapper en une fraction de seconde n'est pas quelque chose que l'on peut faire avec l'hydraulique."
Si vous n'avez pas besoin de contrôler la vitesse, a expliqué Landowski, vous n'aurez peut-être pas besoin d'un servo.
"Si vous fabriquez des rondelles, par exemple, ou de petits rivets ou quelque chose comme ça, vous n'allez pas ralentir la presse, vous n'allez pas contrôler la vitesse. Vous voulez fabriquer autant de pièces que possible, aussi vite que possible. C'est là qu'une presse mécanique brille, dit-il. C'est aussi là que les presses hydrauliques sont les moins appropriées.
Polyvalence servo dans l'assemblage
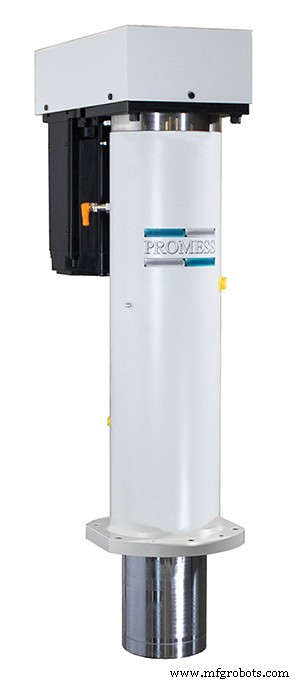
Southwell a ajouté que la capacité d'une servopresse à être facilement reprogrammée pour différentes pièces est un autre facteur de leur succès, même dans le monde automobile à volume élevé.
« La plupart des systèmes de presse sont conçus pour traiter plusieurs types de pièces. Ils utiliseront un outil pendant une heure, le remplaceront et installeront un autre outil. Pratiquement personne ne configure une seule presse et ne fait que la faire fonctionner… Il n'y a aucun moyen qu'ils puissent rester compétitifs. Nous vendons de nombreux systèmes aux équipementiers par le biais des niveaux un et deux pour de grandes familles de différentes pièces ou ensembles de matrices via une seule presse. »
La polyvalence des servopresses va bien au-delà de la programmation simple et s'étend aux opérations d'assemblage délicates, a déclaré Price de Promess.
S'en tenant à un exemple automobile, Price a souligné l'assemblage d'une charnière de porte. Elle a expliqué qu'une servo-presse offre à la fois une haute précision et une boucle de rétroaction inhérente capable de surveiller de près la position et la force. Ainsi, en pressant la charnière ensemble, Promess est également capable d'évaluer la résistance résultante dans le joint, de sorte qu'ils peuvent s'assurer que la porte ne s'ouvre pas trop facilement ni n'est trop rigide pour être inconfortable pour le propriétaire de la voiture.
Cette capacité à activer une pièce mobile et à mesurer les forces en temps réel offre également la possibilité de desserrer les tolérances des pièces, réduisant ainsi les coûts des composants. Comme Price l'a expliqué, sans rétroaction lors de l'assemblage, les ingénieurs sont souvent obligés de concevoir et de fabriquer selon des tolérances très strictes afin de s'assurer que les pièces s'emboîtent correctement.
« Ils utilisent le fait que la presse est allée à une certaine profondeur et, sur la base de leurs tolérances serrées, supposent que la pièce a été assemblée correctement. Ils n'ont aucune analyse de signature pour vérifier cela."
Avec une servo-presse, ils pourraient plutôt assouplir les tolérances et regarder les données pendant le processus d'assemblage pour déterminer que ce qu'ils ont pressé ensemble est réellement correctement installé. Price a déclaré que les capacités de détection intégrées de leurs servopresses ont permis de réduire le taux de rebut jusqu'à 50 % dans certains cas.
Price a également souligné que si une application nécessitait une détection supplémentaire (au-delà du retour du servomoteur), il est facile de l'intégrer à leurs systèmes.
« Nous avons des clients qui utilisent neuf à dix transducteurs de pression différents, ou des transducteurs de position, ou des cellules de charge externes. Nous pouvons recueillir toutes ces informations pour comprendre ce qui se passe dans le processus », a-t-il déclaré. « Et nous pouvons réagir à cela pendant le processus. Et comme tout est électrique, c'est très simple à mettre en place. Branchez simplement un transducteur dans un conditionneur de signal numérique. Le contrôleur peut alors capter ce signal et l'utiliser pour prendre une décision. »
Presses, contrôle et compromis
Les presses hydrauliques ne sont pas aveugles dans ce domaine. Josefiak a déclaré qu'il existe des contrôleurs de mouvement dédiés aux systèmes hydrauliques avec «des temps de balayage extrêmement rapides qui examinent la pression de chaque côté d'un actionneur hydraulique. Et puis, en utilisant des transducteurs de pression à action rapide, nous pouvons montrer la force réelle appliquée au travail. Un tel système met à jour la mesure de la force en moins d'une milliseconde. À son avis, les applications nécessitant une mesure de force plus rapide sont "peu nombreuses et espacées".
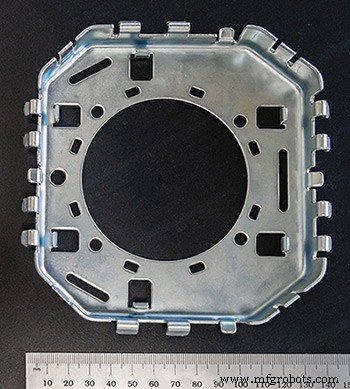
Selon Southwell, les servo-presses sont bien meilleures que les presses hydrauliques pour fabriquer des pièces complexes qui nécessitent une série de matrices. Il y a des années, cela aurait été fait en transférant manuellement les pièces d'une presse à l'autre, a-t-il expliqué. Mais désormais, "la seule façon de rivaliser" est de transférer mécaniquement des pièces d'une étape à l'autre au sein d'une seule presse. Mais "lorsque vous utilisez plusieurs stations pour fabriquer une pièce, vous avez un chargement décentré, ce qui est très préjudiciable à une transmission hydraulique."
Josefiak a répliqué que « le chargement décentré est préjudiciable aux systèmes mécaniques et hydrauliques. Les deux gèrent ces charges excentrées avec une construction et un guidage appropriés de la charpente en acier. Nous avons des systèmes utilisant plusieurs vérins hydrauliques pour permettre un chargement décentré beaucoup plus important qu'une presse servo-mécanique standard. »
Il existe également une certaine controverse concernant les applications nécessitant l'utilisation d'huile de qualité alimentaire comme lubrifiant. Landowski a rapporté que « plusieurs clients sont passés des presses hydrauliques aux presses servomécaniques uniquement en raison du suintement des cylindres et de l'égouttement des lardons sur le matériau. Toutes les pièces doivent être nettoyées après leur formation pour éliminer toute contamination possible. Les clients nous ont également dit que le nettoyage des lubrifiants de qualité alimentaire est moins coûteux que les lubrifiants de qualité non alimentaire en raison des réglementations de la FDA ou de l'EPA."
Josefiak a déclaré avoir satisfait aux normes médicales et de sécurité alimentaire sur un certain nombre de projets "en modifiant l'étanchéité de leurs presses pour utiliser de l'huile de qualité alimentaire à la place des huiles industrielles standard". Alors que Landowski a déclaré que leur servo-presse standard prête à l'emploi ne nécessitait aucune modification, "juste l'huile de qualité alimentaire pour l'entraînement de la presse et le lubrifiant à glissière". Un client « fabrique des bouchons en caoutchouc pour tubes à essai. Chaque coup de presse produit 65 à 75 bouchons en caoutchouc, et des lubrifiants non alimentaires invalideraient ce processus particulier. »
L'hydraulique conquiert l'emboutissage profond
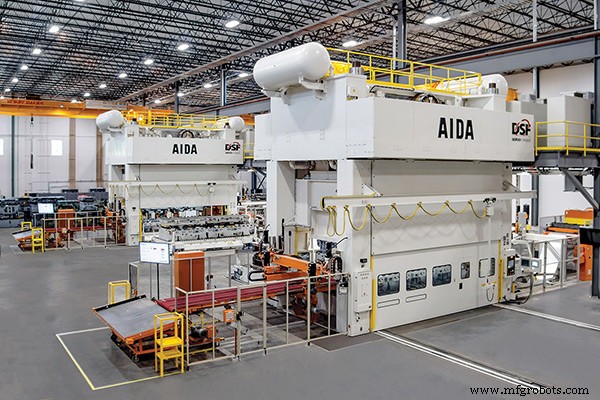
Selon Southwell, "l'avantage d'une presse hydraulique est que vous disposez d'une pleine capacité de tonnage ou de force sur toute la course. Donc, s'il s'agit d'une presse de 200 tonnes et que vous avez une course de douze pouces, vous pouvez appliquer 200 tonnes de pression tout au long de cette course. Avec une servopresse qui a le même train d'entraînement mécanique excentrique que la presse mécanique d'origine, vous avez un engrenage, le vilebrequin ou un arbre central et un entraînement par engrenage central. Il existe une courbe de tonnage ou de couple, et la force que vous pouvez appliquer varie en fonction de l'angle de l'arbre du moteur par rapport au fond. Ce n'est pas le cas des servopresses à entraînement direct comme celles fabriquées par Promess, mais ces systèmes deviennent très coûteux à mesure que le tonnage augmente. Promess culmine à 1 MN (~100 tonnes) dans un seul cylindre, par exemple.
La capacité d'appliquer toute la force sur toute la course rend les presses hydrauliques parfaites pour les applications d'emboutissage profond, et Josefiak est allé jusqu'à dire que c'est "la seule option qui a vraiment du sens".
Un exemple récent qu'il a cité est un projet de production de "réservoirs sous pression relativement grands". Nous avons installé un système automatisé qui charge de grands flans plats dans une presse à emboutissage profond qui a une course de travail de cinq pieds. Le système a plusieurs opérations, a-t-il expliqué. Le premier utilise une presse de 170 tonnes pour dessiner les deux moitiés du réservoir. Ceci est suivi d'une presse à poinçonner automatisée et d'un ébavurage et d'un soudage en aval. La clé ici, a déclaré Josefiak, est qu'un tel coup de travail "n'est pas quelque chose qui se reproduit facilement avec une servo-presse. L'emboutissage profond est donc un domaine où l'hydraulique domine encore. Et c'est dans pas mal d'industries. C'est plus le processus que l'industrie."
Josefiak a déclaré que l'hydraulique "fonctionne également très bien dans des situations avec un temps de cycle très long, où nous pouvons gérer une très faible consommation d'énergie avec une pression constante sur toute la surface du lit et à relativement peu de frais du point de vue du coût en capital". Le moulage par compression en offre un exemple majeur. "Habituellement, le moulage par compression va être une combinaison de temps, de température et de pression formant un matériau en une forme", a expliqué Josefiak. La presse maintiendrait un matériau relativement mince contre une forme de matrice positive ou négative sous pression. « La durée peut être aussi courte que cinq secondes ou aussi longue que deux heures. Et très souvent… nous essayons de maintenir une température de plateau constante dans la zone de travail entre 300 et 700 degrés environ, et nous essayons de contrôler une pression très constante dans la zone de travail. Cela garantit que le matériau formé est uniforme partout. La technique est utilisée pour des éléments tels que les doublures de caisse automobiles (y compris les nouvelles doublures de caisse composites) et les garnitures de toit automobiles fabriquées avec un matériau semblable à un tapis. Un autre exemple qu'il a cité est "le compactage de poudre pour la fabrication de meules en oxyde d'aluminium".
Considérations financières
D'une manière générale, l'investissement en capital pour une servo-presse dépasse celui des presses mécaniques ou hydrauliques traditionnelles. Mais il y a des coûts d'exploitation et des facteurs connexes à prendre en compte qui rendent cette comparaison presque inutile. De plus, toutes les presses d'un type donné ne sont pas égales, même pour les mêmes valeurs de tonnage/couple.
Commençons par la consommation d'énergie. Une presse hydraulique doit maintenir la pression dans les conduites pour déplacer le vérin à la demande, ce qui signifie faire fonctionner les pompes tout au long des cycles. Cela se compare défavorablement à une servo-presse, qui utilise de l'électricité uniquement lorsque le vérin est en mouvement. Selon Landowski, cela permet d'économiser environ "50 % d'énergie avec une servo-presse, en fonction de la taille de la machine". Price s'est référé à une étude de l'Université de Kassel, qui a révélé que la servopresse était efficace à 90 % en termes de conversion d'énergie, contre 57 % pour le système hydraulique comparable. Southwell a déclaré que Honda avait étudié ses propres systèmes et publié la découverte selon laquelle les servopresses permettaient d'économiser 30 % de la consommation d'énergie réelle.
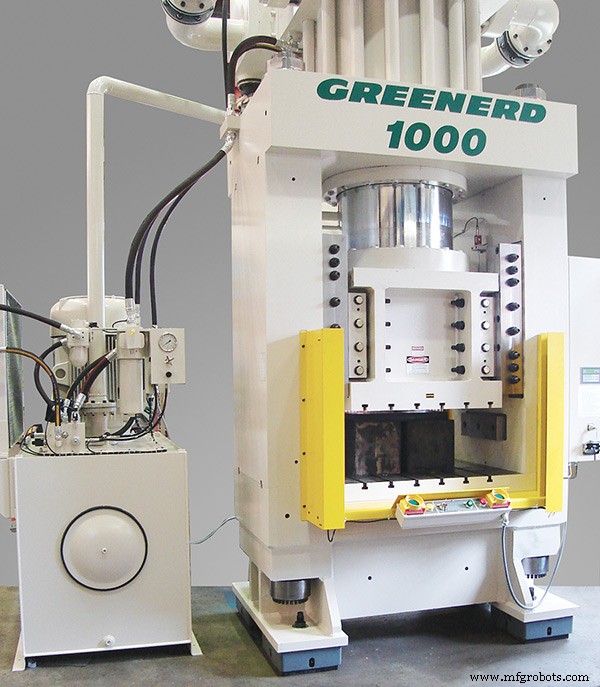
Southwell a également indiqué que certaines presses AIDA utilisent un « système de gestion de l'énergie basé sur des condensateurs à 100 % ». Cela stocke l'énergie de travail requise dans des condensateurs, qui sont rechargés pendant la partie non active de la course. Cela "réduit considérablement la charge de pointe", a-t-il expliqué, par rapport à une presse mécanique ou hydraulique, qui a un "énorme pic lors de leur premier engagement". Le tirage actuel d'AIDA est "assez plat". Ainsi, votre débit de pointe réel peut ne représenter que 20 à 30 % de la charge de pointe des systèmes mécaniques ou hydrauliques. C'est essentiel, car les compagnies d'électricité doivent dimensionner l'électricité qu'elles fournissent au client en fonction de la charge de pointe."
Josefiak a répliqué que dans un environnement de production élevée, il y a peu ou pas de temps d'inactivité, donc "cela n'a vraiment pas trop d'importance" que les pompes hydrauliques fonctionnent en continu. Et "dans les systèmes où nous avons de longs temps d'inactivité de 10 minutes ou plus, nous pouvons installer une commande de moteur de" démarrage progressif "qui arrête le moteur pour économiser l'énergie." Fait intéressant, bien que cette option n'ajoute que 2 à 3 % du coût du système, Josefiak a indiqué qu'il n'y a jamais eu de forte demande pour cela. Il a ajouté que le passage d'une pompe à cylindrée fixe à une pompe à cylindrée variable peut également "réduire considérablement notre consommation d'énergie au ralenti". Mais c'est encore une fois une option qui n'est pas encore devenue la norme aux États-Unis.
Avec toutes ses pompes, vannes, tuyaux et flexibles, la technologie hydraulique est souvent considérée comme plus complexe et plus exigeante en maintenance que les systèmes à servocommande. Price a déclaré que leurs servo-presses ne nécessitent rien de plus que le graissage des vis à billes deux fois par an - et même cela est très prudent. Inversement, maintenez les conduites hydrauliques sous haute pression pendant des mois, cycle après cycle, et tôt ou tard, quelque chose est voué à fuir ou un sous-composant est voué à tomber en panne. Le contre-argument, dit Josefiak, est que « plus personne n'utilise de raccords NPT. Il existe une gamme de joints métal sur métal et de type joint torique, construits avec de meilleurs matériaux, qui ont fait un bien meilleur travail en contrôlant les fuites. De plus, a-t-il ajouté, les composants individuels sont relativement peu coûteux et faciles à réparer, tandis que "réparer un système d'asservissement coûte considérablement plus cher".
Ce dernier point nous amène au sujet du dimensionnement correct des composants pour le travail. Il est vrai que si vous brûlez un servomoteur dans quelques années, vous vous exposez à une grosse facture de réparation. Mais Price a déclaré que leurs systèmes fonctionnaient régulièrement pendant 20 ans sans aucune défaillance de ce type, car ils sont conçus avec un facteur de sécurité de 2,5 ×. Les variateurs sont dimensionnés pour fonctionner dans le courant continu du servomoteur, au lieu du pic, afin que la presse puisse maintenir la pièce indéfiniment sans surchauffe ni panne.
De même, les vis à billes auront une capacité de charge dynamique de 2,5 fois la force nominale de la presse. Par exemple, la vis à billes d'une presse Promess 40 kN a une capacité de charge dynamique de 134 kN et une capacité de charge statique de 320 kN. Price a déclaré qu'un tel système peut fonctionner sans défaillance pendant plus de 22 ans lors de l'exécution d'un travail avec une force moyenne de 30 kN, avec 16 cycles/min sur 14 heures/jour. Comparez cela à seulement 32 semaines pour une vis à billes évaluée à une charge dynamique de 40 kN; même à une puissance nominale de 80 kN, le système durerait moins de cinq ans.
Système de contrôle d'automatisation
- ips pour choisir le bon service de réparation CNC
- Systèmes de soudage robotisés :choisir le bon
- 5 conseils pour choisir le bon système de gestion des commandes
- Choisir les bonnes pinces hydrauliques pour réduire les temps de cycle
- Choisir le bon laser
- Choisir la bonne table plasma CNC
- Choisir le bon équipement pour l'aménagement paysager
- Choisir la bonne assurance pour votre équipement lourd
- Choisir le bon équipement compact pour votre ferme