L'ABS est-il recyclable et également biodégradable ?
La demande d'équipements de protection durables pendant la Seconde Guerre mondiale a déclenché la production de plastiques polymères. À cette époque, l'objectif était de développer des feuilles de plastique copolymère à l'épreuve des balles.
La société Borg-Warner a initialement breveté l'idée du plastique ABS en 1948, mais il a fallu 6 ans de plus pour son introduction commerciale. Leur produit en plastique ABS a été déposé sous le nom de Cycolac. La compagnie de téléphone Bell a d'abord utilisé du plastique ABS pour ses pièces de téléphone domestique.
Aujourd'hui, il existe plus de 6000 qualités de plastique ABS conçues pour plus que les téléphones. Et certains plastiques peuvent être recyclés. Des programmes de recyclage ont été mis en place pour diminuer la pollution de notre air, de notre eau et réduire notre consommation d'énergie. Rejoignez-moi pour tout savoir sur le plastique ABS et s'il s'agit d'un matériau renouvelable pour la prévention des déchets.
Alors, l'ABS est-il recyclable ?
Oui, le plastique ABS est considéré comme "recyclable" puisqu'il s'agit d'un thermoplastique, ce qui signifie que vous pouvez chauffer le plastique et le réutiliser comme filament en l'extrudant.
Cependant, les liaisons moléculaires de l'ABS se décomposent à chaque cycle de chaleur, ce qui le rend moins durable, et pour éviter cela, vous devrez ajouter de l'ABS pur à l'ABS recyclé pour plus de durabilité.
Qu'est-ce que le plastique ABS ?
L'acrylonitrile butadiène styrène est également connu sous le nom d'ABS.
L'ABS est un plastique polymère à base de pétrole qui peut être remodelé à différentes températures. Les polymères thermoplastiques, comme l'ABS, peuvent devenir flexibles ou caoutchouteux lorsqu'ils sont chauffés. Une fois refroidis, ils ont la capacité de se solidifier à nouveau.
L'ABS est classé comme un composé amorphe, ce qui signifie qu'il ne suit pas la tendance de la phase naturelle des autres matériaux commandés. Plus précisément, lorsqu'il atteint une température spécifique, il ne se transforme pas d'un solide à un liquide. En conséquence, il n'a pas de véritable point de fusion. Au lieu de cela, il a une température de transition vitreuse de 105℃.
La température de transition vitreuse est la température à laquelle une substance amorphe passe d'un état rigide à un état caoutchouteux.
L'ABS est appelé un terpolymère car il est composé de 3 polymères différents. Un polymère est un type de matériau composé de grandes sous-unités répétées de molécules.
Les chaînes sont liées par des réactions chimiques appelées polymérisation. Comme vous pouvez le constater d'après son nom complet, les 3 polymères qui composent l'ABS sont l'acrylonitrile, le styrène et le polybutadiène. La structure moléculaire de l'ABS consiste en une longue chaîne de polybutadiène.
De manière entrecroisée, les plus petites chaînes de styrène et d'acrylonitrile sont attachées à la longue chaîne.
La formation moléculaire unique de l'ABS et les propriétés de chaque polymère contribuent à ses caractéristiques globales.
Les groupes de nitrile adjacents dans la chaîne sont attirés les uns vers les autres et augmentent la résistance du plastique. L'acrylonitrile augmente sa rigidité, sa dureté et la température à laquelle le matériau se déforme. De plus, il confère à l'ABS sa résistance à certains produits chimiques et contraintes mécaniques.
Le styrène contribue à la brillance de l'ABS, à son imperméabilité ainsi qu'à sa dureté et sa rigidité.
Le polybutadiène agit principalement pour rendre le matériau plus résistant et malléable. Le pourcentage de chaque composant est généralement de 15 à 30 % d'acrylonite, de 5 à 30 % de butadiène et de 40 à 60 % de styrène.
Mais, les pourcentages de chaque polymère varient selon la qualité du plastique ABS. Cela dépend vraiment de l'objectif de l'application.
Par exemple, si un plastique caoutchouteux et flexible était nécessaire pour les équipements sportifs, les fabricants créeraient un mélange de polymères avec une teneur plus élevée en polybutadiène.
Comment est fabriqué l'ABS ?
Il y a beaucoup de science utilisée dans la fabrication de l'ABS. Au départ, vous devrez isoler les 3 polymères.
L'acrylonitrile peut être fabriqué synthétiquement en combinant du pétrole et de l'ammoniac. Le butadiène étant un hydrocarbure pétrolier, il peut être fabriqué par le procédé pétrochimique de craquage thermique.
Et le styrène est synthétisé par la déshydrogénation d'un composé appelé éthylbenzène. Pour votre information, la déshydrogénation est une réaction chimique qui implique l'élimination d'une molécule d'hydrogène d'un composé.
Maintenant que vous avez les polymères, le plastique ABS peut être fabriqué de 2 manières :polymérisation en émulsion et polymérisation en masse continue.
La polymérisation en émulsion de l'ABS est un processus en plusieurs étapes. L'émulsion consiste à mélanger ensemble 2 liquides non miscibles ou plus.
Tout d'abord, le butadiène et l'eau sont émulsifiés. Un catalyseur est ajouté pour accélérer la réaction et le produit résultant est du latex de caoutchouc. Ensuite, le styrène, l'acrylonitrile et le latex de caoutchouc sont émulsifiés, toujours avec un catalyseur.
Le produit final est un mélange de particules d'ABS dans de l'eau. Une centrifugeuse est ensuite utilisée pour isoler les pastilles d'ABS et elles sont séchées pour extraire l'excès d'eau qui vous donne de l'ABS pur.
Le problème avec la polymérisation en émulsion est qu'il y a de nombreuses étapes. Cela peut entraîner des incohérences entre chaque produit de la séquence. Un autre facteur est les substances ajoutées telles que les catalyseurs et les émulsifiants. Comme les substances se retrouvent dans le produit à la fin du processus, elles sont considérées comme des impuretés.
Ainsi, avec ce produit, vous vous retrouvez avec une résine ABS jaunâtre de mauvaise qualité.
D'autre part, la polymérisation en masse continue est une longue étape et elle n'a pas beaucoup de substances supplémentaires ajoutées.
Vous commencez avec des pastilles de caoutchouc butadiène polymérisé qui sont ensuite décomposées en plus petits morceaux. Ces morceaux sont dissous dans un mélange de styrène et d'acrylonitrile. Plus tard, toute la solution est placée dans un réacteur où le styrène et l'acrylonitrile sont polymérisés.
Pendant la polymérisation, la solution est continuellement mélangée, ce qui décompose les particules en morceaux encore plus petits. Les monomères restants sont isolés et peuvent être recyclés pour recommencer le processus.
La polymérisation en masse continue est une méthode plus efficace pour produire de l'ABS pur car elle permet d'obtenir des plastiques ABS homogènes, de haute qualité et opaques.
À quoi sert l'ABS ?
En plus d'être un matériau utilisé pour la modélisation par dépôt fondu dans l'impression 3D, l'ABS a de nombreuses applications. Les propriétés et le mélange de polymères de l'ABS en font un plastique idéal et polyvalent qui est utilisé dans une variété d'industries.
L'ABS est un plastique léger qui fait partie intégrante de la modernisation de l'industrie automobile. Les constructeurs automobiles abandonnent l'utilisation de métaux lourds pour les matériaux et les pièces. Au lieu du métal, l'ABS est utilisé pour les panneaux, les poignées de porte, les ceintures de sécurité, les tableaux de bord et bien plus encore.
Dans votre maison, je parie que vous pouvez trouver du plastique ABS un peu partout. Il est utilisé dans de nombreux appareils pour les panneaux de commande, les prises murales et dans d'autres appareils comme les aspirateurs, les robots culinaires, les réfrigérateurs et même les meubles et les bagages.
L'ABS est maintenant utilisé dans la plomberie comme substitut du métal dans les tuyaux et les raccords. C'est parce qu'il ne se corrode pas.
Pour l'électronique, les plastiques ABS sont transformés en capuchons pour claviers et boîtiers d'ordinateurs. Nous connaissons tous les jouets LEGO, qui sont en ABS. Et on le trouve dans certains instruments en plastique comme les flûtes à bec, les hautbois, les clarinettes et les pianos.
L'industrie médicale est l'une des utilisations les plus fascinantes du plastique ABS. Il est utilisé pour fabriquer des sutures non résorbables, des tendons artificiels, des attaches pour l'administration de médicaments par des tubes trachéaux, des inhalateurs et des nébuliseurs.
Comment recycler l'ABS
Le plastique ABS s'est vu attribuer le code de résine n° 7, qui correspond à la catégorie des « autres plastiques ». La plupart du temps, l'ABS n'est pas accepté dans les usines de recyclage, mais je suggère de vérifier auprès de votre municipalité au cas où. Certaines entreprises ont développé des programmes de ramassage en bordure de rue pour les plastiques #7.
S'ils sont acceptés dans votre usine locale de récupération de matériaux, ils sont décomposés comme les autres plastiques normaux. L'étape de collecte est réalisée par flottation par mousse.
L'ABS est séparé des autres formes de particules de plastique dans un mélange eau-huile. Ensuite, il est broyé en petits granulés. Les granulés sont ensuite introduits dans des extrudeuses qui peuvent mouler la résine en différentes formes. Les formes peuvent être des feuilles de plastique ABS, des filaments ou la résine peut être directement insérée dans les unités de moulage par injection.
De plus, le matériau imprimé en ABS peut être recyclé et transformé à nouveau en filament à l'aide d'une machine comme le Filastruder.
Le Filastruder peut créer un filament de la couleur et de la taille souhaitées pour votre projet d'impression 3D. Cependant, je recommande de vérifier les tolérances du Filastruder ou de toute machine d'extrusion car elles varient.
Il y a quelques considérations que vous devez prendre en compte lors de l'utilisation de plastique ABS recyclé avec le Filastruder :La taille des pastilles doit être de 5 mm ou moins. Sinon, ils pourraient bloquer ou endommager la machine ou produire un filament non uniforme.
Pour ajouter à cela, si vous avez des impuretés dans les pellets recyclés, vous les aurez dans votre produit fini. Assurez-vous de broyer soigneusement les granulés et d'utiliser le bon équipement pour le travail.
Enfin, parce que vous avez chauffé à plusieurs reprises le plastique ABS, il finira par perdre sa capacité à résister à la chaleur. En effet, les liaisons moléculaires se décomposent à chaque cycle thermique. Pour éviter cela, vous devrez ajouter des granulés ABS purs aux granulés recyclés pour plus de durabilité.
L'ABS est-il un matériau toxique ?
Heureusement, lorsque le plastique ABS est dans sa forme finale, comme les appareils électroménagers ou les jouets, il est considéré comme non toxique.
Il est stable, non lixiviant et jusqu'à présent, ce n'est pas un cancérogène connu. Cependant, il n'a pas été réglementé pour une utilisation dans l'industrie alimentaire ou pour les dispositifs médicaux dans le corps.
Le problème est que l'ABS devient toxique après avoir subi différentes méthodes de traitement. S'il est exposé à des températures extrêmes, le plastique ABS est inflammable. Évidemment, cela provoque un risque d'incendie, mais il y a aussi des fumées toxiques qui sont produites comme le monoxyde de carbone et le cyanure d'hydrogène.
En fait, tout «processus de fusion» subi par le plastique ABS est dangereux car le terpolymère est décomposé en chaque polymère, comme le styrène et l'acrylonitrile. Cela s'applique à l'utilisation de solvants pour lisser les motifs sur des pièces imprimées en 3D.
Troisièmement, ces problèmes constituent des menaces écologiques.
Un autre point est que l'impression 3d provoque la dispersion de la poussière ABS et des particules fines dans l'air. Cela a déjà été connu pour causer des effets néfastes sur la santé. Les particules de poussière sont des irritants pour les yeux, la peau et les poumons.
Enfin, l'ABS subit une dégradation avec l'exposition aux UV, ce qui pourrait entraîner la lixiviation de certains produits chimiques au fil du temps.
L'ABS est-il biodégradable ?
Les matériaux biodégradables sont ceux qui se décomposent par des micro-organismes comme les bactéries et les champignons, et malheureusement, le plastique ABS n'est pas biodégradable.
La plupart finissent dans des décharges car certaines usines de recyclage ne les récupèrent pas. C'est une idée fausse courante que le «plastique biodégradable» peut être recyclé alors que les installations ne les acceptent toujours pas.
Ils affirment que le produit final du compost sera de qualité inférieure ou de mauvaise qualité. Et, il faut en fait très longtemps pour que les matériaux étiquetés comme plastique biodégradable se décomposent naturellement dans l'environnement.
Réflexions finales
Alors, oui le plastique ABS est considéré comme « recyclable », dans le sens où vous pouvez chauffer le plastique et le réutiliser. Outre ses propriétés avantageuses, il présente plusieurs inconvénients. Le plastique ABS se dégrade et se raye facilement.
J'ai expliqué comment les solvants sont utilisés pour lisser les conceptions ABS, mais si vous en utilisez trop, vous risquez de dissoudre les parties essentielles de votre pièce.
De plus, le plastique ABS peut être susceptible de se fissurer si vous utilisez certaines huiles ou graisses comme lubrifiants. Pour l'amélioration, les fabricants ont développé des alliages de plastique ABS avec du polycarbonate. Le polycarbonate augmente encore la résistance, la rigidité et la résistance à la chaleur de l'ABS.
Mais, il existe d'autres alternatives à l'utilisation du plastique ABS pour l'impression 3D qui pourraient vous convenir davantage.
Le plastique PLA ou acide polylactique est une autre option thermoplastique.
Le PLA est un polymère polyester, ce qui signifie qu'il contient des liaisons ester pour relier les chaînes entre elles. C'est un matériau favorable car il est fabriqué à partir de ressources renouvelables telles que les plantes fermentées. C'est un matériau plus solide et plus rigide que l'ABS et il devient flexible à basse température sans se déformer.
L'inconvénient est qu'à des températures modérées, le plastique perd de sa durabilité, ce qui le fait se fissurer facilement.
Le polymère de nylon était en fait le premier polymère thermoplastique créé artificiellement. C'est un polymère polyamide composé de liaisons amide.
En tant que matériau d'impression, il est moins solide et moins rigide que le PLA et l'ABS. Il a une plus grande capacité à résister à la force ou aux chocs que l'ABS et résiste aux produits chimiques.
Cela lui permet d'être utilisé pour des applications plus industrielles. Cependant, il nécessite une température élevée pour l'extrusion. Récemment, les fabricants ont développé des alliages de fibres avec du nylon pour augmenter sa résistance.
À mon avis, lorsqu'il s'agit de votre santé, les plastiques et la chaleur élevée ne font jamais bon ménage. Je vous conseille de bien vous renseigner sur la matière plastique que vous avez choisie pour l'impression.
Il existe toujours des options plus écologiques. Si vous décidez d'utiliser du plastique ABS pour l'impression, essayez d'éviter d'inhaler ces vapeurs et ces particules fines. Je suggère de construire une enceinte autour de votre imprimante. Et, assurez-vous toujours que vous travaillez dans un endroit bien aéré.
Consultez notre section de produits recommandés
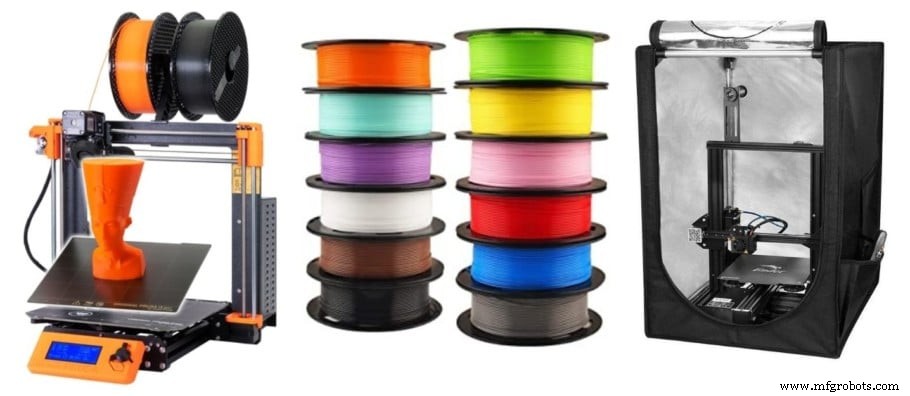
Nous avons créé une section de produits recommandés qui vous permettra d'éliminer les conjectures et de réduire le temps passé à rechercher quelle imprimante, filament ou mises à niveau obtenir, car nous savons que cela peut être une tâche très ardue et qui entraîne généralement beaucoup de confusion. .
Nous avons sélectionné une poignée d'imprimantes 3D que nous considérons comme bonnes pour les débutants comme pour les intermédiaires, et même les experts, facilitant la décision, et les filaments, ainsi que les mises à niveau répertoriées, ont tous été testés par nos soins et soigneusement sélectionnés. , vous savez donc que celui que vous choisirez fonctionnera comme prévu.
impression en 3D
- Soudage et collage de pièces en plastique imprimées en 3D
- Impression 3D avec du plastique ABS :tout ce que vous devez savoir
- Le passé, le présent et l'avenir du recyclage du plastique
- Fabrication de matières plastiques :passé, présent et futur
- Les avantages et les inconvénients du plastique biodégradable
- Types de bavures plastiques et processus d'ébavurage
- Choisir la découpe au jet d'eau pour le caoutchouc et le plastique
- Services de moulage par injection de plastique efficaces et rentables
- Tours à banc incliné et VMC