Conception d'une turbine Tesla imprimée en 3D – Partie 1
Présentation
Bienvenue dans une mini-série en deux parties sur la modernisation d'une turbine Tesla avec des pièces Markforged. Ces blogs sont de l'ingénierie d'application dans sa forme la plus pure; nous utiliserons des techniques définies dans des articles de blog pédagogiques précédents pour concevoir et imprimer cette partie. À la fin, nous aurons, espérons-le, une turbine Tesla fonctionnelle avec des pièces Markforged, capable de tourner à des vitesses extrêmement élevées. Dans le premier article, nous discuterons des bases de la turbine Tesla et de la reproduction Onyx du boîtier de la turbine.
Qu'est-ce qu'une turbine Tesla ?
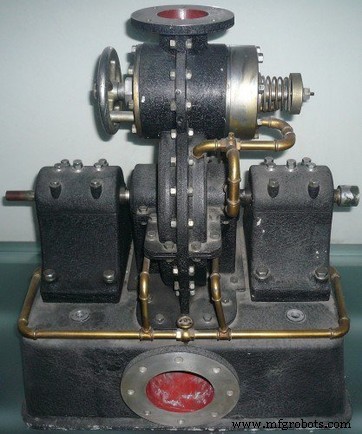
Une turbine Tesla est une turbine à flux centripète sans pale brevetée par Nikola Tesla au début du 20e siècle. Comme ses homologues à turbine à aubes, il convertit les fluides en mouvement en énergie. Cependant, au lieu d'utiliser des lames inclinées pour faire tourner un arbre, il utilise des disques lisses et parallèles. Les fluides pénètrent dans la turbine en se déplaçant de manière tangente aux disques sur le bord extérieur de la turbine, forçant la rotation au moyen de la viscosité et de l'adhérence de la couche de surface. Au fur et à mesure que le fluide ralentit et perd de l'énergie, il spirale vers le centre de la turbine et sort par l'orifice d'échappement. Le GIF ci-dessous montre le mouvement des fluides et le transfert d'énergie dans une turbine Tesla.
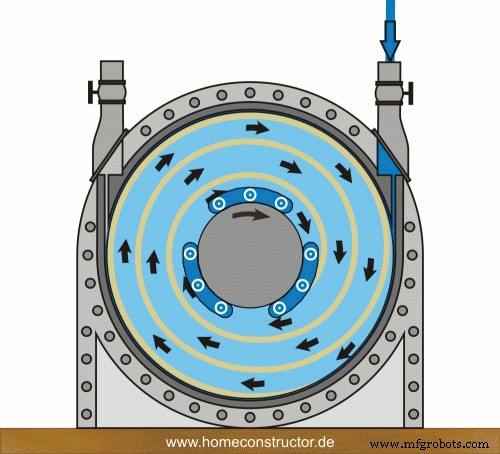
Lorsque Nikola Tesla a créé sa turbine Tesla pour la première fois, il l'a décrite comme son invention «la plus importante». Il a émis l'hypothèse que la turbine pourrait maintenir une efficacité de 90 % et que sa simplicité de conception et de construction pourrait conduire à une révolution dans la production d'électricité. Il avait raison :les deux autres moteurs rotatifs utilisés à l'époque (moteur à pistons et turbine à aubes) étaient coûteux à fabriquer et comportaient de nombreuses pièces qui cassaient souvent. Contrairement à ces deux machines, la turbine Tesla était extrêmement simple. Il n'y avait pas de fonctionnalités complexes à fabriquer ; en fait, les lames n'avaient même pas besoin d'être parfaitement espacées. En théorie, c'était la prochaine étape parfaite dans les moteurs rotatifs.
Malheureusement, dans la pratique, la machine présentait deux points de défaillance clés. Alors que Tesla a annoncé pour la première fois que la turbine était presque parfaitement efficace, en réalité, elle ne fonctionnait qu'à environ 40 % d'efficacité. Sa compréhension de la dynamique de la couche limite n'a pas correctement pris en compte la traînée. Cette évolution était malheureuse, mais nullement accablante; une turbine fonctionnant à 40 % d'efficacité dépasse encore largement les turbines à aubes, qui fonctionnent dans la plage de 25 à 30 %. Si elles pouvaient produire de manière fiable de l'énergie à un taux supérieur à celui des turbines à aubes, les turbines Tesla seraient un nom familier. Ils ne pouvaient pas. Les turbines Tesla tournent à une vitesse extrêmement élevée - les turbines d'essai originales de Tesla tournaient à des vitesses comprises entre 9 000 et 36 000 tr/min - si vite que les pales des turbines se déformeraient gravement pendant le fonctionnement. La déformation n'inspirait guère confiance et l'invention "la plus importante" de Tesla tomba dans l'oubli. Aujourd'hui, les turbines Tesla sont produites à petite échelle en tant qu'accessoires d'enseignement ou de démonstration. Même s'ils n'ont jamais été à la hauteur de leur facture, ce sont toujours des machines fascinantes.
Réinventer une turbine avec des pièces imprimées en 3D
Pour ce projet, nous avons utilisé une conception de turbine Tesla de l'atelier d'usinage du Collège Olin qui comporte trois systèmes de base :un ensemble arbre et rotor, un boîtier de roulement et un boîtier de turbine. L'ensemble arbre est entièrement contraint par le boîtier de palier et contenu par le boîtier de turbine. Le boîtier de roulement et le boîtier de turbine s'emboîtent grâce à un élément de positionnement métallique à ajustement serré et à huit vis.
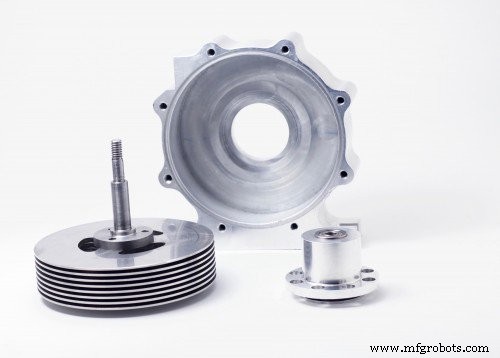
La simplicité de cette turbine se prête bien à l'usinage. Il comporte une grande variété de pièces en termes de matériaux et de fonctionnement, depuis un arbre en acier trempé jusqu'à un couvercle de boîtier en polycarbonate. Chaque pièce de la turbine peut être fabriquée avec une machine CNC à 2 axes ou moins. Ci-dessous se trouve une courte nomenclature de usiné pièces dans la turbine.
Boîtier de turbine : Aluminium fraisé CNC
Support de roulement : Aluminium tourné et fraisé CNC
Arbre : Acier tourné
Entretoises d'arbre : Acier jet d'eau
Lames : Jet d'eau puis acier tourné
Plaque de serrage : Aluminium fraisé CNC
Poulie : Aluminium tourné
Bloc d'entrée : Aluminium fraisé CNC
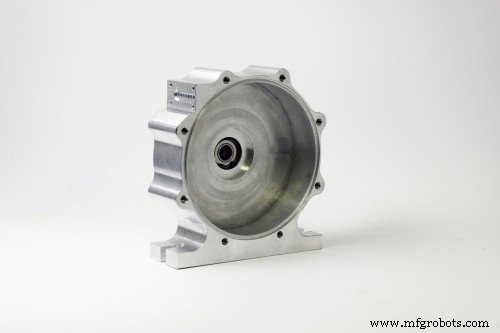
Certaines parties de la turbine ne se prêtent pas bien à la fabrication additive. Les exigences de précision et de résistance axiale rendent l'arbre en acier très difficile à imprimer et les aubes de turbine et les entretoises ont l'avantage d'être lourdes (et donc d'avoir une grande inertie de rotation). Il s'agit d'une application rare dans laquelle notre rapport résistance/poids impressionnant n'est pas bénéfique. Pour ces raisons, nous avons décidé de laisser l'ensemble de l'arbre complet (arbre, entretoises, aubes et plaque de serrage) seul et de nous concentrer sur les parties externes de la turbine. Au lieu de cela, nous nous sommes concentrés sur deux parties :le carter de turbine et le carter de roulement (dont nous parlerons dans le prochain article). Contrairement à l'ensemble arbre, le boîtier était un candidat parfait pour le remplacement. Il est entièrement en aluminium, fraisé CNC et ne présente aucune tolérance inférieure à 0,001 ". En l'imprimant en 3D, nous avons pu conserver notre force tout en réduisant considérablement le poids.
Exigences du boîtier de la turbine
Le carter de la turbine avait plusieurs exigences importantes. Tout d'abord, il devait s'emboîter parfaitement avec le boîtier de roulement. Cela signifiait qu'il devait être de +.001/-0 par rapport à la caractéristique de localisation sur le boîtier de roulement. Sans doute la caractéristique la plus importante de l'ensemble du boîtier, un maillage serré atténue les vibrations qui pourraient déchirer la turbine à grande vitesse. Deuxièmement, le carter de la turbine nécessitait seize trous taraudés; huit sur la plaque arrière pour monter le boîtier de roulement et huit autres à l'avant pour monter une plaque de couverture. La plaque de couverture en polycarbonate est une pièce mineure d'un point de vue structurel, mais elle est extrêmement importante pour garantir que l'air à haute pression circule à travers les aubes de turbine. Enfin, la cavité de la turbine doit avoir un très faible jeu d'ajustement avec les aubes. Un petit jeu d'ajustement permet aux lames de tourner tout en minimisant l'écart entre les lames et la paroi de la cavité, ce qui entraîne une perte d'efficacité significative.
Conception et routage fibre
La refonte de la turbine pour l'impression impliquait quelques modifications mineures pour répondre aux exigences ci-dessus. Tout d'abord, nous avons utilisé des tests unitaires pour vérifier dimensionnellement le tolérancement requis pour le maillage du boîtier de roulement. Pour respecter la tolérance requise, nous avons conclu que nous devions sous-dimensionner le trou en CAO d'environ 0,002" (Remarque :il ne s'agit pas d'un nombre universel, mais plutôt d'un nombre glané à partir des tests unitaires que nous avons effectués. Pour en savoir plus sur les tests unitaires, consultez cet article de blog). Ensuite, nous avons remplacé tous les trous taraudés de la version aluminium par des cavités pour inserts taraudés thermodurcissables (lien ici). Les inserts thermofixés sont une méthode fiable de fixation dans les pièces imprimées en 3D, garantissant des connexions solides là où les trous taraudés ne le peuvent pas.
Nous avons acheminé de la fibre de carbone concentrique dans toute la pièce pour renforcer la conception. Pour garantir que le support du boîtier de roulement et les forces ultérieures ne déformeraient pas la pièce, nous avons rempli la paroi arrière de la pièce avec autant d'anneaux de fibre que possible. Les parois de la pièce nécessitaient moins de résistance, nous avons donc installé un anneau de fibre sur chaque couche de paroi. Nous avons pu grandement augmenter la résistance de la pièce avec un minimum de fibres avec cette stratégie. Une fois la pièce mise en page dans l'Eiger, nous étions prêts à imprimer.
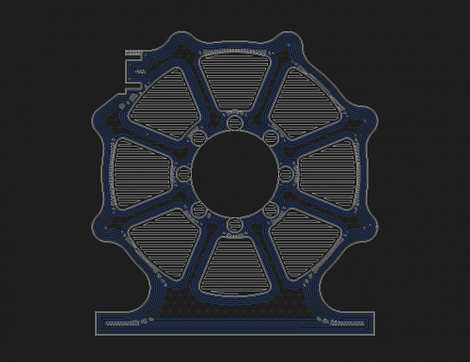
Vérification dimensionnelle
Le corps de turbine s'adapte sur un Mark Two; cependant, nous avons décidé de l'imprimer sur le Mark X pour une raison simple :la vérification des dimensions au laser. Les tests unitaires nous ont dit que nos dimensions devaient être exactes; maintenant, nous pourrions vérifier l'exactitude à mi-impression. Nous avons configuré deux scans laser :un conçu pour vérifier la fonction d'accouplement avec le boîtier de roulement et un autre pour vérifier le diamètre de la cavité. Pendant l'impression, nous avons vérifié chaque numérisation dans Eiger pour assurer la précision dimensionnelle. Le scan dimensionné a montré une erreur de 0,0004″, bien à l'intérieur de la tolérance.
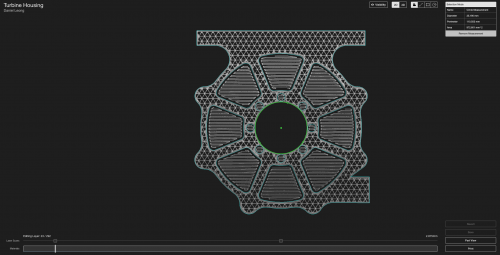
Étapes suivantes
Une fois l'impression terminée, nous avons inséré les inserts filetés et fixé le boîtier de roulement en aluminium. Y compris les inserts, la turbine imprimée 170g, qui était microscopique par rapport au boîtier en aluminium de 570g. Une fois que nous avons vérifié que le boîtier métallique et l'assemblage de l'arbre fonctionnaient, nous avons conçu et imprimé le boîtier de roulement, que nous couvrirons dans le prochain volet de cette série.
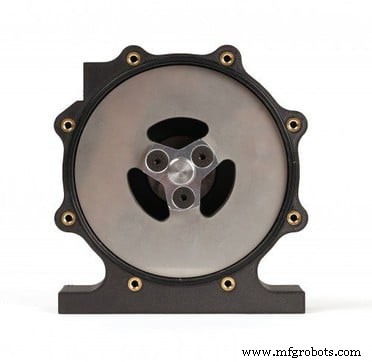
Lisez la deuxième partie de cet article ici et suivez-nous sur Facebook, Twitter, Instagram et Linkedin pour plus de mises à jour !
impression en 3D
- Les 10 meilleurs conseils à prendre en compte lors de la conception de votre pièce FDM
- Applications d'impression 3D métal (partie 2)
- Conception d'une turbine Tesla imprimée en 3D – Partie 1
- Inspection en cours :amélioration des pièces imprimées en 3D
- Drones extrêmes imprimés en 3D
- Précision dimensionnelle des pièces imprimées en 3D
- Comment obtenir des pièces imprimées en 3D plus résistantes
- Méthode d'inspection des pièces imprimées en 3D (partie 3)
- Cylindricité en GD&T