7 conceptions complexes réalisées grâce à l'impression 3D
En tirant parti de la flexibilité de conception offerte par l'impression 3D, les ingénieurs peuvent donner vie aux idées les plus complexes.
L'impression 3D est une technologie qui peut produire des formes et des caractéristiques impossibles à obtenir avec les méthodes de fabrication conventionnelles. Pour montrer la puissance de la technologie, nous explorons 7 exemples de conceptions impressionnantes qui ont été réalisées uniquement avec l'impression 3D.
1. Étrier de frein en titane imprimé en 3D de Bugatti
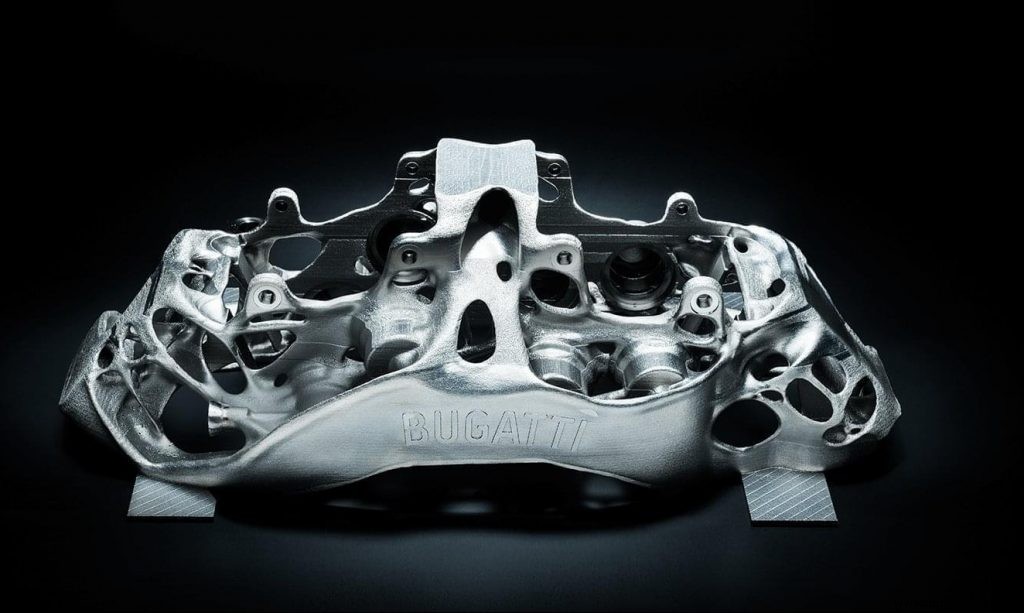
Application :Automobile
Avantages :Légèreté, plus grande résistance
Le constructeur automobile français Bugatti a tiré parti de la liberté de conception de l'impression 3D pour sa dernière supercar Chiron, produisant ce qui serait l'étrier de frein le plus puissant au monde - imprimé en 3D en titane.
Alors que l'étrier de frein fonctionne comme un étrier normal, la combinaison de l'impression 3D et du titane signifie qu'il est beaucoup plus solide et environ 40 % plus léger que la pièce en aluminium actuellement utilisée.
À l'aide d'un procédé d'impression 3D métallique appelé Selective Laser Melting, l'équipe Bugatti a pu expérimenter une variété de géométries et d'épaisseurs de paroi inaccessibles avec les techniques de fabrication traditionnelles.
Le résultat :un étrier de frein de forme complexe avec des épaisseurs de paroi comprises entre 1 mm et 4 mm.
Fin 2018 a vu Bugatti tester avec succès l'étrier à des charges élevées, et l'entreprise se prépare maintenant à mettre le composant en production.
Cependant, Bugatti n'est pas la seule entreprise à révolutionner la conception des étriers de frein. La société britannique de technologie automobile, Carbon Performance, utilise également l'impression 3D pour « générer des conceptions durables » pour les pièces automobiles imprimées en 3D, y compris les étriers.
Pour y parvenir, Carbon Performance utilise sa nouvelle plateforme logicielle basée sur l'IA. La plate-forme aide à concevoir des composants qui peuvent, par exemple, améliorer l'efficacité énergétique d'une voiture.
Grâce à son logiciel de conception et à l'impression 3D, Carbon Performance est en mesure de produire des étriers de frein plus robustes et respectueux de l'environnement grâce, en partie, à leur poids plus léger. Être capable de créer des pièces métalliques légères avec l'impression 3D signifie que moins de matériau est nécessaire et que le processus de production entraîne moins de déchets de matériaux qu'avec la fabrication soustractive.
La création de designs légers est l'un des principaux avantages de l'impression 3D. Alors que la tendance vers des véhicules électriques et plus efficaces continue de croître, nous verrons de plus en plus de constructeurs automobiles explorer l'impression 3D dans leurs efforts pour créer des composants automobiles plus légers et plus performants.
2. Support de siège de conception générative de General Motor
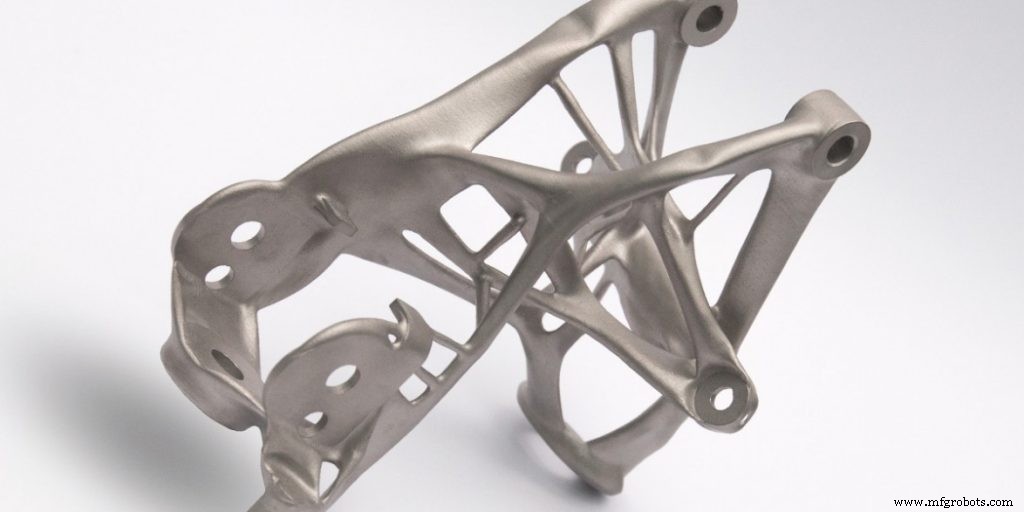
Application :Automobile
Avantage :Gain de poids significatif
General Motors (GM) a récemment créé une version imprimée en 3D d'un support de siège existant à l'aide d'outils de conception générative.
Le logiciel de conception générative utilise des algorithmes avancés pour générer automatiquement plusieurs conceptions variantes basées sur des paramètres spécifiques tels que le poids, le matériau, la taille, la résistance et les méthodes de fabrication. Les conceptions suivantes présentent des formes organiques complexes qui ne peuvent souvent prendre vie qu'à l'aide de l'impression 3D.
C'était exactement le cas avec le support de siège de GM. À l'aide du logiciel de conception générative Fusion 360 d'Autodesk, 150 itérations de conception ont été produites. GM a ensuite sélectionné la conception qui offrait le meilleur compromis entre le poids, les performances et la capacité de fabrication.
Le design final ressemble à peine au support d'origine. Imprimé en 3D en métal, le nouveau support de siège est 40 % plus léger et 20 % plus résistant que l'original. Il a également été fabriqué en un seul composant, contrairement à la pièce d'origine qui doit être assemblée à partir de 8 pièces distinctes.
La capacité de l'impression 3D à créer des pièces complexes plus rapidement et avec plus de flexibilité fait de cette technologie un choix naturel pour produire le composant redessiné. L'avantage illustré dans cet exemple est la consolidation des pièces : la possibilité d'imprimer plusieurs pièces en un seul composant, et ainsi de réduire les délais et les coûts d'assemblage.
Bien que le support de siège de GM reste une preuve de concept, l'entreprise voit un énorme potentiel dans la combinaison de l'impression 3D et des logiciels de conception générative. Les deux technologies joueront certainement un rôle clé dans l'avenir de la fabrication de véhicules en facilitant une conception et un développement de produits plus rapides, ainsi que la production de pièces automobiles complexes.
3. Implant de hanche topologiquement optimisé d'Altair
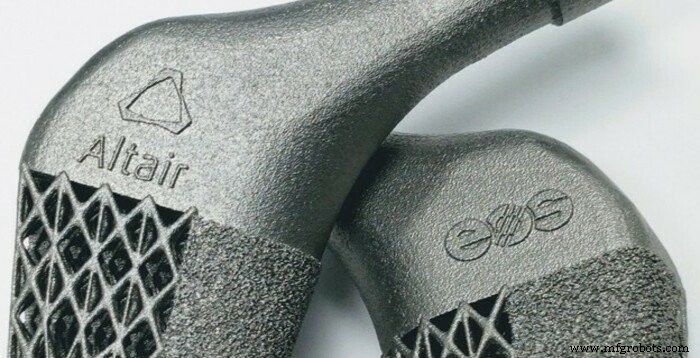
Application :Médical
Avantage :Optimisation des matériaux
L'optimisation de la topologie est une technique de conception générative qui permet aux concepteurs d'appliquer des algorithmes avancés pour optimiser la géométrie d'une pièce. Grâce à cette technologie, la distribution des matériaux d'une pièce peut être optimisée pour éliminer tout matériau inutile de la conception.
Une entreprise tirant parti de l'optimisation de la topologie est la société informatique Altair, qui a combiné l'impression 3D avec l'optimisation de la topologie pour créer un implant de tige de hanche amélioré.
L'impression 3D offre une gamme d'avantages pour les implants de hanche, y compris la possibilité de personnaliser un implant pour les charges spécifiques qu'il doit supporter. Le logiciel d'optimisation de la topologie facilite cela en permettant aux ingénieurs de prendre en compte les différents cas de charge qu'un implant de hanche peut rencontrer au cours de son cycle de vie.
En saisissant des paramètres tels que des cas de charge et des contraintes de conception, le logiciel optimise la répartition des matériaux dans un volume de matériaux défini. Ce processus aboutit à une conception montrant où le matériau peut être retiré pour créer l'implant de hanche le plus performant.
L'équipe Altair a utilisé cette approche pour déterminer les zones solides et semi-denses de l'implant avant de remplir les zones semi-denses avec des structures en treillis pour rendre l'implant plus léger.
Par rapport à un fémur intact ou à un fémur avec un implant standard, l'équipe a découvert que la nouvelle conception permet d'augmenter une limite d'endurance à environ 10 millions de cycles. Cela signifie que l'implant de hanche pourrait supporter le jogging de Los Angeles à New York et retour - deux fois.
Le nouveau design permet également de réduire le stress shielding de 57%. La protection contre le stress fait référence à la réduction de la densité osseuse causée par la mise en place d'un implant en titane à l'intérieur d'un patient et peut finalement entraîner des fractures et des luxations. Pour cette raison, la conception d'un implant aussi proche que possible du tissu osseux d'origine est essentielle pour réduire la protection contre le stress et éliminer ces effets indésirables.
Utiliser l'impression 3D comme technologie de fabrication est le seul moyen de donner vie à de telles conceptions. Non seulement cela permet de créer des formes complexes telles que des treillis, mais cela peut également les produire de manière plus rentable que les méthodes conventionnelles.
Aujourd'hui, les implants imprimés en 3D à topologie optimisée commencent seulement à faire leur chemin dans des cas d'utilisation réels. Il faudra un certain temps aux organismes de réglementation des soins de santé pour développer de nouvelles méthodes de normalisation pour ces nouvelles conceptions d'implants. Cependant, à l'avenir, il est clair que l'impression 3D deviendra une technologie clé pour créer des implants de hanche mieux ajustés, plus durables et plus performants pour un patient spécifique.
4. Le pont piéton imprimé en 3D de MX3D
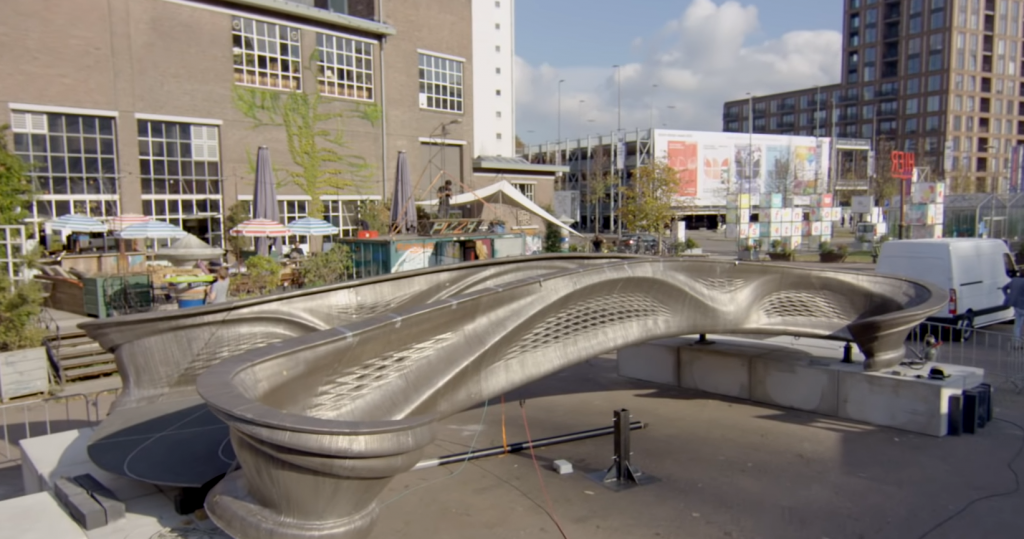
Application :Construction
Avantage :Conception innovante
Dévoilé à la Dutch Design Week en 2018, le pont piéton en acier inoxydable imprimé en 3D de MX3D est l'un des projets de conception les plus passionnants dans le domaine de l'impression 3D.
En installant des machines à souder sur des bras robotisés, l'équipe MX3D a pu imprimer en 3D un pont de 12 mètres de long, obtenant un aspect et une forme uniques. Par exemple, la conception du pont est organique et semblable à du tissu, avec de nombreuses courbes et des caractéristiques complexes. La surface du pont n'a pas été lissée, laissant les couches d'acier déposées visibles qui donnent au pont une finition rugueuse et inhabituelle.
Fait intéressant, l'impression 3D n'était pas la seule technologie de pointe utilisée pour ce projet. Pour assurer à la fois la sécurité et les performances optimisées du pont, la structure en acier imprimée en 3D est équipée d'un réseau de capteurs pour surveiller l'état du pont, enregistrer le nombre de personnes qui le traversent et prendre des mesures comme la dispersion du poids et qualité de l'air.
L'ensemble du projet a duré près de quatre ans et le pont achevé devrait maintenant être installé à Amsterdam plus tard cette année.
5. GE Research développe un échangeur de chaleur bio-inspiré
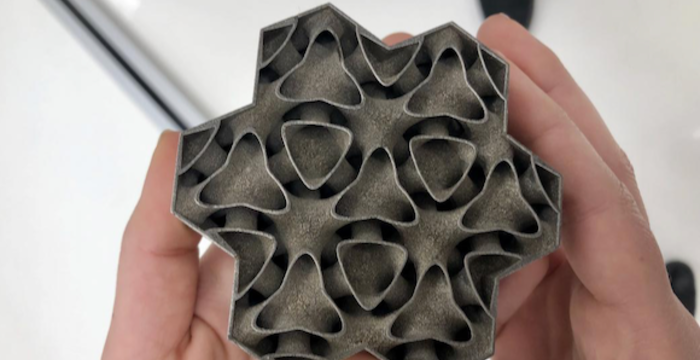
Application :Énergie
Avantage :Performances améliorées
GE Research développe un échangeur de chaleur ultra-efficace et à faibles émissions pour les équipements de production d'électricité tels que les turbines à gaz. Étonnamment, pour y parvenir, l'équipe a proposé un design innovant inspiré des poumons humains.
Les poumons humains sont l'un des échangeurs de chaleur les plus efficaces et les plus compacts. L'organe remplit sa fonction d'échange de chaleur avec un réseau de capillaires, qui divisent le flux sanguin en petits flux. Ce réseau réchauffe l'air plus frais que nous respirons, tout en régulant la température du corps.
L'échangeur de chaleur de GE fonctionne de la même manière, mais à des températures et des pressions beaucoup plus élevées. Le composant comporte un réseau de canaux trifurqués, qui prend l'air chaud sortant d'une turbine à gaz. Ce réseau est entrelacé avec un autre réseau de canaux remplis de fluide de travail plus froid circulant en sens inverse. L'air chaud et le fluide froid ne se mélangent pas, mais leur grande proximité permet de refroidir l'air chaud, améliorant ainsi le rendement thermique d'une turbine à gaz.
Surtout, l'impression 3D était la seule technologie capable de produire un design aussi complexe.
Une fois le processus de développement terminé, GE sera en mesure d'imprimer en 3D un échangeur de chaleur pouvant fonctionner de manière rentable à 250 °C (450 °F) de plus que les échangeurs de chaleur actuels. Avec une température de fonctionnement considérablement augmentée, le composant imprimé en 3D représente une nouvelle génération d'échangeurs de chaleur haute performance.
6. Support de toit léger de BMW
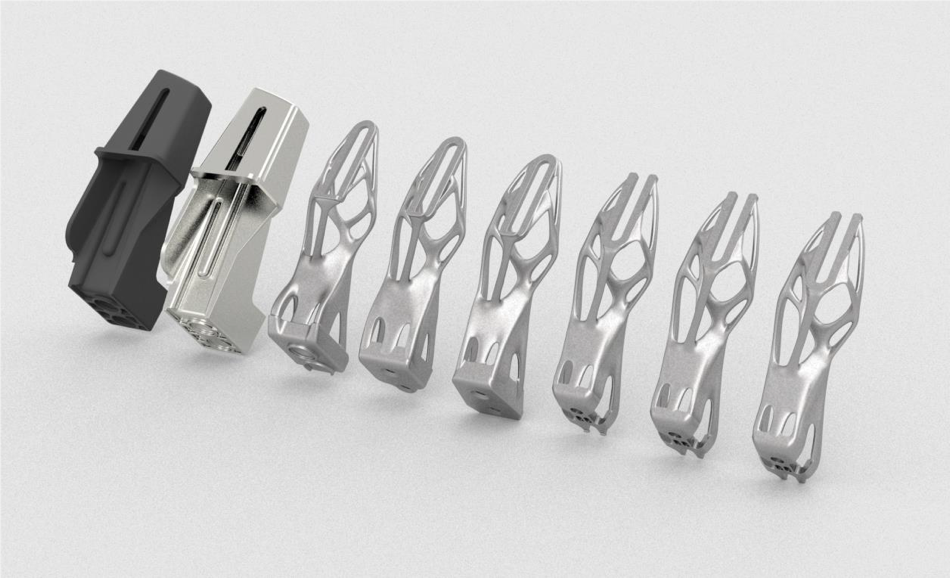
Application :Automobile
Avantage :Gain de poids
En 2018, BMW a lancé sa voiture emblématique i8 Roadster, dotée d'un support de toit en métal imprimé en 3D.
Le support de toit, un petit composant qui aide à se plier et déplier le toit de la voiture, nécessitait une nouvelle conception pour maximiser les performances du mécanisme de pliage du toit. Pour atteindre cet objectif, les ingénieurs de BMW se sont tournés vers un logiciel d'optimisation de la topologie.
En utilisant ce logiciel, les ingénieurs ont pu saisir des paramètres tels que le poids, la taille du composant et la charge qu'il supportera. Le logiciel a ensuite généré une conception qui a optimisé la répartition des matériaux de la pièce.
La conception réalisée par l'équipe d'ingénierie était impossible à couler. L'équipe a découvert que la seule façon de rendre cette conception possible était l'impression 3D en métal.
Grâce à la technologie de fusion sélective au laser (SLM), les ingénieurs ont créé un support de toit en métal qui est 10 fois plus rigide et 44 % plus léger que l'alternative conventionnelle.
La pièce, qui est maintenant produite en petites séries, présente un énorme potentiel de légèreté pour la conception de véhicules lorsqu'elle est combinée à la puissance des techniques d'optimisation de la topologie.
7. KW Micro Power et VELO3D collaborent pour innover un composant de microturbine
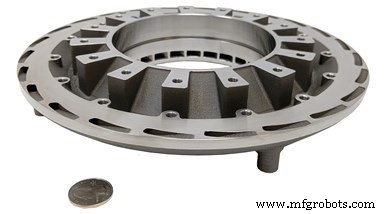
Application :Énergie
Avantage :Fonctionnalités internes complexes
Pendant quelques années, la société d'ingénierie KW Micro Power a travaillé sur la conception d'un générateur à microturbine, mais a rencontré des difficultés pour mettre cette conception en production. Un défi majeur résidait dans la production d'un des composants de l'appareil.
Le composant en question est un disque en titane doté de canaux internes complexes qui permettent de gérer plus efficacement les gaz d'échappement. Lorsqu'il est imprimé en 3D dans du métal, ce composant nécessite des structures de support pour éviter de tomber ou de se déformer pendant le processus d'impression.
Cependant, la complexité des caractéristiques internes du composant a rendu impossible le retrait des supports après la production.
Pour relever ce défi, l'entreprise a collaboré avec VELO3D, un fabricant d'imprimantes 3D qui a développé sa technologie d'impression 3D métal exclusive, Intelligent Fusion. Cette technologie permet à l'imprimante 3D Sapphire de VELO3D d'imprimer des pièces avec des structures de support minimales et des contraintes résiduelles réduites, qui sont souvent la cause du gauchissement.
Ceci est obtenu grâce à une coucheuse brevetée sans contact, qui est utilisée pour fournir une nouvelle couche de poudre à fondre et à fusionner avec un laser. Dans l'impression 3D de métal à base de poudre, lorsque la poudre est déposée sur une autre couche, une coucheuse peut déloger la pièce si elle n'est pas fixée sur une plaque de construction.
Dans le système Sapphire de VELO3D, la lame de revêtement n'est pas en contact avec le lit de poudre. Une fois la poudre déposée, une lame de grattoir et un processus de vide sont appliqués sur le dessus de la poudre pour s'assurer qu'elle est absolument de niveau.
Avec une coucheuse sans contact avec la couche de poudre précédente, une pièce n'a besoin d'aucun support pour l'ancrer sur une plaque de construction en métal. En attendant, la simulation et un système de contrôle en boucle fermée alimentant l'imprimante permettent d'imprimer des fonctionnalités internes complexes sans supports.
Pour tirer pleinement parti de la puissance de l'imprimante 3D Sapphire, l'équipe de VELO3D a aidé KW Micro Power à améliorer encore la conception du composant du générateur. La pièce finie est 37 % plus légère que la conception d'origine et serait plus performante grâce à des contraintes réduites. Mais plus important encore, la conception qui était auparavant considérée comme non manufacturable, a été rendue possible grâce à une nouvelle génération de technologies d'impression 3D métal.
Donner vie aux idées les plus complexes
L'impression 3D offre une grande flexibilité de conception, permettant aux concepteurs et aux ingénieurs d'expérimenter de nouvelles formes et fonctionnalités, notamment des formes optimisées sur le plan topologique, des structures en treillis et des conceptions légères.
Avec autant d'opportunités ouvertes par l'impression 3D, la technologie permet aux fabricants de produire des produits innovants avec des conceptions optimisées et personnalisées, ce qui serait impossible avec une fabrication traditionnelle.
Cependant, pour libérer ce potentiel, il est crucial de suivre les principes de conception propres à la fabrication additive. Ce n'est qu'une fois armés de la compréhension des possibilités et des limites de l'impression 3D que les entreprises peuvent utiliser la technologie pour réaliser leurs idées les plus créatives.
impression en 3D
- Introduction à l'impression 3D avec des plastiques
- Entretien avec un expert :Dr Alvaro Goyanes de FabRx
- Impression 3D avec du silicone — son heure arrive-t-elle ?
- Initiation à l'impression 3D céramique
- Guide d'impression 3D avec HP Multi Jet Fusion
- Impression du fusible 1 avec le fusible 1
- KUHMUTE repense la mobilité avec l'impression 3D SLS
- Impression 3D haute vitesse avec AION500MK3
- Impression 3D de composites avec fibre continue