Entretien d'experts :Armin Wiedenegger, voestalpine High Performance Metals GmbH
L'impression 3D métal continue de faire son chemin dans la fabrication. Aujourd'hui, la technologie devient de plus en plus une solution de production efficace pour les applications de grande valeur et à faible volume dans une gamme d'industries. Cependant, l'évolution continue de l'impression 3D métal dépend fortement du développement de nouveaux matériaux.
Voestalpine, l'une des plus grandes entreprises de technologie sidérurgique en Europe, fait progresser le développement de matériaux pour l'impression 3D métal.
Après plusieurs années à développer son expertise dans les matériaux de FA au sein de sa division Métaux haute performance, voestalpine a ouvert en 2016 son centre de fabrication additive à Düsseldorf. Depuis, l'entreprise n'a cessé d'intensifier ses efforts avec l'ouverture de sites à Taïwan, en Amérique du Nord et à Singapour.
Dans l'entretien d'experts de cette semaine, AMFG s'entretient avec Armin Wiedenegger, Strategy &Business Development for Additive Manufacturing chez voestalpine High Performance Metals GmbH, pour en savoir plus sur ses poudres métalliques AM, ses applications de pointe et success stories.
Pouvez-vous me parler de voestalpine ?
Voestalpine est un groupe mondial de technologie et de biens d'équipement qui offre une combinaison unique d'expertise en matière de matériaux et de traitement.
C'est un partenaire de premier plan de l'industrie automobile et des biens de consommation en Europe, ainsi que de l'industrie aérospatiale, pétrolière et gazière dans le monde, offrant des produits et des solutions de système utilisant de l'acier et d'autres métaux.
Notre Les activités de fabrication additive font partie de la division High Performance Metals du groupe voestalpine, qui est le leader mondial du marché de l'acier à outils et l'un des principaux fournisseurs d'aciers rapides, d'aciers pour vannes et d'autres produits en aciers spéciaux, ainsi que des matériaux en poudre, alliages à base de nickel, titane et composants produits à l'aide de technologies de fabrication additive.
Quels sont les défis liés au développement de matériaux pour l'impression 3D métal et combien de temps dure le processus en moyenne ?
Le développement de matériaux en poudre pour la fabrication additive métallique est un processus très chronophage.
Par exemple, le développement d'un alliage totalement nouveau peut facilement prendre entre 1 et 3 ans. Bien que l'optimisation des alliages existants pour une meilleure imprimabilité 3D puisse être effectuée plus rapidement, cela nécessite encore jusqu'à un an de recherche, de test et de validation.
De toute évidence, les poudres métalliques de haute qualité sont très importantes pour une impression 3D métallique réussie. Pour fabriquer des pièces métalliques cohérentes, vous avez besoin de poudres avec des particules métalliques sphériques étroitement emballées de taille similaire.
Pour y parvenir, les poudres métalliques sont soigneusement fabriquées à l'aide d'un processus d'atomisation au gaz.
Chez voestalpine, il faut quelques semaines pour fabriquer de la poudre métallique à partir d'un alliage existant en utilisant ce procédé d'atomisation.
La Division Métaux Haute Performance dispose de plusieurs imprimantes 3D centres dans le monde entier. Quelles technologies d'impression 3D métal utilisez-vous actuellement ?
Deux technologies de fabrication additive métallique sont utilisées dans nos centres de fabrication additive :la fusion sur lit de poudre et le dépôt direct de métal (DMD).
Avec Powder Bed Fusion, nous pouvons produire des designs plus délicats. Cependant, le processus a tendance à être plus lent et plus coûteux que le DMD.
En ce qui concerne la technologie DMD, nous utilisons des matériaux métalliques sous forme de poudre et de fil. Cependant, bien que la technologie soit moins chère que Powder Bed Fusion, elle est moins flexible en termes de capacités de conception.
Ciblez-vous des secteurs ou des secteurs spécifiques ?
Nos principales cibles sont la fabrication d'outils et les marchés du pétrole et du gaz qui, selon nous, peuvent grandement bénéficier de l'impression 3D métal.
Pouvez-vous partager quelques-unes des réussites de voestalpine ?
Oui, bien sûr.
L'une des applications réussies de la fabrication additive métallique chez voestalpine est les charnières de capot moteur légères que nous avons développées pour une utilisation dans les véhicules.
Ce composant, connu sous le nom de LightHinge+ a été développé en partenariat avec la société d'ingénierie automobile Edag et la société de logiciels de simulation Simufact.
Dans la fabrication traditionnelle, la production de charnières de capot moteur est très coûteuse, notamment en raison des coûts élevés d'assemblage et d'outillage impliqués.
De plus, un tel composant réalisé de manière classique pèse environ 1,5 kg. Comme un véhicule en nécessite environ 40, cela augmente considérablement le poids du véhicule.
Nous avons donc exploité la puissance des outils d'optimisation de la topologie et de simulation pour optimiser le poids du composant. La géométrie requise n'a pu être produite qu'avec Powder Bed Fusion.
Lors de la conception de pièces pour le processus PBF, elles nécessitent généralement de nombreuses structures de support pour permettre une impression réussie. Cependant, les structures de support génèrent beaucoup de déchets matériels et entraînent un post-traitement laborieux.
Les structures de support étaient donc un autre domaine que nous voulions optimiser. Les résultats ont été excellents :
L'utilisation du logiciel de simulation de Simufact nous a permis de réduire le volume des structures de support de plus de la moitié du poids total de la pièce à moins de 18 %. De plus, les techniques d'optimisation nous ont permis de minimiser le temps et les efforts nécessaires pour retirer les supports lors de la phase de post-traitement.
En fin de compte, nous avons pu réaliser un gain de poids de 50 % par rapport à un composant fabriqué avec fabrication de tôles.
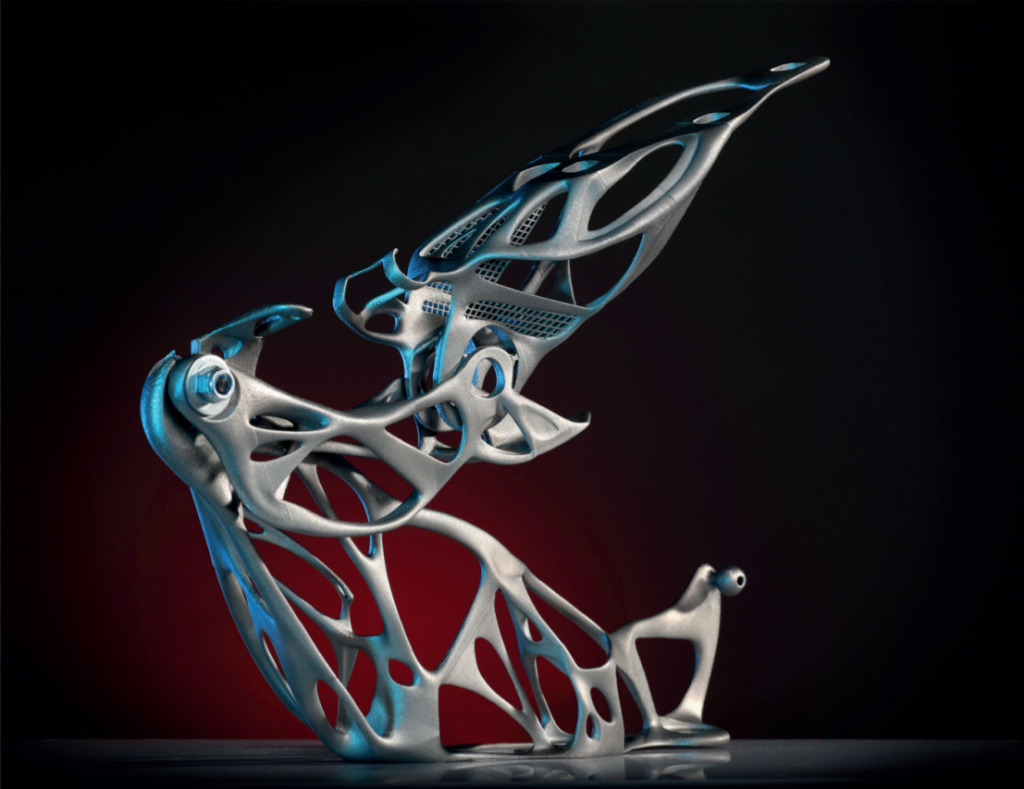
Comment voyez-vous l'état actuel de l'industrie de la fabrication additive et comment voyez-vous son évolution ?
De plus en plus, nous voyons la fabrication additive passer de la production à la pièce à la production en série. Cela indique la reconnaissance croissante de la technologie en tant que solution de fabrication.
Quels défis doivent encore être surmontés pour accélérer l'adoption de l'impression 3D métal ?
La FA est confrontée à plusieurs défis sur la voie d'une technologie viable en production.
Premièrement, les vitesses de production doivent s'améliorer.
Deuxièmement, le coût de l'équipement doit baisser pour débloquer la technologie pour des marchés plus larges.
Enfin, la chaîne de valeur de la FA doit être davantage consolidée pour parvenir à une adoption plus large de l'impression 3D métal. Cela inclut l'intégration de différentes solutions logicielles, de la conception à la fabrication en passant par la gestion, ainsi que l'optimisation de l'étape de post-traitement.
Pour en savoir plus sur la division métaux haute performance de voestalpine, visitez :https://www.voestalpine.com/highperformancemetals/en/
impression en 3D
- Métal à point de fusion élevé | Top 10 des métaux avec des points de fusion élevés
- Entretien avec un expert :professeur Neil Hopkinson, directeur de l'impression 3D chez Xaar
- Entretien avec un expert :Philip Cotton, fondateur de 3Dfilemarket.com
- Entretien avec un expert :Dr Alvaro Goyanes de FabRx
- D'où viennent les métaux ?
- En savoir plus sur les métaux en poudre
- Tournage haute performance
- L'économie de l'usinage des métaux
- Machine de métal déployé à grande vitesse