Redémarrage de la paroi arrière :One-stop, tow to tape to CFRP part
Au début de l'avancée actuelle des composites en fibre de carbone dans les applications automobiles, le constructeur BMW Group (Munich, Allemagne) semblait se démarquer. Premiers travaux pour accélérer le moulage par transfert de résine (RTM) pour la production de son M le toit du modèle sport a conduit à la mise en place d'une chaîne d'approvisionnement complète pour les pièces en plastique renforcé de fibres de carbone (PRFC) sur son i3 et i8 véhicules, puis vers de toutes nouvelles cellules de fabrication et d'assemblage pour la carrosserie multi-matériaux à noyau de carbone en blanc (BIW) sur sa Série 7 .
BMW s'engage pour l'i3 en 2009 en grande pompe, mais la même année, Audi AG (Ingolstadt, Allemagne) a créé un centre technique consacré aux plastiques renforcés de fibres. En 2011, Audi a annoncé un partenariat avec Voith Composites (Garching, Allemagne) pour développer et produire des pièces en PRFC à haut volume. L'année suivante, il a rendu public le développement d'un pilier B en acier renforcé de CFRP, fabriqué à l'aide de moulage par transfert de résine (RTM), et son partenariat avec SOGEFI (Guyancourt, France) pour commercialiser des ressorts de suspension hélicoïdaux composites. En 2012, Audi a également été partenaire fondateur du cluster de pointe MAI Carbon, qui comprenait BMW, Voith Composites, SGL Group (Wiesbaden, Allemagne) et d'autres.
Plus particulièrement, le propre récit d'Audi du développement du CFRP commence avec sa première génération R8 voiture de sport, sortie en 2006. Elle comportait des couvercles de compartiment pour la capote ainsi que des panneaux latéraux fabriqués par moulage par transfert de résine (RTM). L'entreprise est passée d'extérieurs esthétiques et de structures plus petites au système modulaire de voitures de sport (MSS) dans l'Audi R8 e-tron . Bien que la structure principale de cette supercar électrique comprenne des poutres en aluminium extrudé reliées par des pièces moulées en aluminium, tous les panneaux et remplissages étaient en PRFC, y compris un insert de coffre avec des structures de collision ondulées qui ont permis au module arrière d'absorber cinq fois plus d'énergie que le cadre métallique .
L'épine dorsale du MSS est son mur arrière , qui est passé d'un concept initial en 2011 au module actuellement produit pour le R8 non électrique par SGL Technologies (anciennement BENTELER-SGL, Ort im Innkreis, Autriche ; voir « Visite de l'usine :BENTELER SGL »). Mais Audi planifiait déjà sa prochaine étape :itérer la paroi arrière pour une utilisation dans son A8 à volume plus élevé berline de luxe, avec Voith Composites comme partenaire de fabrication.
Voith Composites est une filiale de 10 ans de la multinationale Voith GmbH &Co. KGaA, créée en 1867. La société mère compte aujourd'hui 19 000 employés, réalise un chiffre d'affaires annuel de 4,2 milliards d'euros (5,2 milliards de dollars US) et fournit des équipements et des technologies de fabrication à travers quatre divisions :Voith Digital Solutions, Voith Hydro, Voith Paper et Voith Turbo. Voith Composites est passé de la production de rouleaux de CFRP utilisés dans la fabrication du papier à la fabrication d'arbres de transmission/cardans de CFRP automobiles et industriels et de stratifiés plats.
En 2011, Voith Composites a commencé à travailler sur une chaîne de processus CFRP hautement automatisée, visant à produire le A8 paroi arrière. À la base se trouvait l'applicateur Voith Roving (VRA), qui, en une seule ligne, étend le câble de fibre de carbone 35K de Zoltek (St. Louis, MO, États-Unis) en ruban unidirectionnel (UD) lié, qui est ensuite coupé et empilé pour former un flan sur mesure. Le VRA a été récompensé par un JEC Innovation Award en 2017. Il a également établi une base solide pour les opérations ultérieures de préformage et de moulage. Les meilleurs honneurs de la catégorie automobile ont de nouveau été remportés pour Voith Composites et Audi au JEC World 2018 pour la ligne de production numérique 4.0 basée sur VRA et utilisée pour fabriquer l'Audi A8 module de paroi arrière. En collaboration avec le fournisseur de résine Dow Automotive (Auburn Hills, MI, États-Unis) et Zoltek, ces partenaires ont non seulement développé les matériaux, les processus et les systèmes d'inspection en ligne intégrés nécessaires à la fabrication de pièces CFRP hautes performances à des cadences élevées, mais ont également créé le suite d'outils essentiels de conception/fabrication assistée par ordinateur (CAO/FAO) et de simulation qui sont déjà appliqués pour développer de futures pièces.
Évolution de la conception axée sur l'efficacité
« Nous avons commencé à travailler avec Audi dès le début », déclare le Dr Jaromir Ufer, responsable du développement commercial de Voith Composites. La première priorité était de développer le nouveau A8 conception de la paroi arrière, qui orienterait la façon dont la pièce doit être fabriquée.
« Lorsque nous avons commencé l'ingénierie pour cette production, nous ne pouvions pas trouver de produits [logiciels] prêts à l'emploi qui avaient tout ce dont nous avions besoin », explique Ufer. « Nous avons donc réuni des outils de conception comme ABAQUS, mais avons construit nos propres cartes de matériaux et développé nos propres méthodes de simulation. » Audi avait déjà identifié la réduction du poids BIW et l'augmentation de la rigidité en torsion comme objectifs clés pour la R8 conception de la paroi arrière (voir « Paroi de siège Audi R8 :un prélude à la production »). Pour le A8 module, une conception intégrale a été proposée pour réduire le MSS multi-composant assemblage à un seul panneau en PRFC façonné avec un petit nombre de fixations collées et rivetées. Cette conception a conduit au développement d'un stratifié hautement anisotrope avec des chemins de charge localisés, qui permet à la pièce finie de fournir 33 % de la rigidité en torsion de la cellule d'entraînement à 50 % du poids par rapport à un assemblage de trois à cinq pièces en aluminium soudées.
« La préforme composite pour l'Audi A8 le panneau de paroi arrière varie d'une base de 6 plis jusqu'à 19 plis où un renforcement local est ajouté - par exemple, où il y a des découpes ou des charges ponctuelles, telles que les attaches de retenue pour porte-enfant », explique Ufer (Fig 2).
Applicateur mobile Voith
Ufer note que le développement de cette conception et le VRA se sont déroulés en tandem. « Ce n'est qu'en ayant la liberté de conception qu'offre le VRA que les performances du nouveau A8 mur arrière possible. Le fait que le fournisseur de fibres Zoltek ait pris un engagement de prix de 7 ans dans le programme était également important.
Le processus du VRA commence par un cantre de fibre de carbone PX 35 de Zoltek. Plusieurs bobines de 50K de remorquage sont introduites dans chaque ligne VRA et étalées pour produire des bandes de 50 mm de large. Ensuite, un liant à base d'époxyde est appliqué qui réagira plus tard avec la résine matrice époxy à durcissement instantané Dow VORAFORCE lors du moulage par transfert de résine (RTM) de la pièce composite. Une petite quantité de chaleur infrarouge (IR) est appliquée pour faire fondre le liant suffisamment pour maintenir le ruban ensemble lors des étapes ultérieures de consolidation, de découpe et d'empilage (étape 1).
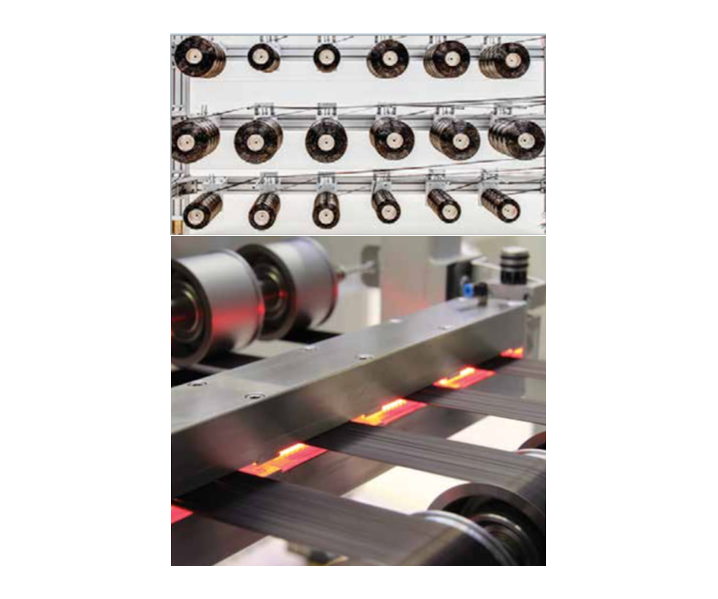
Étape 1 : Le câble en fibre de carbone Zoltek 50K est introduit dans l'applicateur Voith Roving (VRA), où il est d'abord étalé, puis enduit d'un liant à base d'époxyde et ensuite chauffé par infrarouge pour faire fondre partiellement le liant.
« Il s'agit d'un processus continu entièrement automatisé », explique Ufer. « Si pour une quelconque raison il est nécessaire d'arrêter la ligne, l'équipement réagit automatiquement. Par exemple, le chauffage IR est immédiatement éteint et rétracté pour éviter d'endommager la bande par surchauffe. Il existe des centaines de ces détails dans l'équipement et le contrôle numérique permettant cette technologie. »
Étape 2 : La bande de remorquage étalée est ensuite consolidée au fur et à mesure qu'elle passe à travers plusieurs rouleaux sous tension.
Après l'application du liant, la consolidation de la bande est réalisée lorsqu'elle passe à travers plusieurs rouleaux sous tension (étape 2). Ufer explique que cela crée également un tampon pour la ligne. « Nous avons une unité qui interrompt le flux de traction continu de la fibre, fournissant une transition vers le format d'impulsion du mécanisme de coupe et de placement de la bande. » Ce mécanisme à portique coupe les rubans à des longueurs sur mesure et les place à des angles spécifiés de 0 à 360 ° sur une table rotative (étape 3). Chaque pile sur mesure, comprenant 6 à 19 couches de ruban, a une épaisseur de 1,5 à 3,7 mm, respectivement.
Étape 3 : Le VRA coupe ensuite le ruban et place jusqu'à quatre morceaux à la fois sur une table rotative, adaptant à la fois la longueur du ruban et l'angle d'orientation dans la pile de stratifié (par exemple, 45°/90°/30°).
Voith a installé quatre lignes VRA (voir photo d'ouverture), et bien que chacune applique jusqu'à quatre bandes de 50 mm de large à la fois, souligne Ufer, « les lignes ont une approche modulaire, elles peuvent donc appliquer 10 bandes ou plus à un temps. Cela dépend de la taille de la pièce et de la cadence de production.
L'automatisation comprend l'inspection de la qualité. Les scans des bandes et des préformes sont comparés à un algorithme de rejet. « Le balayage à 100 % de la bande par le VRA garantit la bonne distribution des fibres pour l'ensemble de la ligne de production », explique Ufer. « Nous utilisons également la thermographie et des capteurs laser pour vérifier les préformes dans des zones désignées. » Le VRA peut alors réagir à tout problème qu'il détecte. « Si une bande n'est pas correcte », souligne-t-il, « le VRA coupera la longueur défectueuse et en produira une autre pour la remplacer ». Un QR code est placé sur la préforme finie pour la traçabilité. (Les codes QR sont préférés aux étiquettes d'identification par radiofréquence (RFID) car ils résisteraient mieux au processus d'injection de résine.)
Formage, moulage et assemblage
La pile 2D sort du VRA et est transférée dans la section de formage, de moulage et d'assemblage de la ligne de production. La première presse dans laquelle il est placé, fournie par le spécialiste de l'automatisation des composites FILL (Gurten, Autriche), utilise la chaleur et la pression pour façonner la pile de ruban 2D en une préforme 3D (étape 4). Ufer explique que parce que la préforme varie en épaisseur et en forme, la presse peut adapter la pression appliquée lorsqu'elle estampe des régions séparées de la préforme serrée dans l'outil de formage. ALPEX Technologies (Mils bei Hall, Autriche) a fabriqué les moules RTM en acier apparié, sur la base d'une conception fournie par Voith Composites. « Nous avons développé virtuellement l'outillage et le processus de presse », explique Ufer. « Bien qu'aucune boucle de test réelle n'ait été requise, nous avons validé et vérifié les modèles de simulation sur d'autres formes et pièces avant d'usiner le A8 outils de production de paroi arrière. Cette simulation du processus de moulage s'est directement transformée en production réelle et a contribué à accélérer l'optimisation. »
Étape 4 :La pile de rubans est transportée dans une presse, où elle est façonnée dans la forme finale de la pièce 3D.
La presse maintient pendant quelques secondes pour faire réagir le liant en poudre et définir la forme, résultant en une préforme stable qui peut résister au lavage des fibres pendant l'injection de résine. « Les particules de liant servent également à maintenir les fibres séparées pour un meilleur écoulement de la résine pendant la RTM », note Ufer. « Ceci est utile car il n'y a pas de couture dans la préforme pour faciliter l'écoulement de la résine, de sorte que ces particules de liant agissent comme des micro-canaux d'écoulement. »
La préforme façonnée est ensuite transférée par robot dans une cellule CNC d'EiMa Maschinenbau GmbH (Frickenhausen, Allemagne), où un couteau à ultrasons coupe le contour final extérieur. Il est ensuite placé de manière robotique dans une presse RTM (étape 5) fournie par ENGEL (Schwertberg, Autriche). Tous les robots de la gamme sont fournis par KUKA Robotics (Augsbourg, Allemagne).
Étape 5 : La préforme façonnée est placée dans une presse de 350 kN et moulée en ultra-RTM.
Le processus RTM utilisé pour façonner le A8 la paroi arrière est la même que celle développée au Audi Lightweight Center pour la précédente R8 paroi arrière, appelée ultra-RTM. Il permet le moulage de grandes pièces par injection rapide mais basse pression. Par rapport aux 140 bars typiques du HP-RTM, la pression d'injection de résine dans le moule pendant l'ultra-RTM de l'Audi A8 la paroi arrière est <15 bar, encore moins que celle du R8 . En conséquence, au lieu de 2 500 kN de force de presse, seuls 350 kN sont nécessaires. Par conséquent, une presse plus petite et moins coûteuse peut être utilisée pour produire des pièces de haute qualité et à volume élevé de fibres.
La résine époxy VORAFORCE 5300, un système à trois composants qui inclut le démoulage, durcit en 90-120 secondes à 120°C et a une viscosité de traitement de 20 cps. Pour le A8 paroi arrière, une grenaille de résine de 1,3 kg est injectée dans la préforme, suivie d'un durcissement de 120 secondes.
La pièce durcie est démoulée par robot et chargée dans une cellule de fraisage CNC fermée pour l'usinage des découpes. Ensuite, la pièce fraisée est placée dans une machine à laver automatisée pour nettoyer la poussière résiduelle de CFRP.
La paroi arrière lavée est transférée dans une cellule d'assemblage équipée de deux robots. Le premier robot place la pièce moulée dans une machine de rivetage automatisée, qui documente la force appliquée lors de l'installation du rivet. Cela fait partie de l'intelligence de fabrication intégrée au processus global et est ajouté à l'enregistrement de traitement numérique de chaque pièce (c'est-à-dire, le fil numérique). La pièce est ensuite déplacée dans la zone de collage et un deuxième robot prépare les zones de collage, à l'aide d'un essuyage à solvant automatisé. Le même robot applique ensuite l'adhésif structurel polyuréthane à deux composants à durcissement rapide Dow BETAFORCE 9050M (étape 6), qui est compatible avec l'époxyde à trois composants. La pièce est ensuite placée dans un four pour un court cycle de durcissement de l'adhésif.
Étape 6 : L'adhésif polyuréthane BETAFORCE est appliqué de manière robotique pour les fixations collées, puis durci au cours d'un cycle de four court.
Cette ligne de production maintient un temps de cycle de 5 minutes pour la pièce terminée et la demande actuelle de pièces peut être satisfaite en une ou deux équipes de 8 heures. Un appareil de numérisation laser 3D est utilisé périodiquement pour vérifier la forme et les mesures 3D de la pièce. Les pièces finies sont ensuite préparées pour être expédiées vers l'Audi A8 chaîne d'assemblage final à Neckersalm, en Allemagne, à environ 3 heures de route (étape 7).
Étape 7 : La pièce finie est ensuite préparée pour être expédiée vers la chaîne d'assemblage final de l'Audi A8.
Placement direct des fibres =flexibilité future
Avec tous les investissements qui ont été faits, il est surprenant d'apprendre que Voith Composites n'était pas assuré de cette entreprise, mais en effet la société a terminé le développement et a ensuite participé à un processus d'appel d'offres pour remporter la production. « Nous avons pu respecter le coût cible des pièces défini par Audi, ainsi que les exigences de qualité et de performance des pièces », explique Ufer. Ce n'était pas un mince exploit, étant donné que de nombreuses entreprises étaient en lice pour le programme.
Voith Composites a breveté plusieurs parties de son processus. « Le VRA a démontré son industrialisation en utilisant le placement direct des fibres [DFP] de bandes, ce qui réduit les déchets ainsi que le matériau utilisé via une superposition hautement optimisée », explique Ufer. Il utilise également les matériaux les plus économiques - fibre de remorquage lourde non traitée et liant en poudre. Son processus de deuxième génération remplace le liant en poudre par une application directe de résine, éliminant ainsi davantage d'étapes de processus. Cependant, la société a développé d'autres processus DFP, notamment le préformateur Voith Longfiber et le bobinage Voith Prepreg.
« Nous établissons de nouvelles normes pour les pièces en fibre de carbone pour la production en série automobile à grand volume », a déclaré le directeur général de Voith Composites, le Dr Lars Herbeck. « L'usine intelligente que nous avons établie porte la production automatisée de composants CFRP à un nouveau niveau d'efficacité et de flexibilité, y compris presque toutes les formes ainsi que les tailles de lots individuels. » C'est, en effet, où l'industrie se dirige.
Résine
- Pourquoi le matériau PEEK est au sommet de sa catégorie
- Plastique renforcé de fibres de carbone (CFRP)
- K 2019 :Materials Matter à la Messe
- Arkema lance le programme ‘Start-Up Connect’
- Polykemi investit dans sa propre usine de compoundage aux États-Unis
- Polykemi aura une production composée sur trois continents
- Ruban unidirectionnel thermoplastique en fibre de carbone à base de PPS
- La fibre de carbone Split Tow améliore les performances du SMC
- Le module CFRP permet d'économiser du poids sur la conception des fusées