Fabrication continue de fibres (CFM) avec des composites moi
L'impression et le dépôt 3D de fibres en continu prennent de l'ampleur. À mesure que le nombre d'entreprises l'utilisant et la faisant progresser, cette technologie façonnera sans aucun doute l'industrie des composites.
Premièrement, il propose une fabrication sans moule ni outillage. Deuxièmement, il offre des structures multifonctionnelles (par exemple, conductivité électrique, changement de forme, détection). Troisièmement, il ouvre la porte à un monde de fabrication hybride - par exemple, la stratification sur l'impression 3D et le fraisage pendant l'impression - ainsi qu'un paysage presque infini de développement de matériaux, des fibres d'alliage à mémoire de forme (SMA) Nitinol aux solutions nanocomposites conductrices pour la modélisation des dépôts liquides (MLD). Ce dernier est tout un monde en soi sur lequel je reviendrai dans un prochain blog.
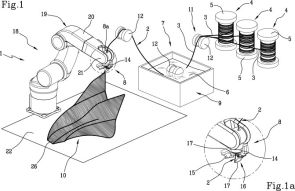
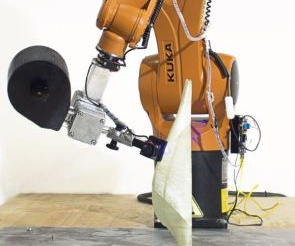
Brevet WO2017085649A1 et système d'impression Atropos. SOURCE :moi composites.
Moi composites a été créé en février 2018 par l'ingénieur en matériaux et professeur Marinella Levi, l'ingénieur concepteur Gabriele Natale et l'architecte Michele Tonizzo. En 2013, le professeur Levi a commencé à travailler avec l'impression 3D au Politecnico di Milano (Milan, Italie). En 2014, elle avait formé +LAB dans le département de chimie, des matériaux et de génie chimique "Giulio Natta" de l'université. Sa vision était de fusionner la R&D, l'enseignement et l'innovation des matériaux en rassemblant des ingénieurs, des designers, des chercheurs et des fabricants dans un pôle d'impression 3D collaboratif et multidisciplinaire.
2014 Premier outil d'impression 3D de composites thermodurcissables à fibres continues 2015 Brevet WO2017085649A1 2016 Partenariats avec Owens Corning et KUKA Robotics,Atropos projet et système d'impression 2017 JEC Innovation Award, partenariat avec Autodesk,
Finaliste du prix James Dyson,
Partenariat avec COMAU automation
(Chronologie complète)
« Nous avons lancé moi composites parce que nous voulions produire des pièces commerciales et participer à des projets internationaux », explique Michele Tonizzo. « Nous avons découvert qu'il y a beaucoup de marché. Nous fabriquons des composants biomédicaux ainsi que des pièces pour les applications marines, pétrolières et gazières et aérospatiales, principalement en fibre de verre. La technologie CFM est capable de fabriquer des solutions uniques qui seraient impossibles avec les méthodes traditionnelles."
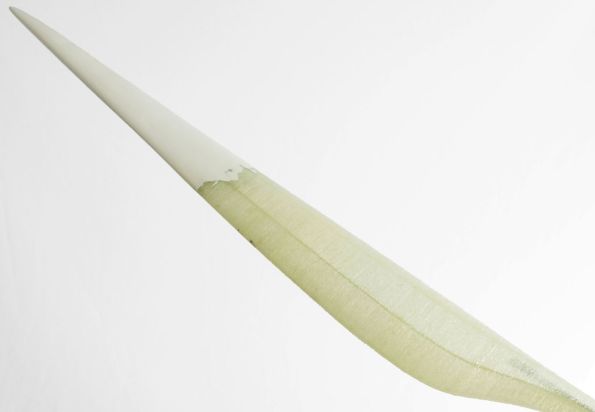
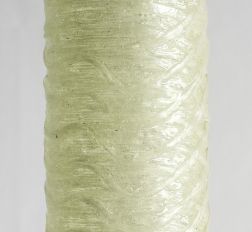
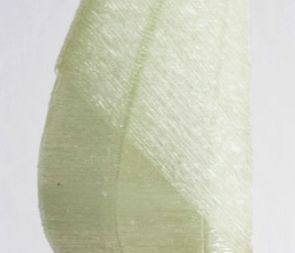
Pale d'hélice imprimée en 3D avec treillis structurel interne utilisant de la fibre de verre continue (en haut). Ce projet a également démontré le placement des fibres le long de courbes non linéaires (en bas à gauche) et des fibres stratifiées continues avec des orientations de fibres traditionnelles (par exemple, 0°, +45 °, -45°, 90°, en bas à droite). SOURCE :composites moi
Gamme de résines et fibres
Atropos a démontré sa capacité à imprimer des polymères thermodurcissables discontinus et continus renforcés de fibres, non seulement couche par couche, mais également le long de courbes non linéaires. Il a utilisé la lumière ultraviolette (UV) pour durcir les polymères en place. « Nous pouvons actuellement imprimer avec un séchage UV dans de l'époxy, de l'acrylique et du vinylester », explique Tonizzo. Il note que l'acrylique fonctionne bien pour les pièces architecturales car il est clair et ne nécessite pas de température pour le durcissement/post-durcissement. Le vinylester est utilisé pour les pièces marines et l'époxy pour les pièces pétrolières, gazières et aérospatiales.
« Pour certaines applications, le durcissement aux UV n'est que l'étape initiale, puis nous post-polymérisons avec un chauffage conventionnel », observe Tonizzo. « Nous ne sommes pas liés au séchage UV. Nous avons imprimé avec des polymères ne durcissant pas aux UV et comprenons que pour les applications à propriétés plus élevées, nous aurons besoin de différentes options de matrice. Pour référence, la température de transition vitreuse (Tg) de leur résine la plus couramment utilisée, un vinylester, est d'environ 140°C.
« Nous travaillons également avec de la fibre de carbone, mais pas avec des résines à séchage UV », explique Tonizzo. Il souligne que la transparence des fibres et la couleur affecte le durcissement UV. « Le problème avec le carbone est qu'il est opaque et noir. C'est la pire combinaison. Nous voulons développer la meilleure solution pour la fibre de carbone en tant que matériau, pas seulement la technologie la plus simple qui fonctionne. Il existe de nombreuses autres options de matériaux de durcissement que nous pouvons utiliser, nous les étudions donc. »
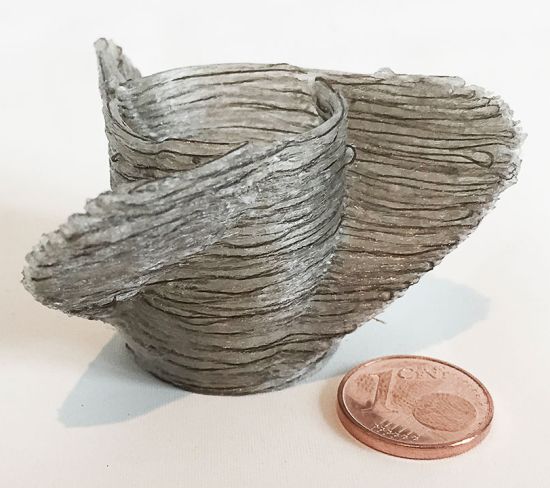
Les composites Moi peuvent imprimer des fibres conductrices continues pour la fonctionnalité électrique/thermique, la détection, le changement de forme, etc. SOURCE :composites moi.
Moi composites a imprimé de la fibre de verre continue jusqu'à 2400 tex (207 yd/lb avec un diamètre maximum de 24 m selon une fiche technique d'Owens Corning) et teste des fibres naturelles. Il a également imprimé avec de la fibre de basalte. « Nous pouvons très bien imprimer avec le séchage UV et la fibre de basalte, car il est en fait un peu transparent et plus marron que noir », explique Tonizzo.
Des fibres conductrices de courant électrique peuvent également être utilisées dans la technologie CFM. Ils peuvent être placés selon les besoins dans la structure en cours d'impression. L'un des projets répertoriés sur le site Web +LAB montre la fibre Nitinol, qui est un alliage à mémoire de forme. « Vous pouvez donc créer des structures qui changent de forme », explique Tonizzo. "Par exemple, vous pouvez l'utiliser pour relâcher les contraintes sur d'autres fibres, comme dans le béton précontraint."
Impression 3D dans le cadre d'une fabrication hybride
Atropos utilise un bras robotique Kuka avec une enveloppe d'impression de 0,5 x 0,5 x 0,5 m de hauteur. "Nous imprimons maintenant sur un robot Comau avec une enveloppe de 1,0 x 0,5 x 0,8 m de hauteur, qui est le système de deuxième génération", explique Tonizzo. "Nous avons également utilisé des robots plus grands avec des tables rotatives et des volumes de construction de 1,5 x 1,5 x 1 m de hauteur et avons démontré que notre technologie est facilement évolutive."
Moi développe également une tête d'impression tout-en-un de troisième génération avec un système pour appliquer une pression sur les fibres, les capteurs, les mécanismes de coupe et l'outil de fraisage. Tonizzo dit que cela comblera l'écart entre l'impression 3D et le placement automatisé des fibres (AFP ). « L'impression 3D n'atteint pas les performances de l'AFP, mais CFM offre plus de flexibilité. Nous pouvons déjà imprimer avec des fibres de 0,25 mm d'épaisseur et avons la possibilité de créer des courbes et de placer des fibres continues dans la position idéale », ajoute-t-il.
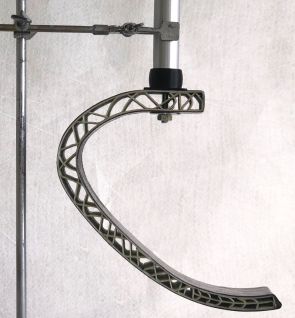
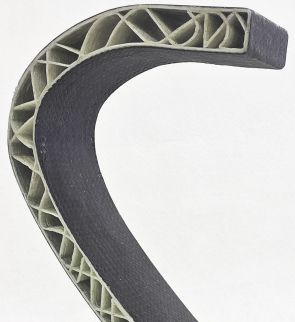
SuPeRIOR est un prothèse de membre inférieur optimisée pour un poids, une déviation et un coût minimaux.
Le noyau structurel imprimé en 3D a ensuite été stratifié avec de la fibre de carbone et de la résine époxy, suivi d'un durcissement VBO. SOURCE :moi composites.
« L'impression 3D doit être utilisée pour ce qu'elle fait de mieux », explique Tonizzo, « ce qui inclut l'optimisation du flux de travail. Par exemple, vous pouvez imprimer en 3D un noyau interne avec des contre-dépouilles et des directions de fibre intelligentes. Vous utilisez ensuite un pelliculage à la main commun sur le dessus et durcissez dans un autoclave ou avec un sac sous vide uniquement. Il décrit une pièce impossible à réaliser de manière conventionnelle avec un moule. « Nous avons imprimé le noyau interne, puis l'avons enveloppé dans un stratifié et l'avons durci à l'autoclave à 110 °C et 2 bars de pression pendant plusieurs heures. La partie s'est très bien passée. Cette partie est couverte par un accord de non-divulgation, donc aucun autre détail n'est disponible, mais moi a produit la prothèse SuPeRIOR d'une manière similaire, durcie non pas dans un autoclave mais avec un sac sous vide uniquement (VBO). « Tous les composants internes utilisent une fibre de verre continue », explique-t-il, « mais le stratifié extérieur est constitué d'un tissu en fibre de carbone et de résine époxy. » L'ensemble de la conception réduit la déflexion et augmente la personnalisation tout en réduisant considérablement les coûts et le temps de production.
Logiciel d'optimisation basé sur Voxel
Tonizzo explique que le processus de conception des pièces combine l'algorithme basé sur les voxels d'Autodesk avec les algorithmes de moi pour l'optimisation des contraintes et des chemins. C'est ce qui produit le chemin de fibre optimisé pour la structure. Le logiciel travaille également à choisir le chemin le plus possible pour fabriquer. « Il s'agit d'un processus itératif », explique Tonizzo. « La conception n'est pas entièrement automatisée comme la conception générative. Il a encore besoin d'ingénieurs pour faire des choix. Mais je pense que c'est ainsi que cela devrait être :le concepteur et le logiciel combinés, pas seulement l'IA seule. »
Avenir multi-matériaux, fort potentiel de marché
Dans l'une des images de la pale d'hélice imprimée Atropos, il y a un gros plan montrant un motif presque tissé. "Ce n'est pas réellement tissé mais ce sera bientôt possible", explique Tonizzo. Il m'oriente vers le projet sine wave sur le site +LAB. « Les démonstrateurs présentés sont imprimés en 3D dans du plastique avec des fibres courtes et le procédé LDM [liquid deposition modeling] alors qu'ils étaient des chercheurs de +LAB. Les algorithmes que nous utilisions alors sont les mêmes que ceux que nous avançons maintenant avec la fibre continue. »
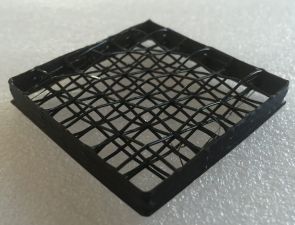
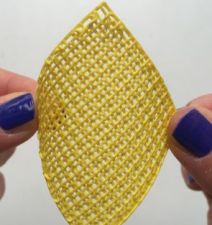
+Sine Wave de LAB démontre des motifs de remplissage en polymère imprimés en 3D avec une réponse élastique ajustable. SOURCE :+LAB.
Il ressort clairement du site Web +LAB que les innovations matérielles et les possibilités pour ce type d'impression sont presque infinies. La question est de savoir ce qui offrira le plus d'opportunités et de potentiel pour des solutions à forte demande. Pendant ce temps, les fournisseurs de matériaux soutiennent le développement continu. Par exemple, Owens Corning souhaite faire la démonstration de la fibre de verre avec plus de matrices, comme la céramique et le béton. De toute évidence, cela est très intéressant pour les applications de bâtiment et de construction, et pourrait avoir un potentiel important à la lumière des tendances actuelles en matière de fabrication numérique et de construction économe en énergie, de modules préfabriqués hors site et d'une durabilité améliorée via des matériaux naturels et recyclés, qui mettent tous l'accent sur la légèreté. « Le département Giulio Natta du Politecnico di Milano participe à un projet européen d'impression de géopolymères qui se comportent comme du béton », ajoute Tonizzo. « Ils durcissent d'eux-mêmes avec le temps mais ont la consistance de l'argile lors de l'impression pour une meilleure fluidité. Nous allons certainement continuer à travailler dans ce domaine, ainsi qu'avec de nouveaux polymères et fibres. »
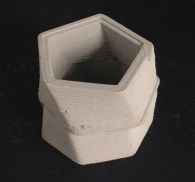
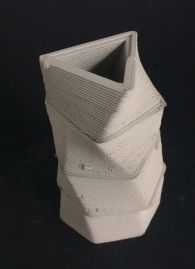
Moi composites est impression également avec des géopolymères, qui se comportent comme du béton.
SOURCE :+LAB.
Vendrez-vous vendre des machines ? "Oui, mais dans le futur", dit Tonizzo. « Pour l'instant, nous produisons des pièces et apportons la technologie à l'installation du client, en utilisant notre savoir-faire, notre tête d'impression et notre logiciel pour réaliser des solutions de pièces à la demande. » Il ajoute qu'après avoir travaillé l'année dernière pour améliorer la technologie avec les premiers utilisateurs de CFM et démontrer l'analyse de rentabilisation de nombreuses pièces différentes sur différents marchés, moi composites recherche maintenant des investisseurs pour faire évoluer davantage les machines et les processus CFM pour les opportunités de marché commercial.
Résine
- Installations d'assemblage d'impression 3D avec composites Markforged
- Fabrication additive avec des composites dans l'aérospatiale et la défense
- Évaluer une chaîne d'approvisionnement composites en évolution
- Recyclage des composites — plus d'excuses
- La fabrication continue de fibres brouille la frontière entre l'impression 3D et l'AFP
- Covestro lance les thermoplastiques à fibres continues Maezio
- Impression 3D de composites avec fibre continue
- Severstal investit dans la robotique pour automatiser la fabrication de composites avancés avec Airborne
- GE Digital :informations opérationnelles avec données et analyses