La fibre de carbone permettra les eVTOL de taxi aérien
Ce blog est en réponse à un article de janvier 2019 dans WIRED magazine, qui affirme que la production de composites en fibre de carbone freine le développement de véhicules électriques (EV)/avions à décollage et atterrissage verticaux (VTOL) pour le marché de la mobilité urbaine et du taxi aérien. Je vais en débattre, mais aussi proposer une nouvelle technologie potentiellement perturbatrice, alors lisez jusqu'au bout.
Bien que j'applaudis l'auteur pour avoir couvert cette industrie en plein essor et pour avoir souligné la nécessité de concevoir en gardant à l'esprit la possibilité de fabrication, il est parfois trompeur, probablement parce qu'il n'est pas très informé sur l'industrie des composites. Par exemple :
Bien que cela soit techniquement vrai, Airbus passera à 60 A320/mois d'ici mi-2019 et Boeing est en route pour 57 appareils/mois pour le B737, également en 2019. Pour l'A320, cela signifie produire trois 6,3 m de haut assemblages d'empennages verticaux en plastique renforcé de fibres de carbone (CFRP) par jour et aussi trois 12,45 m-span Ensembles d'empennages horizontaux CFRP par jour .
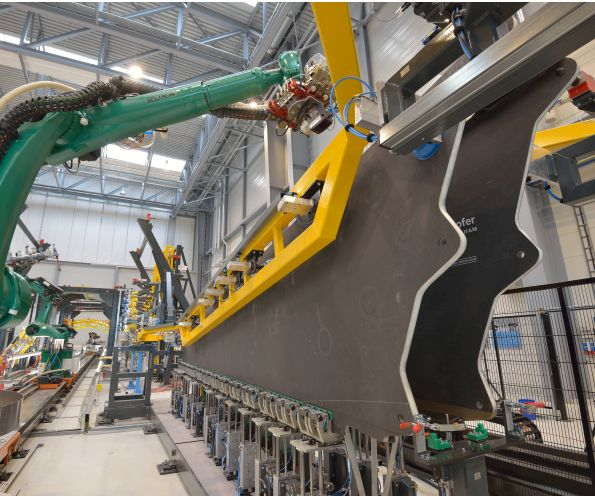
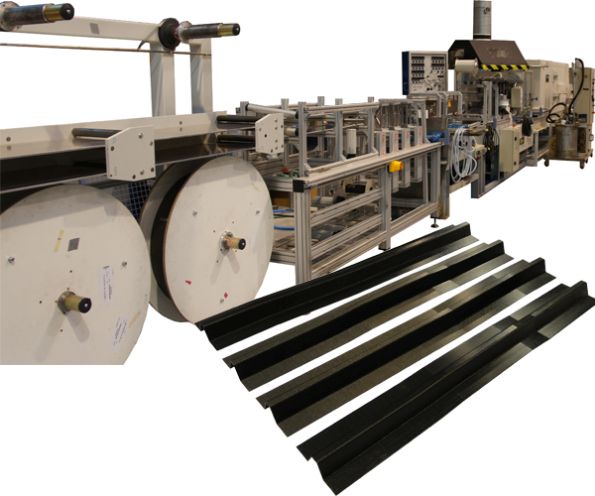
De plus, Airbus a qualifié une technologie après l'autre - beaucoup utilisant des composites et toutes destinées à 60 à 70 avions par mois - pour la prochaine itération de l'A320, appelée A320 Neo Plus. Ces technologies composites couvrent un portefeuille comprenant le moulage par transfert de résine (RTM), le moulage par compression de composés de moulage en feuille (SMC) et les composites thermoplastiques (TPC) qui ont des temps de cycle facilement capables de plus de 700 avions par an. Certaines des technologies les plus récentes en développement réduisent les temps de cycle des pièces en PRFC de 4 heures à 15 minutes ou moins. La plupart des nouvelles technologies qualifiées par Airbus sont fortement automatisées, tout comme les nouvelles méthodes d'assemblage.
L'industrie automobile a également ouvert la voie à une production de masse plus élevée que ce que les eVTOL nécessiteront (WIRED cité une demande projetée de 23 000 véhicules d'ici 2035). BMW augmente la production de son i3 et i8 modèles - les deux sont équipés de cellules passagers entièrement en PRFC - de 130 à 200 unités/jour et le fournisseur d'Audi Voith Composites produit la paroi arrière CFRP pour l'A8 à un rythme de 150-300 unités/jour . A noter que la BMW i3 et i8 Les modules sont très similaires à la cellule illustrée ci-dessous pour l'Airbus Helicopters EC 135 - les deux fabricants fixent ensuite les composants extérieurs et intérieurs à cette structure.
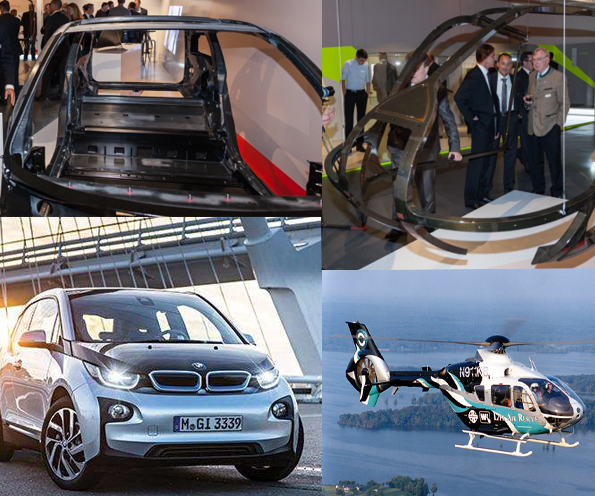
Les cadres de carrosserie BMW i3 et i8 sont très similaire à celui de l'Airbus Helicopters EC135.
SOURCE : Milestones of the Leading-Edge Cluster – Review and Future Prospects, MAI Carbon, pp 36-7 (en haut), BMW et Airbus Helicopter (en bas).
Pendant ce temps, l'Audi A8 la paroi arrière est fabriquée avec un temps de cycle de 5 minutes à l'aide de RTM et d'un placement automatisé de ruban en fibre de carbone sec, adapté en longueur et en orientation de fibre pour répondre à des charges spécifiques, et variant d'une base de 6 plis (1,5 mm d'épaisseur) jusqu'à 19 plis (3,7 mm d'épaisseur) où un renforcement local est ajouté pour répondre aux charges ponctuelles élevées. Cette pièce unique fournit 33 % de la rigidité en torsion de la cellule d'entraînement à 50 % du poids par rapport à un assemblage de trois à cinq pièces en aluminium soudées.
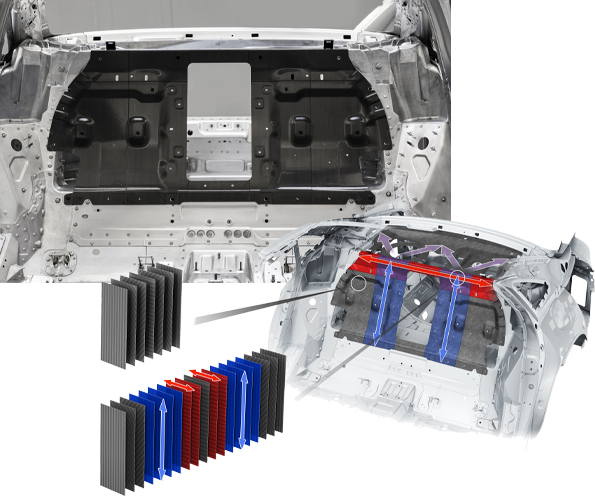
L'Audi 2019 A8 dispose d'une paroi arrière en PRFC fabriquée en 5 minutes à partir de ruban en fibre de carbone.SOURCE :Audi et Voith Composites.
Thermoplastiques
Mais ces exemples n'exploitent même pas la technologie thermoplastique, privilégiée comme choix pour le nouvel avion de taille moyenne (NMA) de Boeing, qui devrait être annoncé avant le deuxième trimestre 2019. Les pièces thermoplastiques volent dans les avions depuis les années 1990, tandis que le développement s'est poursuivi. , avec Airbus et les fournisseurs européens de niveau 1 prototypant des sections d'aile et de fuselage toujours plus grandes (avec raidisseurs intégrés), passant cette année à des démonstrateurs de fuselage pleine grandeur. Notez que les composites thermoplastiques permettent également le soudage, offrant ainsi d'autres possibilités d'éliminer les fixations et l'assemblage.
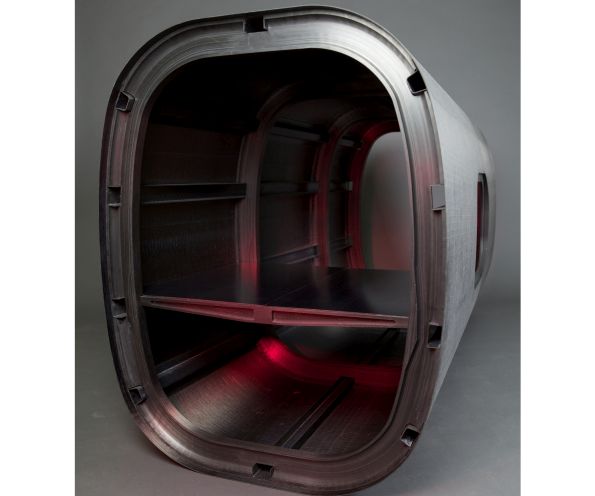
Automated Dynamics, qui fait désormais partie du groupe Trelleborg , a produit cette poutre de queue d'hélicoptère CF/PEEK pleine grandeur et intégralement raidie en 2012 en utilisant la consolidation in situ pendant le placement automatisé des fibres, éliminant ainsi les longs cycles d'autoclave ainsi que les attaches et les adhésifs.
SOURCE :dynamique automatisée, Trelleborg
La chaîne d'approvisionnement des matériaux et du traitement TPC s'est rapidement fusionnée au cours des trois dernières années, tous les principaux fournisseurs de fibres de carbone produisant désormais des rubans thermoplastiques et des pièces surmoulées à temps de cycle réduit démontrées par plusieurs entreprises pour les applications aérospatiales et automobiles. Le soudage thermoplastique a également été démontré par plusieurs entreprises.
Extrait de "Le surmoulage en tant que catalyseur des composites, de l'aérospatiale à l'automobile", interview de Scott King chez le fabricant de composites CCP Gransden :
CCP Gransden a affiné sa technologie de thermoformage et de surmoulage de composites thermoplastiques en une seule étape pour produire des composants légers et complexes avec des temps de cycle généralement inférieurs à 2 minutes, en utilisant une large gamme de polymères et de fibres. SOURCE :CCP Gransden
Technologie la plus récente
Mais la technologie a progressé depuis 2014 pour inclure désormais plusieurs développements intéressants :
Thermodurcissables thermoplastiques surmoulés
Le projet OPTO-Light à AZL Aachen a démontré des nervures et des clips en composite thermoplastique surmoulé (TPC) sur une fibre de carbone/époxy pièce composite.
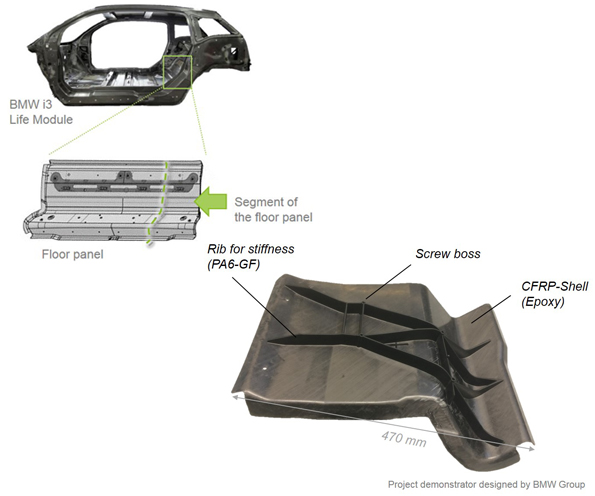
Surmoulage + Pultrusions porteuses UD
Le projet MAI Skelett a démontré des pultrusions TPC surmoulées dans un processus en deux étapes et 75 secondes pour produire un élément de toit structurel/cadre de pare-brise qui dépasse toutes les BMW i3 exigences des pièces tout en intégrant des fixations et des clips, ainsi qu'en modifiant le comportement en cas de collision du mode de rupture fragile au mode de rupture ductile pour une résistance résiduelle BIW accrue.
Le partenaire du projet SGL Carbon fournit désormais de la fibre de carbone avec le dimensionnement approprié pour les solutions à matrice unique utilisant la famille PP ou PA6, y compris les pultrusions, les organofeuilles et les composés de surmoulage ainsi qu'une expertise en conception et en processus pour le développement de pièces, cette dernière via leur centre d'applications légères (LAC, Meitingen, Allemagne).
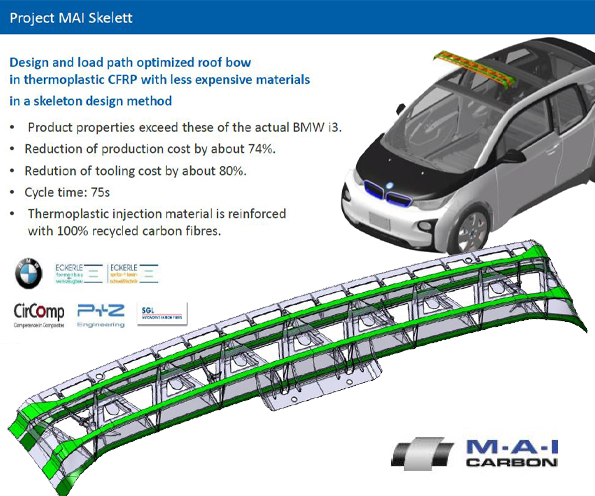
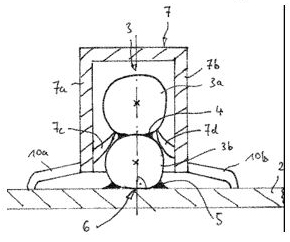
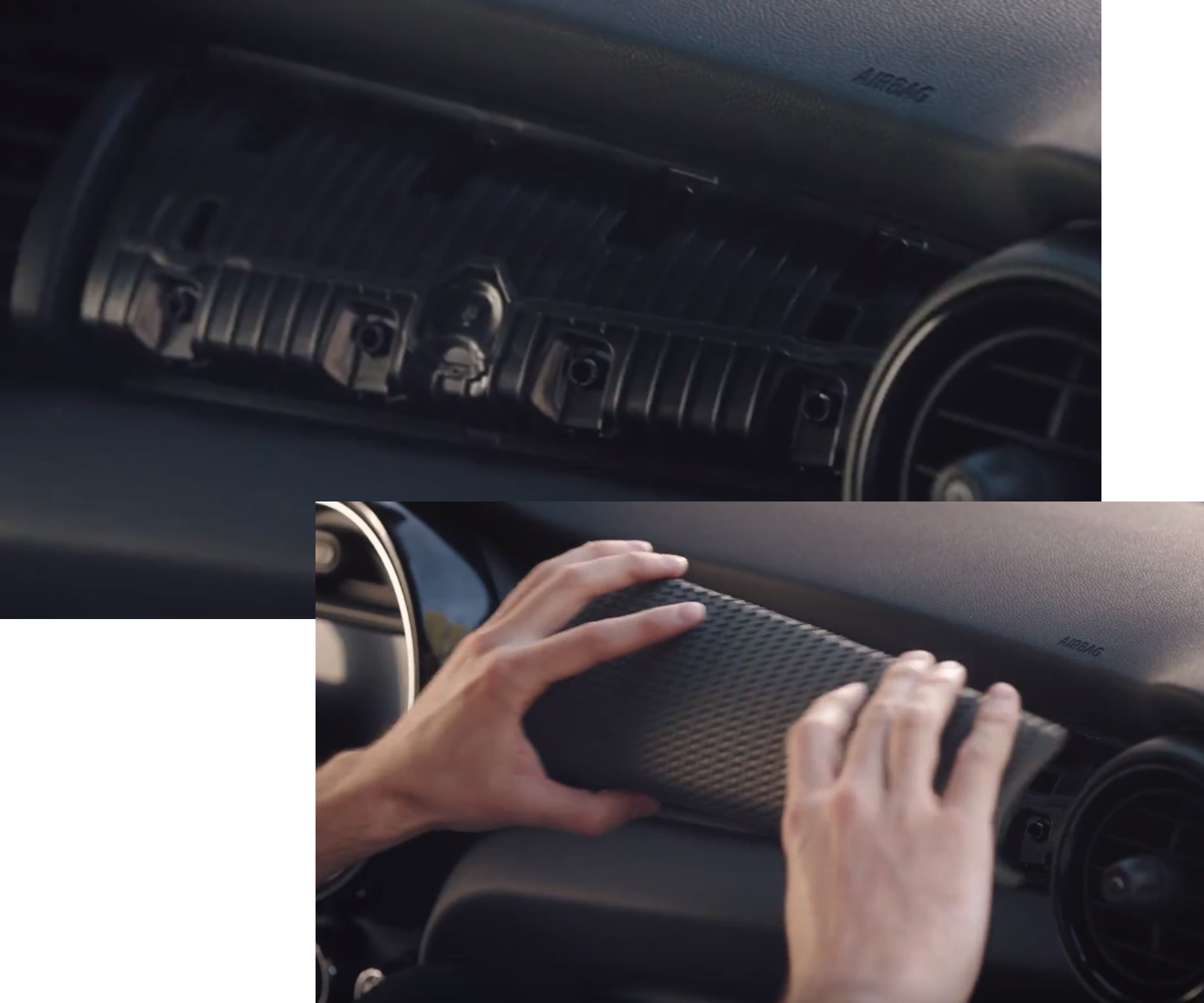
Nouveau brevet de BMW , le système de fixation de haute précision utilise des clips moulés par injection ou surmoulés (en bas) et des billes imprimées en 3D (en haut) sans attaches, trous percés ou adhésif. Les images du bas montrent comment ce système permet de « clipser » les garnitures intérieures personnalisées imprimées en 3D dans le cadre du programme MINI Yours Customized 2019.
SOURCE :Brevet DE 10 2013 214 269 B3 (en haut)
https://www.youtube.com/watch?v=1pyxNKw-nf8 (en bas)
Retour au FILAIRE article et ses allégations non éclairées :
Il est vrai que cette méthode de production de CFRP est utilisée depuis de nombreuses années, mais il est également vrai que les constructeurs aéronautiques et automobiles sont déjà passés à des matériaux et des procédés plus automatisés et à zéro déchet, ainsi qu'à des thermoplastiques avec des avantages avérés dans éliminant les attaches, permettant la recyclabilité/contenu recyclé et la réparabilité.
Au final, le FILAIRE L'auteur contredit toute sa thèse car le pionnier d'eVTOL ICON prévoit non seulement d'aller de l'avant avec sa cellule CFRP, mais aussi de fabriquer des pièces pour des avions plus gros. La fibre de carbone ne va évidemment pas mettre à la terre les eVTOL, mais joue déjà un rôle clé dans les entreprises qui font progresser l'ingénierie intelligente pour une large gamme de futurs véhicules, à la fois dans les airs et sur la route. L'utilisation des dernières technologies est logique, car tous ces nouveaux véhicules doivent de toute façon être certifiés.
Un point clé était réalisé dans l'article du PDG de BetaTechnologies, Kyle Clark :
Le PDG de Blue Force Technologies, Scott Bledsoe, a également souligné l'importance d'avoir l'aérodynamisme, la propulsion, le style, les structures et la fabrication équipes, chacune avec un siège égal à table à chaque étape de la conception et du développement.
Mais la chose la plus importante est peut-être de rester à jour sur l'évolution de la fabrication des composites et de se connecter avec les nombreux fournisseurs de matériaux, d'équipements et de technologies qui souhaitent partager leur expertise et aider à développer de futures applications. Contactez-nous sur CompositesWorld car c'est ce que nous faisons :fournir des connexions et des informations techniques et fiables.
Résine
- Fibre de carbone
- 3 raisons pour lesquelles les fabricants de fibre de carbone en feront plus bientôt
- Qu'est-ce que la fibre de carbone ?
- L'essor des plastiques renforcés de fibres de carbone
- Plastique renforcé de fibres de carbone (CFRP)
- La fibre de carbone est-elle conductrice ?
- La Ford Last GT sera une supercar en fibre de carbone en édition limitée
- La basket en fibre de carbone Air Jordan 1 est un incontournable des collectionneurs
- Recyclage des composites — plus d'excuses