Impression composite en fibre continue industrialisée à Delft
L'impression 3D de composites renforcés de fibres continues continue de se développer et de progresser. De nombreuses nouvelles entreprises et développements ont vu le jour depuis que Markforged a annoncé l'imprimante 3D à fibre continue Mark One en 2014. J'ai blogué sur bon nombre d'entre eux, et je continuerai à explorer le paysage et les acteurs en développement rapide pour CW lecteurs.
CEAD (Delft, Pays-Bas) a été introduit dans la fonctionnalité de mars 2019 de Karen Mason, "Moving Continuous-fiber 3D Printing into production". Dans ce blog, je donne plus de détails sur la base de mes entretiens avec le co-fondateur Maarten Logtenberg, y compris pourquoi l'entreprise vend son extrudeuse séparément et la vision de l'entreprise pour l'avenir de l'impression à fibre continue.
Impression avec et sans fibre continue — dans la même impression
Avec Logtenberg, CEAD a été fondée par Lucas Janssen. Ils formaient la moitié de l'équipe qui a lancé la société néerlandaise d'imprimantes 3D Leapfrog. « Nous avons fabriqué de nombreuses machines d'impression 3D différentes pour l'industrie », déclare Logtenberg. « Je cherchais le marché et j'avais l'impression qu'il manquait l'impression à grande échelle avec des matériaux adaptés à des applications véritablement industrielles. Vous avez besoin de plus de résistance que le thermoplastique seul. C'est ce qu'offre l'impression avec fibre continue. "Nous avons donc développé notre propre technologie, que nous avons brevetée", poursuit-il.
« Nous constatons toujours un besoin d'impressions avec fibre courte et sans fibre. » C'est pourquoi la fabrication additive continue de fibres de CEAD La technologie (CFAM) permet d'imprimer avec des fibres continues et avec extrusion directe à partir de granulés non renforcés ou renforcés de fibres courtes dans la même impression . « Nous n'avons pas besoin de changer la tête d'impression », explique Logtenberg. « Nous plaçons la fibre continue au milieu de la masse fondue, de sorte que les deux sont extrudées en même temps. Mais ils utilisent des systèmes d'entraînement différents. La fibre continue est poussé à travers la tête d'impression mais pré-imprégné pour assurer la qualité. »
Déjà standard dans les composites moulés par injection et surmoulés, ainsi que dans les composites thermoplastiques à fibres longues directes (DLFT) moulés par compression, l'extrusion directe de granulés/matériaux granulés est moins chère pour la production industrielle, explique Logtenberg. « Ces matériaux doivent être séchés pré-impression, et nous avons développé notre propre sécheur, qui est connecté à la machine CFAM. »
Semblable aux composites thermoplastiques surmoulés, pour chaque impression, le même polymère est utilisé à la fois dans le filament continu pré-imprégné et dans l'extrusion directe non renforcée ou renforcée de fibres courtes. L'entreprise a traité une large gamme de polymères, dont l'ABS, le PC, le PEEK, le PET, le PLA et le PP. Ils explorent maintenant le PEKK et le PAEK à faible fusion.
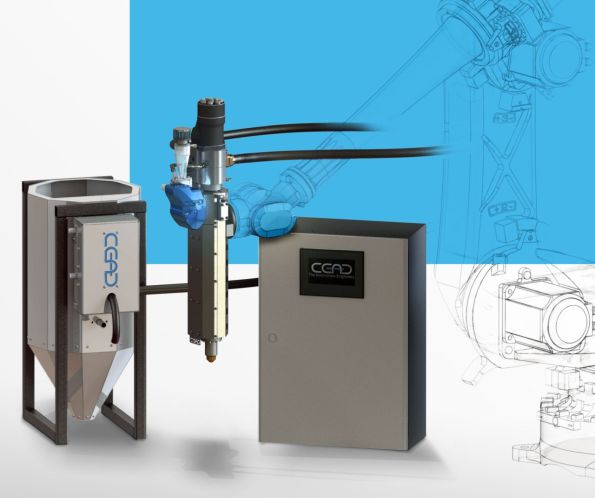
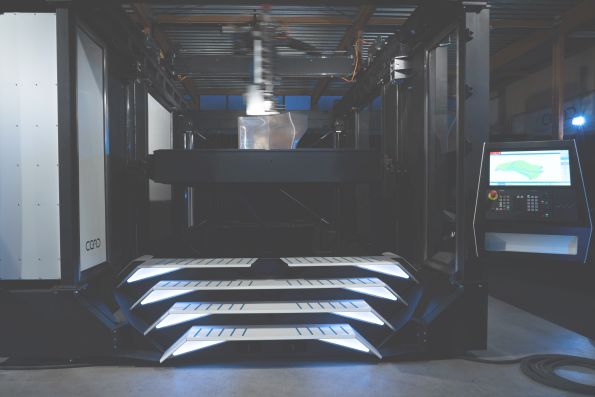
CEAD propose un tête d'extrusion plus petite pour les bras robotiques (en haut) et sa machine à base de portique CFAM Prime (en bas) avec un volume de construction de 4 m x 2 m x 1,5 m.
SOURCE :CEAD
Zones de chauffe et portique vs robot
Actuellement, CEAD propose l'extrudeuse Robot, dotée de quatre zones de chauffe, et son CFAM Prime à portique machine, avec un volume de construction de 4 par 2 par 1,5 mètres et 10 zones de chauffage dans l'extrudeuse. « Nous avons commencé le développement en 2017 », explique Logtenberg. « La tête d'impression est basée sur une extrudeuse à vis unique couramment utilisée avec le moulage par injection. Vous avez besoin de zones pour chauffer progressivement le matériau afin que vous puissiez appliquer la grande pression nécessaire (50-60 bars) pour extruder autant de matériau. Les plombs sont transférés dans le canon, où ils fondent, puis vous comprimez et poussez. Si vous chauffez trop vite, aucune pression ne s'accumulera dans l'extrudeuse. »
Pourquoi vendre l'extrudeuse/tête d'impression séparément ? « Les clients voulaient également une extrudeuse plus petite pour un bras robotique afin de construire leurs propres machines, mais n'utilisant pas de fibre continue, mais uniquement une extrusion directe », explique Logtenberg. Alors pourquoi utiliser un portique pour le CFAM Prime ? La réponse courte :précision et rapidité. « Les robots sont vraiment bons en précision relative », explique-t-il, « mais la façon dont ils arrivent au point B à partir du point A est inexacte. Avec l'impression 3D, vous devez vous déplacer en continu avec précision pour créer une pièce finie de haute qualité. »
"L'autre problème est la vitesse", poursuit-il. « Nous voulions un rendement élevé pour la production industrielle mais aussi avec une haute résolution. Un bras robotique utilisant notre extrudeuse peut se déplacer à 4 m/min, ce qui est très rapide pour un robot, mais la machine à portique peut se déplacer à 60 m/min ."
Bien que le portique offre de la vitesse, une extrudeuse sur un bras robotique offre toujours une impression multi-axes . « Nous sommes intéressés par l'utilisation de l'impression multi-axes pour surmonter le défi actuel avec les propriétés de la direction z [typiques de l'impression en tranches] », reconnaît Logtenberg. « Nous avons d'abord développé le système de portique, mais nous avons maintenant un nouveau système de contrôle de Siemens qui offre le même contrôle sur un bras robotique. Nous développons donc des machines 5 axes . Le système de portique est toujours plus rapide, mais ce nouveau système offre un véritable placement multi-axes. Il envisage de combiner les deux systèmes, similaire à la configuration des fraiseuses CNC à 5 axes.
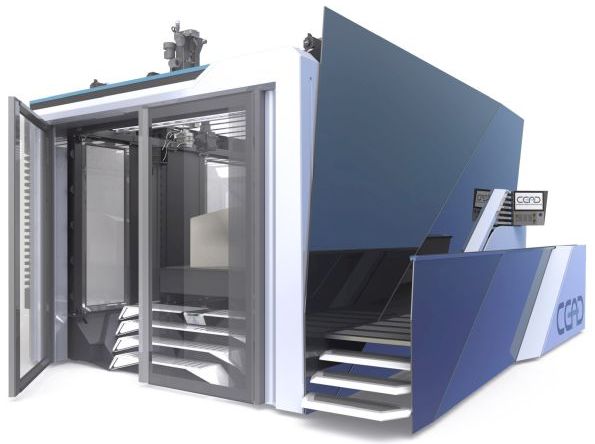
Machine CFAM Prime avec chambre fermée (en bas ).
SOURCE :CEAD
Refroidissement et contrôle
L'un des problèmes de l'impression 3D est de contrôler le retrait de la matrice plastique. Bien que le CFAM Prime ait initialement utilisé un chauffage infrarouge (IR) géré avec l'entrée de caméras thermiques, Logtenberg concède que ce système produisait un chauffage inégal lors de l'impression de formes complexes. « Nous utilisions toujours une chambre d'impression fermée et développent actuellement un lit d'impression chauffant ," il dit. « Cela fournira une chaleur plus uniforme et nous utiliserons toujours des caméras thermiques pour surveiller et gérer le système. Si vous imprimez la même pièce deux fois à six mois d'intervalle, vous aurez le même profil de température et les mêmes conditions dans la chambre d'impression. »
Logtenberg note que le CFAM Prime extrude tellement de matériau qu'il contient beaucoup d'énergie. « Il est donc difficile de le refroidir assez rapidement pour que l'impression soit stable. Vous voulez refroidir les couches pour les rendre stables lors de l'impression. », ajoute-t-il. Comment ce refroidissement est-il réalisé ? « Utiliser de l'air pulsé, et beaucoup d'entre eux », explique Logtenberg. Il note que l'ajout de chaleur dans le lit d'impression et la chambre d'impression fermée fait partie du contrôle du gauchissement. « Vous posez des couches chaudes sur des couches froides. Mais vous voulez garder le matériau au-dessus de sa Tg, qui est supérieure à 150 °C pour certains matériaux, tout en étant stable pour imprimer dessus. Même avec ce processus, Logtenberg note qu'il y aura toujours une certaine contrainte thermique dans la pièce. « Vous pouvez effectuer certaines étapes de post-traitement pour éliminer la tension de la pièce. »
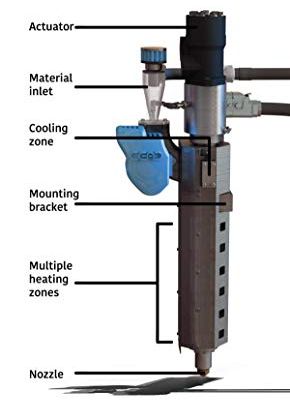
Robot extrudeur avec plusieurs zones de chauffage.
SOURCE :CEAD
CEAD utilise des systèmes Siemens pour contrôler ses machines. « Ceux-ci sont bien pensés et peuvent relever des défis complexes dans le processus et les matériaux », explique Logtenberg. CEAD a écrit son propre logiciel derrière le système Siemens pour fournir une interface utilisateur simple. « La machine fonctionne sur le code G, qui est également la norme utilisée pour les fraiseuses industrielles », note-t-il. « Cela donne de la liberté dans la programmation des pièces. Il peut utiliser des slicers open source mais aussi Siemens NX , qui est un outil logiciel puissant. »
Logtenberg dit que le client peut choisir le niveau de complexité qu'il souhaite atteindre. « Notre approche est très open source , permettant d'utiliser différents types de logiciels d'impression. Ainsi, si le client souhaite une impression très simplifiée, il vous suffit d'appuyer sur un bouton. Mais il est également possible d'utiliser des logiciels plus avancés. Cependant, le client doit alors savoir comment l'utiliser. Notre vision est de laisser les gens décider ce qu'ils veulent utiliser et ensuite nous les soutenons . " Logtenberg note que CEAD vend aux entreprises, pas aux consommateurs. « Nous avons donc la capacité de fournir plus de soutien. »
Pièces et propriétés imprimées
« Vous pouvez sentir la différence entre les pièces imprimées avec des fibres continues et celles imprimées avec des fibres hachées », note Logtenberg. "Mais nous n'avons pas encore testé les propriétés." C'est la prochaine tâche, maintenant que le développement de la machine et le lancement initial sont terminés. "Cette année, nous allons travailler sur la caractérisation complète des matériaux et le développement de fiches techniques avec la résistance à la compression, la rigidité, etc. pour chaque combinaison de matériaux", ajoute-t-il.
La détermination de la teneur en vide et du volume de fibres fait également partie de ce travail de caractérisation. "Notre teneur en fibres n'est pas si élevée pour le moment", concède Logtenberg. « Si vous utilisez des granulés de fibres hachées, vous avez par exemple 30 % de fibres en poids. L'ajout de la fibre continue n'ajoute que 10 % supplémentaires à cela, car la sortie et le volume globaux sont importants. »
Qu'en est-il du compactage pour réduire le contenu en vides ? « La buse elle-même compacte la couche », explique Logtenberg. « Vous devez avoir la bonne hauteur de couche par rapport à la largeur. Si vous avez ce droit, vous obtenez une bonne adhérence entre les couches. Il explique que le rapport hauteur/largeur doit être dans la bonne plage pour permettre une force de compression dans la couche imprimée et suffisamment de chaleur pour obtenir une bonne fusion dans les couches. « Par exemple, dans une couche imprimée de 5 mm de haut et 5 mm de large, il n'y aura quasiment pas de force de compression », note-t-il. "Pour une couche de 5 mm de haut, il faut une largeur de 10 mm."
CEAD améliore continuellement la qualité d'impression CFAM Prime, déclare Logtenberg. « Nous avons développé de nombreux logiciels internes pour l'impression dynamique. Il explique qu'il y a eu des problèmes dans les coins parce que l'extrudeuse pousse le matériau tandis que la machine doit ralentir pour tourner dans le sens. « Nous avons maintenant résolu ce problème. Nous continuons à développer notre suivi en utilisant des capteurs, la dynamique et la température de couche, par exemple, pour améliorer le contrôle de processus . "
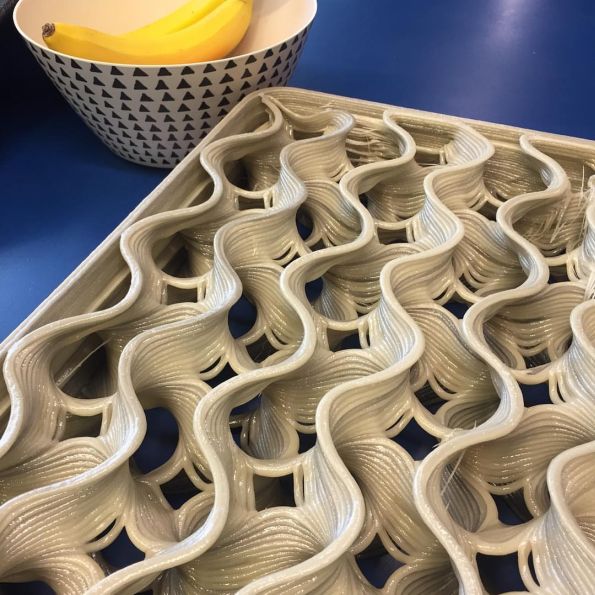
Impression de formes complexes avec CFAM Prime.
SOURCE :Instagram CEAD, mars 2019
Machines pour la marine et la construction
Logtenberg affirme que les premiers objectifs de la capacité de production industrielle de CEAD Prime sont les marchés de la marine et du bâtiment et des infrastructures, car ses pièces composites imprimées sont suffisamment bonnes pour être directement utilisées pour le service final. En effet, ses premiers clients sont Royal Roos (Rotterdam, Pays-Bas), une entreprise d'ingénierie et de construction maritime, et Poly Products (Werkendam, Pays-Bas), un fabricant de composites qui travaille dans les secteurs de la marine, de l'architecture, de l'industrie, des loisirs et des transports.
Cela dit, la CFAM Prime est également utilisée pour imprimer des moules, notamment pour les structures marines. « C'est pourquoi nous avons opté pour le bras robotique », explique Logtenberg, « et nous avons ajouté le fraisage CNC , un peu comme la machine LSAM [de Thermwood] mais un peu plus petite et moins chère. »
« Dans l'UE, le taux de construction pour la marine est en baisse », dit-il. « Parce que la main-d'œuvre est si chère, la production va en Chine. Donc, nous essayons d'établir un moyen de concurrencer. Nous examinons également d'autres marchés, comme l'automobile, l'aérospatiale et d'autres transports. »
La réponse sur le marché de la marine et de la construction a été bonne. « Nous menons de nombreux projets pour montrer ce que la machine peut faire », déclare Logtenberg. « Après le lancement de l'automne dernier, les ventes ont été plus lentes que nous l'aurions souhaité. Mais maintenant ça avance bien, avec des projets qui s'accélèrent et les développements des machines. »
Pour ces nouveaux marchés, CEAD explore de nouveaux matériaux. Par exemple, il teste un matériau de SABIC pour la résistance au feu et en discutant avec les fabricants de trains . Avec la possibilité d'imprimer de la fibre continue, le CFAM pourrait-il également être utilisé pour imprimer avec du fil et/ou des capteurs ? «Nous examinons cela», déclare Logtenberg. « Nous travaillons avec une entreprise pour intégrer la fibre d'acier , qui est également conducteur.
Vision d'avenir
Beaucoup dans l'industrie des composites traditionnels, se demandent comment les composites à fibres continues imprimés en 3D peuvent concurrencer les composites conventionnels lorsqu'ils ont une teneur en fibres si faible et un potentiel de délaminage si élevé entre les couches imprimées. "Bien sûr, la force de la direction z est l'une des choses les plus difficiles pour les composites imprimés en 3D", convient Logtenberg. « Actuellement, nous ne sommes pas en concurrence avec les composites conventionnels. Nous pensons qu'à l'avenir, nous pourrons rivaliser avec les composites conventionnels car notre production est entièrement automatisée, mais nous avons un long chemin à parcourir. À l'heure actuelle, il s'agit d'un ajout aux méthodes de fabrication actuelles, offrant de la flexibilité et ouvrant des possibilités de conception et de production. »
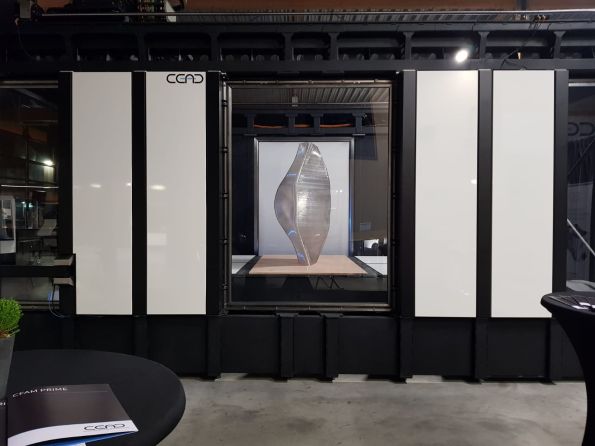
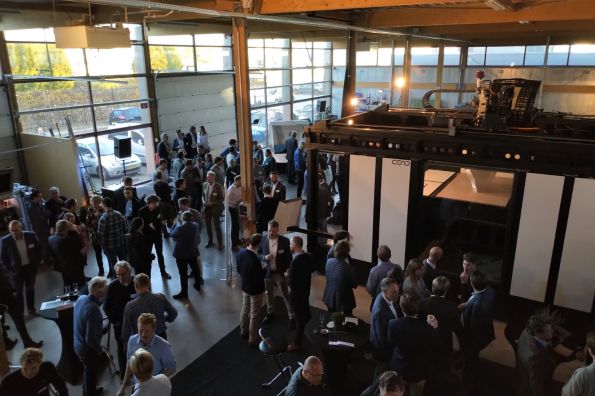
La machine CFAM Prime à son lancement en 2018.
SOURCE :CEAD
Résine
- Comprendre l'ingénierie composite et la fibre de carbone
- Impossible Objects s'associe à BASF pour l'impression 3D composite
- La fabrication continue de fibres brouille la frontière entre l'impression 3D et l'AFP
- Covestro lance les thermoplastiques à fibres continues Maezio
- Fabrication continue de fibres (CFM) avec des composites moi
- matériau composite de SD Mines présenté lors d'un concours de pont composite
- Impression 3D de composites avec fibre continue
- Matériaux composites :où les trouver au NPE2018
- Impression 3D de matériaux composites :un guide d'introduction